
9
.pdf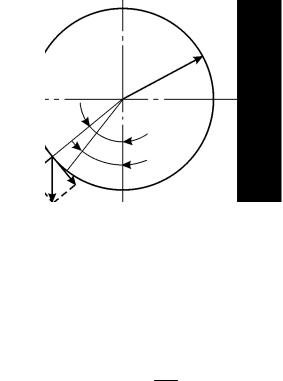
Незважаючи на те, що не вся робоча поверхня сит одночасно працює, продуктивність з одиниці площі сита не набагато менша за продуктивність інших конструкцій грохотів.
У барабанних грохотах робочою частиною слугує решето циліндричної форми. У процесі роботи барабан повільно обертається. Матеріал, що сортують, описує в просторі складну траєкторію. Унаслідок тертя шматків матеріалу об поверхню грохота, матеріал піднімається на деяку висоту. Сила інерції під час обертання змушує матеріал піднятися ще вище. Під час подальшого повороту барабана матеріал сиплеться вниз. Тому що вісь нахилена під кутом β до горизонту, матеріал, пересипаючись, рухається по грохоту до розвантажувальних пристроїв.
Барабан грохота обертається, підтримуваний опорними й опорнопідпорними роликами. Опорно-підпорні ролики обмежують переміщення барабана в осьовому напрямку. За допомогою бандажних кілець, натягнутих на барабан, він контактує з роликами.
Обертова частота. Якщо барабанний грохот нерухомий, шматок матеріалу може утримуватися на внутрішній поверхні барабана не вище точки А (рис. 2.8), положення якої визначається значенням кута β, що дорівнює куту тертя матеріалу об поверхню сита φ, тобто β = φ.
ω
R
F = fGcos α |
Б |
α |
|
β = φ |
|||
Gcos α |
|
||
|
А |
||
|
|
||
Pi |
G |
Gsin α |
|
|
Рис. 2.8 |
||
|
|
Сила тертя
F = fMg cos α.
Під час обертання барабана виникає відцентрова сила інерції
Pi = M VR2 ,
де М — маса завантаженого грохота; V — колова швидкість; R — радіус барабана.
41

Відцентрова сила інерції спричиняє силу тертя
Fi = fPi = fM VR2 .
Унаслідок дії сил F і Fi під час обертання барабана шматок матеріалу піднімається до точки Б. При цьому положення шматка масою G визначаємо з умови:
Mg sin α = fM |
v2 |
+ fMg cos α, |
|||
R |
|||||
|
|
|
|
||
звідки, якщо f = tg φ, одержимо |
|
|
|
||
n = |
1 |
sin(α −ϕ)g . |
|||
|
2π |
|
R sin ϕ |
На практиці під час нормальної роботи грохота α = 4…45°, а φ визначають з розрахунку, що коефіцієнт тертя шматка об поверхню решета через наявність у ньому отворів збільшується до 0,7.
З урахуванням викладеного
n = 10R ... 15R .
Продуктивність. Шматок матеріалу в точці А (рис. 2.9, а) піднімається до точки Б, обумовленої кутом α, після чого починається ковзання шматка до точки А1 по лінії найбільшого схилу, що складає з вертикальною віссю кут γ. Припустімо, що γ = β. Так матеріал рухається по гвинтовій лінії, кут підйому якої дорівнює:
θ = β + γ = 2β.
Розгорнувши на площині циліндричну поверхню сита разом із гвинтовою лінією, одержимо прямокутник АБВГ (рис. 2.9, б), одна сторона якого дорівнює довжині барабана, а друга
АГ = БВ = 2πRn,
де n — обертова частота барабана за час, протягом якого кожний шматок матеріалу пересунеться вздовж грохота на всю його довжину.
Довжина шляху шматка матеріалу
S = sinLθ = sinL2β.
Середня швидкість руху матеріалу вздовж барабана
V0 = V tg 2β = 2πRn tg 2β.
42
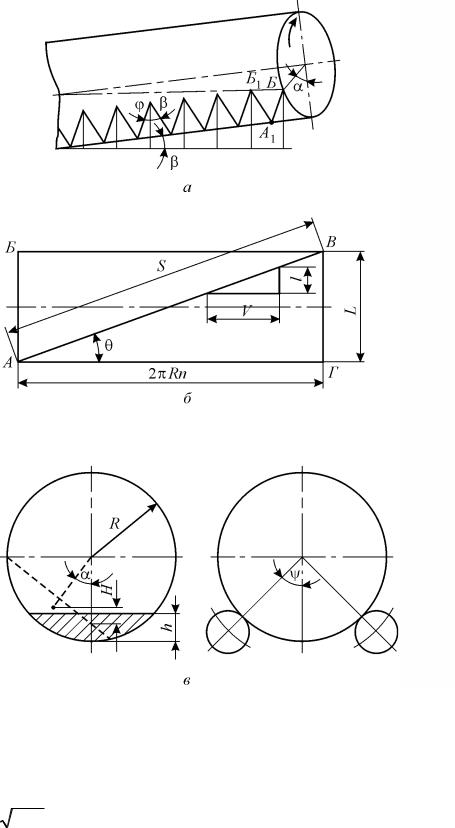
Рис. 2.9
Продуктивність грохота, т/год
Пρ = 3600vo F1ρнас,
де F1 = 2/3ah — площа перерізу матеріалу в грохоті (рис. 2.9, в); a = 2 2Rh; h = 1/ 4R.
Потужність, споживана барабанним грохотом на роликоопорах, витрачається на подолання тертя кочення бандажів барабана по роликах,
43
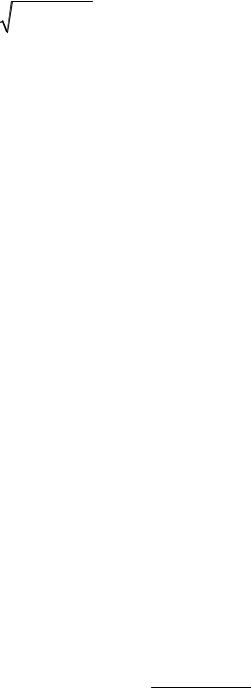
тертя ковзання цапф валів опорних роликів у підшипниках, тертя ковзання матеріалу по поверхні решета, під час сповзання матеріалу вниз і на підйом матеріалу.
Потужність електродвигуна, кВт:
|
|
|
N = |
8,88mRn(g + 23, 4n2 R) |
, |
||
|
|
|
ηn |
||||
|
|
|
|
|
|
|
|
де m =11,3ρµ |
8R |
3 |
′ |
3 |
— маса матеріалу в барабані, т; D'cp — розмір |
||
|
(Dcp ) |
|
шматків матеріалу верхнього класу, м.
2.2. Повітряне розділення матеріалів
Під час сортування сухих порошкових матеріалів, коли із загальної суміші частинок потрібно виділити сорти, у яких розмір зерен матеріалу не повинний перевищувати 100 мкн, застосовувати грохоти економічно недоцільно, тому що вони малопродуктивні. У цьому разі вдаються до повітряного сортування (сепарації) матеріалів.
Повітряне сортування основане на тому, що частинки матеріалу в повітряному потоці за певних умов осаджуються під дією сил тяжіння, відцентрових сил чи під спільним впливом цих сил.
У повітряному розділенні використовують гравітаційний метод, оснований на дії сил тяжіння на частинку, інерційний, оснований на дії відцентрових сил на частинку, і комбінований.
Гравітаційний метод. Рух частинок може бути в рухомому і нерухомому середовищах. Під час осадження в нерухомому середовищі на дуже дрібні частинки діє середовище із силою згідно із законом Стокса:
F = 3πdVoµ,
де d — еквівалентний діаметр частинки, м; Vo — швидкість осадження частинок, м/с; µ — в’язкість середовища, Па · с.
Силу осадження кулястої частинки можна визначити так:
σ = πd63 (ρ1 −ρ2 )g,
де ρ1 — об’ємна маса частинки; ρ2 — об’ємна маса середовища. Для випадку, коли G = F, швидкість осадження
Vo = d 2 (ρ1 −µρ2 )g . 18
44
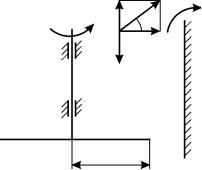
Для більш крупних осаджуваних частинок сила опору середовища за законом Ньютона дорівнює
|
V 2 |
|
|
|
F = ψρ2S |
o |
, |
(2.7) |
|
2 |
||||
|
|
|
де ψ — коефіцієнт опору середовища; S — площа проекції частинки на поверхню осадження; Vо — швидкість осадження. Якщо F = σ, швидкість осадження визначають так:
V = |
4gd(ρ1 −ρ2 ) |
. |
(2.8) |
|
|||
o |
3ψρ2 |
|
|
|
|
У цьому повітряному потоці одні частинки осідають (G > F), інші перебувають у зваженому стані (G = F), треті несуться середовищем
(G < F).
Взаємодію середовища і частинок описують законом Ньютона (2.7), а швидкість розраховують за рівнянням (2.8).
Відцентровий метод. На частинку діє |
|
|
|
|
||||
|
ω |
F |
α |
|||||
|
2 |
/ R , |
сила |
|
||||
|
|
|
||||||
відцентрова сила інерції I = mVц |
|
|
|
G I |
||||
опору середовища (визначають за законом |
|
|
|
|||||
Ньютона) і сила тяжіння, якою можна знех- |
|
|
|
|
||||
тувати (рис. 2.10). Сумарна сила являє со- |
|
|
|
|
||||
бою діагональ прямокутника. Чи винесеть- |
|
|
|
|
||||
ся частинка за межі стінки апарата чи за- |
|
|
R |
|
||||
лишиться, можна судити за значенням |
|
|
|
|||||
|
|
|
|
|||||
кута α: |
|
|
|
|
|
|
Рис. 2.10 |
|
|
F |
|
3ψρ V 2 |
|
|
|
|
|
tg α = |
|
= |
|
2 o |
, |
|
|
|
I |
dρ1R4ω2 |
|
|
|
||||
|
|
|
|
|
|
де ω — кутова швидкість потоку.
2.2.1. Прохідні сепаратори
Повітряні сепаратори в промисловості широко застосовують у помельних установках, що працюють за замкненим циклом. У цих випадках істотно підвищується продуктивність і знижуються витрати енергії млинів унаслідок безперервного відбору готового продукту. У повітряних сепараторах використання гарячих газів дає змогу поєднувати сортування і сушіння матеріалів.
Основна технологічна вимога до сепараторів — точність поділу суміші на фракції. Вона залежить від роду оброблюваного матеріалу, його волого-
45
сті, форми частинок, концентрації їх у потоці, мінливості межі поділу в різних точках об’єму, місцевих турбулентних завихрень у потоці і втрат напору під час його обертання, типу сепаратора та інших факторів.
У реальних умовах роботи сепараторів неможливо точно розділити матеріал, тому що неможливо забезпечити стабільний перебіг процесу. Тому дрібна фракція виявляється «забрудненою» крупними частинками, що погіршує її технологічні якості, а грубий продукт містить багато дрібних частинок, що позначається на економічності.
Пилоповітряна суміш по трубопроводу зі швидкістю 18…20 м/с вдувається в простір між зовнішнім і внутрішнім конусами (рис. 2.11). Унаслідок значного збільшення прохідного перерізу швидкість повітряного потоку спадає до 4…6 м/с. При цьому великі частинки матеріалу під дією сили тяжіння випадають вниз і відводяться через патрубок назад у млин для їх домелу. Пилоповітряна суміш з частинками матеріалу, швидкість падіння яких менша за швидкість повітряного потоку, надходить далі всередину конуса, проходячи на своєму шляху тангенціально встановлені лопатки. Ударяючись об лопатки, пилоповітряна суміш набуває обертального руху. Виникають відцентрові сили інерції, під їх дією великі частинки випадають, опускаються по стінках конуса і далі потрапляють у патрубок, що їх відводить. Пилоповітряна суміш, звільнена від великих частинок матеріалу, через патрубок виходить із сепаратора і направляється далі в пилоосаджувальні пристрої.
Роботу сепаратора регулюють за розмірами частинок, винесених повітряним потоком, такими способами:
—зміною швидкості повітряного потоку (зі зменшенням швидкості повітряного потоку кінцева тонкість частинок зменшується);
—зміною положення тангенціально встановлених лопатей.
Зустановкою лопаток радіальне завихрення потоку на цій ділянці знижується, зменшується вплив відцентрових сил. Отже, кінцева тонкість продукту збільшується.
Розрахування прохідного сепаратора зводиться до визначення критичних розмірів частинок, «нижнього» і «верхнього» класів.
Площа перерізу прохідного сепаратора, де витають частинки «верхнього класу», м2:
Fв = 0,05Dc2 ,
Площа перерізу прохідного сепаратора, де витають частинки «нижнього класу», м2:
Fн = 0,3Dc2 ,
46
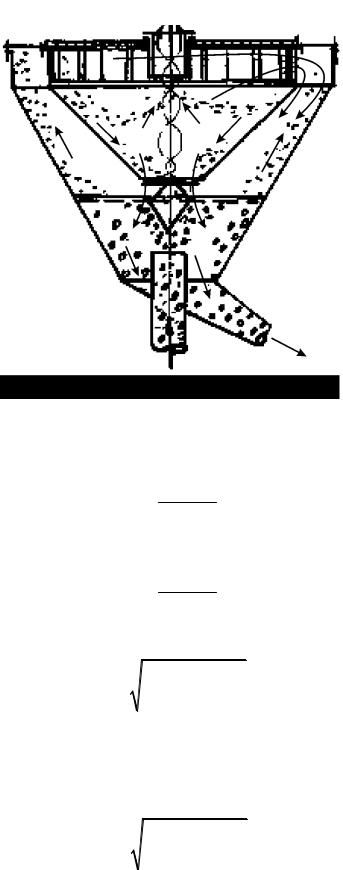
Тонка фракція
Вихідний матеріал Груба фракція
Рис. 2.11
Швидкість витання частинок «верхнього класу», м/с:
Vв = 3600Q Fв .
Швидкість витання частинок «нижнього класу», м/с:
Vн = 3600Q Fн .
Критичний розмір частинок «верхнього класу», м:
dв = 18Kф |
ρ1ν |
|
Vв |
, |
ρ2 |
|
|||
|
|
g |
де Kф — коефіцієнт форми частинки (для кулястих Kф = 1,0; овальних — 1,1; кутастих — 1,53; довгастих — 1,76; пластинчастих — 3,8); ν — кінематична в’язкість газу, м2 /с.
Критичний розмір частинок «нижнього класу», м:
dн = 18Kф |
ρ1ν |
|
Vн |
. |
|
|
|||
|
ρ2 |
g |
47
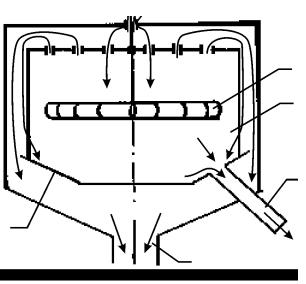
2.2.2. Відцентрові сепаратори
Відцентрові сепаратори застосовують, якщо частинки надходять роздільно від енергоносія.
Відмітна риса циркуляційних сепараторів — те, що вентилятор для створення повітряного потоку, розпилювач для утворення пилоповітряної суміші, пристрої, що сепарують і осаджують пил, об’єднані в одному агрегаті.
Вихідний матеріал надходить механічним шляхом.
У циркуляційних сепараторах порівняно з прохідними в 2…4 рази менше енергоспоживання, вони зручніші в експлуатації, мають вищу точність сортування. Завдяки цим перевагам циркуляційні сепаратори широко використовують у високопродуктивних промислових установках. У відцентрових сепараторах для нагнітання повітря застосовують турбіну 2 (рис. 2.12), що, обертаючись від урухомника, нагнітає повітря в апарат (повітряний потік піднімається вгору по малому конусу 6). Матеріал надходить з верху сепаратора через живильну лійку 1. Частинки проходять цикл засмоктування — нагнітання. Одні частинки, відбиваючись від великого конуса, несуться через нижній отвір 5, а інші потрапляють у малий конус 3 і відводяться через отвір 4.
1
2
3
4
6
5
Рис. 2.12
Параметри сепаратора розраховують за емпіричними формулами з поправковими коефіцієнтами, що можна отримати в результаті випробувань моделі чи зразка сепаратора.
48
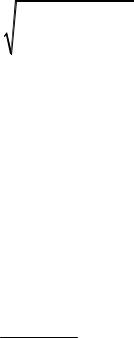
Діаметр робочої зони відцентрового сепаратора, м:
Dc = KПρα,
де K = 1,2…1,5 — коефіцієнт, що залежить від дисперсності частинок «нижнього класу», виду матеріалу, його вологості і форми, α = = 0,31…0,375 — коефіцієнт, що залежить від схеми поділу.
Витрати повітря, м3/с:
Q = 0,85Пρ.
Зовнішній діаметр лопаток вентилятора, м:
D2 = 0,85Dc .
Внутрішній діаметр лопаток вентилятора, м:
D1 = 0,6Dc .
Висота лопаток вентилятора, м:
h = 0,32 |
Q |
3 (Kф |
ρ1 |
)2 |
v |
, |
||
d |
|
|
D5n4 |
|||||
|
н |
|
ρ |
2 |
|
|
||
|
|
|
|
|
1 |
|
де ρ1, ρ2 — об’ємна маса відповідно повітря і частинок, кг/м3; v — кінематична в’язкість, м2/с.
Напір вентилятора, Па:
P =11,6n2 (D22 − D12 ).
Витрати потужності на поділ, кВт:
N = 1,65Пρ.
ККД сепаратора залежить від кількості частинок «нижнього класу» у вихідному матеріалі, конструкцій сепаратора і кількості «нижнього класу» у «верхньому класі»:
η = 100(a −b) , a(100 −b)
де а — масова частка «нижнього класу» у вихідному матеріалі; b — масова частка «нижнього класу» у верхньому класі.
Цю залежність отримано з умов матеріального балансу. ККД ретельно відрегулюваного сепаратора досягає 80…90 %.
49

Частина 2 Гідромеханічні процеси
Розділ 3 Очищення повітря і газів від пилу
3.1. Теоретичні основи процесу
Промислове очищення газів від завислих у них твердих чи рідких частинок проводять, щоб зменшити забруднення повітря, уловлювати з газу коштовні продукти чи видаляти з нього шкідливі домішки, які негативно впливають на подальшу обробку газу, а також руйнують апаратуру.
У промислових умовах пил може утворитися в результаті механічного подрібнювання твердих тіл (під час дроблення, стирання, розламування, транспортування тощо), під час горіння палива (зольний залишок), під час конденсації пари, а також у результаті хімічної взаємодії газів, що супроводжується утворенням твердого продукту. Одержуваний у таких процесах пил складається з твердих частинок розмірами 3…70 мкм. Суспензії, які утворюються в результаті конденсації пари (нафтові дими, тумани смол, сірчаної кислоти й ін.), найчастіше складаються з дуже дрібних частинок розмірами від 0,001 до 1 мкм.
Ступінь очищення газу визначають так:
η = |
G1 −G2 |
100 % = |
V1 X1 −V2 X2 |
100 %, |
|
G |
|
||||
|
|
V X |
1 |
|
|
|
1 |
1 |
|
де G1 і G2 — кількість завислих частинок відповідно у вихідному (забрудненому) і очищеному газі, кг/г; V1 і V2 — об’ємні витрати вихідного й очищеного газу, зведеного до нормальних умов, м3/г; Х1 і X2 — концентрація завислих частинок у запиленому газі, зведеному до нормальних умов, кг/м3.
50