
Radzevich, S.P. Monograph - 2001
.pdf
360 |
6.3. Кинематические геометрические параметры режущих кромок инструмента |
|||
зания t |
и подачи S изменение величины главного угла в плане e |
приводит к соответствующему изменению |
||
толщины a и ширины b срезаемого слоя, поскольку a S sin e |
а b |
t |
. Чем меньше значение угла в |
|
|
||||
|
|
|
sin e |
плане e , тем больше ширина среза b и величина угла при вершине e – это способствует улучшению отвода тепла из зоны резания. Уменьшение главного угла в плане e способствует увеличению стойкости
инструмента. При чрезмерном его уменьшении повышается вероятность появления вибраций в процессе резания.
Придание режущим кромкам инструмента вспомогательного угла в плане 1e приводит к уменьшению трения вспомогательной режущей кромки об обработанную поверхность. Увеличение угла 1e приводит к
увеличению высоты остаточных гребешков на обработанной поверхности детали, к соответствующему уменьшению угла при вершине e , к ухудшению отвода тепла из зоны резания. Максимальная стойкость инстру-
мента обычно наблюдается при 1e 10 .
Главный e и вспомогательный 1e углы в плане обычно рекомендуется уменьшать. Это ведет к соответствующему увеличению угла при вершине e и, как следствие, к уменьшению степени интерференции по-
токов стружки от смежных режущих кромок. С этой же целью режущие кромки выполняют криволинейными по радиусу Rи .
6.3.3.6. Плоскость схода стружки и измеряемый в ней передний угол. При свободном ортогональном ре-
зании вектор скорости схода стружки по передней поверхности перпендикулярен режущей кромке. Кинематические геометрические параметры режущей кромки рассчитывают в плоском сечении, перпендикулярном режущей кромке. Правомерность такого подхода подтверждена экспериментально.
Величину переднего угла, непосредственно определяющего характер протекания процесса резания металлов при косоугольном резании, необходимо определять, принимая во внимание направление схода стружки по передней поверхности режущего инструмента. Точно установить направление движения стружки по передней поверхности при косоугольном резании сложнее – оно определяется процессами, происходящими в зоне стружкообразования и в зоне контакта стружки с передней поверхностью зуба инструмента.
Без учета краевых эффектов ортогональное резание можно рассматривать в плоскости. Косоугольное резание существенно сложнее ортогонального в первую очередь в связи с тем, что деформация металла в процессе резания происходит не в плоскости, проходящей через направление вектора скорости резания и направление нормали к поверхности резания, а в некотором объеме, в связи с чем его следует рассматривать в пространстве. Процесс свободного косоугольного резания является сложным и малоизученным. Он трудно поддается исследованию. Вместе с тем малоизученное косоугольное резание с некоторым приближением можно свести к более изученному ортогональному резанию.
Г.И.Грановский (1948) предложил рассматривать процесс свободого косоугольного резания в плоскости стружкообразования – в плоскости схода стружки, положение которой определено проходящими через
текущую точку режущей кромки вектором результирующей скорости V перемещения режущего клина инструмента относительно поверхности резания Pse и вектором скорости схода стружки Vcf по передней
поверхности. Этим подразумевается, что существует такое плоское сечение режущего клина инструмента, в котором происходит процесс деформирования срезаемого припуска, подобный процессу его деформирования при ортогональном резании1. Передний угол режущего клина инструмента и глубину резания, измеренные в этой плоскости, предложено (Грановский Г.И., 1948) называть эффективным передним углом и эффективной глубиной резания.
Существует иная точка зрения по вопросу о расположении плоскости, в которой следует определять величину эффективного переднего угла. А.М.Розенберг (1976 и более ранние работы) доказывал, что эффек-
тивный передний угол cf следует измерять в плоскости схода не стружки целиком, а в плоскости схода отдельных ее элементов.
1Очевидно, нельзя считать, что при свободном косоугольном резании в плоскости стружкообразования в точности выполняются условия плоского деформирования. Однако поскольку при значениях угла наклона режущей кромки se 30 40 коэффициент уширения стружки Кb близок к единице, эти условия выполняются с достаточно высокой точностью.

6.3. Кинематические геометрические параметры режущих кромок инструмента |
361 |
Закон схода стружки (Stabler, G.V., 1951). Передний угол cf и глубина резания tcf , измеренные в плоскости схода стружки, отличны от соответствующих их значений, измеренных в других секущих плоскостях. Угол схода стружки по передней поверхности связан с шириной стружки bcf и шириной b обрабатываемой плоскости следующей зависимостью:
cos bcf cos se . b
В этом уравнении пренебрегают течением стружки по ее ширине, что находится в соответствии с предположением, что при ортогональном резании деформации по ширине стружки нет (Shaw, M.C., 1984).
Согласно закону схода стружки в широком диапазоне условий резания угол схода стружки примерно равен углу наклона режущей кромки: se . Это следует из предположения, что bcf b В более поздних работах Stabler G.V. уточнил этот закон,
представив его в форме 1,0 0,9 se .
Экспериментально доказано (Бобров В.Ф., 1962), что при свободном резании инструментами с углом наклона режущих кромокse 45 направление скорости Vcf схода стружки составляет с перпендикуляром к режущей кромке, проведенным в передней
плоскости П (или касательно к передней поверхности), угол se . При se 45 величина угла схода стружки превышает угол
наклона режущей кромки se не более, чем на 5 6 .
Наряду с углом схода стружки для определения направления скорости движения стружки по передней поверхности иногда используют величину проекции этого угла на основную плоскость (Stabler, G.V., 1951).
Стремление свести трудно поддающееся исследованию свободное косоугольное резание к более изученному свободному ортогональному резанию явилось причиной введения в рассмотрение понятия плоскость
схода стружки, в которой измеряется т.н. эффективный передний угол cf . Здесь и далее, не вдаваясь в тон-
кости механики процесса резания, рассмотрим как могут быть определены геометрические параматры режущей кромки инструмента в плоскости схода стружки.
Плоскость схода стружки, в которой (с некоторыми допущениями) срезаемый припуск превращается в стружку, проходит через вектор результирующей скорости V движения режущего клина относительно
поверхности резания и вектор Vcf |
скорости схода стружки по передней поверхности. Вектор скорости Vcf |
|||||||||||||||||||||||
лежит в плоскости, касательной в точке M к передней поверхности, и составляет угол с перпендикуляром |
||||||||||||||||||||||||
к режущей кромке, проведенным передней плоскости (рис. 6.20). |
|
|
|
|
|
|
||||||||||||||||||
|
Вектор скорости |
|
Vcf скорости схода стружки ортогонален орту n п нормали к передней поверхности |
|||||||||||||||||||||
Pn . Поэтому Vcf |
n п |
0 . |
|
|
|
|
|
|
|
|
|
|
|
|
|
|||||||||
|
Уравнение плоскости схода стружки Pcf |
может быть составлено как уравнение плоскости, проходящей |
||||||||||||||||||||||
|
|
|
|
|
|
|
|
|
|
|
|
|
|
|
через текущую точкк |
M режущей кромки и содержащей |
||||||||
|
|
|
|
|
|
|
|
|
|
Yи |
|
|
|
два направления – вектор V |
результирующей скорости |
|||||||||
|
|
|
|
|
|
|
|
|
|
|
|
|
||||||||||||
|
|
|
|
|
|
|
|
|
|
|
|
|
движения режущего клина и вектор Vcf |
скорости схода |
||||||||||
|
|
|
|
|
|
|
|
|
|
|
|
|
|
|
||||||||||
|
|
|
P |
n |
se |
|
|
|
|
|
|
стружки по передней поверхности. Вектор |
V определен |
|||||||||||
|
|
|
|
|
|
|
|
|||||||||||||||||
|
|
|
re |
|
|
|
|
|
|
|
выше. Вектор скорости Vcf в проекциях на координатные |
|||||||||||||
|
|
|
П |
|
|
|
|
V |
||||||||||||||||
Pse |
|
|
|
|
|
|
cf |
cf |
оси может быть представлен так: |
|
|
|
|
|
||||||||||
|
|
n п |
|
|
|
|
|
|
|
|
|
|
|
|
||||||||||
|
|
|
|
|
|
|
|
|
|
|
|
|
|
|
|
|
|
|
|
|
|
|||
|
|
|
|
|
|
|
|
|
|
|
|
|
|
|
|
|
|
Vcf iVcf .x jVcf .y kVcf .z . |
||||||
|
|
|
|
|
|
|
|
|
|
|
|
|
|
|
|
|
|
|||||||
Zи |
|
|
|
|
|
|
|
|
|
|
|
|
||||||||||||
|
|
|
|
|
|
|
|
|
|
|
|
|
|
|
|
|
|
|
||||||
|
|
|
V |
|
M |
|
|
З |
С учетом изложенного, уравнение плоскости схода |
|||||||||||||||
|
|
|
|
|
|
|||||||||||||||||||
|
|
|
|
|
|
|
|
|
|
|
||||||||||||||
|
|
|
|
|
|
|
|
|
||||||||||||||||
|
|
|
|
|
|
|
|
|
|
|
|
|
|
стружки Pcf записывается так: |
|
|
|
|
|
|||||
|
|
|
Pcf |
|
|
|
|
Xи |
|
|
|
|
X |
и |
X (M ) |
Y Y(M ) |
Z |
и |
Z (M ) |
|
||||
|
|
|
|
|
|
|
|
|||||||||||||||||
Рис. 6.20. Плоскость схода стружки |
Pcf и из- |
|
|
|
и |
|
|
|
|
|||||||||||||||
|
|
|
V .x |
V .y |
|
|
V .z |
|
0 . |
|||||||||||||||
|
|
|
меряемый в ней передний угол cf . |
|
|
|
|
|
|
|||||||||||||||
|
|
|
|
|
|
Vcf .x |
Vcf .y |
|
|
Vcf .z |
|
|
||||||||||||
|
|
|
|
|
|
|
|
|
|
|
|
|
|
|
|
|
|
|
|
|
|

362 |
|
|
|
6.3. Кинематические геометрические параметры режущих кромок инструмента |
|
|
|
|
|
|
|||||||||||||||
Передний угол cf |
заключен между основной плоскостью Pre |
и вектором Vcf |
скорости схода стружки |
||||||||||||||||||||||
(рис. 6.20). Поэтому: |
|
|
|
|
|
|
|
|
|
|
|
|
|
|
|
|
|
|
|
|
|
||||
|
|
|
|
cf |
V , Vcf 90 |
arctan |
V Vcf |
90 |
arctan |
V Vcf . |
|
|
|
|
|
|
|||||||||
|
|
|
|
|
|
|
|
|
|
|
V Vcf |
|
|
|
|
V V |
|
|
|
|
|
|
|||
|
|
|
|
|
|
|
|
|
|
|
|
|
|
|
|
|
|
|
cf |
|
|
|
|
|
|
Величина эффективного переднего угла cf может быть определена графически. |
Для этого режущий |
||||||||||||||||||||||||
клин инструмента расположим в системе плоскостей проекций |
HVF (рис. 6.21). Здесь и далее проекциям |
||||||||||||||||||||||||
элементов на горизонтальную плоскость проекций H присвоен индекс “1”, их проекциям на вертикальную |
|||||||||||||||||||||||||
плоскость проекций V – индекс “2”, а соответствующим проекциям на фронтальную плоскость проекций F |
|||||||||||||||||||||||||
– индекс “3”. |
|
|
|
|
|
|
|
|
|
|
|
|
|
|
|
|
|
|
|
|
|
|
|
|
|
В процессе обработки режущий клин |
|
|
|
|
Z |
|
|
|
|
|
|
|
|
|
|
|
|||||||||
1 перемещается параллельно оси |
H /V с |
|
2 |
n se |
|
|
12 |
V |
F |
П |
3 |
3 |
n se |
|
1 |
||||||||||
|
|
|
|
|
|
|
|
|
|
|
|
|
|
|
|||||||||||
результирующей скоростью V , вектор |
П2 |
|
|
|
|
|
|
|
|
|
|
3 |
|||||||||||||
которой без искажения проецируется как |
|
|
|
|
cf |
|
|
|
|
|
|
|
|
|
|
||||||||||
на горизонтальную |
плоскость |
проекций |
V |
|
|
|
|
|
|
|
|
|
|
|
3 |
Vcf |
|||||||||
H , так и на вертикальную плоскость про- |
|
|
|
|
|
|
2 V |
|
|
|
|
|
|
|
|||||||||||
екций V (поэтому проекции вектора ско- |
|
|
M2 |
|
|
|
c |
|
|
|
M3 |
|
|
|
|||||||||||
|
|
|
|
|
|
|
|
|
|
|
|
||||||||||||||
рости V дополнительными индексами не |
V |
a2 |
|
|
|
|
|
b2 |
|
|
a3 |
|
|
|
|
b3 |
|||||||||
обозначены). |
|
|
|
|
расположена под |
H |
a1 |
|
|
|
|
|
|
|
|
|
|
|
|
|
|
||||
Режущая кромка ab |
П1 |
|
|
|
1m |
c |
|
|
1 |
|
|
|
|
|
|
|
|||||||||
углом наклона |
|
, |
плоскость P |
|
измере- |
|
|
|
|
|
|
|
|
|
|
|
|
||||||||
se |
|
|
|
|
|
|
|
1 |
|
|
|
|
|
|
|
||||||||||
|
|
|
|
|
se |
|
|
|
V |
|
|
|
|
|
|
|
|
|
|
|
|
|
|
||
ния которого расположена параллельно го- |
|
|
|
|
|
|
1Vcf |
|
|
|
|
a5 |
|
|
15 |
||||||||||
ризонтальной |
плоскости |
проекций |
H . |
|
se |
|
M1 |
|
|
|
|
|
|
|
|
|
|||||||||
Угол наклона |
se |
|
измеряется между по- |
|
|
|
|
|
|
|
|
|
|
|
|
П5 |
|||||||||
строенным в плоскости резания Pse векто- |
|
1n |
|
|
b |
|
|
|
M5 |
|
|
|
|
||||||||||||
ром нормали n c |
к режущей кромке и век- |
|
|
|
c |
|
1 |
|
|
|
|
|
5 |
|
|||||||||||
|
|
|
|
|
|
|
|
|
|
|
|
|
|||||||||||||
тором результирующей скорости V . |
|
Y |
|
|
|
|
|
|
X |
|
b5 |
|
|
||||||||||||
|
|
|
|
|
|
|
|
|
|
|
|
|
|||||||||||||
В текущей точке M режущей кромки |
|
|
|
|
|
|
|
|
|
4 Vcf |
|
5 Vcf |
|
|
|||||||||||
построена нормаль |
|
n se |
к поверхности ре- |
|
|
|
|
|
|
|
H |
M4 |
|
5 m c |
|||||||||||
зания Pse . |
|
|
|
|
|
|
|
|
|
|
|
|
|
|
|
|
W |
4 n se |
|
|
|
|
|
|
|
Чтобы построить вектор V |
|
скоро- |
|
|
|
|
|
|
|
|
|
|
|
U |
|
|
|||||||||
|
|
|
|
|
|
cf |
|
|
|
|
|
|
|
|
|
|
|
|
|
|
|
П4 |
|||
сти схода стружки, введены две допол- |
|
|
|
|
|
|
|
|
|
|
ne |
W |
|||||||||||||
|
|
|
|
|
|
|
|
|
|
|
|
||||||||||||||
нительные плоскости проекций |
W и |
U , |
|
|
|
|
|
|
|
|
|
|
|
|
|
|
|
|
|||||||
проекциям элементов на которые присво- |
Рис. 6.21. К построению натуральной величины переднего угла |
||||||||||||||||||||||||
ены индексы “4” и “5” соответственно. Ось |
|||||||||||||||||||||||||
проекций HW расположена перпендику- |
|
cf , измеренного в плоскости схода стружки Pcf . |
|||||||||||||||||||||||
лярно проекции |
a1b1 режущей кромки на |
|
|
|
|
|
|
|
|
|
|
|
|
|
|
|
|
||||||||
горизонтальную плоскость проекций H . В |
|
|
|
|
|
|
|
|
|
|
|
|
|
|
|
|
|||||||||
дополнительной |
плоскости |
проекций |
W режущая |
кромка |
изобразится точкой |
A4 B4 |
M4 , |
передняя |
|||||||||||||||||
плоскость – следом П4 , а нормальный передний угол проецируется без искажений – в натуральную величину |
|||||||||||||||||||||||||
ne . |
|
|
|
|
|
|
|
|
|
|
|
|
|
|
|
|
|
|
|
|
|
|
|
|
|
Ось проекций W /U проведена параллельно следу |
П4 |
передней плоскости. Следовательно, передняя |
|||||||||||||||||||||||
плоскость проецируется на дополнительную плоскость проекций U |
без искажений. Поэтому в плоскости |
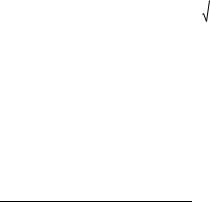
6.3. Кинематические геометрические параметры режущих кромок инструмента |
363 |
|||
проекций U угол схода стружки 1, определяющий направление движения стружки по передней поверх- |
||||
ности, изобразится в натуральную величину. Вследствие этого вектор скорости схода стружки Vcf |
на допол- |
|||
нительной плоскости проекций U проходит под углом к расположенному в передней плоскости перпенди- |
||||
куляру m c к режущей кромке. |
|
|
|
|
Используя известные правила начертательной геометрии, по проекции |
V 5 вектора скорости V |
|||
|
cf |
cf |
||
изображаем его в остальных плоскостях проекций. Развернув проекцию V cf1 |
вокруг оси, параллельной оси |
|||
V / H , до положения, в котором эта проекция параллельна вертикальной плоскости проекций, в плоскости |
||||
проекций V получаем неискаженный передний угол cf (рис. 6.21). |
|
|
|
|
Величина переднего угла cf может быть расчитана аналитически. Для этого в системе координат XYZ |
||||
с началом в текущей точке M режущей кромки (рис. 6.21) для нормированного вектора v |
V |
|
запишем: |
|
V |
|
|||
|
|
|
|
|
|
|
|
|
|
v i sin se j cos se . |
|
|
|
(6.27) |
Аналогично, выбрав модуль вектора vcf таким, чтобы его проекция на плоскость координат YZ равня-
лась единице, получим: |
|
|
|
|
|
|
|
|||||||||||
|
vcf i tan j sin ne k cos ne . |
(6.28) |
||||||||||||||||
Для угла v , vcf справедливо соотношение: |
|
|
|
|
|
|
|
|||||||||||
|
cos v , vcf sin v , vcf 0,5 . |
|
||||||||||||||||
Для переднего угла cf можно записать: |
|
|
|
|
|
|
|
|||||||||||
|
|
|
|
|
|
|
|
|
|
|
|
|
|
|
|
|
||
|
|
|
|
|
|
V Vcf |
|
|
|
|
|
|
||||||
|
sin cf |
|
|
|
|
|
|
v vcf |
. |
(6.29) |
||||||||
|
|
|||||||||||||||||
|
|
V |
|
|
|
Vcf |
|
|
|
|||||||||
|
|
|
|
|
||||||||||||||
|
|
|
|
|
|
|
|
|
|
|
|
|
|
|
||||
Подставив (27) и (28) в (29), после преобразований получим: |
|
|||||||||||||||||
sin cf |
sin se tan |
cos se sin ne |
|
sin se cos tan cos se sin ne cos , |
|
|||||||||||||
|
|
|
|
|
|
|
|
|
|
|
|
|||||||
1 tan 2 |
|
|||||||||||||||||
|
|
|
|
|
|
|
|
|||||||||||
откуда: |
|
|
|
|
|
|
|
|||||||||||
|
sin cf sin sin se cos cos se sin ne . |
(6.30) |
Для широко распространенных случаев обработки резанием угол наклона режущей кромки se 45 .
Экспериментально доказано, что при se 45 выполняется соотношение se , с учетом которого из (30) следует известная формула (Stabler, G.V., 1951):
1Величина угла схода стружки может быть расчитана аналитически (Куцер В.М., 1990). Результаты оаналитических расчетов хорошо согласуются с результатами экспериментальных исследований Н.Н. Зорева.
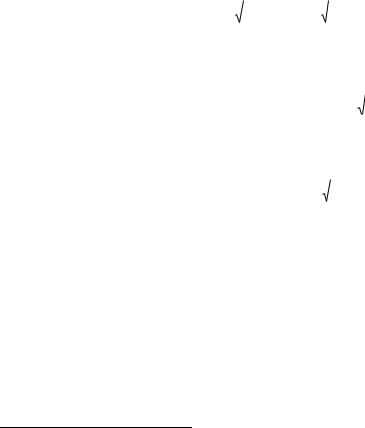
364 |
6.3. Кинематические геометрические параметры режущих кромок инструмента |
|
|
sin cf sin 2 se cos2 se sin ne 1 cos2 se 1 sin ne . |
(6.31) |
Если условие se не выполняется, как это имеет место, например, при шевинговании цилиндри-
ческих зубчатых колес, когда величина угла наклона режущей кромки достигает значения se 80
(Подураев В.Н., Камалов В.С., 1973), следует пользоваться более общей зависимостью (30).
В процессе работы инструмента угол наклона режущей кромки se может изменяться как во времени в текущей точке режущей кромки, так и вдоль ее периметра. Диапазон изменения величины угла se по пери-
метру режущей кромки достигает se 50 , что наблюдается, например, при зубошевинговании дисковым шевером (Петрухин С.С., 1960). Изменение величины угла наклона режущей кромки se существенно сказы-
вается на условиях отделения и отвода стружки.
Принимая во внимание, что величины передних углов ne и ve , измеренных в нормальной и в главной секущей плоскостях, связаны между собой соотношением:
|
|
|
tan ne tan ve cos se , |
|
|
|
|
|
|
|
|
|
|
||||||||||
с учетом того, что: |
|
|
|
|
|
|
|
|
|
|
|
|
|
|
|
|
|
|
|
|
|
|
|
|
sin n |
|
tan n |
|
|
|
tan ve cos se |
|
|
, |
|
|
|
||||||||||
|
|
|
|
|
|
|
|
|
|
|
|
|
|
|
|
|
|
|
|
|
|||
|
1 tan 2 n |
1 tan 2 ve cos2 se |
|
|
|
|
|||||||||||||||||
|
|
|
|
|
|
|
|
|
|||||||||||||||
из (30) получим: |
|
|
|
|
|
|
|
|
|
|
|
|
|
|
|
|
|
|
|
|
|
|
|
sin cf |
sin sin se cos cos2 se |
|
|
tan ve cos se |
|
|
. |
||||||||||||||||
|
|
|
|
|
|
|
|
|
|
|
|
||||||||||||
|
tan 2 ve cos2 |
|
|||||||||||||||||||||
|
|
|
|
|
|
|
|
|
|
|
|
1 |
se |
||||||||||
Из (31) можно получить аналогичную формулу |
|
|
|
|
|
|
|
|
|
|
|
|
|
|
|
|
|||||||
|
|
|
|
|
|
|
|
tan ve cos se |
|
|
|
|
|
|
|
||||||||
|
|
|
|
2 |
|
|
|
|
|
|
|
|
|
|
|||||||||
|
sin cf 1 cos |
|
se 1 |
|
|
|
|
|
|
|
|
|
|
. |
|
|
|
||||||
|
|
|
|
|
|
|
|
|
|
|
|
|
|
||||||||||
|
|
|
|
|
2 |
|
2 |
|
|
|
|
|
|
||||||||||
|
|
|
|
|
|
|
|
1 tan |
ve cos |
se |
|
|
|
|
|||||||||
|
|
|
|
|
|
|
|
|
|
|
|
|
|
Приведенные зависимости справедливы для случая свободного косоугольного резания. Они позволяют рассчитать значение переднего угла cf при любой величине угла наклона режущей кромки se .
При несвободном косоугольном резании надежно определить величину угла аналитически сложно –
для этого требуется проведение экспериментальных исследований.
Использованный подход, базирующийся на применении элементов векторной алгебры, позволяет достаточно просто вывести формулы для расчета величин статических и кинематических геометрических параметров режущей кромки в любом наперед заданном плоском сечении режущего клина инструмента. Его применение эффективно также при выводе формул для расчета значений геометрических параметров процесса резания: угла резания1, углов скалывания, угла действия, глубины резания и др., измеряемых в произвольном сечении.
1Эффективный угол резания cf измеряется между противоположным направлением вектора скорости резания V и вектором скорости схода стружки Vcf . При свободном косоугольном резании величина угла cf зависит от угла наклона режущей кромки se и угла схода стружки : cf arccos cos se cos cos ne sin se sin . Из этой формулы следует, что угол резания cf уменьшается по мере увеличения угла наклона режущей кромки se и угла схода стружки , что хорошо согласуется с экспериментальными данными.
Г л а в а 7. Условия формообразования поверхностей деталей
Обработка детали производится на станке инструментом, который перемещается относительно заготовки. В результате этого материал припуска срезается в виде стружки и таким образом формируется поверхность детали.
Особенности формы обрабатываемой поверхности детали, параметров исходной инструментальной поверхности применяемого инструмента и кинематики формообразования могут привести к тому, что в некоторых случаях обработать деталь в полном соответствие с требованиями чертежа невозможно или такая обработка окажется затруднительной. Часть материала припуска может оказаться несрезанной (в этом случае наблюдается т.н. недорез) или, наоборот, срезанной окажется часть материала детали (в этом случае наблюдается т.н. подрез). И первое, и второе нежелательно, однако может быть допустимо, если размеры окончательно обработанной поверхности детали укладываются в поле допуска на точность ее изготовления.
Важно выявить причины, которые приводят к появлению отклонений формы окончательно обработанной поверхности детали Др от номинальной ее поверхности Дн . Это будет способствовать разработке
эффективных методов и средств по устранению погрешностей формообразования и тем самым позволит повысить эффективность обработки детали с заданной точностью.
Установление условий, при выполнении которых поверхность детали формообразуется геометрически точно (или когда результирующие отклонения формы реальной Д р от номинальной Дн поверхности
находится в пределах допуска на точность обработки детали), является важной инженерной задачей. В общей постановке эту проблему исследовал Родин П.Р. (1960). Впоследствие она изучалась другими исследователями (Лашнев С.И., Юликов М.И., 1975; Перепелица Б.А., 1981; Радзевич С.П., 1991;
Борисов А.Н., 1993; Marciniak K., 1987, 1991; и др.).
Машинная подготовка управляющих программ для станков с ЧПУ предполагает наличие аналитического представления условий, при выполнении которых деталь может быть обработана в полном соответствие с требованиями чертежа. Потребность в формализованном представлении таких условий вызвана тем, что возможность оператора вмешиваться в процесс обработки детали на станке с ЧПУ практически исключена. Поэтому вся информация о процессе, в том числе и ограничения на его параметры, накладываемые необходимостью обеспечения возможности правильного формообразования поверхности детали, должна быть задана в предельно формализованном и удобном для программирования виде.
Изучение и аналитическое описание условий, при выполнении которых поверхность детали может быть формообразована геометрически точно или когда погрешности формообразования не выходят за пределы допуска на точность обработки, предполагает, что кинематика формообразования известна (см. гл. 2), а соответствующая исходная инструментальная поверхность определена (см. гл. 5).
7.1.Аналитическое представление условий формообразования поверхностей деталей
Правильное формообразование поверхности детали заданным инструментом возможно лишь при выполнении комплекса условий, которые принято называть условиями формообразования поверхностей деталей. Система условий формообразования поверхностей определяется структурой обрабатываемой поверхности детали, формообразующей исходной инструментальной поверхности и кинематикой формообразования.
7.1.1. Первое условие формообразования. Это необходимое условие формообразования поверхностей деталей впервые сформулировал Родин П.Р. (1960). Оно заключается в том, что должна существовать исходная инструментальная поверхность.
366 |
7. Условия формообразования поверхностей деталей |
Способы образования исходных инструментальных поверхностей рассмотрены выше (см. гл. 5). Поэтому ограничимся только тем, что сформулируем:
Первое условие: Поверхность Д детали может быть правильно формообразована, если существует сопряженная с ней исходная инструментальная поверхность И .
Это условие формообразования поверхностей деталей выполняется не всегда. Оно может нарушаться для одного или нескольких участков поверхности детали, в том числе может не выполняться и для всей поверхности Д . Если бы не только исходная инструментальная поверхность была огибающей
последовательных положений обрабатываемой поверхности детали, но и наоборот – поверхность Д была
огибающей последовательных положений движущейся поверхности И , исследование процесса формообразования существенно упростилось бы. Однако огибающая поверхности, совершающей движение в пространстве, существует не всегда. Например, если плоскость перемещается в направлении, перпендикулярном ей самой – образовать огибающую движущейся таким образом плоскости невозможно. То же самое наблюдается, если плоскость вращать вокруг оси, лежащей в этой плоскости. Однако если ту же плоскость вращать вокруг оси, параллельной плоскости и не лежащей в ней, либо вокруг оси, перпендикулярной к этой плоскости, найти огибающую несложно.
Обычно выполнение первого условия формообразования поверхностей деталей затруднений не вызывает
– например, варьируя кинематикой формообразования, исходную инструментальную поверхность можно образовать практически всегда, в том числе и такую поверхность И инструмента, форма и параметры которой в процессе обработки изменяется по программе (Родин П.Р., Линкин Г.А., Татаренко В.Н., 1976; Радзевич С.П., 1988). Вместе с тем возможны случаи, когда исходная инструментальная поверхность не существует и образована быть не может. Например, для известных (см. выше, гл. 2) кинематических схем формообразования не существует исходная инструментальная поверхность эвольвентных червячных фрез с
углом профиля и 0 (в этом случае диаметр основного цилиндра инструмента dbи ); нельзя
образовать исходную инструментальную поверхность для случая шлифования колес с эвольвентным профилем зубьев, когда начальный диаметр колеса в станочном зацеплении меньше его основного диаметра; не существует исходная инструментальная поверхность И для инструмента, предназначенного для чистового затылования геометрически точных модульных, шлицевых, фасонных червячных фрез и др. Затыловочные круги в этом случае имеют не точную исходную инструментальную поверхность И , а приближенную
производящую поверхность Пи . Эта поверхность не сопряжена с затылованной поверхностью геометрически
точных червячных фрез и поэтому обеспечивает только приближенное формообразование затылованных поверхностей зубьев инструментов указанных конструкций.
Если первое условие формообразования не выполняется, т.е. не существует сопряженная с поверхностью Д поверхность И , спроектировать соответствующий инструмент невозможно, а потому обработать деталь
без органических погрешностей в этом случае нельзя.
7.1.2. Второе условие формообразования. В процессе обработки сопряженные поверхности детали и инструмента непрерывно или периодически касаются одна другой по линии или в точке (поверхностное их касание при обработке деталей лезвийным и абразивным инструментом не является характерным). Чтобы
поверхности Д |
и И могли касаться одна другой, должно быть выполнено условие касания. Это условие |
обычно записывают в виде уравнения контакта: |
|
(7.1) |
Nд и V 0 , |
где Nд и – вектор контактной нормали к поверхностям Д и И в точке К их касания;
V – вектор результирующей скорости относительного движения поверхностей Д и И в точке К .
Анализ уравнения контакта (1) показывает, что при обработке заданной поверхности детали влиять на процесс формообразования можно в первую очередь за счет изменения направления вектора относительной
скорости V . Направление вектора нормали Nд и для заданной точки поверхности Д детали обычно является
строго определенным, и изменять его, не меняя форму обработанной поверхности, как правило, нельзя. Однако это не всегда так – направление вектора нормали Nд и можно изменять, переводя заготовку в
технологическое состояние, например, когда заготовка упруго деформирована или подвержена иному

7.1. Аналитическое представление условий формообразования поверхностей деталей |
367 |
технологическому воздействию, убираемому после окончания процесса обработки (см. рис. 2.3, с.123). Этот пример достаточно убедительно свидетельствует о том, что в уравнении контакта (1) в общем случае следует вести речь о нормали не к поверхности Д детали, а о нормали к поверхности детали в технологическом
состоянии заготовки, т.е. о нормали к поверхности Дтехнол. . В большинстве случаев эти нормали совпадают
одна с другой.
Уравнение контакта (1) может быть записано в иной форме, если исходить из того, что в точках касания
нормали к каждой из поверхностей Д и И должны |
лежать на одной прямой – |
они должны быть |
коллинеарными и противоположно направленными: |
|
|
n д n и 0 |
|
(7.2) |
или |
|
|
sgn N д sgn Nи |
0. |
(7.3) |
Уравнение контакта отражает только геометрический и кинематический аспекты аналитического
представления |
условия, |
выполнение |
которого необходимо |
для обеспечения возможности касания |
|
|
n д |
И |
nи n д |
И |
n д n u |
|
|
|
K |
|
|
|
|
|
И |
K |
|
|
|
|
Д |
||
|
|
|
|
||
Д |
K |
|
|
|
|
Д
nи |
|
|
1. |
2. |
3. |
Рис. 7.1. Примеры выполнения и нарушения второго условия формообразования поверхностей деталей.
поверхности Д детали и поверхности И инструмента.
Поверхность детали и исходная инструментальная поверхность имеют материальный носитель своей формы. Возможность правильного касания поверхностей Д и И как геометрических образов является
необходимым, но не достаточным условием возможности правильного касания поверхностей реальной детали и реального инструмента. Дополнительно должно быть выполнено очевидное условие физического характера, которое может быть названо физическим условием касания. Суть физического условия заключается в том, что тело детали и часть пространства, ограниченная исходной инструментальной поверхностью И , не должны одновременно занимать одну и ту же область пространства. Например (рис. 7.1), поверхности Д и И как
геометрические образы касаются одна другой в точке К и имеют в ней общую (контактную) нормаль. Вместе с тем очевидно, что при выполнении условия геометрического контакта обработка детали возможна не всегда. Если в первом случае (рис. 7.1.1) обработка детали возможна, то во втором (рис. 7.1.2) – невозможна: по штриховке видно, что в этом случае имеется область, одновременно занятая телом детали и частью пространства, ограниченного поверхностью И инструмента. Очевидно, что в результате взаимной интерференции деталь и инструмент не могут занимать такое положение одна относительно другой. Деталь и инструмент должны касаться одна другой только открытой для контакта стороной.
Интерференцию вида (см. рис. 7.1.3), когда деталь и инструмент располагаются по одну сторону от общей для поверхностей Д и И касательной плоскости, будем называть интерференцией первого рода
детали и инструмента.
Выполнение второго условия формообразования поверхностей не допускает интерференции первого рода и тем самым исключает из дальнейшего рассмотрения все случаи обработки, приводящие к касанию поверхности Д детали и поверхности И инструмента, когда нормали к ним оказываются
однонаправленными или не лежат на одной прямой.

368 7. Условия формообразования поверхностей деталей
Для обеспечения возможности правильного касания поверхностей детали и инструмента необходимо, чтобы в каждой их общей точке К тело детали и часть пространства, занятая инструментом, находились с противоположных сторон от общей касательной плоскости. Это условие аналитически может быть представлено так.
Считаем, что нормаль к поверхности Д направлена от тела детали, а нормаль к поверхности И – от
инструмента. Чтобы указанные нормали были направлены в требуемых направлениях, достаточно проследить за порядком сомножителей в находящемся в числителе векторном произведении:
|
|
|
r д и |
|
rд и |
|
|
|
|
rд и |
|
r д и |
|
|
|
|
|||
(7.4) |
n д и |
|
U д и |
Vд и |
|
|
|
U д и |
Vд и |
|
, |
|
|||||||
|
|
|
|
|
|
|
|||||||||||||
|
r д и |
|
rд и |
|
|
|
|
|
|
|
|
|
|
|
|
||||
|
|
|
E |
G |
|
|
F |
2 |
|
|
|||||||||
|
|
|
|
|
|
|
|
|
|
|
д и д и |
|
д и |
|
|
|
|||
|
|
|
U д и |
Vд и |
|
|
|
|
|
|
|
|
|
||||||
|
|
|
|
|
|
|
|
|
|
|
|
|
|
|
|
|
|
||
которым определяются направления ортов нормалей к поверхностям |
Д(И) . |
|
|||||||||||||||||
|
С учетом изложенного сформулируем: |
|
|
|
|
|
|
|
|
|
|
|
|
|
|
|
|
||
|
Второе условие: Поверхность Д детали может быть правильно формообразована, |
если в текущей |
|||||||||||||||||
точке ее касания с исходной инструментальной |
поверхностью |
И нормали к ним |
коллинеарны и |
||||||||||||||||
противоположно направленны. |
|
|
|
|
|
|
|
|
|
|
|
|
|
|
|
|
|
Для выполнения второго условия формообразования поверхностей деталей должно соблюдаться условие
(2) или (3). Если Nд |
– нормаль к поверхности |
|
Д детали, а Nи |
|
– нормаль к поверхности И инструмента, это |
||||||||||||||||||||||||||||||||||||||
же условие аналитически записывается так: N д Nи |
|
|
0 . Переходя к ортам нормалей, получим: |
||||||||||||||||||||||||||||||||||||||||
(7.5) |
|
|
|
|
|
|
|
|
|
|
|
|
|
|
|
n д n и |
|
1 . |
|
|
|
|
|
|
|
|
|
|
|
|
|
||||||||||||
С учетом (4) формула (5) может быть записана так: |
|
|
|
|
|
|
|
|
|
|
|
|
|
|
|
||||||||||||||||||||||||||||
|
|
|
|
|
|
|
|
|
|
|
|
rд |
|
rд |
|
|
|
|
rи |
|
rи |
|
|
|
|
|
|
|
|||||||||||||||
|
|
|
|
|
|
|
|
|
|
|
|
|
|
|
|
|
|
|
|
|
|
|
|
|
|
|
|
|
|
|
|
|
|
|
|
||||||||
(7.6) |
|
|
|
n |
д |
n |
и |
|
|
U д |
|
|
|
Vд |
|
|
|
|
Uи |
|
|
|
Vи |
1 . |
|
|
|||||||||||||||||
|
|
|
rд |
|
rд |
|
|
|
rи |
|
|
rи |
|
|
|||||||||||||||||||||||||||||
|
|
|
|
|
|
|
|
|
|
|
|
|
|
|
|
|
|
|
|
|
|
|
|
|
|||||||||||||||||||
|
|
|
|
|
|
|
|
|
|
|
|
|
|
|
|
Vд |
|
|
|
|
|
|
Vи |
|
|
|
|
|
|
|
|||||||||||||
|
|
|
|
|
|
|
|
|
|
|
|
U д |
|
|
|
|
|
|
|
Uи |
|
|
|
|
|
|
|
|
|
|
|||||||||||||
В уравнении (6) знаменатели всегда положительны, из чего следует: |
|
|
|
||||||||||||||||||||||||||||||||||||||||
|
|
rд |
|
rд |
|
rи |
|
|
|
rи |
|
|
|
|
|
|
|
|
|
|
|
|
|
|
|
|
|
|
|
||||||||||||||
(7.7) |
|
|
|
|
|
|
|
|
|
|
(E |
д |
G |
д |
F 2 ) (E |
и |
G |
и |
F |
2 ) 0 |
|||||||||||||||||||||||
|
|
|
|
|
|
|
|
||||||||||||||||||||||||||||||||||||
|
|
Uд |
|
Vд |
|
Uи |
|
Vи |
|
|
|
|
|
|
|
|
|
|
|
|
|
|
|
д |
|
|
|
и |
|||||||||||||||
|
|
|
|
|
|
|
|
|
|
|
|
|
|
|
|
|
|
|
|
|
|
|
|
|
|
|
|
|
|
|
|
|
|||||||||||
или в такой форме: |
|
|
|
|
|
|
|
|
|
|
|
|
|
|
|
|
|
|
|
|
|
|
|
|
|
|
|
|
|
|
|
|
|
|
|
|
|
|
|
|
|
|
|
|
|
|
|
|
|
|
|
|
r |
д |
|
|
|
r |
д |
|
|
|
r |
и |
|
r |
и |
|
|
|
|
|
|
|
|
|
|||||||||||
(7.8) |
|
|
|
|
|
sgn |
|
|
|
|
|
|
|
|
|
|
|
|
|
|
|
|
|
|
1 |
; |
|
|
|
|
|||||||||||||
|
|
|
|
|
U |
|
|
V |
|
|
|
|
|
V |
|
|
|
|
|
||||||||||||||||||||||||
|
|
|
|
|
|
|
|
|
д |
|
|
|
U |
и |
|
|
|
|
|
|
|
|
|
|
|||||||||||||||||||
|
|
|
|
|
|
|
|
|
|
|
|
|
|
|
д |
|
|
|
|
|
|
|
|
|
|
и |
|
|
|
|
|
|
|
|
|
||||||||
|
|
|
|
|
|
|
|
|
|
|
|
|
|||||||||||||||||||||||||||||||
(7.9) |
|
|
|
|
sgn |
|
(EдGд Fд2 ) (EиGи |
Fи2 ) 1 . |
|
|
|
Аналитическая форма (7) представления второго условия формообразования поверхностей резанием в развернутом виде записывается так:

|
|
|
|
|
|
|
7.1. Аналитическое представление условий формообразования поверхностей деталей |
|
|
|
|
369 |
|||||||||||||||||||||||||||||||||||||||||||||||||||||||||
Xд |
Yд |
|
|
|
Xи |
|
|
Yи |
|
|
Yд |
Zд |
|
|
|
|
Yи |
|
|
|
Zи |
|
|
|
Zд |
|
|
|
|
Xд |
|
|
Zи |
|
|
Xи |
|
|
|
|
|||||||||||||||||||||||||||||
U д |
U д |
|
|
|
Uи |
|
Uи |
|
|
U д |
U д |
|
Uи |
|
|
Uи |
|
U д |
|
|
|
|
U д |
|
|
U и |
|
|
Uи |
|
0; |
(7.10) |
|||||||||||||||||||||||||||||||||||||
X |
д |
Y |
|
|
X |
и |
|
|
Y |
|
|
Y |
Z |
д |
|
|
Y |
|
|
|
Z |
и |
|
Z |
д |
|
|
|
|
X |
д |
|
Z |
и |
|
|
X |
и |
|
||||||||||||||||||||||||||||||
|
|
|
|
д |
|
|
|
|
|
|
|
и |
|
|
|
|
|
д |
|
|
|
|
|
|
|
|
|
и |
|
|
|
|
|
|
|
|
|
|
|
|
|
|
|
|
|
|
|
|
|
|
|
|
|
|
|
|
|||||||||||||
Vд |
|
Vд |
|
|
|
Vи |
|
|
Vи |
|
|
Vд |
Vд |
|
|
|
|
Vи |
|
|
Vи |
|
|
|
Vд |
|
|
|
|
Vд |
|
|
Vи |
|
|
Vи |
|
|
|
|
|||||||||||||||||||||||||||||
или так: |
|
|
|
|
|
|
|
|
|
|
|
|
|
|
|
|
|
|
|
|
|
|
|
|
|
|
|
|
|
|
|
|
|
|
|
|
|
|
|
|
|
|
|
|
|
|
|
|
|
|
|
|
|
|
|
|
|
|
|
|
|
|
|
|
|
|
|
|
|
|
X |
д |
Y |
|
|
|
|
X |
и |
|
Y |
|
|
|
Y |
|
Z |
д |
|
|
|
|
Y |
|
|
|
Z |
и |
|
|
|
Z |
д |
|
|
|
X |
д |
|
Z |
и |
|
X |
и |
|
|
|||||||||||||||||||||||
|
|
|
|
|
д |
|
|
|
|
|
|
|
|
|
и |
|
|
|
|
д |
|
|
|
|
|
|
|
|
|
|
и |
|
|
|
|
|
|
|
|
|
|
|
|
|
|
|
|
|
|
|
|
|
|
|
|
|
|
|
|||||||||||
sgn |
U д |
U д |
|
|
|
Uи |
|
Uи |
|
|
U д |
|
U д |
|
|
|
|
Uи |
|
Uи |
|
|
|
U д |
|
|
U д |
|
Uи |
Uи |
1. |
(7.11) |
|||||||||||||||||||||||||||||||||||||
|
X |
д |
Y |
|
|
|
|
X |
и |
|
Y |
|
|
|
Y |
|
Z |
д |
|
|
|
|
Y |
|
|
|
Z |
и |
|
|
|
Z |
д |
|
|
|
X |
д |
|
Z |
и |
|
X |
и |
|
|
|||||||||||||||||||||||
|
|
|
|
|
д |
|
|
|
|
|
|
|
|
|
и |
|
|
|
|
д |
|
|
|
|
|
|
|
|
|
|
и |
|
|
|
|
|
|
|
|
|
|
|
|
|
|
|
|
|
|
|
|
|
|
|
|
|
|
|
|||||||||||
|
V |
V |
|
|
|
|
V |
|
V |
|
|
|
V |
|
V |
|
|
|
|
V |
|
|
|
V |
|
|
|
V |
|
|
|
V |
|
V |
|
|
V |
|
|
|
|||||||||||||||||||||||||||||
|
|
|
д |
|
д |
|
|
|
|
|
|
и |
|
|
и |
|
|
|
|
д |
|
|
|
|
д |
|
|
|
|
|
|
и |
|
|
|
|
|
и |
|
|
|
|
|
д |
|
|
|
|
|
|
д |
|
|
|
|
и |
|
|
|
и |
|
|
|||||||
Используя сокращенную форму записи определителей, составленных из производных, можно получить |
|||||||||||||||||||||||||||||||||||||||||||||||||||||||||||||||||||||
еще два уравнения, эквивалентные (10) и (11): |
|
|
|
|
|
|
|
|
|
|
|
|
|
|
|
|
|
|
|
|
|
|
|
|
|
|
|
|
|
|
|
|
|
|
|
|
|
|
|
|
|
|
|
|
|||||||||||||||||||||||||
|
|
|
|
|
Xд, Yд |
|
Xи , Yи |
|
Yд, Zд |
|
|
|
|
Yи , Zи |
|
|
Zд, Xд |
|
|
|
Zи , Xи |
|
0; |
|
|
||||||||||||||||||||||||||||||||||||||||||||
|
|
|
|
|
U |
д |
|
, V |
|
|
U |
и |
, V |
|
|
|
U |
д |
, V |
|
|
|
U |
и |
, V |
|
|
|
U |
д |
, V |
|
|
|
U |
и |
, V |
|
|
|
|
|
|
|
|||||||||||||||||||||||||
|
|
|
|
|
|
|
|
|
|
д |
|
|
|
|
|
и |
|
|
|
|
|
д |
|
|
|
|
|
|
|
|
и |
|
|
|
|
|
|
|
д |
|
|
|
|
|
|
|
|
и |
|
|
|
|
|
|
|
||||||||||||||
|
|
|
|
|
|
X |
д |
, Y |
|
|
X |
и |
, Y |
|
|
Y , Z |
д |
|
|
Y , Z |
и |
|
|
Z |
д |
, X |
д |
|
|
Z |
и |
, X |
и |
|
1 . |
|
|||||||||||||||||||||||||||||||||
|
|
|
|
sgn |
U |
|
|
д |
U |
|
и |
|
|
д |
|
|
|
|
|
|
|
и |
|
|
|
|
|
|
|
, V |
|
|
|
|
, V |
|
|
|
|||||||||||||||||||||||||||||||
|
|
|
|
|
|
д |
, V |
|
|
|
и |
, V |
|
|
U |
д |
, V |
|
|
U |
и |
, V |
|
|
U |
д |
|
|
|
U |
и |
|
|
|
|
|
|||||||||||||||||||||||||||||||||
|
|
|
|
|
|
|
|
|
|
д |
|
|
|
и |
|
|
|
|
|
д |
|
|
|
|
|
|
|
|
и |
|
|
|
|
|
|
|
д |
|
|
|
|
|
|
|
и |
|
|
|
|
|
|||||||||||||||||||
Как видно, в рассмотренной интерпретации второе условие формообразования поверхностей деталей |
|||||||||||||||||||||||||||||||||||||||||||||||||||||||||||||||||||||
достаточно просто описывается аналитически, что в первую очередь важно при составлении управляющих |
|||||||||||||||||||||||||||||||||||||||||||||||||||||||||||||||||||||
программ для систем ЧПУ металлорежущими станками. |
|
|
|
|
|
|
|
|
|
|
|
|
|
|
|
|
|
|
|
|
|
|
|
|
|
|
|
|
|
|
|
|
|
|
|||||||||||||||||||||||||||||||||||
7.1.3. Третье условие формообразования. В зависимости от соотношения величин и знаков радиусов |
|||||||||||||||||||||||||||||||||||||||||||||||||||||||||||||||||||||
кривизны |
|
нормальных |
сечений |
поверхностей |
|
|
Д |
|
|
и |
|
И , |
третье |
условие |
|
формообразования может |
либо |
||||||||||||||||||||||||||||||||||||||||||||||||||||
выполняться (рис. 7.2.1), либо нарушается (рис. 7.2.2). |
|
|
|
|
|
|
|
|
|
|
|
|
|
|
|
|
|
|
|
|
|
|
|
|
|
|
|
|
|
|
|
|
|
|
|
||||||||||||||||||||||||||||||||||
Причиной нарушения третьего условия формообразования поверхностей деталей является локальное |
|||||||||||||||||||||||||||||||||||||||||||||||||||||||||||||||||||||
внедрение инструмента в деталь – внедрение в |
|
|
|
|
|
|
|
|
|
|
|
|
|
|
|
|
|
|
|
|
|
|
|
|
|
|
|
|
|
|
|
|
|
|
|
|
|
|
|
|
|||||||||||||||||||||||||||||
дифференциальной окрестности точки К касания |
|
|
|
|
|
|
|
|
|
|
|
|
|
|
|
|
|
Rд Rи |
|
|
|
|
|
|
|
|
Rи |
Rд |
Rи |
||||||||||||||||||||||||||||||||||||||||
поверхностей Д и И . |
Это |
|
интерференция |
|
|
|
|
И |
|
|
|
|
|
|
|
|
|
|
|
|
|
|
|
|
И |
|
|
||||||||||||||||||||||||||||||||||||||||||
второго рода детали и инструмента. |
|
|
|
|
|
|
|
|
|
|
|
|
|
|
|
|
|
|
|
|
|
|
|
|
|
|
|
|
|
|
|
|
|
|
|
|
|
|
|
|
|
|
|
|
|
|
|
||||||||||||||||||||||
Третье условие формообразования требует, |
|
|
|
|
|
|
|
|
|
|
|
|
|
|
|
|
|
|
|
|
|
Rд |
|
|
|
|
|
|
|
|
|
|
|
|
|
|
|
R |
|
||||||||||||||||||||||||||||||
чтобы деталь и инструмент одновременно не |
|
|
|
|
|
|
|
|
|
|
|
|
|
|
|
|
|
|
|
|
|
|
|
|
|
|
|
|
|
|
|
|
|
|
|
|
|
|
|
|
|||||||||||||||||||||||||||||
занимали одну и ту же часть пространства в |
|
|
|
|
|
|
|
|
|
|
|
|
|
|
|
|
|
|
|
|
|
|
|
|
|
|
|
|
|
|
|
|
|
|
|
|
|
|
|
|
|||||||||||||||||||||||||||||
пределах дифференциальной окрестности точки |
|
|
|
|
|
|
|
|
|
|
|
|
|
|
|
|
|
|
|
|
|
|
|
|
|
|
|
|
|
|
|
|
|
|
|
|
|
|
|
|
|||||||||||||||||||||||||||||
их касания. Это условие формообразования имеет |
|
|
|
|
|
|
|
|
|
|
|
|
|
|
|
|
|
|
|
|
|
|
|
|
|
|
|
|
|
|
|
|
|
|
|
|
|
|
|
|
|||||||||||||||||||||||||||||
локальный |
|
|
|
характер |
|
|
|
– |
|
оно |
|
|
|
относится |
|
|
|
|
|
|
|
|
|
|
|
|
|
|
|
|
|
|
|
|
|
|
|
|
|
|
|
|
|
|
|
|
|
|
|
|
|
|
|
|
|||||||||||||||
исключительно к дифференциальной окрестности |
|
|
|
|
|
|
|
|
|
|
|
|
K |
|
|
|
|
|
|
|
|
|
|
|
|
|
|
|
|
|
|
|
|
|
|
|
|
K |
|
||||||||||||||||||||||||||||||
точки К , несмотря на то, |
|
что при его нарушении |
|
|
|
|
|
|
|
|
|
|
|
|
|
|
|
|
|
|
|
|
|
|
|
|
|
|
|
|
|
|
|
|
|
|
|
|
|
|
|
|
|||||||||||||||||||||||||||
искажения |
|
формы |
|
обработанной |
поверхности |
|
|
|
|
|
|
|
|
|
|
|
|
1. |
|
|
|
|
|
|
|
|
|
|
|
|
|
|
|
|
|
|
|
|
|
|
|
|
2. |
|
|||||||||||||||||||||||||
детали распространяются за пределы ее |
|
|
|
|
|
|
|
|
|
|
|
|
|
|
|
|
|
|
|
|
|
|
|
|
|
|
|
|
|
|
|
|
|
|
|
|
|
||||||||||||||||||||||||||||||||
|
|
|
|
|
|
|
|
|
|
|
|
|
|
|
|
|
|
|
|
|
|
|
|
|
|
|
|
|
|
|
|
|
|
|
|
|
|
|
|
||||||||||||||||||||||||||||||
дифференциальной окрестности. |
|
|
|
|
|
|
|
|
|
|
|
|
|
|
|
|
|
Рис. 7.2. Примеры выполнения и нарушения третьего |
|||||||||||||||||||||||||||||||||||||||||||||||||||
Сформулируем: |
|
|
|
|
|
|
|
|
|
|
|
|
|
|
|
|
|
|
|
|
|
|
|
|
|
|
|
||||||||||||||||||||||||||||||||||||||||||
|
|
|
|
|
|
|
|
|
|
|
|
|
|
|
|
|
|
|
|
|
|
|
|
|
|
|
|
|
|
|
|
|
|
|
условия |
|
формообразования |
поверхностей |
|||||||||||||||||||||||||||||||
|
|
|
|
|
|
|
|
|
|
|
|
|
|
|
|
|
|
|
|
|
|
|
|
|
|
|
|
|
|
|
|
|
|
|
|
|
|
|
|
|
|
|
|||||||||||||||||||||||||||
Третье условие: Поверхность |
|
Д |
|
детали |
|
|
|
|
|
|
|
|
|
|
|
|
деталей. |
|
|
|
|
|
|
|
|
|
|
|
|
|
|
|
|
|
|
|
|
||||||||||||||||||||||||||||||||
|
|
|
|
|
|
|
|
|
|
|
|
|
|
|
|
|
|
|
|
|
|
|
|
|
|
|
|
|
|
|
|
|
|
|
|
|
|
|
|
|
|
||||||||||||||||||||||||||||
может быть правильно формообразована, если |
|
|
|
|
|
|
|
|
|
|
|
|
|
|
|
|
|
|
|
|
|
|
|
|
|
|
|
|
|
|
|
|
|
|
|
|
|
|
|
|
|||||||||||||||||||||||||||||
она не интерферирует с поверхностью И инструмента в дифференциальной окрестности каждой точки их |
|||||||||||||||||||||||||||||||||||||||||||||||||||||||||||||||||||||
касания. |
|
|
|
|
|
|
|
|
|
|
|
|
|
|
|
|
|
|
|
|
|
|
|
|
|
|
|
|
|
|
|
|
|
|
|
|
|
|
|
|
|
|
|
|
|
|
|
|
|
|
|
|
|
|
|
|
|
|
|
|
|
|
|
|
|
|
|
|
|