
monomers-Платэ-книга
.pdf
361
В промышленности реализованы и другие процессы получения ТФК окислением п-ксилола: способы фирм "Тейчжин", "Мобил", "Истман Кодак", "Марузен", "Мицубиси Кемикал", "Мицуи Петрокемикал". Эти процессы во многом аналогичны друг другу, но имеют свои "ноу-хау".
10.1.4.Одностадийный процесс ВНИПИМ
Вначале 70-х годов в Советском Союзе специалистами Всесоюзного на- учно-исследовательского и проектного института мономеров (ВНИПИМ, г. Тула) был разработан способ получения чистой ТФК, основанный на жидкофазном окислении п-ксилола и очистке технического продукта доокислением примесей перманганатом калия. В оптимальном технологическом режиме получа-
ют ТФК с содержанием п- карбоксибензальдегида не более 0,03% (мас.), п- толуиловой кислоты – не более 0,005% (мас.) и цветностью – не более 10о Н.
Промышленная установка включает узлы окисления п-ксилола и сушки ТФК, регенерации уксусной кислоты и катализатора.
10.1.5. Получение ароматических и гетероциклических карбоновых
кислот путем термического превращения их щелочных солей
Способность щелочных солей бензойной кислоты к термическому превращению с образованием тере- и изофталатов была открыта Рихтером и Конрадом более 100 лет назад. Однако интерес к этим реакциям появился лишь в 50-х годах ХХ столетия, благодаря работам Рекке, в которых была показана возможность их практического использования для получения терефталевой и других дикарбоновых кислот из доступных продуктов нефте- и коксохимии.
Первоначально предполагалось, что образование терефталатов из бензоата и фталатов происходит в результате простого перемещения карбоксигруппы от одной молекулы к другой либо вследствие внутримолекулярных превращений - диспропорционирования (1) или изомеризации (2):
2С6Н5СО2К |
С6Н6 + п-С6Н4(СО2К)2 , |
(1) |
о-, м-С6Н4(СО2К)2 |
п-С6Н4(СО2К)2 . |
(2) |
Впоследствии было обнаружено, что приведенные уравнения описывают начальное и конечное состояние лишь одной из стадий сложного процесса пиролитического превращения щелочных солей ароматических и гетероциклических карбоновых кислот.

362
Превращения щелочных солей
Направления термического превращения щелочных солей могут быть представлены следующим образом:
A(CO2M)2
↓ xx -CO2, -CO, -AH ПК-CO2, -CO, -H2 ГК, A(CO2M)2
где А- ароматический или гетероциклический цикл,СО2М – карбоксилатная группа,значок хх означает наиболее термически устойчивый изомер,ПК – первичные продукты конденсации,ГК – продукт глубокой конденсации.
Состав продуктов превращения щелочных солей ароматических и гетероциклических карбоновых кислот определяется условиями реакции. На рис. 10.2 представлены результаты исследования термического превращения калиевых солей бензойной, тиофен-2- и нафталин-2-карбоновых кислот.
Рис. 10.2. Термические превращения калиевых солей бензойной (а), тиофен- 2- (б) и нафталин-2-карбоновых (в) кислот
1 - бензоат калия; 2 - тиофен-2-карбоксилат калия; 3 - нафталин-2- карбоксилат калия; 4 - бензол; 5 - тиофен; 6 - нафталин; 7 - орто- и изофталаты; 8 - терефталат; 9 - тиофен-2,5-дикарбоксилат; 10 - нафталин-2,6- дикарбоксилат; 11 –СО2; 12 -СО; 13 - тяжелый остаток (в % (мас.))
Скорость нагревания соли 6-8 град/мин, газовая среда - гелий.
На первой стадии происходит выделение небольшого количества диоксида углерода, затем преимущественно протекают реакции карбоксилатного обмена с образованием смеси солей поликарбоновых кислот и образованием углеводородов: из бензоата - бензола, из тиофен- и нафталинмонокарбоксилатов – тиофена и нафталина. Высокий выход соли целевой дикарбоновой кислоты обусловливается хорошей способностью реагирующих веществ к карбокси-
латному обмену и устойчивостью промежуточных и конечных продуктов к термическому разложению.
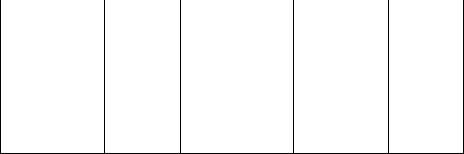
363
Из щелочных солей бензойной кислоты в наибольшей степени этому требованию отвечает калиевая соль, натриевая занимает промежуточное положение между литиевыми и калиевыми солями.
Температуры начала превращения и значения кажущейся энергии активации солей бензойной кислоты коррелируют с величинами потенциала ионизации щелочных металлов, образующих соль (табл. 10.1).
Таблица 10.1
Сравнение температур начала превращения (Тнп)
и кажущейся энергии активации (Еакт) бензоатов металлов (БМ) нафталин-1,8-дикарбоксилатов металлов (1,8-НДКМ)
с потенциалами ионизации (Пи)
Щелочной |
БМ |
1,8-НДКМ |
Еакт, |
|
|
кДж/моль |
Пи, эВ |
||||
металл |
|
|
|||
Тнп, К |
Тнп, К |
||||
|
|
||||
|
|
|
|||
|
|
|
|
|
|
Литий |
723 |
736 |
374,2 |
5,39 |
|
|
|||||
|
|
|
|
|
|
Натрий |
711 |
676 |
343,4 |
5,14 |
|
Калий |
691 |
651 |
236,7 |
4,34 |
|
Цезий |
593 |
568 |
207,0 |
3,89 |
С увеличением ковалентного характера связи О-М в структуре
О
║
R—С—О—М
протекание карбоксилатного обмена затрудняется, а с увеличением ионного характера – облегчается.
Катализаторы термического превращения щелочных солей. В от-
сутствие катализаторов обмен карбоксилатными группами протекает с небольшой скоростью и с невысоким выходом целевых дикарбоновых кислот. Использование катализаторов ускоряет этот процесс и приводит к увеличению выхода бензол-1,4-, нафталин-2,6- и тиофен-2,5-дикарбоксилатов. Наиболее каталитически активными являются соединения кадмия и цинка; менее активны
соединения стронция, бария, магния, марганца, меди, железа, алюминия, ртути, циркония и др. Каталитическая активность зависит от природы аниона и уменьшается в ряду:йодид > бромид > хлорид > карбонат.
Иногда в качестве катализаторов применяют сплавы двух, трех, четырех металлов: кадмия и цинка, цинка и железа, кадмия, висмута, олова и свинца (сплав Вуда).
Синтез терефталевой кислоты из толуола и о-ксилола
Бόльшая часть ТФК или ее диметилового эфира получается окислением п-ксилола. Применение для производства этой кислоты технологий, основанных на термическом превращении бензолкарбоновых кислот, позволило
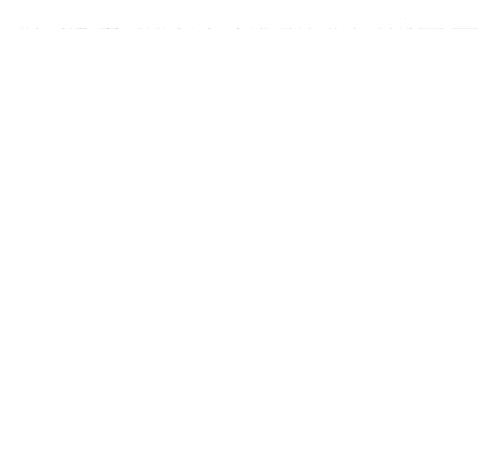
364
значительно расширить сырьевую базу для синтеза этой кислоты. В этом случае источником сырья могут служить толуол, индивидуальные о- и м-ксилолы или смесь ксилолов (без их предварительного разделения).
Процесс получения ТФК из толуола и ксилолов с использованием реакций термического превращения щелочных солей бензолкарбоновых кислот включает две основные стадии: окисление толуола или ксилолов до бензойной, орто-, изо- и терефталевой кислот, а также диспропорционирование и изомеризацию щелочных солей бензойной и фталевых кислот.
Получение терефталевой кислоты из толуола. Процесс получения ТФК из толуола был реализован в Германии во время Второй мировой войны фирмой "Хенкель" и затем использован в Японии фирмой "Мицубиси". Процесс основан на диспропорционировании бензойной кислоты в терефталевую кислоту и бензол:
C6H5CH3 + 1,5O2 C6H5COOH + H2O ,
C6H5COOH + KOH C6H5COOK + H2O ,
2C6H5COOK |
C6H4(COOK)2 + C6H6 , (диспропорционирование) |
C6H4(COOK)2 + H2SO4 C6H4(COOH)2 + K2SO4 .
Принципиальная технологическая схема установки получения ТФК из толуола фирмы "Мицубиси" представлена на рис. 10.3.
Окисление толуола протекает в жидкой фазе в присутствии растворимого катализатора на основе кобальта. Далее, нейтрализуя образовавшуюся бензойную кислоту едким кали, получают бензоат калия, который отделяют центрифугированием. Диспропорционирование бензоата калия проходит при 673-703 К под давлением СО2 1,5-3 МПа в присутствии оксидов кадмия или цинка в кач
естве катализатора. Реакция протекает в твердой фазе. ТФК получают обработкой ее соли серной кислотой.
Рис. 10.3. Принципиальная технологическая схема получения ТФК фирмы "Мицубиси Кемикал" (процесс "Хенкель-II")
1 - реактор окисления; 2 - аппарат получения бензоата; 3 - центрифуги; 4 - аппарат смешения и сушки; 5 - реактор для термической перегруппировки; 6-9
– система выделения ТФК.
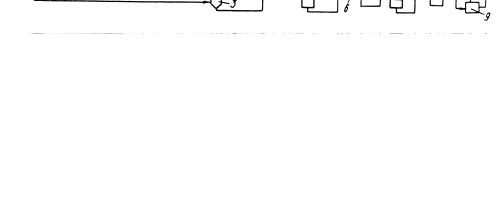
365
Потоки: I - толуол; II - катализатор окисления; III - окисляющий газ; IV - бензойная кислота; V - KOH; VI - бензоат калия; VII - СО2; VIII - бензол; IX - вода; X - катализаторный шлам; XI - H2SO4; XII - сульфат калия и примеси; XIII - растворитель; XIV - ТФК
Недостатками процесса являются трудности, связанные с частым закупориванием установки из-за того, что реакция протекает в твердой фазе, а также образование большого количества сульфата калия, низкие селективность и скорость реакции.
В Советском Союзе была разработан процесс диспропорционирования щелочных солей на примере бензоата калия, схема которого приведена на рис. 10.4.
Порошкообразная или гранулированная смесь сырья и катализатора подается непрерывным потоком на транспортерную жаропрочную стальную ленту, заключенную в цилиндрический корпус, рассчитанный для работы под повышенным давлением углекислого газа. Сырье перемещается через обогреваемую электронагревателями реакционную зону. На выходе из зоны реакции твердые продукты измельчаются и выводятся из системы методом шлюзования. При 698-743 К, давлении СО2 1,0 МПа, времени реакции 8-25 мин, содержании оксида кадмия в сырье от 3 до 5% степень превращения бензоата калия может составлять 81-92%, а выход дикалийтерефталата в расчете на превращенное сырье достигает 85-90% (мас.) от теоретически возможного.
Рис. 10.4. Установка термического превращения щелочных солей ароматических и гетероциклических карбоновых кислот
1а - ленточный реактор; 1б - шахтный реактор с механической мешалкой; 2 - бункеры узлов загрузки и выгрузки; 3 - емкость для растворения
реакционной смеси; 4 - отстойник; 5 - фильтр; |
6 - емкость- |
|
кристаллизатор; 7 - колонна отгонки ацетона; |
8 - выпарная колон- |
|
на; 9 - аппарат сушки; 10 - газосепаратор; |
11 - абсорбер; 12 - десорбер; |
|
13 - циркуляционной компрессор. |
|
|
Потоки: I - исходная соль; II - катализатор; III - твердый разбавитель; IV - продукт перегруппировки; V - вода; VI - катализаторный шлам; VII - ацетон; VIII - дикалиевая соль дикарбоновой кислоты; IX - поглотительное масло; X - бензол, тиофен или нафталин; XI - СО2
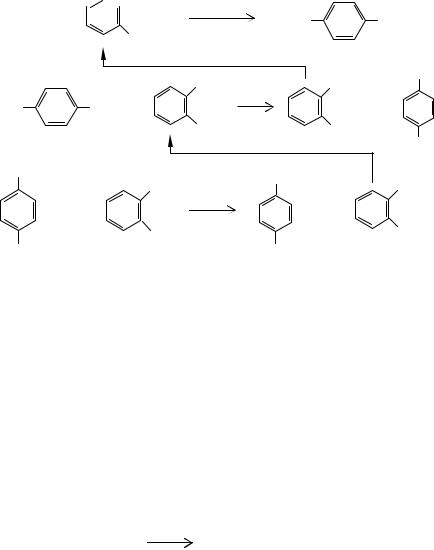
367
Реакция протекает при температуре 273 К и 1,5 МПа в присутствии трифторида бора и фтористоводородной кислоты в количестве 1 моль ВF3 и 5 моль НF на 1 моль толуола. В начальный период при низкой температуре (248 К) образуется комплекс толуол-НВF4. На образование этого комплекса расходуется около половины BF3. Далее смесь подогревают до 273 К для образования комплекса п-толуиловый альдегид-НВF4. Затем добавляют остальное количество ВF3 и завершают реакцию. В качестве побочного продукта образуется небольшое количество о-толуилового альдегида. Конверсия толуола за один проход составляет ~ 90% при селективности по п-толуиловому альдегиду 98% и о- толуиловому альдегиду 2%. мета-Изомер не образуется.
Комплекс п-толуилового альдегида и НВF4 разлагается при нагревании до 403-453 К в присутствии растворителя – бензола. Далее выделяют ВF3, Н2 и непревращенный толуол; о- и п-толуиловые альдегиды разделяют кристаллизацией.
Очищенный п-толуиловый альдегид окисляют воздухом в растворе уксусной кислоты в присутствии ацетата марганца, ацетата кобальта и бромида натрия по технологии, используемой при синтезе терефталевой кислоты из п- ксилола.
СН3С6Н4СНО+ 2О2 НООСС6Н4СООН + Н2О.
Реакция протекает при 473 К и 2 МПа.
10.1.7. Получение терефталевой кислоты из угля
Битуминозные угли с отношением С:Н2, равным 0,8, вследствие их высокой ароматичности являются перспективным источником производства бензолкарбоновых кислот, получаемых окислительным крекингом. В присутствии калиевых солей эти ароматические кислоты в основном превращаются в дикислоты, преимущественно, с пара-расположением карбоксильных групп.
Процесс, предложенный фирмой "Оксидентал Рисерч" (США), состоит в окислении битуминозного угля в присутствии ацетата калия и воды в соотношении (1:3)-(3:10) кислородом при 533 К под давлением 10 МПа и времени пребывания реакционной массы в реакторе 30 мин. Образующийся СО2 непрерывно удаляется и заменяется кислородом. Выходящий из реактора поток отделяется от уксусной кислоты и смешивается с иодидом кадмия в количестве 6% (мас.) от загрузки угля. Далее смесь подогревают до 673 К в присутствии СО2 под давлением 4,0 Мпа, время контакта 2,5 ч. При этом происходит изомеризация орто-кислоты в пара-кислоту и диспропорционирование монокарбоновых кислот в дикарбоновые. После разделения выход ТФК составляет 34% (мас.) по отношению к исходному углю.
Процесс недостаточно селективен по ТФК и представляет интерес лишь как перспектива на будущее.

368
10.2. МАЛЕИНОВЫЙ АНГИДРИД
Малеиновый ангидрид (ангидрид цис-этилен-1,2-дикарбоновой кислоты) O
С — СO
CH—C
O
представляет собой бесцветные кристаллы с ромбической решеткой, т. пл. 325,85 К, т. кип. 475 К. Растворяется в воде с образованием малеиновой кислоты, а также в ацетоне, бензоле, толуоле, хлороформе и др.
Малеиновый ангидрид как мономер широко используют в производстве ненасыщенных полиэфиров. Именно спрос на отверждающиеся полиэфирные полимеры обусловливает в основном развитие производства малеинового ангидрида. Крупным потребителем малеинового ангидрида является также производство алкидных олигомеров. Применение малеинового ангидрида позволяет создавать поверхностные алкидные покрытия с повышенной ударной вязкостью. Кроме того, малеиновый ангидрид используется в производстве тетрагидрофурана, -бутиролактона, армированных пластиков, химикатов для сельского хозяйства.
В 1970 г. 90% всего малеинового ангидрида производилось из бензола, остальная часть – преимущественно из бутан-бутиленовой фракции разгонки нефти. К 1980 г. доля производства малеинового ангидрида из бензола снизилась до 81,3%. В промышленном производстве кроме бутан-бутановой фракции использовался и чистый бутан. В последующие годы эта тенденция сохранилась.
Основными причинами сокращения производства малеинового ангидрида из бензола явились как дефицит бензола, его канцерогенные свойства, так и рост цен на бензол.
В основе технологии производства малеинового ангидрида лежат процессы газофазного окисления бензола, н-бутана или н-бутенов. Его получают также как побочный продукт при производстве фталевого ангидрида. Все процессы окисления характеризуются сильной экзотермичностью, что вызывает необходимость отвода большого количества тепла, как правило, в виде пара.
10.2.1. Получение малеинового ангидрида окислением бензола в газовой фазе
Первый завод по производству малеинового ангидрида газофазным окислением бензола по способу, разработанному фирмами "Халкон" и "Сайентифик
дизайн"(США), был пущен во Франции в 1957 г. В странах Запада свыше всех мощностей по производству малеинового ангидрида из бензола исполь-
зовали этот метод.
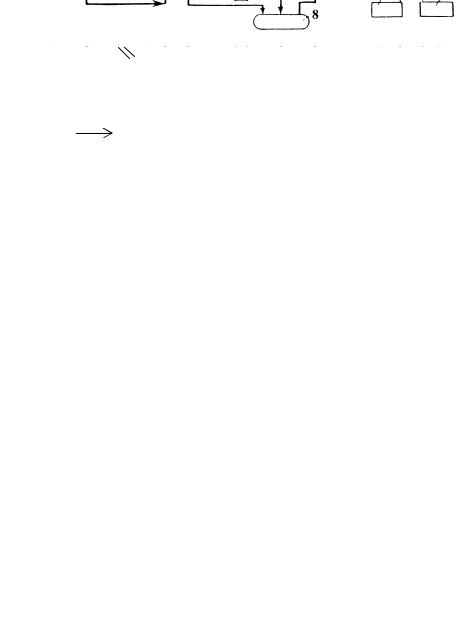
369
Процесс окисления бензола описывается следующими уравнениями: O
C6H6 |
+ 4O2 |
CH—C |
O + CO2 |
+ CO + 2H2O |
H298 = -1470 кДж/моль |
|||
|
|
|
||||||
CH—C |
||||||||
|
|
|
|
|
||||
|
|
|
|
O |
|
|
|
|
|
C6H6 + 6O2 |
3CO2 + 3CO + 3H2O |
H298 = -2320 кДж/моль. |
В процессе окисления концентрация бензола в исходной воздушной смеси не должна находиться в зоне концентраций, лежащих в области пределов взрываемости, т.е. в интервале 1,4-7,1% (об.) при 298 К. Процесс осуществляют в интервале 1,2-1,3 %, т.е. ниже этого предела.
Основу практически всех катализаторов окисления бензола в малеиновый ангидрид составляют пентаоксид ванадия и оксид молибдена, нанесенные на оксид алюминия. Катализатор содержит также пентаоксид фосфора для стабилизации.
Реакцию проводят при 623-723 К и давлении 0,1-0,2 МПа в паровой фазе на стационарном слое катализатора при массовом соотношении бензол : воздух, равном 1:30, что соответствует объемной концентрации бензола 1,2%. Принципиальная технологическая схема процесса фирмы "Сайентифик дизайн" приведена на рис. 10.5.
Рис. 10.5. Технологическая схема получения малеинового ангидрида фирмы "Сайнтифик дизайн"
1 - теплообменник для подогрева сырья; 2 - холодильник; 3 - котелутилизатор; 4 - реактор; 5 - конденсатор-сепаратор; 6 - водный скруббер; 7 - дегидрататор; 8 - емкость для сырого малеинового ангидрида; 9 - ректификационная колонна; 10-12 - узел получения фумаровой и яблочной кислот.
370
Бензоловоздушная смесь подогревается в теплообменнике 1 до 393-423 К и подается в реактор 4, представляющий собой трубчатый теплообменник. Продукты реакции проходят котел-утилизатор 3, теплообменник 1, который используется для подогрева бензоловоздушной смеси, и холодильник 2.Далее они попадают в конденсатор-сепаратор 5, в котором происходит конденсация большей части малеинового ангидрида. Газы подвергают мокрой очистке в водном скруббере 6. Раствор малеиновой кислоты доводится в скруббере до концентрации 40% (мас.), затем подается на дегидратацию и выделение ангид- рида-сырца.
В технологической схеме имеется узел изомеризации малеиновой кислоты в фумаровую.
Степень конверсии бензола за один проход составляет 95%, а селективность по малеиновому ангидриду - 67%, что соответствует выходу за проход
64%.
Процессы окисления бензола до малеинового ангидрида, разработанные другими фирмами ("Лурги", "Байер", "Такеда Якухин", "Ниппон Шокубай"и др.), отличаются от рассмотренного процесса в основном технологией выделения и очистки малеинового ангидрида.
10.2.2. Получение малеинового ангидрида окислением бутана
Первая промышленная установка окисления н-бутана в малеиновый ангидрид была построена "Монсанто" в 1974 г. Впоследствии фирмы "Амоко", "Эшленд", "Денка Кемикал", "Байер и Хюльс", а затем "Шеврон", "Мобил Ойл", "Петротекс", "Стандард Ойл" также освоили промышленный процесс получения малеинового ангидрида, базирующийся на окислении н-бутана. Окисление н-бутана осуществляют в газовой фазе в (трубчатом реакторе) на неподвижном слое катализатора, созданного на основе соединений ванадия, железа и фосфора, нанесенных на алюмосиликат. Соотношение количеств ванадия и фосфора варьируется в широких пределах, но оптимальным является соотношение V:Р, равное 1: (1-1,2). В качестве промоторов применяют цинк, цирконий, кобальт, титан, кремний. Эффективность катализаторов существенно возрастает при приготовлении их из неводных сред, в частности при использовании пропилового, бутилового и изобутилового спирта, тетрагидрофурана. Применение органических растворителей улучшает структурные характеристики катализаторов, в первую очередь увеличивает их удельную поверхность, что приводит к увеличению их активности.
Важным условием хорошей работы катализатора является степень окисления в нем ванадия, которая должно лежать в интервале +4,1 – +4,6. Такое со стояние ванадия достигается контролируемой обработкой катализатора при высокой температуре восстанавливающим агентом, например водородом,
метаном, сероводородом, сероуглеродом.