
monomers-Платэ-книга
.pdf191
5.1.7.Получение винилиденхлорида
Винилиденхлорид (1,1-дихлорэтен) СН2=CCl2 - бесцветная летучая жидкость со слабым запахом, напоминающим запах хлороформа. Основные физические свойства винилиденхлорида приведены ниже:
Т. кип., К 304,7 Т.пл., К 150,47 d420 1,2122 nD20 1,4271
Винилиденхлорид хорошо растворяется в обычных органических растворителях, в воде растворяется плохо.
В присутствии пероксидных инициаторов легко полимеризуется, а также вступает в реакции сополимеризации с различными мономерами. Гомополимеризацию винилиденхлорида используют для синтезаполучения поливинилиденхлорида [—СН2—СС12—]n. Широко распространены сополимеры винилиденхлорида с винилхлоридом. Сополимеризацией винилиденхлорида с акрилонитрилом получают латексы, из которых вырабатывают химически стойкие волокна. Сополимеры винилиденхлорида с бутадиеном обладают повышенной масло- и бензостойкостью, их выпускают в виде латекса и используют для производства искусственной кожи.
Винилиденхлорид применяют также для производства фреонов и метилхлороформа.
В промышленности винилиденхлорид получают главным образом жидкофазным дегидрохлорированием 1,1,2-трихлорэтана (продукт хлорирования винилхлорид) гидроксидом кальция Са(ОН)2 при температуре ~373 К:
CH2=CHCl + Cl2 СНСl2—СН2Сl
СНСl2—СН2Сl СН2=ССl2 + НСl
Вкачестве побочного продукта образуется монохлорацетилен, способный
ксамовоспламенению. Для подавления образования монохлорацетилена применяют водный раствор щелочи, содержащей хлорид натрия. Это позволяет понизить растворимость винилиденхлорида и уменьшить возможность его вторичных превращений.
Принципиальная технологическая схема производства винилиденхлорида из винилхлорида представлена на рис. 5.6. Винилхлорид испаряется в аппарате 1 и вместе с хлором поступает в хлоратор 2, заполненный 1,1,2-трихлорэтаном. Реактор представляет собой вертикальный стальной аппарат с мешалкой и рубашкой для снятия тепла реакции с помощью испаряющегося жидкого винилхлорида. Процесс проводят при 298 К и 0,3 МПа, соотношении винилхлорид : хлор, равном 1:1,05 (моли), в присутствии в качестве катализатора хлорида железа. Газы после прохождения конденсатора 3 и сепаратора 4 отводят на очистку. Образовавшийся 1,1,2-трихлорэтан проходит нейтрализатор 5 для удаления непревращенного хлора и образовавшегося в качестве побочного продукта НСl с помощью 2%-го раствора NаОН.
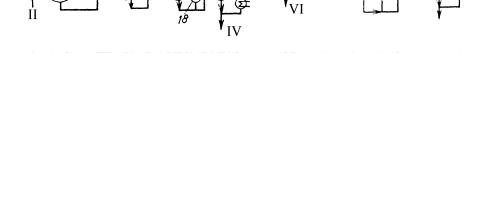
192
Рис. 5.6. Принципиальная технологическая схема получения винилиденхлорида из винилхлорида
1 - испаритель; 2, 10 - реакторы; 3, 6, 9, 11, 13, 16 - конденсаторы; 4, 17 -
сепараторы; 5 - нейтрализатор; 7, 8, 12, 14 - ректификационные колонны; 15 - насадка; 18 - кипятильник.
Потоки: I - хлор; II - винилхлорид; III - щелочь; IV - тетрахлорэтаны; V - Ca(OH)2; VI - шлам; VII - отдувка; VIII - легкая фракция; IX - винилиденхлорид; X - отходы
Далее 1,1,2-трихлорэтан поступает на азеотропную перегонку 7, отделяется от воды в конденсаторе 6 и возвращается в колонну 7 на орошение. Избыток 1,1,2-трихлорэтана рециркулирует в нейтрализатор 5. Из осушенного продукта выделяют 1,1,2-трихлорэтан в колонне 8. Из нижней части колонны 8 удаляется остаток, состоящий из тетрахлорэтанов.
Дегидрохлорирование 1,1,2-трихлорэтана осуществляют в стальном реакторе 10 раствором Са(ОН) концентрацией 160-200 г/л при 353 К. В реакторе поддерживают 50%-ный избыток щелочного агента (по сравнению со стехиометрическим). Для стабилизации винилиденхлорида в реактор постоянно подают аммиак. Смесь винилиденхлорида с парами воды и 1,1,2-трихлорэтаном охлаждается в холодильнике 11 и поступает в аппарат 17 с насадкой, в котором конденсат расслаивается на органический и водный слой. Органический слой возвращается на орошение насадки в аппарате 15, а водный направляют на ректификацию в колонны 12 и 14. В высушенный винилиденхлорид вводят в качестве ингибитора полимеризации хинон. Винилиденхлорид хранят в емкости при 263 К и 0,06 МПа.
Недостатками метода является возникновение большого количества загрязненных сточных вод и образованием трудноутилизируемой соли СаС12. Более эффективно применение для дегидрохлорирования растворов едкого натра или аммиака.
Газофазный процесс проводят при 773 К на хлоридах бария, меди или кальция в качестве катализатора и с добавками хлора, брома или кислорода в качестве инициатора. Мономер в качестве примеси содержит 1,2-дихлорэтан, от
193
которого освобождаются азеотропной перегонкой с метанолом с последующей отмывкой от него водой.
5.1.8. Получение хлоропрена
Хлоропрен (2-хлорбутадиен-1,3) CH2=C(Cl)—CH=CH2 - хлорсодержащее производное бутадиена, в котором атом водорода у второго углеродного атома замещен на хлор. Для получения каучуков специального назначения к основному мономеру при полимеризации добавляют в небольших количествах (3- 15%) другие мономеры: стирол, изопрен, акрилонитрил и пр. Хлоропрен используют в промышленности как мономер для производства масло- и бензостойкого хлоропренового каучука. Такой каучук обладает многими ценными свойствами: негорючестью, свето- и озоностойкостью, повышенной бензо- и маслостойкостью, устойчивостью к действию кислот и щелочей.
Хлоропреновые каучуки используют в производстве разнообразных изделий и деталей, которые эксплуатируются в контакте с агрессивными средами, например уплотнителей, шлангов, рукавов, ремней, прорезиненных тканей, защитных оболочек, кабелей и т.д. Жидкие хлоропреновые каучуки применяют для создания антикоррозионных покрытий.
Промышленное производство хлоропрена было организовано в Советском Союзе еще в 1940 г. В настоящее время выпуск хлоропрена и каучуков на его основе в больших масштабах осуществляется в России, США, Японии, ФРГ и других промышленно развитых странах. Объем мирового производства хлоропреновых каучуков составил в 2000 г. 500 тыс. т.
Мономер хлоропрен - бесцветная легколетучая жидкость, обладающая характерным эфирным запахом. В воде плохо растворяется, слабо смешивается со многими органическими растворителями. Основные физические свойства
хлоропрена приведены ниже:
Т. пл., К 143 Т. кип., К 332.4 n420 1,42194 d420 0,958
Хлоропрен с воздухом образует взрывоопасные смеси, обладает вредным физиологическим действием. Он склонен к самопроизвольной полимеризации, причем при длительном хранении даже в присутствии ингибиторов образуются димеры.
Препаративные способы синтеза хлоропрена
Хлоропрен может быть получен термическим дегидрохлорированием 1,2,3- или 2,2,3-трихлорбутана при температуре ~600 К. Образующееся в качестве интермедиата производное аллена быстро изомеризуется в хлоропрен:
СН2(Сl)—СН(Сl)—СН(Cl)—СН3 → СН2=С=С(Сl)—СН3 + 2НСl
СН2=С=С(Сl)—СН3 → СН2=С(Сl)—СН=СН2.
Хлоропрен образуется также из 1,3-дихлорбутена-2 при 530 К в присутствии SiO2 или каолина с высоким выходом:
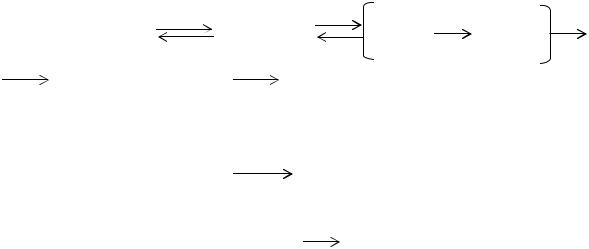
194
СН3—С(Сl)=СН—СН2Сl → СН2=С(Сl)—СН=СН2
Сырьем для получения хлоропрена могут служить винилхлорид и ацетилен:
СН2=СНСl + СН СН СН2=С(Сl)—СН=СН2.
При этом в качестве катализатора используется монохлорид меди. Винилхлорид при температуре 700 К в паровой фазе на медных, кадмие-
вых, оловянных или свинцовых катализаторах также превращается в хлоропрен:
2СН2=СНСl СН2=С(Сl)—СН=СН2 + НСl
Однако в промышленном масштабе хлоропрен получают в основном из ацетилена и бутадиена.
Промышленные способы синтеза хлоропрена
Производство хлоропрена из ацетилена. До недавнего времени это был единственный промышленный способ получения хлоропрена. Синтез хлоропрена на основе ацетилена осуществляют в две стадии: на первой стадии ацетилен димеризуется в винилацетилен, на второй - винилацетилен гидрохлорируется в хлоропрен.
Димеризацию ацетилена проводят при 333-353 К в присутствии катализатора - хлорида одновалентной меди:
2СН СН СН2=СН—С СН В качестве катализаторов могут применяться также катализаторы Нью-
ленда: подкисленный раствор Cu2Cl2, NH4 C1, NаС1. Превращение ацетилена происходит по механизму внедрения:
|
C2H2 Cu—C CH |
C2H2 |
H—C |
||||
0,5Cu2Cl2 |
H—C |
|
|
CuC CH |
|||
Cu—CH=CH—C CH HCl |
|
|
|
|
|
||
0,5Cu2Cl2 |
+ CH2=CH—C CH . |
||||||
Гидрохлорирование винилацетилена |
проводят в среде водного раствора |
||||||
хлорида одновалентной меди при 313-323 К. |
|
|
|
|
|||
СH2=СН—C CH + НСl Cu2C12 |
СН2=С(Сl)—СН=СН2 |
Основной побочной реакцией является дальнейшее гидрохлорирование хло-
ропрена с образованием 1,3-дихлорбутенов-2: |
|
СН2=С(Сl)—СН=СН2 + НСl |
СН3—С(Сl)=СН—СН2Сl |
Принципиальная технологическая схема производства хлоропрена из ацетилена представлена на рис. 5.7.
Исходный ацетилен поступает на димеризацию в реактор 1. Температура реакции поддерживается в интервале 333-353 К, время контакта 15-17 с. Пары реакционной смеси из реактора попадают в скруббер 2, в котором освобождаются от соляной кислоты и поступают на конденсацию.
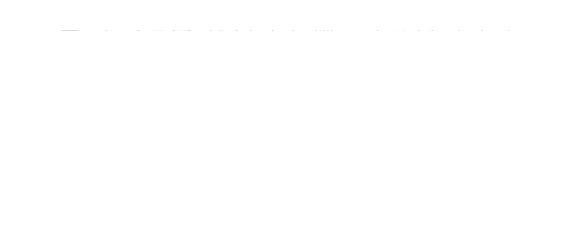
195
Рис. 5.7. Принципиальная технологическая схема получения хлоропрена из ацетилена
1 - реактор димеризации; 2, 7 - скрубберы; 3 - конденсатор-осушитель; 4 - конденсатор; 5, 6, 9, 11, 12 - ректификационные колонны; 8 - реактор гидрохлорирования; 10 - сепаратор.
Потоки: I – ацетилен; II – вода; III – винилацетилен; IV – хлоропрен; V – дихлорбутены; VI – хлорид водорода; VII – дивинилацетилен; VIII – сточные воды на очистку
В конденсаторе-осушителе 3 пары винилацетилена освобождаются от воды, а в аппарате 4 от непрореагировавшего ацетилена. Далее винилацетилен проходит ректификационные колонны 5 и 6, скруббер 7 и затем поступает в реактор 8 на гидрохлорирование. Реакцию проводят при 303-323 К и времени контакта ~5 с. Очистку и выделение товарного хлоропрена производят в ректификационных колоннах.
Достоинством способа получения хлоропрена из ацетилена является то, что в качестве хлорирующего агента используется хлорид водород, который на предприятиях хлорорганического синтеза во многих производствах образуется как побочный продукт. К недостаткам процесса относятся повышенная взрывоопасность, высокие капитальные затраты по сравнению с другими методами.
Производство хлоропрена из углеводородов С4. В 1966 г. во Франции была пущена в эксплуатацию промышленная установка получения хлоропрена из бутадиена.
Хлорирование бутадиена-1,3 осуществляют в паровой фазе при температуре ~573 К. Бутадиен и хлор предварительно подвергают осушке и очистке от кислорода. Во избежание нежелательных побочных реакций бутадиен-1,3 берут в избытке по отношению к хлору. В этих условиях основными продуктами реакции являются цис- и транс-изомеры 1,4-дихлорбутенов-2 и 3,4- дихлорбутенов-1:
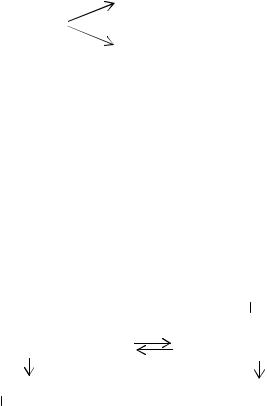
196
4 |
3 |
2 |
1 |
CH2Cl—CH(Cl)—CH=CH2 |
|||
CH2CH—CH=CH2 + Cl2 |
3,4-Изомер |
|
|
CH2Cl—CH=CH—CH2Cl
1,4-Изомер
В качестве побочных продуктов вследствие полного хлорирования бутадиена образуются тетрахлорбутаны.
Получение хлоропрена путем дегидрохлорирования возможно только из 3,4-изомера дихлорбутена. В условиях кинетического контроля образование 3,4-изомера является преобладающим. Термодинамически же предпочтительно образование более устойчивого 1,4-изомера. Это обстоятельство обусловливается механизмом присоединения электрофильных реагентов к бутадиену, соответствующим двум возможным вариантам образования промежуточных продуктов:
+
CH2=CH—CH=CH2 + Cl2 CH2—CH—CH=CH2
+ |
Cl |
+ |
|
||
CH2Cl—CH—CH=CH2 |
CH2Cl—CH=CH—CH2 |
|
CH2C—CH—CH=CH2 |
CH2Cl—CH=CH—CH2Cl |
|
Cl 3,4-Изомер |
1,4-Изомер |
|
Хлорирование бутадиена проводят при повышенных температурах (573 К) и малом времени контакта (0,01 с). Такой технологический прием позволяет повысить концентрацию 3,4-изомера в реакционной смеси до 60-70%. Дальнейшее повышение степени превращения бутадиена в 3,4-дихлорбутен может быть осуществлено путем изомеризации 1,4-дихлорбутена. Процесс изомеризации катализируется солями меди.
Принципиальная технологическая схема получения хлоропрена из бутадиена- 1,3 представлена на рис. 5.8.
Сырье - бутадиен и хлор - подаются в реактор газофазного хлорирования 1. Образовавшаяся в реакторе смесь продуктов хлорирования и непрореагировавшего бутадиена после охлаждения поступает в отпарную колонну 2, в которой происходит отделение бутадиена и хлорида водорода от хлоруглеводородов. В скруббере 3 происходит поглощение хлорида водорода водой, а бутадиен после осушки в аппарате 4 возвращается на хлорирование.
Смесь изомеров дихлорбутенов: 3,4-дихлорбутена-1, цис- и транс-1,4- дихлорбутена-2 из куба колонны 2 поступает на изомеризацию в аппарат 5. Далее паровая смесь из аппарата 5 поступает на ректификацию в колонну 6, откуда 3,4-дихлорбутен-1 выводится в виде дистиллята, а непрореагировавшие 1,4- дихлорбутены-2 возвращаются на изомеризацию. Чистый 3,4-дихлорбутен-1 направляется на дегидрохлорирование в реактор 7, в который подается водный
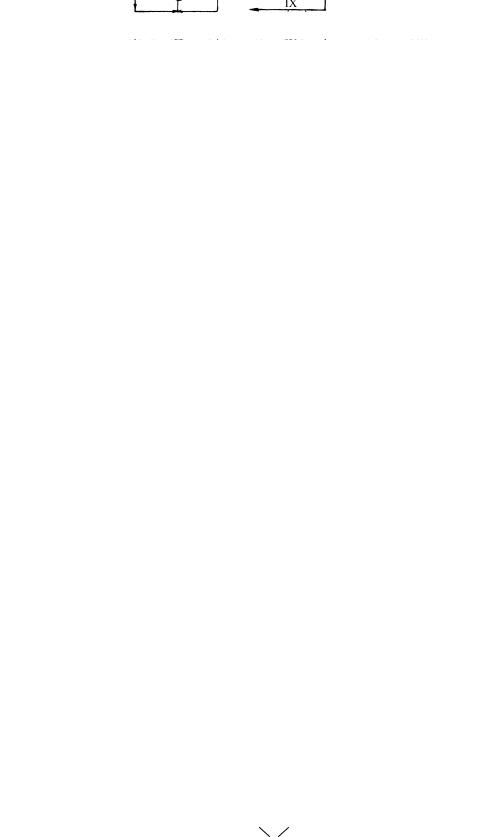
197
раствор NaOH. Образовавшийся хлоропрен поступает на ректификацию в колонну 9, где отделяется от побочных продуктов.
Рис. 5.8. Принципиальная технологическая схема получения хлоропрена из бу- тадиена-1,3
1 - реактор; 2 - отпарная колонна; 3 - скруббер; 4 - осушитель; 5 - аппарат для изомеризации; 6 - колонна выделения 3,4-дихлорбутена-1; 7 - дегидрохлоратор; 8 - колонна для выделения хлорида натрия; 9 - ректификационная колонна.
Потоки: I – бутадиен; II – хлор; III – вода; IV – соляная кислота; V – NaOH; VI – пар; VII – хлоропрен; VIII – 1-хлорбутадиен; IX – раствор NaCl на утилизацию
Сравнение технико-экономических параметров рассмотренных процессов показывает, что себестоимость хлоропрена, полученного из бутадиена, выделенного из фракции С4 пиролиза, ниже, чем при хлорировании чистого бутадиена.
Достоинством же процесса получения хлоропрена из бутан-бутиленовой фракции является доступность углеводородного сырья. Недостатки этого способа: сравнительно большие капитальные затраты, большой расход хлора, образование сравнительно больших количествах побочного хлорида водорода.
5.1.9. Получение эпихлоргидрина
Эпихлоргидрин (1-хлор-2,3-эпоксипропан, хлорметилоксиран) - бесцветная жидкость с резким неприятным запахом; т.пл. 216 К, т.кип. 389,1 К. Хорошо растворяется в органических растворителях.
Н2С—СН—СН2Сl
О
198
Эпихлоргидрин применяют для промышленного производства эпихлоргидриновых каучуков - гомо- и сополимеров эпихлоргидрина. В промышленности выпускают гомополимер эпихлоргидрина общей формулы
[—СН2СН(СН2С1)O—]n ,
сополимер эпихлоргидрина с этиленоксидом
[—СН2СH(СH2Cl)ОСН2СН2О—]n ,
и терполимер эпихлоргидрина, этиленоксида и аллилглицидилового эфира
[—СН2СН(СН2Сl)ОСН2СН2O—]n—СН2—СН(СН2OСН2СН=СН2)O—
Эпихлоргидриновые каучуки применяют для производства маслостойких деталей (шланги, прокладки, рукава, манжеты, кольца, торцевые уплотнители), используемых в нефтяной промышленности, авто- и авиастроении. Гомополимер применяют также как огнестойкий материал и покрытие для кабелей. Из эпихлоргидрина производят глицерин, эпоксидные олигомеры и ионообменные смолы.
Эпихлогидрин получают эпоксидированием аллилхлорида гидроперокси-
дами:
СН2=СН—СН2Сl + RООН Н2С—СН—СН2Сl + RОН
О
Эпоксидирование аллилхлорида проводят при 350-410 К в присутствии
молибденсодержащего катализатора. В качестве катализаторов применяют органические соединения молибдена, полученные взаимодействием Мо с (СН3)3ССООН в присутствии алифатических спиртов фракции С1-С4 при 300400 К.
Исходный аллилхлорид получают заместительным хлорированием пропилена при температуре 773-793 К:
СН2=СН—СН3 + Сl2 СН2=СН—СН2Сl + НСl.
Реакция протекает с выделением большого количества тепла. Для улучшения отвода тепла, а также для предотвращения образования продуктов глубокого хлорирования соотношение пропилен: хлор поддерживают на уровне 5:1. В этих условиях хлор превращается полностью, а пропилен - на 20% за один проход.
Основным побочным продуктом является 1,2-дихлорпропан, образующийся в результате присоединения хлора по двойной связи пропилена:
СН2=СН—СН3 + Сl2 СН2(СI)—СН(Сl)—СН3 .

199
Дихлорпропаны главным образом ответственны и за появление в продуктах реакции 1- и 2-хлоропропенов, образующихся путем дегидрохлорирования дихлорпропанов.
Образование дихлорпропенов связывают с последующим хлорированием образующегося аллилхлорида и его дегидрохлорированием:
СН2=СН—СН2Сl + Сl2 СН2(Сl)—СН(Сl)—CH2Cl ,
СН2(Сl)—СН(Сl)—СН2Сl → НСl +СН(Сl)=СН—СН2Сl .
Более подробно процессы получения эпихлоргидрина рассмотрены в разд. 9.6.
5.2. ФТОРСОДЕРЖАЩИЕ МОНОМЕРЫ
Фторполимеры - гомополимеры фторпроизводных этилена и их сополимеры с другими олефинами и фторсодержащими олефинами - обладают целым рядом ценных свойств: инертностью к большинству химических веществ, тер- мо-, морозо- и атмосферостойкостью, низким коэффициентом трения, высокой адгезионной способностью, негорючестью, водо- и маслоотталкивающими свойствами.
Фторполимеры благодаря высокой термо- и химической стойкости, хорошим диэлектрическим свойствам занимают важное место среди пластических масс. Их широко используют в медицине и технике для изготовления пьезо- и пироэлектриков, электропроводящих материалов, материалов с высокой диэлектрической проницаемостью, резисторов для сверхбольших интегральных схем, оптических волокон.
Наибольшее распространение получили политетрафторэтилен, политрихлорфторэтилен, поливинилиденфторид, а также сополимеры тетрафторэтилена с этиленом, винилиденфторидом, гексафторпропиленом, перфторалкилвиниловыми эфирами и сополимеры хлортрифторэтилена с этиленом.
5.2.1. Теоретические основы процессов фторирования
Прямое фторирование насыщенных углеводородов с замещением атома водорода на фтор, а также присоединение фтора по двойной связи ненасыщенных углеводородов - чрезвычайно экзотермические реакции:
|
СН + F2 |
|
СF + НF |
Н = 435,8 кДж/моль , |
|
|
|||
С=С + F2 |
CF—CF |
Н = 452,5 кДж/моль . |
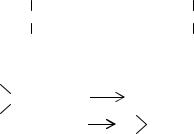
200
Поскольку тепловой эффект фторирования больше теплового эффекта разрыва С—С-связей (335-356 кДж/моль), в условиях фторирования происходит деструкция органического соединения с образованием фторида водорода и продуктов разложения органического соединения - сажа, тетрафторида углерода и др. Реакция протекает бурно, сопровождается вспышками и взрывами. Поэтому для фторирования в газовой фазе молекулярный фтор разбавляют азотом или гелием и используют газовую смесь, содержащую до 10% фтора. При фторировании в жидкой фазе применяют растворители - обычно хлор или хлорфторуглеводороды или уксусную кислоту.
Ниже приведены значения относительных скоростей реакций замещения хлором и фтором первичных, вторичных и третичных атомов водорода в н- бутане и изобутилене:
Группа |
|
F |
C1 |
—СН3 |
1 |
|
1 |
=СН2 |
1,3 |
|
4,6 |
СН |
2,5 |
|
10,3 |
Эти данные свидетельствуют о том, что фторирование является значительно менее селективным процессом, чем хлорирование. Селективность газофазного фторирования еще меньше, чем в жидкой фазе. Вследствие этого низкофторированные углеводороды получают, как правило, не прямым фторированием углеводородов, а замещением атомов хлора на фтор. Прямое фторирование фтором и через высшие фториды металлов используют в промышленности главным образом для получения перфторзамещенных углеводородов, т.е. полностью замещенных насыщенных фторуглеродов. Перфторуглероды обладают исключительно высокой термической и химической стойкостью: только при 1273 К происходит их разложение на углерод и перфторметан. Перфторолефины, у которых связи С—F так же прочны, как и у перфторалканов, сохраняют свойства ненасыщенных соединений, т.е. способность к реакциям присоединения по кратной связи.
5.2.2. Механизм реакций фторирования
Реакция углеводородов с фтором протекает по свободнорадикальному механизму. Зарождение цепи происходит за счет взаимодействия молекулы фтора с органическим соединением:
С—Н + F2 —C + НF2
—C + НF + F
Развитие и обрыв цепи осуществляется также как и при протекании свободнорадикальных реакций других типов:
|
С—Н + F |
C + HF, |
|
||
|
C + F2 |
— CF + F . |