
- •Процессы и инструменты механообработки
- •Введение
- •Общие положения
- •Геометрия передней поверхности сверла
- •Выводы
- •Литература
- •ДГМА, г. Краматорск, Украина
- •Введение
- •Литература
- •Введение
- •Общие положения
- •Методика исследования
- •Коэффициент технологической гибкости
- •Литература
- •Введение
- •Выводы
- •Литература
- •Введение
- •Методика исследований
- •Основная часть
- •Введение
- •Введение
- •Выводы
- •Введение
- •Экспериментальная часть исследований
- •Литература
- •Введение
- •Выводы
- •ДГМА, г.Краматорск, Украина
- •Введение
- •Выводы
- •Литература
- •ДГМА, г.Краматорск, Украина
- •Выводы
- •Вступ
- •Висновки
- •ДГМА, Краматорск, Украина
- •Введение
- •Выводы
- •Література
- •Вступ
- •Основна частина
- •Технология машиностроения
- •Вступ
- •Постановка задач дослідження
- •Результати досліджень
- •Література
- •Введение
- •Постановка проблемы, анализ публикаций
- •Выделение нерешенных ранее частей общей проблемы
- •Постановка задачи
- •Выводы
- •Литература
- •Вступ
- •Вступ
- •ПРИ МЕХАНИЧЕСКОЙ ОБРАБОТКЕ
- •Литература
- •Выводы
- •Литература
- •Поля базы данных (конечные синдромы): SMAX
- •Литература
- •Введение
- •Общие положения
- •Основная часть
- •Выводы
- •Литература
- •Введение
- •Основная часть
- •Введение
- •Выводы
- •Выводы
- •Вступ
- •Основна частина
- •Висновки
- •Фокин А.Г.
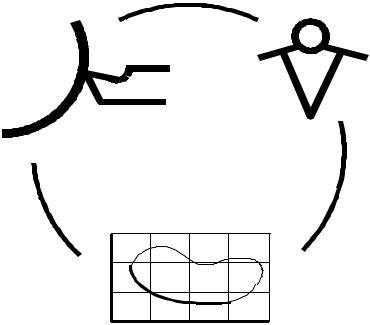
ISBN 966-7851-19-2 Надійність інструменту та оптимізація технологічних систем. №14 2003.
Міністерство освіти і науки України
Донбаська державна машинобудівна академія
НАДІЙНІСТЬ ІНСТРУМЕНТУ
ТА ОПТИМІЗАЦІЯ ТЕХНОЛОГІЧНИХ СИСТЕМ
Збірник наукових праць
Випуск 14
КРАМАТОРСЬК - 2003
1
ISBN 966-7851-19-2 Надійність інструменту та оптимізація технологічних систем. №14 2003.
УДК 621.9: 658.3: 658.5: 519.8
Рекомендовано до видання Вченою радою Донбаської державної машинобудівної академії
Надійність інструменту та оптимізація технологічних систем. Збірник наукових праць. - Краматорськ: ДДМА, вип. №14, 2003. - -204 с.
Надежность инструмента и оптимизация технологических систем. Сборник научных трудов. - Краматорск: ДГМА, вып.№14, 2003. - 204 с.
ISBN 966-7851-19-2
Редакційна рада:
Равська Н.С.
Гузенко В.С.
Верещака А.С. Габузов Г.Г. Грабченко А.І. Клименко Г.П. Ковалевський С.В. Ковальов В.Д. Кузнєцов Ю.М. Матюха П.Г. Мироненко Є.В. Михайлов О.М. Струтинський В.Б. Рогов В.О. Тарасов О.Ф. Федорінов В.А.
д.т.н., професор НТУ “КПІ”, відповідальний редактор к.т.н., доцент ДДМА,
заступник відповідального редактора д.т.н., професор МДТУ “Станкін”
д.т.н., професор ДДМА д.т.н., професор НТУ “ХПІ” д.т.н., професор ДДМА д.т.н., професор ДДМА д.т.н., професор ДДМА д.т.н., професор НТУ “КПІ” д.т.н., професор ДНТУ к.т.н., доцент ДДМА д.т.н., професор ДНТУ д.т.н., професор НТУ “КПІ” д.т.н., професор РУДН д.т.н., професор ДДМА к.т.н., професор ДДМА
Адреса редакційної ради: 84313, Україна, м. Краматорськ, вул. Шкадінова 72, Донбаська державна машинобудівна академія, науково-технічний центр ’'Інструмент''
тел.( 0626) 41-69-42, 41-47-54, 41-47-82
ISBN 966 – 7851 – 19 – 2 © Донбаська державна машинобудівна академія 2003
2
ISBN 966-7851-19-2 Надійність інструменту та оптимізація технологічних систем. №14 2003.
РАЗДЕЛ 1 Процессы и инструменты механообработки
УДК 621.91.02
Равская Н.С., Николаенко Т.П., Мельничук Л.С.
НТУУ«КПИ» г.Киев, Украина
ОБЩАЯ ТЕОРИЯ ОПРЕДЕЛЕНИЯ ГЕОМЕТРИЧЕСКИХ ПАРАМЕТРОВ ИНСТРУМЕНТА
The common approach and techniques of the decision of problems by definition of elements of an edge of the cutting tool irrespective of his kind and a design is offered.
Введение
Геометрические параметры в рассматриваемой точке режущей кромки инструмента характеризуются величинами передних, задних углов, углами
вплане и углами наклона режущей кромки.
Внастоящее время теория определения геометрических параметров разработана для каждого из видов инструмента. Однако, несмотря на общность определения элементов лезвия любого из инструментов согласно ГОСТ 25762-83 методики их количественного определения в исследуемых точках режущей кромки и определение их значений в различных координатных системах не учитывают стандартных определений. Это вносит определенную неточность в расчеты значений геометрических параметров, что объясняется отсутствием общей теории определения геометрических параметров инструментов.
Общие положения
В теории резания и проектирования режущих инструментов определение их геометрических параметров ориентировано относительно поверхности резания [1, 2], которая представляет собой поверхность, образующую режущей кромкой в результирующем движении резания [3]. В тоже время стандартом регламентируются инструментальная, статическая и кинематическая системы координат, в которых определяются инструментальные, статические и кинематические элементы лезвия инструмента независимо от вида и конструкции его. Вместе с тем анализ и определение геометрии режущей части инструмента в современной теории его проектирования осуществляется без учета их ориентации в соответствующих координатных системах. Это привело к разнообразию методик определения геометрических параметров в зависимости от вида инструмента. Стандартные определения геометрических параметров в координатных системах ориентированы относительно плоскостей, определяемых направлением главного или результирующего движения.
К этим плоскостям относятся рабочая плоскость Рs, основная плос-
3
ISBN 966-7851-19-2 Надійність інструменту та оптимізація технологічних систем. №14 2003.
кость Рv, плоскость резания Рn, главная секущая плоскость Рτ, нормальная секущая плоскость Рн и секущая плоскость схода стружки Рc.
Рабочая плоскость Рs это плоскость, в которой расположены направления главного движения и движения подачи.
Основная плоскость в рассматриваемой точке режущей кромки Рv перпендикулярна скорости главного движения V или результирующего движения Vе . Различают инструментальную основную плоскость Рvn, статическую Рvc и кинематическую – Рvк , соответственно в инструментальной, статической и кинематической системах координат.
Координатная плоскость, касательная к режущей кромке К, в рассматриваемой точке и перпендикулярная к Рv является плоскостью резания Рn
соответственно Рnи Pvи, Pnc Pvc и Pnк Pvк.
Координатная плоскость, перпендикулярная линии пересечения Рv и Рn представляет собой главную секущую плоскость резания Рτ. По аналогии с РV и Рn рассматривают секущие плоскости, ориентированые относительно инструментальной, статической и кинематической систем коорди-
нат - Рτи, Рτс и Рτк.
Нормальная секущая плоскость Рн перпендикулярна к режущей кромке в рассматриваемой точке режущей кромки.
Секущая плоскость схода стружки Рc, определяется как плоскость, проходящая через направления схода стружки и скорости резания в рассматриваемой точке режущей кромки.
Расположение и ориентация этих плоскостей служит основой определения геометрических параметров режущего инструмента.
Положение передней поверхности режущего лезвия Аγ, по которой сходит стружка в той или иной координатной системе определяется передним углом γ. Угол γ это угол в секущей плоскости между передней поверхностью лезвия и плоскостью Рv. В зависимости от секущей плоскости Ри, Рτс Рτк или нормальной Рн рассматривают нормальный передний угол - γн, а углы γи, γc, γк, которые называют инструментальным, статическим и кинематическим, передними углами. Угол в секущей плоскости схода стружки Рc между передней поверхностью лезвия и плоскостью Рv называют рабочим передним углом γр.
По аналогии с передними углами рассматривают задние углы αн, αи, αc, αк и αр. Задний угол находится в соответствующей секущей плоскости между задней поверхностью и соответствующей плоскостью резания.
Угол в плоскости резания между режущей кромкой и основной плоскостью является углом наклона режущей кромки λ и аналогично γ и α рас-
сматриваются λи, λc и λк.
Угол в плане – это угол в основной плоскости между плоскостью ре-
4
ISBN 966-7851-19-2 Надійність інструменту та оптимізація технологічних систем. №14 2003.
зания и рабочей плоскостью, соответственно ϕи, ϕc и ϕк являются инструментальным, статическим и кинематическим углами в плане.
Угол между режущей кромкой и рабочей плоскостью является рабочим кинематическим углом в плане – ϕр.
Известно, что на чертеже с целью изготовления и контроля проставляются значения геометрических параметров в инструментальной системе координат.
Вместе с тем для расчетов углов лезвия инструмента в процессе резания и для учета их изменения после установки инструмента на станке, а также при анализе их изменения вдоль режущей кромки и других задачах используются статические, кинематические, нормальные и рабочие углы, что и решается в теории определения геометрических параметров инструмента.
Анализ приведенных стандартных определений геометрических параметров инструмента показывает, что все плоскости, в которых они рассматриваются и относительно которых ориентированы, определяются направлением скорости главного или результирующего движения.
Инструментальные геометрические параметры ориентированы относительно инструментальной системы координат. Инструментальная система координат представляет собой прямоугольную систему координат с началом в вершине лезвия ориентированную относительно геометрических элементов режущего инструмента, принятых за базу [3].
В инструментальной системе координат направление скорости главного движения резания принимается у токарных и строгальных резцов прямоугольного поперечного сечения перпендикулярно конструкторской установочной базе резца, у долбяжных резцов параллельно базе, у дисковых токарных резцов, осевых инструментов – по касательной к траектории вращательного движения инструмента или заготовки, у протяжек – параллельно конструкторской установочной базе или оси протяжки, у долбяков параллельно оси хвостовика или оси посадочного отверстия долбяка.
Анализ основных положений определения элементов лезвия режущего инструмента показывает, что взаимосвязи между геометрическими параметрами, в различных координатных системах, определяются направлением скорости движения резания главного или результирующего.
Методика определения геометрических параметров режущей части инструмента
Согласно стандарту для определения переднего γ и заднего α углов в рассматриваемой точке режущей кромки необходимо определить положение основной плоскости Рv в рассматриваемой системе координат, перпендикулярной направлению скорости движения резания (главного или ре-
5
ISBN 966-7851-19-2 Надійність інструменту та оптимізація технологічних систем. №14 2003.
зультирующего), положение плоскости резания, касательной к режущей кромке в рассматриваемой точке и перпендикулярной Рv и секущей плоскости Рτ, перпендикулярной линии пересечения основной плоскости резания. Так как углы γ и α определяются в одной из секущих плоскостей (Рτ, Рτи, Рτс, Рτк, Рн, Рс), то они заключены между линиями пересечения секущей плоскости с основной и передней поверхностью (γ), и секущей с плоскостью резания, и задней поверхностью (α).
Учитывая, что плоскости Рn и Рτ в рассматриваемой точке режущей кромки ориентированы относительно основной Рv, а она относительно направления скорости движения резания в этой точке, то при определении углов γ и α, прежде всего, возникает задача определения этого направления скорости.
Эта задача решается для каждого из видов инструмента с учетом формообразующих движений, осуществляемых при резании (главного или результирующего), расположением режущей кромки относительно главного или результатирующего движения резания, формой кромки и расположением исследуемой точки на ней.
Главное движение резания представляет собой прямолинейное поступательное или вращательное движение заготовки или режущего инструмента, происходящее с наибольшей скоростью в процессе резания. Результатирующим движением резания является суммарное движение режущего инструмента относительно заготовки, включающее главное движение резания, движение подачи и касательное движение [3].
Следующим этапом при определении углов γ и α является определение положения касательных плоскостей к передней или задней поверхности в рассматриваемой точке режущей кромки. Их положение соответственно зависит от формы передней и задней поверхностей, расположения режущей кромки относительно направления скорости движения резания, формы режущей кромки и расположения на ней рассматриваемой точки.
Таким образом общая методика определения углов γ и α в той или иной системе координат независимо от вида и конструкции инструмента заключается в следующем:
-определение направления скорости движения резания (главного или результирующего);
-определение положения касательной плоскости к передней или задней поверхностей в рассматриваемой системе координат (соответственно при определении γ и α);
-определение положений плоскостей Рv, Pn, Pτ в рассматриваемой системе координат;
-определение линий пересечения секущей плоскости с плоскостями Рv и Рn в соответствующей системе координат;
6