
Radzevich, S.P. Monograph - 2001
.pdf
480 |
|
|
8. Синтез наивыгоднейшего формообразования поверхностей деталей |
|
|
|||||
|
|
h |
|
|
|
|
h |
|
h |
|
Д |
|
|
h |
П |
Д |
Д |
h |
|||
|
|
|
|
|
|
|
|
|
П |
|
hВ |
|
|
|
|
|
hВ |
h |
hВ |
|
|
|
|
|
|
|
|
|
|
|
|
|
|
|
|
|
|
|
|
П |
|
|
|
K |
|
|
|
|
K |
|
|
|
K |
|
|
|
|
S |
П |
|
S |
|
|
S |
|
|
|
|
|
SВ |
П |
SВ |
|
П |
||
SВ |
|
|
|
|
|
|
|
|
||
S |
В |
S |
П |
|
|
S |
S |
|
S |
S |
|
|
|
|
В |
П |
|
В |
П |
||
1. |
|
|
|
|
2. |
|
|
|
3. |
Рис. 8.22. К способу обработки сложных поверхностей деталей (пат. №2050228 ).
Чтобы достичь максимума производительности формообразования Pф , необходимо, чтобы движение формообразования SВ было
направлено под таким углом |
эфф |
к первому главному сечению C |
поверхности Д , при котором выполняется условие |
Pф |
0 . Что- |
|
|||||
|
1.д |
|
|
||
|
|
|
|
бы найденное из этого уравнения значение угла соответствовало именно наибольшему, а не иному экстремальному значению производительности формообразования Pф , необходимо из всех стационарных значений угла выбрать то, при котором выполняется соотно-
шение 2Pф 0 . При этом безразлично, острым или тупым окажется найденный угол эфф . Направление движения формообразования
2
SВ в рассматриваемом случае составляет некоторый угол с направлением, перпендикулярным направлению измерения наименьшего диаметра dconf(min) индикатрисы конформности Indconf Д / И поверхности детали и исходной инструментальной поверхности.
При обработке сложных поверхностей деталей на многокоординатных станках с ЧПУ в соответствие с рассматриваемым способом при прочих одинаковых условиях достигается наиболее высокая производительность обработки.
Пример 8.14. Эффективность обработки сложных поверхностей деталей на многокоординатных станках с ЧПУ может быть повышена за счет согласования между собой величин подач инструмента вдоль и поперек строк формообразования. Для этого разработан способ1 обработки сложных поверхностей деталей лезвийным инструментом.
Для обработки детали по этому способу инструмент, совершающий главное движение, подводят к заготовке, вводят в контакт с ней и движением формообразования SВ перемещают строками по номинальной поверхности детали. После окончания обработки очередной
строки на поверхности Д осуществляют движение подачи поперек строки формообразования на величину шага SП SП между сосед-
ними строками для осуществления обработки очередной строки на поверхности детали. Необходимая для этого кинематика формообразования воспроизводится на станках, имеющих не менее трех одновременно управляемых от системы ЧПУ координат.
На точность обработки поверхности детали задается допуск h . Результирующая погрешность формообразования h не должна превышать допуск на точность поверхности Д , т.е. всегда должно выполняться соотношение h h .
В результате точечного касания исходной инструментальной поверхности И с номинальной поверхностью Д при обработке детали лезвийным инструментом имеет место дискретное формообразование поверхности Д с результирующей погрешностью h . В некотором приближении величина погрешности h определяется суммой двух составляющих: погрешностью hВ , образованной вдоль, и погрешностью hП , образованной поперек строки формообразования, т.е. (рис. 8.22.1): h hВ hП .
Мгновенное значение производительности Pф формообразования сложной поверхности детали определяется текущими значениями подач SВ и SП и величиной угла между направлениями этих подач: Pф SВ SП sin .
Величина подачи на зуб SВ вдоль строки формообразования расчитывается по формуле (32):
S |
2R |
arccos |
Rд.В Rи.В 2 Rд.В hВ sgn Rд.В 2 Rи2.В |
. |
|
||||
В |
д.В |
|
2 Rд.В Rи.В Rд.В hВ sgn Rд.В |
|
|
|
|
1Пат. №2050228 (Россия). Способ обработки сложных поверхностей деталей./С.П.Радзевич. – Опубл. 20.12.95 в БИ, №35, 1995. - МКИ4 B 23 C 3/16. Заявлено 25.12.1990.
8.4. Синтез локального формообразования поверхностей деталей |
481 |
Величина подачи SП инструмента поперек строки формообразования расчитывается по аналогичной формуле (25):
S |
П |
2R |
|
arccos |
Rд.П Rи.П 2 Rд.П hП sgn Rд.П 2 Rи2.П |
. |
|
||
|
|
|
|||||||
|
|
д.П |
|
|
2 Rд.П Rи.П Rд.П hП sgn Rд.П |
|
|||
|
|
|
|
|
|
|
|
||
Из Pф SВ SП sin следует, что для увеличения производительности формообразования следует увеличивать подачи SВ и SП . |
|||||||||
Увеличение подачи SВ до значения SВ |
(рис. 8.22.2) неизбежно ведет к увеличению составляющей hВ до значения hВ и при задан- |
||||||||
ном допуске h (в соответствие с h hВ hП |
|
|
|
|
|
||||
) к уменьшению hП до hП и, как следствие, к уменьшению SП |
до значения SП . Спра- |
||||||||
ведливо и обратное: увеличение подачи SП |
до значения |
|
|
||||||
SП (рис. 8.22.3) ведет к увеличению составляющей hП |
до hП и при заданном |
||||||||
допуске h к уменьшению hВ до значения hВ |
и, как следствие, к уменьшению SВ до значения SВ . |
|
|||||||
В первом случае величина подачи |
SП |
|
|
|
|
|
|
|
|
на строку формообразования уменьшается до значения SП , а во втором – увеличивается до |
|||||||||
|
формообразованной одной режущей кромкой участка строки формообразования в первом случае |
||||||||
SП . Одновременно с этим длина SВ |
увеличивается до значения SВ , а во втором – уменьшается до значения SВ .
Поскольку увеличение подач должно быть направлено, в первую очередь, на увеличение производительности формообразования, то требуется, во-первых, величины подач SВ и SП согласовать между собой и, во-вторых, согласовать их так, чтобы наилучшим образом
распределить допуск h между составляющими hВ и hП , т.е. чтобы производительность формообразования при этом достигала своего максимального значения (помним, что h hВ hП ).
Чтобы распределить допуск h наилучшим образом, выразим составляющие |
hВ и hП через допуск h на результирующую по- |
|||||||||||||||||||
грешность формообразования h . Получим: |
hП c h |
|
и hВ 1 c h , где c |
– текущеее значение параметра распределения допуска |
||||||||||||||||
на точность формообразования (0 c 1 – безразмерная величина). |
|
|
|
|
|
|
|
|
|
|
||||||||||
Выполнив очевидные подстановки и необходимые преобразования, находим, что производительность формообразования Pф в функ- |
||||||||||||||||||||
ции параметра “с” может быть представлена так: |
|
|
|
|
|
|
|
|
|
|
|
|
|
|
|
|
||||
|
|
|
|
2 |
2 |
|
|
|
|
|
|
|
c |
2 |
2 |
|
|
|
|
|
P |
c 2R R |
|
arccos |
c |
|
h cA1 h A2 |
arccos |
|
h cA5 h A6 |
sin . |
|
|
|
|||||||
|
|
|
2cA3 h A4 |
|
|
|
2cA7 h A8 |
|
|
|
||||||||||
ф |
д.В д.П |
|
|
|
|
|
|
|
|
|
|
|
||||||||
|
|
|
|
|
|
|
|
|
|
|
|
|
|
|||||||
Коэффициенты A1 , A2 , ..., |
A8 зависят от параметров процесса формообразования, но не зависят от текущего значения параметра |
|||||||||||||||||||
распределения допуска на точность формообразования. |
|
|
|
|
|
|
|
|
|
|
|
|
|
|
|
|
||||
Таким образом, мгновенная производительность формообразования |
Pф |
является функцией подач SВ |
и SП ; критические значения |
|||||||||||||||||
этих подач в текущей точке траектории формообразования ограничены величинами составляющих hВ и |
hП допуска |
h , которые в |
||||||||||||||||||
свою очередь могут быть представлены в функции параметра “с” распределения допуска на точность формообразования. |
|
|||||||||||||||||||
Величину подачи на зуб SВ |
согласовывают с подачей SП |
на очередную строку формообразования таким образом, |
чтобы текущее |
|||||||||||||||||
|
|
|
|
|
|
|
P |
c |
|
|
|
|
|
|
|
|
P2 c |
|
||
значение параметра “с” равнялось тому из корней уравнения |
|
ф |
|
|
0 |
, при котором выполняется соотношение |
ф |
0 . Такое со- |
||||||||||||
|
c |
c2 |
||||||||||||||||||
|
|
|
|
|
|
|
|
|
|
|
|
|
|
|
|
|
гласование подач SВ и SП гарантированно приводит к увеличению производительности формообразования сложных поверхностей де-
талей на многокоординатных станках с ЧПУ.
Если ставится задача при неизменной производительности увеличить точность формообразования, это также достигается согласованием между собой величин подач SВ и SП в соответствие с рассматриваемым способом.
Пусть допуск на точность обработки локального участка поверхности некоторой детали с нормальными радиусами кривизнами
Rд.В 100 мм и |
Rд.П 20 мм составляет h 0,01 мм . Обработка производится инструментом, нормальные радиусы кривизны локаль- |
||||||||||
ного участка исходной инструментальной поверхности которого равны Rи.В 10 мм и |
Rи.П 50 мм . В процессе обработки направления |
||||||||||
подач S |
В |
и S |
П |
взаимно |
перпендикулярны |
(т.е. 90 ). Переменные A , |
A , |
..., A |
равны: A 20 , |
A 2800 |
, A 70 , |
|
|
|
|
1 |
2 |
8 |
1 |
2 |
3 |
||
A4 A2 2800 , |
A5 100,01 , |
A6 2202,0001 , |
A7 110 , A8 1400,14 . С учетом этого находим, |
что c 0,65 , т.е. величины подач SВ и |
|||||||
SП должны быть согласованы одна с другой исходя из того, что hВ 1 c h 0,35 h и hП 0,65 h . Эти значения hВ |
и hП ис- |
пользуются для расчета критических величин подач SВ и SП инструмента.
Значение параметра c 0,65 позволяет расчитать соответствующую ему мгновенную производительность формообразования.
Если подачи SВ и SП не согласовывать между собой, то допуск h между его составляющими hВ и hП распределяется произвольно и параметр “с” может принимать любое значение, например, c 0,45 . Для этого значения параметра “с” также можно расчитать мгновенную производительность формообразования. Несложный подсчеты показывают, что в рассматриваемом случае тольно за счет согласования подач SВ и SП в соответствие с c 0,65 (вместо c 0,45 ) производительность обработки увеличивается более, чем на
20% .

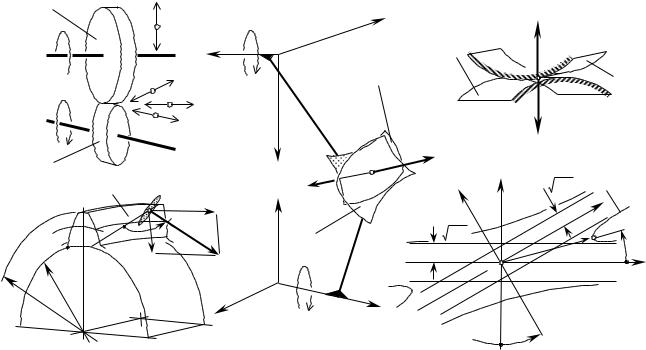

484 |
8. Синтез наивыгоднейшего формообразования поверхностей деталей |
процессе обработки можно как путем изменения конструктивных параметров дискового шевера, так и путем согласования величины и направления движения подачи с частотой вращения детали и инструмента.
Врассматриваемой постановке решением задачи синтеза являются две группы параметров:
-конструктивные параметры наивыгоднейшего инструмента (число зубьев, угол профиля, угол наклона зубьев, ширина зубчатого венца, коэффициента смещения исходного контура и др.);
-кинематические параметры станочного зацеплениния (направление и величина скорости движения подачи, согласованной с часто-
той вращения детали и инструмента).
Для решения задачи синтеза необходима точная и однозначная информация о геометрии обрабатываемой поверхности Д зубьев ци-
линдрического зубчатого колеса (см. выше, Пример 1.3, с. 62-64).
Чтобы решить задачу синтеза локального формообразования, достаточно рассмотреть геометрию касания и кинематику формообразования в окрестности текущей точки К касания поверхности Д зуба колеса и исходной инструментальной поверхности И дискового
шевера (рис. 8.24.2).
Следствием того, что поверхности Д и И являются эвольвентными винтовыми поверхностями, их локальные участки в дифференциальной окрестности точки К представляют собой параболические локальные участки.
Геометрия касания поверхностей Д и И описывается индикатрисой конформности Indconf Д / И поверхностей Д и И (4.83). Из установленных выше свойств индикатрисы конформности Indconf ( Д / И) следует, что в дифференциальной окрестности точки
K направление измерения минимального диаметра действительных ветвей этой характеристической кривой показывает направление наиболее полного прилегания поверхностей Д и И одна к другой. Производительность формообразования рабочих поверхностей зубьев
детали в процессе шевингования достигает своего максимального значения только в случае, когда ширина каждой строки формообразования максимальна. Это возможно, когда в станочном зацеплении “деталь-инструмент” направление относительного перемещения поверх-
ностей Д и И перпендикулярно направлению измерения минимального диаметра действительных ветвей индикатрисы конформности
( Д / И) .
Исходя из того, что при шевинговании направление вектора скорости относительного движения детали и инструмента должно быть ортогональным направлению измерения минимального диаметра dconf(min) 2rconf(min) действительных ветвей индикатрисы конформности Indconf Д / И , можно расчитать наивыгоднейшие значения конструктивных параметров дискового шевера. Для этого необходимо установить относительную ориентацию поверхностей Д и И в точке K их касания, которая определяется углом между прямолинейными образующими (между Uд и Uи линиями) эвольвентных винтовых боковых поверхностей зубьев детали и инструмента. Величина угла относительной локальной ориентации поверхностей Д и И расчитывается по формуле (Палагута В.П., 1987, 1995):
sin |
|
sin sin |
|
. |
|
|
|
||
|
|
|
||
|
|
(1 cos2 sin2 д)(1 cos2 sin2 и) |
|
|
Это уравнение в сжатой форме содержит всю информацию, необходимую для расчета наивыгоднейших значений конструктивных параметров дискового шевера, который следует использовать для обработки заданной детали. Совокупность этих параметров составляет первую группу параметров, получаемых как результат решения задачи синтеза локального формообразования.
После подстановки в уравнение (4.83) индикатрисы конформности Indconf ( Д / И) полученного наивыгоднейшего значения углаэфф относительной локальной ориентации и значений гауссовых коэффициентов Eд , Fд , Gд , Lд , Mд , Nд и Eи , Fи , Gи , Lи , Mи , Nи для эвольвентных винтовых поверхностей Д и И (см. выше, пример 1.3, с. 62-64) в локальной системе координат получим:
r |
|
R2.д |
|
R2.и |
. |
|
|
||||
conf |
|
sin |
sin( ) |
||
|
|
Это уравнение в сжатой форме содержит всю информацию, необходимую для расчета наивыгоднейших значений параметров кинематики формообразования. Совокупность этих параметров составляет вторую группу параметров, получаемых как результат решения задачи синтеза локального формообразования.
На рис. 8.24.5 показана индикатриса конформности Indconf Д / И для случая касания двух эвольвентных винтовых поверхностей Д и И , что имеет место при диагональном зубошевинговании.
Вектор скорости V скольжения зубьев в станочном зацеплении расположен в общей для поверхностей Д и И касательной плоскости, которая совпадает с боковой плоскостью зубьев вспомогательной производящей рейки Tд , а его величина и направление зависят
от угла перекрещивания осей вращения детали инструмента, величины передаточного отношения в станочном зацеплении и от положения текущей точки по высоте зуба детали. Результирующую скорость V скольжения зубьев детали и инструмента в текущей точке К
удобно разложить на две составляющие V V V , одна из которых представляет собой скорость профильного скольжения V , а другая – скорость скольжения V в направлении зубьев колеса. Варьируя параметры процесса формообразования, можно изменять направление скорости скольжения V поверхностей зубьев детали и инструмента в процессе обработки.
8.5. Синтез регионального формообразования поверхностей деталей |
485 |
В процессе формообразования кроме скорости скольжения V в воспроизводимой в станочном зацеплении винтовой зубчатой передаче “деталь-инструмент” на величину и направление вектора скорости резания оказывает влияние вектор скорости подачи Vs , направ-
ленный параллельно плоскости, касательной к начальным цилиндрам зубчатого колеса и дискового шевера, и составляющий некоторый угол с осью вращения зубчатого колеса.
Наивыгоднейшее направление вектора скорости резания Vрез определяется с учетом того, что Vрез V Vs . Этот вектор должен быть перпендикулярным направлению измерения минимальнго диаметра dconf(min) действительных ветвей индикатрисы конформности Indconf ( Д / И) поверхностей Д и И . Исходя из этого устанавливается характер согласования частоты вращения дискового шевера с
величиной и направлением скорости движения подачи стола станка.
Анализ полученных результатов показывает, что несмотря на то, что обе поверхности Д и И выпуклы, направления строк формообразования не совпадают с направлениями линий кривизны на Д .
На основе изложенного разработан алгоритм САПР технологического процесса чистовой обработки цилиндрических зубчатых колес дисковыми обкаточными инструментами (Радзевич С.П., Палагута В.А., 1988).
8.5. Синтез регионального формообразования поверхностей деталей
Совокупность наивыгоднейших направлений движения формообразования определяет наивыгоднейшую траекторию движения инструмента по поверхности детали. Расчет параметров наивыгоденейшей траектории формообразования составляет сущность решения задачи синтеза регионального формообразования.
Аналогично траектории перемещения программируемой точки, параметры траектории формообразования могут быть установлены исходя из выполнения условия: Булево отсечение от заготовки обрабатываемой детали объема, занимаемого последовательными положениями инструмента при отработке станком с ЧПУ управляющей программы, формирует поверхность, отклоняющуюся от номинальной поверхности детали не более, чем на величину допуска на точность обработки.
Как и при решении задачи синтеза локального формообразования, при решении задачи синтеза регионального формообразования обрабатываемый участок сложной поверхности Д детали рассматривается как
неограниченный – при региональном формообразовании влияние “краевого эффекта” на эффективность процесса обработки не учитывается.
8.5.1. Наивыгоднейшие траектории формообразования. Под наивыгоднейшей траекторией формооб-
разования понимается такая траектория, при движении инструмента вдоль которой текущее значение ширины строки формообразования максимально, а формообразованная при этом площадь строки на поверхности детали при прочих одинаковых условиях наибольшая.
Чтобы расчитать параметры наивыгоднейшей траектории формообразования при обработке сложной поверхности детали на многокоординатном станке с ЧПУ, исходим из условия достижения максимальной производительности регионального формообразования. В такой постановке необходимым условием решения задачи синтеза регионального формообразования является поддержание наибольшей ширины строки формообразования в текущей точке К касания поверхности детали и исходной инструментальной поверхности.
Одним из результатов решения задачи синтеза локального формообразования (см. выше, раздел 8.4) является установленое наивыгоднейшее направление движения формообразования и соответствующее ему текущее значение ширины строки формообразования. Для решения этой задачи использована индикатриса кон-
формности Indconf Д / И поверхности Д детали и исходной инструментальной поверхности И применяе-
мого инструмента (4.83).
Текущее значение мгновенной производительности формообразования вдоль строки формообразования переменно. Для увеличения региональной производительности формообразования значение локальной производительности (в текущей точке на поверхности Д детали) должно поддерживаться возможно большим, в
пределе – равном своему экстремальному значению.
Текущее значение ширины строки формообразования максимально, если траектория формообразования в каждой своей точке направлена ортогонально направлению измерения наименьшего диаметра dconf(min) индикатрисы конформности Indconf Д / И .
Из этого следуют принципиально важный вывод: в общем случае задачу синтеза регионального формообразования нельзя рассматривать вне связи с формой и параметрами поверхности И применяемого инструмента. Поэтому для достижения максимума производительности формообразования обработка заданной


8.5. Синтез регионального формообразования поверхностей деталей |
487 |
(U д, Vд) G ), положение касательной плоскости Q , в которой расположен вектор скорости |
Vэфф |
(рис. 8.25), определяется двумя проходящими через точку К пересекающимися прямыми. Одна из них расположена касательно к координатной Uд линии, а другая – касательно к координатной Vд линии. Направле-
ния этих касательных задаются ортами
|
|
|
rд |
|
|
|
|
|
rд |
|
|
|
i |
(K) |
|
U д |
|
и |
j |
(K) |
|
Vд |
|
, |
(8.56) |
|
|
|
|
|
|
|||||||
|
д |
rд |
|
|
|
д |
rд |
|
|
|
||
|
|
|
|
|
|
|
|
|
|
|
||
|
|
|
U д |
|
|
|
|
|
Vд |
|
|
|
которые служат ортами подвижной локальной системы координат xд(K) yд(K) zд(K) с началом в точке К .
В точке К нормаль Nд к поверхности Д определяет направление третьей оси – оси аппликат zд(K) си-
стемы координат xд(K) yд(K) zд(K) .
Нормаль к поверхности ортогональна любой паре проходящих через точку К неколлинеарных касательных прямых, в частности, она ортогональна касательным прямым с ортами (56). Следовательно, орт оси аппликат равен
|
|
|
|
|
|
|
|
|
|
|
|
|
|
|
|
|
|
|
|
|
|
|
|
|
|
|
|
|
|
|
|
rд |
|
|
rд |
|
|
|
(K) |
|
|
|
|
rд |
|
|
(K) |
|
|
|
rд |
|
|
|
(K) |
|
|
|
|
|
|
|
|
|
|
|
|
|
|
|
|
|
|
|
|
|
|
|
|
|
|
|
|
|
|
||||||||||||||||||||||||
|
|
|
|
|
|
|
|
|
|
|
|
|
|
|
|
|
|
|
|
|
|
|
|
|
|
|
|
|
|
|
|
|
|
|
|
|
|
|
|
|
|
|
|
|
|
|
|
|
|
|
|
|
|
|
|
|
|
|
|
|
|
|
|
|
|
|
|
|
|
|
|
|
|
|
|
|
|||||||||||||||||||||||||||||||||
|
|
|
k |
(K) |
n |
(K) |
|
|
Nд |
|
|
|
|
|
Uд |
|
|
Vд |
|
|
|
|
|
|
|
|
|
|
U д |
|
|
|
|
|
|
|
|
Vд |
|
|
|
|
i(K) j |
(K) . |
|
|
|
|
|
|
|
|
|
|
|
|
|
(8.57) |
|||||||||||||||||||||||||||||||||||||||||||||||||||
|
|
|
д |
д |
|
|
|
|
|
|
|
|
|
|
|
|
|
|
|
|
|
|
|
|
|
|
|
|
|
|
|
|
|
|
|
|
|
|
|
|
|
|
|
|
|
|
|
|
|
|
|
|
|
|
|
|
|
|
|
|
|
||||||||||||||||||||||||||||||||||||||||||||||||
|
|
|
|
|
|
|
|
|
|
|
|
|
|
|
|
Nд |
|
|
|
|
|
|
|
rд |
|
|
rд |
|
|
|
|
|
|
|
|
|
|
|
|
rд |
|
|
|
|
|
|
|
|
|
|
|
|
rд |
|
|
|
|
|
|
|
|
д |
|
|
|
д |
|
|
|
|
|
|
|
|
|
|
|
|
|
|
|
|
|
|
|
||||||||||||||||||||||||
|
|
|
|
|
|
|
|
|
|
|
|
|
|
|
|
|
|
|
|
|
|
|
|
|
|
|
|
|
|
|
|
|
|
|
|
|
|
|
|
|
|
|
|
|
|
|
|
|
|
|
|
|
|
|
|
|
|
|
|
|
|
|
|
|
|
|
|
|
|
|
|
|
|
|
|
|
|
|
|
|
|
|
|
|
|
|
|
|
|
||||||||||||||||||||
|
|
|
|
|
|
|
|
|
|
|
|
|
|
|
|
|
|
|
|
|
|
|
|
|
|
|
|
|
|
|
Uд |
|
|
Vд |
|
|
|
|
|
|
|
|
|
|
|
U д |
|
|
|
|
|
|
|
|
|
|
Vд |
|
|
|
|
|
|
|
|
|
|
|
|
|
|
|
|
|
|
|
|
|
|
|
|
|
|
|
|
|
|
|
|
|
|
||||||||||||||||||
Соответствующие производные в (57) записываются так |
|
|
|
|
|
|
|
|
|
|
|
|
|
|
|
|
|
|
|
|
|
|
|
|
|
|
|
|
|
|
|
|
|
|
|
|
|
|
|
|
|
|
|
|
|
|
|
|
|
|
|
||||||||||||||||||||||||||||||||||||||||||||||||||||||||||
|
|
|
r |
д |
|
|
|
X |
д |
|
|
|
|
Y |
|
|
|
|
Z |
д |
|
|
|
T |
|
|
|
|
|
|
|
|
|
|
|
|
|
|
|
|
|
r |
д |
|
|
|
|
|
X |
д |
|
|
|
Y |
|
|
Z |
д |
|
|
|
|
T |
|
|
|
|
|
|
|
|
|
|
|
|
|
|
||||||||||||||||||||||||||||||||
|
|
|
|
|
|
|
|
|
|
|
|
|
|
|
|
|
|
|
|
|
д |
|
|
|
|
|
|
|
|
|
|
1 |
|
|
; |
|
|
|
|
|
|
|
|
|
|
|
|
|
|
|
|
|
|
|
|
|
|
|
|
|
|
|
|
|
|
|
|
д |
|
|
|
|
|
|
|
|
|
1 . |
|
|
|
|
|
|
|
|
|
|
|
|
(8.58) |
||||||||||||||||||
|
|
|
|
|
|
|
|
|
U |
|
|
|
|
|
|
|
|
|
|
|
|
|
U |
|
|
|
|
|
|
|
|
|
|
|
|
|
|
|
|
|
|
|
|
V |
|
|
|
|
|
|
|
|
|
|
V |
|
|
V |
|
|
|
|
|
|
|
|
|
|
|
|
|
|
|||||||||||||||||||||||||||||||||||||
|
|
U |
д |
|
д |
|
|
|
|
U |
д |
|
|
|
|
д |
|
|
|
|
|
|
|
|
|
|
|
|
|
|
|
|
|
|
|
|
|
|
|
|
|
V |
|
|
|
|
|
|
|
|
|
|
|
|
|
|
|
|
|
|
|
|
|
|
|
|
|
|
|
||||||||||||||||||||||||||||||||||||||||
|
|
|
|
|
|
|
|
|
|
|
|
|
|
|
|
|
|
|
|
|
|
|
|
|
|
|
|
|
|
|
|
|
|
|
|
|
|
|
|
|
|
|
|
|
|
|
|
|
|
|
д |
|
|
|
|
|
|
|
д |
|
|
|
|
д |
|
|
|
|
|
д |
|
|
|
|
|
|
|
|
|
|
|
|
|
|
|
|
|
|
|
|
|||||||||||||||||||
С учетом (58) зависимость (57) преобразуется к виду |
|
|
|
|
|
|
|
|
|
|
|
|
|
|
|
|
|
|
|
|
|
|
|
|
|
|
|
|
|
|
|
|
|
|
|
|
|
|
|
|
|
|
|
|
|
|
|
|
|
|
|
|
|
|
|||||||||||||||||||||||||||||||||||||||||||||||||||||||
|
|
Y |
Z |
д |
|
|
|
|
Z |
д |
|
|
Y |
|
|
|
|
|
|
Z |
д |
|
|
|
X |
д |
|
|
|
|
X |
д |
|
|
|
Z |
д |
|
|
|
|
|
|
|
|
X |
д |
|
|
|
Y |
|
|
|
|
|
Y |
|
|
|
X |
д |
|
|
|
|
|
||||||||||||||||||||||||||||||||||||||||||
|
|
|
|
д |
|
|
|
|
|
|
|
|
|
|
|
|
|
|
|
д |
|
i |
с |
|
|
|
|
|
|
|
|
|
|
|
|
|
|
|
|
|
|
|
|
|
j |
с |
|
|
|
|
|
|
|
|
д |
|
|
|
|
|
|
д |
|
|
|
|
k |
с |
|||||||||||||||||||||||||||||||||||||||||
|
|
|
|
|
|
|
|
U |
|
V |
|
U |
|
|
|
|
V |
|
U |
|
|
|
|
|
|
|
U |
|
|
V |
|
|
|
|
|
|
V |
||||||||||||||||||||||||||||||||||||||||||||||||||||||||||||||||||||||||
|
|
U |
д |
V |
|
|
|
|
д |
|
|
|
|
|
|
д |
|
|
|
|
|
|
|
|
д |
|
|
|
|
V |
|
|
|
|
|
|
д |
|
|
|
|
|
|
|
U |
д |
|
|
|
|
|
|
|||||||||||||||||||||||||||||||||||||||||||||||||||||||||
k (K) |
|
|
|
|
|
|
|
д |
|
|
|
|
|
|
|
|
|
|
|
|
д |
|
|
|
|
|
|
|
|
|
|
|
|
|
|
|
д |
|
|
|
|
|
|
|
|
|
|
|
|
|
|
|
д |
|
|
|
|
|
|
|
|
|
|
|
|
|
|
д |
|
|
|
|
|
|
|
|
|
|
|
|
|
д |
|
|
. |
||||||||||||||||||||||||
|
|
|
|
|
|
|
|
|
|
|
|
|
|
|
|
|
|
|
|
|
|
|
|
|
|
|
|
|
|
|
|
|
|
|
|
|
|
|
|
|
|
|
|
|
|
|
|
|
|
|
|
|
|
|
|
|
|
|
|
|
|
|
|
|
|
|
|
|
|
|
|
|
|
|
|
|
|
|
|
|
|
|
|
|
|
|
|
|
|
|
|
|
|
|
|
|
|
|
|
|
|
|
|
|
|
|
|||
д |
|
|
Y |
|
|
|
Z |
|
|
|
|
|
|
Z |
|
|
|
|
|
|
Y |
|
|
2 |
|
|
|
|
Z |
|
|
|
|
X |
|
|
|
|
|
X |
|
|
|
|
|
Z |
|
|
|
2 |
|
|
X |
|
|
|
|
Y |
|
|
|
|
Y |
|
|
X |
|
|
|
|
|||||||||||||||||||||||||||||||||||||||
|
|
|
|
|
|
|
д |
|
|
|
|
д |
|
|
|
|
|
|
|
|
д |
|
|
|
д |
|
|
|
|
д |
|
|
|
д |
|
д |
|
|
|
|
|
|
|
|
д |
|
|
||||||||||||||||||||||||||||||||||||||||||||||||||||||||||||||
|
|
|
|
|
|
|
д |
|
|
|
|
|
|
|
|
|
|
|
|
|
|
|
|
|
д |
|
|
|
|
|
|
|
|
|
|
|
|
|
|
|
|
|
|
|
|
|
|
|
|
|
|
|
|
|
|
|
|
|
|
|
|
|
|
|
|
д |
|
|
|
|
д |
|
|
|
|
|
|
|
|
||||||||||||||||||||||||||||||
|
|
|
|
|
|
|
|
|
|
|
|
|
U |
|
|
|
|
|
|
|
|
|
U |
|
|
|
|
|
|
|
|
|
U |
|
|
|
|
|
|
|
|
|
U |
|
V |
|
|
|
|
|
V |
|
|
||||||||||||||||||||||||||||||||||||||||||||||||||||||||
|
|
|
|
|
U |
д |
|
|
|
V |
|
|
|
|
|
д |
|
|
|
V |
|
|
|
|
|
|
|
д |
|
|
V |
|
|
д |
|
V |
|
|
|
|
|
|
д |
|
|
|
|
|
U |
д |
|
|
|
|
|
||||||||||||||||||||||||||||||||||||||||||||||||||||||
|
|
|
|
|
|
|
|
|
|
|
|
|
|
д |
|
|
|
|
|
|
|
|
|
|
|
|
|
д |
|
|
|
|
|
|
|
|
|
|
|
|
|
|
|
|
д |
|
|
|
|
|
|
|
|
|
|
|
д |
|
|
|
|
|
|
|
|
|
|
|
д |
|
|
|
|
|
|
|
|
|
|
д |
|
|
|
||||||||||||||||||||||||||
В построенной локальной системе координат xд(K) yд(K) zд(K) |
|
|
|
вектор скорости |
Vэфф |
|
может быть пред- |
||||||||||||||||||||||||||||||||||||||||||||||||||||||||||||||||||||||||||||||||||||||||||||||||||||||
ставлен так: |
|
|
|
|
|
|
|
|
|
|
|
|
|
|
|
|
|
|
|
|
|
|
|
|
|
|
|
|
|
|
|
|
|
|
|
|
|
|
|
|
|
|
|
|
|
|
|
|
|
|
|
|
|
|
|
|
|
|
|
|
|
|
|
|
|
|
|
|
|
|
|
|
|
|
|
|
|
|
|
|
|
|
|
|
|
|
|
|
|
|
|
|
|
|
|
|
|
|
|
|
|
|
|
|
|
|
|
||
Vэфф iд(K) |
|
sin эфф jд(K) |
cos эфф |
|
|
|
|
|
|
или так: |
|
|
|
|
Vэфф |
|
|
|
sin эфф |
|
|
|
cos эфф |
|
|
0 |
|
|
|
1 T . |
|
|
|
|
|||||||||||||||||||||||||||||||||||||||||||||||||||||||||||||||||||||||||||
Косинусы углов между ортами i |
(K) |
, |
j(K) |
|
и |
|
k |
|
(K) |
и каждой из осей системы координат X Y Z |
с |
станка с |
|||||||||||||||||||||||||||||||||||||||||||||||||||||||||||||||||||||||||||||||||||||||||||||||||
|
|
|
|
|
|
|
|
|
|
|
|
|
|
|
|
|
|
|
|
|
|
|
|
|
|
|
|
|
|
|
д |
|
|
|
д |
|
|
|
|
|
|
|
|
|
д |
|
|
|
|
|
|
|
|
|
|
|
|
|
|
|
|
|
|
|
|
|
|
|
|
|
|
|
|
|
|
|
|
|
|
|
|
|
|
|
|
|
|
|
|
|
|
|
|
|
|
|
|
с с |
|
|
|
ЧПУ равны коэффициентам при соответствующих ортах:

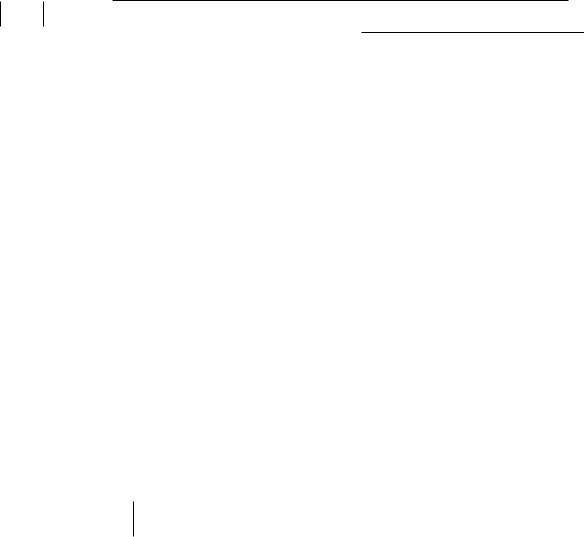
|
|
8.5. Синтез регионального формообразования поверхностей деталей |
|
|
489 |
|||||||||
пр. |
V (c) |
|
dXд(c) |
; |
пр. |
V(c) |
|
dYд(c) |
; |
пр. |
V(c) |
|
dZд(c) |
, |
|
|
|
||||||||||||
|
x эфф |
|
dt |
|
|
y эфф |
|
dt |
|
|
z эфф |
|
dt |
|
|
|
|
|
|
|
|
|
|
|
|
|
поэтому наивыгоднейшая траектория формообразования сложной поверхности Д детали на многокоординатном станке с ЧПУ описывается уравнениями
t |
|
xд U д cos эфф xд Vд sin эфф |
|
|
|||
Xдс 2 |
|
dt ; |
(8.60) |
||||
|
|
|
|
||||
t1 |
|
A |
|
||||
|
|
|
|
|
|
||
t |
yд U д cos эфф yд Vд sin эфф |
|
|
|
|
||
Yдс 2 |
|
dt ; |
(8.61) |
||||
|
|
||||||
t1 |
|
A |
|
||||
|
|
|
|
|
|
||
t |
|
zд U д cos эфф zд Vд sin эфф |
|
|
|
||
Zдс 2 |
|
dt , |
(8.62) |
||||
|
|
||||||
t1 |
|
A |
|
||||
|
|
|
|
|
|
где A V c.эфф dU дdVд ( xд U д cos эфф xд Vд sin эфф) 2 ( yд U д cos эфф yд Vд sin эфф)2
( zд U д cos эфф zд Vд sin эфф)2 .
Для поверхностей Д и И некоторых классов уравнения (60), (61) и (62) могут быть проинтегрированы
в общем виде.
Интегрируя (60), (61) и (62), и исключая из них параметр t , уравнение наивыгоднейшей траектории формообразования сложной поверхности детали представимо в виде
F (X (c) |
, Y(c) |
, Z (c) ) 0; |
|||
|
1 |
|
|
|
|
|
|
|
( X (c) , Y(c) |
, Z (c) ) 0. |
|
F |
2 |
||||
|
|
|
|
|
В криволинейных координатах на поверхности Д уравнения (60), (61) и (62) могут быть преобразованы к виду:
V2 |
|
U д tan эфф dVд . |
(8.63) |
V1 |
|
По уравнению (63) на поверхности детали можно построить семейство линий – семейство наивыгоднейших траекторий формообразования, которые целесообразно использовать в качестве новой системы гауссовых координат на Д . Переход от исходной системы криволинейных координат к новой производится извест-
ными (Радзевич С.П., 1987, 1988; Галимов К.З., Паймушин В.Н., 1985; и др.) методами репараметризации поверхностей.
Если направление движения формообразования постоянно совпадает с одним из главных направлений на поверхности детали, наивыгоднейшие траектории формообразования вырождаются в линии кривизны на Д .
Линии кривизны на поверхности Д детали в общем случае могут быть найдены как результат интегрирования уравнения, которое в обозначениях Гаусса для коэффициентов Eд , Fд , Gд первой Φ1.д и Lд , Mд , Nд второй Φ2.д основных квадратичных форм имеет вид:
EдdU д FдdVд |
FдdU д GдdVд |
|
0 . |
|
|||
LдdU д MдdVд |
MдdU д NдdVд |
|
|