
9
.pdf
|
|
|
|
|
w |
|
|
n+1 |
|
Rn+1 |
− Rn+3 |
||||
|
|
|
|
|
|
|
|
|
|
2 |
1 |
|
|
||
QN = 2πHIK |
|
|
|
|
|
|
|
|
|
|
+ |
||||
|
|
|
|
|
|
|
|
|
|||||||
|
|
|
|
|
|
|
|
|
|
n + 3 |
|
|
|||
|
|
|
|
H |
|
|
|
|
|
|
|
||||
|
|
|
|
|
|
|
|
|
|
|
|
|
(10.74) |
||
|
w |
2n+1 |
|
|
|
2n+3 |
|
2n+3 |
|
||||||
+CK |
|
|
|
|
R2 |
|
|
− R1 |
|
||||||
|
|
|
|
|
|
|
|
|
|
|
|
. |
|||
|
|
|
|
|
|
2n + |
3 |
||||||||
|
|
H |
|
|
|
|
|
|
|
||||||
|
|
|
|
|
|
|
|
|
|
|
|
|
|
|
У рівнянні (10.74) К визначають за залежністю (10.63), де t — середньоінтегральне значення температури в робочому зазорі, яке отримуємо внаслідок розв’язання рівняння енергії.
Знаючи QN, можна визначити потужність урухомника дискового екструдера:
N= QN/I.
Зрівняння (10.73) можна визначити Qн, тобто кількість теплоти, яку треба підвести до екструдера чи відвести від нього:
±Qн = QN − Пρ (iп′′ − iп′ ),
де Пρ — масова продуктивність дискового екструдера:
|
1 |
|
|
Пρ = 2πrH ∫ |
Ydη γ. |
(10.75) |
|
|
0 |
|
|
Рівняння (10.75) можна розв’язати методом Бубнова — Гальоркіна:
Пρ = 2πrH (−0,083a − 0,05b)ρ, |
(10.76) |
де а та b — параметри, отримані для певного зазору радіусом r за умови сталості витрат полімеру через зазор:
|
|
|
|
|
|
|
1 |
|
|
|
|
|
|
|
|
|
|
|
|
|
|
|
|
|
|
2πrH ∫ |
Vr dη = const. |
|
|
|
|
|
|||||||||
|
|
|
|
|
|
|
0 |
|
|
|
|
|
|
|
|
|
|
|
|
|
З урахуванням (10.76) та (10.74) маємо |
|
|
|
|
|
|
|
|
|
|||||||||||
|
|
w |
n+1 |
n+1 |
|
|
n+3 |
|
|
|
w |
2n+1 |
2n+3 |
2n+3 |
|
|
||||
|
|
|
R2 |
|
− R1 |
|
|
|
R2 |
− R1 |
|
|||||||||
QN |
= 2πHIK |
|
|
|
|
|
|
|
|
|
+ CK |
|
|
|
|
|
|
|
− |
|
|
|
|
|
|
|
|
|
|
|
|
||||||||||
|
|
|
|
|
n + 3 |
|
|
|
|
|
2n + 3 |
|
|
|||||||
|
|
H |
|
|
|
|
|
|
H |
|
|
|||||||||
|
|
−2πHρr(−0,083a − 0,05b)(iп′′ − iп′ ). |
|
|
|
|
||||||||||||||
|
|
|
|
|
|
|||||||||||||||
Інтенсивність тепловіддачі від дисків до полімеру чи навпаки |
|
|
||||||||||||||||||
|
|
|
|
|
|
αп = |
|
|
±Qн |
|
|
, |
|
|
|
|
|
|
||
|
|
|
|
|
|
(F |
+ F )∆t |
|
|
|
|
|
|
|
||||||
|
|
|
|
|
|
|
|
|
1 |
2 |
|
|
|
|
|
|
|
|
|
де F1, F2 — площа поверхні відповідно рухомого та нерухомого диска; ∆t — перепад температур між поверхнями дисків та розплавом полімера в зазорі.
221
Перепад ∆t у разі підведення теплоти |
|
||||||
∆t = |
(tp.д −tcp )F1 |
+ (tн.д −tcp )F2 |
|
(10.77) |
|||
F1 |
+ F2 |
||||||
|
|
|
|||||
У разі відведення теплоти від робочого зазору |
|
||||||
∆t = |
|
(tcp −tp.д)F1 |
+ (tср −tн.д)F2 |
. |
(10.78) |
||
|
F1 |
|
|||||
|
|
+ F2 |
|
У разі плоскопаралельного зазору між дисками рівняння (10.77)—(10.78) спрощують до
∆t = |
tp.д +tн.д |
−t |
; |
(10.79) |
|||
|
|||||||
2 |
|
cp |
|
|
|
||
∆t = tcp − |
tp.д +tн.д |
|
. |
(10.80) |
|||
|
2 |
|
|||||
|
|
|
|
|
|
У формулах (10.77)—(10.80) tcp — середньоінтегральне значення температур у зазорі, отримане в результаті розв’язання рівняння енергії.
10.9. Роторні змішувачі
За основу розрахування двороторного гумозмішувача взято те, що корисна потужність двигуна повністю перетворюється на теплоту.
Кількість теплоти, яка виділяється за одну годину роботи змішувача, така:
QN = Nкор.
Знаючи корисний об’єм камери та час перебування маси у змішувачі, можна визначити продуктивність машини, яку розраховують не враховуючи завантаження та розвантаження суміші:
Пρ = Gсмш / τ1,
де Gсмш — маса суміші; τ1 — час перебування маси в камері.
Знаючи продуктивність гумозмішувача, можна визначити кількість теплоти, витраченої на нагрів гумової суміші:
Q1 = Пρ (tк – tп) Сс,
де Сс — питома теплоємність суміші; tп, tк — відповідно початкова та кінцева температура гумової суміші.
222
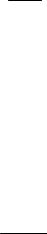
Кількість теплоти, яку слід відвести охолодною водою, визначають як різницю
Qв = QN – Q1.
Витрати охолодної води
Gв = CQ∆вt ,
де С — теплоємність води; ∆ t — перепад температур у каналах камери,
∆t = 3,5…6 °C.
За відомою конструкцією гумозмішувача визначають дійсну поверхню охолодження, яка складається з поверхонь горбуші Fгрб, вантажу Fван, камери Fк та двох поверхонь роторів Fрот:
F = Fван + 2Fрот +Fгрб + Fк.
Теоретична поверхня охолодження
Fт = Qв , K∆tcp
де ∆tcp — середній температурний напір; коефіцієнт теплопередачі
K = |
|
1 |
|
|
|
|
, |
|
|
1 |
+ ∑ |
δ |
+ |
1 |
|
||
|
|
α |
λ |
α |
||||
|
|
1 |
|
|
|
2 |
|
|
де δ — товщина стінки; λ — теплопровідність матеріалу камери; α1 — коефіцієнт тепловіддачі від гумової суміші до стінки камери; α2 — визначають з критеріальних рівнянь вимушеної конвекції.
Для визначення α2 розраховують спочатку швидкість течії рідини (води) в каналах
Vв = |
Gв |
3600F |
|
|
кан |
та швидкість гумової суміші в камері залежно від швидкості руху роторів. Середній температурний напір ∆tcp залежно від виду руху теплоносіїв
∆tcp = |
∆tб − ∆tм |
. |
|||
|
|||||
|
ln |
∆tб |
|
|
|
∆tм |
|||||
|
|
Якщо Fт < F, то відведення зайвої (надлишкової) теплоти в камері гумозмішувача забезпечено.
223
10.10. Вулканізатори
Розрахування вулканізатора покришок зводиться до складання теплового балансу. Загальні сумарні витрати теплоти складаються з кількості теплоти, витраченої на нагрівання парової камери Qп.к; кількості теплоти, витраченої на нагрівання півформ Qп.ф; кількості теплоти, витраченої на нагрівання покришек Qпкр; кількості теплоти, витраченої на нагрівання та продування діафрагми Qд та витрат теплоти в навколишнє середовище за рахунок вільної конвекції Qк та випромінювання Qвпр:
∑Q = Qп.к + Qп.ф + Qпкр + Qд + Qк + Qвпр. |
(10.81) |
Складові рівняння (10.81): |
|
Qп.к = Gп.кC1(tп – tк), |
(10.82) |
де Gп.к — маса парової камери; С1 — питома теплоємність металу, з якого виготовлено камеру; tп — початкова температура камери; tк — кінцева температура чи температура, до якої охолоджується парова камера;
Qп.ф = Gп.фС1(tп – tк), |
(10.83) |
де Gп.ф — маса напівформи; tп, tк — початкова та кінцева температура півформи;
Qпкр = GпкрС2(tср – t0), |
(10.84) |
де Gпкр — маса заготовки покришки; С2 — питома теплоємність матеріалу заготовки; tср — середня температура нагрівання покришки; t0 — температура завантаженої заготовки;
Qд = GдС3(tк – tп) + nVβρi,
де Gд — маса діафрагми; С3 — питома теплоємність матеріалу діафрагми; п — кількість продувок за один цикл вулканізації; V — об’єм діафрагми; і — ентальпія пари за робочої температури; ρ — об’ємна маса пари;
Qк = (F1K1 + F2K2 + F3K3)(t1 – t2), |
(10.85) |
t1 — температура корпусу; t2 — температура навколишнього повітря; F1 = F3 — площини верхнього та нижнього днищ корпусу:
F1 = F3 = πD2/4;
F2 — площа поверхні бокової стінки корпусу:
F2 =πDН;
224
К1 — коефіцієнт теплопередачі через верхнє днище корпусу:
K1 |
= |
|
|
|
1 |
|
|
|
|
|
|
|
; |
|
|
1 |
+ |
δ1 +δ2 |
|
+ |
δi3 |
+ |
1 |
|
|||||
|
|
|
|
|
|
|||||||||
|
|
|
α |
λ |
|
α |
|
|
|
|||||
|
|
|
|
|
λ |
i3 |
|
2 |
|
|
||||
|
|
|
1 |
|
|
|
|
|
|
|
|
|
α1, α2 — коефіцієнт тепловіддачі відповідно у разі конденсації пари та вільної конвекції; δ1, δ2 — товщина відповідно стінки верхнього днища та кожуха; δіз, λіз — відповідно товщина та теплопровідність ізоляції; К3 — коефіцієнт тепловіддачі через нижнє днище та стіл:
K3 |
= |
|
|
|
1 |
|
|
|
|
|
|
|
; |
|
1 |
+ |
δ3 +δ4 +δ2 |
+ |
δi3 |
+ |
1 |
|
|||||
|
|
|
α |
λ |
|
α |
|
|
|
||||
|
|
|
|
|
λ |
i3 |
|
2 |
|
|
|||
|
|
|
1 |
|
|
|
|
|
|
|
|
δ3 — товщина нижнього днища; δ4 — товщина листа столу; К2 — коефіцієнт теплопередачі через бокову стінку:
K2 |
= |
|
|
|
|
|
|
1 |
|
|
|
|
|
|
|
; |
|
|
|
|
1 |
|
+ |
δ5 |
+ |
1 |
|
|
|
|
|
||||||||||
|
|
|
|
|
|
|
|
|
|
|||||||||||
|
|
|
|
α |
|
λ |
α |
2 |
|
|
|
|
|
|
|
|||||
|
|
|
|
|
|
|
|
|
|
|
|
|
|
|
||||||
|
|
|
|
|
1 |
|
|
|
|
|
|
|
|
|
|
|
|
|
||
δ5 — товщина бокової стінки; |
|
|
|
|
|
|
|
|
|
|
|
|
|
|
|
|
|
|
|
|
|
|
|
|
T |
|
4 |
|
|
|
|
|
T |
4 |
|
||||||
Qвпр = εC0 F |
1 |
|
|
|
− |
|
2 |
|
, |
(10.86) |
||||||||||
|
|
|
100 |
|||||||||||||||||
|
|
|
|
100 |
|
|
|
|
|
|
||||||||||
|
|
|
|
|
|
|
|
|
|
|
|
|
|
|
|
|
|
|
де ε — ступінь чорноти матеріалу, з якого виготовлено прес-форму; С0 — константа випромінювання чорного тіла; F — сумарна площа випромінювання; Т2, Т1 — абсолютна температура відповідно повітря та пресформи.
Витрати пари на формування покришок
Gф.п = ρVnK,
де ρ — густина пари; V — об’єм діафрагми; п — кількість циклів формування; К — коефіцієнт витрат.
Кількість теплоти, яку витрачає пара, йде на нагрів діафрагми та покришки зсередини, на компенсацію втрат теплоти, на обігрівання парової камери, півформи та покришки ззовні.
Отже, сумарні витрати:
∑G =G2 +Gф.п +Gвт +G1.
225
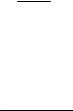
Кількість теплоти на нагрівання діафрагми та покришки зсередини:
Q2 = (0,5GФС1 + GпкрС2 )(tк −tп),
де Gф, Gпкр — маса форми та покришки, tк, tп — кінцева та початкова температура форми.
Витрати нагрівальної пари з урахуванням Q2 на нагрівання діафрагми та покришки зсередини
G2 = iQ−2r +Vρ,
де і — ентальпія пари; r — прихована теплота пароутворення. Витрати пари на компенсацію втрат теплоти
Gвт = Qвпрi −+rQк +Vρ,
де Qк та Qвпр визначають відповідно за формулами (10.85) та (10.86). Витрати пари на обігрівання парової камери, півформи та покришки
ззовні
G |
= Qп.к +Qп.ф +Qпкр +Vρ, |
||
1 |
|
i − r |
|
|
|
де складові теплоти Q визначають за формулами (10.82)—(10.84).
Окрім пари, у процесі вулканізації використовують також перегріту та охолодну воду. Витрати перегрітої води мають умовний характер, оскільки вода циркулює по замкненому контуру.
Vв = V / τ,
де τ — час наповнення об’єму V діафрагми. Витрати охолодної води на одну секцію
Vо.в = Qпкр / (tк – tп),
де tк, tп — кінцева та початкова температура охолодної води; Qпкр — кількість теплоти, яку слід відібрати від покришки, щоб охолодити її до визначеної температури:
Qпкр = (GдС3 + GпкрС2 + 0,5Gп.фС1)·2(tпкр – tв.ох),
де tв.ох — температура охолодної води; tпкр — температура покришки.
226

10.11. Тепловий розрахунок формувальних інструментів
Правильно сконструйована система охолодження литтєвих форм забезпечує скорочення часу охолодження, циклу лиття, а також високу якість готового виробу. Час циклу лиття залежить від швидкості охолодження виробів та форми, тобто від температури форми. На якість виробу впливає однорідність температури цієї форми.
Для одновимірного температурного поля характерне таке рівняння нестаціонарної теплопровідності
dt |
= а |
d 2t |
. |
(10.87) |
dτ |
|
|||
|
dx2 |
|
Розв’язання рівняння (10.87), коли Fо > 0,2, має такий вигляд:
tк −tп |
=1 − |
4 |
|
− |
π2 |
|
|
||
|
|
|
|
exp |
|
Fo . |
(10.88) |
||
t |
−t |
|
π |
4 |
|||||
ф |
|
п |
|
|
|
|
|
|
|
Після деяких перетворень, рівняння можна записати в іншому вигляді:
tф −tк |
= |
4 |
|
− |
π2 |
|
|
||
|
|
|
|
exp |
|
Fo . |
(10.89) |
||
t |
−t |
|
π |
4 |
|||||
ф |
|
п |
|
|
|
|
|
|
|
У рівняннях (10.88) та (10.89) tф — середня за цикл температура поверхні форми. Ця температура під час циклу лиття не залишається постійною, але її коливання не перевищують 3 °С; tк, tп — температура маси матеріалу відповідно у кінці та на початку процесу; величина а, яка вхо-
дить до критерію Fo = δa2τ — середньоінтегральне значення температуро-
провідності матеріалу в умовах переробки; δ — товщина виробу, а якщо охолодження двостороннє — половина товщини виробу; τ — час охолодження. З рівняння (10.89) можна визначити час охолодження матеріалу у формі:
τ = |
0,933δ2 |
|
tф −tк |
|
||
|
tg 1,27 |
|
|
|
. |
|
а |
t |
−t |
|
|||
|
|
|
|
|||
|
|
|
ф |
|
п |
Як бачимо, на час охолодження виробу впливає товщина виробу, температуропровідність матеріалу виробу, а також температура форми. Отже, для конкретного матеріалу, коли відомо величини a, δ, tп, tк, час охолодження залежить тільки від температури охолодного теплоносія,
227

який проходить по каналах форми. Чим нижча його температура, тим менший час охолодження.
Знаючи масу виробу G, різницю його температур (tп – tк), середню теплоємність матеріалу в межах температур переробки ∆t, можна визначити кількість теплоти, яку охолодний теплоносій має відвести від форми.
Qм =G Cz(tп −tк ),
де z = 3600 /τц — кількість виробів, отриманих за одну годину роботи. Повний час циклу лиття τц складається з часу охолодження τох та ме-
ханічного часу τмех, витраченого на змикання (розмикання) прес-форми:
τц = τох + τмех.
Витрати охолодного теплоносія можна визначити з рівняння теплового балансу:
Qт =Qм +Qо.с, |
(10.90) |
де Qо.с — витрати теплоти в навколишнє середовище. Запишемо рівняння (10.90) в розгорненому вигляді:
GтCт (tтк −tтп ) = GCz(tп −tк ) − αFф (tф −tс ),
де Gт — часові витрати охолодного теплоносія; Fф — площа поверхні форми; tс — температура навколишнього середовища. Різниця температур (tтк – tтп) не має перевищувати 2 °С; α ≈ 5,8 Вт/(м2 · °С) — коефіцієнт тепловіддачі природною конвекцією.
Якщо рідину, яка випаровується в каналах, використовувати як охолодний теплоносій, то
Qт = Gт rт,
де rт — прихована теплота пароутворення охолодного теплоносія.
Щоб забезпечити рівномірне охолодження, слід визначити максимально допустиму відстань між охолодними каналами у формі
|
R = |
2lg D |
; |
|||||
|
|
|
||||||
|
|
|
|
A |
|
|
||
D = |
t |
2 |
|
t |
2 |
2 |
||
|
± |
|
|
−1 , |
||||
t1 |
|
|
||||||
|
|
t1 |
|
де t1, t2 — температура відповідно форми в середині відстані між каналами та на поверхні форми біля охолодних каналів. Різниця між цими температурами не має перевищувати 0,5 °С.
228

Коефіцієнт форми
A = |
αP |
, |
|
λF |
|||
|
|
де α — інтенсивність тепловіддачі між рідиною, яка протікає в каналах та формою; Р = 2(B+h) — периметр форми; B, h — ширина та висота форми; λ — теплопровідність матеріалу форми; F= Bh — переріз форми між каналами.
Щоб визначити площу перерізу каналів, швидкість течії охолодного теплоносія беруть у межах 1…1,5 м/с.
Витрати охолодного теплоносія між пуансоном та матрицею розподіляють пропорційно поверхні оформлення виробу:
Gп(м) = GтFп(м) ,
Fзаг
де Gп(м) — витрати охолодного теплоносія на пуансон (матрицю); Fп(м) — площа частини поверхні виробу, яка формується пуансоном (матрицею); Fзаг — сумарна поверхня виробу.
Переріз каналу, яким рухається охолодний теплоносій в пуансоні чи матриці:
fп(м) = |
Gп(м) |
. |
||
3,6 |
106V |
|||
|
|
Якщо канал круглий, то його діаметр
dп(м) = |
4 fп(м) |
. |
|
π |
|||
|
|
Поверхня теплообміну каналів з рівняння теплового балансу
Fп(м) = Gп(м)C(tк −tп ) .
Довжина каналів в пуансоні та матриці
L |
= |
Fп(м) |
. |
(10.91) |
|
||||
п(м) |
|
πd |
|
Розміщуючи охолодні канали у формі, треба мати на увазі, що виріб має бути оточений цими каналами. Крім того, канали в матриці мають бути розміщені проти виштовхувальних шпильок.
229

Якщо використовують як охолодний теплоносій рідину, що випаровується, розрахунок проводять так:
—визначивши витрати охолодного теплоносія та коефіцієнт тепловіддачі під час кипіння рідин, розраховують поверхню теплообміну каналу:
Fп(м) = Qαтп∆(tм) ;
— за формулою (10.91) визначають довжину каналу Lп(м).
Практика лиття та експерименти показали, що зниження температури води взимку до 2…5 °С порівняно з літньою 20…25 °С та збільшення витрат цієї води в 1,5—1,75 разу, дає можливість підвищити продуктивність лиття на 35—60 %.
10.12. Теплообмін під час вакуумного формування, зварювання та нанесення покриття
10.12.1. Вакуумне формування
Під час вакуумформування лист з термопласту закріплюють по контуру форми та нагрівають радіаційними нагрівачами. Тиск, потрібний для формування, створюється за рахунок різниці тисків між зовнішнім атмосферним тиском та внутрішнім розрідженням, яке виникає в порожнині між листом та поверхністю форми. Після охолодження відформованого виробу, потрібного для фіксації форми, його видаляють з матриці.
Розглянемо випадок двостороннього радіаційного нагрівання плоского листа та припустимо таке:
—лист темний щодо інфрачервоного випромінювання, у цьому разі промениста енергія переходитиме в теплову безпосередньо на поверхні листа, а теплота поширюватиметься у товщі листа за рахунок теплопровідності;
—тепловіддачею за рахунок конвекції на поверхні листа нехтуємо;
—вважаємо, що кількість теплоти, переданої з поверхні листа, не залежить від температури; це допущення обумовлює сталість теплового потоку через поверхню листа.
Рівняння нестаціонарної теплопровідності у цьому разі має вигляд:
dt |
= a |
d 2t |
|
|
|
|
. |
(10.92) |
|
dτ |
dx2 |
230