
РАМАЗАНОВА К.Р
..pdf91
и Ф12) (табл.3.20). Отметим, что в обессоленной смоле содержание ионов натрия ≤ 6•10-4 % и в почти в 10 раз ниже, чем требования ≤ 5•10-3 % масс для фенольной смолы используемого в производстве технического углерода. Действительно, проведённые испытания опытных образцов обессоленной фенольной смолы с содержанием иона натрия не более 6х10-4 % в ООО «Ивановский завод технического углерода» показали, что обессоленная фенольная смола является высококачественным сырьём для производства технического углерода.
Таблица 3.19 Хромато-масс-спектрометрический анализ дымовых газов при сжигании
обессоленной фенольной смолы
Обнаруженные компоненты |
Брутто формула |
Вероятность содержания |
|
|
вещества в пробе, % |
Диоксин |
C12 H4 CII4O2 |
отсутствие |
Триметилпентан |
C8H18 |
9 |
Метилбензол |
C7H8 |
94 |
Трихлорэтан |
C2H3CI3 |
96 |
Ацеталь |
C6H14O2 |
83 |
Диэтилкарбонат |
C5H10O3 |
43 |
4-метил-2-гексанол |
C7H16O |
50 |
Хлорбензол |
C6H5CI |
96 |
Пара-ксилол |
C8H10 |
97 |
1-метилэтилбензол |
C9H10 |
91 |
Фенилацетилен |
C8H6 |
94 |
Стирол |
C8H8 |
95 |
Тетрахлорэтан |
C2H2CI4 |
97 |
Фенол |
C6H6O |
94 |
Бензофуран |
C8H6O |
96 |
Инден |
C9H8 |
94 |
Дибутилфталат |
C12H14O4 |
97 |
Ацетофенон |
C8H8O |
91 |
Нафталин |
C10H8 |
93 |
1-метилнафталин |
C11H10 |
94 |
2-метилнафталин |
C11H10 |
97 |
Бифенил |
C12H10 |
97 |
Дибензофуран |
C12H8O |
97 |
Системное исследование процесса обессоливания и очистки от механических примесей фенольной смолы позволило разработать эффективную двухступенчатую технологию и установку получения качественной обессоленной смолы [219а], которая по аппаратурному оформлению отличается простотой и высокой производительностью и менее энерго- и материалоёмкая (рис. 3.14), чем известный промышленный процесс [1а]. При этом сам процесс характеризуется двухстадийностью (смешение компонентов и фазовое разделение) с экономией эфира, не требует использования конденсата с получением обессоленной смолы с низким содержанием ионов натрия ≤ 6•10-4 масс.% (без механических примесей) или в 5 раз ниже, чем содержание иона натрия 3•10-3 масс.% в промышленном процессе [1а].
92
Отметим, что разработанные процесс, технология и установка получения повышенного качества обессоленной фенольной смолы с низким содержанием ионов натрия и без механических примесей [210а-213а, 218а-220а] позволяют устранить трудности утилизации фенольной смолы в качестве котельного топлива или переработки в функциональные прекурсоры для получения полимеров, расширить области квалифицированного применения [1а, 70, 71].
Таблица 3.20 Качественные показатели исходной и обессоленной фенольной смолы,
мазута различных марок
|
Фенольная смола |
ТУ 2424-020- |
ГОСТ 10585-75 «Мазут |
|||
|
5757601-98 |
|||||
|
|
|
||||
Показатели |
|
|
флотский» (марки) |
|||
|
|
|||||
|
|
«Смола фе- |
||||
качества |
Исход- |
Обессо- |
|
|
||
нольная» |
|
|
||||
|
ная |
ленная |
|
|
||
|
|
|
|
|||
|
|
|
|
Ф5 |
Ф12 |
|
Внешний вид |
Вязкая жидкость тёмного цвета |
|
|
|||
Ионы натрия, 104, |
133-336 |
≤ 6 |
- |
|
- |
|
масс.% |
|
|||||
|
|
|
|
|
||
Температура вспыш- |
105 |
95 |
≥ 62 |
≥ 80 |
≥ 90 |
|
ки, ºС |
||||||
|
|
|
|
|
||
Вязкость условная, |
7,5 |
4,0 (30ºС) |
≤ 5 (80ºС) |
≤ 5 (50ºС) |
≤ 12 (50ºС) |
|
усл. гр. |
(30ºС) |
|||||
|
|
|
|
|||
Фенол, масс.% |
8 |
7 |
≤ 8 |
- |
- |
|
|
|
|
|
|
|
|
Сера, масс.% |
0,3 |
≤ 0,2 |
- |
≤ 2,0 |
≤ 0,6 |
|
|
|
|
|
|
|
|
Коксуемость, масс.% |
5,0 |
≤ 2,2 |
- |
≤ 6,0 |
||
|
|
|
|
|
|
|
Зольность, масс.% |
0,22 |
≤ 0,05 |
- |
≤ 0,05 |
≤ 0,10 |
|
|
|
|
|
|
|
|
Механические при- |
11,4 |
отс. |
- |
≤ 0,10 |
≤ 0,12 |
|
меси, мас.% |
||||||
|
|
|
|
|
||
Вода, масс.% |
|
отс. |
- |
≤ 0,3 |
||
Теплота сгорания, |
37254 |
40740- |
- |
≥ 41454 |
||
кДж/кг |
42420 |
|||||
|
|
|
|
3.7. Выводы по главе 3
По результатам теоретических, расчётных и экспериментальных данных можно сделать следующие выводы.
1.Катализаторный комплекс на основе хлорида алюминия весьма чувствителен к серосодержащим примесям в углеводородном сырье (бензоле, пропилене и его фракциях) и при производстве кумола скапливается в пяти основных рециклах промышленных потоков, проходящих через алкилатор, отравляющих и осмоляющих катализаторный комплекс. В этом и состоит основная причина дестабилизации производства и понижения качества прекурсора (кумола) поликонденсационных мономеров.
2.Основными критериями стабильности производства и качества прекурсора поликонденсационных мономеров являются содержание серосодержащих примесей
(в пересчёте на общую серу) в углеводородном сырье (смеси бензолов различных марок и сортности) – не более 15•10-5 масс.% и пропилене и его фракции или смесях
93
различных сортов олефина – не более 3 мг/м3 и оптимальная дозировка воды для полного растворения различных марок хлорида алюминия в смеси бензола с ПАБ, что особенно важно при приготовлении активного катализаторного комплекса.
3.Разработанные научно-обоснованные рекомендации по оптимальной дозировке воды при приготовлении катализаторного комплекса на основе различных марок хлорида алюминия и критерий выбора углеводородного сырья (бензол и олефин) внедрены для обеспечения стабильного производства прекурсора поликонденсационных мономеров.
4.Применение смесителя потоков на стадиях разложения и нейтрализации алкилата, а также полное (100 %-ное) извлечение из него кислых примесей адсорбции катионитом и возврат промывной воды регенерации катионита на стадию разложения позволяет:
- повысить эффективность извлечения остаточного катализаторного комплекса
ифенола из потока алкилата; - сэкономить воду на узле разложения;
- исключить образование трудно утилизируемого отхода – «мульмы», затрудняющего фазовое разделение алкилата и водно-щелочного раствора; - повысить качество алкилата и кумола по содержанию фенола.
Данная разработка имеет экологический и экономический эффект. Изготовлена пилотная установка и внедрена для научно-исследовательских целей.
5. Исследован процесс очистки от механически и органических примесей и переработки алюмохлорида – отхода кумольного производства поликонденсационных мономеров, подобраны оптимальные регулируемые условия получения функциональных добавок различного назначения в полимерные композиты - гексагидрата, полиоксихлоридов и гидроксида и оксида алюминия. Установлено, что, регулируя последовательно процесс отгона солянокислого конденсата из очищенного алюмохлорида при «деликатных» условиях пониженного остаточного давления от - 0,2 до -0,9 кгс/см2 и Т = 72-115ºС, а также последовательно при атмосферном давлении в интервале температур 160°С < Т < 200 и 550ºС можно получать ряд важных различного назначения функциональных добавок в полимерные композиты – гексагидрат хлорида алюминия, полиоксихлориды алюминия, гидроксид алюминия и оксид алюминия. При этом выделенная органическая составляющая, хотя и в небольшом количестве, может возвращаться в производство прекурсора (кумола), а нетоксичный 2-5%-ный раствор хлорида натрия – отводиться на очистные сооружения.
6.Учитывая, что из 2-4 т алюмохлорида с общей стоимостью 200-400 руб./т можно получить 1 тонну ПОХА и особую коммерческую актуальность представляет переработка алюмохлорида в новый импорт замещающий флокулянт ПОХА.
7.Сравнение трёх экспериментально проверенных вариантов термического разложения ГПК высокотоксичного щелочного стока (табл. 3.10, А, Б, В) показывает, что наиболее предпочтительным по эффективности и капитальным вложениям для реализации в промышленном масштабе является вариант А – без насадки. Оптимальным технологическим режимом разложения ГПК токсичного щелочного стока
является: Т = 90-95ºС, время пребывания стока в реакторе 2,5-5 ч и подача щелочного стока со скоростью 0,6 м3 /ч при максимальном объёме промышленного реактора 3 м3. Результаты биотестирования очищенного стока показывают, что предлагаемые процессы и технология термического разложения ГПК щелочного стока производства ГПК приводят к снижению токсического воздействия стока на микрофлору
94
очистных сооружений. Разработанные процесс и технология очистки высокотоксичного стока от ГПК кумольного производства поликонденсационных мономеров направлены на охрану водного бассейна с положительным экологическим эффектом. Изготовленная пилотная установка внедрена для научно-исследовательских целей.
8. Для повышения качества фенола и снижения негативного влияния его примесей на синтез, физико-химические и эксплуатационные свойства поликонденсационных полимеров создана опытная установка испытания новых механически прочных, термостойких гетерогенных катализаторов очистки фенола от органических примесей, и установлены диапазоны изменения технологических параметров в процессе их эксплуатации. Установлено, что при Т = 100-132°С очистки сырца фенола от органических микропримесей происходит механическое разрушение гранул катионитов КУ-2-8чс и КУ-23-12/100 и по уменьшению степени эффективной очистки сырца фенола от органических микропримесей испытанные гетерогенные катализаторы можно расположить в ряд: Леватит К 2341 ≥ КУ-2-8чс> Амберлист 36 WET>КУ-23-12/100> ЦСК. В этом ряду гетерогенных катализаторов с увеличением температуры происходит интенсивное образование 2-МБФ, загрязняющего товарный фенол. На основании результатов испытания гетерогенных катализаторов на опытной установке показано, что наиболее подходящим для очистки сырца поликонденсационного мономера (фенол) от органических микропримесей в «мягком» температурном режиме Т = 55-100°С в промышленных условиях является макропористый катионит Леватит К 2341. Опытная установка и разработанная инструкция для аппаратчика по его обслуживанию внедрены в производство поликонденсационных мономеров для исследовательских целей.
9. Исследован процесс обессоливания и очистки от механических примесей фенольной смолы – основного отхода производства фенола и ацетона по кумольной технологии и подобраны оптимальные условия (температура, соотношения компонентов, кратность рецикла отработанного водного слоя, температурный режим регенерации и рецикла эфира). Разработаны эффективная технология и установка обессоливания до содержания ионов натрия 6•10-4 масс.% и полной очистки от механических примесей фенольной смолы, которая позволяет устранить трудности утилизации и переработки, расширить область рационального её использования. Показано, что полученные опытные образцы обессоленной смолы являются высококачественным сырьём для получения технического углерода – наполнителя полимеров. Сравнением установлено, что полученные образцы обессоленной смолы являются высококалорийным котельным топливом и при сжигании не образуют диоксина, по техническим показателям находятся на уровне высококачественных сортов «Мазута флотского» марки Ф5 и Ф12 по ГОСТ 10585-75. Изготовлена и запатентована конструкция смесителя промышленных потоков и пилотная установка и внедрена для исследовательских целей.
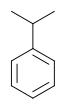
95
Глава 4. ФИЗИКО-ХИМИЧЕСКИЕ И ТЕХНОЛОГИЧЕСКИЕ ОСНОВЫ
БЕЗОТХОДНОГО КУМОЛЬНОГО СИНТЕЗА КУМОЛА, ФЕНОЛА И АЦЕТОНА, α – МЕТИЛСТИРОЛА КАТАЛИТИЧЕСКОЙ
ДИСТИЛЛЯЦИИ НА ГЕТЕРОГЕННЫХ КАТАЛИЗАТОРАХ
На основных стадиях кумольного процесса использование низкоселективных и коррозионно-активных гомогенных катализаторов (каталитический комплекс хлорида алюминия и серная кислота) приводит к образованию множества побочных продуктов, неликвидных и трудно утилизируемых отходов, загрязнённых примесями, экологически опасными сточными водами и усиленной коррозией оборудования, нестабильному качеству целевых продуктов, извлекаемых из многокомпонентных си-
стем [1а, 27-33, 36, 74-77].
Множество рециклов побочных продуктов, их нагрев, охлаждение и транспортировка существенно усложняют аппаратурное оформление кумольного процесса, повышая энергоёмкость в себестоимости фенола и ацетона на более чем 30%, хотя реакции алкилирования идут с выделением тепла более 900 кДж на кг превращённого бензола и разложения ГПК более 2000 кДж на кг превращённого ГПК [1а, 32, 33].
Поэтому разработка безотходного кумольного процесса на активных и селективных гетерогенных катализаторах стадии синтеза кумола и фенола и ацетона с использованием энергетического потенциала экзотермических реакций алкилирования и разложения ГПК является актуальной задачей.
4.1. Моделирование каталитического алкилатора синтеза кумола
Кумол (изопропилбензол) –
C6H5CH (CH3)2 |
(4.1) |
бесцветная жидкость с приятным запахом; Тпл. = -96,03°С, Ткип. = 152,39оС, плотность 0,8618 г/см3 (20°С), показатель преломления nD20 = 1,4913 К; хорошо растворяется в органических растворителях, в воде – плохо; образует взрывоопасные паровоздушные смеси (Твсn. = 38°С); при попадании внутрь вызывает острые и хронические поражения кроветворных органов.
Кумол является промежуточным продуктом при получении фенола и ацетона одним из промышленных способов. Процесс известен под названием реакция «Удриса-Сергеева», т.е. окисление изопропилбензола кислородом воздуха в кумил гидропероксид с последующим его разложением серной кислотой
C6H5CH(CH3)2 + O2 → C6H5С(CH3)2OOH → C6H5OH + (CH3)2CO |
(4.2) |
96
Применяют изопропилбензол для производства главным образом фенола и ацетона (через кумилгидропероксид) и альфа-метилстирола, а также как добавку к авиационным бензинам, повышающую октановое число.
На всех фенольных заводах России [1а, 32-36] при синтезе кумола используют коррозионно-активный гомогенный катализаторный комплекс на основе хлорида алюминия, что приводит к образованию побочных продуктов, трудно утилизируемых отходов, сточных вод, нестабильному качеству кумола, высоким значениям расходных коэффициентов сырья на 1 т кумола.
Альтернативой гомогенному катализатору на основе хлорида алюминия получения кумола с точки зрения активности и селективности, экологической безопасности, лёгкости разделения продуктов реакции и простоты регенерации являются гетерогенные катализаторы – модифицированные и синтетические цеолиты [1а]. Принципиальная возможность использования гетерогенных катализаторов – различные алюмосиликаты и широкий спектр модифицированных и синтетических цеолитов типа Y, β, МСМ-22 и др., имеющих промышленное значение, доказана в промышленных условиях за рубежом [1а, 103-135].
В настоящее время геометрические параметры экспериментальных и промышленных реакторов вообще, в частности, алкилатора или трансалкилатора является предметом «ноу-хау» производителя. Поэтому для предварительной оценки геометрических размеров экспериментальной установки (высота слоя гетерогенного катализатора h и диаметр алкилатора) и определения оптимальных условий алкилирования бензола пропиленом необходимо разработать математическую модель каталитического алкилатора получения кумола.
Данный раздел посвящён моделированию каталитического алкилатора синтеза кумола для оптимизации режима проведения реакции алкилирования бензола пропиленом в зависимости от его геометрического размера [221а].
Химический состав и физико-химические показатели [1а] использованного для моделирования синтеза кумола на гетерогенном катализаторе приведены в табл. 2.3 раздела 2.2.
Кинетическая модель процесса синтеза кумола. Кинетика реакции гетероген-
ного каталитического алкилирования бензола пропиленом описывается последовательностью трёх стадий [1а,221а]
С6Н6 + С3Н6 → С6Н5СН(СН3)2 (при k1), |
(4.3) |
С6Н5СН(СН3)2 + С3Н6 → С6Н4 [СН(СН3)2]2 (при k2), |
(4.4) |
С6Н4 [СН(СН3)2]2 + С6Н6 ↔ 2С6Н5СН(СН3)2, (при k3), |
(4.5) |
где k1, k2, k3 – константы скоростей.
Пусть С1, С2, С3, С4 – концентрации бензола С6Н6, пропилена С3Н6, кумола С6Н5СН(СН3)2, диизопропилбензола С6Н4 [СН(СН3)2]2 или ПАБ, соответственно в молях на 100 г смеси. Тогда получаем систему из четырёх дифференциальных уравнений, описывающих скорости протекания реакции (4.3)-(4.5):
k1С1С2 = dC3/dτ, |
(4.1) |
k2С2С3 = dC4/dτ, |
(4.2) |
k3С1С4 = 2dC3/dτ, |
(4.3) |
k4С32 = -2dC3/dτ, |
(4.4) |
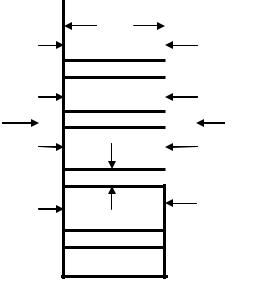
97
где: τ – время алкилирования; k4 – константа скорости.
Интегрируя (4.1) и (4.2) при постоянных концентрациях бензола и пропилена имеем:
С3 = k1С1С2 τ , |
(4.5) |
С4 = 0,5k1k2С1С2 τ2, |
(4.6) |
линейный и квадратичный законы нарастания концентраций продуктов во времени до достижения стационарного состояния. Складывая (4.3) и (4.4) в квазистационарном приближении, получаем:
k3С1С4 = k4С32 |
(4.7) |
или, после подстановки С3 и С4 из (4.5) и (4.6):
k2/k1 = 2k4/k3. |
(4.8) |
Если k1º, k2º, k3º, k4º - аррениусовские предэкспоненты и А1, А2, А3, А4 – энергии активации реакций (4.3)-(4.5), то условие стационарности процесса алкилирования приобретает вид:
k2º/k1º = 2(k4º/k3º)exp(A2 + A3 - A1 - A4). |
(4.9) |
При характерных k1º = 5,45∙109, k2º = 2,63∙1010, k3º = 3,80∙1010, k4º = 5,83∙1012,
А1=51 кДж/моль, А2=61,7 кДж/моль, А3=66 кДж/моль, А4=93 кДж/моль, Т=473К [1а] левая и правая части уравнения (4.9) совпадают, что свидетельствует о его выполнимости в реальных условиях.
Схема четырёхслойного каталитического алкилатора получения кумола приведена на рис. 4.1.
|
|
|
|
|
|
|
|
|
|
|
|
|
|
|
|
|
|
|
2R0 |
|
|
|
|
|
|
||
|
|
|
|
|
|
|
|
|
|
|
|
|
|
|
|
|
|
|
|
|
|
|
|
|
|
|
|
|
|
|
|
|
|
1 |
|
|
|
||||
|
|
|
|
|
|
|
|
|
|
|
|
|
Рис. 4.1. Модель алкила- |
ПРОПИЛЕН |
|
|
|
|
|
|
|
|
2 |
|
БЕНЗОЛ |
||
|
|
|
|
|
|
тора для синтеза кумола: |
|||||||
|
|
|
|
|
|
|
|
|
|
|
|
|
|
|
|
|
|
|
|
|
|
|
|
|
|
|
1-4 – слои катализатора, |
|
|
|
|
|
|
|
|
|
|
|
|
|
где h – высота слоя ката- |
|
|
|
|
|
|
3 |
|
|
лизатора, R0 – радиус ал- |
||||
|
|
|
|
|
|
|
|
|
|
|
|
|
|
|
|
|
|
|
|
h |
|
|
|
|
|
|
килатора |
|
|
|
|
|
|
|
|
|
|
|
|
||
|
|
|
|
|
|
|
|
|
|
|
|
|
|
|
|
|
|
|
|
|
|
|
|
|
|||
|
|
|
|
|
|
|
|
|
|
4 |
|
|
|
АЛКИЛАТ
Пусть С11, С12, С13, С14 – концентрации бензола на j = 1, 2, 3, 4 слоях цилиндрического алкилатора (рис. 4.1) и С2 – концентрация пропилена в реакционной мас-
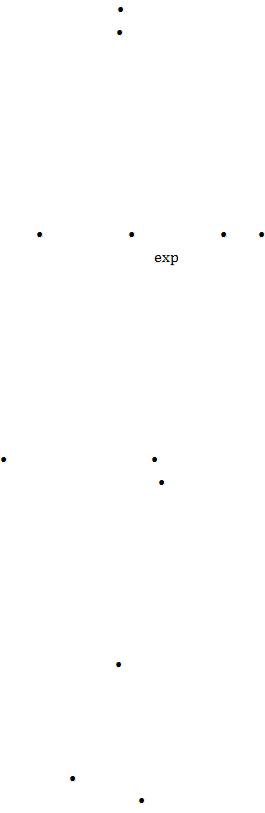
98
се, которую можно принять как постоянную. Тогда, на основании вышеизложенного, можно записать следующие выражения для концентраций кумола и ПАБ для j – катализаторного слоя:
С3j = k1ºС1jС2 |
exp[-А1/RT1]τ + С3j-1, |
(4.10) |
С4j = 0,5k1ºk2ºС1jС22 |
exp[(-А1+А2)/RT1] τ2 + С4j-1, |
(4.11) |
где при j=1, С30 = 0, С40 = 0 или до первого катализаторного слоя кумол и ПАБ не образуются.
Выход кумола α < 1 можно рассчитать по соотношению:
α = С34•(С14+С34+С44) -1, |
(4.12) |
где пренебрегаем концентрацией бензольных примесей.
После подстановки С3j и С4j из (4.10) и (4.11) в (4.12) получаем для j = 1, 2, 3, 4:
α = k1ºС2 τ ΣС1j exp[-А1/RTj] (С14 |
+ k1ºС2 τ ΣС1j |
exp[-А1/RTj] + |
(4.13) |
|
+ 0,5k1º k2ºС22 τ2 Σ С1j• |
(-А1 + А2)/RTj])-1. |
|||
|
Пусть h – толщина или высота слоя катализатора (рис. 4.1) , а Dэф. – эффективный коэффициент диффузии алкилата по его порам, тогда время просачивания алкилата через слой катализатора может быть оценено как:
τ0 = h2/π Dэф. |
(4.14) |
Полагая, что время контакта алкилата со слоем катализатора τ =4τ0 при Т1 = Т2 = Т3 = Т4 = ₸ из (4.13) получаем:
α=[1 + πDэф exp[-А1/R₸]/4h2k1ºС2 (С11/С14 + С12/С14 + С13/С14 |
+1) + |
+ (2 k2ºС2h2/ πDэф) exp[-А2/R₸]]-1. |
(4.15) |
|
В качестве характерных концентрационных отношений |
можно |
выбрать |
С11/С14=1,64; С12/С14=1,42; С13/С14=1,20 [1а], тогда из (4.15) имеем: |
|
|
α={1 + πDэфexp[-А1/R₸] / 21h2k1ºС2 + (2k2ºh2С2 / πDэф)exp[-А2/R₸]}-1. |
(4.16) |
Концентрация пропилена С2 в алкилате связана с его давлением в газовой фазе P соотношением Генри [1а]:
С2=krº P•exp[-Qk/R₸], |
(4.17) |
где krº - константа Генри, равная С2/P при бесконечно большой температуре и Qk=18,41 кДж/моль – теплота конденсации пропилена [1а].
Подставляя С2 из (4.17) в (4.16), получаем:
α={1+πDэф |
exp[(-А1 |
+ Qk)/R₸] / 21k1ºkrºh2P + |
(4.18) |
|
+ (2k2ºkrºh2P / πDэф) exp[(-А2 + Qk)/R₸]}-1. |
||||
|
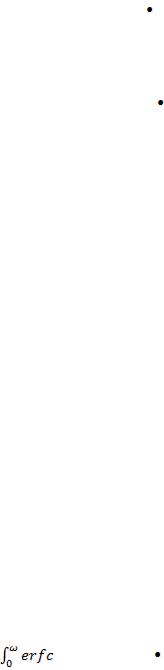
99
Вычислив производную ∂α-1/∂h2 и приравняв к нулю полученное выражение, находим толщину слоя катализатора hmax., отвечающую максимальному выходу кумола α0max. по соотношению:
h2max=P-1πDэф(42k1º2k2ºkrº)-0,5 exp[(А1 + А2 + 2Qk)/ R₸]. |
(4.19) |
Подставляя (4.19) в (4.18), имеем выражение, согласно которому α0max. зависит только от соотношения констант и температуры:
α0max={1+(42k2º/441k1ºkrº)0,5 exp[(-А2 |
+ Qk)/R₸] + |
(4.20) |
|
+ (2k2ºkrº/21k1º)0,5•exp[(А1 + Qk)/R₸]}-1 . |
|||
|
Целесообразно выполнить прямой теоретический расчёт средней температуры алкилата. Для этого предположим, что толщина h каждого из четырёх слоёв катализатора (рис. 4.1) много меньше его диаметра 2R0, слой катализатора можно считать термически тонким и пренебречь распределением температуры t, отсчитанной от температуры алкилата за пределами слоя T0. Пусть также λ, ɑ и ε – соответственно коэффициенты теплопроводности, температуропроводности и объёмной пористости слоя катализатора. При этом на границах идёт теплообмен с алкилатом по закону Ньютона-Рихмана [1а, 221а] при коэффициенте теплообмена γ. Выберем цилиндрическую систему координат O, r, z, φ и поместим её в начало координат в центре слоя катализатора и будем считать, что в порах слоя работают энтальпийные химические источники с равномерной тепловой интенсивностью q. После введения безразмерных переменных: Φ= λt/(qh) – безразмерной температуры, β2 = 2γh/λ – безразмерного коэффициента теплообмена, η = r/h – безразмерного радиуса, ω= ɑτ/ h2 – безразмерного времени и ξ = q/q0 – безразмерной интенсивности источника (q0 – характерный масштаб интенсивности химического тепловыделения) нагрев слоя катализатора может быть описан дифференциальным уравнением [1а, 221а]:
∂Φ/∂ω = ∂2Φ/∂η2 + η-1∂Φ/∂η - β2Φ+f(ω)ξ |
(4.21) |
с начальным условием Φ(η,0) = 0 и граничным условием Φ(η, ω) = 0. Здесь f(ω) – функция Хэвисайда, описывающая работу источника, которая f(ω) = 0 при ω = 0 и f(ω) = 1 при ω > 0.
Приближенным решением (4.21) является функция [1а, 74а]:
Φ≈ - 0,5ξ(η0/η)-0,5 |
[0,5(η0-η) ω-0,5] exp(-β2ω)dω+ ξ(1- exp(-β2ω)) / β2, |
(4.22) |
где =1-erf(x), erf(x)=2π-0,5
(-y2)dy – функция ошибок [1а, 221а].
Интеграл в (4.22) не берётся в аналитическом виде, поэтому решение мы можем найти только в стационарном режиме нагрева при ω →
Φ ≈ ξ[1-0,5(η0/η)0,5•exp[-β(η-η0)]] / β2. |
(4.23) |
Возвращаясь к размерным переменным, имеем:
T = q{1-0,5(R0/r)0,5•exp[-(2γ/λh)0,5(R0-r)]} / 2γ |
(4.24) |
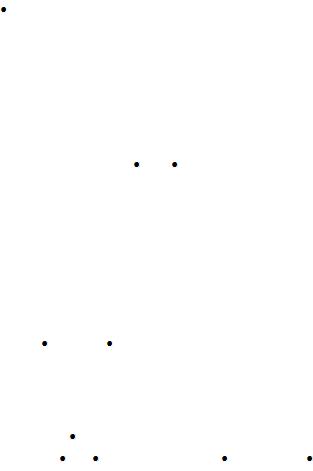
100
и при r ≈ R – среднерадиальная температура нагрева слоя катализатора составит:
tср = q[1- (λh/2γ)0,5/2R0)] / 2γ. |
(4.25) |
Интенсивность теплового источника можно найти по уравнению:
q = (εDэф/h) [Q1(ρк/Мк) – Qисп(ρб/Мб) + Q2(ρпаб/Мпаб) + Q3(ρк/Мк)], |
(4.26) |
где Мб, Мк, Мпаб и ρб, ρк, ρпаб – молекулярные массы и плотности бензола, кумола и диизопропилбензола или ПАБ, соответственно; Qисп-теплота испарения бензола, а Q1, Q2, Q3 – теплоты или тепловые эффекты реакции (4.3)-(4.5).
При ламинарном движении алкилата коэффициент теплообмена определяется из известного критериального уравнения [1а]:
Nu = 0,66 Re0,5 Pr алк, |
(4.27) |
где Nu = γR0 / λалк – критерий Нуссельта; Re = πDэфR0/(hνалк) – критерий Рейнольдса; Pr алк = νалк / ɑалк – критерий Прантдля, λалк, ɑалк, νалк – коэффициенты теплопроводности, температуропроводности, кинематической вязкости алкилата за пределами слоя катализатора.
Это приводит к следующему выражению для неизвестного коэффициента теплообмена:
γ = 0,66 ( λалк/R0) (πDэф R0/hνалк)0,5•( Pr алк)0,33. |
(4.28) |
Подставляя величины γ из (4.28) и q из (4.26) в (4.25), получаем уравнение для расчёта средней абсолютной температуры:
₸ = Т0 + 0,76εDэф. R0 [Q1(ρк/Мк) – Qисп(ρб/Мб) + Q2(ρпаб/Мпаб) + |
|
+ Q3(ρк/Мк)] λалк (πDэф R0 / hνалк)0,5 ( Pr алк)0,33]-1 |
(4.29) |
•{1-0,5[0,76λh/λалк•(πDэфR0/hνалк)0,5•(Pr алк)0,33]0,5}. |
|
Из соотношения (4.29) видно, что ₸ зависит сложным образом от таких конструктивных параметров алкилатора, как его радиус R0 и высота слоя катализатора h. По формуле (4.20) находим значения для α0max при различных h и R0, чтобы предсказать поведение алкилатора на начальных стадиях рабочего цикла.
Более детальные исследования требуют учёта «старения» и дезактивации слоя катализатора во время его эксплуатации. С этой целью можно предполагать, что дезактивация определяется транспортом диизопропилбензола или ПАБ в поры слоя катализатора [1а, 221а] с эффективным коэффициентом диффузии Dэфпаб., а также константой скорости дезактивации kдез. с температурными аррениусовскими зависимостями:
Dэфпаб. = D0паб.exp(-Ad/R₸), |
(4.30) |
kдез. = k0дез. exp(-Aдез/R₸), |
(4.31) |
где D0паб., k0дез. и Ad, Aдез. – аррениусовские предэкспоненты и энергии активации процессов транспорта и химического взаимодействия ПАБ с катализатором.