
monomers-Платэ-книга
.pdf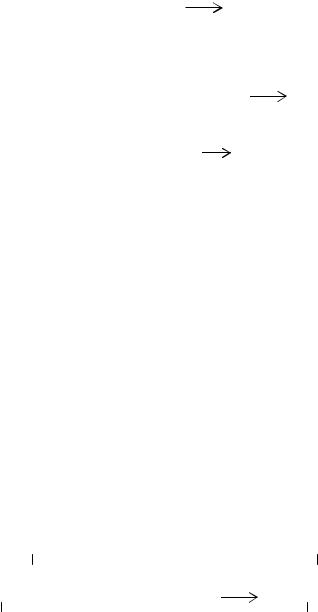
271
|
|
|
|
|
|
|
|
|
|
|
|
|
|
|
|
||||
|
|
(CH3)2C-CN + H2SO4 |
|
|
|
+ |
- |
||||||||||||
|
|
|
(CH3)2C—C=NH HSO4 |
|
|||||||||||||||
|
|
|
|
|
|
OSO3H |
- |
|
|
|
|
|
|
OSO3H |
|
|
|
|
|
|
|
|
|
|
|
|
|
|
|
|
|||||||||
|
|
|
|
|
|
|
|
|
|
|
|
|
|
|
|
|
|||
|
|
+ |
|
|
|
|
|
|
|
|
|
|
|
|
|||||
|
|
|
|
|
|
|
|
|
|
|
|
|
|
||||||
|
(CH3)2 |
|
C—C=NH HSO4 |
+ H2O |
|
|
(CH3)2 |
|
C—CONH2 H2SO4 |
||||||||||
|
|
|
|
||||||||||||||||
|
|
|
|
OSO3H |
|
|
|
|
|
|
|
|
|
|
OSO3H |
||||
|
|
|
|
|
|
|
|
|
|
|
|
|
|
(CH3)2 |
|
C—CONH2 H2SO4 |
CH2 |
|
=C—CONH2 H2SO4 + H2SO4. |
|
|
||||
|
|
OSO3H |
|
CH3 |
Во избежание образования -гидроксиамидов, которые труднее превращают в сульфаты метакриламида, на первой стадии гидролиза используют безводные реагенты. Реакцию проводят в жидкой фазе при атмосферном давлении и температуре 353-383 К в начале реакции с последующим ее повышением до 398-418 К в присутствии 98%-й серной кислоты.
Время пребывания реагентов в зоне реакции 1 ч. В реакционной зоне поддерживается соотношение серная кислота : циангидрин, равное 1,5:2. Выход сульфата метакриламида составляет 95-98%. В качестве побочных продуктов образуются оксид углерода и ацетодисульфокислота.
Спонтанную полимеризацию можно избежать, вводя в реакционную смесь ингибиторы : фенол, фенолтриазин и др.
Гидролиз или этерификация сульфата метакиламида
Гидролиз или этерификацию сульфата метакриламида проводят с применением соответственно воды и спирта – метанола:
CH2=C—CONH2 H2SO4 + H2O CH2=C—COOH + NH4HSO4,
CH3 |
CH3 |
CH2=C—CONH2 H2SO4 + CH3OH |
CH2=C—COOCH3 + NH4HSO4. |
CH3 |
CH3 |
Реакцию осуществляют при 353-383 К и атмосферном давлении в избытке метанола. По другому варианту процесс осуществляют при 373-423 К, под давлением 0,8 МПа, времени пребывания ~ 1 ч в избытке серной кислоты при максимальном содержании воды в реакционной смеси 0,02%. Выход метилметакрилата составляет 90% на ацетонциангидрин и 80-90% - на метанол. Основными побочными продуктами являются диметиловый эфир, метилформиат, ацетон, -изомасляная кислота, метил- -гидроксиизобутират и метил- - метоксиизобутират. В реакционную смесь вводят также ингибиторы полимеризации.
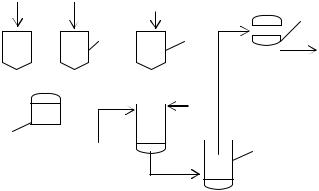
272
Промышленная реализация процесса
Промышленный метод получения метакриловых мономеров был реализован фирмой "АйСиАй", а затем улучшен фирмами "Дюпон", "Ром и Хаас" и др. Большой вклад в модернизацию этого метода внесли фирмы "Асахи", "Мицубиси", "Монтедисон", "Норсолор" и др.
Превращение ацетонциангидрина проводят в две стадии.
На первой - ацетонциангидрин взаимодействует с серной кислотой с образованием метакриламида (см. выше). Процесс осуществляется в серии реакторов с мешалкой при 403-423 К и давлении 0,7-0,8 МПа. Далее реакционную смесь охлаждают до 333 К и дросселируют для выделения оксида углерода, синильной кислоты, ацетона и др.
Затем, на второй стадии, проводят этерификацию амида водным метанолом (во избежание образования диметилового эфира). Побочными продуктами наряду с диметиловым эфиром являются -гидроксиизомасляная кислота и ее эфир, которые получаются при гидролизе и этерификации не полностью дегидратированного ацетонциангидрина.
Принципиальная технологическая схема производства метилметакрилата представлена на рис. 7.5.
Серная кислота из емкости 1 подается в реактор-дегидрататор 4 первой стадии, снабженной мешалкой. Туда же из емкости 2 подают ацетонциангидрин. После полной загрузки ацетонциангидрина реакционную массу нагревают до 398 К для полного завершения процесса. Затем реактор охлаждают до температуры 353-363 К и реакционную смесь подают на следующую стадию.
H2SO4 |
Ацетонциангидрин |
|
|
|
||||
CH3OH |
|
7 |
||||||
|
|
|||||||
1 |
2 |
3 |
|
|
||||
|
|
ММА |
||||||
|
|
|
|
|
|
|
|
|
|
|
|
|
|
|
|
|
Метилметакрилат |
|
|
|
|
|
|
|
|
Н2О
4 6
5
Рис. 7.5. Принципиальная технологическая схема получения метилметакрилата
1 - емкость с серной кислотой; 2 - емкость с ацетонциангидрином; 3 - емкость с метанолом; 4 - реактор-дегидрататор; 5 - реактор-эфиризатор; 6 - перегонный куб; 7 - конденсатор.
Этерификацию проводят в реакторе эфиризаторе 5 периодического действия, в который загружают реакционную массу из дегидрататора 4, метанол из емкости 3 и воду с небольшим содержанием гидрохинона для предотвращения полимеризации эфира. По окончании реакции этерификации содержимое эфи-

273
ризатора подают в перегонный куб 6 и отгоняют эфир вместе с непрореагировавшим метанолом и парами воды. Пары конденсируются в конденсаторе 7. Далее смесь поступает в систему выделения метилметакрилата.
Растворы бисульфата, сульфата аммония и серной кислоты можно использовать для получения удобрений либо превращать их в концентрированную серную кислоту. Для этого потоки сжигают в струе метана и воздуха при температуре ~ 1273 К и давлении 1 МПа. Сернистый ангидрид, содержащийся в потоке после охлаждения, сначала превращают в серный ангидрид пропусканием над катализатором на основе оксида ванадия, а затем в серную кислоту взаимодействием с водой.
7.6.2. Получение метилметакрилата из трет-бутилового спирта
трет-Бутиловый спирт в промышленности получают двумя путями: как побочный продукт при производстве пропиленоксида, а также гидропероксидированием изобутана и гидратацией изобутенов, содержащихся во фракции С4 каталитического крекинга. Последний способ используется фирмами "Мицубиси Рэйон" и "Ниппон Шокубай" для производства метилметакрилата.
Процесс превращения трет-бутилового спирта в метилметакрилат проводят в три стадии.
Окисление трет-бутилового спирта в метакролеин
Окисление спирта в метакролеин
(CH3)3COH + O2 |
CH3=C(CH3)CHO + 2H2O H298 = -275 кДж/моль |
ведут в газовой фазе при 603-633 К, давлении 0,3-0,4 МПа в присутствии воздуха или пара при соотношении трет-бутиловый спирт : воздух : пар, равном 1: (10-15): (6-12). В качестве катализаторов используют оксиды молибдена, кобальта, железа, никеля, а промоторами являются щелочные металлы, сурьма, теллур, фосфор, олово и др.
При времени пребывания реакционной смеси в зоне реакции 2-3 с достигается практически полная конверсия трет-бутилового спирта при селективности по метакролеину свыше 85%. В качестве побочных продуктов образуются СО2, СО, изобутен, уксусная и метакриловая кислоты, смолы.
Окисление метакролеина в метакриловую кислоту
Процесс также проводят в газовой фазе при 573-623 К и давлении 0,1-0,5 МПa в присутствии воздуха, разбавленного водяным паром во избежание образования взрывоопасных смесей.

274
CH2=C(CH3)CO O2 СН2=C(CH3)COOH. H
Типичный состав исходной смеси: метакролеин 3-6%, воздух 10-60%, водяной пар 20-75%.
В качестве катализаторов используют фосфаты молибдена, промотированные оксидами висмута, сурьмы, тория, хрома, меди, циркония и др., нанесенные на инертный носитель – карбид кремния, -оксид алюминия, оксид титана и др.
При времени пребывания 2-5 с конверсия за проход составляет 90-95% при селективности по метакриловой кислоте 85-90%. В качестве побочных продуктов образуются СО, СО2, и др.
Этот процесс разработан фирмами "Дайсел", "Джапан Каталитик", "Мицубиси", "Убе"и др.
Этерификация метакриловой кислоты до метилметакрилата
Реакцию этерификации метакриловой кислоты
CH2=C(CH3)COOH + CH3OH CH2=C(CH3)COOCH3 + H2O
H298 = 1,2 кДж/моль проводят в жидкой фазе при 383-388 К, давлении 30-50 кПа в присутствии сер-
ной кислоты или ионообменных смол как катализатора. При времени пребывания 1 ч степень конверсии за один проход достигается практически полная, селективность составляет ~ 99 %.
7.6.3. Получение метилметакрилата из изобутилена
Возможные варианты получения метилметакрилата из изобутилена представлены на схеме 7.1.
В середине 1950-х годов фирма "Эскамбия" (США) разработала метод получения метилметакрилата, основанный на окислении изобутилена азотной кислотой и тетраоксидом азота. Процесс протекает через промежуточное обра-
зование нитрата -изомасляной кислоты и -гидроксиизомасляной кислоты. Путем этерификации последней метанолом и последующей дегидратации серной кислотой получают метилметакрилат.
Разработан также метод окисления изобутилена кислородом воздуха в присутствии аммиака с получением метакрилонитрила, который с помощью серной кислоты переводят в сульфат метакриламида, а затем путем этерификации метанолом - в метилметакрилат:
СН2=С(СН3)2 NН3; О2 СН2=С(СН3)СN Н2О; Н2SО4 СH2=(СН3)СОNН2 Н2SО4 СН3ОН СН2=С(СН3)СООСН3 + NН4НSО4
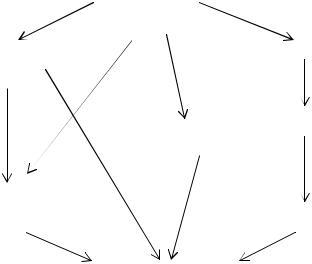
275
Схема 7.1
|
|
O2 |
|
CH2=C—CH3 |
N2O4, HNO3 |
|||
|
|
|
|
|
CH3 |
|||
CH2=C—CHO |
O2 |
|
(CH3)2C(ONO2)COOH |
|||||
|
NH3, O2 |
|||||||
|
|
|
|
|
|
|||
|
CH3 |
|
|
|
||||
|
|
|
|
|
||||
O2 |
O2, CH3OH |
|
CH2=C—CN (CH3)2C(OH)COOH |
|||||
|
|
CH3 |
CH3OH |
|||||
|
|
|
|
|
||||
|
|
|
|
|
|
|
|
|
CH2=C—COOH |
|
|
H2SO4, CH3OH, H2O |
|||||
|
|
|
|
|
||||
|
|
|
|
|
|
|
(CH3)2C(OH)COOCH3 |
|
CH3 |
|
|
|
|
|
|||
|
CH3OH |
|
|
|
|
|
H2SO4 |
CH2=C—COOCH3
|
СН3
Технология, базирующаяся на изобутилене, включает выделение его из фракции С4, гидратацию в трет-бутанол с последующим его двухступенчатым окислением сначала в метакролеин, а затем в метакриловую кислоту. Этот способ в основном используют японские фирмы. Фирма «Асахи» разработала также способ окисления трет-бутанола в присутствии аммиака с получением метакрилонитрила, его дегидратации в амид метакриловой кислоты и ее этерификации в метакрилаты.
Технология, базирующаяся на изобутане, включает дегидрирование изобутана в присутствии водяного пара с последующим окислением изобутилена в метакролеин, а затем в метакриловую кислоту и метакрилаты.
В Советском Союзе был разработан промышленный метод получения метакриловых мономеров из изобутилена через метакрилонитрил. Окислительный аммонолиз изобутилена осуществляют в присутствии висмутмолибденвольфрамовой кислоты в качестве катализатора со степенью конверсии изобутилена 95% и селективностью по метакрилонитрилу 70-75%.
Этот процесс целесообразно проводить в реакторах, обеспечивающих его протекание в условиях, близких к изотермическим. При весьма высокой экзотермичности процесса реакторы со стационарным слоем катализатора могут применяться в случае небольших мощностей производства. Оптимальными параметрами процесса являются следующие: температура 733 К, время контакта 5 с, мольное соотношение изо-С4Н8:NH3:О2, равное 1:1,7:2,6, давление менее 0,25 МПа. В этих условиях конверсия изобутилена за один проход составляет 95%, а
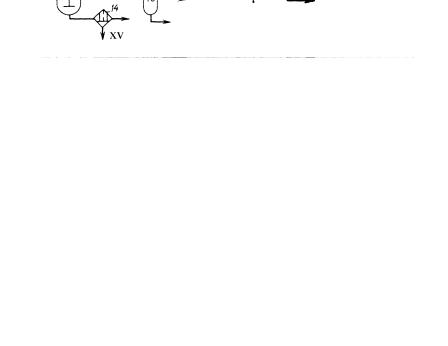
276
селективность по метакрилонитрилу - 65-70%. Выход ацетонитрила 10-15%, синильной кислоты 8-10%, диоксида углерода 8-10%, других побочных продуктов – до 2%.
Принципиальная технологическая схема получения эфиров метакриловой кислоты (в том числе метилметакрилата) представлена на рис. 7.6.
Описываемый способ производства метилакрилатов из изобутилена включает две стадии. Сначала окислительным аммонолизом изобутилена получают смесь продуктов, которые затем превращают в эфиры метакриловой кислоты.
Этот способ получения эфиров метакриловой кислоты из изобутилена имеет следующие преимущества по сравнению с ацетонциангидринным способом: уменьшен расход серной кислоты и аммиака, исключено использование токсичной синильной кислоты, практически отсутствуют побочные продукты (за исключением гидросульфата аммония).
Рис. 7.6. Принципиальная технологическая схема получения эфиров метакриловой кислоты на основе изобутилена
1 - реактор; 2 - теплообменник; 3, 13, 19 - нейтрализаторы; 4 - абсорбер; 5 - десорбер; 6-10 - ректификационные колонны; 11 - амидатор; 12 - насосы; 14 - фильтр; 15 – флорентийский сосуд; 16
-эфиризатор; 17, 20 - отстойники; 18 - промыватель.
Потоки: I - изобутилен; II - аммиак; III - воздух; IV - сульфат аммония; V - серная кислота; VI - вода; VII - газ из абсорбера на сжигание; VIII - синильная кислота и альдегиды; IX - ацетонитрил; X - спирты; XI - метакрилонитрил; XII - раствор КОН; XIII - гидросульфат аммония; XIV - метакриловая кислота; XV - раствор гидросульфата аммония; XVI - полимеры; XVII - метакрилат-сырец
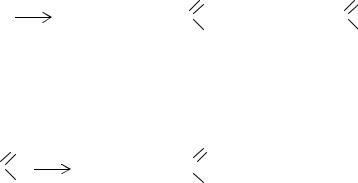
277
Экономический эффект достигается за счет сокращения расхода серной кислоты (примерно в 2 раза) и уменьшения расхода аммиака, используемого для превращения гидросульфата аммония в кристаллический сульфат аммония (примерно в 3 раза).
Сравнение технико-экономических показателей различных процессов получения метилметакрилата показало, что процесс на основе метакрилонитрила, полученного окислительным аммонолизом изобутилена, является более предпочтительным.
Фирма "Мицубиси Касей" (Япония) разработала также метод получения метилметакрилата, основанный на окислении изобутиральдегида. Процесс протекает через промежуточное образование изомасляной кислоты, которую затем путем окислительного дегидрирования переводят в метилметакрилат.
7.6.4. Новые методы получения метилметакрилата
Повышение цен на сырую нефть в 70-е годы ХХ столетия и необходимость решения экологических проблем сместили центр исследований в сторону процессов, использующих монооксид углерода для получения ценных полупродуктов и продуктов. В связи с этим интенсифицируются исследования процессов получения метилметакрилата с использованием реакций карбонилирования. Среди них наиболее продвинутыми являются процессы, использующие пропилен, метилацетилен и аллен.
Синтез метилметакрилата через изобутиральдегид
Этот способ предусматривает сначала гидроформилирование пропилена до изобутиральдегида:
2CH2=CH—CH3 + 2CO + 2H2 |
O |
O |
CH3—CH(CH3)C |
+ CH3CH2CH2C |
|
|
H |
H |
а затем окисление изобутиральдегида до изомасляной кислоты кислородсодержащим газом в жидкой фазе при 293-393 К в присутствии или в отсутствие катализатора:
O |
O2 |
O |
CH3CH(CH3)C |
|
CH3CH(CH3)C |
H |
|
OH |
Далее изомасляную кислоту этерифицируют метанолом при 323-373 К в присутствии серной кислоты в качестве катализатора для получения метилизобутирата. Последний окисляют в жидкой фазе кислородом или кислородсодержащим газом при 323-423 К в присутствии катализатора или без него до метил-
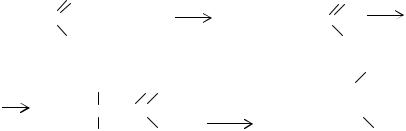
278
гидроксиизобутирата, дегидратацией которого в жидкой фазе при 333-413 К в присутствии сульфонированной смолы и ингибитора полимеризации получают метилметакрилат.
CH3 |
O |
|
|
CH3 |
|
|
O |
O2 |
||
CH3- |
|
|
|
|
|
|
|
|
|
|
C—C |
|
+ CH3OH |
CH3—CH—C |
|
||||||
|
|
OH |
|
|
|
|
|
OCH3 |
||
|
|
|
CH3 |
O |
|
|
|
|
CH3 |
О |
|
|
|
|
|
|
|
|
|||
|
|
|
|
|
|
|
||||
|
CH3—CH—C |
|
|
|
|
|||||
|
|
- Н2О CH2=C—C |
||||||||
|
|
OH |
OCH3 |
|
|
|
|
|
OCH3 |
Карбометоксилирование пропилена
Исследования в области гидрокарбалкоксилирования олефинов традиционно развивались в направлении поиска каталитических систем на базе металлов восьмой группы с целью повышения выхода линейных продуктов синтеза. Эта проблема остро стоит и в настоящее время, так как для нужд промышленности предпочтительно использование преимущественно спиртов и кислот линейного строения. Однако в последнее время коммерческое значение стали приобретать и продукты изо-строения. Создание эффективного процесса получения метилметакрилата через карбалкоксилирование пропилена состоит в создании таких каталитических систем, которые давали бы максимальную селективность по продукту разветвленного строения.
Получение метилметакрилата этим способом осуществляют в две стадии. На первой стадии пропилен карбометоксилируют до метилизобутирата:
CH2=CH—CH3 + CO + CH3OH CH3CH(CH3)COOCH3.
Распределение региоизомеров определяется направлением присоединения карбонильной группы по двойной связи.
В качестве катализаторов могут быть использованы комплексные соединения никеля, кобальта, родия, иридия, рутения, палладия. Палладиевые катализаторы являются наиболее эффективными: они высокоактивны в мягких условиях и обладают высокой региоселективностью. Селективность по целевому продукту определяется давлением, температурой, концентрацией реагентов, природой растворителя, а также структурой лиганда и его содержанием в каталитической системе.
Процесс осуществляют при температуре не выше 423 К, так как при более высоких температурах каталитический комплекс подвержен термическому распаду. Палладий вводят в реакцию, как правило, в виде соли РdСl2, в качестве лигандов используются фосфорорганические соединения, чаще всего трифе-

279
нилфосфин Р(Рh)3. В отсутствие лиганда процесс не протекает из-за восстановления активной формы палладия Рd (II) до неактивного металлического палладия:
PdCl2 + CO + H2O Pd(O) + CO2 + 2HCl
На второй стадии метилизобутират дегидрируют в метилметакрилат:
CH3CH(CH3)COOCH3 CH2=C(CH3)COOCH3 + H2
Стадия дегидрирования проводится в газовой фазе при 623-723 К и атмосферном давлении в присутствии оксидов молибдена, фосфора, железа, ванадия.
Карбометоксилирование метилацетилена
Карбометоксилирование метилацетилена до метилметакрилата было осуществлено в середине 1990-х годов фирмой "Шелл":
СН3—С СН + СО + СН3ОН СН2=С(СН3)СООСН3.
В процессе используются палладиевый катализатор Рd(ОAс)2, лиганд 2- пиридилдифенилфосфин и кислоты, которые образуют слабые или координированные анионы, составляющие каталитическую систему в растворе N- метилпирролидона.
Гомогенный палладиевый катализатор представляет собой катионный комплекс палладия с 2-пиридилфосфиновым лигандом (2-РуРРh2) и кислотный промотор со слабокоординируемыми анионами. Метанол применяют как в качестве растворителя каталитической системы, так и в качестве реагента.
Лиганд 2-РуРРh2 координируется к палладию в напряженной 4-членной хелатной группировке. При введении в пиридиловую группу лиганда объемного заместителя (например, метильной группы) сохраняется активность и увеличивается селективность, обеспечивая 20-кратное снижение скорости образования метилкротоната. В зависимости от типа координации молекулы метилацетилена на палладии, как указано ниже, могут образовываться метилметакрилат или метилкротонат:
Ph |
|
|
|
COOCH3 |
|
Ph-P |
Pd |
|
|
||
N |
|
CH |
CH3—CH=CH—COOCH3 |
||
R) |
H |
C |
C |
||
H |
|
Метилкротонат |
|||
|
|
H |
|||
|
|
|
|

280
Ph |
COOCH3 |
|
|
|
Ph-P |
H |
CH2=C(CH3)—COOCH3. |
||
N Pd |
C |
C |
||
R) HC |
H |
H |
Метилметакрилат |
|
|
|
При 723 К процесс реализуется со скоростью 40 000 ч-1 с селективностью по метилметакрилату 99,9%.
Процесс подготовлен к промышленному внедрению.
Карбометоксикарбонилирование аллена и метилацетилен-алленовой фракции
Получение метилметакрилата по методу фирмы "Шелл" Голландия), несмотря на все свои достоинства, имеет один существенный недостаток: реакция ингибируется алленом. В настоящее время единственным источником получения метилацетилена является метилацетилен-алленовая фракция, которую выделяют из продуктов пиролиза нефтяных углеводородов при получении этилена (пропилена). Для проведения процесса карбометоксилирования по методу фирмы "Шелл" необходимо выделить метилацетилен с остаточным содержанием аллена не более 1%. Поскольку выделение метилацетилена с чистотой 99% является довольно дорогим процессом, то оно влияет на экономическую эффективность всего процесса. В связи с этим может быть перспективным процесс получения метилметакрилата карбометоксилированием метилацетиленалленовой фракции без ее разделения (Институт нефтехимического синтеза им. А.В. Топчиева РАН; Г.А. Корнеева, Е.В. Сливинский).
CH2=C=CH2
+ CO + CH3OH CH2=C(CH3)COOCH3.
CH3–C CH
В карбометоксилировании аллена активность проявляют комплексы палладия, кобальта, родия, однако наиболее активным является рутениевый катализатор: в его присутствии при 413 К, давлении оксида углерода 5,0 МПа, концентрации рутения 1,1 10-3 моль/л в среде метанола достигается селективность
по метилметакрилату, близкая к 100% при частоте оборотов катализатора 700
ч-1.
Карбометоксилирование метилацетилен-алленовой фракции реализовано на палладиевом катализаторе, модифицированном азотсодержащим лигандом, В оптимальных условиях - при 383 К, давлении оксида углерода 5,0 МПа, концентрации катализатора 8,5 10-3 моль/л - достигается конверсия исходных реагентов свыше 75% при селективности 96-97% и частоте оборотов катализатора свыше 300 ч-1.