
РАМАЗАНОВА К.Р
..pdf
101
В этом случае средний за время рабочего цикла выход кумола может быть оценён по соотношению:
αср= α0max[1-h-1(πD0паб. / k0дез.)0,5 exp(- A/ R₸)], |
(4.32) |
где A = Aдез. - Ad.
Очевидно, что численное моделирование алкилатора следует начинать с многоступенчатого расчёта рабочих температур. Тепловые эффекты реакции (4.3)-(4.5) рассчитывали по закону Гесса [1а, 221а]. При энтальпиях образования соответствен-
но бензола, пропилена, кумола и диизопропилбензола или ПАБ, равных |
H0б = -82,98 |
кДж/моль, ΔH0п = -20,42 кДж/моль, ΔH0к = - 41,3 кДж/моль и ΔH0паб = -29,6 кДж/моль |
|
[1а,74а], тепловые эффекты реакции (4.1)-(4.2) составляют: Q1= ΔH0к - |
H0б - ΔH0п = |
62,1 кДж/моль; Q2 = ΔH0паб - ΔH0к - ΔH0п = 32,12 кДж/моль; Q3 = 2 ΔH0к - H0б -
ΔH0паб = 29,98 кДж/моль. С учётом плотности жидких фаз при ρб = 0,88∙103 кг/м3, ρк = 0,86∙103 кг/м3, ρпаб = 0,87∙103 кг/м3, молекулярных масс Мб = 78∙10-3 кг/моль, Мк =
120∙10-3 кг/моль, Мпаб = 162∙10-3 кг/моль и теплоты испарения бензола Qисп= 30,77 кДж/моль получается следующая удельная энергия выделения тепла в объёме слоя катализатора:
Q1(ρк/Мк) – Qисп.(ρб/Мб) + Q2(ρпаб./Мпаб.) + Q3(ρк/Мк) = 4,85∙108 Дж/м3. |
(4.33) |
Для ε = 0,76 (табл. 2.11), Dэф. = 5∙10-8 м2/с [1а,74а] и (4.33) имеем рабочую фор-
мулу вычисления интенсивности тепловыделения в слое катализатора, получаемую на основании соотношения (4.26):
q = 18,43/h [Вт/м2]. |
(4.34) |
Если принять, что при средней температуре реактора 160ºС теплофизические параметры алкилата примерно соответствуют таковым для воды на линии насыще-
ния, т.е. λалк. = 0,681 Вт/(м∙К), νалк. = 0,191∙10-6 м2/с, Pr алк. = 1,1 [1а, 221а], то для вы-
шеупомянутого Dэф.=5∙10-8 м2/с на основании соотношения (4.31) получаем следующую рабочую формулу для расчёта коэффициента теплообмена:
γ = 0,42(hR0)-0,5 [Вт/(м2/К)]. |
(4.35) |
Подставляя величины q и γ из соотношений (4.34) и (4.35) в соотношение (4.25) при λ = 0,582 Вт/(м•К) [1а, 221а], находим рабочую формулу для расчёта средней температуры перегрева слоя катализатора относительно температуры алкилата за его пределами:
Тср.= 21,92(R0 /h)0,5[1-0,83(h3/R0)0,25]. |
(4.36) |
Из (4.36) следует, что величина Тср. увеличивается с радиусом алкилатора R0 и уменьшается с толщиной слоя катализатора h. Действительно, расчёты показывают, что наибольшая температура перегрева слоя катализатора относительно алкилата Тср = 81о относится к самому тонкому слою катализатора с h = 0,1 м и максимальному из рассмотренных в нашей работе радиусу алкилатора R0 = 1,5 м.
При вышеупомянутых значениях k1º, k2º, А1, А2, Qк полученная на основании соотношения (4.20) рабочая формула для вычисления выходов кумола в начальный
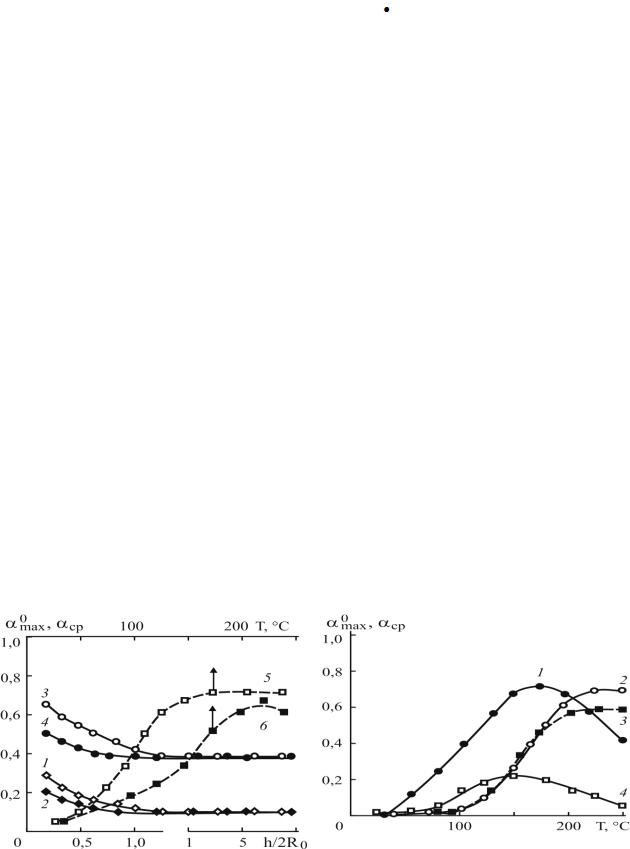
102
период работы алкилатора без существенной дезактивации слоя катализатора имеет вид:
α0max = [1+0,675(krº)-0,5•exp(-9674/₸) + 0,675(krº)0,5 exp(8347/₸)]-1, |
(4.37) |
где величина подгоночного параметра krº = 6∙10-16, отвечающая безразмерным относительным концентрациям и давлениям пропилена в законе Генри (4.17) рассчитывалась из имеющихся в нашем распоряжении экспериментальных результатов по за-
висимости выхода кумола от h, R0, ₸=Т0 + tср при Т0=433К.
При D0паб = 1∙10-8 м2/с, k0дез = 1,61∙10-8 с-1 и А=10 кДж/моль [1а,221а] на основании соотношения (4.32) и (4.37) были получены соответственно рабочие формулы
для вычисления среднего выхода αср кумола с учётом старения и дезактивации катализатора за время рабочего цикла (2 года) [1а] и максимального выхода кумола α0max в начальный период работы алкилатора без существенной дезактивации слоя катализатора:
αср = α0max•[1-(1,40 / h)•exp(-962 / Т)], |
(4.38) |
α0max=[1 + 2,756•107 • exp(-9674/Т) + 0,165•10-7• exp(8347 / Т)]-1, |
(4.39) |
где Т= Т0 + Тср ; Т0, Тср - температура алкилата и средняя температура перегрева слоя катализатора соответственно [°С].
Таким образом, мы получили выражения (4.38) и (4.39) для αср. и α0max. кумола, которые зависят только от температуры процесса алкилирования и геометрических параметров каталитического алкилатора (рис. 4.1).
Расчёты по формулам (4.38) и (4.39) показывают, что при абсолютной температуре алкилата Т0 = 303К (30ºС) и ₸ ≤ 384К (111ºС) алкилатор практически неработоспособен даже в самом тонком h = 0,1 м и широком R0 = 1,5 м слоях катализатора,
где величина α0max. ≤ 0,02. На рис. 4.2, а приведены результаты расчёта α0max и αср в зависимости от геометрического размера алкилатора или соотношения высоты слоя
катализатора h к его диаметру 2R0 при температуре алкилата 140ºС (кр. 1,2) и 180ºС (кр. 3,4) и зависимости их (кр. 5) и (кр. 6) от температуры алкилата, а на рис. 4.2, б –
зависимости α0max. (кр. 1,2) и αср (кр. 3,4) от температуры алкилата при тонком слое h = 0,1 м (кр. 1,4) и толстом слое h = 1 м (кр. 2,3) катализатора.
а |
б |
103
Рис. 4.2. Зависимости наибольших начальных выходов α0max (1, 3) и среднего выхода αср (2, 4) кумола: а – от соотношения высоты слоя катализатора h к диаметру алкилатора 2R0 при температуре алкилата 140ºС (1, 2) и Т = 180ºС (3,4); α0max (5) и αср (6) от температуры алкилата при h=1 м; б – α0max (1,2) и αср (3,4) от температуры алкилата при тонком h=0,1 м (1, 4) и толстом слоях h=1 м (2, 3) катализатора
В тонком и широком слоях катализатора в зависимости от h/2R0 до величины
h/2R0=1 на рис. 4.2,а – выходы кумола α0max и αср уменьшаются, они совпадают и не зависят от h/2R0 в рассчитанном диапазоне величин 1 ≤ h/2R0 ≤ 10, причём с увели-
чением температуры от 140 до 180ºС выходы кумола возрастают (сравни кр.1, 2 и кр. 3,4). Вместе с тем наблюдается увеличение выхода кумола в начальный период α0max. (рис. 4.2,а, кр. 4) в наиболее приемлемом практическом диапазоне изменения температуры 140-180ºС (рис. 4.2, а, кр. 5), поскольку в процессе эксплуатации катализатора за счёт его старения и дезактивации величина выхода αср достигает максимума при Т = 250ºС со снижением активности или быстрой дезактивации уже при Т = 300ºС (рис.4.2, а, кр. 6).
Результаты расчётов на рис. 4.2, б показывают, что с увеличением высоты слоя катализатора и температуры возрастает выход кумола α0max. и αср. (тонкий h = 0,1 м, кр. 1,4 и толстый слой катализатора h = 1 м, кр. 2,3), достигая максимума при Т = 175ºС (кр. 1) и Т = 150ºС (кр. 4), выходы кумола соответственно α0max и αср в тонком слое с последующим снижением за счёт «старения» и дезактивации тонкого слоя катализатора с повышением температуры (кр. 1, 4). Для толстого слоя катализатора (рис. 4.2, б, кр. 2, 3) для важного при эксплуатации катализатора технологического параметра αср наиболее приемлемым температурным диапазоном является Т = 140180ºС, поскольку с увеличением температуры также проявляется тенденция усиления и дезактивации катализатора, к примеру, при температуре Т = 200ºС (рис. 4.2, б, кр. 3) уже достигается максимальный выход кумола (кр. 3).
Таким образом, хотя математическая модель алкилатора предсказывает максимальные выходы прекурсора (кумол) с увеличением температуры, однако выше 200ºС (рис. 2, б) происходит быстрее «старение» и дезактивация катализатора – величины α0max и αср стремятся к «насыщению», проходят через максимум и снижаются
(рис. 2, а, кр. 5 и 6; б, кр. 1-4).
Для реальных практических условий процесса алкилирования для алкилатора оптимальным геометрическим параметром является 1≤ h/2R0 ≤ 10, а наиболее приемлемым температурным режимом эксплуатации цеолитсодержащего катализатора Т =
140-180ºС (рис. 2, а, кр. 1-4) с ожидаемым выходом прекурсора 10 ≤α0max = αср ≤ 40 масс.%. Эти результаты использованы ниже при создании и испытаниях реактора и
установки синтеза кумола каталитической дистилляции [211а-213а, 222а-225а]. Предсказанный математической моделью оптимальный температурный режим 140180°С (рис. 4.2) подтверждён максимальным выходом 26-30 масс.% и чистотой полученного прекурсора (кумола) (см. ниже) на экспериментальной установке и согласуется с результатами работы промышленного каталитического дистиллятора фирмы
Lummus Global [1а, 116].
4.2. Экспериментальная установка каталитической дистилляции синтеза кумола алкилированием бензола пропиленом
Предложенное техническое решение (полезная модель) [224а] представлена на рис. 4.3-4.5 блок-схема созданной экспериментальной установки каталитической ди-

104
стилляции непрерывного синтеза кумола алкилированием бензола пропиленом (вариант выполнения). Наиболее важными элементами предложенной установки каталитической дистилляции кумола являются конструкции реакционноректификационных колонн – алкилатора и трансалкилатора, узлов подачи бензола и пропилена, исходные данные которых были рассчитаны по предложенной выше математической модели (раздел 4.1).
В реакционно-ректификационных колоннах 1 и 2 (рис. 4.3) в качестве насадки использовали гетерогенный катализатор, который представляет собой цеолит типа Y с шифром ЦАИ МН, синтезированный в ИОХ РАН (г. Москва, д.т.н., профессор Е.С. Мортиков). В ректификационных колоннах 3 и 4 в качестве насадки используют мелко раздробленные керамические кольца Рашига, паровая часть которых снабжены термопарами, сверху – игольчатыми вентилями для регулировки давления паров бензола в колоннах, соединёнными через дефлегматоры с общим предохранительным клапаном. Колонны 1 и 2 снизу снабжены клапанами-регуляторами с манометрами, предназначенными для задания и обеспечения требуемого давления в колоннах, а также рубашкой для нагрева или охлаждения слоя катализатора, устройством замера уровня кубовой жидкости (не показано на рис. 4.3).
Воздушная линия
Рецикл бензола |
|
ПАБ |
|
|
|
||
|
|
|
Кумол |
|
|
30 |
4 |
Бензол |
1 |
3 |
|
|
|
||
2 |
|
|
|
|
|
|
|
|
|
|
32 |
|
|
31 |
|
Пропилен |
|
|
33 |
Азот |
Смола ПАБ |
|
11 |
12 |
10 |
|
|
|
Рис. 4.3. Блок-схема экспериментальной установки каталитической дистилляции непрерывного синтеза кумола алкилированием бензола пропиленом (Патент № 115779, 16.12.2011): 1 и 2 – реакционно-ректификационные колонны с гетерогенным катализатором; 3 и 4 - ректификационные колонны с инертной насадкой; 5 – пустотелая колонна; 6 и 7 – регулировочные вентили; 8 – предохранительный клапан; 9 – первый клапан-регулятор давления; 10 – второй клапан-регулятор давления; 11 и 12 – манометры; 30 и 32 – ёмкости; 31 и 33 – насосы (на рис. 4.3 насосы между колоннами, дефлегматоры, термопары и устройство замера уровня кубовой жидкости колонн не показаны)

105
Бензол |
Воздушная линия |
|
14 |
|
|
Азот |
1 |
|
|
1 |
|
13 |
1 |
В первую |
|
||
|
|
|
|
|
реакционно- |
|
|
ректификационную |
1 |
|
колонну 1 |
Рис. 4.4. Устройство подачи бензола (Патент № 115779, 16.12.2011): 13 – ёмкость для бензола; 14 – калиброванная мерная бюретка с выходом на воздушную линию; 15 – насос; 16 – предохранительный клапан; 17 – манометр; 18 – регулировочный вентиль
|
21 |
|
|
22 |
23 |
|
|
|
|
2 |
|
24 |
2 |
|
|
|
|
|
|
2 |
2 |
2 |
В первую |
|
|
||
|
|
|
реакционно- |
|
|
|
ректификационную |
|
|
|
колонну 1 |
|
1 |
|
|
Пропилен 20
Рис. 4.5. Устройство подачи пропилена (Патент № 115779, 16.12.2011): 19 – капилляр в виде спирали; 20 – термостат; 21 – дифференциальный манометр; 22 и 23 – регулировочные вентили; 24 и 25 – манометры; 26 и 27 – регулировочные вентили; 28 и 29 – вентили
На рис. 4.6 приведена конструкция алкилатора 1 и траналкилатора 2 или реак- ционно-ректификационных колон 1 и 2 (рис. 4.3) на основе геометрических размеров математической модели (раздел 4.1).
В колоннах 1 и 2 два входа друг против друга в кубовую часть расположены на высоте 40 мм, а вход пропилена с бензолом в колонну 1 – на высоте 70 мм от основания, вход для свежего бензола сверху металлической сетки слоя катализатора. В колоннах 1-4 и в колонне 5 (условно) термопара расположена на высоте 20 мм от верхней металлической сетки слоя насадки. Вход в колоннах 3-5 расположен на высоте 200 мм от основания или в середине слоя инертной насадки для колонн 3 и 4. Нижняя и верхняя крышки колонн 1-5 выполнены в виде «глухих» фланцев с соответствующими выходами в виде штуцеров с резьбой. Фланцы крышек и трубы имеют выступы и зазоры типа «шип-паз», обеспечивающие герметичность соединяемых элементов. Средняя часть колонн 1 и 2 со слоем катализатора снабжена рубашкой
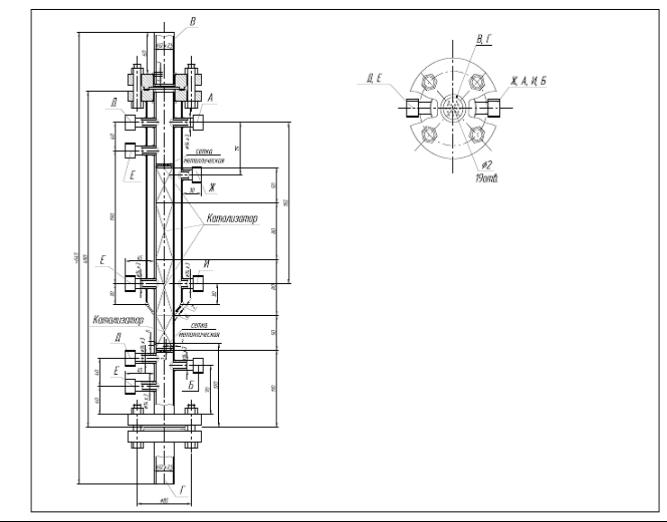
106
для нагрева паром или охлаждения водой. Верхняя часть кубовой части колонн 1-5 снабжена электронагревателем в виде спирали из вольфрама, который регулирует температуру кубовой части колонны изменением напряжением тока.
Устройство подачи бензола (рис. 4.4) представляет собой толстостенную стеклянную трубку с контрольными метками минимально и максимально допустимого уровня кубовой жидкости (смонтирована с внешней стороны, которая сообщается с полостью кубовой части колонн 1 и 2). Устройство выполнено в виде ёмкости, калиброванной мерной бюретки, соединённого с ней насоса с манометром и предохранительным клапаном. Реакционно-ректификационные колонны 1 (алкилатор) и 2 (трансалкилатор) содержат слой гетерогенного катализатора, расположенный в средней части или над кубовой частью колонн (рис. 4.6), а ректификационные колонны 3 и 4 с инертной насадкой для последовательной отгонки бензола и кумола и 5 – пустотелая колонна для отгонки ПАБ. Колонны 1-5 – «близнецы», имеют диаметр 27 мм и для колонн 1-4 высота слоя катализатора или насадки h = 260 мм с геометрическими параметрами h/2•R0 = 9,63 или удовлетворяют условию 1 ≤ h / 2R0 ≤10 математической модели.
Рис. 4.6. Конструкция алкилатора и трансалкилатора (Патент № 115779, 16.12.2011) на основе математической модели: А – вход бензола, Б – вход бензола и пропилена, В – выход абгазов, Г
– выход алкилата, Д и Е – штуцера для мономеров и термопар, Ж и И – выход воды (конденсата) и вход воды (пара)
107
Устройство подачи пропилена в колонну 1 (рис. 4.5) сконструировано в виде капилляра, скрученного в спираль и погруженного в термостат, соединённый с дифференциальным манометром, двумя манометрами и регулировочными вентилями. Дифференциальный манометр 21 (рис. 4.5) предназначен для измерения перепада давления на концах капилляра на линии подачи пропилена в колонну 1 и представляет собой промышленный манометр с контрольной шкалой 0-2 кгс/см2. Основными элементами в устройстве подачи пропилена (рис. 4.5) являются капилляр 19, скрученный в спираль, и регулировочный вентиль 27.
Предварительно проведены расчёты для линейного капилляра с целью нахождения диаметра d и длины капилляра L при заданном расходе пропилена W и перепаде давления ∆Р = 1 атм по формуле [1а, 224а]
∆Р~ L∙W / d4, |
(4.40) |
где единицы измерения L [м], W [л/ч] и d [мм].
Из результатов расчёта установлено, что при расходе пропилена W~5 л/ч и перепаде давления ∆Р = 1 атм длина линейного капилляра L = 5 м и диаметр d=0,3 мм. Линейный капилляр такой длины был скручен в спираль диаметра 100 мм, концы которого соединены с линией подачи пропилена в колонну 1, и помещён в термостат 20 для выдерживания при постоянной температуре (рис. 4.5). Испытания показали, что такая спираль при подаче пропилена под давлением 4-7 атм обеспечивает перепад давления ∆Р ~ 1 атм., а при точной регулировке перепада давления ∆Р = 1 атм. игольчатым регулировочным вентилем 27 (рис. 4.5) обеспечивает требуемую скорость подачи пропилена W = 4,7 л/ч в колонну 1 для выдерживания мольного соотношения пропилена и бензола 1:8 при скорости подачи бензола 150 мл/ч. Для исключения потерь тепла колонны 1-5 и все трубопроводы установки каталитической дистилляции (рис. 4.3), устройства подачи бензола (рис. 4.4) и пропилена (рис. 4.5) изолированы асбестом и асбестовым шнуром на силикате натрия.
Введение колонны 2 каталитической дистилляции кумола необходимо для обеспечения физического процесса равновесия пар-жидкость при изотермических условиях. Равновесие пар-жидкость при каталитической дистилляции кумола обусловливает равновесную концентрацию остаточного пропилена в жидкой фазе - алкилате кубовой жидкости и дистилляте колонны 1. Поэтому рециклы, которые содержат остаточный пропилен и кумол, не должны подаваться сверху колонны 2, а подаваться в её кубовую часть.
Поэтому для предотвращения образования нежелательных примесей и загрязнения ими гетерогенного катализатора и достижения 100%-ной конверсии пропилена организована оптимальным образом рециклы (рис. 4.3), которая достигается последовательностью соединения реакционно-ректификационных колонн 1 и 2 (рис. 4.3) и устройств подачи бензола (рис. 4.4) и пропилена (рис. 4.5).
Каталитическую дистилляцию кумола в изотермическом режиме осуществ-
ляли в колонне 1 алкилированием бензола пропиленом при мольном соотношений пропилена к бензолу 1:8, Т = 130ºС и Р = 4 атм, в колонне 2 алкилированием бензола остаточным пропиленом и трансалкилированием ПАБ при Т = 180ºС и давлении 10 атм, согласно математической модели по оптимальному температурному режиму алкилирования (рис. 4.2, формулы (4.38) и (4.39).
108
На экспериментальной установке (рис. 4.3-4.5) при каталитической дистилляции кумола происходит совмещение процесса алкилирования бензола пропиленом в колоне 1, алкилирования бензола остаточным пропиленом и трансалкилирования ПАБ в колонне 2 (рис. 4.3) с процессом фракционирования продуктов их реакции и бензола. При этом «моющий» эффект бензола слоя гетерогенного катализатора позволяет снизить образование дополнительного количества ПАБ и смолы ПАБ, добиться 100 %-ной конверсии пропилена, увеличивает выход и улучшает качество синтезируемого кумола, способствует увеличению срока службы гетерогенного катализатора [1а, 116-125].
Экспериментально была найдена полезная на практике (типа уравнения Антуана) аппроксимация зависимости давления P насыщенных паров бензола от его температуры кипения Ткип. для ректификации бензола при проведении в изотермическом режиме процесса каталитической дистилляции кумола путём алкилирования бензола пропиленом или трансалкилирования ПАБ при избытке бензола на гетерогенных катализаторах для диапазонов 80,1°С ≤ Ткип. ≤ 220°С и 1 атм ≤ Р ≤ 20 атм.
ℓgP = 4,0312 - 1214,65 / (221,21 + Ткип.). |
(4.41) |
Основными технологическими параметрами работы установки каталитической дистилляции кумола (рис. 4.3) являются:
-скорость подачи бензола 150 мл/ч в колонну 1 с помощью устройства подачи бензола (рис. 4.4), скорость подачи пропилена 4,7 л/ч с помощью устройства подачи пропилена (рис. 4.5) в колонну 1 при величине перепада давления пропилена ∆Р = 1 атм по дифференциальному манометру 21 и двум контрольным манометрам 24 и 25 до и после капилляра 19;
-изотермический режим в колоннах 1-3, т.е. температура пара бензола 130ºС и давление 4 атм в колонне 1, температура пара бензола 180ºС и давление 10 атм в колонне 2, Т = 80ºС при давлении в колонне 3 атм;
-температура паровой части колонн 4 и 5;
-величина остаточного давления (вакуума) – 0,85 кгс/см2 в колонне 5;
-оптимальный уровень кубовых жидкостей колонн 1-5 в пределах минимально
имаксимально допустимых значений по контрольным меткам устройства замера уровня кубовой жидкости. Детально технология работы экспериментальных узлов установки и ее в целом (рис. 4.3-4.6) представлена в нашей публикации [77а].
Втабл. 4.1 приведены экспериментальные результаты синтеза кумола каталитической дистилляции алкилированием бензола пропиленом на гетерогенном катализаторе на экспериментальной установке (рис. 4.3-4.5). Получаемый после колонны 2 (рис. 4.3, табл. 4.1) алкилат содержит бензол, кумол и незначительное количество 0,01 масс.% смолы ПАБ, который легко разделяется на стадии ректификации.
Таблица 4.1 Состав алкилата с установки каталитической дистилляции кумола (рис. 4.3-4.5)
Время, |
|
|
Состав алкилата, масс.% |
|
|
№ колонны |
|
|
|
|
|
|
|
|
|
||
час. |
|
|
|
|
|
|
Бензол |
Кумол |
Диизопропилбензол |
Смола ПАБ |
|
|
|
||||
|
|
|
|
|
|
8 |
1 |
72 |
22 |
3 |
Х |
|
|
|
|
|
|
109
|
2 |
74 |
26 |
Х |
Х |
|
20 |
1 |
73 |
24 |
3 |
Х |
|
2 |
72 |
28 |
Х |
Х |
||
|
||||||
36 |
1 |
70 |
27 |
3 |
Х |
|
2 |
69 |
30,1 |
Х |
0,01 |
||
|
||||||
720 |
1 |
70 |
27 |
3 |
Х |
|
2 |
69 |
30,1 |
Х |
0,01 |
||
|
Примечание: Х – отсутствует.
В табл. 4.2 приведены характеристики синтезированного кумола каталитической дистилляции на гетерогенном катализаторе на экспериментальной установке (рис. 4.3-4.5) и физико-химические показатели кумола, получаемого в промышленности на каталитическом комплексе хлорида алюминия. Чистота синтезированного кумола на гетерогенном катализаторе не менее 99,98 % с минимальным содержанием непредельных примесей не более 0,002 г брома на 100 г продукта или с бромным индексом 2 (табл. 4.2). В алкилате содержание кумола 26-30 масс.%, селективность гетерогенного катализатора 88,9-96,8 %, конверсия пропилена 100 % и за время испытаний в течение 720 ч не отмечено признаков дезактивации цеолитсодержащего катализатора. В табл. 4.3 приведены сравнительные характеристики синтеза кумола на основе каталитического комплекса хлорида алюминия в России и гетерогенном цеолитсодержащем катализаторе ЦАИ МН (ИОХ РАН, г. Москва) на экспериментальной установке (рис. 4.3).
Таблица 4.2
Сравнительные характеристики синтезированного кумола на гетерогенном катализаторе и промышленного образца кумола
на каталитическом комплексе хлорида алюминия
|
Природа катализатора |
||
Наименование показателя, |
Каталитический ком- |
Цеолит ЦАИ МН (ИОХ РАН, |
|
плекс на AICI3 |
г. Москва) |
||
по массовым долям: |
|||
|
Кумол |
||
|
|
||
- основного вещества, %, |
99,9 |
99,98 |
|
не менее |
|||
|
|
||
- органических примесей, |
0,15 |
0,02 |
|
%, не более: |
|||
|
|
||
- непредельных соедине- |
|
|
|
ний, г брома на 100 г продукта, |
0,015 |
0,002 |
|
не более |
|
|
|
- фенола, %, не более |
0,001 |
Х |
|
- хлора, %, не более |
0,0004 |
Х |
|
|
|
|
Примечание: Х – отсутствует.
Таблица 4.3
Показатели производства кумола на каталитическом комплексе хлорида алюминия на фенольных заводах России и синтеза кумола на
гетерогенном цеолитсодержащем катализаторе ЦАИ МН (ИОХ РАН, г. Москва) на экспериментальной установке (рис. 4.3-4.5)
Категория |
|
Нормы расхода сырья, образования побочных |
||
|
продуктов, отходов в кг на 1 т кумола |
|||
вещества |
Название вещества |
|||
Каталитический |
Цеолит ЦАИ МН |
|||
|
|
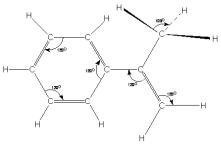
110
|
|
комплекс на AICI3 |
(ИОХ РАН, г. Москва) |
|
|
Бензол |
695 |
650 |
|
Сырье |
Пропилен |
375 |
350 |
|
|
ALCI3 |
6,0-11,0 |
не используется |
|
|
Едкий натр |
2,0-2,7 |
не используется |
|
|
ДБФ |
0,04 |
не обнаружено |
|
Побочные |
ЭБФ |
19,0 |
Х |
|
ББФ |
8,0 |
Х |
||
продукты |
||||
Смола ПАБ |
35,0 |
0,1 |
||
|
||||
|
Алюмохлорид |
30,0-36,0 |
Х |
|
|
Смола алкилирования |
0,01 |
Х |
|
|
«Мульма» |
2,0 |
Х |
|
Отходы |
Сточные воды (в т. ч.): |
2840,0 |
Х |
|
|
- AI+3 |
0,25 |
Х |
|
|
- органические примеси |
0,68 |
Х |
|
|
- фенол |
0,03 |
Х |
Примечание: Х – отсутствует.
Побочным продуктом является незначительное количество смолы ПАБ, которое можно использовать непосредственно на производстве в качестве котельного топлива для выработки тепла и пара. Экологических опасных и сточных вод и отходов не образуется (рис. 4.3). Реактор (алкилатор) и экспериментальная установка каталитической дистилляции (рис. 4.3-4.5) внедрена в научно-исследовательскую практику.
4.3. Технология и экспериментальная установка каталитической дистилляции синтеза поликонденсационных мономеров и α-метилстирола разложением технического гидропероксида кумола
α – метилстирол
С6Н5С(СН3)=СН2 |
(4.6) |
(изопренилбензол) ) – подвижная бесцветная жидкость с резким специфическим за-
пахом; Ткип. = 165,38оС, Тпл. = -23,14оС, d20 = 0,9106 г/см3, Т всп =. 58оС, nD = 1,5386,
уд. теплоёмкость 0,49 кал/(г.оС), теплота полимеризации 8,4 ккал/моль, энтропия полимеризации -26 кал/(моль.оС). Растворимость α-метилстирола в воде 0,01 об.%; 0,056 об.% α- метилстирола смешивается в любых соотношениях с ацетоном, СCl4, бензолом, н-гептаном и этанолом. Поверхностное натяжение при Т = 25оС составляет 32,8 дин/см; динамическая вязкость при Т = 20оС – 940 мг.с/м2. По физиологическому действию близка к стиролу; ПДК 5 мг/м3.
Углеродный скелет молекулы α-метилстирола лежит в плоскости бензольного кольца (4.1). Устойчивость молекулы повышается за счет энергии сопряжения бен-