
monomers-Платэ-книга
.pdf441
адипиновой кислоты основаны на реакциях окисления циклогексана, циклогексанола, циклогексена различными окислителями, а также на реакциях озонолиза циклогексена и других ненасыщенных соединений. Адипиновую кислоту можно также получить из фурфурола через дихлорбутан и адипонитрил, карбонилированием тетрагидрофурана и другими способами.
В промышленности адипиновую кислоту преимущественно получают из циклогексана или фенола.
Синтез адипиновой кислоты из циклогексана
Процесс осуществляют в две стадии. На первой стадии проводят окисление циклогексана в циклогексанон и циклогексанол, а на второй – доокисление циклогексанона в адипиновую кислоту.
Окисление циклогексана воздухом. Окисление осуществляют в жидкой фазе при 418-448 К и 0,8-1 МПа в присутствии в качестве катализатора растворимых солей кобальта. Степень конверсии за один проход составляет 4-6%. Общий выход циклогексанона, циклогексанола, адипиновой кислоты и ее эфиров - свыше 80%.
Окисление в присутствии борной кислоты (процессы фирмы "Сайентифик дизайн и ФИН") позволяет повысить степень конверсии за проход до 10%, увеличить выход смеси циклогексанол-циклогексанон до 95% при мольном соотношении циклогексанол : циклогексанон, равном ( 9-10) : 1 вместо 1:1.
Дальнейшее окисление происходит с деструкцией цикла с образованием дикарбоновых кислот, среди которых преобладает кислота с тем же числом атомов углерода в цепи. Осуществить одностадийное окисление циклогексана до адипиновой кислоты с выходом более 50% не удается, поэтому оно практически не применяется. Доокисление продуктов окисления первой стадии осуществляют в двух вариантах: окислением азотной кислотой и воздухом.
Доокисление циклогексана. Реакция окисления циклогексана азотной кислотой с образованием адипиновой кислоты была впервые осуществлена Н.Д. Зелинским в 1903 г. Смесь, полученную на выходе из реактора окисления на первой стадии, обрабатывают 60%-ной азотной кислотой при давлении 0,2-1 МПа в присутствии меднованадатного катализатора. Реакция сильно экзотермична и поэтому процесс проводят в двух реакторах при 333-353 К и времени пребывания в них 57 мин. Выход адипиновой кислоты составляет 82-86% (мол.).
Окисление циклогексана воздухом проводится при 343-353 К и 0,7 МПа в присутствии ацетата меди и марганца как катализатора. В этом процессе выход адипиновой кислоты не столь высок, однако здесь меньше проблем с коррозией, что является значительным его достоинством.
Окисление циклогексана тетраоксидом азота. В промышленности разра-
ботан вариант получения адипиновой кислоты окислением циклогексана и его производных тетраоксидом азота. Окисление протекает в мягких условиях при 293-333 К и 0,10-0,3 МПа в жидкой фазе, при этом оксид азота восстанавлива-

442
ется до азота. В результате окисления получается смесь адипиновой, глутаровой, янтарной и щавелевой кислот.
Синтез адипиновой кислоты из тетрагидрофурана
Тетрагидрофуран получают гидрированием фурфурола или фурана, которые в свою очередь, получают из пентозанов - отходов продуктов сельского хозяйства.
Адипиновую кислоту можно получить из тетрагидрофурана через дибром- или дихлорбутан, образующийся при взаимодействии тетрагидрофурана с хлоридом или бромидом водорода:
H2C CH2
H2C CH2 + 2HCl Cl(CH2)4Cl + H2O.
O
Далее дихлорбутан обрабатывают цианидом натрия для получения динитрила адипиновой кислоты (адиподинитрил):
Cl(CH2)4Cl + 2NaCN N≡C(CH2)4C≡N + 2NaCl,
из которого омылением получают адипиновую кислоту.
Синтез адипиновой кислоты из фенола
По этому способу на первой стадии фенол гидрируют до циклогексанола в присутствии никелевого катализатора при ~423 К и 0,3 МПа. Конверсия фенола за один проход составляет 99,5%. На второй стадии проводят окисление циклогексанола в адипиновую кислоту, которое катализируется азотной кислотой в присутствии соединений ванадия или меди. Мольный выход адипиновой кислоты в расчете на превращенный фенол составляет 85-90% от теоретического.
Другие промышленные методы синтезы адипиновой кислоты
Прямое окисление циклогексана в уксусной кислоте (процесс фирмы
"Асахи"(Япония). Процесс осуществляют при 363-373 К в присутствии в качестве катализатора ацетата кобальта, конверсия за один проход составляет 5075%..
Карбометоксилирование бутадиена (процесс фирмы "БАСФ"). Процесс проводят в две стадии.
На первой стадии бутадиен реагирует с оксидом углерода и метанолом при 393 К и 6,0 МПа. В качестве катализатора используют октакарбонил кобальта, модифицированный азотсодержащими соединениями:
CH2=CH—CH=CH2 + CO + CH3OH CH3—CH=CH—CH2—COOCH3

443
На второй стадии ненасыщенный эфир подают в другой реактор со свежей смесью СО и СН3ОН. Реакция протекает при 458 К и при более низком давлении - 3 МПа. Метиладипинат образуется с выходом 75%.
СH3—CH=CH-CH2-СOOCH3+CO+CH3OH
→ CH3—OC(O)—(CH2)4— COOCH3.
Димеризация метилакрилата. Процесс включает стадии окисления пропилена в акриловую кислоту с последующей этерификацией кислоты метанолом:
CH2=CH—CH3 + O2 CH2=CH—COOH
CH2=CH—COOCH3.
Полученный метилакрилат димеризуют в присутствии PdCl2 и бензонитрила в качестве катализатора при 353 К в атмосфере азота. За 35 мин Степень конверсии за один проход составляет 45% при селективности по линейному димеру 92% (мол.):
2CH2=CH—COOCH3 CH3—COO—CH2—CH=CH—CH2—COOCH3.
Гидрированием и последующим гидролизом диэфира получают адипиновую кислоту.
11.2.2. Получение адиподинитрила
Адипонитрил (гександинитрил-1,6) – бесцветная маслянистая жидкость с т. заст. 276,5 К и т. кип. 568 К.
Адипонитрил используют главным образом для получения гексаметилендиамина. Его мировое производство превышает 1 млн. т/ в год.
Производство адиподинитрила базируется на трех видах сырья: адипиновой кислоте, бутадиене и акрилонитриле.
Синтез адиподинитрила из адипиновой кислоты
Реакция катализируется фосфорной кислотой согласно уравнению: HOОC—(CH2)4—COОH + 2NH3 NC—(CH2)4—CN + 4H2O.
Первоначально в парофазном процессе смесь аммиака и адипиновой кислоты в объемном соотношении 20:1 при 573-623 К превращали на фосфорнокислотном катализаторе в адипонитрил с селективностью по адипонитрилу 80%. В настоящее время процесс ведут в жидкой фазе по технологии, разработанной фирмами "Империал Камикал Индастриз" и "Монсанто" в расплаве кислоты при 473-573 К в присутствии фосфорной кислоты. Селективность по адипонитрилу составляет 90%.

444
Синтез адиподинитрила из бутадиена
Адиподинитрил из бутадиена может быть получен двумя методами: через дихлорбутены и прямым гидроцианированием.
Способ получения адиподинитрила через хлорирование бутадиена был разработан и реализован в промышленности фирмой "Дюпон" в 1950 г. Он включает три стадии: хлорирование бутадиена, гидроцианирование дихлорбутенов и гидрирование дицианбутенов.
Некаталитическое хлорирование бутадиена осуществляют в паровой фазе. В интервале температур 398-503 К при избытке бутадиена общая селективность по дихлорпроизводным бутадиена 96 %:
ClCH2—CH=CH—CH2Cl ~ 66% CH2=CH—CH=CH2 + Cl2 цис- + транс-
CH2=CH—CH(Cl)—CH2Cl ~ 33%
Гидроцианирование дихлорбутенов проводят в жидкой фазе при ~353 К в присутствии в качестве катализатора комплекса цианида меди.
ClCH2—CH=CH—CH2Cl — HCN
|→ NCCH2—CH=CH—CH2N.
CH2=CH—CH(Cl)—CH2Cl —
Селективность процесса составляет около 95%.
Гидрирование дицианбутенов проводят в паровой фазе при 573 К на паладиевом катализаторе. Селективность процесса составляет 95-97%.
Технология прямого цианирования бутадиена была разработана и реализована в промышленных условиях фирмой "Дюпон" в 1971 г. Способ осуществляется в две стадии.
На первой стадии сухая смесь бутадиена и хлорида водорода смешивается с циангидрином и азотом в мольном соотношении бутадиен: HCN:N2:HCl = 1:1:1:0,1 в присутствии в качестве катализатора хромата меди или магния при 483-493 К. В течение менее 1 ч смесь превращается в эта смесь превращается в смесь дицианбутенов:
НСl CH3—CH=CH—CH2—CN
CH2=CH—CH=CH2 + HCN |
1-цианбутен-2 |
HCl CH2=CH—CH2—CН2—СN
4-цианбутен-1
На второй стадии смесь линейных цианбутенов вновь обрабатывают циангидрином в присутствии в качестве катализатора комплекса никельтетра
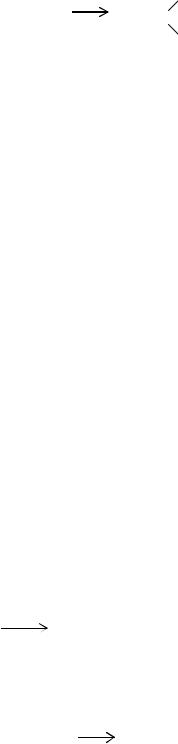
445
толуолфосфита и SnCl2 в качестве сокатализатора.
CH3—CH=CH—CH2—CN HCN |
CN |
+ |
(C2H2)4 |
СH2═CH—CH2—CH2—CN |
CN |
Синтез адиподинитрила из акрилонитрила электрохимическим методом
Димеризация акрилонитрила, совмещенная с гидрированием, осуществляется электрохимическим методом, который был разработан в 60-е годы фирмой "Монсанто" и реализован в промышленности как метод электрогидродимеризации. Другие фирмы, производящие полиамид-6,6 - «Асахи", "Дюпон", "Халкон", - разработали различные варианты этого процесса, по которым реакция проводится в электрохимической ячейке согласно схеме:
на катоде
2 CH2=CH—CN + 2H2O + 2e NC—(CH2)4—CN + 2OH- ;
на аноде
H2O 2H+ + 0,5O2 + 2e;
суммарная реакция
2 CH2=CH—CN + 2H2O NC—(CH2)4—CN +0,5O2.
Двухэлектронный механизм реакции предполагает образование дианиона :
- -
CH2=CH—CN + 2e CH2—CH—CN
с- последующей димеризацией с другой молекулой акрилонитрила:
- |
- |
- |
CH2—CH—CN + CH2=CH—CN |
CN—CH—CH2—CH2—CH—CN. |
Образующийся дианион нейтрализуется протонами, получаемыми электролизом воды:
- |
- |
NC—(CH2)4—CN |
NC—CH—(CH2)2—CH—CN + 2H+ |
Однако электрохимический способ получения адипонитрила отличается высоким потреблением энергии. Поэтому более перспективными являются чисто химические способы димеризации акрилонитрила.
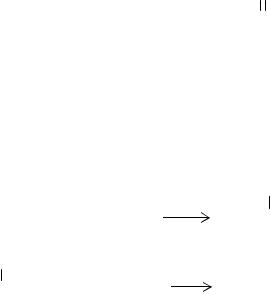
446
Каталитическая димеризация акрилонитрила
Процесс фирмы «Мицуи Тоатсу". В этом процессе в качестве гидрирующего агента используют амальгаму калия (в формамиде):
2CH2=CH—CN + 2K(Hg)n + H2SO4 NC—(CH2)4—CN + nHg + K2SO4.
Процесс фирмы "Халкон". Фирма "Халкон" разработала двухстадийный процесс димеризации акрилонитрила.
На первой стадии акрилонитрил димеризуется в метиленглутародинитрил:
CH2 2CH2=CH—CN NC—C—CH2—CH2—CN
Реакция протекает в жидкой фазе в присутствии в качестве катализатора цинк-п-толуиленцинксульфоната и триэтиламина.
На второй стадии разветвленный динитрил изомеризуется в присутствии 0,5% (мол.) цианида лития:
CH2 |
HCN |
CH2—CN |
||
|
|
|
NC—CH—CH2—CH2—CN |
|
NC—C—CH2—CH2—NC |
CH2—CN
NC—CH—CH2—CH2—CN -HCN NC—CH=CH—CH2—CH2—CN +
+NC—CH2—CH=CH—CH2—CN.
Врезультате получают 1,4-дицианбутены-1 и -2 с селективностью более 83% при степени конверсии за один проход более 70%.
Далее дицианбутены гидрируют на никеле Ренея в адиподинитрил или непосредственно в гексаметилендиамин.
Процесс фирмы "Империал Кемикал Индастриз". В процессе этой фирмы при димеризации сразу образуются линейные димеры. Катализатором служит фосфинит или фосфонит, используемый, как правило, в присутствии спирта (в качестве донора протона) при 303-373 К. Выход линейных димеров- 1,4-дицианобутенов-1 и -2 - превышает 95%. Их гидрируют так же как и в пре-
дыдущем процессе.
447
11.2.3. Получение гексаметилендиамина
Гексаметилендиамин (гександиамин-1,6; 1,6-диаминогексан) H2N(CH2)6NH2 представляет собой бесцветные кристаллы со слабым аммиач-
ным запахом; т. пл. 312-315 К, т. кип. 477-478 К.
Гексаметилендиамин был впервые синтезирован В.А. Солониной в 1896 г. взаимодействием пробковой кислоты с бромом и NaOH (реакция Гофмана).
Практически весь производимый в мире гексаметилендиамин используется для производства полиамида-6,6 (95%) и гексаметилендиизоцианата O=C=N—(CH2)6—N=C=О. Последний применяют для производства некоторых полиуретанов, полиимидов и других полимеров.
Гексаметилендиамин получаются каталитическим гидрированием адиподинитрила или через промежуточное получение гександиола-1,6. Процессы получения гексаметилендиамина из адипиновой кислоты и диамина представлены на схеме 11.2.
Синтез гексаметилендиамина из адипиновой кислоты
Достоинством этого процесса (см. схему 11.2) является то обстоятельство, что гексаметилендиамин может быть получен именно из адипиновой кислоты.
На первой стадии происходит испарение адипиновой кислоты в газообразном аммиаке и дегидратирование газообразной смеси с образованием динитрила.
На второй стадии - гидрирование адиподинитрила:
NC—(CH2)4—CN + 4H2 H2N—(CH2)6—NH2 .
Процесс осуществляют на кобальтовом или медном катализаторе при давлении 60-65 МПа и температуре 373-408 К. Селективность процесса состав-
ляет 90-95%.
Фирма "Рон Пуленк" разработала процесс получения гексаметилендиамина при низком давлении. Процесс проводят при 348 К и 3 МПа в жидкой фазе с использованием суспензии никелевого катализатора в едком натре. Селективность по гексаметилендиамину составляет 99%.
Основным побочным продуктом реакции являются диимины, образующиеся из-за неполного гидрирования адиподинитрила:
NС—(CH2)4—CN + 2H2 HN═СН—(CH2)4—СН═NH.
Имины могут реагировать с аминами с образованием вторичных и третичных аминов.
Получение гексаметилендиамина из адипиновой кислоты практически лишено существенных недостатков и поэтому наиболее широко распространено в промышленности.
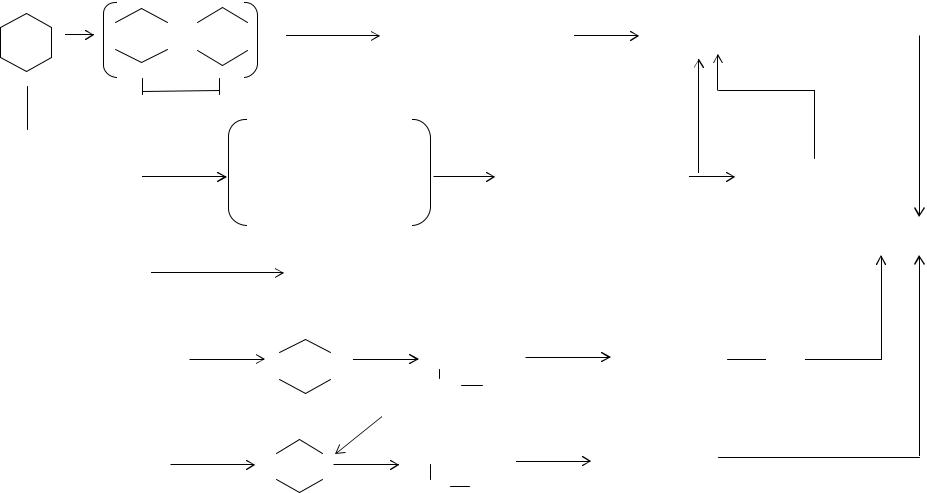
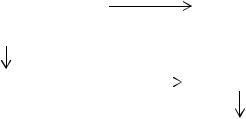
449
Синтез гексаметилендиамина через гександиол-1,6
Фирма "Селаниз" разработала и реализовала в промышленности трехстадийный процесс получения гексаметилендиамина через промежуточное образование гександиола-1,6. На первой стадии циклогексан окисляют при 423 К и давлении 3,3 МПа для получения смеси адипиновой кислоты и гидроксикапроновой кислоты. Смесь кислот этерифицируют гександиолом, полученным предварительно.
На второй стадии эфир подвергают гидрогенолизу с получением гексан- диола-1,6, который подвергают очистке.
На третьей стадии диол аминируют аммиаком на катализаторе Ni Ренея при 473 К и 23,0 МПа. Гексаметилендиамин получают с выходом 90% (мол.). В качестве побочных продуктов образуются гексаметиленимин и 6-аминогексан.
Достоинством этого процесса является возможность объединения стадий получения циклогексана и стадии получения исходного соединения в производстве адипиновой кислоты. К недостаткам процесса следует отнести его многостадийность и низкое качество образующегося амина.
Синтез гексаметилендиамина из бутадиена
Впервые этот процесс был разработан и освоен в промышленном масштабе фирмой "Дюпон". Схематически он представлен на схеме 11.2. Выход адиподинитрила в этом процессе почти такой же, как и в процессе на основе адипиновой кислоты. Несмотря на такие достоинства процесса, как низкая стоимость бутадиена, достаточно высокие степень конверсии и выход продукта, использование значительных количеств цианистого водорода и хлора отрицательным образом сказывается на капитальных расходах.
Позднее фирма "Дюпон" разработала более перспективный с коммерческой точки зрения процесс получения гексаметилендиамина из бутадиена без применения хлора. В результате этого стоимость адиподинитрила удалось понизить на 15%. Основные стадии усовершенствованного процесса:
CH2=CH-CH=CH2 + HCN Ni-кат.
Смесь мононитрилов
Разделение и изомеризация
Пентеннитрилы HCN Динитрилы
Разделение
Адиподинитрил .
Другой способ получения адиподинитрила из бутадиена был разработан фирмой "Эссо Рисерч энд Инжиниринг". По этому способу бутадиен взаимодействует с цианидами иода и меди. При этом образуется медноиодного комплекс дегидроадиподинитрила, который затем обрабатывают HCN для повышения
450
выхода дегидроадиподинитрила и восстановления цианидов иода и меди. Возможность рециркуляции компонентов, образующих комплексное соединение, делает этот процесс экономически довольно выгодным.
Димеризация акрилонитрила
Этот процесс был создан фирмой "Монсанто" и реализован в промышленности в 1965 г.(см. Схему 11.2). Акрилонитрил, полученный из пропилена, растворяется в водном растворе тетраэтиламмоний-п-толуолсульфоната в электролитической ванне. Димеризация осуществляется в результате протекания восстановительных реакций на катоде. Главным достоинством этого способа является использование в качестве исходного сырья дешевого акрилонитрила, а недостатком - сравнительно большое потребление энергии.
11.2.4.Получение других мономеров для синтеза полиамидов
Для синтеза полиамидов можно использовать также димеры ненасыщенных карбоновых кислот, получаемых из природных масел. Однако эти полимеры имеют чрезвычайно низкие температуры плавления, низкую степень кристалличности и невысокий начальный модуль, что препятствует их применению для выработки волокон.
Для увеличения растворимости и прозрачности полиамида при его получении можно использовать разветвленные дикарбоновые кислоты, в частности, -,-диэтиладипиновую и -этил-пробковую кислоты. Волокна из таких полимеров обладают хорошей способностью к холодной вытяжке. Однако из-за низкой кристалличности прочность этих волокон очень мала. Такой же небольшой прочностью обладают волокна на основе N-алкилированных диаминов, в то же время они высокоэластичны, что позволяет использовать их для изготовления некоторых бытовых изделий.
Волокна, полученные из высших ненасыщенных дикарбоновых кислот и первичных диаминов, обладая малой прочностью и низкой термостойкостью, значительно превосходят промышленные образцы полиамидов-6 и -6,6 стойкостью к-облучению.
Таким образом, увеличение длины углеродной цепи в кислоте или амине, разветвление основной полимерной цепи или введение в нее гетероатомов приводит к уменьшению степени кристалличности полимера, что, в свою очередь, ведет к снижению температуры плавления и ухудшению волокнообразующих свойств.
Поэтому с учетом изложенного выше можно было бы ожидать наличие интересных свойств у полиамидов на основе щавелевой кислоты:
nH2N—R—NH2 + nHOOC—COOH [—NH—R—NHCO—CO—]n