
9
.pdf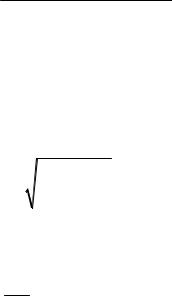
Центральний кут кола ролика, що відповідає дузі між лініями зіткнення ролик — шматок і ролик — кільце, рад,
β = arccos d(D − d) − Dcp (d + D) .
Зусиллястисканняматеріалуміжроликом, щообертається, ікільцем, МН,
P = d 2βσ/ 4,
де σ — межа міцності матеріалу на стискання, МПа. Обертова частота вертикального вала, с–1,
n > |
1 |
|
2P |
, |
2 |
|
G(D − d) |
||
|
|
|
де G — сила тяжіння ролика, Н. Продуктивність млина, т/год:
Пρ = 1 3600VрbhρV z,
Kц
де Kц — коефіцієнт, що враховує кратність циркуляції матеріалу у млині; Vр — колова швидкість ролика, що дорівнює швидкості обертання на радіусі від центра вертикального вала до кільця, м/с; b — ширина ролика, м; h — товщина шару матеріалу під роликом, м; ρV — об’ємна маса матеріалу, Т/м3; z — кількість роликів.
Потужність, споживана млином, витрачається:
— на подолання тертя кочення ролика по матеріалу, Вт:
N1 = PµVролz,
де µ — коефіцієнт опору коченню ролика;
— на подолання сил тертя, спричинених проковзуванням ролика, Вт:
N2 = PfVквзz,
де f — коефіцієнт тертя валка об матеріал; Vквз — швидкість ковзання, pекомендовано брати Vквз = (0,095…0,098)Vрол;
— на подолання сил тертя в підшипниках вала маятника з роликом, Вт:
N = 0,1Pfквзrnpолz,
де fквз — коефіцієнт, що враховує ковзання; nрол — обертова частота ролика, с–1.
31
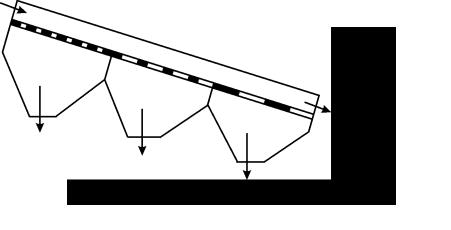
Розділ 2 Розділення сипучих матеріалів
2.1. Просіювання матеріалів
Механічне сортування (просіювання) виконують за допомогою машин з пристроями для просіювання. Застосовують просіювання, щоб одержати два чи декілька сортів зерен, що різняться крупністю. Кількість одержуваних сортів залежить від кількості решіт (сит), через які було пропущено оброблюваний матеріал. Якщо застосувати n решіт, то виходить (n + 1) сорт матеріалу.
Просіювання буває самостійне, коли отриманий матеріал — це готова продукція для споживача, проміжне, коли продукти і надалі подрібнюють, і допоміжне — для виділення дрібних фракцій, наявність яких у матеріалі зменшує продуктивність устаткування.
Послідовність механічного сортування матеріалу залежить від розміщення сит і решіт. Розрізняють три схеми розміщення решіт: «від дрібного до крупного», «від крупного до дрібного», комбінована схема.
Просіювання вихідного матеріалу за схемою «від дрібного до крупного» починають з решета із найменшими отворами, продовжують на решетах із щораз більшими отворами і закінчують на решеті з найбільшими отворами (рис. 2.1).
Вихідний
матеріал
12 мм
25 мм
50 мм
+50 мм
12—0 мм
25—12 мм
50—25 мм
Рис. 2.1
Розміщені за цією схемою сита зручно ремонтувати, а також знімати з них готовий продукт. Однак якість просіювання погіршується через стирання крупного матеріалу.
32
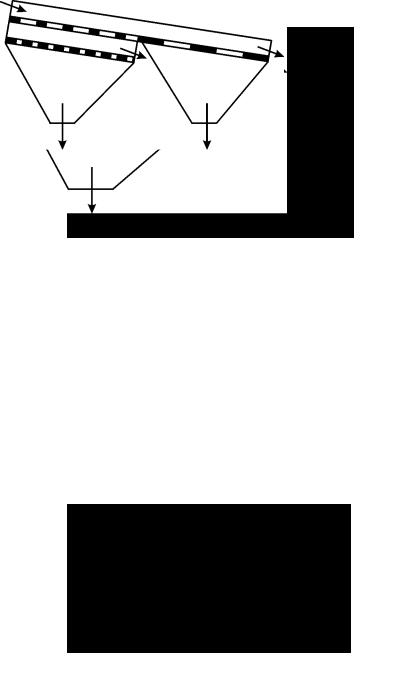
У схемі просіювання «від крупного до дрібного» верхнє сито має найбільші отвори, а нижнє — найменші (рис. 2.2).
Вихідний
матеріал
50 мм
25 мм
12 мм
+50 мм 50—25 мм
25—12 мм
12—0 мм Рис. 2.2
Недоліки схеми — велика висота установлення і вузький фронт розвантаження сортів.
У процесі просіювання за комбінованою схемою суміш надходить спочатку на решето з отворами середнього розміру. Шматки, які пройшли через отвори в першому решеті, надходять на розміщене під ним решето із найменшими отворами, тоді як шматки великих розмірів надходять на друге решето із найбільшими отворами (рис. 2.3). Ця схема поєднує в собі недоліки і переваги двох перших схем.
Вихідний матеріал
25 мм |
50 мм |
12 мм |
+50 мм
25—12 мм
12—0 мм |
50—25 мм |
Рис. 2.3
Усі частинки матеріалу, що пройшли через отвори в ситі, являють собою продукт нижнього класу, а всі частинки великого розміру, що не пройшли через сито, — продукт верхнього класу.
Показником ефективності сортування може слугувати відношення кількості продукту нижнього класу, отриманого у процесі просіювання,
33

до фактичної кількості частинок у вихідному продукті, розмір яких менший за розмір отвору в ситі. Звідси коефіцієнт якості просіювання:
η= АА1 100 %,
де А1 — кількість частинок нижнього класу, що пройшли через сито; А — кількість частинок нижнього класу у початковому продукті.
Коефіцієнт якості просіювання чи ККД грохоту залежить від конструкції установки, її кінематики, гранулометричного складу матеріалу, вологості матеріалу.
Пристрої для механічного сортування матеріалу називають грохотами. Грохоти поділяють:
—за принципом дії (на нерухомі і рухомі);
—за орієнтацією в просторі (на похилі і горизонтальні);
—за видом руху робочих органів (на обертові, хитні, гіраційні і вібраційні);
—за видом поверхонь для просіваюння (плоскі листові, дротяні і колосникові, а також барабанні).
2.1.1. Гіраційні грохоти
Гіраційні грохоти — це машини, у яких поверхня для просіювання робить коловий плоскопаралельний рух.
Розрахування швидкостей грохота. Розгляньмо умову підкидання шматка матеріалу на поверхні для просіювання (рис. 2.4). Аналіз схеми дії сил показує, що в квадрантах I і IV матеріал може підкидатися вгору, у I і II — рухатися вправо, у III i IV — уліво. Запишемо умови підкидання:
Iн > G cos α,
тобто нормальна складова сили інерції, що дорівнює Isinγ, більша від нормальної складової сили тяжіння частинки G. Підставивши значення сили інерції, одержимо
G |
4π2n2r sin γ > G cos α, |
(2.1) |
|
g |
|||
|
|
де r — радіус кривошипа; γ — кут розміщення кривошипа. Максимальна висота підкидання буде, якщо γ = 90°, тобто sinγ = 1, і з
(2.1) дістанемо:
n |
> |
1 |
|
g cos α. |
|
підк |
|
2π |
|
r |
|
34
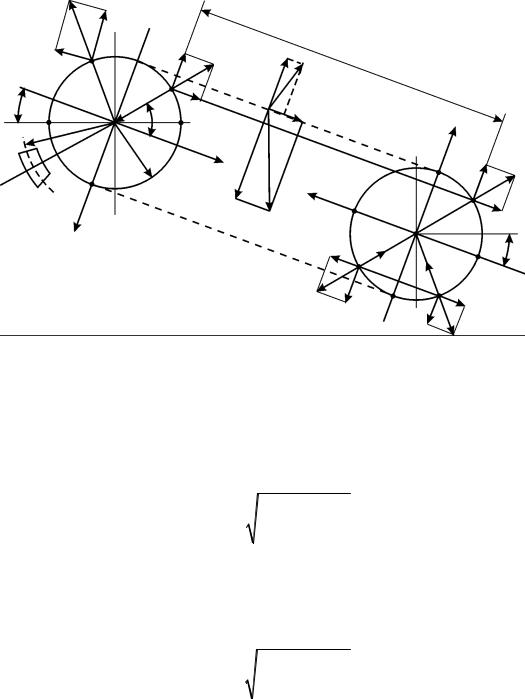
|
|
I |
Iн |
|
|
|
|
|
|
|
|
|
|
|
|
Iт |
|
|
6 |
Iн |
I |
Iн |
l |
|
|
|
|
|
|
|
|
|
|
|
|
|
|
|
||||||
|
|
|
B |
|
|
I |
|
|
|
|
|
|||
|
|
|
|
|
|
|
|
|
|
|
||||
|
|
|
|
B |
|
|
|
|
|
|
|
|
|
|
α |
|
|
O1 |
a |
|
|
|
Gsinα |
|
|
|
|
|
|
0 |
|
γ |
|
Iт |
|
I |
|
|
|
|
||||
|
r0 |
|
|
|
r |
|
12 |
|
|
|
|
|
|
|
|
|
|
|
|
|
I |
|
|
6 |
|
|
|
|
|
|
|
|
|
|
|
|
|
|
Iн |
|
|
|
||
|
|
|
|
|
|
|
|
|
|
I |
|
|
||
|
|
18 |
|
|
|
|
Gcosα |
|
I |
|
|
|
||
C0 |
R |
|
|
|
|
|
|
|
|
|
||||
|
|
|
|
G |
0 |
|
B Iт |
|
|
|
||||
|
|
|
|
|
|
|
|
O2 |
|
|
|
|
||
|
|
|
|
|
|
|
|
|
Iт a |
a |
12 |
α |
|
|
|
|
|
|
|
|
|
|
|
|
|
|
|
||
|
|
|
|
|
|
|
|
|
I |
|
|
|
|
|
|
|
|
|
|
|
|
|
|
|
|
|
|
|
|
|
|
|
|
|
|
|
|
|
Iн 18 |
|
Iт |
|
|
|
|
|
|
|
|
|
|
|
|
Iн |
|
I |
|
|
|
|
|
|
|
|
|
|
|
|
|
|
|
|
|
|
|
|
|
|
|
|
|
|
Рис. 2.4 |
|
|
|
|
|
|
Умова руху матеріалу вниз |
|
|
|
|
|
|
|
|||||||
|
|
|
|
|
Iτ < f (G cosα − In ) −G sin α, |
|
|
(2.2) |
Розв’язуючи (2.2) для випадку, коли γ = 0, тобто cos γ = 1, одержимо розрахункову залежність для визначення швидкості
n |
> |
1 |
|
g sin(ϕ− α) |
. |
2π |
|
||||
вн |
|
|
r cos ϕ |
Умова руху матеріалу вгору
Iτ > F + G cos α
дає значення швидкості
n |
> |
1 |
|
g sin(ϕ+ α) . |
|
вг |
|
2π |
|
r cos ϕ |
|
Потужність урухомника грохота витрачається на подолання сил тертя
вцапфах, зумовленого силами інерції і силами тяжіння. Робота сил тертя
вцапфах
A = A1 + A2 = M ω2r2πrц f + 2 fMgπrц = 2πMfrц(ω2r + g),
де М — маса завантаженого грохота; ω — обертова частота вала урухомника; r — ексцентриситет; rц — радіус цапфи.
35

Потужність урухомника, кВт:
N = 1000Anη,
де η — ККД урухомника.
На рис. 2.1 наведено схему нестійкої конструкції грохота. Різновид традиційних грохотів — грохоти на похилих гнучких стояках (рис. 2.5).
|
Iн |
I |
|
|
|
F |
|
Iт |
|
|
|
|
G |
2 |
r |
|
1 |
α |
|
3 |
α |
|
4 |
|
Рис. 2.5
Розрахування швидкостей грохота. Умова підкидання матеріалу
(рис. 2.5)
|
Iн > G, |
|
|
||||
звідки |
|
|
|
|
|
|
|
n |
> |
1 |
|
|
g |
. |
|
2π r sin α |
|||||||
підк |
|
|
Якщо матеріал рухається вправо,
Iτ > f (G − Iн).
Тоді швидкість
n |
> |
1 |
|
fg |
. |
2π |
|
r(cos α + f sin α) |
|||
впр |
|
|
|
Якщо матеріал рухається вліво,
Iτ > f (G + Iн).
36
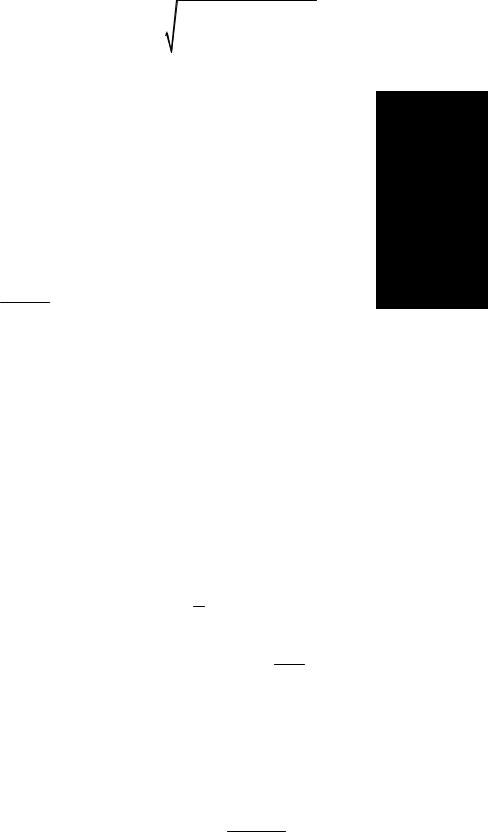
Тоді швидкість
n |
> |
1 |
|
fg |
. |
2π |
|
r(cos α − f sin α) |
|||
вл |
|
|
|
Для зрівноважування грохотів стояки защемляють жорстко, роблячи їх пружинними. Зрівноважування грохота на похилих пружинних, жорстко затиснених стояках зводиться до розрахунку цих стояків на міцність (рис. 2.6).
Вимоги до розрахування стояка:
—стояк має працювати на ділянці пружних деформацій за умови
I1 = P2,
де I1 = M ωi 2r — сила інерції; М — маса заванта-
женого грохота; ω, r — відповідно обертова частота і радіус кривошипа; i — кількість стояків;
I1 P
r r
l
r/2
Рис. 2.6
—зрівноважування визначають за певної обертової частоти. Розрахування стояка подібне розрахуванню пружинної опори. Стояк розглядають як дві консольні балки з величиною прогину
f |
= |
r |
= |
1 |
|
|
P(1/ 2)3 |
= |
Pl |
, |
||
|
3 |
|
24EI |
|||||||||
|
2 |
|
|
|
EI |
|
|
|||||
де l — довжина стояка; I = |
ab3 |
— момент інерції перерізу стояка. |
||||||||||
12 |
||||||||||||
|
|
|
|
|
|
|
|
|
|
Згинальний момент
Mзг = P 2l =[σ]зг W ,
де [σ] — межа міцності на згинання; W = ab62 — момент опору.
Вибирають співвідношення розмірів a/b = x, що дорівнює 8…12. У результаті розв’язання наведених вище рівнянь одержимо значення розмірів стояка (b, a, l).
Потужність урухомника витрачається:
— на надання кінетичної енергії хитним масам
N1 = MV 2n = M ω3rπ2 , 2000
37

— на деформацію стояків
|
|
Eab3r2 |
ω |
|
N2 |
= |
|
i |
. |
|
|
|||
|
|
2000πl3 |
Оптимальна продуктивність грохотів — це максимальна продуктивність грохота за заданого коефіцієнта корисної дії. За методом транспортера масова продуктивність
Пρ = 3600BDcp′ ρµV ,
де V — швидкість переміщення насипного вантажу з максимальним розміром шматка по поверхні, через яку просіюють:
V ≤ D2cp′′ (1− tg α) g cos α/ D2cp (1− tg α)sin 2α + Dcp′′ ,
де D''cp — розмір нижньої фракції; α — кут нахилу сита; µ — коефіцієнт розпушення матеріалу на ситі.
2.1.2.Вібраційні грохоти
Увібраційних грохотах коливання сита зумовлюють динамічні фактори — інерційні, ударні чи електромагнітні сили. Вібраційний грохот має такі особливості:
—траєкторія сита визначається динамічними факторами;
—амплітуда коливань змінна.
Залежно від конструкції пристрою, що спричиняє вібрації сита, віб-
раційні грохоти поділяють на інерційні, ударні, електричні.
Вібраційні інерційні грохоти застосовують для класифікації порошків. Інерційний грохот відрізняється від гіраційного конструкцією механізму, який забезпечує вібрацію рухомого жолоба, установленого на пружинах.
Ефективність просівання, %:
|
А− А |
|
100, |
|
Е = С − |
1 |
(100 −С) |
||
А1 |
||||
|
|
|
де С — зміст фракцій нижнього класу у вихідному материалі, %; А — маса відібраної проби верхнього продукту просівання, кг; А1 — маса проби верхнього продукту після відсівання з неї зерен нижнього класу, кг.
Значення Е можна визначити і як середнє значення з розсіву не менш трьох проб, відібраних у різний час роботи грохота:
E = lK1K2K3, |
(2.3) |
де l — еталонне значення ефективності просівання; K1 — коефіцієнт, що враховує кут нахилу грохота; K2 — коефіцієнт, що враховує відсотковий
38
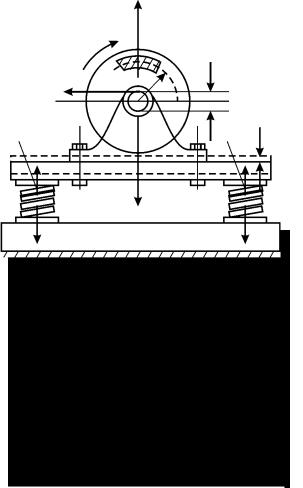
уміст нижнього класу у вихідному матеріалі; K3 — коефіцієнт, що враховує відсотковий уміст у нижньому класі зерен, менших за половину розміру отворів сита. Продуктивність грохота, м3/год:
ПV = mgFK1′K2′K3′,
де т — коефіцієнт, що враховує можливу нерівномірність живлення і зернового складу матеріалу, форму зерен і тип грохота (для горизонтального грохота т = 0,8…0,65; для похилого т = 0,5…0,6); g — питома продуктивність сита площею 1 м2; F — площа сита, м; K'1, K'2, K'3 — коефіцієнти, фізичне значення яких відповідає коефіцієнтам з формули (2.3).
Потужність, споживана інерційним грохотом, кВт:
= 4 fmπ3n3rd
Nдв η ,
де f — зведений коефіцієнт тертя кочення підшипників, що дорівнює 0,01…0,0025; m — маса дебаланса, кг; n — обертова частота вала, с–1; r — відстань від центра ваги неврівноваженої частини дебаланса до осі обертання, м; d — діаметр цапфи вала, м; η — КKД грохота.
Розрахування вібратора. На систему (рис. 2.7) діють сили тяжіння вібрувальних мас М та інерції дебаланса, радіус якого ro і маса m. На одну пружину (якщо грохот чотирипружинний) діє зусилля, що дорівнює Mg/4, і сила інерції I/4.
|
|
|
|
G'0 |
|
|
|
|
|
|
f0P0 |
G0 |
P |
|
|
|
|
|
|
r0 |
|
|
|
|
||
|
I0/4 |
E |
O |
|
I0/4 |
S |
|
|
|
|
|
|
|
|
|
||
A |
|
|
|
|
|
|
A |
|
|
|
|
|
G |
|
|
|
|
|
B G/4 |
|
B |
|
|
|
|
|
|
|
|
G/4 |
|
||||
|
|
|
|
|
|
|
|
|
|
|
|
|
|
|
|
|
|
Рис. 2.7
Навантаження на пружину від дії сили тяжіння
M g |
= ak, |
(2.4) |
|
4 |
|||
|
|
де а — статичне осідання, м; k — жорсткість, Н/м.
39
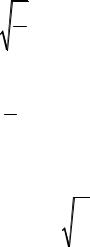
Період вільного коливання грохота
Tв = 2π ag .
Період вимушеного коливання грохота
Tвим = 1n ,
де n — обертова частота дебалансного вала. Під час резонансу
Т |
вим |
=T , тобто 1 |
= 2π |
a |
. |
|
|
||||||
|
в |
n |
|
g |
||
|
|
|
|
Підставивши значення а з рівняння (2.4), одержимо значення жорсткості пружини для умов резонансу:
|
|
k = π2Mn2. |
(2.5) |
||
За цією жорсткістю підбирають пружини. |
|
||||
Значення жорсткості пружини з умови дії сил інерції |
|
||||
|
I |
|
mω2r |
|
|
|
|
= kR = |
o |
, |
|
4 |
4 |
|
|||
|
|
|
де R — половина амплітуди коливання системи; m — маса дебалансу; ro — радіус дебалансу.
Звідки
k = |
π2n2mr |
(2.6) |
o . |
||
|
R |
|
З рівності співвідношень (2.5) і (2.6) випливає
MR = mro,
що дозволяє розрахувати масу дебалансу.
2.1.3. Барабанні грохоти
Барабанні обертові грохоти застосовують для сортування всіляких сипучих матеріалів.
Основна перевага барабанних грохотів — повільне і рівномірне обертання, що дає можливість установлювати їх на верхніх поверхах виробничих будівель, у пересувних установках. Недолік барабанних грохотів — значне запилення під час сухого просіювання і невелика робоча поверхня сита (12…20 % усієї поверхні сита).
40