
Radzevich, S.P. Monograph - 2001
.pdf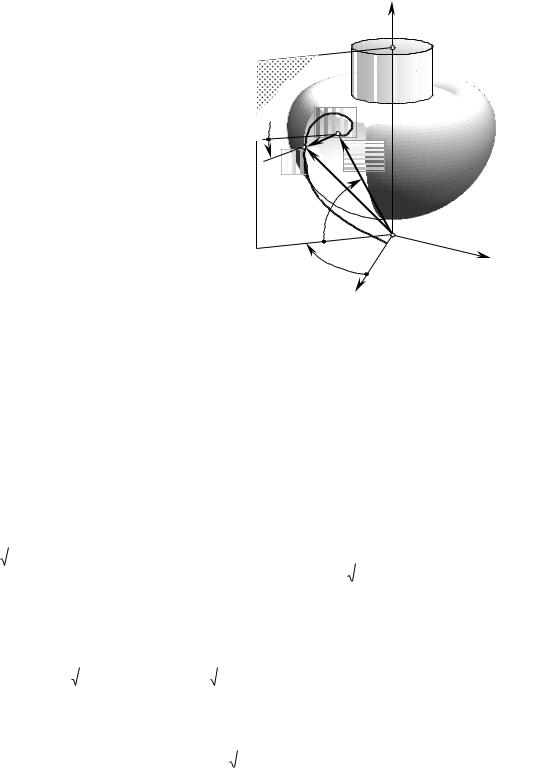
310 |
|
|
|
|
|
|
|
|
5. Профилирование фасонных режущих инструментов |
|
|
|
|
||||||
где Rп – расположенный под постоянным углом радиус-вектор, определяющий положение полюса систе- |
|||||||||||||||||||
мы координат. |
|
|
|
|
|
|
|
|
|
|
|
|
|
|
|||||
В этих уравнениях первое слагаемое постоянно по величине. Поэтому |
|
|
|
|
|
||||||||||||||
|
X |
и |
r |
и |
R |
cos sin ; |
|
|
Zu |
|
|
||||||||
|
|
|
|
|
|
и |
|
|
|
|
|
|
|
|
|
|
|||
|
Yи |
rи Rи cos cos ; |
|
|
|
|
|
||||||||||||
|
Z |
и |
r |
tan R |
sin . |
|
|
|
|
|
|||||||||
|
|
|
и |
|
|
|
|
|
|
и |
|
|
|
|
|
|
|
||
Подставив (48) в последние уравнение, получим уравне- |
|
|
|
|
|
||||||||||||||
ние поверхности |
И инструмента, |
записанное в параметричес- |
|
|
|
|
|
||||||||||||
кой форме: |
|
|
|
|
|
|
|
|
|
|
|
|
|
|
R u |
|
|
|
|
|
|
|
|
|
rи |
|
Rоe |
c |
cos sin ; |
|
R n |
|
|
|
|||||
|
Xи |
|
|
|
A |
|
|
|
|||||||||||
(5.50) |
|
|
|
|
rи |
Rоe |
c |
cos |
cos ; |
ru |
|
|
|
|
|||||
Yи |
|
|
|
|
|
|
|
||||||||||||
|
Z |
и |
r |
tan R ec sin . |
|
|
|
|
|
||||||||||
|
|
|
и |
|
|
|
|
|
|
о |
|
|
|
|
|
|
|
||
|
|
|
|
|
|
|
|
|
|
|
|
|
|
|
|
|
|
|
|
|
|
|
|
|
|
|
|
|
|
|
|
|
|
|
|
|
|
|
|
Таким путем можно образовать исходную инструменталь- |
|
|
|
|
Yu |
||||||||||||||
ную поверхность как с выпуклой, |
|
так и с вогнутой образую- |
|
|
|
|
|
||||||||||||
щей, поверхность |
И инструмента охватывающего типа и др. |
|
|
|
|
||||||||||||||
|
|
|
|
|
|||||||||||||||
На основе найденных поверхностей И |
проектируются раз- |
|
Xu |
|
|
|
|||||||||||||
личные конструкции фасонных фрез, шлифовальных кругов и |
|
|
|
|
|||||||||||||||
др. фасонных инструментов. |
|
|
|
|
|
|
|
Рис. 5.15. Образование |
исходной |
инстру- |
|||||||||
Чтобы найти |
уравнение |
индикатрисы кривизны Ind И |
ментальной поверхности фасон- |
||||||||||||||||
исходной инструментальной поверхности и таким путем полу- |
ного |
инструмента |
вращением |
||||||||||||||||
чить информацию о геометрической структуре этой поверхно- |
логарифмической спирали. |
||||||||||||||||||
сти в дифференциальной окрестности текущей точки на ней, |
|
|
|
|
|
||||||||||||||
необходимо определить гауссовы коэффициенты Eи , Fи , Gи первой Φ1.и |
и Lи , Mи , Nи |
второй Φ2.и основ- |
|||||||||||||||||
ных квадратикных форм. Для этого продифференцируем каждое из уравнений (50) по |
и |
и подставим |
|||||||||||||||||
найденные значения производных в (1.47). После преобразований получим: |
|
|
|
|
(5.51) |
|
|
E |
и |
R2e2c 1 c2 ; |
|
|
|
F |
и |
0 ; |
|
|
G |
и |
|
r R ec |
cos 2 . |
|
|
|
|
|
|||||||||||||||
|
|
|
|
|
|
o |
|
|
|
|
|
|
|
|
|
|
|
|
и |
o |
|
|
|
|
|
|
|
|
|
|
||||||||
Вычислив вторые производные (50) по |
и и подставив найденные их значения в (1.48)-(1.50), |
|||||||||||||||||||||||||||||||||||||
находим, что: |
|
|
|
|
|
|
|
|
|
|
|
|
|
|
|
|
|
|
|
|
|
|
|
|
|
|
|
|
|
|
|
|
|
|
|
|
|
|
|
|
R ec |
|
|
|
|
|
|
|
|
|
|
|
|
|
|
|
|
R ec |
cos |
c sin |
cos |
. |
|
|
|||||||||||||
(5.52) |
L |
1 c2 ; |
|
M |
и |
0 |
, |
|
N |
и |
r |
|
|
|
|
|||||||||||||||||||||||
|
|
|
|
|
|
|
||||||||||||||||||||||||||||||||
|
и |
|
o |
|
|
|
|
|
|
|
|
|
|
|
|
|
и |
|
|
o |
|
|
|
1 c2 |
|
|
||||||||||||
|
|
|
|
|
|
|
|
|
|
|
|
|
|
|
|
|
|
|
|
|
|
|
|
|
|
|
|
|
|
|
|
|
||||||
Подставив (51) и (52) в (4.52), приходим к уравнению индикатрисы кривизны |
Ind И поверхности И |
|
||||||||||||||||||||||||||||||||||||
инструмента: |
|
|
|
|
|
|
|
|
|
|
|
|
|
|
|
|
|
|
|
|
|
|
|
|
|
|
|
|
|
|
|
|
|
|
|
|
|
|
|
|
|
|
|
|
|
|
|
|
1 |
|
|
|
x2 |
|
c sin cos |
|
|
y2 1. |
|
|
|
|
|
|
|||||||||||||
|
|
|
|
|
|
|
|
|
|
|
|
|
|
|
|
|
|
|
|
|
|
|
|
|
|
|
|
|
|
|
||||||||
|
|
|
|
|
|
|
|
R ec |
|
|
|
|
|
R ec |
|
|
|
|
|
|
|
|
|
|
|
|
|
|
||||||||||
|
|
|
|
|
|
|
|
1 c2 |
|
1 c2 |
|
|
|
|
|
|
||||||||||||||||||||||
|
|
|
|
|
|
|
|
|
|
r |
cos |
|
|
|
|
|
|
|
|
|
|
|
||||||||||||||||
|
|
|
|
|
|
|
|
o |
|
|
|
|
|
|
и |
o |
|
|
|
|
|
|
|
|
|
|
|
|
|
|
|
|
|
|
|
|
|
|
Значения главных радиусов кривизны исходной инструментальной поверхности И рассчитываются как |
||||||||||||||||||||||||||||||||||||||
корни квадратного уравнения (1.110), которое для рассматриваемого случая преобразуется к виду: |
|
|
||||||||||||||||||||||||||||||||||||
c sin cos |
R2 |
|
|
|
R ec cos R ec |
c sin cos |
|
|
|
|
R ec r |
|
R ec cos |
|
|
|||||||||||||||||||||||
|
|
r |
|
1 c2 R |
|
и |
1 c2 |
0. |
||||||||||||||||||||||||||||||
|
|
1,2.и |
|
|
и |
o |
|
|
o |
|
|
|
|
|
|
|
|
|
|
|
|
1,2.и |
|
o |
|
o |
|
|

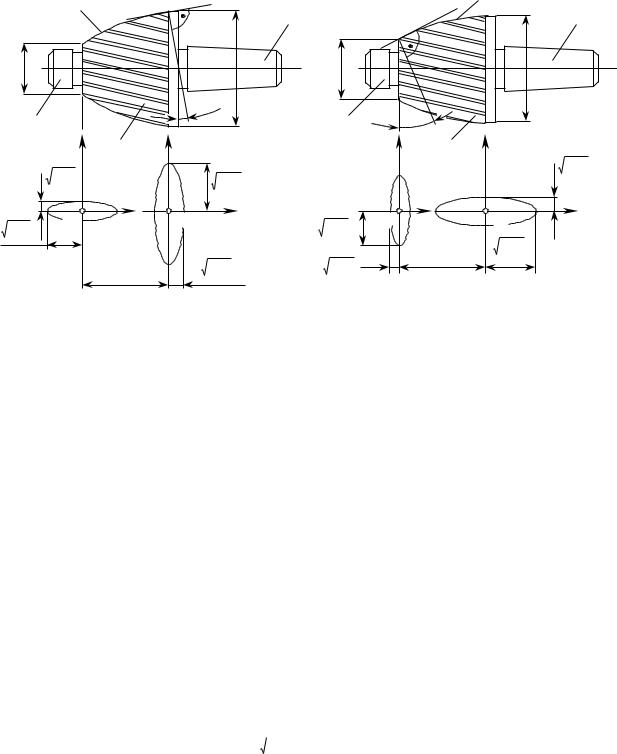
312 |
5. Профилирование фасонных режущих инструментов |
|
|
4 |
4 |
|
|
|
|
2 |
2 |
|
Dи |
Dи |
|
dи |
dи |
|
|
|
1 |
|
|
|
|
3 |
|
|
|
3 |
2 |
|
|
|
|
|
|
|
|
|
|
yи |
1 |
yи |
|
yи |
1 |
yи |
|
|
|
|
Rmin |
||||
Rmin |
|
|
max |
|
|
|
2.и |
|
|
|
|
|
|
||
1.и |
|
xи |
R2.и |
Ind Иd |
|
|
|
|
|
|
xи |
|
|
||
|
|
|
|
|
|
||
|
|
|
x |
|
|
|
x |
Md |
|
MD |
Md |
|
MD |
||
Rmin |
Ind Иd |
и |
min |
|
|
и |
|
|
R1.и |
|
|
|
|||
2.и |
|
|
|
|
|
|
|
|
|
|
|
|
Ind ИD |
Rmax |
|
|
|
|
|
|
|
|
|
|
|
|
|
lи |
1.и |
|
|
|
|
Ind ИD |
Rmax |
R2.maxи |
|
|
|
|
|
lи |
|
|
|
||
|
|
1.и |
|
|
|
|
|
|
|
|
1. |
|
|
|
2. |
Рис. 5.18. Инструмент для обработки сложных поверхностей деталей (а.с. №1355378).
принимает соответственно минимальное Rmin |
и максимальное |
Rmax |
значения. Можно также указать не менее двух точек, в которых |
||
|
1.и |
|
1.и |
|
|
второй главный радиус кривизны R |
принимает минимальное |
Rmin |
и максимальное Rmax |
значения. В частном случае точки (две пары |
|
2.и |
|
|
2.и |
2.и |
|
точек), в которых главные радиусы кривизны принимают экстремальные значения, могут попарно совпадать. Возможны два варианта таких пар точек.
|
|
В первом случае главные радиусы кривизны принимают экстремальные значения Rmin |
, |
Rmin |
в одной из точек поверхности И и |
|||||||||||||||||||||||||||||||||
|
|
|
|
|
|
|
|
|
|
|
|
|
|
|
|
|
|
|
|
|
|
|
|
|
|
|
|
|
1.и |
|
2.и |
|
|
|
|
|
|
|
Rmax , |
Rmax |
– в другой. Во втором случае они принимают экстремальные значения |
Rmin , Rmax в одной и Rmax , Rmin – в другой точке |
|||||||||||||||||||||||||||||||||||
|
1.и |
2.и |
|
|
|
|
|
|
|
|
|
|
|
|
|
|
|
|
|
|
|
|
|
|
|
|
|
1.и |
2.и |
|
|
1.и |
2.и |
|
|
|||
исходной инструментальной поверхности. |
|
|
|
|
|
|
|
|
|
|
|
|
|
|
|
|
|
|
|
|
|
|
|
|||||||||||||||
|
|
Ориентация образующей 4 поверхности И инструмента (рис. 5.18) относительно оси его вращения зависит от диаметров dи |
и Dи у |
|||||||||||||||||||||||||||||||||||
его торцов и расстояния lи |
между ними. С учетом изложенного выше она может быть увязана с этими параметрами двумя путями. |
|||||||||||||||||||||||||||||||||||||
|
|
В первом случае (рис. 5.18.1) образующая 4 так расположена относительно оси вращения инструмента, что экстремальные значения |
||||||||||||||||||||||||||||||||||||
главных радиусов кривизны исходной инструментальной поверхности принимают значения |
|
Rmin , |
Rmin |
у торца меньшего диаметра и |
||||||||||||||||||||||||||||||||||
|
|
|
|
|
|
|
|
|
|
|
|
|
|
|
|
|
|
|
|
|
|
|
|
|
|
|
|
|
|
|
1.и |
2.и |
|
|
|
|
|
|
Rmax , |
Rmax |
– у торца большего диаметра. В точке M |
образующей у торца меньшего диаметра индикатриса кривизны поверхности И |
|||||||||||||||||||||||||||||||||||
|
1.и |
2.и |
|
|
|
|
|
|
|
|
|
|
|
|
|
|
|
d |
|
|
|
|
|
|
|
|
|
|
|
|
|
|
|
|
|
|
|
|
инструмента имеет вид |
|
|
|
, а в точке |
|
|
|
|
|
|
|
|
|
|
|
|
|
|
|
|
|
|
|
|
и |
|
||||||||||||
Ind Иd |
MD у торца большего диаметра – Ind ИD . Индикатрисы кривизны |
Ind Иd |
Ind ИD |
|||||||||||||||||||||||||||||||||||
построены каждая в своей локальной системе координат x M |
y |
и x M |
y |
|
соответственно. |
|
|
|
|
|
|
|
|
|||||||||||||||||||||||||
|
|
|
|
|
|
|
|
|
|
|
|
|
|
|
|
|
|
|
|
и |
d |
и |
|
и |
D |
и |
|
|
|
|
|
|
|
|
|
|
|
|
|
|
Во втором случае (рис. 5.18.2) образующая 4 расположена относительно оси вращения инструмента так, что экстремальные значения |
||||||||||||||||||||||||||||||||||||
главных радиусов кривизны поверхности И инструмента принимают значения Rmin , Rmax |
у торца меньшего диаметра и Rmax , |
Rmin – |
||||||||||||||||||||||||||||||||||||
|
|
|
|
|
|
|
|
|
|
|
|
|
|
|
|
|
|
|
|
|
|
|
|
|
|
|
|
1.и |
2.и |
|
|
|
|
|
|
|
1.и |
2.и |
у торца большего диаметра. В точке |
Md |
образующей у торца меньшего диаметра индикатриса кривизны поверхности И инструмента |
||||||||||||||||||||||||||||||||||||
|
|
|
|
|
|
|
|
|
|
|
|
|
|
|
|
|
|
|
|
|
|
|
|
|
|
|
|
|
|
|
|
|
|
построены каждая в |
||||
имеет вид Ind Иd , а в точке MD |
у торца большего диаметра – Ind ИD |
. Индикатрисы кривизны Ind Иd |
и Ind ИD |
|||||||||||||||||||||||||||||||||||
своей локальной системе координат |
|
|
|
|
|
и |
|
|
соответственно. |
|
|
|
|
|
|
|
|
|
|
|
|
|
||||||||||||||||
|
xиMd yи |
|
xиMD yи |
|
|
|
|
|
|
|
|
|
|
|
|
|
||||||||||||||||||||||
|
|
Значения главных радиусов кривизны |
R1.и |
и R2.и |
исходной инструментальной поверхности |
И в произвольной ее точке равны |
||||||||||||||||||||||||||||||||
(4.101) |
|
|
|
|
|
|
|
|
|
|
|
|
|
|
|
|
|
|
|
|
|
|
|
|
|
|
|
|
|
|
|
|
|
|
|
|
||
|
|
|
|
|
|
|
|
|
|
|
|
|
|
|
|
|
|
|
|
|
|
|
|
|
|
|
|
|||||||||||
|
|
|
|
|
|
|
|
|
(E |
и |
N |
и |
2F M |
и |
G L ) (E N |
и |
2F M |
и |
G L )2 |
4(E G F 2 )(L N |
и |
M 2 ) |
|
|
|
|||||||||||||
|
|
|
|
|
|
R1,2.и |
|
|
|
|
|
и |
и и |
|
|
и |
и |
|
|
и и |
и и |
и |
и |
и |
|
|
|
|||||||||||
|
|
|
|
|
|
|
|
|
|
|
|
|
|
|
|
|
|
|
|
|
|
|
|
|
2 |
|
|
|
|
|
|
. |
|
|
|
|||
|
|
|
|
|
|
|
|
|
|
|
|
|
|
|
|
|
|
|
|
|
|
2(LиNи Mи ) |
|
|
|
|
|
|
|
|
|
|
||||||
|
|
Больший диаметр D |
инструмента (см. рис. 5.18.1) равен |
D 2Rmax cos , |
а меньший диаметр инструмента (см. рис. 5.18.2) – |
|||||||||||||||||||||||||||||||||
|
|
|
|
|
|
|
и |
|
|
|
|
|
|
|
|
|
|
|
|
|
|
|
|
и |
2.и |
|
1 |
|
|
|
|
|
|
|
|
|
|
|
d |
и |
2Rmin cos |
2 |
. Здесь |
|
и |
2 |
– углы между касательными к образующей исходной инструментальной поверхности и осью вращения |
||||||||||||||||||||||||||||||
|
|
2.и |
|
|
1 |
|
|
|
|
|
|
|
|
|
|
|
|
|
|
|
|
|
|
|
|
|
|
|
|
|
|
|
|
|
|

314 5. Профилирование фасонных режущих инструментов
Применение инструмента (см. рис. 5.19) поволяет увеличить производительность обработки и улучшить ее качество.
Для многокоординатной обработки сложных поверхностей деталей находят применение инструменты, параметрами формы исходной инструментальной поверхности которых можно управлять от системы ЧПУ станком (Родин П.Р. и др., 1976; Радзевич С.П., 1988; и др.). Такого типа инструменты используются, например, при изготовлении деталей оснастки из древесины, пластмасс, легких сплавов и др. Уравнение исходной инструментальной поверхности фасонных инструментов подобного типа всегда содержит не менее одного переменного параметра, которым в процессе обработки можно управлять от системы ЧПУ станком.
Очевидно, что для случаев формообразования сложных поверхностей деталей на многокоординатных станках с ЧПУ образовать исходную инструментальную поверхность И фасонного режущего инструмента как огибающую последовательных положений поверхности Д в ее движении относительно системы коорди-
нат инструмента нельзя – кинематика формообразования заранее не известна. Одна и та же сложная поверхность детали может быть обработана одним и тем же фасонным инструментом при различной кинематике формообразования. Поэтому для случаев обработки сложных поверхностей деталей на многокоординатных
станках с ЧПУ наивыгоднейший фасонный инструмент может быть спроектирован только исходя из -ото- бражения поверхности Д на поверхность И , т.е. на основе соответствия элементов локальной топологии в
точках поверхности И элементам локальной топологии в точках поверхности Д .
Использование частных способов образования ИИП И предполагает, что для заданной детали анализируется возможность ее формообразования в соответствие с каждой из принципиальных кинематических схем формообразования (см. гл. 2). Те принципиальные кинематические схемы формообразования, в соответствие с которыми для заданной поверхности Д детали образовать поверхность И инструмента нельзя, из дальней-
шего рассмотрения исключаются. Те же принципиальные кинематические схемы формообразования, в соответствие с которыми для заданной поверхности Д может быть образована исходная инструментальная по-
верхность И , подвергаются детальному анализу, в соответствие с ними образуют исходные инструментальные поверхности, на основе которых проектируются соответствующие конструкции режущих инструментов.
5.4.Основные задачи профилирования режущего инструмента
иформообразования поверхности детали
Профилирование фасонных режущих инструментов представляет собой сложную инженерную проблему, сущность решения которой заключается в том, чтобы определить всю информацию о геометрии рабочих поверхностей режущего клина, необходимую для изготовления инструмента.
Чтобы решить задачу профилирования инструмента относительно простой конструкции достаточно найти профиль некоторого (обычно нормального) сечения его задней (при известной передней) или передней (при известной задней) поверхности. Например, профилирование призматического фасонного резца, сводится к нахождению профиля нормального сечения его задней поверхности; круглого фасонного резца – к нахождению профиля осевого сечения его задней поверхности; затылованных дисковых фрез – к отысканию профиля нормального сечения затылованной задней поверхности и т.д. Найденных параметров профиля нормального сечения задней поверхности достаточно для изготовления такого инструмента.
Вопрос о сущности решения задачи профилирования усложняется, когда речь идет о профилировании более сложных фасонных режущих инструментов, например, инструментов, работающих по методу обката – затылованных червячных фрез и др.
Единственно правильной постановкой задачи профилирования фасонных режущих инструментов следует считать такую, при которой найденное решение позволяет однозначно ответить на все принципиальные вопросы формообразования рабочих поверхностей режущего клина инструмента. В таком аспекте сущность решения проблемы профилирования режущего инструмента сводится к нахождению полной геометрической информации о рабочих поверхностях режущего клина фасонного режущего инструмента и формы его режущей кромки, совпадающей с линией пересечения рабочих поверхностей режущего клина инструмента.
Проблема профилирования фасонных режущих инструментов в такой постановке является наиболее полной и имеет законченную форму. Она включает в себя нахождение исходной инструментальной поверхности, образование передних и задних поверхностей зубьев инструмента и формообразование его рабочих поверхностей. В этом разделе ограничимся рассмотрением только первого этапа решения рассматриваемой проблемы, а именно: определения формы и параметров исходной инструментальной поверхности профилируемого



318 |
5. Профилирование фасонных режущих инструментов |
ция (8) приводит к тому, что формообразование поверхности Д производится не геометрически точной исходной инструментальной поверхностью ИR(1) , а приближенной производящей поверхностью Пи(2) . Поверх-
ность Пи(2) аппроксимирует поверхность ИR(1) так, что погрешность аппроксимации минимальна и не превышает заданный допуск на точность профилирования.
Данные о геометрии поверхности Д детали (9) и производящей поверхности Пи(2) инструмента (10) позволяют найти кинематику формообразования Krm(2) .
Затем по данным о геометрии производящей поверхности Пи(2) инструмента (11) и о кинематике формообразования Krm(2) (12) определяются параметры фактически формообразованной поверхности Дф(2) детали.
Эти параметры сопоставляются (13) с соответствующими параметрами номинальной поверхности Д , на
основании чего делается вывод о том, насколько точно решены задачи аппроксимации поверхности И инструмента и формообразования поверхности детали.
Найденное таким путем решение будет позитивным решением задачи профилирования режущего инструмента и формообразования поверхности детали. Наивыгоднейшее решение задачи может быть
получено путем синтеза наивыгоднейшей геометрии касания поверхности Д детали и производящей поверхности Пи(2) инструмента. Для этого:
Задача 3. по данным (1) о геометрии поверхности Д и производящей поверхности Пи(2) (14) (параметры которой связаны (10) с кинематикой формообразования) синтезируется (15) наивыгоднейшая кинематика формообразования Krm(3) (с учетом ограничений, являющихся следствием замены геометрически точной
исходной инструментальной поверхности И производящей поверхностью Пи(2) инструмента). После этого по данным (16) о геометрии поверхности Пи(3) Пи(2) инструмента и о кинематике формообразования Krm(3) (17) находится фактически формообразованная поверхность Дф(3) детали. Сопоставление (18) параметров ее формы с параметрами формы поверхности Д позволяет сделать вывод о том, насколько точно решены зада-
чи аппроксимации поверхности И поверхностью Пи(2) и синтеза кинематики формообразования Krm(3) .
Задача 4. Обработка детали, как правило, ее сложной поверхности, может быть произведена инструментом, выбранным из номенклатуры имеющегося. В этом случае параметры его исходной инструментальной
поверхности И(4) непосредственно не связаны с параметрами поверхности ИR(1) , найденной как -отобра-
жение поверхности Д .
Исходя из геометрии заданной чертежом номинальной поверхности Д детали (19) и геометрии поверх-
ности И(4) выбранного инструмента (20) расчитываются параметры кинематики формообразования Krm(4) .
Так находится позитивное решение задачи профилирования фасонного режущего инструмента и формообразования поверхности детали.
При выборе инструмента из номенклатуры имеющегося не исключена возможность, что будет выбран инструмент, исходная инструментальная поверхность которого совпадает с -отображением поверхности Д ,
т.е. |
И(4) И(1) |
(см. выше, Задача 1). В этом случае кинематика формообразования заданной поверхности Д |
|
|
R |
|
|
детали поверхностью И(1) |
инструмента находится как и для любой другой поверхности И выбранного |
||
|
|
R |
|
инструмента.
Информация о геометрии поверхности И(4) выбранного инструмента (21) и о кинематике формообразования Krm(4) используется (22) для нахождения фактически формообразованной поверхности Дф(4) детали. Ее
параметры сопоставляются (23) с соответствующими параметрами номинально поверхности Д детали. На
этом основании делается вывод о том, насколько удачно решены задачи выбора инструмента и формообразования поверхности детали.
5.4. Основные задачи профилирования режущего инструмента и формообразования поверхности детали |
319 |
Задача 5. Обработка детали инструментом выбранной конструкции может производиться при наивыгоднейшей для него кинематике формообразования. Для этого по данным о геометрии поверхности Д детали (1)
и поверхности И(4) инструмента (24) синтезируется наивыгоднейшая геометрия касания поверхностей Д и И(4) и на этом основании чего расчитываются (25) параметры наивыгоднейшей кинематики формообразования Krm(5) заданной поверхности детали выбранным инструментом.
Если (в частном случае) эта задача решена для исходной инструментальной поверхности, в качестве которой выбрана поверхность ИR(1) , то формообразованная поверхность Дф(5) детали будет идентична
поверхности Дф(1) , формообразование которой рассмотрено выше (см. выше. Задача 1).
Данные о геометрии поверхности И(5) И(4) выбранного инструмента (26) и о синтезированной кинематике формообразования Krm(5) (27) позволяют определить фактически формообразованную поверхность
Дф(5) детали. Сопоставив Дф(5) с номинальной поверхностью Д , заключаем (28) насколько точно решены
задачи выбора инструмента, синтеза кинематики и формообразования поверхности детали.
Этот подход к решению задачи профилирования режущего инструмента и формообразования поверхности детали находит практическое применение.
Задача 6. На параметры синтезированной наивыгоднейшей кинематики многокоординатного формообразования могут быть наложены ограничения, которые могут носить такой характер, что наивыгоднейшая ”гибкая” кинематика формообразования заменяется “жесткой” принципиальной кинематической схемой формообразования. Общее количество потенциально возможных принципиальные кинематические схемы формообразования конечно (см. выше, раздел 5.3) и исчерпывается двадцатью принципиальными кинематическими схемами формообразования (см. рис. 2.14 и рис. 2.15). Очевидно, что кинематика формообразования
Krm(6) , реализуемая одной из принципиальных кинематических схем формообразования, является частным
случаем “гибкой” кинематики формообразования Krm(1) .
Решение задачи профилирования инструмента, а затем – задачи формообразования поверхности детали при использовании “жестких” принципиальных кинематических схем формообразования, выполняется в такой последовательности.
По данным о геометрии обрабатываемой поверхности Д детали (29) и выбранной из рис. 2.14 и рис. 2.15 кинематической схеме формообразования Krm(6) находится (30) исходная инструментальная поверх-
ность И(6) . Поверхность И(6) |
инструмента является огибающей последовательных положений поверхности |
Д детали в ее одно-, двух- |
или многопараметрическом движении относительно системы координат, с |
которой впоследствие будет связан инструмент (см. выше, раздел 5.3).
Найденная поверхность И(6) инструмента совершает относительно детали одно-, двухили многопараметрическое движение. Это движение имеет те же параметры, что и движение, рассматриваемое при профилировании инструмента, но противоположно направленно. Это дает возможность по данным о геометрии
поверхности И(6) инструмента (31) и о реализуемой принципиальными кинематическими схемами кинематике формообразования Krm(6) (32) найти фактически формообразованную поверхность Дф(6) детали. Поверх-
ность Дф(6) является огибающей последовательных положений поверхности И(6) , движущейся относительно
системы координат детали. Сопоставление (33) параметров геометрии поверхности Дф(6) с параметрами
номинальной поверхности Д дает основание сделать вывод о том, насколько точно решены задачи профили-
рования инструмента и формообразования поверхности детали.
Этот подход к решению задачи профилирования режущего инструмента и формообразования поверхности детали находит практическое применение.
Таким путем находится позитивное решение задачи профилирования фасонного режущего инструмента и формообразования поверхности детали при использования “жестких” принципиальных кинематических схем формообразования. Чтобы найденное решение было наивыгоднейшим (т.е. чтобы найти наивыгодней-