
Статистические исследования контроля качества в автоматизированных
..pdf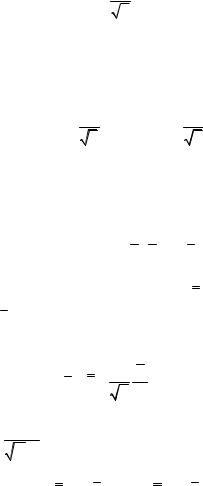
μ ± 3 σ . n
При этом, если известны μ, σ, можно следующим образом определить UCL (верхний контрольный предел) и LCL (нижний контрольный предел):
UCL = μ + 3 σ ; UCL = μ − 3 σ , n n
где σ – стандартное отклонение.
Таким образом строятся контрольные пределы на основе метода «3 сигма». Однако при этом необходимо знать генеральное среднее μ и генеральное стандартное отклонение σ. Их оценки рассчитывают по выборочным средним x1, x2 , ... , xk k групп с объёмом выборок n.
Оценка математического ожидания μ = x , оценка стандарт-
ной ошибки σ = R /d3, где d3 – коэффициент, зависящий только от n. Используя эти оценки, получаем контрольные пределы:
x = x ± 3 R . n d3
Обозначив 3 = A2 , получаем контрольные пределы: n d3
UCL = x + A2 R, LCL = x − A2 R.
Контрольные пределы для R определяются таким же образом на основе метода «3 сигма». При получении отрицательного значения нижний контрольный предел в расчёт не принимается.
161

5.11.3. Контрольные карты для регулирования по качественным признакам
5.11.3.1. Контрольная карта «р»
Анализ проводят в следующей последовательности:
1. Подсчитывают долю дефектных изделий на этапе исследуемого технологического процесса и подбирают такой объём выборки n, в котором содержалось бы от 1 до 5 дефектных изделий. Число обнаруженных дефектных изделий в выборках заносят в листок данных для 20–25 выборок. При этом объём каждой выборки n должен быть по возможности одинаковым. Кроме того, чтобы подобрать нужный объём выборки n, предварительно подсчитывают долю дефектных изделий p.
Используя выражение pn = 1…5, откуда n = 1/p…5/p единиц, определяют число дефектных изделий. Так, например, если предположить, что доля дефектных изделий p равна 0,05 (5 %), то получится
n = 1/0,05…5/0,05 = 20…100.
2. Вычисляют долю дефектных изделий p по каждой выборке:
p = (pn/n) ·100 %,
где pn – число дефектных изделий в выборке; n – объём выборки.
3.В бланк контрольной карты на шкалу ординат наносят деления для долей дефектных изделий (в процентах) p (%), а по абсцисс – номера выборок.
4.В контрольную карту наносят точки, соответствующие значениям p.
5. Вычисляют среднее p от p:
p = |
pn |
100 %, |
(5.14) |
n |
где Σpn – суммарное число дефектных изделий; Σn – суммарное число проверенных изделий.
162
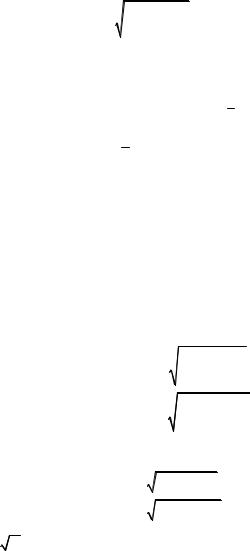
6. Рассчитывается среднее квадратическое отклонение Sp:
|
|
|
(100 − |
|
) |
,%. |
|
Sp = |
|
p |
p |
(5.15) |
|||
|
|
|
|
|
|||
|
|
|
n |
|
В рассматриваемом примере объём выборки n – постоянный. На практике часто объём выборки меняется. Если объём выборки меняется не очень существенно, то для расчёта Sp можно применить простой и дробный метод, используя среднее n от n:
n = |
n |
, |
(5.16) |
k
где n – суммарное число проверенных изделий за рассматривае-
мый период времени; k – суммарное число проверенных выборок (расчёт sp по n при переменном n не приведет к существенным погрешностям в том случае, если n для конкретных выборок изменяется относительно найденного по приведенной выше формуле n в пределах от 1/2 до 2 раз). Как правило, в реальном производстве имеют место изменения объёмов выборок в указанных пределах.
7. Вычисляются координаты границ регулирования p:
|
|
|
|
|
|
|
|
|
|
|
|
|
|
|
|
|
|
|
|
(100− |
|
|
) |
, |
||||||
UCL = |
|
|
+ 3Sp = |
|
|
+ 3 |
|
|
p |
p |
||||||||||||||||||||
p |
p |
|||||||||||||||||||||||||||||
|
|
|
|
|
n |
|||||||||||||||||||||||||
|
|
|
|
|
|
|
|
|
|
|
|
|
|
|
|
|
|
|
|
|
|
(5.17) |
||||||||
|
|
|
|
|
|
|
|
|
|
|
|
|
|
|
|
|
|
|
(100− |
|
|
) |
||||||||
|
|
|
|
|
|
|
|
|
|
|
|
|
|
|
|
|
||||||||||||||
LCL = |
|
|
− 3Sp = |
|
|
− 3 |
|
|
p |
p |
, |
|||||||||||||||||||
p |
p |
|||||||||||||||||||||||||||||
|
|
|
|
|
|
n |
||||||||||||||||||||||||
|
|
|
|
|
|
|
|
|
|
|
|
|
|
|
|
|
|
|
|
|
|
|
||||||||
или |
|
|
|
|
|
|
|
|
|
|
|
|
|
|
|
|
|
|
|
|||||||||||
UCL = |
|
|
+ A |
|
|
|
|
(100− |
|
|
), |
|
||||||||||||||||||
p |
p |
p |
|
|||||||||||||||||||||||||||
UCL = |
|
− A |
|
|
(100− |
|
), |
|
||||||||||||||||||||||
p |
p |
p |
|
где A= 3 / n.
Долю дефектных изделий и границы для выборки вычисляют каждый раз, если объём выборки n неодинаков при каждом отборе.
163
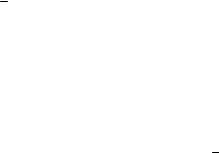
При отрицательном значении LCL оно приравнивается к нулю. 8. Полученные значения UCL и LCL наносят на контрольную карту. Значение p обозначается сплошной линией, а границы UCL,
LCL – пунктирной.
9. Технологический процесс протекает стабильно, если все наносимые точки находятся внутри границ регулирования. При выходе некоторых точек за границы регулирования изучается причина этого явления, и принимаются меры воздействия, предупреждающие его повторение. Эти точки исключаются, и координаты границ регулирования пересчитывают.
10. Полученное в 5-м действии значение p анализируется
в техническом и экономическом аспектах, насколько оно отвечает требованиям. Если оно окажется удовлетворительным, то используют его как среднюю контрольную линию. Если же доля дефектных изделий слишком велика, то первоочередной проблемой является выработка технических мер воздействия, предусматривающих такую технологию, которая могла бы уменьшить возникновение дефектных изделий. Применив такие технические меры воздействия, повторяют отбор предварительных данных.
Предварительно определяют долю дефектных изделий на этапе контроля технологического процесса, подбирая такой объём выборки n, в котором содержалось бы от 1 до 5 дефектных изделий. Число обнаруженных дефектных изделий выборки заносят в листок данных для 20 выборок. При этом объём каждой выборки n должен быть по возможности одинаковым. Кроме того, чтобы подобрать нужный объём выборки n, предварительно подсчитывают долю дефектных изделий p.
5.11.3.2. Контрольная карта доли дефектных изделий при постоянном числе проверяемых изделий
Пример5.12. Рассмотрим пример расчёта контрольной карты p. С 1 по 29 марта 2011 г. было проверено 20 выборок изделий одинакового объёма (табл. 5.14).
164
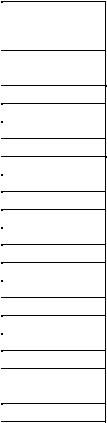
Таблица 5 . 1 4
Исходные и расчётные значения параметров для построения контрольной карты p при постоянном
числе проверяемых изделий
Дата, |
Номер |
Число |
Числодефект- |
Долядефектных |
|
проверенных |
ныхизделий pn, |
изделийр, % |
|||
март 2011 |
выборки |
||||
|
|
изделийn, шт. |
шт. |
p = pn /n · 100 % |
|
1 |
1 |
500 |
4 |
0,80 |
|
2 |
2 |
500 |
0 |
0,00 |
|
|
|
|
|
|
|
3 |
3 |
500 |
10 |
2,00 |
|
6 |
4 |
500 |
8 |
1,60 |
|
7 |
5 |
500 |
4 |
0,80 |
|
|
|
|
|
|
|
8 |
6 |
500 |
4 |
0,80 |
|
9 |
7 |
500 |
6 |
1,20 |
|
10 |
8 |
500 |
4 |
0,80 |
|
|
|
|
|
|
|
14 |
9 |
500 |
2 |
0,40 |
|
15 |
10 |
500 |
2 |
0,40 |
|
16 |
11 |
500 |
6 |
1,20 |
|
|
|
|
|
|
|
17 |
12 |
500 |
0 |
0,00 |
|
20 |
13 |
500 |
8 |
1,60 |
|
21 |
14 |
500 |
4 |
0,80 |
|
|
|
|
|
|
|
22 |
15 |
500 |
6 |
1,20 |
|
23 |
16 |
500 |
10 |
2,00 |
|
24 |
17 |
500 |
6 |
1,20 |
|
|
|
|
|
|
|
27 |
18 |
500 |
10 |
2,00 |
|
28 |
19 |
500 |
0 |
0,00 |
|
29 |
20 |
500 |
0 |
0,00 |
|
|
|
|
|
|
|
Всего |
k = 20 |
Σn = 10 000 |
Σpn = 94 |
– |
Цель контроля заключается в констатации реального уровня дефектности в наблюдаемый период, необходимости анализа производственного процесса и определения реальных возможностей на ближайший плановый период.
165
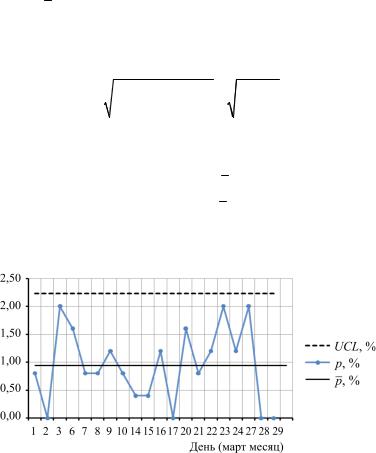
Решение.
1.Рассчитываем среднюю долю дефектных изделий: p = (Σpn)/Σn · 100 = 94/10000 · 100 = 0,94 %.
2.При колебании объёмов проверяемых изделий стандартное отклонение рассчитывается следующим образом:
Sp |
= 0,94(100 |
− 0,94) = |
53,12 . |
|
n |
|
n |
3. Определим верхнюю и нижнюю границы регулирования исследуемого производственного процесса:
–верхняя граница регулирования p + 3 Sp = 2,23 ;
–нижняя граница регулирования p − 3 Sp ≤ 0 .
Нижняя граница регулирования получилась меньше нуля, следовательно, она принимается равной нулю (рис. 5.36).
Рис. 5.36. Контрольная карта p при постоянном числе проверяемых изделий
На основании приведенных данных можно сделать выводы:
1.В исследуемый период процесс протекал достаточно точно
истабильно. Установлена доля дефектных изделий – 0,94 %.
166
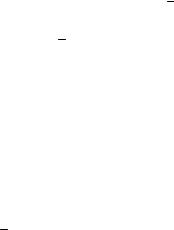
2. Учитывая результаты анализа технологического процесса, можно рекомендовать переход от сплошного контроля к выборочному по ГОСТ 18242-72 («Статистический приемочный контроль по альтернативному признаку. Планы контроля»), что приведет
кснижению трудозатрат на контроль.
3.По результатам проверки выборок из партии следует осуществлять наблюдение за технологическим процессом с помощью контрольных карт с целью своевременного обнаружения отклонений и их устранения.
Аналогичным образом строится контрольная карта p для переменного объёма выборки n.
5.11.3.3. Контрольная карта доли дефектных изделий при переменном числе проверяемых изделий
Пример 5.13. Рассмотрим пример расчёта контрольной карты p. С 1 по 29 марта было проверено 20 выборок изделий разного объёма (табл. 5.16).
Решение. Учитывая, что n переменное и объём выборки меняются не очень существенно, то для расчёта Sp можно применить простой и дробный метод, используя среднее n от n:
n = n / k,
где Σ n – суммарное число проверенных изделий за рассматриваемый период времени; k – суммарное число проверенных выборок.
Расчёт Sp по n при переменных n не приведет к существенным погрешностям в том случае, если для конкретных выборок изменяется относительно найденного по приведенной формуле n в пределах от ½ до 2 раз.
Используя приведенное рассуждение, найдем среднее от n:
n = n / k =18430 / 20 =921,5.
167

Наименьшее число согласно табл. 5.15 (680 шт.) проверялось 17 марта (порядковый номер 12). Тогда n =680 / 921,5=0,738. Наи-
большее число проверяемых деталей – 1050 ( n =1050 / 921,5 =1,139. ),
то есть изменение конкретных объёмов проверяемых деталей по отношению к среднему лежит в пределах от ½ до 2. Поэтому все расчёты можно выполнять по приведенным выше формулам, пренебрегая тем, что n – переменное.
Однако на примере приведем расчёты с учетом переменного n:
1.Рассчитываем среднюю долю дефектных изделий: p = (Σ pn) /Σn·100 = 94/18430·100 = 0,51 %.
2.При колебании объёмов проверяемых изделий стандартное отклонение рассчитывается следующим образом:
Sp |
= 0,51(100 − 0,51) = |
50,74 . |
|
n |
n |
3. Определим верхнюю и нижнюю границы регулирования исследуемого производственного процесса:
–верхняя граница регулирования p + 3 Sp ;
–нижняя граница регулирования p − 3 Sp .
В табл. 5.15 приведены исходные данные для построения контрольной карты p и полученные расчётные значения верхней и нижней границ регулирования.
На основе данных табл. 5.15 построим контрольную карту p
(рис. 5.37).
На основании полученных результатов данных можно сделать выводы:
1.В исследуемый период времени процесс протекал стабильно. Процент дефектных изделий находится в пределах от 0,00 до 1,05 %.
2.Учитывая результаты анализа технологического процесса, можно рекомендоватьпереходотсплошного контроляквыборочному.
168
Таблица 5 . 1 5
Исходные и расчётные значения параметров для построения контрольной карты p при переменном
числе проверяемых изделий
|
№ |
Число |
Число |
Доля |
|
|
|
Дата |
прове- |
дефектных |
дефектных |
Sp, |
UCL, |
LCL, |
|
выборки |
ренных |
изделий |
изделий |
% |
% |
% |
|
|
|
изделий n |
pn |
p, % |
|
|
|
1 |
1 |
950 |
4 |
0,42 |
0,23 |
1,20 |
–0,18 |
2 |
2 |
950 |
0 |
0,00 |
0,23 |
1,20 |
–0,18 |
|
|
|
|
|
|
|
|
3 |
3 |
1050 |
10 |
0,95 |
0,22 |
1,17 |
–0,15 |
6 |
4 |
950 |
8 |
0,84 |
0,23 |
1,20 |
–0,18 |
7 |
5 |
950 |
4 |
0,42 |
0,23 |
1,20 |
–0,18 |
|
|
|
|
|
|
|
|
8 |
6 |
950 |
4 |
0,42 |
0,23 |
1,20 |
–0,18 |
9 |
7 |
950 |
6 |
0,63 |
0,23 |
1,20 |
–0,18 |
10 |
8 |
950 |
4 |
0,42 |
0,23 |
1,20 |
–0,18 |
|
|
|
|
|
|
|
|
14 |
9 |
900 |
2 |
0,22 |
0,24 |
1,22 |
–0,20 |
15 |
10 |
900 |
2 |
0,22 |
0,24 |
1,22 |
–0,20 |
16 |
11 |
950 |
6 |
0,63 |
0,23 |
1,20 |
–0,18 |
|
|
|
|
|
|
|
|
17 |
12 |
680 |
0 |
0,00 |
0,27 |
1,33 |
–0,31 |
20 |
13 |
950 |
8 |
0,84 |
0,23 |
1,20 |
–0,18 |
21 |
14 |
950 |
4 |
0,42 |
0,23 |
1,20 |
–0,18 |
|
|
|
|
|
|
|
|
22 |
15 |
950 |
6 |
0,63 |
0,23 |
1,20 |
–0,18 |
23 |
16 |
950 |
10 |
1,05 |
0,23 |
1,20 |
–0,18 |
24 |
17 |
950 |
6 |
0,63 |
0,23 |
1,20 |
–0,18 |
|
|
|
|
|
|
|
|
27 |
18 |
1050 |
10 |
0,95 |
0,22 |
1,17 |
–0,15 |
28 |
19 |
750 |
0 |
0,00 |
0,26 |
1,29 |
–0,27 |
29 |
20 |
750 |
0 |
0,00 |
0,26 |
1,29 |
–0,27 |
|
|
|
|
|
|
|
|
Всего |
k = 20 |
Σn = 18 430 |
Σpn = 94 |
– |
– |
– |
– |
169
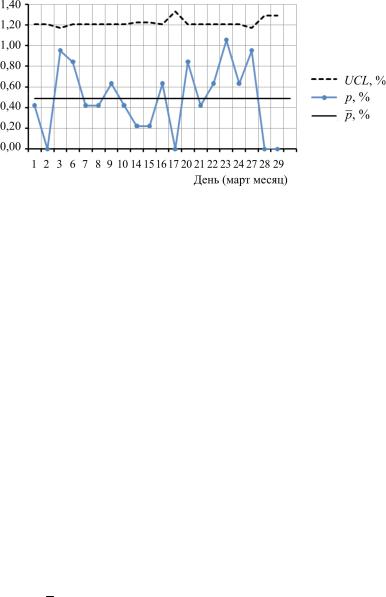
Рис. 5.37. Контрольная карта p при переменном числе проверяемых изделий
При этом следует отметить, что при наличии факта выхода контролируемого процесса за верхнюю или нижнюю границу регулирования он должен фиксироваться и тщательно анализироваться с целью выявления и устранения причин дефектов. Проведение такой планомерной работы будет способствовать не только стабилизации, но и улучшению качества, поскольку постепенно будут выявляться наиболее существенные и часто повторяющиеся причины дефектов.
5.11.3.4. Контрольная карта числа дефектных чисел «pn»
Примем, что средний процент брака в производственном процессе стабилизирован на уровне p. Это значит, что процент брака в генеральной совокупности равен p. Тогда, если обозначить через X число бракованных единиц из общего числа отобранных изделий n, то X будет следовать биномиальному распределению
B(n, p), и поэтому:
♦среднее Мх = pn;
♦дисперсия Dx = pn (1 – p).
Однако, поскольку неизвестен генеральный процент брака p, используется p , определяемое на основе предварительных данных,
а именно
170