
monomers-Платэ-книга
.pdf
391
прореагировавший ацетилен и азот непрерывно удаляются и перед рециклом компримируются. Продукты реакции отводят из верхней части реактора в жидком виде, и их основное количество поступает на центрифугу, где отделяют катализатор, который затем возвращают в реактор вместе со свежим формалином. Бутиндиол в виде 35%-ного водного раствора выделяют ректификацией.
Гидрирование бутин-2-диола-1,4. Процесс гидрирования бутин-2- диола-1,4 с образованием бутандиола
HOCH2C C-CH2OH + 2H2 HOCH2CH2CH2CH2OH
осложнен протеканием побочных реакций гидрогенолиза и дегидратации, приводящих к образованию фурана, гидроксимасляного ангидрида и ненасыщенных соединений.
Гидрирование проводят в два этапа. Первый этап осуществляется в реакторе с мешалкой при 323-333 К и 1,4-2,0 МПа в присутствии никеля Ренея и ацетата меди. Полученная реакционная смесь, содержащая бутандиол, гидроксимасляный альдегид и ненасыщенные соединения, направляется во второй реактор, заполненный стационарным слоем катализатора. Процесс протекает при 393-413 К и 14-20 МПа. Катализатор включает никель, медь и марганец, нанесенные на оксид алюминия в соотношении (по массе) 15:78:0,5. Бутандиол выделяют ректификацией.
Синтез бутандиола-1,4 из пропилена
Разработаны различные способы получения бутандиола-1,4 на основе пропилена. В большинстве из них промежуточным продуктом является аллиловый спирт или аллилацетат.
Процесс "Дженерал Электрик". На первой стадии процесса происходит парофазное окислительное ацетоксилирование пропилена до аллилацета-
та:
CH2=CH—CH3 + CH3COOH + 0,5O2 |
O |
CH2=CH—CH2—O—C + H2O. |
|
|
CH3 |
Ацетоксилирование пропилена можно проводить как в жидкой, так и в газовой фазах, однако опыт эксплуатации жидкофазных установок показал, что сильная коррозия аппаратуры, вызванная действием катализаторного раствора и уксусной кислоты, делает такой вариант процесса неэффективным. Поэтому в 1960-1970-х годах от него отказались.
Процесс газофазного ацетоксилирования пропилена до аллилацетата как самостоятельный способ для получения на основе аллилацетата аллилового
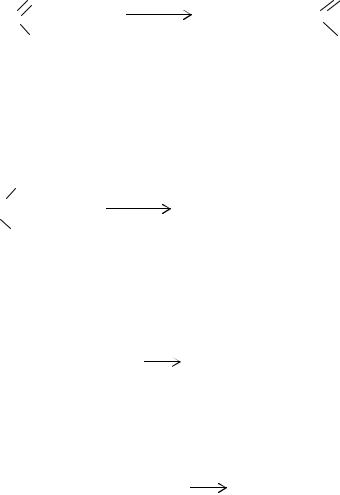
392
спирта, глицидола, эпихлоргидрина, бутандиола-1,4, тетрагидрофурана был разработан ВНИИОС (СССР). По этому способу газофазное ацетоксилирование пропилена осуществляют при 453-473 К и 0,7-0,8 МПа.
Нижний предел температуры процесса определяется минимальной температурой газообразного состояния уксусной кислоты в смеси с пропиленом при заданном давлении, верхний – значительным снижением селективности реакции за счет горения исходных продуктов и образования диокисда углерода. В качестве катализатора используется палладийвисмуткалиевая композиция, нанесенная на силикагель, которая обеспечивает высокую селективность и срок службы до 4000 ч.
Далее аллилацетат гидроформилируют смесью оксида углерода и водорода до 4-ацетоксибутанола:
O |
O |
CH2=CH—CH2O—C + CO + H2 Co2(CO)8 |
HO(CH2)4O—C |
CH3 |
CH3 |
Гидроформилирование осуществляют в присутствии карбонилкобальтового катализатора при 398 К и 2,0 МПа. Одним из недостатков процесса гидроформилирования является образование смеси диолов.
На последней стадии 4-ацетоксибутанол гидролизуют до бутандиола-1,4 и уксусной кислоты:
O |
Кислота HO(CH2)4OH + CH3CООН. |
HO(CH2)4O—C + H2O |
|
CH3 |
|
Процесс "Дэви - Дженерал Электрик". Этот процесс предполагает взаимодействие на первой стадии аллилового спирта с изобутиленом с образованием аллил-трет-бутилового эфира:
CH2=CH-CH2OH + CH2=C(CH3)2 |
CH2=CH—CH2—O—C(CH3)3, |
а также гидроформилирование, гидрирование и разложение аллил-трет- бутилового эфира на бутандиол и рециркулируемый изобутилен на второй стадии
(CH3)3C-O-CH2-CH=CH2 + CO + H2
→ (CH3)3C—O-CH2CH2CH2CH2OH ,

393
(CH3)3C—O-CH2CH2CH2CH2OH→ (CH3)2C=CH2 + HOCH2CH2CH2CH2OH.
Процесс «БАСФ – Селаниз - Дюпон». Процесс заключается в предварительной защите альдегидной группы акролеина ацетилизацией спиртом с последующим гидроформилированием непредельного ацеталя:
СН2=СН—СНО + 2ROH СН2=СН—СН(ОR)2 + Н2О,
СН2=СН—СН(ОR)2 + СО + Н2 → НОС—СН2—СН2—СН(ОR)2.
Полученный продукт далее гидролизуют и гидрируют в бутандиол-1,4.
Синтез бутандиола-1,4 на основе возобновляемого сырья (процесс фирмы "Квакер Оатс")
По этому процессу бутандиол-1,4 может быть синтезирован из фурфурола, который, в свою очередь, получают гидролизом растительного пентозансодержащего сырья – кукурузных початков, овсяной и рисовой шелухи, хлопковых коробочек и др.:
|
|
|
|
CHO |
-CO |
|
|
|
|
|
H2 |
|
Н2О |
HOCH2CH2CH2CH2OH |
|
|
|
|
|
|
|
|
|
|
|||||
|
|
|
|
|
|
|
|
|
|
|
||||
|
|
|
|
|
|
|
|
|
|
|
|
|||
|
|
O |
|
|
O |
|
|
O |
|
|||||
|
|
|
|
|
|
|
Бутандиол-1,4 |
|||||||
Фурфурол |
|
Фуран |
Тетрагидро- |
фуран
Синтез бутандиола-1,4 ацетоксилированием бутадиена
(процесс фирмы "Мицубиси")
Процесс заключается в ацетоксилировании бутадиена с получением бу- тандиола-1,4 и состоит из следующих стадий:
-ацетоксилирование бутадиена в 1,4-диацетоксибутен-2;
-гидрирование 1,4-диацетоксибутена-2 в 1,4- диацетоксибутан;
-гидролиз 1,4-диацетоксибутана в бутандиол-1,4.
Ацетоксилирование бутадиена осуществляют в жидкой фазе при 353 К и 3 МПа в присутствии катализатора на основе палладия, нанесенного на активированный уголь. В реактор вводят бутадиен и уксусную кислоту вместе со сжатым воздухом. Катализатор готовят в отдельном аппарате, снабженном мешал
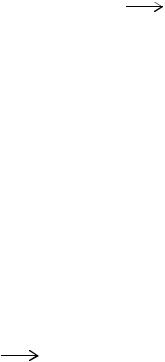
394
кой, в виде суспензии. Время контакта составляет ~ 2 ч, 1,4-диацетоксибутен-2 выделяют ректификацией.
Гидрирование проводят в реакторе с неподвижным слоем катализатора палладий на угле в два этапа: сначала при 333 К и затем при 383 К. Выход 1,4- диацетоксибутана составляет 94%.
Гидролиз 1,4-диацетоксибутандиола протекает при 333 К и атмосферном давлении в присутствии ионообменных смол. Бутандиол-1,4 выделяют ректификацией.
Синтез бутандиола-1,4 через стадию хлорированиябутадиена
(процесс фирмы "Тойо Сода")
Процесс заключается в получении бутандиола-1,4 через стадию хлорирования бутадиена и состоит из следующих стадий:
-получение 1,4-дихлорбутена-2;
-гидролиз 1,4-дихлорбутена-2;
-гидрирование бутендиола-1,4.
Хлорирование бутадиена протекает в газовой фазе при 523-573 К с образованием двух изомеров - 1,4-дихлорбутена- 2 и 3,4-дихлорбутена-1:
CH2=CH-CH=CH2 + Cl2 |
ClCH2-CH=CH-CH2Cl + |
+ CH(СI)=CH-CH2-CH2Cl
H298 = -165 кДж/моль.
В качестве побочных продуктов образуются три- и тетрахлорпроизводные. Во избежание получения большого количества полихлорированных соединений соотношение бутадиен:хлор поддерживают на уровне 6:1. В этих условиях селективность по дихлорпроизводным при полной конверсии по хлору достигает 95% при содержании 1,4-дихлорбутена-2 ~60%. Продукты разделяют ректификацией.
Для того, чтобы исключить протекание нежелательных реакций изомеризации и конденсации, гидролиз проводят не щелочью, а натриевой солью органической кислоты:
ClCH2-CH=CH-CH2Cl + 2HCOONa + 2H2O
HOCH2-CH=CH-CH2OH + 2HCOOH +2NaCl.
В реактор одновременно вводят 1,4-дихлорбутен-2, формиат натрия и щелочь для нейтрализации образующейся муравьиной кислоты. Реакцию осу-

395
ществляют при температуре кипения реакционной массы (383 К), за счет испарения которой отводится избыточное тепло. Целевой продукт выделяется дистилляцией.
Гидрирование бутендиола-1,4 осуществляют при 373 К и 3 МПа, на катализаторе никель Ренея.
Синтез бутандиола-1,4 через стадию гидроформилирования аллилового спирта
(процесс фирмы "Кураре")
По этому процессу бутандиол-1,4 получают гидроформилированием аллилового спирта синтез-газом в присутствии родиевых катализаторов с образованием 4-гидроксибутиральдегида (который далее гидрируют до бутандиола- 1,4 в присутствии никелевых катализаторов):
|
O |
|
O |
|
CH2=CH—CH2OH + CO + H2 |
Rh |
C—CH2CH2CH2OH + C—CH—CH2OH |
||
|
H |
4-Гидрокси |
|
|
|
H CH3 |
|||
|
|
бутиральдегид |
3-Гидрокси-2- |
метилпропионовый альдегид
O OH
H2, Ni |
|
|
CH3 |
|
|||
HOCH2-CH2CH2-СH2OH + HOCH2—CH—CH2OH |
Наряду с линейным альдегидом, который изомеризуется в ходе реакции в 2-гидрокситетрагидрофуран, образуется изомерный продукт - 3-гидрокси-2- метилпропионовый альдегид, в результате гидрирования превращающийся в 2- метил-пропандиол-1,3.
Реакцию гидроформилирования аллилового спирта проводят в органическом растворителе в присутствии комплекса карбонила родия, нерастворимого в воде. Далее образовавшиеся продукты экстрагируют водой и жидкую смесь
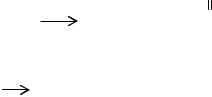
396
разделяют на органическую фазу, содержащую катализатор, и водную фазу с растворенными продуктами реакции –альдегидами. Органический растворитель с катализатором рециркулируют с повторным использованием в реакции гидроформилирования без какой-либо активации. Водный раствор с продуктами гидроформилирования направляют на гидрирование. В этом процессе катализатором является комплекс родия преимущественно с трифенилфосфином следующей формулы:
[LmRh(CO)nXq] r,
где L – фосфин, стибин или тризамещенный арсин, общей формулы YRR R , (здесь Y – атом фосфора, сурьмы или мышьяка, а R, R и R равны или не равны между собой и представлены арильной группой, имеющей от С6 до С20, алкильной группой, имеющей от С1 до С12 , или диаралкиламиновой группой, в которой аралкильная группа имеет от С7 до С24); Х – атом водорода, электроотрицательная группа или анионный заместитель в свободном состоянии; m = 0, 1, 2, 3 или 4; n = 0, 1, 2, 3 или 4; q = 0, 1 или 3; r = 1 или 2, при условии, что m, n
и q не равны нулю одновременно.
Скорость реакции и селективность зависят от общего давления синтезгаза, соотношения водорода и оксида углерода, концентрации родиевого комплекса, мольного соотношения РРh3:Rh.
Процесс осуществляют при 323-343 К и 2,0-3,0 МПа с выходом 4- гидроксибутиральдегида ~ 90%.
Аллиловый спирт в настоящее время производят в основном путем изомеризации пропиленоксида, катализируемой кислотами. Его можно также получать восстановлением акролеина, гидролизом аллилхлорида или аллилацетата, которые, в свою очередь, синтезируют окислением, хлорированием или ацетоксилированием пропилена соответственно.
В настоящее время в промышленности (в России) аллилацетат получают окислительным ацетоксилированием пропилена в газовой фазе в присутствии палладиевого катализатора при 373-523 К и давлении несколько атмосфер:
CH2=CH—CH3 + CH3COOH + 0,5O2 |
Pd |
O |
|||||
CH2=CH—CH2OCCH3 + Н2О, |
|||||||
O |
H+ |
|
|
||||
CH2=CH—CH2 |
|
|
|
OCCH3 + H2O |
CH2=CH—CH2OH + CH3COOH. |
||
|
|
Процесс получения бутандиола-1,4 из пропилена через аллиловый спирт имеет ряд преимуществ по сравнению с другими процессами, в том числе и методом Реппе. Конкурентоспособность этого способа сохранится даже при малом масштабе производства бутандиола-1,4 (примерно несколько тысяч тонн в

397
год), что обусловлено низкими капитальными вложениями.
Фирма "Арко" (США) и независимо от нее ВНИПИМ ( В.П. Юрьев, В.В. Каверин) и ИНХС им. А.В. Топчиева РАН (Г.А.Корнеева, Е.В. Сливинский) разработали процесс получения бутандиола-1,4 одностадийным гидроформилированием аллилового спирта в присутствии гомогенного родийкарбонильного катализатора, модифицированного трифенилфосфином. Особенностью процесса являются водная экстракция продукта реакции и рецикл раствора каталитического комплекса. Процесс осуществляют при 353-373 К и 0,5-1,0 МПа.
По методу ИНХС бутандиол-1,4 и -бутиролактон можно получить гидроформилированием и карбонилированием аллилового спирта и гидроформилированием аллилацетата различными путями:
|
|
O |
|
|
|
|
|
|
|
|
|
|
|
|
|
|
|
|
|
|
|
|
|
|
I |
|
(CO, H2) |
|
|
|
|
|
|
|
|
||||||||
CH2=CH—CH2—O—C |
|
|
|
|
|
|
|
|
|
|
|
||||||||||
|
|
|
|
|
- ROAc |
|
|
|
|
|
|
|
|||||||||
|
+ HOH |
|
|
|
|
|
|
|
|
|
|
|
|
||||||||
|
|
|
|
|
|
|
|
|
|
|
|
|
|
|
|
|
|
|
|
||
|
- CH3COOH CH3 |
|
|
|
|
|
|
|
|
|
|
|
|
|
|
|
|
||||
|
|
|
|
|
|
|
|
|
|
|
|
(H2) |
|
|
|||||||
CH2=CH—CH2—OH |
II |
(CO, H2) |
|
|
|
|
|
|
|
|
|
||||||||||
|
|
|
|
|
|||||||||||||||||
|
|
|
|
|
|
|
|
OH |
|
||||||||||||
|
|
|
|
|
|
|
O |
|
|
||||||||||||
|
|
|
|
|
|
|
|
|
|
|
|
|
|
|
|
CH2—CH2—CH2—CH2 |
|||||
|
|
III(CO, H2) |
|
|
|
|
|
|
|
|
|
|
|
|
|||||||
|
|
|
|
|
|
|
|
|
|
|
|
|
|
|
|
|
|
|
OH |
OH |
|
|
|
IV |
|
|
|
|
|
|
|
|
|
|
|
|
|
|
|
|
|
|
|
|
|
|
|
|
|
|
|
|
|
|
|
O |
|
|
(H2) |
|
|||||
|
|
|
|
|
|
|
|
|
|
|
|
|
|
|
|||||||
|
|
|
|
|
|
|
|
|
|
|
|
|
|
|
|||||||
|
|
(CO, Н2) |
|
|
|
|
|
|
O |
|
|
|
|
|
|
|
При этом используются различные каталитические системы:
I – ацетилацетонат родия Rh(АсАс)2(СО)2 в смеси с алкоголятом натрия NаОR (эта система позволяет осуществить в мягких условиях гидрофор-
милирование аллилацетата - в спиртовой среде - в 2-окситетрагидрофуран);
II – ацетилацетонат родия или трихлорид родия, модифицированные трифенилфосфином или этриолфосфитом;
III – ацетилацетанат родия Rh(АсАс)2(СО)2 + А1(АсАс)3;
IV - трихлорид родия RhС13, модифицированный полиэтиленимином.

398
10.9.4. Получение 1,4-дигидроксиметилциклогексана
Дигидроксиметилциклогексан применяют в производстве полиэфирных волокон, ненасыщенных полиэфиров и высококачественных покрытий, а также при синтезе некоторых полиуретанов. Однако его промышленное значение гораздо меньше, чем значение этиленгликоля и бутандиола.
Фирма "Тенесси Истман" осуществила промышленное производство 1,4- дигидроксиметилциклогексана из диметилтерефталата. Восстановление диметилтерефталата протекает в две стадии:
|
|
|
|
COOCH3 |
|
|
|
|
|
|
|
COOCH3 |
||||
|
|
|
|
|
|
+ 3H2 |
|
|
|
|
|
|||||
|
|
|
|
|
|
|
|
|
|
|
||||||
|
|
|
|
|
|
|||||||||||
|
|
|
|
|
|
|
COOCH3 |
|||||||||
|
|
|
|
|
|
|
|
|
|
|
|
|
|
|
||
|
|
|
|
|
|
|
|
|
|
|
|
|
|
|
||
|
|
|
|
|
|
|
|
|
|
|
|
|
|
|||
|
|
|
COOCH3 |
|||||||||||||
|
|
|
|
|
|
|
|
|
|
|
|
|
|
|||
|
COOCH3 |
|
|
CH2OH |
||||||||||||
|
|
|
+ 4H2 |
|
|
|
|
|
|
|
+ 2CH3OH. |
|||||
|
|
|
|
|
|
|
|
|
|
|||||||
|
|
|
|
|
|
|
|
|
|
|||||||
|
|
|
|
|
|
|
|
|
|
|||||||
|
COOCH3 |
|
|
|
CH2OH |
|||||||||||
|
|
|
Реакцию проводят при 433-453 К под давлением 30-40 МПа в присутствии палладия на носителе. Селективность по насыщенному эфиру превышает 95%. Далее полупродукт направляют в реактор гидрогенолиза, в котором в присутствии хромита меди он превращается в дигидроксиметилциклогексан и метанол. Дигидроксиметилциклогексан содержит ~ 33% цис- и ~76% транс- изомера.
399
Глава 11
МОНОМЕРЫ ДЛЯ ПОЛИАМИДОВ
Полиамиды – высокомолекулярные гетероцепные соединения, содержащие в основной цепи макромолекулы повторяющиеся амидные группы
–СО-NН–. К полиамидам относят продукты поликонденсации аминокислот или диаминов с дикарбоновыми кислотами или их хлорангидридами. Вместо поликонденсации аминокислот часто проводят полимеризацию их лактамов.Карбоцепные полиамиды с боковыми амидными группами, например полиакриламид, обычно к полиамидам не относят.
В настоящее время приняты цифровые обозначения полиамидов. Если полиамид синтезирован из аминокислоты или лактама, то цифра после слова «полиамид» обозначает число атомов углерода в звене полимера между амидными группами, включая карбонильный атом. Если полиамид получен поликонденсацией диамина с дикарбоновой кислотой, то ставятся две цифры. Первая цифра после названия обозначает число атомов углерода в исходном диамине, вторая – число атомов углерода в дикарбоновой кислоте. В случае полиамидов, содержащих циклические звенья, иногда в названии используются буквенные обозначения. Например, название "полиамид-6Т" обозначает полиамид на основе гексаметилендиамина и тетрагидрофуран-2,5-дипропионовой кислоты.
Благодаря высокой кристалличности, износостойкости, низкому коэффициенту трения, коррозионной стойкости, хорошим электроизоляционным свойствам полиамиды нашли широкое применение в самых различных областях. Их используют для изготовления волокон и тканей, а также в технических целях для изготовления роликов, опор трения, различных вращающихся деталей, например лопастей вентиляторов пропеллеров и крыльчаток насосов, разъемных корпусов промышленных станков, бытовых приборов и т.д. Но самое главное их применение – это выработка синтетических волокон и тканей.
Впервые один из наиболее известных полиамидов – полиамид-6,6 ( полигексаметиленадипинамид, найлон-6,6) - был синтезирован У. Карозерсом в 1934 г. (фирма "Дюпон"). В 1939 г. на Всемирной выставке в Нью-Йорке и Чикагской ярмарке были впервые продемонстрированы женские чулки, изготовленные из нового полимера.
Ниже приведены наиболее распространенные полиамиды и соответствующие мономеры, из которых они получаются.
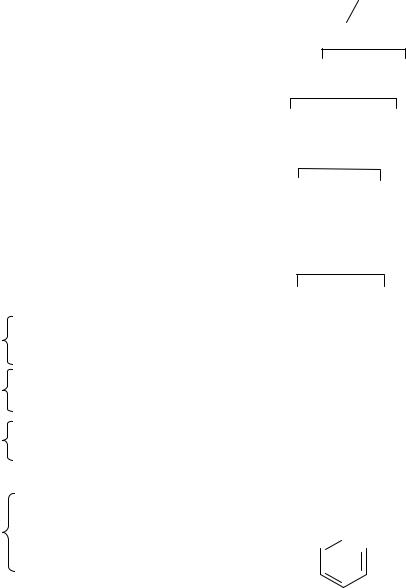