
9
.pdf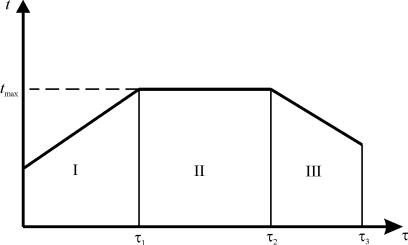




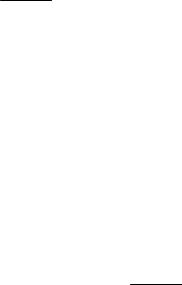
Параметр |
Місце |
Вхідна величина |
Вихідна величина |
|
регулювання |
регулювання |
|||
|
|
|||
Вологовміст мате- |
Сушильна установка |
d′м |
d''м |
|
ріалу |
|
|
|
|
Вологовміст теп- |
Перед калорифером |
х0 |
хсм |
|
лоносія |
||||
|
|
|
||
Відносна вологість |
На виході із сушарки |
ϕ1 |
ϕ2 |
|
теплоносія |
|
|
|
|
Температура теп- |
На виході з калорифера |
tсм |
t1 |
|
лоносія |
|
|
|
|
Розрідження |
У сушарці |
P1 |
P2 |
Примітка: d'м, d''м — вологовміст матеріалу на вході та на виході; хсм = х1 — вологовміст повітря на вході та виході з калорифера; х0 — вологовміст свіжого повітря, яке добавляють до відпрацьованого; ϕ1, ϕ2 — відносна вологість повітряної суміші на вході та виході із сушарки; t1 — температура теплоносія на виході з калорифера чи на вході до сушарки; tсм — температура повітряної суміші на вході до калорифера; ∆P = Р1 – Р2 — перепад тиску (розрідження).
Характерна особливість більшості машин для переробки пластмас полягає в тому, що під час транспортування матеріалу в машинах одночасно з підведенням теплоти через стінку ззовні виділяється теплота дисипації від докладеної сили.
Рівняння теплового балансу для таких машин має такий вигляд: qi + qн = С + mC(tк − tп ),
де С — постійні втрати в навколишнє середовище; mС — питома теплоємність матеріалу.
У цьому разі вхідний параметр автоматизації складається з двох показників: продуктивності внутрішнього джерела теплоти qi та теплоти нагрівачів qн. Вихідний параметр автоматизації — кінцева температура мате-
ріалу tк.
Продуктивність внутрішнього джерела qi визначає криву постійного зростання температури матеріалу від початкової tп по довжині устаткування. Змінюючи qн, можна змінювати хід кривої наростання температури та отримувати матеріал відповідної якості.
Дедалі більші масштаби застосування пластмас у різних галузях промисловості та підвищення вимог до якості виробів ставлять перед спеціалістами з переробки полімерів та розробниками обладнання серйозні проблеми, пов’язані з підвищенням точності вимірювання технологічних параметрів та якості керування процесами переробки. Вирішення цих
249