
Статистические исследования контроля качества в автоматизированных
..pdf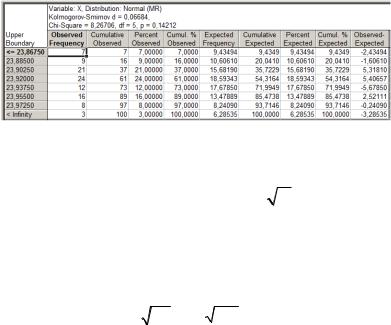
Рис. 5.16. Оценки по критерию Пирсона и Колмогорова
Максимальное значение критерия Колмогорова Dmax = 0,067
(см. рис. 5.16). При этом значение λк = Dmax N = 0,67, которому соответствует вероятность принятия гипотезы P(λк) = 0,8 (приложение 10).
Значение критерия Романовского:
AP = |
χ2 − f |
= |
|
8,67 − 5 |
|
= 1,16. |
|
|
|||||
|
|
|
|
|||
2 f |
|
2 5 |
|
|||
|
|
|
|
|
Величина Aр < 3, следовательно, практическое распределение по этому критерию также соответствует нормальному теоретическому закону распределения.
Поскольку отклонение теоретических частот mi′, определённых по закону модуля разности и в программе «STATISTICA 8» (кривая без маркеров, см. рис. 5.12), различаются не более чем на 1,41 %, то гипотеза о нормальном законе распределения изучаемого признака одинаково подтверждается в этих двух случаях.
5.4. РАССЛАИВАНИЕ (СТРАТИФИКАЦИЯ) ДАННЫХ
Расслаивание – один из наиболее простых, эффективных и распространенных методов выявления причин несоответствий влияния различных факторов на показатели качества процесса.
111
Расслоение заключается в разделении данных на группы в соответствии с их особенностями. В этом случае такие группы именуют слоями (стратами), поэтому метод разделения на слои (страты) называют расслаиванием (стратификацией). При этом исходят из того, чтобы различия в пределах слоя были как можно меньше,
аразличия между слоями – как можно больше.
Впроцессе измерений исходят из предположения, что всегда можно обнаружить больший или меньший разброс контролируемых параметров. Осуществляя стратификацию разброса результатов, порожденного рассматриваемыми факторами, можно выявить главную причину появления наблюдаемого разброса, уменьшить его и добиться тем самым повышения качества продукции.
Взависимости от конкретных решаемых задач применяются различные способы расслаивания. Наиболее часто при исследовании производственных процессов используют способ, называемый 4М, в котором учитывают факторы, зависящие:
♦ от человека (man);
♦ машины (machine);
♦ материала (material); ♦ метода (method).
Расслаивание можно осуществить:
♦ поисполнителям– по работающим, полу, стажу работыит.д.; ♦ машинам и оборудованию – по новому и старому; ♦ марке оборудования, конструкции, фирмам-производите-
лям и т.д.;
♦материалу – по месту производства, партии, качеству сырья, фирме-производителю и т.д.;
♦способу производства – по температуре, технологическому приему, месту производства работ.
На практике стратификация используется для расслаивания статистических данных по различным признакам и анализа выявленной при этом разницы в диаграммах Парето, схемах Ишикавы, гистограммах, диаграммах рассеивания и т.д.
112
В качестве примера рассмотрим обработку одноименных деталей одного класса точности на станках различных марок
иразного года производства. В этом случае есть разница в технических данных станков в зависимости от завода-изготовителя
исрока службы станков. Все это является причиной разброса точностных характеристик деталей. В этом случае можно получить информацию об отклонениях параметров деталей от заданных в конструкторском чертеже. Для этого необходимо проанализировать данные, расслоив станки по производителям и срокам их эксплуатации.
На разброс точностных характеристик деталей оказывают влияние и другие факторы: квалификация и внимание исполнителей (если обработка идет не на автоматически настроенных станках), качество исходных заготовок, методы и условия организации технологических процессов и т.п. Используя эти факторы для расслаивания, можно провести анализ исследуемых процессов и повысить достоверность проведенных исследований.
Проводя стратификацию по факторам первого порядка, можно в дальнейшем изучать факторы второго и даже третьего порядка, которые могут оказывать влияние на разброс показателей качества.
Метод расслоения данных применяют:
♦при расчёте стоимости изделия, когда требуется оценка прямых и косвенных расходов отдельно по изделиям и по партиям;
♦оценке прибыли от продажи изделий отдельно по клиентам
ипо изделиям;
♦оценке качества хранения по изделиям и по партиям и т.д.
Пример 5.6. В табл. 5.5 представлены результаты измерений размеров деталей и распределения частот. Первые 50 деталей изготовлены исполнителем А, а детали 50…100 – исполнителем В.
Решение. Из полученного расслоения (см. табл. 5.5) видно, что результаты работы исполнителей А и В отличаются друг от друга весьма заметно.
Рассчитаем по формулам среднее
113

x= mi xi
mi
и дисперсию
D= mi (xi − x)2
хmi
результатов измерений, расслоенных по исполнителям А и В. Среднее для исполнителя А = 19,94; дисперсия = 0,001684. Среднее для исполнителя В = 19,99; дисперсия = 0,001216. Общее для исполнителей А и В среднее составит 19,96, дис-
персия – 0,001868.
Из этих результатов видно, что благодаря проведенному расслоению дисперсия внутри слоев уменьшилась.
Таблица 5 . 5
Распределение результатов измерений по исполнителям
Результаты |
Граница |
|
Частота |
|
|
измерений, |
интервалахi, |
Исполнитель А |
|
Исполнитель В |
Сумма |
интервалы, мм |
мм |
|
|
|
|
19,85…19,87 |
19,87 |
2 |
|
– |
2 |
19,87…19,89 |
19,89 |
8 |
|
– |
8 |
19,89…19,91 |
19,91 |
8 |
|
– |
8 |
19,91…19,93 |
19,93 |
6 |
|
3 |
9 |
19,93…19,95 |
19,95 |
9 |
|
11 |
20 |
19,95…19,97 |
19,97 |
10 |
|
13 |
23 |
19,97…19,99 |
19,99 |
3 |
|
8 |
11 |
19,99…20,01 |
20,01 |
1 |
|
10 |
11 |
20,01…20,03 |
20,03 |
3 |
|
2 |
5 |
20,03…20,05 |
20,05 |
– |
|
1 |
1 |
20,05…20,07 |
20,07 |
– |
|
1 |
1 |
20,07…20,09 |
20,09 |
– |
|
1 |
1 |
Итого |
|
50 |
|
50 |
100 |
114
Кроме того, для удобства анализа данных при их расслоении также может осуществляться построение рассмотренных выше гистограмм (например, в табл. 5.5 для исполнителей А и В).
Пример 5.7. При изучении сроков поставок комплектующих выявлено, что из общего количества заказов 136 часть не выполняется в срок. Необходимо разработать комплекс мероприятий по сокращению количества задержек поставок.
Решение. Проанализированные данные по срокам поставки представлены в табл. 5.6.
|
|
|
|
Таблица |
5 . 6 |
|
||
|
Результаты анализа заказов по срокам поставки |
|
|
|||||
|
|
|
|
|
|
|
|
|
|
Оформление |
Выполнение |
Выполнениезаказа |
|
Всего |
|
|
|
|
заказа |
заказавсрок |
|
сопозданием |
|
случаев |
|
|
|
Всоответствии |
44 |
6 |
|
50 |
|
|
|
|
сустановленнойдатой |
|
|
|
||||
|
|
|
|
|
|
|
|
|
|
Сопозданием |
8 |
88 |
|
96 |
|
|
|
|
|
|
|
|
|
|
|
|
|
Всегослучаев |
52 |
94 |
|
146 |
|
|
|
|
|
|
|
|
|
|
|
|
|
При расслоении данные оказываются расположенными менее |
|||||||
упорядоченно (табл. 5.7). |
|
|
|
|
|
|
||
|
|
|
|
Таблица |
5 . 7 |
|
||
|
Стратификация выполнения заказов |
|
|
|
||||
|
|
|
|
|
|
|||
|
Оформление |
Выполнение |
|
Выполнениезаказа |
Всего |
|||
|
заказа |
заказавсрок |
|
сопозданием |
случаев |
|||
Всоответствии |
14 |
|
36 |
|
50 |
|
|
|
сустановленнойдатой |
|
|
|
|
||||
|
|
|
|
|
|
|
||
Сопозданием |
38 |
|
56 |
|
94 |
|
|
|
|
|
|
|
|
|
|
|
|
Всегослучаев |
52 |
|
92 |
|
144 |
|
|
|
|
|
|
|
|
|
|
|
|
В этом случае проводим расслоение по видам комплектующих, которые составляют заказ (табл. 5.8).
115
|
|
|
Таблица 5 . 8 |
|
Стратификация заказов по видам комплектующих |
||||
|
|
|
|
|
Детали |
Выполнение |
Выполнениезаказа |
|
Всегослучаев |
|
заказавсрок |
сопозданием |
|
|
А |
6 |
20 |
|
26 |
В |
12 |
23 |
|
35 |
С |
3 |
22 |
|
25 |
D |
27 |
8 |
|
35 |
E |
19 |
13 |
|
32 |
F |
13 |
3 |
|
16 |
Всегослучаев |
80 |
89 |
|
169 |
Согласно полученным исследованиям (см. табл. 5.8) наибольшее число случаев задержек поставок относится к поставкам деталей В, D, Е. Необходимо проанализировать причину такой разницы в сроках поставок и разработать необходимые мероприятия.
5.5. ДИАГРАММА ПАРЕТО
Диаграмма Парето используется для оценки качества продукции или услуги. Для этого из большого числа факторов выделяется часть главных факторов, влияющих непосредственно на качество.
При построении диаграммы Парето по горизонтальной оси откладывают в определенном порядке наименования анализируемых факторов (признаков), а по вертикальной – значения каждого из факторов в безразмерных единицах (%) или размерных единицах, общих для анализируемых признаков.
Эффективность диаграммы Парето повышается при соблюдении следующих рекомендаций:
1. Отбирая среди факторов доминирующие, оказывающие наибольшее влияние на качество исследуемой системы, за критерий выбора следует принимать стоимостные показатели. Число факторов не должно превышать 7…10.
116
2.В качестве критерия оценки качества выбирают один результирующий показатель, на который влияют различные факторы,
исреди них выделить тот, который оказывает наибольшее влияние.
3.В случае, если отобранные факторы оказывают равное влияние или среди них выделяется один значимый, то необходимо пересмотреть перечень отобранных факторов и заново проверить полученные данные.
4.Отбирая факторы в столбец таблицы факторов «Прочие», следует обратить внимание на его показатель: при слишком большом его значенииследуетизнеговыделитьнесколькои повторитьанализ.
5.Анализируя данные различных типов однородной продукции, диаграмма Парето позволяет оценить их уровень качества и степень совершенства.
6.Исследуя качество продукции через определенные интервалы времени (через 3, 6 месяцев, 1 год), можно оценить уровень мероприятий, направленных на совершенствование производства для ее повышения.
Диаграммы Парето строят в следующей последовательности: 1) исходя из критерия выбора и цели проведения исследования, отбирают соответствующие факторы (признаки) и период сбо-
ра данных; 2) сбор данных и заполнение соответствующих таблиц;
3) обработка данных;
4) анализ данных и выдача рекомендаций по совершенствованию качества исследуемой продукции.
Пример 5.8. Для проверки правильности выбора из возможных испытательных стендов стенда для испытания агрегатов автомобиля, определения «узких» мест его ремонта и организации рабочих мест выделить наиболее «дефектоносные» агрегаты.
Для принятия решения:
1) в качестве признаков выбираем: двигатель; ходовую часть; рулевое управление; трансмиссию; тормозную систему; кузов; электрооборудование;
2) время сбора данных – 6 месяцев;
117
3)определяем число дефектов, приходящихся на каждый аг-
регат (ni) по дефектным ведомостям, полученным в результате возврата автомобилей после ремонта. Общее число дефектов N = 100.
Вспециальный учетный листок (табл. 5.9) заносим результаты наблюдений. При построении диаграммы Парето персоналом ремонтного предприятия результаты, представленные в табл. 5.9, можно было бы при аудите рассматривать в качестве исходной документации как протоколы испытаний и их считать относящимися к документации системы качества;
4)по данным табл. 5.9 формируем таблицу для построения диаграммы Парето (табл. 5.10) таким образом, чтобы в первой строке содержалась информация об агрегате с максимальным числом дефектов; в последующих – по уменьшению.
Таблица 5 . 9
|
Данные учетного листка |
||
|
|
|
|
Наименование |
|
Число |
Примечание |
агрегата |
|
дефектов |
|
|
|
||
Двигатель |
|
9 |
Критериидефектовзаданы |
|
вТУ и программеиспытаний |
||
|
|
|
|
Трансмиссия |
|
23 |
– |
Ходоваячасть |
|
12 |
– |
Рулевоеуправление |
|
6 |
– |
Тормознаясистема |
|
2 |
– |
Кузов |
|
18 |
– |
Электрооборудование |
|
30 |
– |
Итого |
|
100 |
– |
При накопленной сумме дефектов, отличной от N, или накопленной сумме процентов, отличной от 100 %, следует проверить вычисления и определить ошибку, которая может быть связана с округлением чисел. На основании данных табл. 5.10 строится диаграмма Парето:
♦на горизонтальной оси отмечены наименования агрегатов
втой же последовательности, что и в табл. 5.10;
118
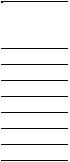
♦на левой вертикальной оси откладывается в соответствующем масштабе суммарное число дефектов, максимальное значение которых должно соответствовать общему числу дефектов N;
♦на правой вертикальной оси откладываются в соответствующем масштабе, значения накопленного процента дефектов, максимальное значение которых должно соответствовать 100 %.
Таблица 5 . 1 0
Данные диаграммы Парето
Наименование |
Число |
Накопленная |
Число |
Накопленная |
агрегата |
дефектов |
сумма |
дефектов, |
сумма |
дефектов |
% |
дефектов, % |
||
Электрооборудование |
30 |
30 |
30 |
30 |
Трансмиссия |
23 |
53 |
23 |
53 |
Кузов |
18 |
71 |
18 |
71 |
Ходоваячасть |
12 |
83 |
12 |
83 |
Двигатель |
9 |
92 |
9 |
92 |
Рулевоеуправление |
6 |
98 |
6 |
98 |
Тормознаясистема |
2 |
100 |
2 |
100 |
Максимальные значения накопленных сумм дефектов (количество и %), отложенные в соответствующем масштабе в виде «столбиков» на левой и правой вертикальных осях, равны между собой.
Анализ диаграммы Парето (рис. 5.17), построенной по данным табл. 5.10, показывает, что 71 % дефектов приходится на 3 системы автомобиля: электрооборудование, трансмиссия, кузов. Эта диаграмма Парето является источником информации, подтверждающей правильность выбора испытательного стенда, а также организации рабочих мест диагностирования и свидетельствует о наличии «узких» местах производства, на которых должны быть повышены требования к системе качества.
Опираясь на результаты диаграммы Парето, отдел качества ремонтного предприятия получает информацию о месте проведения первоочередных мероприятий по повышению качества ремонта автомобиля. В систему мероприятий в первую очередь должны быть включены 3 выделенных агрегата автомобиля.
119
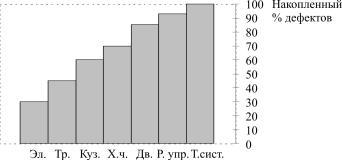
Рис. 5.17. Диаграмма Парето
Причинами, влияющими на качество продукции, могут быть дефекты сборочных единиц, технологические операции, исполнители и т.д., которые следует расположить по убывающей степени влияния (для этого необходимо провести стратификацию) и необходимо определить степень влияния дефектных агрегатов на убытки, число и интенсивность отказов и т.п.
Можно сказать, что левая часть диаграммы определяет факторы, которые показывают последовательность их анализа для повышения системы качества.
Подобным же образом строят диаграммы, у которых по оси абсцисс под номерами вместо наименований деталей, как это указано на рис. 5.18, фигурируют дефекты одной из деталей, например: занижен наружный диаметр; на режущей кромке резца имеются налипы; завышен шаг резьбы; увеличен скос кромки и т.д., или причины одного конкретного дефекта, например: неопытность оператора; неточность станка; неточность инструмента и т.д.
Для анализа информации о дефектах и оценки уровня надежности конструкции необходимо создание информационно-поисковой системы (ИПС) с созданием банка данных как части общей информационной системы предприятия.
В банке данных хранится информация о дефектах и разработанных мероприятиях по их предотвращению. Наличие большого объема статистических данных будет способствовать повышению
120