
dl/d/V, мм/цикл
Рис. 7,24. Влияние асимметрии цикла нагружения на скорость РУТ и параметры КДУР (Al-M g-Zn, В- t = 300 . 10 мм)
При Л: 1 - 0,12; 2 - 0,33; 3 - 0,50
Рис. 7.25, Зависимость параметров п2 и С2 второго участка КДУР от толщины об разцов
1 —сплав АМг-61, 2 —сплав А1—Mg—Zn
dl/dAf, мм/цинл
Рис. 7,26. Кинетические диаграммы усталостного разрушения для ос новных зон сварного стыкового соединения сплава АМг-61
Зоны: 1 — основной металл и линии сплавления, 2 — сварного шва, 3 — сварного шва, испытания в 3%-ном растворе NaCl
ло зависит от металлургических и структурных факторов, от воздействия коррозионной среды.
Для второго участка КДУР скорость РУТ и параметр С2 в металле шва в ^ 1,5 раза выше, чем в основном металле и металле у линии сплавления. Коррозионная среда увеличивает скорость РУТ во всех зонах сварного со-
Статистические характеристики параметров второго участка КДУР основных зон сварного стыкового соединения (АМг-61, t = 10 мм, воздух)
Параметр КДУР |
Зона сварного |
х |
S |
и, % |
Значимость |
|
|
|
соединения* |
различия |
|||
|
|
|
|
|
||
|
|
ОМ |
2,29 |
0,055 |
2,4 |
|
п2 |
|
ЛС |
2,30 |
0,050 |
2,2 |
Нет |
|
|
МСШ |
2,34 |
0,048 |
2,0 |
|
Сг • 10- |
|
ОМ |
1,5 |
0,117 |
7,8 |
Да |
|
|
МСШ |
2,32 |
0,80 |
34,5 |
|
|
|
|
||||
Рг |
|
ОМ |
1,25 |
0,125 |
10,0 |
Да |
|
МСШ |
1,06 |
0,465 |
44,0 |
||
|
|
|||||
|
|
|
||||
Kfs, МПа • / |
T |
ОМ |
28,2 |
1,86 |
6,6 |
Да |
ЛС |
24,3 |
1;77 |
7,3 |
|||
N |
N |
|
|
|||
|
1,55 |
|
||||
|
|
МСШ |
24,6 |
6,3 |
|
•ОМ —основной металл, ЛС —линия сплавления, МСШ —металл сварного шва.
единения в 1,6—2,5 раза, отмечено некоторое уменьшение л3, статистики которого дня КДУР металла шва равны: и з = 7,0; s = 1,2. Статистические характеристики параметра р в формуле (7.14) для воторого участка КДУР металла шва равны: р 2 = 1,06; s = 0,46 при испытаниях в воздухе и р 2 = = 0,75 и s = 0,40 при испытаниях в коррозионной среде.
7.3.2.Вероятностные аспекты зарождения
иразвития разрушения в сварных соединениях
Результаты исследований и накопленный опыт эксплуатации позволяют сделать вывод, что инициатором разрушения сварных конструкций в боль шинстве случаев являются концентраторы напряжений. Например, из ана лиза, проведенного Международным институтом сварки, следует, что на до лю этого фактора приходится более 50% случаев разрушения [22]. Вместе с тем имеется немало примеров успешной эксплуатации конструкций с де фектами достаточно большого размера.
Все это способствовало формированию концепции неизбежного присут ствия дефектов во всех сварных конструкциях. Принятие такой концепции требует более глубокого изучения факторов, контролирующих процесс развития разрушения сварных соединений с учетом стохастической приро ды образования дефектов, случайного колебания их геометрических пара метров и случайного расположения инициаторов разрушения в сварных соединениях. При малоцикловом нагружении разрушение инициируется на различных участках сварной конструкции практически одновременно. Взаимное влияние инициаторов существенно изменяет кинетику разруше ния и может повлиять на долговечность соединения. Поэтому прогнозиро вание работоспособности и надежности сварных конструкций, подвержен ных действию переменных нагрузок, должно осуществляться с учетом специфических особенностей механизма их разрушения.
Анализ многочисленных экспериментальных исследований кинетики
разрушения сварных крупногабаритных конструкций позволяет выделить три типа инициаторов разрушения, обусловливаемых их взаимным распо ложением: точечные, линейные и плоскостные [23].
Примером точечных инициаторов являются одиночные шлаковые вклю чения, поры, короткие по длине подрезы, т.е. дефекты, имеющие малую про тяженность. Их взаимное влияние с точки зрения инициации и развития разрушения исключено. Развитие разрушения от таких инициаторов проис ходит путем распространения изолированных трещин.
Для прогнозирования разрушения от таких инициаторов необходимо кроме механических характеристик располагать информацией о статисти ческих законах распределения геометрических параметров дефектов. При меры прогнозирования влияния точечных инициаторов, выполненного на вероятностной основе, приведены в работах [24, 25].
Ко второму типу инициаторов разрушения относятся ориентирован ные вдоль линии цепочки дефектов или участки конструкции с резко вы раженной геометрической или структурной неоднородностью. Характерной особенностью таких инициаторов является взаимное влияние соседних оча гов разрушения. Вследствие этого процесс распространения разрушения происходит путем непрерывного образования новых трещин на различных, не связанных между собой участках, подрастания их и слияния. Слияние мелких трещин, возникших в отдельных точках, в единую, протяженную по длине магистральную трещину способствует существенному по сравне нию с точечным инициатором увеличению скорости роста трещины в глубину.
В плоскостном инициаторе трещины также возникают в различных точ ках, однако их слияние увеличивает размер магистральной трещины в двух направлениях: по глубине и по длине. Скорость роста трещины, проходя щей через участки с дефектами, значительно возрастает, кроме того, облег чается переход к хрупкому разрушению.
Первый тип инициатора разрушения встречается в конструкциях, свар ные швы которых механически обрабатывают после сварки (например, корпуса реакторов, детали машин и др.у. Третий тип инициатора встречает ся относительно редко, преимущественно в сварных швах толстостенных конструкций, выполненных электронно-лучевой, электрошлаковой свар кой или в случае использования узкощелевой разделки кромок сварного соединения.
Линейные инициаторы относятся к числу наиболее распространенных в сварных конструкциях, и, несмотря на это, закономерности разрушения при наличии таких инициаторов изучены недостаточно.
Результаты экспериментального исследования закономерностей разру шения крупногабаритных элементов сварных корпусных конструкций свидетельствуют о том, что усталостное разрушение инициируется, как пра вило, в зонах концентрации напряжений —около линии сплавления в свар ных соединениях с механически необработанными швами или в вершинах различных сварочных дефектов.
Концентрация напряжений, обусловленная усилением сварного шва, зависит от многих параметров, но в пределах одного сварного соединения наибольшее относительное колебание имеют радиус перехода от шва к ос новному металлу R и угол сопряжения в. Именно эти два параметра оказы вают главное влияние на величину и характер изменения концентрации
напряжений вдоль кромки шва. Наиболее вероятным местом зарождения разрушения является зона перехода от усиления шва к основному металлу.
Значительные колебания геометрических параметров профиля сварного соединения в этой зоне способствуют тому, что при стабильной технологии сварки концентрация напряжений на различных участках вдоль зоны пере хода от шва к основному металлу может изменяться в широких пределах. Обычно при расчете долговечности конструкции принимают либо среднее значение, либо с заданной вероятностью минимальное значение радиуса пе рехода. Однако как в первом, так и во втором случае сохраняется двух стадийный подход к процессу разрушения, т.е. рассматривается зарождение трещины и последующий ее рост. Появление трещин на других участках шва игнорируется. Вместе с тем экспериментально установлено, что кинети ка образования новых очагов разрушения на соседних участках шва значи тельно влияет на форму фронта поверхностной трещины и, следовательно, на скорость ее роста. Очевидно, в данном случае традиционную двухстадий ную схему разрушения необходимо дополнить рассмотрением стадии на копления очагов разрушения вдоль линии сплавления.
В зонах перехода от шва к основному металлу с высоким уровнем концентрации деформаций реализуются условия жесткого асимметричного цикла нагружения, что позволяет для расчета долговечности до зарождения разрушения N0 использовать уравнение малоцикловой усталости следующе го вида [6]:
_ |
In [100/(100 - ф ) |
(7.15) |
|
€ а _ 4N 'S + (1 + г)/(1 -г ) + £(1 + (о_ i / ая )(1 + r)/(1 - |
|||
г)) |
|||
где еа |
—амплитуда деформаций; N0 —число циклов до зарождения разру |
||
шения; г — коэффициент асимметрии цикла; Е, ob, а_ |
ф — соответст |
венно модуль упругости, предел прочности, предел усталости и попереч ное сужение металла; т = 0,5приаь < 700 МПа; т = 0,5 + 0,002 (рь —700) при оъ = 700-М200 МПа.
Обширные теоретические и экспериментальные исследования [6, 7] позволяют считать, что при установившемся режиме циклического нагру жения значения коэффициента концентрации деформаций ке в вершине сварочного дефекта при а# < а0>2 можно принять приближенно равным коэффициенту концентрации напряжений а а. Следовательно, амплитуду деформаций в (7.15) можно выразить в зависимости от коэффициента концентрации напряжений в зоне перехода от шва к основному металлу
(7.16)
Поскольку изменение геометрических параметров сварного соединения имеет случайный характер, процесс зарождения разрушения на отдельных участках и накопление повреждений целесообразно рассмотреть в вероят ностной постановке.
Число нагружений до появления трещины зависит от характеристик рассеяния механических свойств металла околошовной зоны (obi а_х, ф, Е) и характеристик рассеяния коэффициентов концентрации напряже ний а ст. Учет случайного колебания всех параметров, входящих в (7.15),
при построении аналитической модели приводит к сложным для после дующего анализа зависимостям. Поэтому целесообразно в первом прибли жении рассмотреть только влияние случайного колебания значения аа, так как при стабильной технологии сварки этот параметр изменяется вдоль границы шва в более широких пределах, чем механические свойства.
Пользуясь результатами измерения профиля шва, можно показать, что во многих случаях функция распределения величин оса соответствует зако-
ну Вейбулла |
, |
|
F(a0) = 1 - ехр^- ^ |
° д С ^ | |
(7.17) |
Согласно положениям теории вероятности, если известна плотность рас пределения случайной величины / ( а ст) и задана функция N0 = y(oHi а а), то плотность распределения случайной величины определяется соотно шением [26]
g (N o )= fM N 0)} I * '(N0) | |
(7.18) |
Плотность распределения случайной величины otaопределяется дифферен цированием выражения (7.17). Используя уравнение (7.15) с учетом выра жений (7.16) —(7.18), определим плотность распределения долговечности до зарождения разрушения:
<Р(Мо) - с * |
Ь ~ 1 |
|
g(N0) = - |
X |
|
а чф о) |
|
|
|
|
т — 1 |
Xexp I - т » ) - |
4т lg [100/(100 —<//)]No |
|
|
(7.19) |
|
( |
/ |
1 + Г V |
где функция ip(No) определена следующим соотношением:
V(N0) = |
£’lg[100/(100 —ф)] |
аьа _ 1 |
|
+1й |
+ |
(7.20) |
|
|
|
Он{°Ь+ ° - 1 1+г j |
|
|
) |
|
Обозначив NH —число нагружений, которые должна выдержать конст рукция согласно установленному ресурсу, можно вычислить вероятность появления трещин на линии сплавления в период ее эксплуатации
P ( N < N H) = / g(N 0)d N 0 |
(7.21) |
i |
|
Следует обратить внимание на тот факт, что применительно к конструк циям с достаточно протяженными швами функция плотности распреде ления долговечности до зарождения разрушения (7.19) фактически ха рактеризует плотность распределения суммарной длины поврежденных участков вдоль шва при заданном значении N{. Вследствие этого
вероятность зарождения разрушения численно равно отношению суммар ной длины поврежденных участков к общей протяженности шва, а пра вая часть уравнения (7.21) выражает зависимость относительного накоп ления повреждений L ^ lL m от числа нагружений Nf
— |
Nt |
(7.22) |
= ; g(N)dN. |
||
Ьш |
i |
|
Для экспериментальной проверки уравнения (7.22) воспользуемся результатами испытания на малоцикловую усталость сварных штуцер ных соединений в виде дисков диаметром 980 мм, толщиной 40 мм с диаметром кругового шва 120—260 мм. Сварные швы выполнены руч ной дуговой сваркой. Функция распределения случайной величины под чиняется закону Вейбулла (7.17) с параметрами а = 3,08;' Ъ = 6,9; с = 0.
В процессе испытания фиксировали длину отдельных трещин на гра нице шва и суммарную длину трещин в зависимости от числа нагруже ний. Как и предполагалось, при осесимметричном нагружении зарожде ние разрушения на различных участках имело случайный характер, а распределение координат этих участков подчинялось равномерному рас пределению.
Процесс накопления повреждений на линии сплавления иллюстрирует рис. 7.27. Обращает на себя внимание тот факт, что независимо от длины шва экспериментальные точки располагаются вблизи кривой, рассчитан ной по уравнению (7.22)». Это позволяет предположить, что вдоль линии сплавления разрушение развивается только путем слияния вновь образо ванных трещин. Интенсивное накопление повреждений на линии сплав ления вызывает опережающее увеличение размера большой полуоси поверхностной трещины по сравнению с усталостным ростом ее малой
полуоси в глубину.
В зависимости от вида функции плотности распределения коэффициен та ке зона перехода от шва к основному металлу может быть отнесена либо к линейному инициатору, либо к точечному.
При относительно малой дисперсии и высоком уровне среднего значе
ния |
коэффициента концентрации деформаций ке (рис. 7.28, кр. 2) дли |
тельность AN0 периода распространения разрушения вдоль зоны перехода |
|
от |
шва. к основному1 металлу существенно меньше количества цик |
лов |
Np, затраченных на развитие изолированной одиночной трещиной |
от момента зарождения до критического размера. При такой ситуации сравнительно быстро образуется протяженная магистральная трещина в результате накопления повреждений вдоль кромки шва. Подрастание отдельных трещин за этот период не вносит заметного вклада в общий процесс развития разрушения. Такой характер распределения / (ке) сви детельствует о наличии ярко выраженного линейного инициатора. С уве личением дисперсии ке (см. рис. 7.28, кр. 1) возрастает длительность периода образования новых трещин вдоль кромки шва и при Np процесс образования новых трещин перестает играть преобладающую роль. В предельном случае имеет место рост одиночных изолированных
трещин.
Таким образом, статистические закономерности зарождения разру-
Рис» 7.27. Зависимость накопления повреждений в линейном инициаторе от числа
нагружений при а = 480 (1) и 680 МПа (2)
Длина шва Lm = 470 мм (7) , L ш = 630 (IT), L m = 820 мм (III)
Рис. 7.28, Функции плотности распределения коэффициента концентрации деформа ций вдоль зоны перехода от шва к основному металлу
1 — при малой дисперсии и сравнительно высоком уровне среднего значения Ке% 2 —при большой дисперсии
шения на линии сплавления влияют на кинетику формирования поверх ностных усталостных трещин и последующее их развитие.
Приравняв уравнение (7.22) нулю и единице, можно определить дли тельность периода образования новых трещин вдоль линии сплавле ния AN и путем сопоставления величин AN и Np выделить два крайних случая, для которых возможно использовать расчет долговечности по традиционной двухстадийной схеме. При этом в случае точечного ини циатора коэффициент интенсивности напряжений необходимо подсчи тывать как для равновесной поверхностной трещины, а в случае линей ного инициатора —как для краевого надреза.
Однако наиболее часто дисперсия коэффициента концентрации дефор маций вдоль зоны перехода от шва к основному металлу соответствует некоторому промежуточному случаю, при котором достижению предель ного состояния препятствует процесс подрастания отдельных трещин, возникших на различных участках вдоль кромки сварного шва, в глуби ну и длину, появление новых трещин и слияние соседних, что является наиболее сложным для инженерных расчетов. Многообразие случайных
186
факторов, влияющих на зарождение и распространение разрушения вдоль шва, затрудняет построение аналитических моделей.
Действительно, как показывают экспериментальные исследования, параметры формы возникающих усталостных трещин колеблются слу чайным образом. Стохастической является природа распределения ини циаторов разрушения, обусловленная геометрической и структурной неоднородностью зоны перехода от шва к основному металлу. Наблю дается разброс значений механических свойств и характеристик трещиностойкости в локальных зонах сварного соединения.
Подводя итого рассмотрению вероятностных аспектов проблемы ма лоцикловой усталости сварных соединений необходимо подчеркнуть, что разрушение крупных конструкций, насыщенных сварными швами, относится к числу сложных многофакторных явлений и может быть пред ставлено в виде случайного сочетания нескольких одновременно разви вающихся процессов: зарождение отдельных трещин на различных, не связанных между собой участках —инициаторах; их рост и появление новых трещин; объединение между собой трещин, развивающихся на соседних участках.
Стохастическая природа явления создает предпосылки к многовариант ности путей и траекторий развития разрушения. В этих условиях аналити ческие модели мало пригодны для предсказания надежности и долговеч ности сварных конструкций. По-видимому, наиболее перспективным для этих целей является метод имитационного моделирования, кото рый представляет собой статистический численный эксперимент, осу ществляемый на ЭВМ путем последовательного пошагового анализа про цесса разрушения, имитирующего реальный характер распространения разрушения в конструкции с учетом вероятностной природы действующих факторов. Имитационное моделирование позволяет на каждом шаге оце нивать сложившуюся ситуацию и в соответствии с ней определять или из менять дальнейший ход развития разрушения, учитывать влияние неиз бежно присутствующих случайных возмущений процесса. В частности, учитывать акты появления новых очагов разрушения и связанное с ними изменение напряженно-деформированного состояния конструкции, учи тывать объединение соседних трещин, возникновение на отдельных
участках актов хрупкого разрушения или коррозионного растрескивания и др. Все это создает возможность учитывать в машинном эксперименте многовариантность путей эволюции разрушения в сложных сварных кон струкциях, приближая тем самым его к реальности.
7,3,3, Имитационное моделирование развития разрушения в сварных соединениях
Основой для имитационного моделирования являются результаты экспериментальных исследований, анализ которых позволяет учесть в модели закономерности и специфические особенности процесса разру шения, выявить и оценить основные стохастические факторы и параметры их распределений.
Экспериментальное изучение закономерностей разрушения проводи ли в лабораторных условиях путем малоцикловых испытаний круглых
стальных дисков диаметром 550, |
980 и 1300 мм, толщиной |
30 100 мм |
|||
с диаметрально |
расположенным |
стыковым |
швом или |
с круговым |
|
швом, приваривающим в центре |
диска штуцер. Методика испытаний та |
||||
ких образцов в условиях |
двухосного осесимметричного изгиба изло |
||||
жена в работах |
[27, 28]. |
При |
изготовлении |
образцов стремились со |
хранить технологическое подобие по отношению к реальной конструкции. Лабораторные испытания показали, что в образцах, как и в реальных конструкциях, усталостные трещины возникают практически одновре менно на различных участках, расположенных случайным образом вдоль шва. Развитие разрушения идет путем подрастания возникших трещин, появления новых и слияния соседних (рис. 7.29). Статистическая обра ботка длин исходных трещин выявила, что они подчиняются вейбуллов-
скому распределению с параметрами с = —2,0; а = 6,02; Ъ= 1,57. Устойчивой формой одиночной поверхностной трещины в условиях
двухосного изгиба является полуэллипс, отношение осей которого по мере роста трещины непрерывно изменяется в соответствии со следую щей эмпирической зависимостью:
Ъ |
Ь |
(7.23) |
- |
= 0,96 - 0,78 — , |
|
/ |
t |
|
где b, I, t —размеры полуосей трещины и толщина образца соответственно. Эта же закономерность сохраняется и в случае развития нескольких близко расположенных в одной плоскости полуэллиптических трещин. Изменение конфигурации фронтов отдельных трещин из-за наличия со
седних не существенно до момента их объединения.
После слияния внутренних краев соседних трещин образовавшийся фронт приобретает сначала седлообразную форму (рис. 7.30), в дальней шем сравнительно быстро происходит выравнивание формы фронта тре щины и начинается переход к устойчивой форме. Аналогичные законо мерности наблюдались при объединении трещин, имеющих неодинаковые исходные размеры, а также одновременно объединении нескольких трещин.
Проведенный анализ позволяет предположить, что за условие объеди нения можно принять момент слияния внутренних краев соседних трещин. При этом за длину эквивалентной им полуэллиптической трещины при
расчетах следует |
принять расстояние между внешними концами тре |
щин, а за глубину |
—глубину наибольшей из них. |
Результаты проведенных экспериментов позволяют перейти к созданию имитационной модели Процесса разрушения, при разработке которой приняты следующие допущения: зона перехода шва к основному металлу состоит из отдельных участков длиной 2/,• (случайная величина), в пре делах которой профиль контура перехода принят неизменным, а величи на коэффициента концентрации напряжений а0 постоянной; функция распределения ota для заданного типа соединения зависит от случайных независимых параметров: радиуса R и угла в зоны перехода; случайные величины 21f и аа являются независимыми; в момент инициации усталост ная трещина имеет длину, равную длине участка 2//, и глубину Ь0 =0,5 мм; длительность периода зарождения трещин Afo на каждом участке зави-
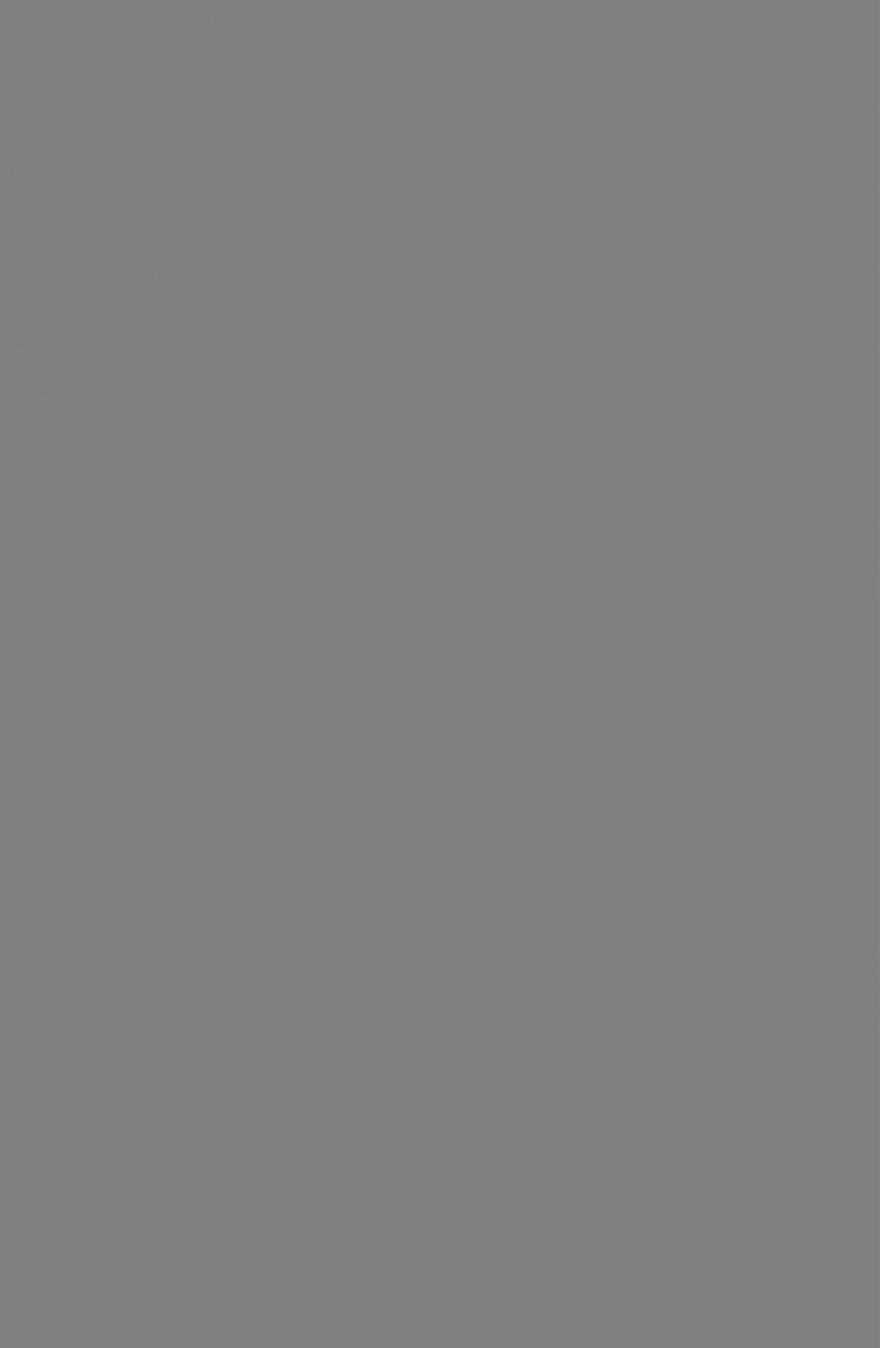
Рис, 731, Структура алгоритма расчета, ос нованного на имитационном моделирова нии процесса разрушения
щая его физическую сущность. Банк жспериментальных данных включает информацию о параметрах функций распределений длин возникающих тре щин, величин R и в , характеристи ках механических свойств и трещи ностойкости сварного соединения. Пе речисленные данные получены эк спериментально в результате испыта ния крупногабаритных сварных образ цов, в которых сохранены технологическое подобие и схема нагруже ния по отношению к реальной конст рукции, а также взяты частично из литературных источников.
Банк теоретических зависимостей содержит формулу для вычисления
коэффициентов концентрации напряжений и деформаций, долговечности до зарождения разрушения, коэффициентов интенсивности напряжений вдоль фронта трещины, усталостного подрастания трещин.
В исходных данных указывается информация о типе сварного соеди нения, его геометрических параметрах, условиях нагружения, предель ном состоянии разрушения, уровне номинальных напряжений, количестве вариантов численного эксперимента. В зависимости от исходных усло вий управляющая программа выбирает из информационных банков соот ветствующие данные и теоретические зависимости и включает их в ал горитм имитационной модели, которая реализуется в следующей после довательности.
Сначала производится разбиение шва на отдельные участки произволь ной длины 2//, величины которых задают с помощью генератора случай ных чисел (ГСЧ) в соответствии с экспериментально установленной функцией распределения F (211 ). Аналогичным образом каждому участку присваивают значения R и в и определяют величины аа, после чего на основе деформационного критерия малоцикловой усталости подсчиты вают число циклов до зарождения разрушения N0f. В результате получа ют значения координат участков, их длин и долговечностей. Затем на ходят участок с минимальным значением 7V0/» характеризующим долго вечность сварного соединения до зарождения разрушения А^0, и увели чивая значение N0 на величину А = 50 -г 500 циклов, производят расчет подрастания трещин в глубину и длину на участках, где N0{ < N 0 4-/А, и определяют их новые координаты и размеры. При этом анализируется возможность слияния соседних трещин. Расчет прекращают при достиже нии предельного состояния разрушения. Для учета рассеяния парамет ров действующих факторов методика предполагает многократное повто
рение расчетов на ЭВМ при идентичных исходных данных с измененным начальным состоянием ГСЧ. Завершается расчет статистической обработ ки полученных результатов.
Рассмотрим возможности практической реализации метода имитацион ного моделирования на примере прогнозирования долговечности круг лой крышки со стыковым диаметрально расположенным швом. Крыш ка имеет диаметр 550 мм и толщину 30 мм, она шарнирно закреплена по контуру и нагружена равномерно распределенным давлением. Цикл нагружения — пульсирующий, с номинальными напряжениями 400— 900 МПа.
Уравнение скорости роста трещины принято в виде v = = 5,21 10”8А ^12,45мм/цикл. Рассеяние механических свойств сварного соединения, контролирующего сопротивление разрушению, учитывали путем вариации параметра с в уравнении Пэриса. В соответствии с ре зультатами экспериментов закон распределения значений с принят лог нормальный со среднеквадратическим отклонением S\gc = 0,102. Резуль таты расчетов показали на рис. 7.32, где представлены 95%-ные границы доверительных интервалов, построенные по моменту зарождения разруше ния N0 и по моменту нарушения герметичности плоской крышки NH. Точками показаны результаты экспериментальных исследований аналогич ных образцов при двухосном осесимметричном изгибе. Расположение то чек на графике свидетельствует о достоверности расчетного метода.
Длительность периода развития разрушения при малоцикловом на гружении и переход к нестабильному росту трещины существенно зави сят от формы фронта поверхностной трещины, характеризуемого отно шением полуосей Ь/1. Имитационное моделирование позволяет просле дить кинетику изменения формы магистральной трещины, образуемой путем случайного слияния отдельных трещин, возникающих вдоль кром ки шва в процессе циклического нагружения сварного соединения.
На рис. 7.33 представлены результаты расчетов применительно к плоской круглой крышке при изгибе. Кривая 1 характеризует изменение полуэллиптической трещины, возникшее от точечного инициатора, т.е. одиночной растущей трещины. Кривая 2 характеризует такую трещину, для которой значение К\ вдоль всего фронта остается постоянным. При циклическом нагружении сварного соединения с необработанными швами рост большой полуоси значительно превышает по темпу изменения малой полуоси (см. рис. 7.33, кр. 4). Очевидно, что это происходит благодаря интенсив ному накоплению вдоль кромки шва сливающихся между собой мелких трещин. В результате этого соотношение полуосей поверхностной тре щины в процессе всего циклического нагружения остается весьма низ ким. Это означает, что, во-первых, скорость развития разрушения в на правлении трещины элемента в сварных соединениях с необработанными швами будет выше, чем в листовом металле, и, во-вторых, такая форма поверхностной трещины способствует переходу от усталостного разру шения к нестабильному хрупкому при достижении трещиной критической
глубины.
Моделирование показывает, что форма поверхностной трещины, об разующаяся при случайном слиянии отдельных трещин вдоль кромки
Рис. 7.32. Долговечность сварных соединений до зарождения разрушения (7) и нару шения герметичности (2) плоской крышки с диаметральным швом при осесиммет ричном изгибе
7 — экспериментальные данные, 7/ — расчетные 95%-ные доверительные границы областей 7 и 2, 77/ —расчетные значения N без учета объединения трещин
Рис, 7.33. Изменение формы фронта поверхностной трещины 1 — при устойчивом росте одиночной трещины, 2 —при развитии трещины вдоль
кромки сварного соединения после оплавления шва, 3 —равновесный фронт трещи ны, 4 —при развитии трещины вдоль кромки необработанного шва; 7 —данные ими тационного моделирования
шва, существенно зависит от технологии сварки и последующей обра ботки сварного соединения. Например, оплавление границ шва по тех нологии ИЭС им. Е.О. Патона благоприятно влияет на кинетику форми рования фронта усталостной трещины. Значения bjl существенно воз растают (см. рис. 7.33, кр. 2) по сравнению с соединениями, непрощедшими такой обработки. Однако и в этом случае отдельные случайные акты слияния соседних трещин способствуют образованию более вытя нутых, чем при точечном инициаторе, поверхностных трещин.
В связи с тем, что процесс объединения трещин носит случайный ха-
рактер, изменение формы фронта трещин сопровождается значительным рассеянием значений параметра Ь/1, поэтому имитационное моделирова ние позволяет получить более объективный прогноз надежности и дол говечности сварной конструкции, чем при использовании детерминиро ванных подходов.
7.4. Рассеяние параметров нагружения и надежность при случайном нагружении
7.4.1. Факторы, обусловливающие рассеяние усталостного ресурса стандартных образцов
Процесс накопления усталостных повреждений является случайным процессом. Это в равной степени относится и к стадии зарождения макротрещины и к периоду ее распространения. Поэтому даже при проведении усталостных испытаний практически одинаковых образцов, изготовлен ных из одного и того же прокатного листа, нагруженных регулярным воздействием с постоянной амплитудой, результаты ресурсных испытаний имеют значительный статистический разброс.
К числу факторов, влияющих в данном случае на рассеяние долговеч ности образцов, относятся и неизбежные отклонения размеров сечений, формы концентратора, чистоты обработки поверхности, отклонения от заданных значений амплитуды и частоты нагрузки. Но в большей степени на случайный характер накопления усталостных повреждений оказывает влияние неоднородность механических свойств и структурная неодно родность материала (наличие микропустот, микровключений и т.д.).
Так при проращивании трещины в условиях постоянного размаха КИН (АК = const) наблюдаются резкие увеличения и уменьшения ее скорости. Все известные уравнения механики разрушения не учитывают эти эффекты. Правда, при выполнении инженерных расчетов (на макроуровне) локаль ные колебания скорости роста трещины имеют второстепенное значение.
Использование при вычислении ресурса аппроксимированной диаграм мы усталостного роста трещины приводит к сглаживанию (нивелирова нию) этих скачков, что вполне оправдано при оценке ресурса элементов конструкций. Случайная неоднородность свойств материала на пути роста трещины в конкретном образце ’’перемешивается” с рассеянием этих свойств во всей испытанной выборке образцов и в расчетах характери зуется коэффициентами вариации vm и vc параметров диаграммы усталост ной трещиностойкости (параметров С и т уравнения Пэриса). Если эта выборка является достаточно представительной и отражает свойства ма териала рассматриваемой конструкции, то полученные статистические оценки средних значений параметров трещиностойкости и их дисперсий могут быть использованы для прогнозирования роста трещины в элемен тах данной конструкции.
Получение статистических оценок для механических характеристик ма териалов существенно осложняется, когда прогнозирование долговечности выполняется на стадии проектирования конструкций. В этом случае ге
неральная совокупность должна включать выборки образцов, |
взятые |
на множестве заводов, производящих рассматирваемую марку |
металла, |
13. З а к . 1830 |
193 |
Т а б л и ц а 7.7
Коэффициенты, характеризующие корреляционную связь параметров уравнения Пэриса
а * |
Ъ* |
Источник |
а * |
Ь * |
Источник |
-1 ,3 9 |
-7 ,1 0 |
[32] |
-1 ,3 5 |
-7 ,0 5 |
[34] |
-1 ,2 8 |
—7,21 |
[33] |
-1 ,4 5 |
-6 ,7 6 |
[35] |
и учитывать рассеяние механических характеристик металла в различных плавках.
В отечественных справочниках и нормативных документах приводят ся статистические оценки лишь для некоторых механических характе ристик: модуля упругости Е , предела текучести от , относительного уд линения б5 и относительного сужения при разрыве j//. Так для сталей конструкционных марок, технология производства которых достаточно стабильна, значения коэффициентов вариации указанных характеристик находятся в пределах: vE = 0,03-г0,04; vOT = 0,05 -г0,08; Рф = 0,11 -г0,19.
По зарубежным данным коэффициент вариации вязкости разрушения
для низколегированных сталей не превышает pKl = 0,06-^0,09. Статисти-
1с
ческие распределения всех указанных механических характеристик близки к нормальному закону.
Опубликованные в отечественной и зарубежной литературе резуль таты анализа статистических характеристик параметров циклической трещиностойкости ( С и т ) также свидетельствуют о том, что распреде ления этих параметров не противоречат гипотезе нормального распреде ления [29-31].
Кроме того, статистическая обработка большого объема эксперимен тальных данных, полученных при испытании образцов из различных ма рок сталей и ;алюминиевых. сплавов [32—35], показала, что между зна чениями lgC и т (в уравнении Пэриса) существует тесная корреляцион
ная связь |
(коэффициент корреляции к (lgC, т) « —0,98) |
с линейным |
уравнением регрессии |
|
|
lgC = |
+ б*, |
(7.24) |
где а* и Ь* < 0.
Обобщая результаты испытаний до 200 марок малоуглеродистых и ле гированных сталей, а также алюминиевых сплавов, испытанных при от-
нулевом цикле нагружения (га = 0 |
0,1) авторы работ [32—35] получили |
следующие значения коэффициентов а*иЬ* (табл. 7.7). |
|
При использовании (7.24) в |
вероятностных расчетах уравнения Пэ |
риса лишь параметр т можно рассматривать как случайную величину. Согласно опубликованным данным, значения коэффициента вариации т для сталей и алюминиевых сплавов лежат в пределах vm = 0,12 -г 0,16.
7.4.2. Факторы, обусловливающие рассеяние ресурса элементов конструкций и деталей машин
Неоднородность механических свойств, вариация статистической и цик лической трещиностойкости материалов составляют лишь часть комп лекса факторов, оказывающих влияние на рассеяние усталостного ресурса.
На стадии зарождения малоцикловой трещины к существенным факто рам относится также дисперсия размеров концентраторов напряжений: ра диусов кривизны зон сопряжения элементов, вырезов, галтелей; размеров технологических дефектов сварки (газовых пузырей, неметаллических включений и т.д.).
На стадии роста трещин, помимо рассеяния характеристик трещино стойкости, доминирующее влияние на статистическое распределение ре сурса оказывает рассеяние размеров исходных макротрещин (непроваров, подрезов и других трещиноподобных дефектов), их формы и ориен тации.
Кроме того, статистические закономерности и образования и развития трещин определяются нерегулярным характером силовых и температур ных воздействий. Следовательно, прогнозирование долговечности кон струкций и деталей машин должно базироваться на анализе и использова нии совокупности статистических характеристик всех расчетных пара метров, определяющих случайный характер процессов накопления и развития усталостных повреждений. Рассмотрим характер статистиче ских распределений указанных расчетных параметров долговечности.
Распределение начальных размеров трещин и трещиноподобных дефек тов. На рис. 7.34 для качественно выполненных сварных швов приведена гистограмма распределения глубины подрезов, полученных при 136 не зависимых измерениях на 9 сварных стыках. Плотность распределения глубины подрезов дп имеет экспоненциальный характер с X = 0,12 мм”1
Авторы [36] исследовали распределение глубины обнаруженных тех нологических дефектов, трансформировавшихся в макротрещины. По лученные ими данные, а также данные, взятые из других работ, аппрок симированы на рис. 7.35 тремя функциями распределения: экспонен циальной, логнормальной и 7-распределением:
/ (а„)=Хе-х°п, |
|
|
(7.25) |
|||
где Л = 0,588 мм-1, |
|
|
|
|||
/ |
(Ai) = -------------- |
ехр[-А п — — \ |
— -— , |
(7.26) |
||
|
y/2nDaan |
I \ Ма„ ) |
2Da |
|
||
W |
: |
1 мм; |
5 ап = 1 мм, |
|
|
|
Мвп ■ |
|
|
|
|||
|
* |
1 |
|
|
|
|
f(flП ) = |
|
1 ехр (—Хдп) |
при ап > 0,45 мм |
|
||
F 0 ) |
|
|
||||
|
. |
|
|
|
|
|
|
|
0 |
|
|
при ап < 0,45 мм. |
(7.27) |
Здесь X = 0,313 мм”1, 0 = 0,044. |
|
|
Уас/ля/яа |
У а с /п я /п а |
Рис, 7,34, Распределение глубины подреза (И) вдоль границы сплавления качественно выполненных угловых сварных швов
Рис, 735. Распределение обнаруженных технологических дефектов, трансформиро вавшихся в поверхностные трещины
1 —экспоненциальная, 2 —логнормальная, 3 —7-распределение
Как видно на рис. 7.35, все предложенные функции хорошо аппрок симируют экспериментальные данные при глубине трещины менее 10 мм; при больших размерах трещины ближе к опытным данным 7-распреде ление.
В работе [37] приведены результаты дефектоскопии стыковых свар ных соединений фасонок с поясами ферм, выполненных полуавтоматиче ской сваркой в среде углекислого газа (проконтролировано 157 участ
ков |
длиной 300 мм), и стыковых швов балок коробчатого сечения |
(446 |
участков длиной 250 м м ). |
На рис. 7.36 показаны гистограммы распределения размеров обнару женных пор (рис. 7.36, д) и подрезов (рис. 7.36,6). Частичная аппрок симация полученных гистограмм кривыми распределения свидетельст вует о том, что начиная с некоторого размера (порядка 1—1,5 мм) плот ность вероятностей удовлетворительно описывается экспоненциальной зависимостью со значением X « 0,8 -И ,2 мм-1
На рис. 7.37 приведен^ графики функции распределения размеров неметаллических включений, обнаруженных в стыковых швах судокор
пусных конструкций, выполненных из сталей 10ХСНД и 09Г2С |
(2) (тол |
щина листа Ь = 10 -г 14 мм) и стали 16ГС (2) (6 = 10 28 мм) |
[38]. Рас |
пределение глубины обнаруженных поверхностных трещин в угловых швах соединений из стали 4340 показано на рис. 7.38 [39]. Функция плот ности распределения глубины Дд дефектов близка к нормальному за кону, но имеет небольшую скошенность в области малых значений Дд.
Следует отметить, что приведенные данные характеризуют статисти ческое распределение обнаруженных дефектов, а не реально существующих. Современные методы неразрушающего контроля позволяют обнаружить
а |
б |
Частота |
Рис» |
736, Гистограммы распределения размеров обнаруженных пор (а) и подре |
зов |
(б) |
Р /а ) |
Частата |
Рис. 737. Графики функции распределения размеров дефектов-включений в стыко вых сварных швах судокорпусных конструкций
Рис. 738, Распределение глубины поверхностных трещин в угловых швах соедине ний из стали 4340
лишь часть дефектов и тем более не могут дать точной картины относи тельно их формы и размеров. Каждый метод имеет характеристическую кривую чувствительности обнаружения дефектов, которая зависит от материала, конфигурации элемента конструкции, формы и местополо жения дефекта, методики испытаний и других факторов. Конечно, в лю бом случае вероятность обнаружения дефектов (трещин) возрастает
pfzaj, °А |
|
|
|
|
Рис, 739 . Характеристические кривые |
|
|
|
|
|
|
|
чувствительности обнаружения дефектов |
09,99 |
|
|
|
|
|
методами неразрушающего контроля |
|
|
|
|
|
1 —рентгеновский метод, 2 —приме |
|
99,9 |
|
|
3 / f |
j |
нение окрашивающих жидкостей, 3 — |
|
|
|
ультразвуковой импульсный метод |
||||
00 |
|
|
|
|
Л |
|
05 |
|
|
|
|
} |
|
ОО |
|
|
|
|
|
|
|
|
|
|
|
|
|
70 |
|
f i t |
|
|
|
|
50 |
|
|
|
|
||
30 |
|
|
{7 |
|
|
|
20 |
|
|
|
|
|
|
/О |
|
|
|
|
|
|
5 |
|
|
|
|
|
|
2 |
|
|
|
|
|
|
Of25 |
0,5 |
7,0 7,5 2f0 |
5,0 |
70 |
2a,мм |
|
|
|
а |
|
|
|
6 |
Рис, 7.40, Распределение длины / трещины (а) и непроваров L (б)
1 — прогнозируемое распределение образующихся дефектов, 2 — распределение протяженности, 3 —гистограмма обнаруженных непроваров
с увеличением их размеров. Об этом можно судить по графикам на рис. 7.39 [39], определяющим зависимость вероятности обнаружения дефекта от его размеров при использовании различных методов дефекто скопии стальных изделий.
На рис. 7.40 приведены гистограммы и графики плотности распреде ления размеров обнаруженных трещин (рис. 7.40, а) и непроваров (рис. 7.40, б) [40].
На основании анализа большого объема экспериментальных данных
автор работы |
[41] предложил описывать вероятность Необнаруженных |
|
дефектов (трещин) экспоненциальной функцией |
|
|
^N D (®д) = е |
(7.28) |
|
где X = 0,0256 |
мм-1 , а распределение размера фактически |
существую- |
198
щих дефектов к началу эксплуатации конструкции — с помощью выра жения
оо |
|
/ ( Дд)факт “ / ( Дд ( Дд ) / / /0*д) P N D (^д ) ^ ад ' |
(7.29) |
Распределение д/с. Для схематизированного представления поверхност ной трещины в виде полуэллипса с полуосями а и с в работе [42] иссле довано статистическое распределение начального отношения д/с. Установ лено, что для интервала значений 0 < д/с < 1 плотность распределения д/с хорошо аппроксимируется нормальным законом с параметрами :М* (д/с) = = 0,55 и S*(a/c) = 0,18. Фактически параметры этого распределения могут существенно меняться в зависимости от вида конструкции и типа дефек та. Например, при непроваре в стыковом соединении труб или наличии мелкого подреза в протяженном шве М'*(д/с) -►О; •S'* (д/с) ^0,11 -^0,13.
Распределение предельных размеров трещин дпр и спр. Характер ста тистического распределения критических размеров трещин дпр и сПр, а также значения параметров этих распределений можно установить лишь косвенно, с использованием метода статистической линеаризации выраже ний типа
2С п р = 2 /п р — X j с*/ 7Гстопах |
(7.30) |
и располагая стохастическими характеристиками входящих в эти выраже ния параметров.
Распределение К\ О |
(или Кс), как |
отмечается в |
большинстве работ, |
подчиняется нормальному распределению. В работе |
[43] для реактор |
||
ной стали приведены |
значения Af£ |
= 220 МПа\/м, |
= 17 МПа Vм |
|
Iс |
|
с |
и i>Ki ^0,08.
*с
В работе [37] установлено, что для стали ВСтЗсп при температуре —80° и —100° С нормально распределены не только значения вязкости разрушения /с, но и критические размеры трещины. Данные о нормаль ном распределении критических длин трещин для алюминиевого сплава D-16-AT приведены также в работе [30].
Рассматривая выражение (7.30) как функцию случайных независи мых величин и линеаризируя ее в окрестности математического ожида ния, можно вычислить дисперсию предельного размера трещины
|
|
2 |
А пр |
+ |
ш а х |
и стандарт |
5 /пр |
|
*/„р = |
( ™ Klc/ * M l m ax)[DK + ^ т а х ( ^ 1 с/ ^ тах)2] 1/2.(7.31) |
Например, для образцов из стали 09Г2С толщиной 20 мм в работе [44] получено среднее значение Кс при —60° С M% =109 МПа\/м. При сред-
нем уровне критической нагрузки ^ * тах = 0,8аг (и ^сттах = 0,05) для

0' |
/2 |
24 |
?,ма// |
fffS5 |
/fffS |
9 /4 *
Рис, 7,41, Графики нормированной корреляционной функции вертикальных нагру зок от мостовых кранов
Точки — виды технологических режимов нагруженности кранов
Рис, 7,42, Статистическое распределение максимумов нагрузок от подвесных одно балочных кранов
цессы, обладающие свойством эргодичности: стабилизация среднего числа ’’нулей” (пересечений реализациями среднего уровня) наступает в течение 50—60 ч регистрации. Графики нормированных корреляцион ных функций процессов вертикальных воздействий на подкрановые балки показаны на рис. 7.41.
Результаты исследования вертикальных нагрузок от однобалочных подвесных кранов в цехах автозаводов приведены на рис. 7.42. Установ лено, что процессы нагружения от подвесных кранов являются квазистационарными; средний уровень и дисперсия слабо зависят от времени при увеличении продолжительности регистрации реализаций; характер распределения положительных экстремумов близок к рэлеевскому рас пределению.
Измерения внутреннего давления на участках магистральных нефте проводов (на входе и выходе насосных станций), измерения изменений давления продукта в газгольдерах и в других сосудах и аппаратах также свидетельствуют о случайном характере процесса их нагружения.
Таким образом, можно констатировать, что циклические нагрузки на конструкции и детали машин изменяются во времени по типу случай
ных процессов и |
(кроме сейсмических воздействий) имеют, |
как пра |
|
вило, квазистационарный характер. |
|
||
|
Проведение любых вероятностных расчетов неизбежно базируется |
||
на |
детерминистической модели рассматриваемого явления. |
Поэтому |
|
и |
для проведения |
расчетной оценки усталостной долговечности |
(на ста |
дии зарождения или развития трещины) случайный процесс нагружения должен быть заменен некоторым схематизированным регулярным ре жимом нагружения, моделирующим эксплуатационный. В качестве мо делирующих используются регулярные моногармонические и бигармонические с постоянными значениями параметров циклов; программные (блочные) режимы со ступенчатым изменением параметров цикла.
Моделирование нерегулярного процесса моногармоническим явля ется наименее точным из-за отсутствия теории подобия для обоснования назначения параметров циклов, эквивалентных по повреждающей спо собности случайному процессу. Если функция спектральной плотности эксплуатационного процесса имеет два четко выраженных экстремума, т.е. характеризует процесс, представляющий собой суммирование двух достаточно узкополосных процессов, то в качестве моделирующего ре жима бывает целесообразно использовать двухчастотное нагружение.
Наиболее широко для расчетов усталостной долговечности исполь зуется блочное нагружение. При компановке блочного нагружения при меняются методы схематизации случайного процесса, позволяющие выделить циклы (или полуциклы) регулярного нагружения. Из сово купности таких циклов, расположенных в порядке убывания или воз растания амплитуд, и составляются блоки нагружения.
Для нахождения функции распределения амплитуд применяется два
способа: 1) непосредственная схематизация, использующая |
результаты |
|
статистической |
обработки реализации эксплуатационного |
процесса и |
2) применение |
математического аппарата теории случайных функций. |
В ГОСТ 25.101-83 сформулированы правила схематизации случайного процесса методами: экстремумов, максимумов и минимумов, методом размахов, а также более трудоемкими — методом выделения полных циклов и так называемым методом ’’дождя”. Каждый метод имеет свои особенности и обладает различной повреждающей способностью при оцен ке усталостной долговечности расчетного сечения. Различие в оценках ресурса, полученных разными методами схематизации, значительно воз растает при увеличении степени широкополосности моделируемого про цесса.
Таким образом, применение того или иного метода схематизации слу чайного процесса позволяет определить функции распределения макси мумов, минимумов, амплитуд и т.д. Для стационарных случайных про цессов такие функции распределения могут быть получены с использо ванием теории выбросов.
Для компановки блока нагружения графики эмпирических распре делений амплитуд и средних значений цикла, полученные при непо средственном анализе реализации, или графики функций распределений, полученных методами спектральной теории случайных процессов, заме няют ступенчатой линией, которая в графической форме представляет собой один блок нагружения, моделирующего исходный процесс. Число циклов в блоке принимают таким, чтобы прогнозируемый ресурс конст рукции или детали содержал не менее 12—15 блоков. Число ступеней нагружения в блоке назначается в пределах 7—10. Число циклов каждо го уровня (ступени) определяется по функции распределения в соот ветствии с относительными частотами нагрузок этих уровней.
При расчете ресурса на стадии зарождения макротрещины и на стадии ее развития блочная схематизация нагружения используется в совокуп ности с принципом линейного суммирования повреждений. При действии программной нагрузки, состоящей из блоков, в которых уровни амплитуд oaj и числа циклов ступеней п * (/ = 1, 2,..., к), длина сквозной тре-
щины Ik, достигнутая после приложения fc-й ступени нагрузки, может быть представлена в виде
/£ = / 0* + C K ^ o ^ n f , |
(734) |
где /0 ~ начальная длина трещины; С и т —параметры Пэриса; к = 1—ш/2. Это выражение определяет линейное суммирование приращений уста лостной трещины в том смысле, что порядок приложения нагрузок (сту пеней блока) не‘оказывает влияния на ее итоговую длину. При выпол нении вероятностных расчетов уровень нагрузки каждой ступени блока рассматривается как случайная величина, а процессы накопления уста лостных повреждений (роста трещины) и процесс нерегулярного нагру
жения принимаются стохастически не связанными.
Как будет показано в п. 7.4.4, этот приближенный подход находит широкое применение в инженерной практике. Вместе с тем эксперимен тально установлено, что компановка блочного нагружения в соответст вии с функцией плотности распределения экстремумов моделируемого случайного процесса, но без учета взаимодействия амплитуд разных сту пеней блока не обеспечивает идентичности скорости роста трещины при блочном и исходном случайном нагружении. Дня учета влияния на рост усталостной трещины вероятностных характеристик случайного процесса, влияния редких выбросов процесса и их взаимодействия разработаны сложные многофункциональные модели; при использовании этих мо делей получение статистического распределения прогнозируемого ресур
са расчетных сечений осуществляется с привлечением метода Монте-Карло
г» QDA/f
7.4.5.Расчетные модели теории надежности
Втеории надежности одной из основных характеристик является ве роятность безотказной работы объекта в течение определенного интер вала времени его эксплуатации. Когда объект эксплуатируется до пер вого отказа, безотказность работы одновременно характеризует и его долговечность. Однако определение вероятности отказа может выпол няться на основе различных подходов, поэтому оценки надежности од ного и того же объекта (элемента конструкции) при различных исход ных предпосылках окажутся несопоставимыми.
Можно выделить три существующих в настоящее время подхода к оцен ке надежности элементов конструкций. Одним из распространенных и срав нительно простых является оценка надежности, при которой прочность материалов и действующие на конструкцию нагрузки рассматриваются как случайные величины. При этом факт ’’развертывания” вероятност ных свойств нагрузок во времени, а также снижение несущей способ ности сечения во времени условно заменяется понятием статистической
изменчивости этих параметров. При таком подходе может быть опреде лена лишь начальная надежность объекта.
Второй подход базируется на математической (формальной) теории надежности, предполагающей, что изменение надежности системы (или элемента) во времени подчиняется определенным статистическим за
кономерностям, которые определяются на основе экспериментальных данных, полученных при обработке большого объема эксплуатационных отказов. В качестве основных характеристик надежности рассматривают ся: функция надежности, интенсивность отказов, среднее время между двумя соседними отказами и др. Непосредственная реализация этого направления обычно вызывает затруднения из-за отсутствия в достаточ ном объеме информции об отказах изучаемых конструкций.
Третий подход [45] рассматривает пространство качества системы, область допустимых состояний и траектории изменения качества систе мы во времени. Выход траектории из области допустимых состояний (выброс) трактуется как отказ. При таком подходе и воздействия, и по ведение конструкции в период эксплуатации рассматирваются как слу чайные процессы, а достижение предельного состояния (отказ) может явиться также следствием постепенного накопления повреждений, из носа, развития макротрещины; т.е. расчетная модель позволяет учиты вать изменение несущей способности элементов конструкций в период эксплуатации сооружения.
С использованием названных расчетных моделей выполним оценку долговечности элементов конструкций, предельным состоянием кото рых является либо образование малоцикловой усталостной трещины, либо достижение развивающейся усталостной трещиной критического размера.
Воспользуемся широко распространенной в теории надежности кон цепцией, согласно которой выбор закона распределения времени безот казной работы (или ресурса) производится в соответствии с имеющейся информцией о статистических закономерностях появления отказов рас сматриваемой конструкции за период ее эксплуатации.
Поскольку время работы элемента до первого отказа —случайная ве личина Т с плотностью вероятности
Рт = |
- H \ t ) \ t = T9 |
(7.35) |
где Я (г) |
—вероятность безотказной работы на отрезке времени |
[0; Т\ , |
то во многих работах для неремонтируемых элементов при внезапных отказах вместо функции надежности рассматривают связанную с ней функцию интенсивности отказов
Х(0 = -Я '(0 /Я (г ). |
(7.36) |
Для инженерных конструкций вероятности отказов весьма малы, так что интенсивность отказов близка к плотности вероятности (7.36) при t = Т. Если интенсивность отказов известна (получена на основе анализа достаточно большого объема экспериментальных данных), то выраже ние (7.36) можно рассматривать как дифференциальное уравнение от носительно функции tf '( f ) . Решение этого уравнения
Я (г)= Я (0)ехр [ - / X(r)rfr]. |
(7.37) |
о |
|
Обычно начальное значение функции надежности |
(в начальный мо |
мент t = 0) принимается как Я (0) = 1. |
|
Поскольку в данной работе расчетная модель накопления повреждений во времени —образование усталостной трещины или ее развитие —стро ится в функции числа циклов нагружения N , то в дальнейшем будет ис пользоваться N\ ресурс конструкции (или сечения) —N3T циклов. Вы ражение (7.37) при этом запишется в виде
N 3т
Н (N3T) = exp [ - / \( N ) dN]. (7.38)
о
Если за начало эксплуатации сооружения принять стадию завершения приемочных испытаний, то в течение периода эксплуатации можно считать интенсивность отказов постоянной, X = const, и тогда вместо (7.37) ис пользовать
H (t) = exp(-X f). |
(7.39) |
Эта формула выражает экспоненциальный закон надежности, который широко применяется в прикладных расчетах.
Помимо экспоненциальной, широко применяется также модель на дежности, в основе которой —распределение Вейбулла:
Н (Г) = ехр [(- t/tcf о ], |
(7.40) |
где t c = 1/Х —матеиматическое ожидание срока службы (ресурса); 0О — положительный параметр, варьирование которого позволяет описать ши рокий класс распределений. При 0О > 1 выражение (7.40) описывает по ведение ’’стареющих” объектов, у которых интенсивность отказов со временем возрастает.
В расчетах надежности элементов, накапливающих повреждения в про цессе эксплуатации, используется также 7-распределение. Плотность 7-распределения
Р (0 |
= |
г(<3о) exp ( - t/tc) , |
или |
|
|
р (0 |
= |
-------- \ 0о fPo - 1 e- Xt |
|
Г(0о)
где 0О> 1; Г (0О) ~ 7-функция,
Г(0О) = /° x fio ~ 1е~хс1х.
о
(7.41)
(7.42)
(7.43)
Если распределение усталостной долговечности (ресурса N3T) описы вается 7-распределением, вероятность безотказной работы элемента конструкции в течение срока службы т определяется по формуле
Х^о |
т |
|
Н(т > Т) = 1 ------------ |
/ fio - l e~Xtdt. |
(7.44) |
Г (0О) |
о |
|
Параметры распределения (7.44) X и /30 связаны с |
математическим |
||
ожиданием и коэффициентом вариации ресурса М ^эт и |
^^-соотнош е |
||
ниями: |
|
|
(7.45) |
X - 1I M N 3 T v N2 3 r , 0о - ^ л г з т |
|
||
7,4.4. Приложение простейших моделей |
теории надежности к расчету |
||
малоциклового усталостного ресурса элементов конструкций |
|||
Пусть |
вероятность безотказной работы |
цилиндрического газгольдера |
|
в течение |
срока службы т подчиняется 7-распределению. Определим па |
раметры этого распределения и построим функцию надежности для зоны сопряжения оболочки газгольдера с отбортованным патрубком, если отка зом будем считать зарождение в этой зоне малоцикловой усталостной тре щины. В качестве детерминистической расчетной модели используем моди фицированное уравнение Коффина—Мэнсона для условий ’’жесткого нагру жения” [46], преобразованное к виду
2о _ г1Е
о~\ 1+га |
(7.46) |
|
|
1 + |
У |
°ъ |
|
где N 3T — число циклов нагружения до зарождения макротрещины; та — |
|
коэффициент асимметрии цикла напряжений; ф, |
o__l9 оъ, Е — механи |
ческие характеристики материала. |
|
В табл. 7.8 приведены статистические характеристики всех параметров, входящих в выражение (7.46).
Математическое ожидание ресурса M(N3T) вычисляется с помощью формулы (7.46) при подстановке в нее средних значений расчетных па раметров: Л^зт = 7,623 • 104 цикл.
Считая, что рассеяние ресурса газгольдера до появления отказа (зарож дения макротрещины) обусловливается рассеянием определяющих его параметров, для вычисления дисперсии ресурса DNзт может быть исполь-
Т а б л и ц а |
7 Я |
|
|
|
Статистические характеристики расчетных параметров уравнения (7,46) |
||||
Параметр |
Среднее значение, |
Стандарт, SX( |
Коэффициент ва |
|
|
|
|
|
риации, vXi |
€а |
2 ,2 |
• 1 0 -J |
3,52 • 10- 4 |
0,16 |
га |
0,65 |
0,104 |
0,16 |
|
Ф |
0,56 |
0,061 |
0 ,1 1 |
|
|
216 МПа |
38,9 МПа |
0,18 |
|
°Ъ |
540 МПа |
29,5 МПа |
0,055 |
|
Е |
2,1 |
10’ МПа |
8,4 • 10э МПа |
0,04 |
зован метод статистической линеаризации выражения (7.46) вблизи его математического ожидания
DN ST = |
2 1(ЭЛГзх/Эх() 2Dx/, |
|
|
(7.47) |
|
где /= 1,2 |
.........6; х, |
= еа, га, ф, |
а _ ь |
ab, Е. |
|
ЭЛ^эт |
1 - |
In2 |
|
I |
|
|
|
(7.48) |
|||
Эе„ |
2о_! IE |
|
|||
|
|
||||
|
1 + g - i 1 + 'о |
|
|||
|
|
»ь |
1 - Л |
|
|
ЭА^зт
дф
ЭЛ^зх
Эга
ЭЛ^зх Эа_1
ЭЛГэт
1 |
|
1 |
2 |
I - |
”(rhr)Ф |
2а_1/Е |
||
|
1 + 0-1 1 +г< 1 |
|
|
|
1 - г( |
In
1 - ф
2а_ 1 /£
е„ —
0-1 1 + ^о
1 +
д6 1 - г ,
In2
2o_ilE
1 + 2 = i i ^
Оь 1 -» а
2 / |
1 |
\ |
= ________\ |
1 - ф |
) ___________ |
(1 - * )
2а1 1/£’оь(1 - г 0):
д- 1 |
1 +Гд ] 2 » |
1 + |
1 - ''а |
°ь |
g - i 1 +Га 1 2 >
дь 1 - Г а J
f L 1 |
1 +г° |
а1 |
1 ~ го |
8"» “ Г |
---- га-х/е---- 1 3 |
t |
III2.12 |
L |
+ g-i_ 1 +ra J |
L |
аь 1 - г0 J |
|
д* 1 - г о |
|
|
Рис» 7,43, Графики функции вероятности безотказной работы зоны сопряжения па трубка с оболочкой цилиндрического газгольдера в период до зарождения макро трещины
1 — статистическое рассеяние расчетных величин принято по табл. 7.1; 2 —значе ния коэффициента вариации величин, использованных в расчете; умен. 1,5
зт ^ |
\ 1 — Ф J |
|
|
|
0_I |
|
|
|
L |
^0 - 1 |
1 +Га |
1 3 , ( , , ! = * 1 1 М ' |
|||||
J |
\ |
аъ |
1 -га/ |
|||||
|
Оь |
1 - |
Го |
|
|
|
|
|
DN3T = 2,315109 (цикл)2, |
5Лгзт |
= 4,81 |
104 цикл, |
vN3J |
= 0,629. |
|||
Значения параметров 7-распределения |
|
|
|
|
|
|||
X = 1lMN 3rv2N3r |
= 3,3 • 10-5; |
/Jo |
= 1 / ^ зт |
= 2,52. |
|
|
||
С использованием |
полученных значений X, р0 и номограммы |
[47] на |
рис. 7.43 построена зависимость вероятности безотказной работы рас смотренного узла газгольдера от наработанного ресурса (N3T) Д° наступ ления отказа — зарождения макротрещины (кр. 1). При детерминисти ческом подходе определяется среднее значение ресурса и априори назна чается коэффициент запаса по числу циклов nN. Например, в рассмотрен ном случае средний ресурс составил MNsT = 76,23 103 циклов, так что при наработке газгольдером примерно 6500 циклов в год с момента нача ла его эксплуатации и до образования малоцикловой трещины должно пройти свыше 10 лет. Профилактические обследования газгольдера, прово димые каждые 5 лет, позволят в этом случае предотвратить наступление отказа. Однако вероятность безотказной работы газгольдеров в течение планируемого срока невелика: Н(т) « 0,5. Согласно рис. 7.43, кривая 7, при относительно высоком уровне надежности Н(т) = 0,99 и 0,95 период эксплуатации до наступления отказа составит 0,69 и 2,55 года соответ ственно, т.е. гораздо меньше периода профилактических обследований.
208
Нужна ли столь высокая надежность данного сооружения и как опре делить оптимальный уровень его надежности? Решение этих вопросов затруднено тем обстоятельством, что применяемые в отечественной прак тике методики оценки оптимальной надежности распространяются лишь на конструкции и элементы машин, отказ которых сопряжен только с экономическими потерями и не приводит к человеческим жертвам. В рам ках таких ограничений оптимальная вероятность безотказной работы объекта в течение заданного срока службы ориентировочно определяет ся по формулам [48]:
Л ш т » [2и + |
1 |
- (4и + 1)1/2]/2 м, |
(7.49) |
« = К Тн [Ср |
+ |
Сс( 1 + Г„р/Гн)]/СК) |
(7.50) |
где Ср —нормативная стоимость ремонта данного типа конструкции в год, руб.; ке —коэффициент, учитывающий тип конструкции (для емкостных конструкций ке = 90 т 120); ТК — нормативный срок службы данного типа конструкции, год; Сс —средние затраты на обслуживание конструк ции в год, руб.; Ск —стоимость конструкции, руб.; tnj? —время простоев в год. Значения указанных параметров принимались из [48,49].
Для рассматриваемого газгольдера вычисленная по формулам (7.49) и (7.50) оптимальная вероятность безотказной работы до профилактиче ского обследования составила # (т ) = 0,93. По рис. 7.43, кр. 1 это соотвествует примерно трем годам эксплуатации, что меньше межремонтно го периода. Для того чтобы увеличить ресурс, обычно снижают уровень нагрузки либо изменяют конструктивную форму (в зоне концентрации напряжений), наконец, используют материал с более высокими механи ческими характеристиками.
Вероятностная методика позволяет реализовать иной подход: при не изменном среднем значении ресурса увеличить продолжительность без отказной работы при более высоком уровне надежности за счет умень шения коэффициента вариации основных расчетных параметров. Так на рис. 7.43 кривая 2 построена при тех же средних значениях парамет ров, что и i, но изменчивость нагрузки и пластичности металла уменьше на в 1,5 раза. При этом коэффициент вариации ресурса стал i ^ 3T = 0,42,
характеристики 7-распределения: X |
7,4 10“5 и Р0 = 5,66, а период без |
отказной работы при оптимальной |
надежности Н(т) = 0,93 увеличился |
почти в 2 раза. |
|
Таким образом, рассмотренный вероятностный анализ позволяет более
обоснованно назначать периодичность |
профилактических обследований, |
а также нормировать изменчивость тех |
характеристик материала и воз |
действий, которые вносят наибольший вклад в рассеяние долговечности проектируемого объекта.
В рассмотренном примере в качестве отказа, характеризующего пре кращение нормальной эксплуатации газгольдера, принято условие за рождения макротрещины. Однако использованные расчетные выраже ния не позволяют определить ни размер образовавшейся трещины, ни возможность ее самопроизвольного распространения. Размеры этой тре щины зависят от относительного градиента деформаций в зоне ее зарож дения: длина трещины тем больше, чем меньше градиент.
14. Зак. 1830
Практика проведения малоцикловых усталостных испытаний показа ла, что в зоне сопряжения отбортованных патрубков с оболочкой длина зародившейся трещины 1,5 -г25 (5 — толщина стенки сосуда). Приведет ли трещина такого размера только к потере герметичности сосуда или к катастрофическому хрупкому разрушению? Ответ на этот вопрос зави сит от вязкости разрушения металла при минимальной температуре экс плуатации сосуда, а также рассеяния значений этой характеристики.
Кроме того, при вычислении ресурса с помощью выражения (7.46) не учитывается вероятное наличие исходных технологических дефектов (пор, неметаллических включений, микротрещин и т.д.), которые суще ственно влияют на механические характеристики металла. Поэтому при прогнозировании усталосного ресурса элементов конструкций во мно гих случаях предпочтение отдается расчетной модели, описывающей рост усталостной трещины от начального до критического размера. В качестве детерминистической модели роста усталостной трещины обычно исполь зуется выражение для ресурса NpT, полученное при интегрировании урав нения Пэриса:
N pr = (2/4m |
-2)/2 - |
~2)/2)/(m - 2)САо%Рт, |
(7.51) |
где ао и апр — |
начальный и предельный размер трещинй; |
Аон — размах |
номинальных напряжений в сечении с трещиной; С и т — параметры цик
лической трещиностойкости материала; F |
— коэффициент, зависящий |
от отношения полуосей полуэллиптической |
поверхности трещины. При |
этом расчетная модель вероятности безотказной работы объекта может быть принята в виде экспоненциального закона, распределения Вейбулла или 7-распределения, а статистические характеристики величин, вхо дящих в уравнение (7.51), в соответствии с рекомендациями и п. 7.4.1
и7.4.2.
Вработе [50] приведен пример определения вероятности безотказной
работы зоны примыкания патрубка к оболочке шарового газгольдера с использованием 7-распределения потока отказов, а в качестве отказа — принято условие достижения усталостной трещиной критического размера.
7.4.5. Стохастическая связь характеристик случайных процессов нагружения и роста усталостной трещины
К недостаткам рассмотренных моделей теории надежности следует отнести, во-первых, то, что закон распределения ресурса принимается либо на основе априорных представлений о поведении объекта, либо на основе небольшого объема информации об отказах конструкций, подоб ных рассматриваемой. Во-вторых, при нерегулярном циклическом воз действии собственно процесс случаного наружения игнорируется, а ам плитуда представляется как случайная величина.
Совершенствование моделей теории надежности основано на представ лении поведения конструкций и внешних воздействий в виде случайных процессов, а предельного состояния —как случайного выброса из области допустимых состояний. При таком подходе и воздействия, и снижение несущей способности в период эксплуатации рассматриваются как случай ные процессы.
Для задачи о распределении долговечности сечения с одной развиваю щейся трещиной в [54] приведено приближенное решение в виде
Я(т) = 1 - f r +(aKp,t)dt, |
(7.52) |
о |
|
где у+(акр, О — математическое ожидание числа положительных пересе чений предельного уровня (границы предельных состояний) в единицу времени; акр (f) — процесс снижения остаточной прочности сечения с растущей усталостной трещиной, текущая длина которой а{(^\а0) в рас сматриваемый момент определяется с помощью уравнения Пэриса.
Для центрированного узкополосного процесса нагружения
€5е |
° к р ( 0 |
(7.53) |
|
(Ркр> О |
|
ехр ( - а * р(0/2А ,е), |
|
V 2Z VD 7e |
|
||
где ае (t) — огибающая |
случайного процесса нагружения с эффективной |
||
частотой сое. |
|
|
|
При реализации |
этого |
решения трудности вычислительного |
характе |
ра приводят к необходимости введения упрощающих предпосылок. Так, принимается, что процессы ае (f) и акр (t ) являются стохастически не свя занными; для описания кинетики роста трещины при случайном процессе нагружения используется уравнение Пэриса, в котором параметры С и т получены при гармонической нагрузке; используется принцип линейно го суммирования повреждений без учета влияния на скорость роста тре щины амплитуд разных уровней.
В работе [12] описана методика расчета кинетики роста усталостной трещины при случайном стационарном процессе нагружения, позволяю щая учитывать: статистические характеристики режима нагружения (вклю чая его спектральный состав), влияние на скорость роста трещины отно сительно редких выбросов и взаимодействие последовательности выбро сов. Поскольку описанная расчетная модель является сложной много функциональной и ее реализация возможна только с применением ЭВМ, то и для определения вероятности безотказной работы элементов кон струкций с развивающейся трещиной целесообразно использовать числен ный метод статистического моделирования.
На рис. 7.44 показана блок-схема реализации статистического моде лирования. Все используемые для расчета кинетики роста трещины вход ные параметры рассматриваются как независимые случайные величины Еи (и = 1,2, ..., Л), функции распределения которых могут быть заданы эмпирически; для каждого входного параметра назначаются также грани цы области изменения значений случайных величин: EUtн, EUtB — ниж няя и верхняя границы соответственно. Рассматриваемая область значений разбивается на d интервалов и находится вероятность попадания значений случайной величины x ue {е = 1, 2,..., d) в заданный интервал.
Таким образом, исходной информацией для статистического модели рования служат составленные для каждого входного параметра Еи мат рицы значений хие, соответствующих заданным интервалам интегральной вероятности: [0 ; Pu\ ] t [Ри\\ Л л Ь —> [Рud\ 1 ]. Для рандомизации выбора случайного значения х ие величин Еи используется генератор (датчик)
212
I ®
Генератор равномернораспределен ных случай ных чисел
[0 ; 1]
Е
Повторение
операций
I ® |
Н Р |
Статистические распределения входных параметров |
|||
P |
|
|
|
И Р |
|
|
|
Еи= |
|
|
|
|
d |
|
Xld |
|
|
@ [ 0 ;Л .] [ Л .; |
Л 2] [Рц;1] |
[0;J>a ,][J>a i ;J>aa] |
[Pld \ 1] |
|
[0Л ,][Р * |Л а] |
Вероятностьтпопадания значений1[хи случайной величины Еи в заданный интервал |
|||||
Ек ~ [*1 2, *2 1 |
|
|
|
-------------- 1f----------------- |
|
|
|
|
*hd\ |
||
|
|
|
|
|
|
Формирование вектора случайно выбранных значений входных параметров |
|||||
I |
3 |
|
Е |
I |
т а) |
Ек |
Ек+1 |
|
E z-i |
Et |
|
_______Z J Z : _____ |
______________________________ |
Г |
f |
______ |
|
( 5 ) Вычисление ресурса Na с помощью программы C1CL |
|
|
|||
г |
|
|
♦ |
Л |
|
^Я,к |
к+1 |
|
^Д.Х-1 |
NJX.z |
|
I I
(б)Статистическая обработка массива и распечатка функции надежности
-Г
^8) Вычисление статистических моментов M*(Nд),0(Л /д), Дз(^д)» АиС^д) |
|
при г = 250; 400; 600 |
Л^д, цикл |
|
|
Рис, 7,44. Блок-схема процедуры статистического моделирования |
|
Рис, 7.45, График функции ве роятности безотказной работы газгольдера, условием отказа ко торого является достижение усталостной трещиной критиче ского размера
случайных чисел 7, равномерно распределенных в интервале [0; 1]. Каж дое поступающее от генератора число у т сравнивается с интервалами м-й
матрицы. Если у т попадает в интервал |
[Рие; |
Ри>с + 1], то значение случай |
ной величины Еи = х ие9 где и = 1 , 2 , h\ |
е = 1 |
, 2 , d. |
В результате последовательного обращения ко всем h-м матрицам (от 1 до И) формируется очередной к-н вектор Ек случайно выбранных значе ний рассматриваемой системы случайных величин Еи. Затем операции по рандомизированному выбору случайных значений входных параметров повторяются и формируется вектор Ek+i, затем Ек+2 и т.д. до EZi где z — заранее заданное число статистических моделирований.
Полученные таким образом векторы Ек поступают на вход программы, осуществляющей вычисление роста трещин до предельной величины и опре деление к-то значения ресурса расчетного сечения Ыдг к (5). После того как получено z значений ресурса, производится статистическая обработка массива значений вычисляются оценки математического ожидания, дисперсии, а также моменты третьего и четвертого порядка.
Стабилизация значений этих моментов при увеличении числа модели рований z служит признаком достоверности полученной функции распре деления. В качестве примера реализации описанной методики на рис. 7.45 построен график функции вероятности безотказной работы рассмотрен ного цилиндрического газгольдера. Принято, что изменение давления в газгольдере можно представить в виде узкополосного случайного про цесса с коэффициентом вариации ^ = 3 МПа/110 МПа = 0,65. Статистические характеристики входных величин Еи, используемые при вычислении распределения усталостной долговечности газгольдера, при ведены в табл. 19.
Здесь п и tgotj. — характеристики материала, определяющие торможе ние роста трещин при действии выбросов нагрузки [12].
Среднее значение предельного размера сквозной трещины ^Сщ, полу чено из условия квазихрупкого разрушения стенки оболочки при мини мальной эксплуатационной температуре (—60 °С) (см. п. 7.4.2).
Статистические характеристики параметров расчета усталостной долговечности конструкции
Еи |
M l |
VE |
SE |
,^м,н» Еи%в |
|
|
Ьи |
Ьи |
|
|
|
ао |
0,0025, м |
0 ,2 |
0;0007, м |
0,0014; |
0,004, м |
*о |
0,0095, м |
0,17 |
0,0016, м |
0,0055; |
0,0143, м |
2 С П р |
0,05, м |
0,18 |
0,009, м |
0,023; |
0,077, м |
т |
3,5 |
0,05 |
0,17 |
2,89; 3,91 |
|
° Т |
350, МПа |
0,05 |
17,5, МПа |
297,5; |
402,5, МПа |
п |
0 ,6 |
0 ,1 2 |
0,072 |
0,384; |
0,816 |
tg < * T |
0,4 |
0,08 |
0,032 |
0,304; |
0,496 |
В соответствии с графиком функции #*(т), построенным на рис. 7.45 по результатам статистического моделирования (z = 400), при уровне надежности Н - 0,93 ни один из исходных трещиноподобных дефектов глубиной д0 = 1,4-5-4 мм и длиной 2с0 = 1СН28 мм, оказавшихся в зоне сопряжения патрубка с оболочкой, не достигнет предельного размера в течение 7,5 лет эксплуатации газгольдера.
7.5. Теория приспособляемости и структурные модели
В машинах и аппаратах, подверженных повторяющимся воздействиям механической нагрузки и температурных полей, нарушение работоспо собности часто связано с образованием и развитием трещин (малоцикло вая усталость, квазистатическое разрушение) либо с прогрессирую щими изменениями геометрии, происходящими вследствие накопления пластических деформаций в каких-либо ответственных деталях.
Модель идеального упругопластического тела положена в основу пре дельного пластического анализа и, в частности, теории приспособляемости конструкций к циклическим нагружениям [52]. Эта теория позволяет определять предельные значения параметров нагружения, при которых циклические воздействия не приведут к повторяющейся с каждым цик лом неупругой деформации; такая деформация может возникнуть при первых циклах нагружения, но после образования соответствующего поля остаточных напряжений должна прекратиться. Соответственно при использовании теории приспособляемости в расчетах на прочность основ ная концепция состоит в том, что возникновение непрекращающейся циклической пластической деформации любого типа — знакопеременной или односторонней — рассматривается как опасное состояние, исходя из того, что продолжение этого процесса в конце концов (долговечность остается неопределенной) приведет к нарушению работоспособности кон струкции.
Обычно задачи приспособляемости формулируются в детерминирован ной постановке [52]. Однако фактически параметры внешних нагрузок и температурных полей, как и механические характеристики материала, являются случайными величинами. Учет этого обстоятельства позволяет
понять, почему в некоторых случаях при величинах средних запасов по критериям приспособляемости, существенно превышающих единицу, определенная часть объектов по мере увеличения срока эксплуатации требует ремонта или замены в связи с образованием значительных тре щин или с недопустимыми изменениями геометрии. Для определения размахов и приращений неупругой деформации с последующей оценкой долговечности конструкции необходимы методы анализа процессов де формирования, опирающиеся на надлежащие реологические модели.
В последние годы все более широкое признание получают реологиче ские модели, в основе которых лежит представление о том, что многие наблюдаемые эффекты пластического и вязкого деформирования, час то внешне не связанные между собой, можно объяснить микронеоднород ностью реальных материалов, возникающими вследствие этого самоуравновешенными микронапряжениями и их эволюцией в процессе дефор мирования (см. гл. 4). Существует класс статистических моделей, ко торые можно рассматривать как попытку моделирования реальной струк туры металлического сплава — случайного распределения зерен, плос костей скольжения, механических характеристик в микрообъемах [53, 54].
Существенными преимуществами в этом смысле обладает класс моде лей, получивших название структурных, в основе которых лежит извест ная схема Мазинга. В этих моделях реализуется идея конструкционного моделирования микронеоднородности, согласно которой для описания процессов неупругого деформирования с особенностями, наблюдаемыми в опытах, достаточно ввести микронеоднородность в уравнения механи ки формализованно, не ставя задачу отражения реальной структуры сплава.
Развитие структурных моделей привело в последнее десятилетие, по существу, к созданию внутренне непротиворечивой теории неупругого деформирования, охватывающей как реономные, так и склерономные процессы, обобщающей ряд классических теорий (теория течения, дефор мационная теория, теория упрочнения при ползучести) и распространяю щей их на условия повторно-переменного нагружения [55, 56]. Базовый, наиболее простой вариант структурной модели отражает деформационное поведение циклически стабильных (или стабилизированных) сплавов. Если ограничиться условиями пропорционального повторно-переменного нагружения (в частности, в таких условиях находятся опасные точки в зонах концентрации напряжений) и принять во внимание, что в диапазо не рабочих температур реологическая функция любого конструкционно го сплава имеет специфический характер (по форме она приближается к реологической функции идеально-пластического материала), из опре деляющих уравнений структурной модели может быть получено уравнение состояния, формулируемое непосредственно в макропараметрах [55, 56]. Благодаря данному уравнению обнаруживается, что кривые повторно переменного деформирования при различных температурах и скоростях после очередного реверса связаны между собой простой зависимостью — они центрально подобны. Эта и другие вытекающие из анализа законо мерности явились основанием для того, чтобы назвать полученное урав нение состояния принципом подобия.
Уравнение содержит два новых параметра, которым можно дать меха
ническую интерпретацию с позиций принятой концепции микронеодно родности реального материала. Перенос данных параметров из модели деформирования в модель накопления малоциклового повреждения [56, 57] оказался довольно эффективным: полученное уравнение позволяет суммировать накопленное повреждение в соответствии с действительной программой циклического нагружения (этапы быстрого нагружения, выдержки при различных статико-кинематических условиях), при этом соответствие опытным данным оказалось лучше, чем ори использовании метода ’’разделения размахов” Мэнсона.
7.5.1. Оценка вероятностей накопления односторонней деформации и знакопеременного течения
При |
применении теории приспособляемости определению подлежат ве |
||||
роятности |
возникновения |
непрекращающейся циклической деформа |
|||
ции |
— односторонней |
или |
знакопеременной. Время или другой связан |
||
ный |
с |
ним |
параметр |
(число циклов) в расчетах на приспособляемость |
не фигурирует, поэтому о долговечности можно судить лишь косвенно: чем большей оказывается вероятность возникновения одного из опас ных состояний, тем, очевидно, меньше долговечность рассматриваемого объекта, поскольку за заданное время в нем могут бытьнакоплены боль шая деформация или повреждение.
Вероятностные формулировки основных теорем теории предельного равновесия были предложены авторами работы [58], затем по аналогии ими были сформулированы теоремы для определения двусторонних оце нок вероятности прогрессирующего разрушения [59].
Прогрессирующее формоизменение и коробление весьма характерны, например, для металлургического оборудования. Этот эффект приво дит к необходимости частых ремонтов и замен узлов и агрегатов и соот ветственно большим затратам металла и труда.
Теория приспособляемости основывается на двух фундаментальных теоремах — статической и кинематической, с помощью которых можно определить двусторонние оценки для предельных значений параметров нагружения, при которых обеспечивается приспособляемость. Ограни чимся здесь использованием кинематической теоремы, в ней наиболее отчетливо выделены условия возникновения каждого из двух типов циклической деформации — односторонней, накапливающейся с каждым циклом и знакопеременной. Условие накопления односторонней дефор
мации (условие неприспособляемости), |
согласно |
данной теореме, мож |
|
но представить в виде [52] |
|
|
|
/ min [(Ру ~ а*т) Де®(/ ] dv = 0. |
|
(7.54) |
|
Г |
|
|
|
Здесь Ofj |
— напряжение на поверхности текучести |
(обычно используется |
|
кусочно-линейная поверхность Треска); |
o?jT — фиктивные упругие на |
||
пряжения |
от изменяющихся во времени внешних воздействий (механи |
||
ческих нагрузок, температурных полей); Ae°pij |
— кинематически воз |
можное распределение приращений пластической деформации за цикл (механизм прогрессирующего разрушения); знак min означает, что перед
интегрированием по объему детали, в которой ожидается прогрессирую щее формоизменение, в каждой ее точке должно быть определено мини мальное за время цикла значение произведения, стоящего в квадратных скобках; при этом необходимо учитывать, что напряжение а*.т и механизм
разрушения |
связаны ассоциированным законом |
течения, согласно |
которому вектор Де°/;- нормален к поверхности |
= 0 в соответствую |
щем многомерном пространстве.
Согласно кинематической теореме действительный (оптимальный) меха низм разрушения определяет минимальные значения предельных парамет ров нагружения, при которых возможна неприспособляемость [52]. Его отыскание в общем случае сводится к проблеме математической теории оптимальных процессов. При дискретизации задачи, если ограничения и целевая функция линейны, для решения может быть использован аппа рат линейного программирования. Однако если ограничиться определе нием оценок ’’сверху”, можно применить более простой приближенный метод, в котором ’’подходящий” механизм разрушения задается из числа кинематически возможных.
При записи соотношения (7.54) для упрощения были отброшены чле ны, отражающие влияние постоянных составляющих нагрузки; в примере расчета, который будет дан ниже, такие нагрузки отсутствуют. В дальней шем ограничимся случаем циклически изменяющихся тепловых воздей ствий, когда под а!ут следует понимать термоупругие напряжения.
В случае, если напряженное состояние объекта линейное, оц = ±а$, где знак при пределе текучести зависит от знака напряжения а^т , дейст вующего в точке; при этом может учитываться его зависимость от тем пературы. Приращения неупругой деформации, определяющие диссипа цию и работу упругих напряжений, в этом случае также сведутся к од ному компоненту Дер.
Предположим, что параметры внешних воздействий и механические характеристики материала — случайные величины. Тогда определение вероятности возникновения односторонней деформации (вероятность
прогрессирующего формоизменения) |
при принятых |
ограничениях фор |
|
мулируется в следующем виде: |
|
|
|
Дф = Р {/min [(0$ - |
а*) Аер ] < 0 |
1 |
(7.55) |
Т |
|
|
|
Выражение в фигурных |
скобках можно представить в более компактной |
||
форме |
|
|
|
Яф = P \ A S - А е < 0 1 |
|
(7.56) |
Здесь — пластическая диссипация энергии; А е — работа фиктивных напряжений на возможном механизме разрушения. Важно отметить, что при их определении в соответствии с соотношением (7.55) предваритель но в каждой точке рассматриваемого объекта должны быть выделены те значения os и о?, которые при заданном механизме определяют ми нимум произведения в квадратных скобках; лишь после этого выпол няется интегрирование по всему объему.
Другим состоянием, которое в теории приспособляемости рассмат-
ривается как предельное, является возникновение знакопеременной плас тической деформации. Соответствующее достаточное условие (относя щееся к опасной точке) в общем случае циклического неизотермического нагружения может быть представлено в форме
min [(a,/ - |
afjT ) e°pij ] - |
max [(- ац - |
afj7 ) е pij° ] < 0. |
(7.57) |
Т |
|
Т |
|
|
Здесь e^ij |
— скорость |
деформации |
в рассматриваемой |
точке объекта |
в одном из полуциклов, определяющая направления нормали к поверх ности текучести и, следовательно, значение напряжения а/;-, в другом полуцикле знак скорости деформации изменяется на обратный, соот ветственно изменяется напряжение на поверхности текучести. Предпо лагается, что при изменении температуры последняя расширяется (или сужается —при нагреве), не изменяя своей формы.
В случае линейного напряженного состояния соотношение (7.57) при
обретает |
вид |
|
|
min ([oST - a * ) —max (—oST - |
а* ) < 0, |
(7.58) |
|
г |
т |
|
|
где oST |
— значения зависящего |
от температуры циклического |
предела |
текучести в моменты времени тх и т2, отвечающие достижению выра жениями в скобках минимума или максимума.
Выражению, формулирующему задачу определения вероятности
возникновения знакопеременной неупругой деформации, можно |
при |
||
дать |
следующую компактную форму, аналогичную |
(7.58), но |
более |
простую при реализации: |
|
|
|
R |
3n = P { A S T - A o ? < 0 } |
(7.59) |
Здесь AST = oST\ — (—о&гг) = °S T I + °S T I ~ циклический предел теку
чести |
(например, при |
изотермическом |
растяжении—сжатии AS? = |
= os |
— (—os ) = 2os ); |
Да* = ofx — o*2\ |
моменты времени тх и т2 уста |
навливаются из условий, указанных выше. |
|
Соответственно вероятностям достижения двух опасных состояний
могут |
быть определены вероятности |
безотказной работы конструкции |
по каждому из критериев |
|
|
R = |
1 - R - |
(7.60) |
Рассмотрим два возможных подхода к решению, имея в виду исполь зование каждого из них для определения вероятности безотказной ра боты конструкции по двум критериям достижения предельного состояния, принятым в теории приспособляемости. В качестве примера используем объект, подверженный повторяющимся случайным воздействиям неста ционарного температурного поля при несущественных механических на грузках [61].
Первый вариант решения состоит в выполнении последовательных операций над численными характеристиками случайных полей—математи ческими ожиданиями и дисперсиями. На определенном этапе здесь вво дится предположение о нормальном законе распределения и допущение о независимости случайных распределений, характеризующих термоупру гие напряжения и механические характеристики материала (в данной за-
218
даче — предела текучести при однократном нагружении и циклического предела текучести). При этих условиях вероятность безотказной работы по критерию накопления односторонней деформации определяется вы ражением
As ~ А е______
[D[As \+ D [ A e] f ' s |
|
(7.61) |
|
|
|
Здесь Ф(лг) — интеграл вероятностей; As, А е |
— математические ожида |
|
ния величин, входящих в выражение (7.56); |
D[As], D[Ae] |
—их дис |
персии. |
^ |
|
Аналогично определяется вероятность безотказной работы R3n по кри терию возникновения знакопеременной деформации.
Другой путь решения рассматриваемой задачи не требует использова ния предположения о нормальном (или каком-либо другом) законе рас пределения. С помощью неравенства Чебышева можно установить связь между вероятностью безотказной работы конструктивного элемента #, средним значением коэффициента запаса по приспособляемости п и коэф
фициентом вариации данного коэффициента |
Vn = у/Ъ [п]/п |
[60]: |
R > 1 - n V n2 [nV n2 + (п - I)2]"1. |
|
(7.62) |
Среднее значение запаса п и вариация Vn определяются |
(для каждого |
|
из принятых критериев разрушения) по |
данным расчета |
соответствую |
щих значений всех реализаций, обеспеченных исходными данными по температурным полям и характеристикам материала. Заметим, что при использовании теории приспособляемости под коэффициентом запаса (для каждой реализации) понимается обычно множитель при фиктив ных упругих напряжениях, при котором неравенство, соответствующее данному предельному состоянию, обращается в равенство; механические характеристики материала при этом полагают не изменяющимися [52].
Как следует из выражения (7,62), неравенство Чебышева позволяет получить оценку ’’снизу” для вероятности безотказной работы.
Приведем теперь результаты, полученные при исследовании работы тележек конвейера машины для обжига окатышей —сырья для домен ного производства1. Анализ, проведенный на ряде горно-обогатитель ных комбинатов, показал, что часть тележек постепенно становится не работоспособной вследствие накопленной деформации и возникнове ния трещин, требует ремонта или замены. Сроки службы различных те лежек могут отличаться в 1,5—2 раза. Экспериментально, путем термометрирования в условиях эксплуатации, были исследованы температур ные поля, изменяющиеся по ходу конвейера. Процесс обжига предусмат ривает прогрев газовым потоком с последующим охлаждением продув кой воздуха; на изменяющееся во времени температурное поле тележки оказывают влияние температура и давление теплоносителя, скорость дви жения конвейера, высота слоя окатышей и другие технологические па раметры, которые могут колебаться от цикла к циклу.
Исследование выполнено инженером А.В?Худяковым под руководством до цента И,М, Платова-
По данным измерений в ряде точек тележки в фиксированные моменты времени цикла были определены математические ожидания и дисперсии температуры, Анализ множества реализаций позволил обосновать допу щение о приблизительном подобии температурных полей в соответствен ные моменты времени и установить, что рассматриваемое множество характеризуется законом распределения, близким к нормальному.
Следующий этап состоял в определении термоупругих напряжений в раме тележки. Последняя представляет довольно сложную, многократ но статически неопределимую конструкцию, Для ее расчета первоначально был использован МКЭ, однако анализ результатов показал, что напря жения, связанные с несовместностью тепловых деформаций в сечениях стержней (в связи с нелинейным законом их изменения), являются пре валирующими сравнительно с напряжениями, за счет которых компенси руется различие тепловых деформаций стержней, образующих раму. Пре небрежение последними позволило существенно упростить последующие расчеты без заметной ошибки. Таким путем, с использованием соответ ствующих уравнений были получены математические ожидания и диспер сии для термоупругих напряжений в точках рамы в фиксированные мо менты времени. Аналогичные характеристики были определены по данным опытов для пределов текучести при однократном и при циклическом нагружениях при ряде значений температуры в диапазоне ее изменения; при этом учитывались разбросы характеристик технологического проис хождения, а также связанные со случайными изменениями температуры.
Затем с точностью до множителей был задан механизм накопления деформаций Аер. Последующий анализ показал, что наилучшей верхней оценке (согласно кинематической теореме) отвечает изгиб продольных стержней рамы выпуклостью вниз с одновременным уменьшением их длины: это полностью соответствует характеру нарастающей деформа ции, наблюдаемой при эксплуатации. Задание механизма позволяет оп ределить математические ожидания и дисперсии, доставляющие мини мум в фиксированные моменты времени выражениям, аналогичным пред ставленным в квадратных скобках (7.55). После интегрирования послед нее (для математических ожиданий и дисперсий) может быть представ лено в форме (7.56). Вероятность безопасной работы по критерию на чала прогрессирующего формоизменения определяется из (7.61).
Вероятность безотказной работы по критерию возникновения знако переменной деформации может быть найдена аналогично на основании соотношения (7.59), при этом не приходится выполнять интегрирование по объему.
При втором подходе задача сводится к статистической обработке ре зультатов расчета для отдельных реализаций (исходными данными каж дой реализации являются температурные поля в раме тележки в течение одного цикла). Использование соотношения (7.62), вытекающего из неравенства Чебышева, позволило получить зависимости между вариацией коэффициента запаса и вероятностью безотказной работы при различ ных значениях среднего коэффициента запаса; такая зависимость, по строенная согласно критерию знакопеременного течения, дана на рис. 746.
На рис. 7.47 дана зависимость между вероятностью безотказной ра боты и средним коэффициентом запаса при коэффициентах вариации
0,2 0,0 0,ff 0,0
Рис. 7.46
Рис. 7.46. Вероятность безотказной работы тележки по критерию начала знакоперемен ного течения
Рис. 7.47. Зависимость вероятности безотказ ной работы от среднего запаса прочности (по критериям формоизменения и знакопере менного течения)
1 —Йф, 2 —Йзп
Рис. 7,48. Вероятность безотказной работы в зависимости от значения предела текучести
Рис. 7.48
Уп = 0,37 (при определении Лф) и Vn = 0,3 (для Язп). Влияние предела текучести на вероятность безотказной работы иллюстрируется рис. 7.48.
Расчеты, основывающиеся на предположении о нормальных законах распределения входящих величин, дали для регламентированного режима работы исследуемого обжигового конвейера горно-обогатительного ком бината значения вероятности безотказной работы соответственно двум использовавшимся критериям, близкие к 0,99 (это верхняя оценка). При использовании неравенства Чебышева по критерию начала формо изменения получено Яф = 0,9, по критерию знакопеременного течения Яф ^ 0,85 (оценка ’’снизу”). Вместе с тем расчеты показали, что нару шение регламентированных правил эксплуатации (например, остановки конвейера или снижение его скорости без соответственного изменения параметров теплоносителя), как и использование сталей с пониженными механическими характеристиками (например, тележки, изготовленные из стали 11ХМФБЛ), приводят к существенному повышению вероятности отказов по обоим критериям.
7.5,2, Структурная модель и расчеты кинетики деформирования конструкций
От простой однородной идеально пластической среды реальный мате риал отличается в первую очередь неоднородностью, которая схематично может быть разделена на три уровня: разброс свойств от детали к дета ли; в пределах одной детали —от одного макрообъема к другому (под макрообъемом для определенности понимается типичный объем одного конечного элемента при конечноэлементной дискретизации детали); и, наконец, в пределах микрообъема — от одной его микросоставляющей к другой (микронеоднородность),
Роль неоднородности каждого уровня специфична: первый отражает разброс свойств металла от плавки к плавке, последний — особенность структуры поликристаллического материала. Отличие реологических свойств в микрообъемах (зерна, блоки, дефекты и т.д.) приводит к неодновременному вовлечению в пластическое течение различных со ставляющих, образованию вследствие этого микронапряжений, кото рые, по-видимому, и определяют механизм ’’памяти” материала о пред
ыстории деформирования, оказывая влияние на последующую ползу честь. Использование для отражения реальной микронеоднородности ма териалов структурных моделей среды [55, 56] оказалось существенно ближе к инженерному воплощению, чем статистических моделей (ко торые для условий циклического неупругого деформирования еще не разработаны) и многих феноменологических теорий.
Структурные модели строятся на простом предположении, что фи зическая микронеоднородность принципиально не отличается от неод нородности конструкционной, т.е, элементарный объем деформируемо го тела ведет себя подобно некоторой гипотетической статически неоп ределимой неупругой конструкции. Элементы этой ’’конструкции” (под элементы структурной модели) удобнее всего полагать соединенными параллельно, когда деформация каждого из них (подэлементов) равна деформации всего моделируемого элемента объема.
Для задания реологических свойств может быть использована любая из уже разработанных теорий пластичности и (или) ползучести. Оказалось, что для моделирования пластичности и ползучести материалов, находя щихся в циклически стабильном состоянии, достаточно 'считать подэлемен ты идеально вязкими, т,е. обладающими свойством установившейся пол зучести со скоростью, однозначно зависящей от напряжения подэлемен та и температуры; функция, определяющая эту зависимость, названа реологической функцией подэлемента.
Можно предположить, что реологические функции различных подэле ментов подобны между собой и, следовательно, подобны некоторой об щей для всего элемента реологической функции, Экспериментальные проверки подтверждают практическую допустимость такого предполо
жения |
[55, 56]. Тогда реологические свойства элемента определяются |
общей |
реологической функцией Ф и значениями коэффициентов |
подобия z подэлементов. При таком определении модели нетрудно отра зить неоднородность любого уровня, задавая разброс значений г (детер минированный или случайный) между подэлементами одного элемен
тарного объема либо между объемами одной детали, а также между дета лями.
Для конструкционных металлических сплавов именно последняя неод нородность играет существенно более заметную роль, чем макронеод нородность детали, Если последнюю полагать несущественной, то для от ражения разброса характеристик между плавками удобно принять, что
z = za, |
(7.63) |
где распределение у = y ( z ) во всех плавках одинаковое, а коэффициент а одинаков во всех подэлементах одной плавки, но случайным образом меняется от плавки к плавке, при этом математическое ожидание а = 1, Реологическую функцию Ф удобно считать детерминированной. Тогда в рассматриваемом вероятностном варианте структурной модели эта
функция определяется путем усреднения зависимостей скорости устано вившейся ползучести от напряжения, полученных на образцах из раз ных плавок. Усреднение ведется в предположении осевого подобия соот ветствующих кривых относительно оси скоростей ползучести. Распре деление коэффициентов осевого подобия зависимостей скорости уста новившейся ползучести, полученных для различных плавок, по отноше нию к реологической функции Ф определяет закон распределения слу чайных множителей а, Что касается детерминированного распределения параметров z, то оно определяется обычным путем по кривой цикличе ского деформирования с постоянной скоростью [55, 56].
Таким образом, решение задачи идентификации вероятностной мо дели с конкретным материалом не связано с какими-либо принципиаль ными трудностями,
Для определения z могут быть также использованы циклические кри вые стабилизированного материала, связывающие амплитуды напряже ний оа и деформаций еа , В табл, 7.10 для десяти конструкционных ма териалов при ряде температур приведены параметры К (ГПа), т , п цикли
ческих кривых в координатах |
оа, вра |
|
° а |
К е т |
(7.64) |
(вра — амплитуда пластической деформации) и кривых циклического деформирования при стабилизированном состоянии материала,
О* = 2оа (ер*1{2ера))п |
(7.65) |
(а*э ер* — изменение напряжения и пластической деформации, отсчиты ваемое от момента реверса деформирования); эти данные могут быть использованы при определении параметров z [56].
Если ограничиться аппроксимацией (7.64), полученная модель адек ватно отражает размахи неупругой деформации, однако лучшее прибли жение к диаграмме деформирования можно получить при совместном использовании выражений (7,64) и (7.65), правда, в ограниченном диапа зоне амплитуд,
При отсутствии опытной диаграммы деформирования моделируемого материала можно использовать для той же цели справочные данные по пределам прочности оъ и текучести o0t2 • При представлении кривых рас-
Материал
1
Сталь
20Х23Н18
(ЭИ417)
ХН51ВМТЮКФР
(ЭП220)
Х16Н11МЗ
ХН70ВМЮТ
(ЭИ765)
12Х18Н9
ХН80ТБЮ
(ЭИ607)
ХН60ВТ
(ЭИ868)
*3 о п
2
20
100
200
300
400
500
20
400
600
700
800
20
400
600
700
800
900
20
200
400
600
700
20
500
600
700
20
100
200
300
400
500
600
700
20
600
700
20
500
600
700
800
Х Ю “ 3, |
т |
п |
МПа |
|
|
3 |
4 |
5 |
1,2 |
0,23 |
0,12 |
1,0 |
0,24 |
0,12 |
0,8 |
0,13 |
0,10 |
1,3 |
0,18 |
0,09 |
1,3 |
0,22 |
0,09 |
0,8 |
0,20 |
0,09 |
2,1 |
0,31 |
0,13 |
2,6 |
0,38 |
0,16 |
1,5 |
0,28 |
0Д1 |
1,1 |
0,27 |
0,11 |
0,4 |
0,15 |
0,07 |
2,6 |
0,16 |
0,16 |
2,1 |
0,13 |
0,13 |
2,3 |
0,15 |
0,15 |
2,0 |
0,1.2 |
0,12 |
2,2 |
0,18 |
0,18 |
1,3 |
0,18 |
0,18 |
1,95 |
0,30 |
0,11 |
2,0 |
0,35 |
0,11 |
2,5 |
0,37 |
0,11 |
1,7 |
0,32 |
0,10 |
1,0 |
0,30 |
0,08 |
3,2 |
0,24 |
0,13 |
2,2 |
0,20 |
0,10 |
1,8 |
0,18 |
0,09 |
1,6 |
0,16 |
0,10 |
4,0 |
0,42 |
0,15 |
2,8 |
0,40 |
0,13 |
3,0 |
0,42 |
0,13 |
2,4 |
0,40 |
0,14 |
2,8 |
0,42 |
0,13 |
1,9 |
0,35 |
0,12 |
1,8 |
0,34 |
0,10 |
0,8 |
0,25 |
0,07 |
2,5 |
0,22 |
0,10 |
2,0 |
0,20 |
0,11 |
1,5 |
0,12 |
0,12 |
2,2 |
0,20 |
0,14 |
2,6 |
0,27 |
0,08 |
3,6 |
0,32 |
0,07 |
1,8 |
0,22 |
0,08 |
1,0 |
0,17 |
0,08 |
1 |
2 |
3 |
4 |
5 |
ХН73МБТЮ |
20 |
3,0 |
0,19 |
0 ,1 0 |
(ЭИ698) |
300 |
2,7 |
0 ,2 0 |
0,08 |
|
500 |
3,6 |
0,26 |
0 ,1 0 |
|
600 |
2 ,8 |
0,23 |
0,08 |
|
700 |
2 ,0 |
0,16 |
0,08 |
ХН60МЮВТ |
2 0 |
2 ,0 |
0,13 |
0,13 |
(ЭП539) |
500 |
2,3 |
0,17 |
0,17 |
|
600 |
1,6 |
0 ,1 0 |
0 ,1 0 |
|
700 |
2 ,0 |
0,15 |
0,15 |
Т а б л и ц а 7.11
Связь циклической кривой с диаграммой растяжения при исходном состоянии материала; а - К 0 е Ро° — уравнение, аппроксимирующее исходную диаграмму
растяжения; оа
___________
Материал
— К в т
ра
и о
—циклическая кривая
____ ______ п__________ ______ _______ ______
m jm 0 |
к / к 0 Материал |
,4 по |
т /т 0 |
К/К о |
12Х18Н9 |
2 0 |
1,8 |
4,0 |
20Х23Н18 |
20 |
1,6 |
2 ,0 |
|
2 0 0 |
1,8 |
4,0 |
(ЭИ417) |
400 |
1,7 |
3,0 |
|
300 |
1,5 |
3,0 |
|
600 |
1,4 |
2 ,0 |
|
400 |
1,5 |
4,0 |
|
700 |
1,8 |
2 ,0 |
|
500 |
1,3 |
3,0 |
|
800 |
2 ,0 |
2 ,0 |
|
600 |
1,2 |
3,0 |
|
|
|
|
|
700 |
1,2 |
2 ,0 |
|
|
|
|
Сталь 20 |
2 0 |
1,2 |
1,6 |
ХН60ВТ |
20 |
1 ,0 |
2 ,0 |
|
1 0 0 |
1,3 |
1,7 |
(ЭИ8 6 8 ) |
800 |
1,5 |
4,0 |
|
2 0 0 |
0,7 |
1,7 |
|
|
|
|
|
300 |
0 ,8 |
1,8 |
|
|
|
|
|
400 |
1,0 |
2 ,0 |
|
|
|
|
|
500 |
1,3 |
2,4 |
|
|
|
|
ХН70ВМЮТ |
2 0 |
1,6 |
2 ,0 |
ХН73МБТЮ |
2 0 |
1,2 |
1,4 |
(ЭИ765) |
500 |
1,4 |
1,6 |
(ЭИ698) |
500 |
2 ,0 |
2 ,0 |
|
600 |
1,3 |
1,4 |
|
600 |
1,8 |
2 ,0 |
|
700 |
1,2 |
1,4 |
|
700 |
1,6 |
1;5 |
тяжения в виде, аналогичном (7,64) и (7.65), |
|
|||
а = К0е? • . |
|
|
|
(7.66) |
После некоторых преобразований могут быть получены |
соотношения: |
|||
т0 = (а + \п(рь /а0)2У)/Ь, К0 = ао,2/(0,002)т о , |
(7-67) |
|||
где а = 0,05, |
ft = 3,2 |
при |
аь /а0,2 <1,25; |
(7.68) |
д = 0,17, |
Ъ - 4,6 |
при |
ob/o0i2 > 1,25. |
|
15. Зак. 1830.
Т а б л и ц а |
7.12 |
|
|
|
|
Разбросы механических характеристик конструкционных материалов |
|
||||
Материал |
а о,*/°сп |
D lot ,t ]/D \ob ] |
Коэффициент вариации, % |
||
|
|
|
|
|
|
|
|
|
°Ъ |
а о,а |
6 |
Сталь 10СП |
0,70 |
1 ,2 0 |
1 |
12 |
10 |
Сталь 2Осп |
0,64 |
0,85 |
9 |
И |
12 |
30ХГСА |
0,70 |
1 ,2 0 |
8 |
1 0 |
20 |
1Х21Н5 |
0,70 |
1,30 |
5 |
8 |
13 |
12X2 НВФА |
0,78 |
1,40 |
11 |
2 0 |
2 0 |
15Х5МА |
0,80 |
1,30 |
И |
2 0 |
16 |
Х18Н10Т |
0,60 |
1,50 |
4 |
11 |
8 |
23ХН2ВФА |
0,65 |
1,40 |
6 |
10 |
8 |
1Х21Н5 |
0,80 |
1,40 |
5 |
10 |
13 |
Сг. 3 |
0,76 |
1 ДЗ |
7,6 |
11 |
13 |
Д16Т |
0,7 |
1 ,1 0 |
2,4 |
4 |
9 |
Д1АМТ |
0 £ |
1 ,0 |
4 |
7 |
8 |
С р е д н е е |
0,70 |
1,28 |
8 |
10 |
12 |
Характеристики X, т диаграмм в циклически стабильном состоянии отличаются от начальных (7.66); в первом приближении соответствую щая корректировка может быть произведена с использованием инфор мации, приведенной в табл. 7.11. Конечно, при использовании справоч ных данных для оъ и o0 t 2 достоверность модели уменьшается.
Реологическая функция также может быть приближенно определена по табличным данным —значениям пределов длительной прочности в за висимости от времени разрушения, Для этого используется известная формула Хоффа
TfGpmin ” const, |
(7.69) |
где Tf — время до разрушения; |
ерт{П — скорость ползучести во второй |
фазе, зависимостью которой от напряжения и температуры и определяет ся реологическая функция материала Ф. Например, для степенной рео логической функции
^pmin = А ( Т ) о п |
(7.70) |
величину п находят из выражения |
|
п = lg(r2 / Т!)/lg (<7t /а2). |
(7.71) |
здесь ог —предел прочности при длительности Т\ , аналогично 02 —при т2 • В частности, при длительностях 100 и 1000 ч
п = [lg(ffi<>o/aiooo)] |
(7.72) |
Множитель А (Т) может быть найден по условному пределу ползучести (напряжение а0, при котором за заданное время т0 изменение деформа ции, найденное в предположении установившейся ползучести из выраже-
ния (7.70), оказывается равным заданному допуску Авро) :
А (Т )= Аер01(т0о2). |
(7.73) |
Имея параметры детерминированной модели, остается задать закон распределения а (7.63). Математическое ожидание этой величины должно быть равно единице (детерминированная модель отвечает средним свой ствам); закон распределения следует принять таким же, какой обнару живается, например, для условного предела текучести о012.Для а0>г обыч но принимают нормальный закон; коэффициент вариации Оо(2 для мно гих сплавов оказьюается практически одинаковым, он составляет в сред нем 10% (табл. 7.12).
Рис. 7А9. Изменение вероятности |
|
|
|
безотказной работы тележки по числу |
|
|
|
циклов (по критерию возникновения |
|
|
|
трещины) |
|
|
|
2. |
¥ 0 |
0 / |
0 |
/ У / # *, |
ц и к л |
|
|
Принятая относительно простая вероятностная |
модель |
материала |
позволяет получить и достаточно простую модель конструкции с един ственным, общим для всей детали случайным параметром а (напомним, что разбросы деформационных характеристик в пределах одной детали полагаются несущественными). Расчет кинетики неупругого деформиро вания такой детали, как следует из простых соображений подобия, ана логичен расчету той же детали при детерминированных значениях меха нических характеристик, но случайном нагружении.
В качестве примера рассмотрим расчет рамы тележки обжиговой ма шины с целью определения ее надежности по критерию образования тре щины малоцикловой усталости1. Условия работы тележки были указаны в п. 7.5.1, где приведены результаты ее расчета на приспособляемость, однако здесь используются данные по температурным полям, экспери ментально полученным на другом горно-обогатительном комбинате. Па раметры структурной модели взяты для стали 15ХМЛ, из которой из готовлены тележки, по справочным данным было найдено распределе ние параметров z; ползучесть в расчете не учитывалась, поскольку в дан ных условиях ее влияние незначительно.
Для экспериментально найденных температурных полей с помощью ЭВМ были определены размахи деформаций в точках сечений рамы при различных реализациях (циклах конвейера), вычислены их среднее зна чение и дисперсия. По этим данным и по экспериментально найденному пороговому значению N0 с использованием формулы Коффина (с ее кор-
1Пример расчета был выполнен инженером А.В. Худяковым
ректировкой для неизотермического нагружения) определено измене ние вероятности безотказной работы по числу циклов на основе крите рия возникновения трещины малоцикловой усталости (рис. 7.49, кр. 1). Использовался логнормальный закон распределения. Полученные ре зультаты расчета сопоставляются с опытными данными. При построении кривой 2 фиксировались трещины, -достигающие длины 100 мм, для кривой 3 — 200 мм. По-видимому, разбросы воздействий в данном слу чае оказывают более существенное влияние, чем разбросы реологиче ских свойств материала тележек.
7.5:3. Принцип подобия реологических свойств и модель накопления повреждения
При циклическом нагружении конструкций весьма типична ситуация, когда в точке конструкции на некоторое постоянное во времени напря женное состояние накладывается циклически изменяющееся, причем изменение происходит пропорционально некоторому параметру (или близко к этому закону). Постоянное напряженное состояние может быть другого вида, чем переменное, поэтому данное нагружение в об щем случае нельзя назвать пропорциональным. Назовем его циклически пропорциональным. Деформацию в точке в данном случае также сле дует разделить на две части: ”постоянную” (она может постепенно, от цикла к циклу накапливаться) и изменяющуюся в цикле. Если материал изотропен, девиаторы последней и переменного напряжения пропорцио нальны. Анализ на основе структурной модели показывает, что перемен ная (циклическая) составляющая деформации связана только с цикли ческой составляющей напряжения, тогда как ’’статическая” —с обеими — циклической и статической.
Это позволяет ’’циклические” свойства материала (и, как следствие, конструкции) исследовать отдельно, независимо от статической состав ляющей. Для случая циклически пропорционального нагружения приме нительно к циклической составляющей неупругой деформации на основе уравнений структурной модели было получено уравнение состояния, позволяющее исключить необходимость расчета по подэлементам. Урав нение состояния связало между собой макроскопические параметры а,
еэлементарного объема [55,56].
Всоответствии с рассмотренным в данном параграфе вероятностным вариантом структурной модели аналогичный вариант уравнения состоя ния представляется уравнением, которое отличается от детерминирован ного только введением случайного параметра а:
ёр = Ф ( 9 М 7 ) ( 1 - « ( 0 ) . |
(7.74) |
Напомним [55] особенности входящих в уравнение параметров. Вся предыстория нагружения делится на этапы, ограниченные последователь ными ”поворотными” моментами. Информация об этих моментах со храняется в ’’памяти” материала. Параметры в , с уравнения состояния (7.74) определяются текущими значениями упругой деформации ее = = о/Е (Е — модуль упругости) и полной деформации е , а также значе
ниями параметров ее, е, 0, С в последний поворотный момент: eeVi eVi 6V9 cv. На первом этапе нагружения эти четыре параметра равны нулю.
Вводятся вспомогательные переменные
& е * ~~ ^ e v t ~ ( 7 .7 5 )
и некоторая функция у = /(* ), центрально подобная (с произвольным коэффициентом к) диаграмме деформирования моделируемого материала:
о = Ек/(е/к). |
(7.76) |
Параметр 0 определяется выражением |
|
0 = 0, +0* |
(7.77) |
после вычисления 0* по известным ееФ, е, из параметрического уравнения
ее* = 0 J ( e m/9J . |
(7.78) |
Проще всего этот параметр находить графически, откладывая на графике
У ~ / 0 0 |
точку у = ее0, х = е фи определяя по лучу из начала координат, |
насколько она отстоит от кривой /. |
|
Второй параметр находится из отношения |
|
С — |
. |
Функция К (С), входящая в выражение (7.74), представляет зависимость касательного модуля на диаграмме / от секущего модуля
K(f(x)/x) = /'(*).
Функция Ф — реологическая, ее определение было дано в п. 7.3.2; прак тически она может быть найдена путем совместного использования диаг раммы деформирования и кривой ползучести [56]. Поворотными мо ментами являются все моменты реверса деформации, а также моменты реверса (под реверсом понимается изменение знака скорости соответ ствующей величины) параметра С.
И последнее: при достижении текущим параметром С значения Cv из ”памяти” исключается информация о предыдущем (если 0м/0 < 1) или в противном случае двух предыдущих поворотных моментах (0Мзна чение параметра 0 в предпоследний поворотный момент).
Уравнение состояния (7.74) отражает целый комплекс свойств подо бия в деформационном поведении материала, относящихся как к дефор мированию с заданной скоростью, так и к ползучести. Поэтому оно было названо принципом подобия [56].
Модели металла разных плавок отличаются (вследствие наличия в уравнении состояния (7.74) случайного параметра а) характеристиками сопротивления деформированию: их диаграммы деформирования цент рально подобны с коэффициентом подобия у , равным отношению значе ний реализаций а для этих плавок. Кривые ползучести при напряжениях, отличающихся в у раз, подобны с коэффициентом подобия (относитель но оси времени) 7.
Довольно хорошее соответствие с данными экспериментов, прове денных на различных сталях и сплавах при разнообразных программах циклического нагружения, показало, что параметры состояния 0 и С, вхо-
Прогнозирование параметров модели рассеянного разрушения жаропрочных ма териалов (среднее значение по результатам испытаний 5 —12 образцов)
Материал
12X18Н9 ХН60ВТ (ЭИ8 6 8 )
ХН70ВМТЮФ
(ЭИ826)
20Х23Н18
(ЭИ417)
ХН60МЮВТ
(ЭП539)
Х16Н11МЗ
ХН35ВТ
(ЭИ612)
37Х12Н8Г8МФБ
(ЭИ481)
ХН51ВМТКЖФР
(ЭП220)
С р е д н е е
М |
о О |
700
700
700
700
700
700
650
700
850
° р |
° с |
-D-c |
ePf |
5,5 |
70 |
35 |
0,73 |
14 |
38 |
31 |
0,43 |
71 |
2 0 0 |
1 2 0 |
0,16 |
6,4 |
35 |
21 |
0,45 |
50 |
98 |
58 |
0,16 |
8 |
77 |
52 |
0,62 |
12 |
72 |
16 |
0,42 |
13 |
6 8 |
64 |
0,45 |
50 |
204 |
154 |
0,16 |
дящие в уравнение состояния (7.74) и вытекающие из разработанного варианта структурной модели, являются наиболее подходящими для описания реологических свойств в данных условиях. Связь между про цессами деформирования и разрушения при малоцикловом нагружении послужила основанием для предположения о том, что данные параметры позволят с приемлемым соответствием отразить накопление усталост ного повреждения. В дальнейшем оказалось, что более удобно вместо параметра С использовать близкий к нему по смыслу параметр ^ ^ о т ражающий изменение неупругой деформации с момента последнего ре верса.
Наличие на реологической функции материала двух участков, отвеча ющих различным механизмам ползучести (один из которых близок к склерономному — механизму пластичности), подтвердило вытекающее из опытов предположение о возможности повреждения двух типов (со =
~ СО! + СО2 )*
Уравнения предложенной кинетической модели рассеянного повреж-
дения имеют вид |
|
|
|
|
|
|
со* |
= WH(со/), |
|
|
|
|
(7.79) |
W = D (6 ,T )\e p. \а^ \ ё |
р 1, |
(7.80) |
||||
т/ |
(о?! + со2 )d,T |
= |
1. |
|
|
(7.81) |
Г |
|
|
||||
> |
|
|
|
|
|
|
Здесь |
- 1 при |
I в I |
< |
во (Т) и о>! > 0, в противном случае # ( сох) = |
||
= 0; Н( со2) = 1 при |
I в I > |
во (Т) и со2 > 0, иначе # ( со2) =0; |
в0 — харак- |
230
ecf |
тп |
пг |
|
°с |
D’c |
|
iepf)m |
(ecf)m |
™ /(«р/)т |
||||
|
|
OS |
||||
|
|
|
|
|
||
0,17 |
2,8 |
32 |
1,96 |
2,2 |
0,5 |
|
0,18 |
7 |
29 |
1,98 |
1,3 |
0,8 |
|
0,10 |
36 |
78 |
1,97 |
2,5 |
0,6 |
|
0,23 |
7 |
17 |
1,60 |
2,1 |
0,6 |
|
0,15 |
36 |
40 |
1,40 |
2,4 |
0,6 |
|
0 Д 6 |
4 |
36 |
2,00 |
2,1 |
0,7 |
|
0Л 5 |
7 |
36 |
1,40 |
2,0 |
0,2 |
|
0,15 |
6 |
36 |
2,00 |
1,8 |
0,9 |
|
0,13 |
36 |
108 |
1,40 |
1,9 |
0,8 |
|
|
|
|
1,74 |
2,0 |
0,6 |
терное значение этого параметра, разделяющее два отмеченных физи чески отличающихся механизма неупругого деформирования. Определя ющие функции модели а(Т) и D(6, Т) могут быть найдены по данным изотермических испытаний материала на малоцикловую усталость при ряде значений температур; при этом удобны испытания с различающи мися скоростями деформирования в полуциклах.
Опыт показал, что вполне удовлетворительные результаты можно по лучить и при кусочно-постоянной аппроксимации D(0, Т) значениями
Д (0, Т) = J[ Щ (?) при 0 > 0о *D+C(T) |
в диапазоне 0 < 0 < 0О, |
(7.82) |
I Dc(T) в диапазоне 0О< 0 |
< 0, Dp(T) при 0< —0О* |
|
Интегрирование за цикл при этом упрощается. В частности, для изо термического испытания с выдержкой в двух полуциклах получим
1 |
Ае™ |
к?) +1Х к” +ДГ(1 - к - ) ] , |
(7.83) |
||
Дсо = — = — ~ [ D U ? + £>+(1 - |
|||||
N |
m |
|
|
|
|
где m = а + |
1; к+ = е+,/Дер, к"= I е~, 1/Дер; е |
е ~ , |
- значеше |
I ер, I |
|
в момент перехода от 10 1 > 0О к |
I 0 I < 0О; |
- |
размах неупругой |
деформации.
Анализ модели накопления повреждений и сопоставление с экспери ментальными данными показали, что, несмотря на относительную про стоту, она неплохо отражает известные закономерности малоциклового разрушения. При быстром нагружении без выдержек из уравнении мо дели следует формула Коффина—Мэнсона; модель подтверждает также
известный метод стока, и поэтому ее можно использовать и дня оценки долговечности в условиях двухчастотного нагружения.
Случайное изменение сопротивления малоцикловому разрушению мо жет быть отражено в модели введением множителя в формулу (7.80)
В(в, Т) = ф ( в , Г).
Л |
_ |
Здесь D — среднее значение функции; (3 — случайный множитель, стати стические характеристики которого могут быть определены по данным испытаний.
При отсутствии данных испытаний при малоцикловом нагружении в условиях ползучести параметры модели разрушения при Т = const при ближенно могут быть определены по известным разрушающим дефор мациям при статическом разрушении (ер/) и деформациям ползучести (<ecf ) в испытаниях на длительную прочность (имеются в виду логариф мические деформации):
m
D P = 1,74 ТГ - ^ |
’ |
(7-84) |
|
(epf) |
|
|
|
D* = 2,0 |
m |
> |
|
m |
|
||
ы |
) |
|
|
D-= -0,6 ££,
Здесь m = 1/a ~ 1,67, где a — параметр уравнения Мэнсона—Коффина (на клон кривой малоцикловой усталости).
Значение epf обычно определяют по значению относительного суже ния при разрыве ф:
epf = |
|
1 |
111-------- |
||
PJ |
1 |
- ф |
Аналогично можно определить
1
е с/ = 1л
1 - Ф (т) ’
где ф (т) — сужение при разрыве в испытаниях на длительную прочность. Значение ecf существенно зависит от времени и при вязком разруше нии, согласно данным А.В. Станюковича, связано с наклоном кривой
длительной прочности п
ec f =Do°’3n, |
(7.85) |
где D — константа материала, значение которой можно найти из усло |
|
вия ecf = п~1 при о = оь, которое следует из модели вязкого |
разруше |
ния Ю.Н. Работнова при кратковременной ползучести. |
|
Значение п определяем по двум значениям пределов длительной проч
ности |
aTj и аТа на участке вязкого разрушения. Если Тх < т2, имеем |
п |
ln(r2/ri) |
т2 < 104 ч. |
|
|
In (oTJ o Ti) |
В табл. 7.13 приведены значения epf и ecf , полученные для ряда ма териалов.
Величина ecf определена при напряжении о - о02 с использованием выражения, следующего из (7.85):
Как видно из данных таблицы, коэффициенты корреляции ряда ме ханических характеристик для различных материалов мало отличаются друг от друга.
7.5.4. Расчетдолговечности по критерию образования трещин в зоне концентрации напряжений
Анализ поведения конструкций из материала, описываемого струк турной моделью, показал, что свойства памяти о характерных момен тах предыстории (и, что не менее важно, свойства забывания этих мо ментов в определенных ситуациях) являются довольно общими и при сущими не только элементарному объему материала, но и конструкции в целом при циклически пропорциональном нагружении. Подобие за кономерностей деформирования после каждого поворотного момента, которое также вытекает из уравнения состояния (7.74), для конструк ции выполняется уже не так строго, как для структурной модели ма териала (т.е. не для всех конструкций и видов нагружения), но в боль шом числе случаев вполне адекватно отражает реальное поведение кон струкций.
Особенностью использования принципа подобия для конструкции в целом является необходимость предварительного определения ее ’’диа граммы деформирования” / — связи между параметром внешнего воз действия и искомым кинематическим или силовым параметром (напри мер, интенсивностью деформации в опасной точке) при однократном нагружении с постоянной базовой скоростью нагружения. Если такая диаграмма найдена (из расчета либо эксперимента), то далее при про извольной программе циклического воздействия на основе соответст венно записанного уравнения состояния (см., например, [62]) находим закон изменения искомого параметра в цикле. В это уравнение, как и в уравнение (7.47), входат реологическая функция материала конструкции.
При расчете неупругого деформирования в зоне концентрации напря жений для получения кривой / может использоваться формула Нейбера либо другая, связывающая состояния в опасной точке упругой и реаль ной неупругой конструкции при одной и той же нагрузке. В этом случае в качестве параметра внешнего воздействия выступает величина е*е — деформация в опасной точке идеально упругой конструкции.
|
Построим диаграмму е% = f* (е) (где е — деформация в опасной точ |
||
ке |
неупругой конструкции), мы далее обращаемся к уравнениям прин |
||
ципа подобия, в которых ее заменяем на е е,* а функцию / —на /* |
|||
|
При заданной |
истории нагружения (заметим, |
что в е* могут входить |
и |
деформации, |
соответствующие термоупругим |
напряжениям) уравне- |
ние принципа подобия при известных функциях / * и Ф позволяет рассчи тать историю изменения деформации е в соответствующей неупругой конструкции.
Рассмотрим в качестве примера следующую ситуацию: диск ГТД из сплава 20Х23Н18 работает при циклических сменах частоты вращения и температуры. Расчет в предположении идеальной упругости определил размахи напряжений в зоне отверстий в полотне даска; концентрация напряжений в расчете не учитывалась. Температура приблизительно по стоянная — 700 °С. Теоретический коэффициент концентрации известен; это позволяет найти размах напряжений в опасной точке зоны концент рации напряжений в идеально упругом диске; зная модуль упругости, нашли размах упругой деформации Ае* = 0,52%.
С использованием данных табл. 7.10 построили кривую деформиро вания о ~ е (рис. 750, кр. 1). После деления на модуль упругости по лучили кривую ее ~ е (на рис. 7.50 это та же кривая в новом масштабе
по оси ординат). С помощью формулы Нейбера о* el |
= ое (индекс |
|||
отвечает идеально |
упругой детали), преобразованной |
к |
виду |
{el)2 = |
= еее, построена |
зависимость е*е = f* {e ) (см. рис. 7.50, |
кр. |
2); далее |
можно использовать уравнение состояния принципа подобия.
При циклическом изотермическом нагружении без выдержек из него
следует |
|
|
ееа = Г (еа), |
(7.86) |
|
где еа, |
e l a — амплитуды деформации в |
неупругой и упругой деталях. |
Таким образом, зная е*еа = 052/2 = 0,26%, с помощью функции /* (см.
рис. 7.50) |
находим еа |
- 0,43%. Тут же, по кривой / |
находим ера = 0,30%. |
|
Напомним, что найдено |
(приближенно) лишь математическое ожида |
|||
ние еpQ. |
|
|
|
|
Чтобы |
определить |
ее |
дисперсию, удобно найти |
вначале зависимость |
ер = <р(е1), реализующую тот путь, по которому уже найдена ера (см. рис. 7.50, кр. 3). Аналитическое выражение функции у довольно гро моздко, но графически она строится просто. Учитывая разбросы (слу чайный параметр а) , можно получить
ера = a v ’Oea/'*)- |
|
(7.87) |
Дифференцируя, найдем приближенное выражение дня дисперсии |
|
|
D [ера\ = (<Р(еёа) ~ е'еаЧ>' (e*ea)?D [a]. |
|
(7.88) |
Заметим, что если случайно и воздействие, то |
|
|
D iepa] = У (еёа) - e'eaV{elaj\2D[a\ |
+ (fi'(e*a))2D [e*a] . |
(7.89) |
В нашем случае (£>[<*] = 0,01,£)[е*а] = |
0,<р'(е*еа) = 2) получим D [eva] = |
|
= 4,9 1(Г8 |
|
|
Долговечность найдем из выражения (7.83)
-. Ае m
Н 1 = —т ---- Фр + Dp), |
(7.90) |
где т = 1,67, Dp = 6,4 {D~ в табл. 7.13 принято равным нулю), N - 480.
d,M/7a
МПа
Рис. 7 .50 . К р и вая деф орм и рован и я а-е стали 20Х 23Н 18 (7) и зависимости, получен ны е по ф о р м у л е К оф ф ин а: е^—е (2) и е£-ер (3)
Рис. 7 .51 . П етли пластического гистерезиса в зоне концентрации напряжений 1 — без вы д ер ж ек, 2 —с вы д ер ж кам и
Для коэффициента вариации VN из выражений (7.83) и (7.84) следует
V 2N = m2 V i ep + V p . |
(7.91) |
Приняв Vp = 0,1, что соответствует обычному 100%-ному разбросу дан ных испытаний на малоцикловую усталость, найдем VN = 0,13.
В другом варианте нагружения в конце одного полуцикла происхо дит выдержка в течение 10 ч при практически постоянной нагрузке; размах напряжения в упругой детали сохраняется прежним. В этом случае на участке выдержки уравнение состояния интегрировалось; полученная петля гистерезиса приведена на рис. 7.51 штриховой линией. Расчет дол говечности производился по выражению
-Ает
N - ' --------е - ф |
к ? + я с+ (1 - к?1)). |
т |
|
Найдено: N = 130. |
Коэффициент вариации VN остается прежним (7.91). |
В заключение отметим, что здесь для двух подходов, которые в де терминистической постановке достаточно удобны для практической оценки работоспособности пластических конструкций по критерию ма лоцикловой усталости (идеально пластическое тело, теория приспособ ляемости; микронеоднородное тело, циклически стабильное состояние, структурная модель), рассмотрен возможный первый шаг к уточнению расчетной модели путем учета вероятностного характера отражаемых
процессов. В рамках естественных упрощающих допущений усложнение оказалось не чрезмерным, о чем свидетельствуют приведенные примеры расчетов. По мере накопления соответствующей информации и опыта расчетов модели, несомненно, будут совершенствоваться.
7.6. Статистические факторы в анализе процессов деформирования и оценке ресурса
Оценка остаточного ресурса оборудования химических,энергетических и других установок в процессе их эксплуатации имеет важное значение для обеспечения безопасной и надежной их работы. На стадии проектирования соответствующего оборудования определяется расчетный его ресурс, в ос нову оценок которого положен анализ повреждаемости конструкционных материалов от циклического нагружения, обусловленного проектными нес тационарными режимами работы.
Для оценки остаточного ресурса оборудования необходима полная ин формация об изменении параметров эксплуатационных режимов. Объем этой информации определяется в первую очередь принятой методологией расчета. В настоящее время широкое распространение получили два подхо да к оценке остаточного ресурса. Первый связан с регистрацией реальных режимов, их классификацией и оценкой остаточного ресурса путем сумми рования повреждений от каждого из этих регламентированных режимов. Второй подход основывается на анализе повреждаемости конструкционных материалов в зависимости от реальной истории нагружения. Этот подход представлятся более перспективным, так как он дает возможность достато чно полно учесть особенности влияния эксплуатационных режимов приме нительно к конкретному оборудованию.
Важной проблемой, которая должна быть решена при оценке остаточно го ресурса, является создание методик, адекватно отражающих поведение реального материала.
Среди существующих концепций, положенных в основу описания процес сов упругопластического деформирования, особое место принадлежит мо делям, отражающим структурную неоднородность реальных материалов. Согласно этому подходу, среда, подобно классическим теориям термоуп ругости, рассматривается как однородная в макрообъеме. При этом вся кий бесконечно малый элемент среды моделируется совокупностью связан ных между собой первично-изотропных структурных частиц, свойства которых определяют поведение материала в целом [53, 56, 63,64].
В рамках этого подхода напряжения и пластические деформации в каж дой точке тела могут быть описаны следующими тензорными полями:
Ofj — ^ 0 ( j } + Ojj,
eg = (efj ) + 7у.
Здесь <a//> —среднее вероятное напряжение, Оц — поля микронапряжений. Принимая, что число структурных элементов в элементарном объеме велико, т.е. N -►°°, среднее вероятное напряжение и пластическую дефор-
мадию определяем в соответствии с зависимостями:
оо
<о,/> = ; atf(z)Y0(z)dz,
<*6 >= (z) Ye(z)dz, (?'92)
гдеУ(г) — функция плотности распределения соответствующей случайной величины механических свойств микроструктурных составляющих.
Для описания деформационных свойств моделируемого материала не обходимо получить функции плотности распределения Ya(z) напряжений и 76(z) пластических деформаций по структурным элементам. Зная величи ны напряжений a/y(z) во всей совокупности структурных элементов и функ цию плотности распределения, можно восстановить напряжения в некото ром элементарном объеме и, таким образом, перейти к описанию напряжен но-деформированного состояния конструкций в целом.
Для получения функции плотности распределения Y = Y(z) могут быть использованы результаты испытаний материалов на микротвердость. В дан ном случае были использованы результаты испытаний микротвердости, про веденные на трубчатых образцах из стали Х18Н10Т. Поверхность образцов электрополировалась для снятия наклепанного поверхностного слоя. Изме рения осуществлялись с помощью прибора ПМТ-3 алмазной пирамидой с углом при вершине 136° и нагрузкой на индентор 20-100 гс. Отпечатки на носились по образующей на рабочей базе образца и приблизительно через 0,5 мм, а их диагонали измеряли при 500-кратном увеличении.
На рис. 7.52 представлены кривые плотности вероятности микротвердо сти материала в зависимости от уровня нагрузки на индентор.
Проведенная статистическая обработка результатов измерений Ям и применение этих результатов к статистической модели Н.Н. Афанасьева позволили описать зависимость между значениями микротвердости Яд и значениями параметров отрасчетной структурной модели.
На рис. 7.53, а показана гистограмма распределения микротвердости Ям стали Х18Н10Т. Здесь же приведены графики, связывающие микротвер дость Ям с пределами текучести структурных элементов. На рис. 7.53,6 показана диаграмма деформирования (7) и диаграмма восстановления по структурной модели (2) с использованием результатов испытаний на микротвердость.
В соответствии с моделью Н.Н. Афанасьева средние напряжения в метал
ле определяются зависимостью вида |
||
оо |
оо |
|
/ |
Yb-pdoT+o / Ydo |
|
о |
оо |
|
&€“ |
(7.93) |
/ Ydoj1
о
Первый член в этом уравнении определяет вклад в среднее напряжение структурных частиц, деформирующихся упругопластически. Второй член — вклад частиц, деформирующихся упруго.
Следуя от интегральной совокупности с N 00 к выборке с конечным числом структурных элементов, переходим к известной модели типа моде ли Бесселинга [63].
Рис, 7.52, Кривые плотности вероятности микротвердости материала в зависимости от нагрузки на индентор
$М/7а.
-■ —
^ г
300
/ /
\\
200
т
Ц2 |
4 # S /0 -3 |
Рис. 7.53. Гистограмма распределения микротвердости стали Х18Н10Т |
(а), экспери |
ментальная и расчетная диаграммы деформирования стали (б) |
р |
а. 1 —l g я —0,0024Яд + 6,55; 2 —Нц = —326 lg c ^ + 2560 |
|
Численный алгоритм этой модели предусматривает описание диаграммы деформирования материала совокупностью диаграмм деформирования структурных элементов. Выбор характеристик этих структурных элемен тов может осуществляться на основе экспериментальных данных или чисто формально на основе аппроксимации диаграммы деформирования кусоч но-ломаной линией [65].
Применение структурной модели в численных расчетах позволило каче ственно правильно описать идеальный эффект Баушингера. Использование поцикловых диаграмм деформирования и введение в модель зависимости характеристик структурных элементов от температуры позволило авторам получить картину кинетики деформирования сложных конструкций энерге тического оборудования, работающих при циклическом неизотермическом нагружении [66, 67].
В рамках рассматриваемой модели численно решается краевая задача термоупругопластичности, которая описывается уравнениями вида
(ХГ, ?),/ — рс Т — TfijkCjk + W - 0, |
|
(7.94) |
|||||||
г(* у , |
7) = |
0 (х;, 7), |
x e s T |
t e D t , |
|
(7.95) |
|||
ХГ,/^ |
+^ + а ( Г - Г оо) = 0, |
x e s q u s a, |
(7.96) |
||||||
7X*/, 0 = |
0 (* /, |
p), |
X f G D U S , |
7 = 0, |
(7.97) |
||||
°jk, |
* + ^ у |
= 0, |
D X D t, |
|
|
(7.98) |
|||
°i.f |
nj |
= |
xi ^ |
|
t ^ |
|
|
(7.99) |
|
“j(*k , |
t) = Uj (Xk, |
7), |
Xf e s u, 7 E |
Dt, |
(7.100) |
||||
d tij = |
1IT, (ui,j + utj ) |
= dey + dejj + aefy, |
(7.101) |
||||||
defj = CijjctdOki+dCjjkiOki, |
|
|
(7.102) |
||||||
dejj = a Td7bij + d a T 7b ijy |
|
|
(7.103) |
||||||
defj = |
d \ |
• grad Ф. |
|
|
|
(7.104) |
При этом температурные поля T(xj, 7) определяются из решения краевой задачи теплопроводности (7.94) —(7.97). Определение полей оц и е/у осу ществляется при решении краевой задачи атермической пластичности (7.98) —(7.104), для которой температура Гявляется известным парамет ром. При этом уравнения (7.98) и (7.101) справедливы как для микро объема, представляющего собой конгломерат структурных частиц, так и для макрообъема, в рамках которого материал рассматривается как одно родный.
В качестве примера численной реализации рассматриваемой структур ной модели проведен анализ кинетики напряженно-деформированного сос тояния в вершине кольцевой трещины глубиной а = 20 мм, расположенной на внутренней поверхности цилиндрического сосуда (рис. 7.54). Радиус сосуда R = 1,73 м, толщина стенки h = 200 мм. Цилиндр нагружен осевым усилием </, график изменения которого приведен на рисунке. Анализ кине тики напряженно-деформированного состояния в корпусе сосуда осущест вляется при изотермическом нагружении. Наибольшие напряжения в цилин дре без трещины составляют о = 0,65а^.
Расчетная область цилиндра с трещиной была покрыта конечно-элемент ной сеткой из криволинейных четырехугольных изопараметрических эле ментов.
Г |
£гШМ£гг),М//а |
Рис. 7.54. Расчетная схема для сосуда с трещиной
1—17 —последовательные моменты времени в истории нагружения; q — распре деленная нагрузка, МПа; T l t T2 —уровни температурного нагружения
На рис. 7.55 показано раскрытие трещины в процессе нагружения. В первом цикле нагружения в вершине трещины за счет неполного ее закры тия образуется полость. На том же рисунке показаны области, в которых пластические деформации образуются при приложении сжимающих нагру зок (а, б — последовательное положение берегов трещины при цикличе ском нагружении). На рис. 7.56 приведены графики распределения напря жений Oi I, а22 и ог33 и деформаций б ц и е 22 непосредственно перед фрон том трещины на 3, 6 и 9-м этапах нагружения.
Использование результатов численного анализа кинетики напряженнодеформированного состояния в областях концентрации, полученных с по мощью структурной модели, позволяет определить уровень накопленных повреждений в материале. Оценки получены согласно деформационно кинетическому критерию на основе изучения петель упругопластического гистерезиса.
Рис, 7,55, Раскрытие трещины в процессе нагружения Зона: 1 —пластичности, 2 —обратной пластичности
/7,2 |
/7,3 |
х /а |
Рис. 7.56. Изменение напряжений и деформаций перед вершиной трещины
16. Зак. 1830 |
241 |
Критерий разрушения может быть представлен в виде [69]
Np 8et |
N P Де |
(7.105) |
|
J — i~ d N + |
f |
------ dN= 1, |
|
о e |
о |
e |
|
при жестком нагружении
/“ Г dN= 1,
или, принимая 5 s const,
betNp = const = €2 |
(7.106) |
Здесь 5 —ширина петли гистерезиса в полуцикле растяжения; Ае — накоп ленная за цикл остаточная пластическая деформация; е —предельная дефор мация при однократном статическом разрыве; et —упругопластическая де формация в цикле, et = d f e y ) Np— разрушающее число циклов, еу — уп ругая деформация в цикле.
Следует отметить, что зависимости (7.105) и (7.106) справедливы как для малоцикловой, так и многоцикловой усталости.
В экспериментальных и расчетных работах величины 6 и Де могут легко определяться для случая симметричной петли гистерезиса, т.е. в случае, когда среднее напряжение цикла равно нулю. В общем случае нагружения определение этих величин связано с определенными трудностями. При менение структурной модели позволяет определять эти величины при про извольном изменении внешних нагрузок. Это объясняется тем, что струк турные элементы в рамках рассматриваемой модели при любых условиях нагружения остаются изотропными и среднее напряжение в каждом струк турном элементе всегда равно нулю.
Значения 6 и Де получаются суммированием соответствующих значений 5(к) и 6e(fc) по всей совокупности структурных элементов, т.е.
5 = <5(*)>, Д е = <Де(*)>. |
(7.107) |
На основе структурной модели можно расчетным путем получить дан ные по повреждаемости металла в вершине трещины при ее циклическом нагружении. Для этого могут быть использованы диаграммы раскрытия трещины.
На рис. 7.57 приведен график движения берегов трещины (ее раскры тие) в процессе циклического нагружения. Видно, чточ нагружение и наг рузка осуществляются по существенно различным траекториям.
Критерий, определяющий повреждаемость материала в вершине трещи ны, имеет вид
(7.108)
а-
0 ,5
0,5
0 ,0
0,3
0,2
0,/
Рис» 7,57, Максимальное раскрытие берегов трещины в соответствии с историей нагру жения
1 —1 1 — соответствуют этапам нагружения рис. 7.54
Здесь бт —остаточное обратимое раскрытие трещины в полуцикле растя жения; 8t — упругопластическое раскрытие трещины (бг=бу +5>,); Адт- односторонне накопленное (необратимое) раскрытие трещины; бс - пре дельное раскрытие трещины; 5^ —упругое раскрытие трещины.
Зависимость (7.108) определяет момент страгивания трещины, а ее развитие определяется количеством и величиной приращений, которое за висит от размера пластической зоны. Неопределенность в определении ве личины прироста трещины и трудность измерения раскрытия в вершине трещины затрудняют использование зависимости (7,108) в расчетах живу чести элементов конструкций.
При выводе этой зависимости учитывалось, что критическое раскрытие трещины бс определяется предельной пластической деформацией при раз рыве.
Все величины, входящие в эту зависимость, могут быть получены из диаграммы раскрытия трещины в ее вершине.
Применение структурной модели значительно упрощает процесс анализа влияния нестабильности материала при циклическом нагружении. Для реше ния этой задачи в качестве исходной информации должны быть использо ваны данные о изменении параметров структурных составляющих. Эта ин формация может быть получена при обработке поцикловых диаграмм
деформирования.
Экспериментальное изучение особенностей развития микродеформаций также проводилось на трубчатых образцах из аустенитной стали Х18Н10Т с рабочей частью / = 40 мм, на которой с помощью алмазной пирамиды на приборе ПМТ-3 наносились риски на расстоянии 0,5 мм. Измерение дефор маций на базе образца осуществлялось с помощью продольного деформометра.
На рис. 7.58 представлены кривые плотности вероятности для величин местных циклических деформаций б/и односторонне накопленных дефор маций б/. В работах [68,69 ] было показано, что неоднородность цикличе-
20 20 0000 AfM
0 0 /0 70 20 2000 00 AfM
Рис, 7.58. Кривые плотности вероятности местных циклических (а) и односторонних
накопленных (б) деформаций
ской пластической деформации может быть охарактеризована коэффици ентами макронеоднородности циклической и односторонне накопленной пластической деформации (см. гл. 4). Введение в расчетную практику коэффициентов неоднородности деформации позволяет по ее средним зна чениям охарактеризовать условия локального разрушения. К числу моде лей, также учитывающих наличие микропластических деформаций в поликристаллических материалах, относится модель Эсина, где в качестве па раметра усталостного повреждения выбрана энергия пластического гисте резиса, которая рассматривается как ’’вероятностная” величина [70 J .
Таким образом, применение структурных моделей позволяет не только описать процесс нагружения конструкций, но и использовать их при разра ботке критериев циклической прочности.
ЛИ Т Е Р А Т У Р А
1.Материалы Всесоюзного симпозиума по малоцикловой усталости при повышен ных температурах (Челябинск, 18—21 июня 1974 г .): В 4 вып. Челябинск: ЧПИ, 1974.
2.Малоцикловая усталость элементов конструкций: Тез. докл. и сообщ. III Всесоюз. симпоз. (Паланга, сентябрь 1979 г.): В 3 вып. Вильнюс: РИСО Минвуза ЛитССР, 1979.
3.Малоцикловая усталость — механика разрушения, живучесть и материалоемкость конструкций // Тез. докл. и сообщ. IV Всесоюз. симпоз. (Краснодар, сент. 1983 г .): В 2 вып. М.: ЦП НТО Машпром, 1983.
4.Степнов М.Н. Статистическая обработка результатов механических испытаний. М.: Машиностроение, 1972. 232 с.
5.Методика определения характеристик выносливости деталей машин. Минск: Ин-т пробл. надежности и долговечности машин АН БССР, 1978. 53 с.
6 . Махутов Н.А. Деформационные критерии разрушения и расчет элементов кон струкций на прочность. М.: Машиностроение, 1981. 272 с.
7. Карзов Г.П., Леонов В.П., Тимофеев Б.Т. Сварные сосуды высокого давления. Л.: Машиностроение, 1982. 287 с.
8 . Каган В.А., Ляонавичус М.-К.В. Влияние масштаба на распространение трещин и разрушение в зонах высокой концентрации при малоцикловом нагружении // Литов, механ. сб. Вильнюс: РИСО Минвуза ЛитССР, 1977. С. 99-106. (Тр. вузов ЛитССР; №2 (18)).
9.Болотин В.В. Статистические методы в строительной механике. М.: Стройиздат, 1961. 202 с.
10.Большее Л.Н., Смирнов Н.В. Таблицы математической статистики. М.: Наука,
1983. 416 с.
11.Серенсен С.В., Когаев В.П., Шнейдерович Р.М. Несущая способность и расчет дета лей машин на прочность. М.<: Машиностроение, 1975. 488 с.
12.Махутов Н.А., Бурак Н.И., Гаденин М.М. и др. Механика малоциклового разруше
ния. М.: Наука, 1986. 264 с.
13.Гальперин М.Я. О рассеянии характеристик выносливости по началу образования трещины и окончательному разрушению // Механическая усталость в статистиче ском аспекте. М.: Наука, 1969. С. 52-68.
14.Доценко A M ., Денисова Г.В. Влияние коэффициента интенсивности размаха нап ряжений цикла на характеристики рассеяния скорости роста усталостной трещи
ны II Тр. ЦАГИ. 1977. Вып. 1879. С. 25-27.
15.Богданов Б.Ф., Калганова З.Н., Сеник В.Я. Исследование рассеяния характеристик сопротивления усталости материала крупногабаритных штамповок из сплава
В93ПК в состоянии Т1 и Т2 // Там же. 1981. Вып. 2117. С. 76—87.
16.Йодер, Кули, Крукер. 50-кратное различие в сопротивлении росту усталостных тре щин на стадии 2 для титановых сплавов. Влияние размера зерна // Теорет. основы инж. расчетов. М.: Мир, 1979. № 1. С. 89-94.
17.Симонова, Хамагути. Зависимость между распределением числа циклов до раз рушения, конфигурацией надреза и кривой S -N для алюминиевого сплава 2024-Т4 II Там же. 1985. № 3. С. 60—73.
18.Бойцов Г.В., Палий О.М. Прочность и конструкция корпуса судов новых типов.
Л.: Судостроение, 1979. 459 с.
19.Савицкий В.Е. Исследование скорости распространения усталостных трещин // Тр. Горьк. ин-та инж. вод. транспорта. 4979. Вып. 171. С. 70—100.
20.Кузнецов А.А., Алифанов ОМ., Ветров В.И. и др. Вероятностные характеристики прочности авиационных материалов и размеров сортамента: Справочник. М.:
Машиностроение, 1970. 567 с.
21.Шашин М.Я. Вопросы перенапряжения и наклепа при усталости металлов // Неко торые вопросы усталостной прочности стали / Под ред И.Н. Давиденкова. М.; Л.:
Машгиз, 1953! С. 140-155.
22.Мацкевич В.Д. Анализ случаев хрупких разрушений сварных конструкций (по материалам МИС) // Сопротивляемость сварных конструкций хрупким разру шениям. Л.: ЛДНТП, 1971. С. 81-90.
23.Лукьянов В.Ф., Напрасников В.В. Влияние типа инициатора разрушения на разви тие трещин в сварных соединениях // Свароч. пр-во. 1983. № 5. С. 3 -5 .
24.Лукьянов В.Ф., Напрасников В.В., Ильинский К.Л. и др. Оценка допустимых раз меров дефектов сварных соединений методом статистического моделирования // Там же. 1986. № 4. С. 34-36.
25.Куркин С.А., Тарасов С.И., Волченко В.Н. Оценка вероятности отказа сварного сосуда при наличии технологических дефектов // Там же. 1987. № 4. С. 29-32.
26.Вентцель Е.С. Теория вероятностей. М.: Наука, 1969. 572 с.
27.Лукьянов В.Ф., Сигаев А.А. Установка для испытания крупногабаритных образцов при двухосном растяжении и изгибе // Завод, лаб. 1971. № 6 . С. 730-732.
28.Лукьянов В.Ф., Людмирский Ю.Г., Напрасников В.В. Малоцикловая усталость сварных штуцерных соединений // Свароч. пр-во. 1982. № 12. С. 26-28.
29. Хазанов И.И., Попитое В.А. Вероятностная модель усталостной долговечности в свете представлений линейной механики разрушения // Пробл. прочности. 1977. №2. С. 10-15.
30. Пуш Е А . Статистический анализ закономерностей развития усталостных трещин в пластинах из материала Д-16-АТ // Расчеты на прочность и жесткость: Межвуз. сб. науч.тр. М.: Мосстанкин, 1979. Вып. 3. С. 120-124.
31.Сюсюкалов Г.Б. Анализ надежности силовых элементов планера самолета с учетом кинетики процесса усталостного разрушения: Автореф. дис. канд. техн. наук. М., 1977.19 с.
32.Килю Н„ Kenji Н., Ikushi К. Fatigue crack propagation behaviours of various steel 11 The Sumitomo Search. 1977. N 17. P. 39—51.
33. Ярема СЛ., Красовский А Л ., Осташ О.П. и др. Развитие усталостного разрушения в листовой малоуглеродистой стали при комнатной и низкой температурах // Пробл. прочности. 1977. № 3. С. 21 -26 .
34.Ромвари П Т о т Л., Надь Д. Анализ закономеростей распространения усталостных трещине металлах //Там же. 1980.№ 12 .С. 18-28.
35. NiccolsE.H. A correlation for fatigue crack growth rate 11 Ser. Met. 1976. VoL 10, N 4.
P. 295-298.
36.Becker PJE., Hunsen B. Statistical evaluation of defects in welds and .design implication. Dan. Atom. Energy Comis., 1974. P. 836-852.
37.Лепихин A M ., Козлов A T ., Москвичев В.В. Прогнозирование надежности элемен тов сварных металлических конструкций по критериям механики разрушения //
Металлические конструкции для работы в суровых климатических условиях. Красноярск: Промстрой НИИпроект, 1982. С. 38-52.
38.Гололобов Б.А., Артемьев А Л . Статистические принципы определения требований на допустимые размеры технологических дефектов сварки // Выбор и обосно вание методов и норм контроля качества сварных соединений. Л.: ЛДНТП, 1976.
С.15-20.
39. Krupp W £., Hoeppner D.W. Fracture mechanics application in materials selection, fabrication sequencing and inspection // J. Aircraft. 1973. VoL 10. P. 682-688.
40. Труфяков В.И., Гиренко В.С., Давыденко В.Ф. Оценка надежности сварных соеди нений с учетом свойств материала, особенностей технологии сварки и методов
контроля // Выбор и обоснование методов и норм контроля качества сварных соединений. Л.: ЛДНТП, 1976. С. 69-73.
41. WeUein R. Beurteilung der Zuverlassjgkeit der Stahlhiille mit Hilfe der probabiHstisdien Bruchmichanik // Schuller G.I. et aL Zuverlassjgkeitsbeurteilung fiir den Sicherheitseinschhiss am Beispiel des Druckwasserreaktors. Miinchen, 1981. S. 276-291.
42.Bruckner A ., Munz D. Prediction of failure probabilities for cleavage fracture from the scatter of crack geometry and of fracture toughness using the weekest link model // Eng. Fract. Mech. 1983. Vol. 18, N 2. P. 359-375.
43.Marriott D.L., Hudson JM . Prediction of failure risk in a pressure vessel due to a manu facturing defect // Reliability problems of reactor pressure components: Proc. Symp. (Vienna, Okt. 10-13, 1977). Vienna: Intern. Atomic Energy Agency. 1978. Vol. 1. P. 95-115.
44.Злочевский A S ., Ларионов В£ . tВоронецкий A S ., Хануков X.M. Исследование характеристик трещино стой кости строительных сталей в условиях низких тем ператур // Прочность материалов и конструкций при низких температурах. Киев: Наук, думка, 1984. С 84-91.
45.Болотин В В . Методы теории вероятности и теории надежности в расчетах соору жений. М.: Сгройиздат, 1982. 351 с.
46.Прочность конструкций при малоцикловом нагружении. М.: Наука, 1983. 270 с.
47.Герцбах И.Б., Кордонский Х Б . Модели отказов. М.: Сов. радио. 1966.166 с.
48.Нормы расчета надежности металлоконструкций землеройных машин дня транс портного строительства. М.: ВНИИС Минтрансстроя, 1972.84 с.
49.Прейскурант № 23-03. Оптовые цены на химическое оборудование. Нефтехими ческая аппаратура. М.: Прейскурантиздат, 1971.67 с.
50. Бондарович Л Л ., Злочевский A S ., Шувалов А Н . и др. Оценка эксплуатацион ной надежности емкостных конструкций в условиях низких температур // Пром. стр-во. 1979. №4. С. 19-21.
51.Болотин В В . Прогнозирование ресурса машин и конструкций. М.: Машинострое ние. 1984. 312 с.
52.Гохфельд Д А ., Чернявский О.Ф. Несущая способность конструкций при повтор ных нагружениях. М.: Машиностроение, 1979.263 с.
53.Зарубин В.С. Прикладные задачи термопрочности элементов конструкций. М.:
Машиностроение. 1985. 293 с.
54. Богачев ИМ., Вайнштейн А А ., Волков СД. Статистическое металловедение.
М .: Металлургия, 1984.176 с.
55.Махутов Н.А., Гаденин ММ ., Гохфельд Д А . и др. Уравнения состояния при мало цикловом нагружении. М.: Наука, 1981.244 с.
56. Гохфельд Д .А ., Садаков О.С. Пластичность и ползучесть элементов конструкций при переменном нагружении. М.: Машиностроение, 1984.256 с.
57.Порошин B S . Влияние формы цикла деформирования на накопление поврежде ний при различных типах малоциклового нагружения с выдержками // Пробл. прочности. 1988. № 4. С. 38-43.
58.Augusti G., Buratta A. Theory of probability and limit analysis of structures under multi-parameter loading II Found of plasticity: Intern. Symp., Warsaw, Aug. 30 - Sept. 2,1972. Leiden: Noordhoff, 1972. P. 347-361.
59.Augusti G., Baratta A. Plastic shakedown of structure with stochastic local strength // Rapp, commis. trav. Assoc, intern.ponts et charpentes. 1973. Vol. 13. P. 287-292.
60.Кайур В., Ламберсон Л. Надежность и проектирование систем. М.: Мир, 1960. 604 с.
61.Худяков А В . О вероятностно-статистической оценке коэффициента запаса по
приспособляемости конструкций при теплосменах // Прочность машин и аппара тов при переменных нагружениях.Челябинск: ЧПИ, 1986.С. 55—59.
62. Садаков О.С. Однопараметрическая модель неупругой конструкции // Прочность машин и аппаратов при переменных нагружениях. Челябинск: ЧПИ, 1983.
С.27-35.
63.Бесселинг Дж.Ф. Теория пластического течения начально-изотропного материала,
который анизотропно упрочняется при пластических деформациях // Механика: Период, сб.: Пер. с иностр. яз. М.: Мир, 1961. № 2. С. 124-168.
64. Афанасьев НМ. Статистическая теория усталостной прочности металлов. Киев: Изд-во АН УССР, 1953.128 с.
65.Болотин В.В. Механика деформируемого твердого тела и теория надежности конструкций. М.: Наука, 1975. 370 с.
6 6 . Петушков В А ., Кащенко С.Ф. Структурное моделирование нелинейных процессов деформирования конструкций при циклических нагружениях // Машиноведение. 1988.№ 1. С. 3-11.
67.Кащенко С.Ф,, Романов А Л ., Петушков В.А. Численное моделирование процессов циклического деформирования элементов конструкций при неизотермическом
нагружении // Пробл. прочности. 1987. № 2. С. 24-29.
6 8 . Романов А Л ., Гаденин М.М. Особенности рассредоточенного трещинообразования
всвязи с неоднородностью развития деформаций при малоцикловом нагружении
//Структурные факторы малоциклового разрушения металлов. М.: Наука, 1977. 293 с.
69.Романов А.Н. Разрушение при малоцикловом нагружении. М.: Наука, 1988.280 с. 70. Эсин А. Применение критерия энергии микропластической деформации к устало
сти // Теорет. основы инж. расчетов. 1968. № 1. С. 33 —41.