
monomers-Платэ-книга
.pdf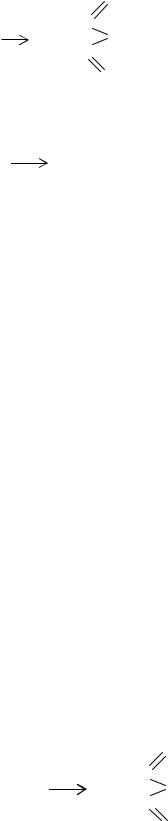
371
Окисление н-бутана происходит в соответствии со схемой:
|
|
|
|
|
|
O |
|
|
C4H10 + 3,5O2 |
|
|
|
|
CH—C |
O + 4H2O |
H298 = -1240 кДж/моль |
|
|
|
|||||||
CH—C |
||||||||
|
|
|
||||||
|
|
|
|
|
|
O |
|
Основная реакция сопровождается побочной реакцией горения сырья:
C4H10 + 5,5O2 |
2CO2 + 2CO + 5H2O |
H298 = -2090 кДж/моль |
Одним из преимуществ использования в качестве сырья бутана является то обстоятельство, что число атомов углерода в бутане и малеиновом ангидриде совпадает, тогда как в случае бензола дополнительно образуются два моля СО2, хотя окисление углеводородов С4 протекает с меньшей селективностью и с образованием большего количества продуктов. Тепловой эффект реакции окисления бутана в малеиновый ангидрид ниже, чем при окислении бензола, но суммарное тепловыделение в процессе остается значительным за счет сгорания побочных продуктов реакции до СО и СО2.
Условия окисления бензола и бутана различаются мало и поэтому реконструкция установок для перехода от бензола к бутану является минимальной. Различия касаются стадии выделения малеинового альдегида и связаны в основном с существенно большей концентрацией воды в реакционной смеси в случае окисления бутана.
10.2.3.Получение малеинового ангидрида окислением н-бутенов
Вначале 50-х годов фирма "Петротекс" (США) осуществила промышленное производство малеинового ангидрида окислением н-бутена. В дальнейшем этот процесс получил распространение в Западной Европе и Японии. В ка-
честве сырья в процессе используют фракцию С4 пиролиза нафты, освобожденную от бутадиена и изобутена и содержащую ~90% бутена-1 и цис- и транс- бутенов-2 и ~10% бутана. В качестве катализатора применяют смесь оксидов молибдена, ванадия и фосфора.
Окисление бутенов осуществляется в соответствии со схемой
|
|
|
|
|
|
O |
|
CH3CH2-CH=CH2 + 3O2 |
|
|
|
|
CH—C |
O + 3H2O H298 = -1130 кДж/моль |
|
|
|
||||||
CH—C |
|||||||
|
|
||||||
|
|
|
|
|
|
O |

372
и сопровождается реакцией горения бутена:
CH3CH2-CH=CH2 + 5O2 2CO2 + 2CO + 4H2O H298 = -1980 кДж/моль.
Кроме этих продуктов образются также различные кислородсодержащие соединения: масляный и кротоновый альдегиды, пропионовая, уксусная, акриловая кислоты и др.
Условия окисления бутена близки к условиям окисления бензола. Реакцию проводят при 633-713 К с селективностью по малеиновому ангидриду ~ 50% в расчете на бутены.
Фирма "Мицубиси" осуществила промышленное производство малеинового ангидрида окислением бутенов в реакторе с "кипящим слоем" катализатора, по составу сходного с катализатором в стационарном слое. Основным преимуществом процесса в "кипящем слое" катализатора является легкость отвода тепла при осуществлении сильноэкзотермических реакций.
10.2.4. Выделение малеинового ангидрида как побочного продукта в производстве фталевого ангидрида
Производство фталевого ангидрида окислением нафталина или о-ксилола сопровождается образованием 5-6% малеинового ангидрида, который может быть выделен из оборотной воды. Предварительно воду упаривают до содержания малеинового ангидрида 15-20%. Около 10% производимого в Западной Европе малеинового ангидрида вырабатывается по этой схеме.
10.3. ФТАЛЕВЫЙ АНГИДРИД
Фталевый ангидрид (ангидрид бензол-1,2-дикарбоновой кислоты) представляет собой бесцветные орторомбические кристаллы, т. пл. 403,85 К, т. кип. 567,5 К, растворимые в муравьиной кислоте, пиридине, сероуглероде, воде и др.
O
СС
O
O
Фталевый ангидрид широко используют в производстве пластических масс, лаков, а также красок, лекарственных препаратов, красителей.
В промышленности фталевый ангидрид получают пароили жидкофазным окислением кислородом воздуха о-ксилола или нафталина в стационарном
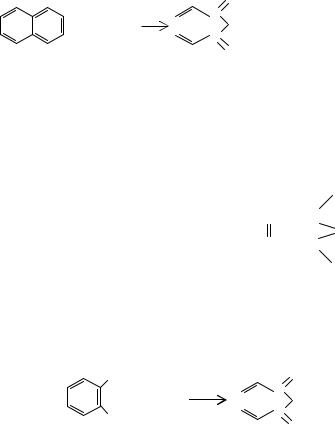
373
или "кипящем слое" катализатора. Нафталин в качестве сырья для получения фталевого ангидрида применяли в основном до конца Второй мировой войны. В дальнейшем он был вытеснен о-ксилолом, который в достаточных количествах содержится в нефтяных фракциях.
В середине 1960-х годов появление "нефтехимического" нафталина вновь вызвало интерес к нему как сырью для производства фталевого ангидрида, ~ 80% которого получали из нафталина. Около половины этого количества поставляли нефтехимические производства. В настоящее время доля о-ксилола в сырьевом балансе промышленного производства фталевого ангидрида составляет 70-95% и зависит от уровня развития коксо- и нефтехимической промышленности страны.
Процессы окисления нафталина и о-ксилола описываются следующими реакциями.
Окисление нафталина:
|
|
|
|
|
|
С |
O |
+ 4,5O2 |
|
|
|
|
|
O + 2CO2 + 2H2O H298 = -1790 кДж/моль |
|
|
|
|
|||||
|
|
|
|
|
|
С |
O |
|
|
|
|
|
|
||
|
|
|
|
|
|
|
Побочные реакции:
C10H8 + 12O2 10CO2 + 4H2O,
O
CH—C
C10H8 + 9O2 CH—C O + 6CO2+ 3H2O.
O
Окисление о-ксилола:
CH3 |
|
С |
O |
|
||||
|
|
|
||||||
+ 3O2 |
|
|
|
|
|
O |
+ 3H2O H298 = -1780 кДж/моль. |
|
|
|
|
||||||
CH3 |
|
С |
O |
|
||||
|
|
|
|
|
|
|
|
Окисление о-ксилола также сопровождается реакциями образования малеинового ангидрида и полного сгорания сырья. Все реакции окисления сильно экзотермичны.
374
10.3.1. Парофазное окисление о-ксилола или нафталина
Окисление исходных продуктов может проводиться в неподвижном слое катализатора, в трубчатых реакторах, имеющих несколько тысяч трубок. Отвод тепла осуществляется жидким теплоносителем - расплавом солей (нитритнитрат) или эвтектической смесью натрия и калия.
В качестве катализаторов окисления используют пентаоксид ванадия и диоксид титана (анатаз), имеющие селективность действия 77-83% (мол.). В промышленности применяют катализаторы с большим содержанием пентаоксида ванадия (фирмы "Фон Хейден" и "Вакер хеми") и катализаторы, содержащие до 10% пентаоксида ванадия (фирма БАСФ). В качестве стабилизирующего агента используют фосфор.
Окисление проводят при 623-673 К избытком кислорода воздуха при мольном отношении воздух : углеводород между 60 и 120, т.е. ниже нижнего предела области воспламенения.
При производстве фталевого ангидрида образуется большое количество газов. Основным методом выделения фталевого ангидрида является десублимация, осуществляемая в теплообменниках с ребристыми трубами, обтекаемыми в поперечном направлении газовой смесью. Таким образом удается собрать 99,5% фталевого ангидрида, находящегося в реакционном потоке.
Сырой фталевый ангидрид содержит различные кислоты: фталевую, малеиновую, бензойную. Целевой продукт выделяют дистилляцией под вакуумом.
Выход фталевого ангидрида при окислении о-ксилола составляет 75-80%, а при окислении нафталина – 85-88%.
При окислении до фталевого ангидрида (процесс "Шервин-Вильямс" нафталин переводится в жидкое состояние, испаряется и вводится в реактор на слой разогретого катализатора. Окисление нафталина кислородом воздуха проводят при 613-658 К. В качестве катализатора применяют оксид ванадия, нанесенный на силикагель.
Недостатками парофазных способов являются их взрывоопасность и необходимость работы с большим избытком воздуха, что снижает эффективность использования реакционного объема и создает большие трудности при выделении фталевого ангидрида из реакционной смеси. Проведение же процесса окисления в паровой фазе при высокой температуре (723 К) приводит к сгоранию значительной части сырья и превращению его в побочные продукты, т.е. к снижению выхода целевого продукта и усложнению очистки ангидрида-сырца от примесей.
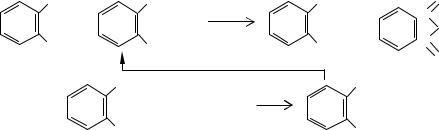
375
10.3.2.Жидкофазное окисление о-ксилола или нафталина
Вконце 1960-х годов в ФРГ был разработан способ получения фталевого ангидрида окислением о-ксилола в растворе уксусной кислоты в присутствии кобальтмарганцевых катализаторов, промотированных соединениями брома. Выход фталевого ангидрида составляет 85%. Однако из-за трудностей в подборе материалов для реактора и холодильников, стойких к парам уксусной кислоты и соединениям брома при высокой температуре, этот процесс не получил широкого распространения.
10.3.3. Процесс ВНИИОС
Этот процесс получения фталевого ангидрида окислением о-ксилола в жидкой фазе лишен недостатков парофазного и рассмотренного жидкофазного способов. Он обеспечивает селективность по фталевому ангидриду свыше 90%.
Процесс ВНИИОС состоит в совместном каталитическом окислении о- ксилола и метилового эфира о-толуиловой кислоты (о-метилтолуиат) кислородом воздуха под давлением. Образующийся при окислении о-метилтолуилата метиловый эфир о-фталевой кислоты при 463 К практически количественно распадается на фталевый ангидрид и метанол. Получающаяся при окислении о- ксилола о-толуиловая кислота этерифицируется метанолом до о- метилтолуилата, который вновь подается на окисление.
Процесс может быть описан следующими реакциями:
о-Ксилол
CH3 |
COOCH3 |
3O2 |
COOH |
С |
O |
|
O + CH3OH + 2H2O |
||||||
CH3 |
+ |
|
+ |
|||
CH |
|
CH3 |
С |
|
||
|
3 |
|
|
|
O |
|
|
|
|
|
|
||
|
COOH |
|
COOCH3 |
|
|
|
|
+ CH3OH |
CH |
+ H2O |
|||
|
CH3 |
|
|
|
||
|
|
|
3 |
|
|
о-Метилтолуилат
Процесс включает следующие стадии:
-совместное окисление о-ксилола и о-метилтолуилата;
-выделение фталевого ангидрида;
-этерификация о-толуиловой кислоты метанолом.
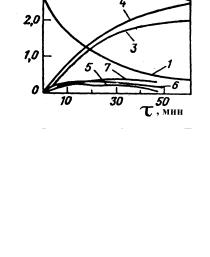
376
Процессы окисления о-ксилола и о-метилтолуилата протекают при одинаковых давлении и концентрации катализатора, близких расходах воздуха и описываются кинетическим уравнением:
ω = kн с1,2
где ω - скорость окисления сырья, моль/л · с); kн – наблюдаемая константа скорости, л/моль· с); с - концентрация сырья, моль/л; 1,2- порядок реакции по сырью.
Совместное окисление о-ксилола и о-метилтолуилата проводят в две стадии. Процесс осуществляют при давлении 1,0 МПа в интервале температур 453473 К. При проведении процесса по непрерывной схеме наилучшие результаты были получены при использовании реактора полного смешения реагирующих веществ. Кинетические кривые, характеризующие изменение состава оксидата при совместном окислении компонентов в оптимальном режиме, представлены на рис. 10.6.
Рис. 10. 6. Зависимость состава оксидата от продолжительности процесса совместного окисления о- ксилола и о-метилтолуилата
Ксилол : эфир = 1:3, 473 К, 1 Мпа 1 - о-ксилол; 2 - о-метилтолуилат; 3 - о-
толуиловая кислота; 4 - фталевый ангидрид; 5 - о- толуиловый альдегид; 6 – альдегидоэфир фталевой кислоты; 7 - фталид
При времени пребывания сырья в зоне реакции 20 мин имели место максимальный выход продуктов и оптимальное соответствие между выходами фталевого ангидрида и о-толуиленовой кислоты.
Степень конверсии о-ксилола в о-толуиловую кислоту составляет 56%, а о-метилтолуилата во фталевый ангидрид - 25%. Суммарный выход целевых продуктов – 98%.
В результате совместного окисления о-ксилола и о-метилтолуилата получают оксидат сложного состава, содержащий непрореагировавший эфир, о- толуиловую кислоту, фталевый ангидрид, фталид и другие продукты. Фталевый ангидрид из этой смеси выделяют методом гидротации его во фталевую кислоту полуторным избытком воды по отношению к реакционной массе при 373378 К и 0,12 МПа. Образующаяся фталевая кислота практически полностью растворяется в горячей воде. При охлаждении водного раствора до 313 К из него выделяют фталевую кислоту, которую при 503 К дегидратируют во фталевый ангидрид чистотой 99,9%.
Синтез метилового эфира о-толуиловой кислоты осуществляют в условиях некаталитической этерификации при сверхкритических для метанола темпе-
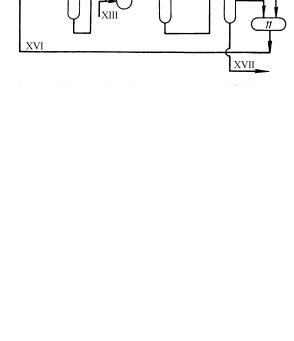
377
ратуре и давлении. В оптимальных условиях при мольном соотношении кислота:метанол, равном 1:10, конверсия кислоты составляет 98% при селективности
100%.
Принципиальная технологическая схема процесса получения фталевого ангидрида жидкофазным окислением о-ксилола представлена на рис.10.7.
Рис. 10.7. Техн. схема получения фталевого ангидрида жидкофазным окислением о-ксилола
1, 11 - емкости; 2 - реактор окисления; 3 - гидрататор; 4 - экстрактор для про-
мывки о-ксилолом; 5 - кристаллизатор; 6 - дегидрататор; |
7, 9, 10 - ректифи- |
||
кационные колонны; 8 - эфиризатор. |
|
|
|
Потоки: I, II - свежий и обедненный воздух; III - о-ксилол; IV - катализатор; |
|||
V - оксидат; VI - эфирный слой; VII - водный слой; |
VIII - ксилольный |
||
слой; IX - вода; X - фталевая кислота; XI - фталевый ангидрид; XII - смесь о- |
|||
ксилола и о-метилтолуилата; XIII, |
XIV - свежий и возвратный метанол; XV - |
||
метилтолуилат; |
XVI - смесь о-метилтолуилата и фталида; XVII - смолы. |
Основные показатели паро- и жидкофазного процессов получения фталевого ангидрида приведены в табл. 10.2.
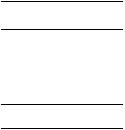
378
Таблица 10.2.
Основные показатели паро- и жидкофазного процессов получения фталевого ангидрида
Показатель |
Парофазный процесс |
Жидкофазный процесс |
|||
|
|
|
|
||
отечественный |
зарубежный |
отечественный |
зарубежный |
||
|
|||||
|
|
|
0,80 |
|
|
Расходный коэффициент |
0,95 |
0,92 |
0,85 |
||
о-ксилола, т/т |
|
|
90 |
|
|
Выход фталевого ангид- |
75 |
75-79 |
85 |
||
рида, % |
|
|
320,5 |
|
|
Электроэнергия, кВт/ч |
750 |
|
|
||
|
|
|
|
|
10.4. ФУМАРОВАЯ КИСЛОТА
Малеиновая (цис-этилен-1,2-дикарбоновая) и фумаровая (транс-этилен- 1,2-дикарбоновая) кислоты
H-C-COOH |
HOOC-C-H |
|||
H- |
|
|
H- |
|
C-COOH |
C-COOH |
|||
Малеиновая кислота |
Фумаровая кислота |
были впервые получены французским химиком Лассенем в 1819 г. дегидратацией яблочной кислоты. В 1919 г. Вейсс и Даунс (фирма "Баррет") показали возможность получения малеинового ангидрида парофазным окислением бензола над пентаоксидом ванадия.
Малеиновую кислоту применяют в производстве отверждающихся полимерных материалов, алкидных смол, винной и яблочной кислот. Фумаровую кислоту используют для получения полиэфиров вместо фталевого ангидрида, синтетических высыхающих масел, как заменитель винной и лимонной кислот.
Малеиновая и фумаровая кислоты по строению являются цис- и трансформами. Обе кислоты при отщеплении воды образуют малеиновый ангидрид.
Фумаровую кислоту получают изомеризацией малеиновой кислоты. Изомеризация проходит в водном растворе при 378 К в присутствии бро-
мида аммония и персульфата аммония или соляной кислоты. Чистую фумаровую кислоту получают охлаждением реакционной массы и сушкой полученных кристаллов.
Малеиновая кислота легко теряет молекулу воды, переходя в ангидридную форму, а фумаровая кислота, в силу своей транс-структуры, теряет воду лишь в жестких условиях.

379
10.5.ДИХЛОРМАЛЕИНОВАЯ И ДИХЛОРМУРОВАЯ КИСЛОТЫ
ИИХ ПРОИЗВОДНЫЕ
Использование хлорзамещенных аналогов малеиновой и фумаровой кислот – дихлормалеиновой кислоты и ее ангидрида, впервые полученных Дж.Чамичаном и П.Зильбером в 1883 г., позволяет получить полиэфиры и сополимеры с качественно новыми свойствами: повышенной огнестойкостью, устойчивостью к агрессивным средам. Так, введение до 10% диалкиловых (С1-С4) эфиров дихлормалеиновой кислоты при полимеризации винилиденхлорида придает высокую пластичность получаемым полимерам. Аллиловые эфиры дихлормалеиновой кислоты (80-95%) при сополимеризации с N- винилпирролидоном (5-20%) образуют синтетические смолы с высокой адгезией к стекловолокну, их применяют для изготовления высококачественных слоистых пластиков.
В состав большинства ударопрочных химически стойких самозатухающих композиций, пригодных для изготовления литых изделий, защитных покрытий, слоистых пластиков, используемых в строительстве, судостроении, автомобилестроении, входят полиэфиры, получаемые конденсацией ангидридов ненасыщенных кислот, в том числе в значительной степени и дихлормалеиновой, с гликолями.
Дихлормалеиновый ангидрид – твердое кристаллическое вещество белого цвета, т. пл. 393 К, т. кип. 403 К.
10.5.1. Получение дихлормалеиновой кислоты и ее ангидрида
Дихлормалеиновая кислота может быть получена непосредственным хлорированием малеинового ангидрида газообразным хлором в присутствии катализаторов хлорирования - порошкообразного железа при 403 К и FеС13 при 453 К с выходом дихлормалеинового ангидрида ~80%:
|
O |
|
|
Cl |
O |
|
O |
H |
Cl2 |
H |
C |
O |
|
H |
|
C |
|
|
O |
||||
|
O |
|
H |
C |
|
|
Cl |
H |
C |
|
|
Cl |
O |
-HCl |
O |
|
|
|
|||||
|
O |
|
|
|
|
|
|
Cl2 |
Cl |
O |
|
Cl |
O |
|
|
|
|||
H |
C |
|
|
|
|
O |
-HCl |
|
O |
||
|
C |
Cl |
|||
Cl |
|
|
|||
O |
|
O |
|||
|
Cl |
|
|
|
|
|
|
|
|
|
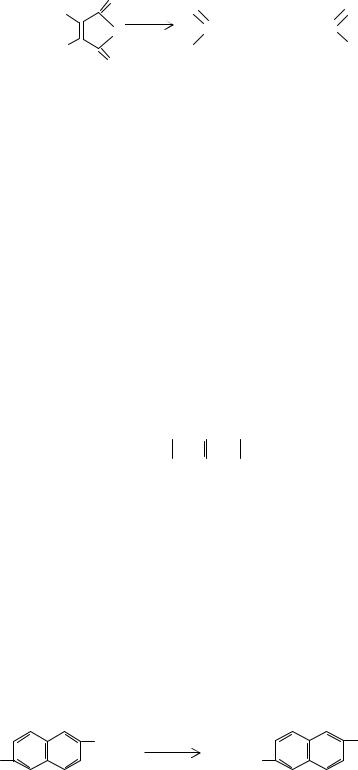