
Radzevich, S.P. Monograph - 2001
.pdf

8.2. Производительность формообразования поверхностей деталей |
441 |
ного тела в работоспособный инструмент (например, шлифовальные круги, многозубые лезвийные инструменты типа шеверов с небольшим шагом расположения режущих кромок и др.)
r р r р Uи; Vи; T , |
(8.9) |
где T – фиксированный момент времени t .
Второй вариант: при дискретном воспроизведении исходной инструментальной поверхности И при превращении ИИТ в работоспособный инструмент (например, фрезы различных конструкций и др.)
|
|
r р r р |
|
|
U р; t , |
|
|
|
|
(8.10) |
|||||||||||
где U р – координата вдоль лезвия применяемого режущего инструмента. |
|||||||||||||||||||||
Векторный элемент площади dF р поверхности резания равен: |
|
||||||||||||||||||||
|
|
|
|
r |
р |
|
|
|
|
r |
р |
|
|
|
|
|
|
|
|||
dF |
р |
|
|
|
|
|
|
|
|
|
dU |
р |
dV |
р |
|||||||
U |
|
|
|
V |
|
|
|||||||||||||||
|
|
|
р |
|
|
|
р |
|
|
|
|
|
|||||||||
|
|
|
|
|
|
|
|
|
|
|
|
|
|
|
|
|
|
||||
для первого (9) и |
|
|
|
|
|
|
|
|
|
|
|
|
|
|
|
|
|
|
|
|
|
|
|
|
|
|
r |
р |
|
|
r |
р |
|
|
|
|
|
||||||
dF |
р |
|
|
|
|
|
|
|
dU |
р |
dt |
|
|||||||||
U |
|
V |
|
|
|
|
|||||||||||||||
|
|
|
|
|
р |
|
р |
|
|
|
|
||||||||||
|
|
|
|
|
|
|
|
|
|
|
|
|
|
|
|
||||||
для второго (10) вариантов. |
|
|
|
|
|
|
|
|
|
|
|
|
|
|
|
|
|
|
|
|
|
Перемещаясь в толще материала заготовки, |
векторный элемент площади dF р охватывает объем, равный |
||||||||||||||||||||
удаляемому в единицу времени объему припуска |
|
dvп ω dF р , где ω – скорость перемещения элемента |
dF р относительно обрабатываемой детали. Скорость ω находится дифференцированием по времени вектора rд , а именно: ω rд . С учетом изложенного находим, что:
Pс t |
|
rд dF р |
|
|
rд |
dF р . |
(8.11) |
||
|
t |
||||||||
|
|
|
|
|
|
|
|
|
|
|
(Fр) |
(Fр) |
|
|
|||||
|
|
|
|
Для случая обработки детали многолезвийным инструментом формула (11) преобразуется к виду:
N* |
rд.i dF р.i |
N* |
|
|
rд dF р.i , |
|
Pс t |
|
|
||||
i 1( |
|
р.i ) |
i 1( |
|
р.i ) |
t |
F |
F |
где N* – число режущих кромок инструмента, одновременно участвующих в резании;
Fр.i – площадь поверхности резания, образуемая i м лезвием инструмента.
8.2.2.2.Производительность формообразования Pф определяется интенсивностью увеличения формообразованной площади номинальной поверхности Дн в процессе обработки детали. В качестве показателя
производительности формообразования принимают среднюю производительность ~ , равную
Pф
~ |
|
F |
д |
|
P |
|
, |
||
|
|
|||
ф |
|
t |
||
|
|
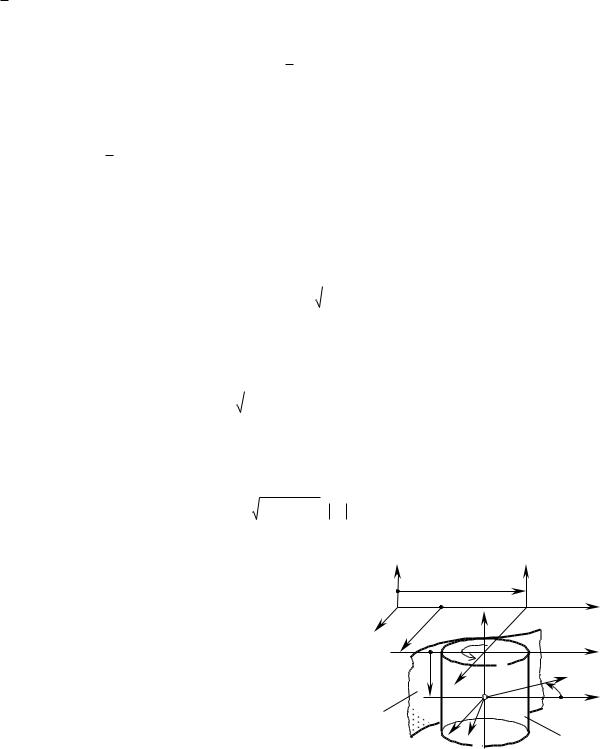

|
|
|
|
|
8.2. Производительность формообразования поверхностей деталей |
|
|
|
|
|
|
|
|
|
443 |
|||||
Rи |
|
– радиус шлифовального круга; |
|
|
|
|
|
|
|
|
|
|
|
|
|
|
|
|||
Zи |
|
– координата вдоль оси шлифовального круга ( 0 Zи Bи ); |
|
|
|
|
|
|
|
|
|
|
|
|
|
|||||
Bи |
|
– ширина шлифовального круга. |
|
|
|
|
|
|
|
|
|
|
|
|
|
|
|
|||
Знак “–” при X и Y в формуле (15) означает, что фактически перемещение совершает система координат Si 1 , а не система Si . |
|
|
||||||||||||||||||
|
|
|
|
|
Формообразующая система контурно-шлифовального станка |
|
|
|
|
|
|
|
Таблица 8.1. |
|||||||
Система |
|
Звено формообразующей |
|
Перемешение относительно предыдущего звена |
||||||||||||||||
|
|
|
|
|
|
|
||||||||||||||
координат |
|
системы |
|
описание |
|
|
|
|
|
|
оператор |
|
|
|
|
|||||
|
|
|
|
|
|
|
|
|
|
|
|
|
|
1 |
0 |
0 |
0 |
|
|
|
X Y Z |
|
Обрабатываемая деталь со |
|
|
|
|
|
|
|
|
|
1 |
0 |
|
|
|
|
|||
|
Исходное звено (условно неподвижно) |
|
|
|
E 0 |
0 |
|
|
|
|||||||||||
|
д |
д д |
столом |
|
|
|
|
|
|
0 |
0 |
1 |
0 |
|
|
|
||||
|
|
|
|
|
|
|
|
|
|
|
|
|
|
|
|
|||||
|
|
|
|
|
|
|
|
|
|
|
|
|
|
0 |
0 |
0 1 |
|
|
|
|
|
|
|
|
|
|
|
|
|
|
|
|
|
|
|
|
|
|
|
|
|
|
|
|
|
|
|
Формообразующее поступательное |
|
|
|
|
|
|
|
1 |
0 |
0 |
0 |
|
||
|
|
|
|
|
|
|
|
|
|
|
|
|
|
|
|
|
|
|
||
X Y Z |
|
Поперечные салазки |
перемещение вдоль оси Y на величину |
Y |
Trans (Y , Y ) 0 |
1 |
0 |
Yи |
|
|||||||||||
|
1 |
1 1 |
|
д |
и |
|
|
|
д |
и |
|
0 |
1 |
0 |
|
|
||||
|
|
|
|
|
|
(перемещение стола относительно станины) |
|
|
|
|
|
|
0 |
|
|
|||||
|
|
|
|
|
|
|
|
|
|
|
|
|
0 |
0 |
|
|
||||
|
|
|
|
|
|
|
|
|
|
|
|
|
|
|
0 |
1 |
|
|||
|
|
|
|
|
|
|
|
|
|
|
|
|
|
|
|
|
|
|
|
|
|
|
|
|
|
|
Формообразующее поступательное |
|
|
|
|
|
|
|
1 |
0 |
0 |
Xи |
|
||
|
|
|
|
|
|
|
|
|
|
|
|
|
|
|
|
|
|
|
||
X |
2 |
Y Z |
2 |
Станина |
перемещение вдоль оси X на величину |
X |
Trans (X |
д |
, X ) 0 |
1 |
0 |
0 |
|
|||||||
|
|
2 |
|
1 |
и |
|
|
|
|
и |
|
0 |
1 |
0 |
|
|||||
|
|
|
|
|
|
(перемещение салазок относительно станины) |
|
|
|
|
|
|
0 |
|
||||||
|
|
|
|
|
|
|
|
|
|
|
|
|
0 |
0 |
|
|
||||
|
|
|
|
|
|
|
|
|
|
|
|
|
|
|
0 |
1 |
||||
|
|
|
|
|
|
|
|
|
|
|
|
|
|
|
|
|
|
|
|
|
|
|
|
|
|
|
|
|
|
|
|
|
|
|
cos |
sin |
0 |
|
0 |
||
X Y Z |
|
|
Формообразующее поворотное движение |
|
Rot (Z |
|
|
|
|
|
|
cos |
0 |
|
|
|||||
|
Шпиндель |
|
2 |
, ) sin |
|
0 |
||||||||||||||
|
3 |
3 |
3 |
вокруг оси Z2 |
на угол |
|
|
|
|
|
|
0 |
0 |
1 |
|
0 |
||||
|
|
|
|
|
|
|
|
|
|
|
|
|
||||||||
|
|
|
|
|
|
|
|
|
|
|
|
|
|
|
0 |
0 |
0 |
|
1 |
|
|
|
|
|
|
|
|
|
|
|
|
|
|
|
|
|
|
|
|
|
|
В функциональной системе шлифовального станка имеются:
–скрытая связь ;
–кинематическая (функциональная) связь Yд Yд Xд ;
–связь огибания rX rZ r 0 .
Таким образом, dYд cot 0 . dXд
Следовательно, уравнение обработанной поверхности Д после выполнения преобразований (15) с учетом (16) и уравнений связи примет вид
r |
д |
R cos |
X |
д |
|
|
R sin Y |
X |
Z |
|
1 T ; |
|
|
arctan Y |
X |
д |
. |
(8.17) |
|||||||||||||
|
|
и |
|
|
|
|
|
|
|
и |
|
д |
|
д |
д |
|
|
|
|
|
|
|
|
|
д |
|
|
|
|||
Необходимые производные вектора r0 (см. (17) и др.) по координатам Xи |
и Yи равны: |
|
|
|
|
|
|
|
|||||||||||||||||||||||
|
|
|
|
|
|
|
|
|
|
|
1 |
|
|
|
|
0 |
|
|
|
|
|
|
3 |
|
|
|
|
||||
|
|
|
rд |
|
|
Rи |
|
|
|
|
rд |
|
|
|
|
|
2 |
2 |
|
|
|
|
|||||||||
|
|
|
1 |
|
|
|
Y |
|
; |
|
|
0 |
; |
|
|
1 Yд |
|
|
, |
|
|
(8.18) |
|||||||||
|
|
|
X |
|
|
|
д |
|
|
|
и |
|
|
|
Z |
|
|
|
|
д |
Y |
|
|
|
|
|
|
||||
|
|
|
и |
|
|
|
|
|
|
0 |
|
|
|
и |
|
|
1 |
|
|
|
|
д |
|
|
|
|
|
|
|
||
|
|
|
|
|
|
|
|
|
|
|
|
|
|
|
|
|
|
|
|
|
|
|
|
|
|
|
|
|
|
||
|
|
|
|
|
|
|
|
|
|
|
|
|
|
|
|
|
|
|
|
|
|
|
|
|
|
|
|
где д – радиус кривизны криволинейного контура Yд Yд Xд , соответствующий моменту времени t .
Вформуле (18) знак “+” берется при обработке вогнутого участка поверхности Д детали, а знак “–” – при обработке выпуклого.
Ввыражении (17) переменная Xд и, следовательно, Yд представляют собой функции времени t . Преобразование (7) в рассматри-
ваемом случае имеет вид: Zд Z и |
Xд SX t , где SX – подача вдоль оси |
Xд . Якобиан этого преобразования равен J SX . |
||||||||||||||||||||||
Подставив найденные зависимости в (14), получим |
|
|
|
|
|
|
|
|
|
|
|
|
|
|
|
|
||||||||
|
Z2 |
|
r |
|
|
r |
|
|
B |
|
R |
|
|
|
|
|
|
|
|
|
R |
|
||
|
|
0 |
|
0 |
|
|
|
|
|
2 |
|
2 |
2 |
|
|
|
||||||||
|
|
|
|
|
|
|
|
|
|
и |
|
|
|
|
|
|
и |
|
||||||
Pф t |
|
Z |
|
X |
SXdZд |
SX |
1 |
|
д |
1 |
Yд |
dZд |
SX SY |
|
1 |
|
д |
Bи , |
||||||
|
Z |
|
|
д |
|
|
д |
|
0 |
|
|
|
|
|
|
|
|
|
|
|
|
|
||
|
1 |
|
|
|
|
|
|
|
|
|
|
|
|
|
|
|
|
|
|
|
|
|
|
|

444 8. Синтез наивыгоднейшего формообразования поверхностей деталей
где SY – подача инструмента вдоль оси Yд .
Таким образом, производительность контурной обработки зависит от радиуса кривизны траектории перемещения оси вращения шлифовального круга. Нетрудно видеть, что множитель при Bи есть скорость перемещения точки шлифовального круга вдоль профиля обра-
батываемой детали. В частном случае, при обработке плоскости, для которой кривизна контура равна нулю, получим Pф BиS , где
S S |
2 |
S |
2 |
. При этом формообразуемая плоскость располагается под некоторым углом к оси X |
д |
, величина которого определяется |
|
|
X |
Y |
|
|
|
||
отношением |
|
SX |
. |
|
|
||
|
|
|
|
SY |
|
|
8.2.2.3. Производительность съема стружки. Для расчета производительности удаления операционного припуска Pс неоходимы векторные уравнения поверхности заготовки и обработанной поверхности детали,
записанные в общей системе координат.
В качестве показателей производительности съема стружки может быть использована средняя производительность съема стружки
~ |
|
V |
|
P |
|
с |
, |
|
|||
с |
|
t |
|
|
|
(здесь Vс – объем стружки, снятый за время t ) и мгновенная производительность съема стружки:
|
P |
dVс |
. |
|
|
||
|
с |
dt |
|
|
|
||
Элемент объема определяется по формуле |
|
|
|
(8.19) |
dvс b dF , |
где dF – векторный элемент площади;
b – вектор толщины припуска, определяемый как разность двух векторов
|
b r з rд , |
гдеr з |
– радиус-вектор текущей точки поверхности З заготовки; |
rд |
– радиус-вектор текущей точки поверхности Д детали (помним, что rд и r з записаны в одних и тех |
|
же криволинейных координатах Uд и Vд ). |
Интегрируя (19) по поверхности S , получаем выражене для объема срезанной стружки
|
|
|
|
r |
д |
|
r |
д |
|
|
|
V |
|
b d F |
b |
|
|
|
dU |
dV . |
|||
|
|
|
|
||||||||
с |
|
|
U |
д |
V |
д д |
|||||
|
(S) |
|
(S) |
|
|
|
д |
|
По аналогии с вычислением площади поверхности по формулам (13), выражаем Uд и Vд через новые
переменные w и t , где t – текущее значение времени обработки поверхности.
Тогда по аналогии с (14) получим выражение для расчета мгновенной производительности съема операционного припуска:
|
|
w |
t |
|
|
|
|
|
|
|
|
|
|
|
t |
2 |
|
r |
д |
|
r |
д |
|
|
|
|
|
P |
|
b |
|
|
|
|
J |
|
dw , |
||||
|
|
|
|
|
|
||||||||
с |
|
|
U |
д |
|
V |
|
д |
|
||||
|
|
|
|
||||||||||
|
|
w |
t |
|
|
|
|
д |
|
|
|
||
|
|
1 |
|
|
|
|
|
|
|
|
|
|
|
где w1 t и w2 t – предельные значения переменной w |
на координатной линии t Const , соответствующее |
границам контура обрабатываемой поверхности Д детали;
8.2. Производительность формообразования поверхностей деталей |
445 |
J д – якобиан преобразования (см. выше, с. 440).
Производительность срезания стружки Pс также может быть расчитана другим способом. Радиус-вектор r рез поверхности резания может быть найден из функции формообразования rи Aи,l rl
|
l |
|
|
|
(здесь |
Aи,l Aij,1,l |
i |
) путем подстановки вместо зависящих от времени t |
переменных q j соответствующих |
|
i 1 |
|
|
|
выражений q j q j t . В результате получим уравнение поверхности резания в одном из двух вариантов:
– при формообразовании исходной инструментальной поверхностью инструмента:
r рез r рез Uи, Vи , T , |
(8.20) |
где Uи и Vи – криволинейные координаты исходной инструментальной поверхности;
T– фиксированный момент времени t .
–при формообразовании отдельной режущей кромкой инструмента:
r рез r рез U р, t , |
(8.21) |
где U р – координата вдоль режущей кромки инструмента.
Векторный элемент площади dS рез поверхности резания Р равен:
– при формообразовании исходной инструментальной поверхностью (20):
|
r рез |
|
r рез |
||
dS рез |
|
|
|
|
dUиdVи ; |
U |
|
V |
|||
|
и |
|
|
||
|
|
|
и |
|
– при формообразовании отдельной режущей кромкой инструмента (21):
|
r рез |
|
r рез |
||
dS рез |
|
|
|
dU рdt . |
|
U р |
t |
||||
|
|
|
|||
|
|
|
|
|
Элемент площади, перемещаясь в толще материала срезаемого припуска, охватывает в единицу времени объем dvс w dS рез , где w – скорость перемещения элемента dS рез относительно обрабатываемой детали.
Она определяется дифференцированием по времени t вектора rд :
l |
r |
д |
|
d q j |
|
w rд |
|
|
|
. |
|
|
|
d t |
|||
j 1 q j |
|
Отсюда производительность срезания стружки равна:
Pс t |
rд d S рез . |
(8.22) |
|
(S) |
|
Для случаев обработки деталей многолезвийным инструментом формула (22) преобразуеся к виду:
Pс t |
N р.к |
rд(n) d S(резn) , |
|
||
|
n 1 |
(S(резn) ) |


|
|
|
|
8.2. Производительность формообразования поверхностей деталей |
447 |
|||||||||
Мгновенное значение ширины строки формообразования измеряется в направлении подачи S П |
и равно |
|||||||||||||
длине дуги SП 2Rд.П . По теореме косинусов (см. рис. 8.4) имеем: |
|
|
|
|
|
|||||||||
|
|
|
|
arccos |
Rд.П Rд.П Rи.П hП Rд.П 0,5 h |
. |
|
|
|
|||||
|
|
|
|
|
|
|||||||||
|
|
|
|
|
|
|
|
Rд.П Rи.П Rд.П hП |
|
|
|
|
|
|
Следовательно |
|
|
|
|
|
|
|
|
|
|
|
|
|
|
|
|
|
|
2R |
|
|
|
Rд.П Rд.П Rи.П hП Rд.П 0,5 hП |
|
|
|
|||
S |
П |
arccos |
. |
(8.23) |
||||||||||
|
|
|||||||||||||
|
|
д.П |
|
|
|
Rд.П Rи.П Rд.П hП |
|
|||||||
|
|
|
|
|
|
|
|
|
||||||
Формула (23) допускает упрощение, вытекающее из того, что SП Rд.П . В этом случае выполняется |
||||||||||||||
соотношение SП AB SП , с учетом которого (см. рис. 8.4) |
|
|
|
|
|
|||||||||
|
|
|
|
|
|
|
|
|
|
|
|
|
||
|
|
|
|
|
|
|
Rд.П Rд.П Rи.П hП Rд.П 0,5 |
|
2 |
|
||||
S |
П |
2R |
1 |
|
hП . |
(8.24) |
||||||||
|
||||||||||||||
|
|
д.П |
|
|
Rд.П Rи.П Rд.П hП |
|
|
|
||||||
|
|
|
|
|
|
|
|
|
|
|
Подача SП может быть также определена по обобщенной формуле, применимой к формообразованию не только выпуклых, но и вогнутых участков поверхности Д :
|
|
|
|
Rд.П Rи.П |
2 |
Rд.П hП sgn Rд.П |
2 |
2 |
|
|
|
2R |
|
|
|
Rи.П |
|
|
|||
S |
П |
arccos |
|
|
, |
(8.25) |
||||
|
|
|
|
|
||||||
|
д.П |
|
2 Rд.П Rи.П Rд.П hП sgn Rд.П |
|
||||||
|
|
|
|
|
в которую подставляются алгебраические значения радиусов кривизны Rд.П и Rи.П , а именно: эти радиусы
кривизны берутся каждый со своим знаком – со знаком “+” для выпуклых и со знаком “–” для вогнутых участков поверхностей Д и И .
Если пренебречь членами второго порядка малости, а именно, величиной hП2 , то зависимость (25) упрощается и может быть записана так:
|
|
|
2 |
|
|
|
|
||
|
2R |
|
Rд.П Rи.П Rи.П hП sgn Rд.П |
|
|
. |
(8.26) |
||
S |
|
arccos |
|
|
|||||
П |
Rд.П Rи.П Rд.П hП sgn Rд.П |
|
|||||||
|
д.П |
|
|
|
|||||
|
|
|
|
|
|
В соответствие с формулой Эйлера
Rд.П |
|
|
|
R1.дR2.д |
|
|
; |
|
(8.27) |
|
|
R |
sin |
2 R |
cos2 |
|
|
||||
|
|
|
|
|
||||||
|
|
|
1.д |
|
2.д |
|
|
|
|
|
Rи.П |
|
|
|
|
R1.иR2.и |
cos2 . |
(8.28) |
|||
R |
sin 2 |
R |
||||||||
|
1.и |
|
|
|
2.и |
|
|
|
|
|
На основании (27) и (28) формула (23) представима в виде:
|
|
2R |
arccos |
Rд.П ( ) Rд.П ( ) Rи.П ( ; ) hП Rд.П ( ) 0,5 hП |
|
|
|
S |
П |
. |
(8.29) |
||||
|
|||||||
|
д.П |
|
Rд.П ( ) Rи.П ( ; ) Rд.П ( ) hП |
|
|||
|
|
|
|
|
В случае обработи сложных поверхностей деталей лезвийным инструментом вдоль каждой строки формообразования образуется волнистость, высота которой ограничивает критическое значение подачи S В


8.3. Производительность формообразования как функция конформности |
449 |
поверхности детали и исходной инструментальной поверхности |
|
Допуск h на точность формообразования распределяется на две части. В пределах его части hП c h находится составляющая hП результирующей погрешности h формообразования (hП hП ), а в пределах части hВ 1 c h – составляющая hВ погрешности h , т.е. hВ hВ . Здесь c – некоторая фиксированная для текущей точки K величина (0 c 1 ).
Вид функции (35) производительности формообразования Pф существенно проще аналитического опи-
сания приведенных затрат на изготовление детали, а использование ее в качестве аналитически описанного критерия эффективности механической обработи обеспечивает получение практически того же результата. Поэтому при выборе критерия эффективности обработки сложных поверхностей деталей на многокоординатных станках с ЧПУ предпочтение следует отдавать производительности формообразования, представленной, например, в виде (35).
Дальнейшее упрощение аналитического описания критерия эффективности обработки возможно путем введения в рассмотрение его геометрических аналогов. Таким аналогом может служить любая функция из установленного (см. выше, гл. 4) класса (4.76) функций конформности, в частности, индикатриса конформно-
сти Indconf ( Д / И) поверхности детали и исходной инструментальной поверхности (4.83). Такая замена фор-
мы аналитического представления критерия эффективности обработки возможна на том основании, что структура функции (35) производительности формообразования соответствует структуре функций конформности. Но, как было установлено (см. выше, гл. 4), все функции конформности имеют экстремумы при одних и тех же значениях входных параметров.
8.3. Производительность формообразования как функция конформности поверхности детали и исходной инструментальной поверхности
Как следует из формулы (1), производительность формообразования Pф прямо зависит от величины подачи SВ инструмента вдоль и SП поперек строки формообразования. Поэтому чем больше значения подач SВ и SП , тем выше производительность формообразования Pф .
Для заданной поверхности детали управлять величинами подач SВ и SП можно за счет изменения по-
ложения и ориентации инструмента относительно детали, а также путем управляемого изменения по программе от системы ЧПУ станком формы и параметров исходной инструментальной поверхности.
Один и тот же локальный участок поверхности детали может быть формообразован локальными участками исходной инструментальной поверхности различной формы. Локальное формообразование возможно в следующих случаях1.
~ |
~ |
|
|
|
|
|
1. Выпуклый локальный участок поверхности Д ( Gд 0 ; |
Mд 0 ): |
~ |
|
|
|
~ |
1.1. выпуклым локальным участком исходной инструментальной поверхности И |
|
0 |
; |
|||
( Gи |
|
Mи 0 ); |
||||
1.2. выпукло-вогнутым локальным участком исходной инструментальной поверхности |
И |
|
~ |
|||
( Gи 0 ). |
||||||
1.3. вогнутым локальным участком исходной инструментальной поверхности И |
~ |
|
|
|
~ |
|
( Gи |
0 , Mи 0 ); |
|||||
2. Выпукло-вогнутый локальный участок поверхности Д |
~ |
|
|
|
|
|
( Gд 0 ): |
~ |
|
|
|
~ |
|
2.1. выпуклым локальным участком исходной инструментальной поверхности И |
|
0 |
; |
|||
( Gи |
|
Mи 0 ); |
||||
2.2. выпукло-вогнутым локальным участком исходной инструментальной поверхности |
И |
|
~ |
|||
( Gи 0 ). |
||||||
~ |
~ |
|
|
|
|
|
3. Вогнутый локальный участок поверхности Д ( Gд 0 , Mд 0 ): |
~ |
|
|
|
~ |
|
3.1. выпуклым локальным участком исходной инструментальной поверхности И |
|
0 ; |
||||
( Gи |
|
Mи 0 ). |
Чем принципиально отличаются один от другого, например, случаи 1.1, 1.2 и 1.3?
Рассмотрим произвольное плоское нормальное сечение поверхности детали (рис. 8.5). В точке K линия сечения поверхности Д имеет некоторый радиус кривизны Rд . Если поверхность Д обрабатывать ин-
1Это необходимые, но не достаточные условия.