
monomers-Платэ-книга
.pdf
211
Процесс проводят в жидкой фазе в присутствии SbF3 и SbF5 при 383 К и 3
МПа.
Наряду с жидкофазным фторированием в промышленности осуществляют и газофазный процесс при 523-723 К, атмосферном давлении в присутствии катализатора FeCl3 на активированном угле. Дифтордихлорметан и дифторхлорметан получают с высокими выходом и селективностью.
Промышленный метод получения дифторхлорметана (Ф-12) и фтортрихлорметана (Ф-11) заключается в хлорировании метана на катализаторе AlF3:
Cl2, HF
nCH4 CCl2F2 + CCl3F + HCl.
Трифтортрихлорэтан (Ф-113) получают действием на перхлорэтилен смеси Cl2 и HF при 573-773 К в присутствии AlF3, CrF3 или гидрофторированием гексахлорэтана в присутствии SbF3.
Из фторхлоралкенов наибольшее значение имеет трифторхлорэтилен, получаемый дегидрохлорированием трифтортрихлорэтана в газовой фазе:
CClF2СCl2F + H2 CClF=CF2 + 2HCl.
Трифтортрихлорэтан обрабатывают водородом при мольном соотношении фреон : водород, равном 5:1, 763-823 К и 0,1 МПа на медной сетке. В качестве катализаторов могут быть использованы также кобальт, серебро, платина. В качестве побочных продуктов образуются винилиденфторид и трифторэтилен, которые очень плохо отделяются от трифторхлорэтилена.
Жидкофазный процесс дехлорирования фреона-113 осуществляют в присутствии порошка цинка в виде суспензии в метаноле или этаноле при 323-423 К и 0,2 МПа при времени пребывания реагентов в зоне реакции в течении нескольких секунд.
Галогенфторолефины находят широкое применение в синтезе различных фторированных соединений путем замещения галогена. Например, из доступного -хлорперфторизобутилена кипячением с иодидом натрия в ацетоне получают -иодперфторизобутилен, а на его основе перфторизобутенилмагнийбромид, который используют в синтезе ряда производных перфторизобутилена.

212
Глава 6
ВИНИЛОВЫЕ МОНОМЕРЫ С АРОМАТИЧЕСКИМИ И ГЕТЕРОЦИКЛИЧЕСКИМИ
ЗАМЕСТИТЕЛЯМИ
К виниловым мономерам с ароматическими и так называемыми сложными заместителями относятся стирол, -метилстирол, винилтолуол, винилкетоны, винилпиридины, винилкарбазолы и др.
6.1. СТИРОЛ И ЕГО ПРОИЗВОДНЫЕ
Стирол (винилбензол, фенилэтилен) |
CH=CH2 |
|
|
||||
|
|
|
|
|
|
|
|
|
|
|
|
|
|
|
|
является исходным мономером для производства полистирола. |
|
||||||
Впервые стирол был |
выделен в 1831 г. Однако до |
Второй мировой |
|||||
войны стирол и его полимеры |
широко не |
применялись в |
промышленности. |
||||
В промышленном масштабе стирол был |
получен впервые в |
Германии в |
|||||
1930 г. Производство стирола |
началось |
в США в 1933 г., но |
ситезиро- |
||||
ванный из него полистирол |
был низкого |
качества и высокой |
стоимости. |
Стирол использовали только для производства полистирола в виде порошка для литья под давлением. Наличие же больших производственных мощностей по производству мономерного стирола стимулировало расширение исследований по применению полистирола в новых областях, в частности, в производстве товаров массового потребления.
Развитие исследований в области синтеза полимеров и сополимеров стирола привело к созданию большой группы полимерных материалов с самыми разнообразными свойствами.
Из мономеров для производства каучука общего назначения стирол как
сомономер по объему производства находится |
на |
третьем |
месте, |
уступая |
||||
изопрену и бутадиену. До |
начала 1960-х годов, |
когда |
появились |
стереоре- |
||||
гулярные |
бутадиеновые |
и изопреновые каучуки, |
бутадиен-стирольные |
|||||
каучуки были наиболее массовыми среди всех выпускаемых эластомеров. |
||||||||
В |
промышленном масштабе выпускаются различные многокомпонент- |
|||||||
ные сополимеры стирола. Наиболее крупнотоннажные из |
них |
- |
акрило- |
|||||
нитрил-бутадиен-стирольные (АБС-сополимеры), |
вырабатываемые |
в ши- |
||||||
роком ассортименте в зависимости от соотношения |
исходных мономеров и |
условий проведения процесса. На их основе получены самые разнообразные
ударопрочные конструкционные материалы, с |
усиливающими наполните- |
лями или в сочетании с другими полимерами. |
Пластмассы на основе АБС- |
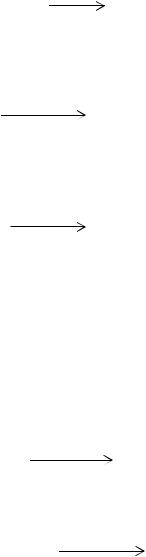
213
сополимеров получили широкое распространение в различных областях промышленности благодаря высокой химической стойкости, ударопрочности, теплостойкости и другим свойствам. Эти пластмассы легко перерабатываются литьем, экструзией, прессованием.
Разработаны также сополимеры винилхлорид-бутадиен-стирол, акрилат- стирол-диеновый каучук, сополимер стирол-акрилонитрил-метилмета-крилат,
сополимер акрилонитрил-стирол-эфир или амид -цианокоричной кислоты и другие.
6.1.1. Получение стирола
Препаративные методы синтеза стирола
Термическое декарбоксилирование коричной кислоты. Получение стирола путем декарбоксилирования коричной кислоты
С6Н5СН=СНСООН t◦ С6Н5СН=СН2 + СО2 проводится при 393-403 К и атмосферном давлении. Выход стирола составляет
~ 40%.
Коричная кислота может быть получена из бензальдегида и уксусного ан-
гидрида: |
CH3COOK |
|
C6H5CHO + (CH3CO)2O |
C6H5CH=CHCOOH + CH3COOH |
Дегидратация - или -фенилэтилового спирта. -Фенилэтиловый спирт является более доступным соединением, чем коричная кислота, поэтому именно его, как правило, используют для получения стирола:
C6H5CH(OH)CH3 -H2O C6H5CH=CH2
Реакция может быть реализована как в газовой, так и в жидкой фазе. Жидкофазная дегидратация -фенилэтилового спирта осуществляется в присутствии фосфорной кислоты или бисульфита калия. Дегидратация в паровой фазе проводится над катализаторами: оксидами алюминия, тория или вольфрама. При использовании оксида алюминия выход стирола составляет до 90% от теоретического.
-Фенилэтиловый спирт превращают в стирол дегидратацией в присутствии спиртового раствора едкого кали:
|
Спирт.р-р КОН |
|
C6H5CH2CH2OH |
-H2O |
C 6Н5CH=CH2 . |
|
|
Синтез из ацетофенона. Стирол можно получить по реакции ацетофено-
на с этиловым спиртом над силикагелем:
C6H5COCH3 + CH3CH2OH SiO2, 623 К C6H5CH=CH2.
Выход составляет около 30%.
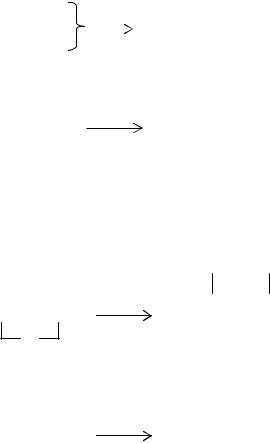
214
Получение стирола из галогенэтилбензола. Наиболее широко приме-
няемым лабораторным способом получения стирола является отщепление галогенводорода от галогенэтилбензола:
C6H5CHXCH3 |
|
C6H5CH=CH2 |
|
|
C6H5CH2CH2X |
-HX |
|
|
|
|
|
|
||
Например, стирол можно |
синтезировать пиролитическим |
разложением |
||
-хлорэтилбензола: |
t° |
|
|
|
C6H5CH2CH2Cl |
C6H5CH=CH2 |
+ HCl. |
|
|
|
|
Стирол может быть получен также взаимодействием бензальдегида с кетеном в присутствии борной кислоты или хлорида цинка при 273-283 К и последующим декарбоксилированием путем нагревания в присутствии борной кислоты:
C6H5CHO + CH2=C=O C6H5CHCH2C=O
C6H5CHCH2C=O t° |
|
|
O |
|
|
|
|
|
|||
C6H5CH=CH2 + CO2. |
O
Можно также использовать реакцию отщепления галогена от -, - дибромфенилэтана, например с помощью магния:
2C6H5CHBrCH2Br 2CMg С6H5CH=CH2 + MgBr2.
Промышленные методы синтеза стирола
Промышленное производство стирола в США и Германии в 30-х годах ХХ столетия заключалось в дегидрировании этилбензола. Этот метод не устарел и до настоящего времени.
Получение стирола из этилбензола. Этилбензол содержится в С8-
фракции ароматических углеводородов - продуктов каталитического риформинга, откуда и может быть выделен ректификацией. Однако это дорогой способ На практике этилбензол получают путем алкилирования бензола этиленом в жидкой фазе в присутствии хлорида алюминия в качестве катализатора по классической экзотермической реакции:
AlCl3
C6H6 + CH2=CH2 C6H5CH2CH3.
Этой реакции благоприятствуют повышение давления и понижение температуры. Ее проводят в мягких условиях при ~ 358 К и 0,1 МПа. Выход этил-
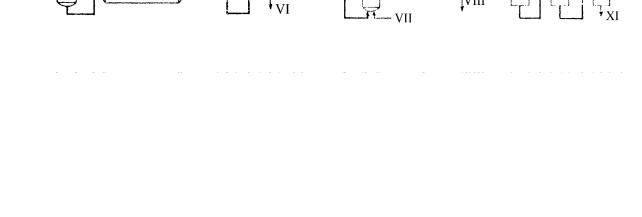
215
бензола превышает 90%. В качестве побочных продуктов образуются полиэтилированные бензолы, часть которых возвращают в реактор для увеличения выхода этилбензола.
Реакция дегидрирования этилбензола по своей природе является эндотермической; ее обычно проводят при высоких температурах (~873 К) и низких парциальных давлениях этилбензола, т.е. при условиях, которые термодинамически способствуют образованию стирола:
C6H5CH2CH3 C6H5CH=CH2 + H2.
Из нескольких возможных методов уменьшения парциального давления этилбензола на практике, как правило, применяют разбавление водяным паром. В процессах получения стирола, разработанных в различных странах, используются оксидные катализаторы различного состава. В качестве катализатора в процессе, разработанном в Германии, применяют оксид цинка, активированный калием. В процессе, разработанном в США, используют оксид магния, промотированный щелочью и оксидами железа. Промышленный катализатор фирмы "Шелл" имеет следующий состав: Fе203 – 75-80%, К2СО3 – 15-20%, Сr2О3 – 2- 3%, SiО2 - 0,1-0,5%.
Принципиальная технологическая схема получения стирола представлена на рис. 6.1.
Рис. 6.1. Принципиальная технологическая схема получения стирола
1 - реактор для алкилирования бензола; 2 - нейтрализатор; 3, 4 - ректификационные колонны; 5 - аппарат для дегидрирования этилбензола; 6 - конденсатор; 7-9 - ректификационные колонны.
Потоки: I - бензол; II - этилен; III - AlCl3; IV - непрореаги-ровавший бензол; V – этил-бензол; VI – полиэтилированные бензолы; VII – пар; VIII – вода; IX – смесь бензола и толуола; X – стирол; XI – остаток
Дегидрирование этилбензола проводят в реакторе адиабатического типа. Пар проходит через слой катализатора снизу вверх. Необходимое тепло частично подводится за счет теплообмена между выходящими из реактора и по-
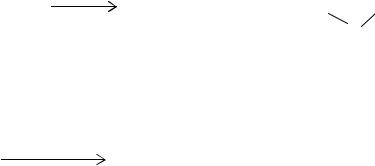
216
ступающими в него парами, а частично - с помощью перегревателей. Продукты, выходящие из реактора охлаждаются, при этом конденсируются пары воды и органических веществ. Отходящие газы содержат водород, оксид углерода, диоксид углерода (за счет взаимодействия пара с коксом, образовавшимся в результате пиролиза), метан и этан (за счет вторичных реакцией пиролиза). После отделения воды жидкие углеводороды направляют в ряд непрерывно действующих перегонных аппаратов.
Типичный состав жидкого конденсата (в % (мас.)) приведен ниже.
Стирол…….. |
37,0 |
Бензол …….. |
0,6 |
Этилбензол .. |
61,1 |
Смолы …….. |
0,2 |
Толуол ……. |
1,1 |
|
|
Совместное производство стирола и пропиленоксида. Этот процесс включает три основные стадии.
Первая из них состоит в синтезе гидропероксида этилбензола окислением
этилбензола воздухом:
O2, 403 К
C6H5CH2CH3 C6H5CH(OOH)CH3.
В качестве побочных продуктов на этой стадии образуются ацетофенон и фенилметилкарбинол. Окисление ведут до накопления в реакционной смеси ~ 10% гидропероксида.
Вторая стадия – жидкофазное эпоксидирование пропилена в присутствии гомогенного или гетерогенного катализатора с образованием фенилметилкарбинола:
C6H5CH(OOH)CH3 + CH3CH=CH2 |
C6H5CH(OH)CH3 + CH3CH—CH2 |
|
О |
Жидкофазный процесс проводят при 353-403 К и давлении 1,6-6,5 МПа, в качестве катализатора используют нафтенат молибдена. Степень превращения гидропероксида этилбензола достигает 90%.
На третьей стадии осуществляют дегидратацию фенилметилкарбинола в
стирол: |
TiO2, 373 К |
|
C6H5CH(OH)CH3 |
C6H5CH=CH2 + H2O |
Получение стирола метатезисом этилена со стильбеном. Процесс про-
водят в две стадии.
На первой стадии получают стильбен окислением толуола в присутствии PbO2 или Bi2O3 при температуре ~ 873 К:
2C6H5CH3 + O2 C6H5CH=CHC6H5 + 2H2O
На второй стадии осуществляют собственно метатезис этилена со стильбеном в присутствии WO3 при температуре 723 К:
C6H5CH=CHC6H5 + C2H4 2C6H5—CH=CH2.
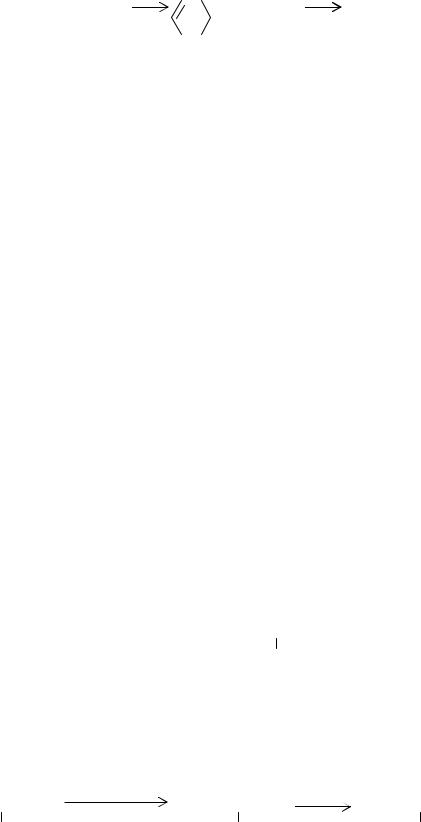
217
Получение стирола каталитической циклодимеризацией бутадиена.
Стирол можно получать каталитической циклодимеризацией бутадиена с последующим дегидрированием образующегося 4-винилциклогексена:
2CH2=CHCH=CH2 |
|
|
|
O2 C6H5CH=CH2 + H2O |
|
||||
|
|
|
|
CH=CH2 |
|
|
|
|
Термическую циклодимеризацию проводят в присутствии ингибиторов полимеризации. При 553 К и времени контакта 1 ч выход целевого продукта достигает 98% в пересчете на исходный бутадиен. Каталитическую циклодимеризацию бутадиена осуществляют в присутствии карбонилов железа.
Однако в настоящее время производство стирола из бутадиена экономически менее выгодно, чем из бензола.
6.1.2. Получение -метилстирола
Блоксополимеры типа термоэластопластов на основе диеновых углеводородов и -метилстирола характеризуется высокой температуростойкостью, совместимостью с другими полимерами, способностью к наполнению маслом и минеральными наполнителями. Улучшение этих свойств в сополимерах происходит за счет замены стирола как исходного мономера -метилстиролом.
Производство -метилстирола по объему значительно уступает сти-
ролу.
Основной метод получения -метилстирола заключается в каталитическом дегидрировании изопропилбензола. Этот процесс во многом аналогичен описанному выше процессу дегидрирования этилбензола. Поскольку условия термодинамического равновесия реакции дегидрирования для изопропилбензола более благоприятны, чем для этилбензола, -метилстирол синтезируют при температурах на 80-100о ниже, чем температура дегидрирования этилбензола. При степени превращения 60-70% селективность по целевому продукту превышает 90%.
-Метилстирол может быть получен также из кумола (изопропилбензол) через стадию его окисления.
На первой стадии – происходит окисление кумола в его гидропероксид:
C6H5CH(CH3)2 + O2 C6H5—C(CH3)2 OOH
Эта стадия аналогична стадии получения гидропероксида изопропилбензола в процессе синтеза фенола и ацетона.
На второй стадии гидропероксид кумола под влиянием щелочей превращается в диметилфенилкарбинол:
C6H5—C(CH3)2 |
NaOH |
C6H5—C(CH3)2 |
H2O |
C6H5—C(CH3)2 + 0,5O2 |
|
|
|
||||
|
|
||||
-H2O |
|
-NaOH |
|||
OOH |
|
OONa |
OH |
||
|
|
|
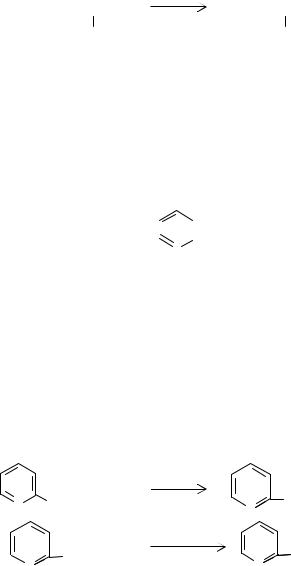
218
На третьей стадии последний подвергается каталитической дегидратации на оксиде алюминия при 593 К:
C6H5—C(CH3)2 |
- H2O |
C6H5—C=CH2 |
OH |
|
CH3 |
Этот метод менее экономичен по сравнению с прямым дегидрированием и поэтому в настоящее время его промышленная эксплуатация прекращена.
6.2. ВИНИЛПИРИДИНЫ
Винилпиридины
5 |
4 |
|
3 |
|
|
|
|
|
CH=CH2 |
||
|
|
|
|||
6 |
|
N |
|
2 |
|
|
|
|
|||
|
|
|
|
|
|
|
1 |
|
|
|
-бесцветные жидкости, хорошо растворимые в органических растворителях и плохо растворимые в воде. Физические характеристики винилпиридинов приведены в табл. 6.1.
Впервые 2-винилпиридин был синтезирован в 1887 г. при пропускании смеси пиридина с этиленом через раскаленную металлическую трубку. Позднее А. Ладенбургом был получен 2-винилпиридин с высоким выходом путем оксиметилирования 2-пиколина (2-метилпиридин) в 2-пиридилэтанол и дегидратации последнего в 2-винилпиридин:
N |
CH3 |
+ CH2O |
|
N CH2CH2OH |
||
N |
CH |
CH OH |
-H O |
N |
CH=CH2 |
|
|
2 |
2 |
2 |
|
Синтез винилпиридинов данным методом получил название "способ Ладенбурга".
Впервые винилпиридины были использованы для получения сополимеров в 30-х годах ХХ столетия. Германская фирма "И.Г. Фарбениндустри" попыталась заменить стирол в сополимере бутадиена со стиролом 2- винилпиридином. В дальнейшем основным направлением исследований по применению винилпиридинов явилось использование их для приготовления сополимеров с другими мономерами. Наибольшее распространение получили двойные сополимеры бутадиена или изопрена с винилпиридином и тройные сополимеры бутадиен-стирол-винилпиридин и бутадиен-акрилонитрил- винилпиридин. В этих сополимерах в качестве винилпиридинов обычно приме-
219
няют 2-винил-пиридин или 5-винил-2-метилпиридин, содержание которых в полимере колеблется в пределах 5-25%. Вулканизаты на основе таких сополимеров обладают рядом ценных свойств. Например, резины, приготовленные из бутадиен-винилпиридиновых каучуков, содержащих 15-25% 5-винил-2-метил- пиридина, превосходят соответствующие вулканизаты из бутадиен-стирольных каучуков по эластичности, сопротивлению истиранию, морозостойкости.
|
|
Таблица 6.1 |
|
|
Физические характеристики винилпиридинов |
|
|||
|
|
|
|
|
Пиридин |
Т кип., К/Па |
|
Т пл., К |
d420 |
2-Винилпиридин |
333/167 |
|
431,0 |
0,9757 |
3- Винилпиридин |
341/176 |
|
421,0 |
0,9879 |
4-Винилпиридин |
331/147 |
|
448,0 |
0,9836 |
5-Винил-2-метилпиридин |
348/147 |
|
433,0 |
0,9779 |
2-Винил-5-этилпиридин |
370/176 |
|
402,5 |
0,9449 |
Винилпиридиновые сополимеры в виде латексов широко применяются в качестве различного рода адгезивов, покрытий, клеев и т.д. Однако наибольшее применение латексы нашли в производстве шин. Пропитка шинного корда винилпиридиновыми латексами увеличивает сцепление корда с резиной, что приводит к повышению прочности шин. За рубежом для этих целей производятся в основном латексы в виде сополимеров бутадиена, стирола и винилпиридинов. В этих латексах используется 2-винилпиридин или 5-винил-2-метилпиридин. В нашей стране разработана технология производства латексов на основе сополимера бутадиена с 10% 5-винил-2-метилпиридина, полученного низкотемпературной сополимеризацией, а также сополимера того же состава, но полученного высокотемпературной полимеризацией, и сополимера бутадиена, стирола и 2-винилпиридина с соотношением мономеров 70:15:15. Для приготовления винилпиридиновых латексов возможно также использование 2-винил-5- этилпиридина.
Мономерный 5-винил-2-метилпиридин применяется в производстве поливинилпиридиновых каучуков.
Винилпиридины используются в текстильной промышленности, производстве ионообменных смол, кинофотоматериалов, физиологически активных препаратов.
6.2.1. Общая характеристика основных способов получения винилпиридинов
Синтез винилпиридинов осуществляется по двум принципиально различным схемам:
- дегидрирование этилпиридинов в соответствующие винилпиридины;
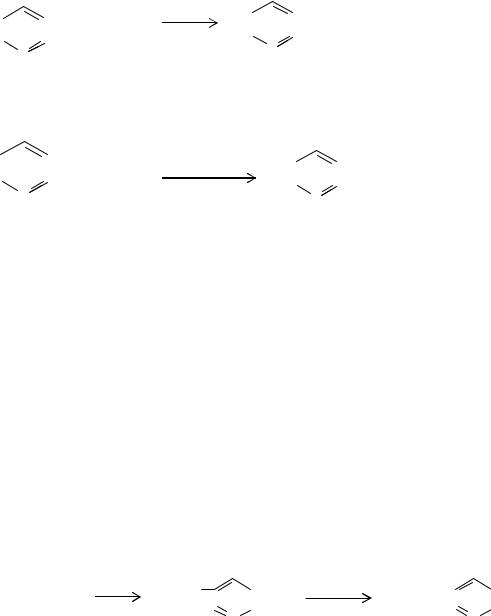
220
- оксиметилирование метилпиридинов в пиридилэтанолы с последующей дегидратацией их в винилпиридины.
Первый способ одностадийный. По этому способу можно получить в зависимости от строения молекул исходного сырья различные винилпиридины, например метилэтилпиридин, дегидрированием которого получают метилвинилпиридин.
Второй – двухстадийный способ синтеза винилпиридинов по методу Ладенбурга - основан на применении алкилпиридинов, имеющих метильные группы в 2-, 4- или в положении 6 пиридинового цикла. При конденсации таких алкилпиридинов с формальдегидом образуются соответствующие пиридилэтанолы:
R |
|
|
|
|
|
|
CH3 + CH2О |
R |
|
|
|
|
|
|
CH2CH2OH , |
|
|
|
|
|
|
|
|
|
|
|
|
||||
|
|
|
|
|
|
|
|
|
N |
|
|||||
|
|
|
|
N |
|
|
|
|
|
||||||
|
|
|
|
|
|
|
|
|
|
|
|
где R = H, CH3 или C2H5 в положении 3- или 5- пиридинового кольца. Каталитическая дегидратация этих пиридилэтанолов позволяет получать
соответствующие винилпиридины:
R |
|
|
|
|
|
|
CH2CH2OH Кат. |
R |
|
|
|
|
|
|
CH=CH |
|
|
|
|
|
|
|
|
|
|
|
|
||||
|
|
|
|
|
|
|
|
|
|
|
|
||||
|
|
|
|
N |
|
- H2O |
|
|
|
|
N |
2 |
|||
|
|
|
|
|
|
|
|
|
|
По данной схеме в промышленности освоен синтез 2- и 4-винилпиридинов и винилэтилпиридинов соответственно из 2- и 4-пиколинов и метилэтилпиридинов.
6.2.2. Промышленные методы получения винилпиридинов
Синтез 5-винил-2-метилпиридина
Этот способ получения 5-винил-2-метилпиридина включает стадию получения исходного алкилпиридина – метилэтилпиридина. Сырьем для его получения являются ацетальдегид и аммиак, причем первый применяется в виде его тримера – паральдегида.
При нагревании паральдегида с избытком NH3 в жидкой фазе при 473-523 К и давлении 5,0-10,0 МПа в присутствии ацетата или фторида аммония или уксусной кислоты образуется 2-метил-5-этилпиридин. Далее метилэтилпиридин подвергается дегидрированию:
4CH3—CHO + NH3 |
-н2о |
C2H5 |
|
|
CH3 |
-H2 |
CH2=CH |
|
|
|
|
CH3 |
|
|
|
|
|
|
|||||||
|
|
|
N |
|
|
|
N |
|
|