
Radzevich, S.P. Monograph - 2001
.pdf
510 |
8. Синтез наивыгоденйшего формообразования поверхностей деталей |
|
подстановкой в них выражений (81). |
|
|
Пример 8.19. Рассмотрим задачу параметризации сферического участка поверхности |
Д детали некоторого радиуса R , имеющей |
|
эксцентрично (с эксцентриситетом c ) расположненное отверстие, проекция области Д |
которой на плоскость координат O1 xy име- |
|
ет вид (рис. 8.36). |
|
|
|
Y |
|
Y |
|
|
|
1 |
|
|
|
|
Z1 |
Z |
|
|
|
A |
|
|
|
|
|
|
|
|
|
|
|
|
|
|
R0 |
|
|
|
|
|
|
|
||
H |
R |
O1 |
|
C |
|
O |
|
|
|
x(x1 ) |
|
|
b |
|
|
|
|
|
|
|
|
|
Rn |
|
x(x ) |
|
|
R |
|
|
1 |
C |
|
|
|
|
|
|
|
Рис. 8.36. Параметризация поверхности детали в виде полусферы с эксцентрично расположенным отверстием.
Обозначим через b расстояние между плоскостью граничного среза поверхности Д и плоскостью координат O1 xy . Используем последнюю в качестве координатной плоскости. Область 0 Д0 в рассматриваемом случае является двусвязной. Полюс полярной систе-
мы координат целесообразно совместить с точкой O (см. рис. 8.36). Если принять 1н rн R0 , это позволяет считать F1н 0 .
Чтобы найти длину отрезка |
AB , рассматрим треугольники OAO1 |
и OAC , из анализа которых запишем |
|||||||
(8.82) |
|
OC c RП cos OAsin ; |
|||||||
|
|
OA |
|
RП |
|
|
RП |
||
(8.83) |
|
sin |
|
|
|
|
|
|
. |
|
|
|
|
|
cos |
||||
|
|
|
sin |
2 |
|
||||
|
|
|
|
|
|
Из равенства (83) находим, что
cos 1 OA2 cos 2 ,
RП2
подставляя которое в (82), получим
(8.84) OA2 2 OA c sin c2 RП2 0 .
Принимая во внимание равенство F1к OA R (см. рис. 8.36), из (84) найдем
F1к c sin R RП2 c2 cos 2
Функция F1(r, ) определяется формулой
(8.85) |
F1 (r, ) A( ) r B( ) , |
где в силу F1н 0

|
|
|
|
|
|
8.6. Репараметризация поверхности детали |
|
|
|
|
|
|
|
|
511 |
|||||||||||||||
|
|
|
|
|
|
|
R H к ( ) |
|
|
|
|
H |
к ( ) |
|
|
|
|
|
|
|
|
|
|
|
|
|||||
|
|
|
|
|
|
A( ) |
0 |
|
1 |
|
|
; |
|
B( ) |
|
1 |
|
. |
|
|
|
|
|
|
|
|
(8.86) |
|||
|
|
|
|
|
|
R0 R |
|
|
|
R0 |
R |
|
|
|
|
|
|
|
|
|
||||||||||
|
|
|
|
|
|
|
|
|
|
|
|
|
|
|
|
|
|
|
|
|
|
|
|
|
|
|||||
Построим теперь функцию |
H(r, ) , входящую в уравнение (78) |
и определяющую отображение области |
Д0 |
на область Д . Из |
||||||||||||||||||||||||||
уравнения поверхности x2 y2 |
z2 R2 для точек верхней полусферы |
|
|
|
|
|
|
|
|
|||||||||||||||||||||
Д |
запишем |
z |
R2 x2 |
y2 . Перенося начало координат в |
||||||||||||||||||||||||||
точку O и имея в виду, что H Z , получим |
|
|
|
|
|
|
|
|
|
|
|
|
|
|
|
|
|
|
|
|
|
|
|
|
||||||
|
|
|
|
|
|
|
|
|
|
|
|
|
|
|
|
|
|
|
|
|
|
|
|
|
|
|
|
|||
|
|
|
|
|
|
|
|
H |
|
R2 (x c)2 |
y |
2 |
|
|
|
|
|
|
|
|
|
|
|
|
|
|
(8.87) |
|||
|
|
|
|
|
|
|
|
|
|
1 |
|
1 |
|
|
|
|
|
|
|
|
|
|
|
|
|
|
|
|||
Радиус-вектор r 0 |
определяет точку с координатами r* r F1 и |
, поэтому |
|
|
|
|
|
|
|
|
|
|
|
|
|
|||||||||||||||
|
|
|
|
|
|
|
x1 |
r * sin (r |
F1 ) sin ; |
|
|
|
|
|
|
|
|
|
|
|
|
|
(8.88) |
|||||||
|
|
|
|
|
|
|
y |
r * cos (r |
F ) cos , |
|
|
|
|
|
|
|
|
|
|
|
|
|
||||||||
|
|
|
|
|
|
|
|
1 |
|
|
|
|
1 |
|
|
|
|
|
|
|
|
|
|
|
|
|
|
|
|
|
где функция F1 |
определяется формулой (85). Внося (87) и (88), для функции H(r, ) окончательно получим |
|
|
|
|
|||||||||||||||||||||||||
|
|
|
|
|
|
|
|
|
|
|
|
|
|
|
|
|
|
|||||||||||||
|
|
|
|
|
|
H (r, ) |
R2 c2 (r H1 )2 2(r H1 ) c sin . |
|
|
|
|
|
|
|
|
(8.89) |
||||||||||||||
Далее для поверхности |
Д могут быть найдены компоненты первого и второго метрических тензоров, а также символы Кристоффеля |
|||||||||||||||||||||||||||||
второго рода. |
|
|
|
|
|
|
|
|
|
|
|
|
|
|
|
|
|
|
|
|
|
|
|
|
|
|
|
|
|
|
Приведенное решение справедливо лишь для случая, |
когда b 0 . При b 0 во всех точках, соответствующих r R , угол между |
|||||||||||||||||||||||||||||
векторами r1 и r10 становится равным , что приводит отображение (78) к вырождению. |
|
|
|
|
|
|
|
|
|
|||||||||||||||||||||
|
|
|
|
|
|
2 |
|
|
|
|
|
|
|
|
|
|
|
|
|
|
|
|
|
|
|
|
|
|
|
|
8.7.4. Приведение квадратичных форм к главным осям. Под квадратичной формой относительно пе- |
||||||||||||||||||||||||||||||
ременных u |
, u |
2 |
, |
, u |
n |
понимается выражение вида |
uT A u , где |
|
u u , u |
2 |
, , u |
n |
и |
A a |
ik |
– симме- |
||||||||||||||
1 |
|
|
|
|
|
|
|
|
|
|
|
|
|
|
|
|
|
|
|
1 |
|
|
|
|
|
|||||
тричная матрица, |
aik |
– действительные числа. Матрицу A принято называть матрицей квадратичной фор- |
мы. Для решения задачи синтеза наивыгоднейшего формообразования поверхностей деталей интерес, в первую очередь, представляют случаи, когда u1 U д и u2 Vд .
Например, выражение Φ1.д dUд2 6 dUдdVд 4dVд2 является квадратичной формой, так как
Φ |
dU |
|
|
1 |
3 |
dU |
д |
|
|
|
, dV |
|
|
|
|
uT A u . |
|||
1.д |
|
д |
д |
3 |
4 |
|
dV |
|
|
|
|
|
|
|
|
|
|
д |
|
Задача репараметризации поверхности детали в рассматриваемом случае сводится к нахождению такой ортогональной матрицы C , которая после введения новых переменных v1 , v2 , , vn при помощи уравне-
ния вида u C v преобразует заданную квадратичную форму к виду: |
|
|
|||||
uT A u |
v2 |
|
v2 |
|
v2 |
, |
|
|
u C v |
1 1 |
|
2 2 |
|
n n |
|
|
|
|
|
|
|
|
который содержит только слагаемые с квадратами текущих координат. Такой вид квадратичной формы явля-
ется каноническим.
После замены переменных u C v форма uT A u преобразуется к виду vT CT A C v и содержит слагаемые только с квадратами переменных. Таким образом, задача репараметризации поверхности дета-
ли сводится к нахождению такой ортогональной матрицы C , которая приводит матрицу CT A C к диагональному виду. Это всегда можно выполнить для симметричной матрицы A , если в качестве столбцов искомой матрицы C выбрать ортонормированную систему собственных векторов матрицы формы A . Тогда по-

512 |
8. Синтез наивыгоденйшего формообразования поверхностей деталей |
|
|
|
|
||||
средством замены |
u C v |
квадратичная форма приводится к виду v2 |
|
v2 |
|
v2 |
, где |
i |
– соб- |
|
|
1 1 |
|
2 2 |
|
n n |
|
|
ственные значения матрицы A с учетом кратности. Собственные векторы матрицы A , стоящие в столбцах C , называются главными осями квадратичной формы, а процесс преобразования квадратичной формы в ее ка-
ноническую форму – приведением к главным осям или приведением к каноническому виду.
8.8.Обобщенная структура системы автоматизации программирования обработки сложных поверхностей деталей на многокоординатных станках с ЧПУ
Разработка высокоэффективного процесса формообразования сложной поверхности детали на многокоординатном станке с ЧПУ включает ряд основных задач:
-определение наивыгоднейшей ориентации детали на столе многокоординатного станка с ЧПУ;
-установление формы и параметров исходной инструментальной поверхности И применяемого инстру-
мента в функции обрабатываемой поверхности Д детали;
-решение траекторных задач – расчет параметров наивыгоднейших траекторий формообразования сложной поверхности детали;
-нахождение положения и вычисление координат наивыгоднейшей точки начала формообразования по-
верхности Д на многокоординатном станке с ЧПУ и др.
Решение перечисленных задач и проблемы синтеза наивыгоднейшего формообразования вцелом может быть получено на основе применения дифференциально-геометрического метода формообразования поверхностей при механической обработке деталей. Этот метод позволяет синтезировать процесс формообразования исходя из достижения максимальной его эффективности при гарантированном обеспечении заданной точности обработки.
Практическое решение этой проблемы требует разработки САП – системы автоматизации программирования обработки сложных поверхностей деталей на многокоординатных станках с ЧПУ (Радзевич С.П., 1988).
В качестве входной в САП используется информация (I) о форме, параметрах и требованиях к точности
|
|
|
|
|
формообразования |
поверхности |
II |
|
VI |
Д детали (рис. 8.37). Исходя из |
|||
|
|
|
|
|
этого для обрабатываемого участ- |
|
|
|
|
|
|
||
|
|
|
|
|
ка поверхности Д |
определяется |
|
|
|
|
|
Начало |
|
|
I |
|
|
III |
|
|
IV |
|
|
V |
|
Конец |
(II) наивыгоднейшая его ориента- |
||
|
|
|
|
|
|
|
|
|
|||||||||
|
|
|
|
|
|
|
|
|
ция на столе станка с ЧПУ. Затем |
||||||||
|
|
|
|
|
|
|
|
|
|
|
|
|
|
|
|
||
|
|
|
|
|
|
|
|
|
|
|
|
|
|
|
|
профилируется (III) специальный |
|
|
|
|
|
|
|
|
|
|
|
|
|
|
|
|
|
||
|
|
|
|
|
|
|
|
|
|
|
|
|
|
|
|
режущий инструмент для обра- |
|
|
|
|
VII |
|
|
|
|
|
|
|
|
|
|
|
|||
|
|
|
|
|
|
|
|
|
|
|
|
|
|
ботки заданной детали. После |
|||
|
|
|
|
|
|
|
|
|
|
|
|
|
|
|
|
этого решаются (IV) траекторные |
|
Рис 8.37. Основные этапы решения задачи синтеза наивыгоднейшего |
задачи и устанавливается (V) по- |
||||||||||||||||
ложение наивыгоднейшей точки |
|||||||||||||||||
|
формообразования сложных поверхностей деталей на мно- |
||||||||||||||||
|
начала обработки. |
||||||||||||||||
|
гокоординатных станках с ЧПУ |
|
|
|
|
|
Если имеется возможность |
||||||||||
|
|
|
|
|
|
|
|
|
|
|
|
|
|
|
|
выбора готового инструмента из имеющейся его номенклатуры, по требуемому критерию эффективности формообразования выбирается наивыгоднейший инструмент из имеющегося в наличии (VI). Дополнительно могут быть учтены (VII) требования по поддержанию в процессе обработки заданных (не обязательно экстремальных) параметров геометрии касания поверхностей Д и И .
На базе дифференциально-геометрического метода формообразования поверхностей может быть разработано реализуемое на ЭВМ полное математическое обеспечение САП обработки на многокоординатных станках с ЧПУ сложных поверхностей деталей (рис. 8.38).
На первом этапе САП определяются основные геометрические параметры формы поверхности Д , заданной (1) известным методом. В случае аналитического задания поверхности Д детали (2) вводится (3) ее уравнение, затем расчитываются (4) первые и вторые производные. После этого определяются (5) гауссовы

514 |
8. Синтез наивыгоденйшего формообразования поверхностей деталей |
тичных форм поверхности |
Д в подсистеме (II) расчитываются (15) параметры наивыгоднейшей ориентации |
поверхности Д на столе станка с ЧПУ, которые подаются (16) на выход этой подсистемы.
Подсистема (III) профилирования фасонного режущего инструмента для обработки сложных поверхностей деталей на многокоординатных станках с ЧПУ функционирует по результатам расчетов, произведенных
в подсистеме (I): по значениям гауссовых коэффициентов Eд , Fд , Gд и Lд , Mд , Nд поверхности Д . В
случаях, когда имеется возможность для заданной детали спроектировать, изготовить, перетачивать и контролировать специальный фасонный режущий инструмент, принимается (17) решение о его профилировании и
изготовлении. Для этого на основе -отображения поверхностей (см. гл. 5) расчитываются (18)-(19) гауссовы коэффициенты Eи , Fи , Gи и Lи , Mи , Nи первых двух основных квадратичных форм Φ1.и и Φ2.и исходной
инструментальной поверхности И , которые подаются (20) на выход подсистемы (III). По начальным условиям (21), определяющим положение инструмента в системе координат станка с ЧПУ, и гауссовым коэффициентам первых двух основных квадратичных форм (19) определяются (22) параметры формы и геометрии наивыгоднейшей поверхности И инструмента, которые затем выводятся (23) на печать. Подсистема (VII) САП допускает возможность профилирования такого специального фасонного режущего инструмента, при использовании которого в процессе формообразования обеспечиваются (24) наивыгоднейшие значения параметров геометрии касания поверхностей Д и И и тем самым достигается максимум его эффективности.
Если нет возможности для заданной детали спроектировать и изготовить специальный фасонный режущий инструмент, принимается (17) решение о выборе (25) наилучшего инструмента из имеющейся его номенклатуры либо о программировании обработки для заданного инструмента.
В первом случае производится:
(27) (28) (29)
определение параметров формы поверхности Иi всех инструментов из его номенклатуры, на основании чего
имеющиеся в наличии инструменты сопоставляются (30) между собой по эффективности их использования для формообразования заданной поверхности Д детали и производитсся (31) выбор наилучшего инструмен-
та. Гауссовы коэффициенты Eи , Fи , Gи и Lи , Mи , Nи первых двух основных квадратичных форм Φ1.и и Φ2.и поверхности И выбранного инструмента подаются (20) на выход подсистемы (III).
Во втором случае, когда инструмент задан, по уравнению его исходной инструментальной поверхности И расчитываются
(33) (34) (35) (32)
гауссовы коэффициенты Eи , Fи , Gи и Lи , Mи , Nи , которые затем подаются (20) на выход подсистемы
(III).
Результатом работы подсистемы (III) является полная информация об исходной инструментальной поверхности наивыгоднейшего в конкретных условиях обработки инструмента.
Синтез наивыгоднейших траекторий формообразования производится в подсистеме (IV). Для этого рас-
читываются (36) параметры ортов n д и n и нормалей к поверхностям |
Д и И , после чего поверхность И |
|
вводится (37) в касание с поверхностью |
Д путем совмещения орта n и |
с противоположным направлением ор- |
та n д в точке К касания поверхностей |
Д и И . Затем проверяется (38) выполнение условий формообразова- |
ния поверхностей деталей, в случае возможного нарушения которых (39) вводится (40) коррекция на положение инструмента относительно детали. Если условия формообразования поверхностей деталей выполняются (39) и формообразование поверхности Д производится (41) при постоянной ширине строки формообразова-
ния, то наивыгоднейшие траектории формообразования расчитываются (42) как линии, эквидистантные к геодезической линии наибольшей длины на обрабатываемом участке поверхности Д с учетом (43), при необхо-
димости, влияния на параметры траекторий формообразования формы и параметров границ контура участка поверхности Д (с учетом краевого эффекта), после чего параметры наивыгоднейших для данного случая об-
работки траекторий формообразования подаются (44) на выход подсистемы (IV).
8.8. Обобщенная структура системы автоматизации программирования обработки сложных поверхностей деталей |
515 |
на многокоординатных станках с ЧПУ |
|
Если обработка детали производится (41) инструментом, исходная инструментальная поверхность И которого касается поверхности Д в точке (это наиболее распространенный случай касания поверхностей Д и
И при обработке сложных поверхностей деталей на многокоординатных станках с ЧПУ), расчитываются (45) параметры индикатрисы конформности Indconf Д / И поверхностей Д и И , затем движениями ориентиро-
вания второго рода с заданной точкой на поверхности Д вводится (46) в касание наивыгоднейшая точка по-
верхности И и движениями ориентирования первого рода инструмент наивыгоднейшим образом ориентируется (47) относительно детали.
Далее, если для обработки используется (48) инструмент, полностью воспроизводящий поверхность И (а это практически все абразивные инструменты, инструменты типа шеверов и пр.), устанавливается (49) наивыгоднейшее направление мгновенного относительного движения формообразования, совокупность которых определяет (50) наивыгоднейшие траектории формообразования. После учета (51), при необходимости, влияния краевого эффекта и степени интерференции (52) соседних строк формообразования параметры наивыгоднейших траекторий формообразования подаются (44) на выход подсистемы (IV).
Если обработка детали производится (48) инструментом, дискретно воспроизводящим исходную инструментальную поверхность И в виде конечного числа отдельных редущих кромок (это практически все виды фасонного лезвийного режущего инструмента), предварительно учитываются (53) ограничения на параметры наивыгоднейших траекторий формообразования дискретности воспроизведения в реальном инструменте его поверхности И , производится (54) распределение допуска на точность между элементарными составляющими результирующей погрешности формообразования и учитываются (55) ограничения на параметры траекторий формообразования, накладываемые критическими значениями кинематических геометрических параметров режущих кромок лезвийного инструмента. Далее обработка информации в САП производится в такой последовательности:
(55) (49) (50) (51) (52) (44)
Результатом функционирования этапа (IV) в САП (см. рис. 8.38) являются параметры наивыгоднейших
траекторий формообразования сложной поверхности детали на многокоординатном станке с ЧПУ. Последняя (V) подсистема позволяет расчитать координаты наивыгоднейшей точки начала обработки
сложной поверхности детали – точки, в которую в начале обработки перемещается инструмент из стартовой точки. Для этого устанавливается (56) непересекающаяся сеть линий на поверхности Д , из которой выше бы-
ли выбраны наивыгоднейшие траектории формообразования. При необходимости учитывается влияния краевого эффекта и других ограничений на наивыгоднейшие направления движений формообразования. Из полученного семейста линий отбираются (57) две линии, касательные с проитивоположных сторон к контуру, ограничивающему обрабатываемый участок поверхности Д или совпадающие с ним. После этого из точек ка-
сания крайних линий построенной указанным путем сети линий на Д производится (58) смещение от ограни-
чивающего контура в сторону детали на полшага между соседними строками формообразования. Вдоль полученных таким образом наивыгоднейших крайних траекторий отсчитываются (59) расстояния от контура, необходимые для врезания инструмента в заготовку и вывода его из контакта с ней. Из полученных точек выбирается (60) одна, при обработке начиная с которой при прочих одинаковых условиях обеспечивается наивысшая эффективность формообразования. Координаты выбранной точки начала обработки подаются (61) на выход подсистемы (V).
Процедура выбора одной точки из найденных может быть дополнена (62) информацией об особенностях врезания инструмента в заготовку и вывода его из контакта с ней (попутное или встречное фрезерование, тип применяемого режущего инструмента и др.), выбором такой точки, при движении из которой суммарная длина траекторий врезаний-выходов инструмента минимальна, а также другими дополнительными требованиями.
Система автоматизации программирования (см. рис. 8.38) является потенциально полной. Она допускает возможность учета информации не только о форме, параметрах и требованиях к точности формообразования сложной поверхности детали, но и информации о физических процессах, всегда протекающих в реальном процессе обработки деталей на металлорежущих станках. Это позволит на более высоком уровне синтезировать технологии наивыгоднейшей обработки сложных поверхностей деталей на многокоординатных станках с ЧПУ.
Гл а в а 9. Топология формообразованных поверхностей деталей
Кважнейшим показателям качества деталей относится их точность. Требования к точности изготовления изделий непрерывно растут, а темпы этого роста более высокие, чем темпы роста возможностей технологии и оборудования для обеспечения требуемого ее уровня.
Одним из аспектов точности является топология обработанных поверхностей деталей.
Топология поверхностей деталей изучает некоторые из составляющих результирующей погрешности – те из них, которые определяются геометрией поверхности детали и исходной инструментальной поверхности, их относительной ориентацией и параметрами кинематики формообразования.
Как это принято (Исаев А.И., 1950; и др.), ниже топология обработанных поверхностей рассматривается только с учетом погрешностей, вносимых собственно процессом формообразования – с учетом остаточного детерминированного регулярного микрорельефа на обработанной поверхности детали. Величины возникающих при этом погрешностей всегда могут быть расчитаны аналитически. Для этого достаточно сведений о ге-
ометрии поверхностей Д и И , их относительной ориентации и параметрах кинематики формообразования.
Погрешности оборудования и оснастки, погрешности ориентирования, базирования и крепления детали и инструмента и др. при этом во внимание не принимаются. Не рассматриваются также погрешности, для расчета величин которых дополнительно требуется информация о физических процессах, протекающих при обработке деталей на металлорежущих станках.
Принятый подход правомерен и согласуется с основным допущением в теории формообразования поверхностей деталей (см.выше, с. 22, допущение 1.1).
9.1. Дополнительные допущения
Для обработки многих деталей характерно точечное касание поверхности Д детали и исходной инструментальной поверхности И . Например, точечное касание поверхностей Д и И имеет место при нарезании
зубчатых колес, шлицевых валов и других зубчатых деталей червячными фрезами и др. При обработке сложных поверхностей деталей на многокоординатных станках с ЧПУ точечное касание поверхностей Д и И
имеет место практически всегда – такой вид их касания является превалирующим. В связи с тем, что при точечном касании потренциальные возможности кинематики формообразования наибольшие, с этой точки зрения точечный вид касания поверхностей Д и И следует рассматривать как наиболее общий.
При точечном касании сопряженных поверхностей в течение конечного промежутка времени нельзя геометрически точно формообразовать поверхность детали движением одной точки К касания поверхностей Д
и И . Аналогичное наблюдается при линейном касании этих поверхностей, но дискретном воспроизведении в реальном инструменте его поверхности И . Обобщая, можно утверждать, что точечное касание поверхностей Д и И и дискретное воспроизведение в реальном инстременте исходной инструментальной поверхности И
как по отдельности, так и в совокупности, исключают возможность геометрически точного формообразования номинальной поверхности Дн детали. В этом случае имеет место дискретное формообразование, при кото-
ром неизбежно образуются принципиально неустранимые без последующей обработки детали погрешности в виде остаточного детерминированного регулярного микрорельефа. В соответствие с шестым условием формообразования поверхностей деталей (см. выше, с. 382-383, раздел 7.1.6) величины этих погрешностей не должны превышать допуск на точность обработки.
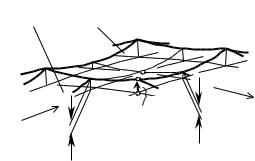
|
9.1. Дополнительные допущения |
517 |
||
|
|
|
Определение 9.1. Дискретное формообразование |
|
Дн |
Др |
|
поверхностей деталей – это формообразование, кото- |
|
|
рое имеет место при точечном касании поверхности |
|||
|
|
(m 1) |
детали и исходной инструментальной поверхности, |
|
|
K |
при дискретном воспроизведении в реальном инстру- |
||
|
1) |
менте его исходной инструментальной поверхности |
||
|
(n |
|||
n |
|
|
или при точечном касании поверхностей Д и И и дис- |
|
m |
S П |
|
кретном вопроизведении поверхности И одновременно. |
|
SВ |
n д.нh |
|
Дискретное формообразование не только допуска- |
|
hП |
|
|||
|
|
ется, но и находит широкое применение в машиностро- |
||
|
hВ |
|
||
|
|
ении. Это объясняется тем, что на размеры, форму и |
||
|
|
|
||
|
|
|
шероховатость обработанных поверхностей деталей за- |
|
|
|
|
даются предельные отклонения. Поэтому допустимо, |
|
Рис. 9.1 Элементарная ячейка на обработанной по- |
чтобы заданная чертежом номинальная поверхность |
|||
|
верхности детали. |
|
совпадала с обработанной поверхностью детали лишь |
|
|
|
|
частично, но с требуемой точностью. |
|
|
|
|
При дискретном формообразовании |
остаточный |
детерминированный регулярный микрорельеф на обработанной поверхности детали образуется неизбежно, а причины этого явления достаточно очевидны. В процессе обработки режущие кромки зубьев инструмента, совершая сложное многопараметрическое движение относительно заготовки, описывают дискретное семейство поверхностей резания, которые разделяют операционный припуск на срезанные и несрезанные (остаточные) части. В результате интерференции соседних поверхностей резания, образованных не обязательно смежными режущими кромками многолезвийного инструмента или единственной режущей кромкой однолезвийного инструмента, образуются остаточные гребешки, что является причиной появления органических погрешностей обработанных поверхностей деталей.
Результирующая погрешность формообразования h определяется высотой гребешков hВ волнистости, образованной вдоль строк формообразования, и высотой гребешков hП огранки, образованной поперек строк формообразования. Обе составляющие hВ и hП , как и сама результирующая погрешность h , отсчитываются вдоль нормали n д.н к номинальной поверхности детали Дн .
Из-за трудностей измерения и дефицита измерительных средств величины элементарных погрешностей hВ и hП обычно расчитывают. Во многих случаях расчетные значения этих элементарных составляющих
являются единственным источником достоверной информации о величине результирующей погрешности h формообразования.
Участок реальной поверхности Др детали, заключенный между двумя соседними дугами m и (m 1)
подачи вдоль строки формообразования, и двумя соседними дугами n и (n 1) подачи поперек строки формообразования условимся называть элементарной ячейкой регулярного микрорельефа на обработанной поверхности Др детали (рис. 9.1). Длина дуги SВ элементарной ячейки вдоль траектории формообразования
численно равна подаче на зуб инструмента, а длина дуги SП поперек строк – подаче на строку формообразования. Параметры hВ , SВ , hП и SП элементарной ячейки в общем случае переменны в пределах обрабатываемого участка поверхности Д , а их текущие значения зависят от параметров кривизны поверхностей Д и И в точке К , их относительной локальной ориентации, допуска [h] на точность формообразования и параметров кинематики формообразования. Поэтому величина h , i результирующей погрешности формообразования в текущей i й точке на поверхности Д детали равна
h , i |
h , i (hВ, i , hП, i ) , |
(9.1) |
|
где hВ, i и hП, i – значения составляющих hВ |
|
и hП в текущей точке поверхности Д |
детали (очевидно, что |
hВ, i hВ, i (U д , Vд ) , hП, i |
hП, i (U д , Vд ) ). |
|

518 |
8. Топология формообразованных поверхностей деталей |
Количественно требования, предъявляемые к точности формообразования, можно оценить по величине наибольшей погрешности, возникающей при обработке. Результирующая погрешность h формообразования
будет тем меньше, чем меньше ее максимальное значение в пределах всего обрабатываемого участка сложной поверхности детали. Поэтому оценивать точность формообразования величиной наибольшей результирую-
щей погрешности формообразования h(max) правомерно, тем более, что ее значение может быть расчитано с
требуемой точностью. Возможности более полного использования потенциальных возможностей технологии обработки сложных поверхностей деталей на многокоординатных станках с ЧПУ в этом случае расширяются за счет того, что появляется возможность разрабатывать в некотором смысле предельные способы обработки,
применение которых обеспечивает равенство максимальной погрешности h(max) допуску [h] на точность
формообразования (h(max) [h] ) в пределах всего обрабатываемого участка поверхности детали. Производи-
тельность обработки в этом случае увеличится и достигает своего предельного значения.
Принято считать, что при многокоординатном формообразовании сложных поверхностей Д деталей с
большой степенью точности справедлив принцип суперпозиции элементарных составляющих результирующей погрешности формообразования. Исходя из допустимости его применения результирующая погрешность
формообразования в текущей точке номинальной поверхности Дн равна h ahВ bhП , где a и b – некоторые константы для текущей точки К на поверхности Дн ( 0 a 1 ; 0 b 1 ).
Результирующая погрешность фомообразования максимальна, когда a b 1 – для такого случая
(9.2) |
h(max) h |
(max) h |
(max) . |
|
|
В |
П |
В общем случае зависимость h h (hВ, hП ) |
имеет более сложный нелинейный характер (об этом см. |
||
ниже, раздел 9.7). |
Д и И касаются одна другой по линии, то в плоском нормальном сечении, касатель- |
||
Если поверхности |
ном к этой линии, исходная инструментальная поверхность И предельно конформна номинальной поверхности детали Дн . В этом случае одна из составляющих погрешности h равна нулю. Как правило, hВ 0 и в
этом случае h hП . Принципиально возможны способы обработки1, когда hП 0 , тогда h hВ .
Если обработка производится инструментом, полностью воспроизводящим исходную инструментальную поверхность И , как это имеет место при шлифовании, то hВ 0 и, как следствие, h hП . Если же при пол-
ном воспроизведении в реальном инструменте его поверхности И она линейно касается поверхности Дн ,
формообразование номинальной поверхности детали перестает быть дискретным и лишено органических погрешностей. В этом случае hВ 0 , hП 0 и в результате h 0 .
9.2. Образование волнистости и огранки
Простым примером дискретного формообразования поверхностей при обработке деталей на металлорежущих станках служит точение круглого валика резцами разной конструкции (рис. 9.2). В процессе обработки
деталь вращается вокруг своей оси Од Од с постоянной угловой скоростью д . Обработка производится резцом с главным и вспомогательным 1 углами в плане (рис. 9.2.1). В процессе обработки инструмент перемещается вдоль оси детали на величину Sи на каждый ее оборот. Очевидно, что при этом на обработанной поверхности Д образуются остаточные грабешки, высота h которых равна
(9.3) h Sи sin sin 1 .
|
sin( 1 ) |
|
1Такие способы обработки обладают интересными потенциальными возможностями, однако в настоящее время в промышленности не используются.

|
|
9.2. Образование волнистости и огранки |
519 |
||
Из формулы (9.3) следует, что высота h остаточного регулярного микрорельефа зависит от величины |
|||||
подачи Sи на оборот детали и от значений углов в плане и 1 . Если уменьшить углы в плане и 1 , то |
|||||
при неизменной подаче |
Sи высота остаточных гребешков уменьшится (рис. 9.2.2). Полное исключение воз- |
||||
можности образования остаточных гребешков, когда h 0 , наблюдается в случае использования инструмен- |
|||||
тов с углами в плане, равными 0 |
и 1 0 . Реально это может быть осуществлено лишь на достаточно |
||||
короткой (длиной порядка (1,1 1,2) Sи ) вспомогательной режущей кромке инструмента (рис. 9.2.3). В рассма- |
|||||
триваемом случае остаточный регулярный микрорельеф не образуется и поэтому h 0 . |
|||||
Деталь |
Oд |
Oд |
Деталь |
Oд |
|
Oд |
|
|
|||
д |
|
|
д |
|
|
|
1 |
Д |
|
1 |
Д |
|
|
|
|
||
|
h |
|
|
h |
|
Sи |
|
Sи |
|
||
|
|
|
|||
Инструмент |
|
|
Инструмент |
|
|
|
1. |
Sи |
|
2. |
Sи |
|
|
|
|
||
Деталь |
Oд |
Oд |
Деталь |
Oд |
|
Oд |
|
|
|||
д |
1 |
0 |
д |
|
|
0 |
|
Д |
|
|
Д |
|
|
|
|
||
Sи |
1,2Sи |
h 0 |
Sи |
R |
h |
|
|
|
|
и |
|
Инструмент |
|
|
Инструмент |
|
|
|
3. |
|
|
4. |
Sи |
Рис. 9.2. Примеры дискретного формообразования при точении. |
|
Обработка круглого валика на токарном станке может производиться резцом, оснащенным круглой режущей пластиной радиуса Rи (рис. 9.2.4). Применение такого инструмента также приводит к образованию
остаточного регулярного микрорельефа на обработанной поверхности Д детали. Высота h остаточных гре-
бешков в этом случае равна h Rи Rи2 0,25 Sи2 .
Для уменьшения высоты h остаточных гребешков необходимо использовать инструмент с возможно большим радиусом Rи кривизны режущей кромки или производить обработку с возможно меньшей подачей Sи на оборот детали.
Рассмотреные примеры образования остаточных гребешков на обработанной поверхности детали при точении (см. рис. 9.2) тривиальны. В общем случае задача расчета параметров остаточного регулярного микрорельефа при формообразовании сложных поверхностей деталей на многокоординатных станках с ЧПУ сложнее.