
9
.pdf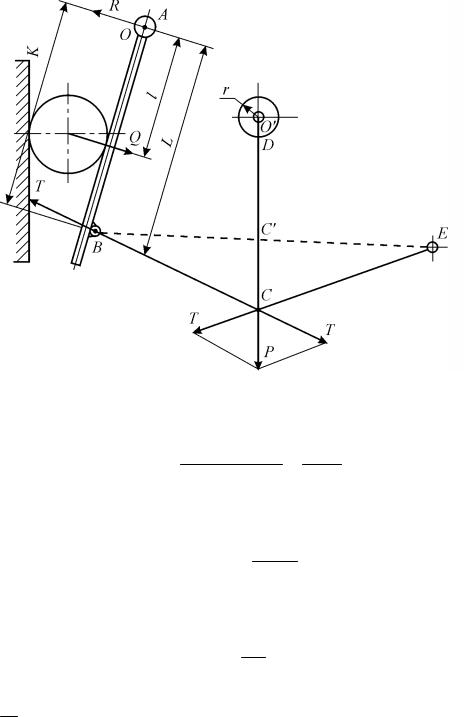
На рис. 1.8 позначено: центр обертання щелепи — O; r — радіус кривошипа; L — плече дії зусилля Т; l — плече дії зусилля Q; K — плече дії реакції R.
Рис. 1.8
Середнє значення максимального зусилля за один хід щелепи:
Qср = О+ Qmax + О = Qmax .
2 2
Робота роздавлювання на шляху ходу щелепи S
А= QсрS = Qmax2 S;
звідки знаходимо зусилля роздавлювання:
Q = 2SA ,
де A = Nn , кДж.
11
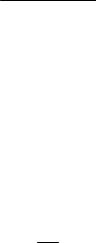
Тоді
|
2σ2П (i −1) |
|
Q = |
V |
(1.3) |
2,4nES . |
За відомим значенням Q визначають основні зусилля, що діють у вузлах машини. Щоб спростити розрахунок, припускаємо рівність кутів β1 і β2 і вважаємо, що в цьому випадку шатун СD займає вертикальне положення.
Зусилля Т визначаємо із суми моментів відносно точки О: ∑MO = −Ql +TL = 0,
звідки
T = QlL .
З паралелограма сил, прикладених у точці С, визначаємо зусилля Р в шатуні СD:
P = 2T cosβ,
де β — кут між розпірною плитою і шатуном. Реакцію R визначаємо із суми моментів у точці В:
∑MB =Q(k −l) − Rk = 0,
звідки
R = Q(kk−l) .
Графічний метод. Щоб розрахувати зусилля у щелепній дробарці з простим коливанням рухомої щелепи, аналітично визначаємо значення зусилля Q за формулою (1.3) і в масштабі відкладаємо від центра шматка матеріалу, який вважаємо кулею, перпендикулярно до рухомої щелепи та продовжуємо лінію дії сили (рис. 1.9). Проводимо вісь розпірної плити до перетинання з лінією дії зусилля Q. Будуємо паралелограм сил, попередньо провівши лінію дії реакції R на підвіску рухомої щелепи. Таким чином одержуємо величину і напрямок реакції R.
Переносимо в масштабі зусилля R і Т в точки їх прикладання і будуємо паралелограм сил у точці С. Одержуємо зусилля, що діє в шатуні, і зусилля, що діє в другій плиті.
Для дробарки зі складним коливанням щелепи відкладаємо в масштабі зусилля Q під кутом 90° до рухомої щелепи (рис. 1.10).
12
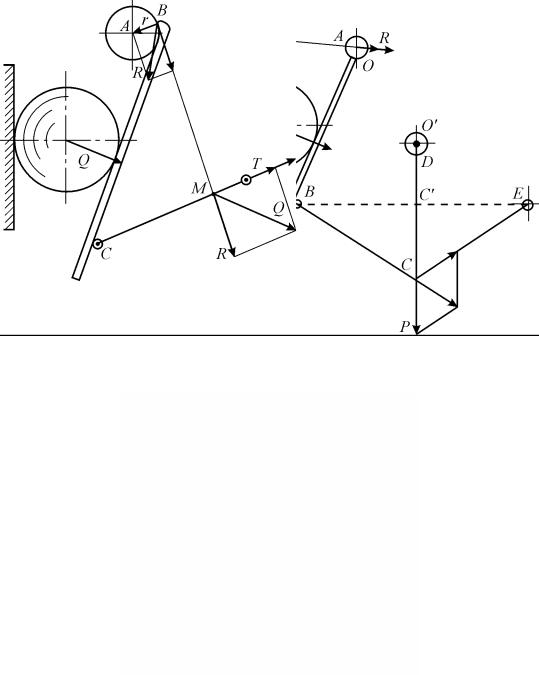
S
Рис. 1.9
Рис. 1.10
Продовжуємо лінію розпірної плити СD до перетинання з лінією дії сили Q і отриману точку М з’єднуємо з точкою В. Будуємо паралелограм сил, у результаті одержимо зусилля R і Т (Т — сила розпірної плити СD; R — сила тиску на вісь підвіска рухомої щелепи). Переносимо дію зусилля R у точку В і розкладаємо на складові. Перша складова Р спрямована по дотичній до точки В. Друга складова — зусилля S — спрямована до центра обертання. Зусилля S діє на ексцентриковий вал і на підшипники. Тангенціальна сила Р розвиває момент Рr, який чинить опір обертанню вала дробарки.
13
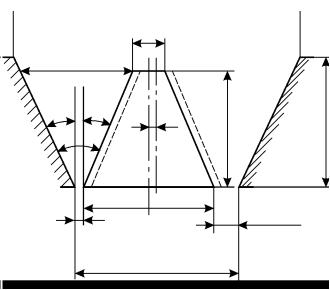
1.2.2. Конусні дробарки
Конусні дробарки застосовують для дроблення всіляких порід, за винятком в’язких і дуже твердих.
У конусних дробарках шматки матеріалу роздавлюються між зовнішнім і внутрішнім конусами у результаті натискання внутрішнього конуса на матеріал. Конус при цьому переміщається по коловій траєкторії, коливаючись щодо нерухомої точки (гірації). Під час зближення конусів матеріал дробиться, а під час віддалення — вивантажується. Конусні дробарки класифікують за такими ознаками:
а) технологічним призначенням: дробарки крупного дроблення
(Dср = 0,3…1,5 м; dср = 0,05…0,2 м, де Dср, dср — середній розмір відповідно завантажуваного і вивантажуваного шматка); дробарки середнього
дроблення (Dср = 0,075…0,3 м; dср = 0,015…0,05 м); дробарки дрібного і середнього дроблення (Dср = 0,03…0,075 м; dср = 0,003…0,015 м);
б) конструктивним оформленням: дробарки з підвішеним валом, дробарки ексцентрикові, дробарки з консольним валом.
Кут захоплення дробарки з крутим конусом визначають так само, як і для щелепної дробарки (рис. 1.11):
α1 + α2 ≤ 2ϕ.
Dв
dв
a
α1 |
α2 |
r |
α
e dн
Dн
Рис. 1.11
H |
H |
|
1 |
e + s
Визначення обертової частоти рухомого конуса. У конусній дро-
барці з крутим конусом за один оберт випадає об’єм матеріалу, який до того був між двома конусами (рис. 1.12, 1.13).
14
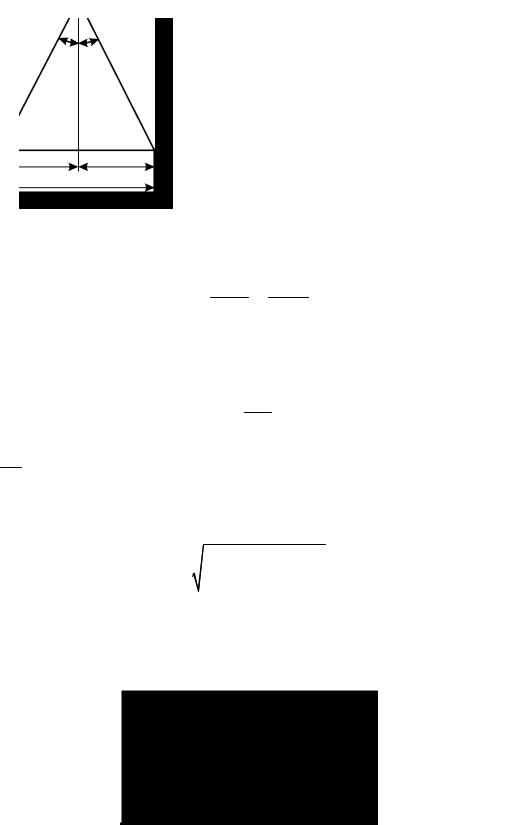
α1 α2
h
s1 s2 s
Рис. 1.12
α
α1 α2
h
e |
e s |
dн |
|
Dср |
|
Рис. 1.13 |
|
Висоту шару матеріалу, що випадає з дробарки, визначають так:
R = tgSα1 1 = tgSα2 2 ,
де S1 + S2 = S.
Шлях матеріалу, що вільно випадає,
h = gt2 , 2
де t = 21n .
З огляду на тертя між шматками матеріалу і конусом остаточно одержимо
n = |
(tg α1 |
+ tg α2 )g |
, |
|
8S |
||
|
|
|
де S = 2r ≈ 1,3dср; r — ексцентриситет, м.
Щоб визначити обертову частоту конусної дробарки з положистим конусом, розглянемо поводження матеріалу в зоні паралельності (рис. 1.14).
I |
In |
|
|
fGcosγ |
|
||
|
Gsinγ |
Gcosγ |
γ |
|
Iτ |
|
|
|
|
|
|
|
|
G |
|
|
|
Рис. 1.14 |
|
|
|
|
15
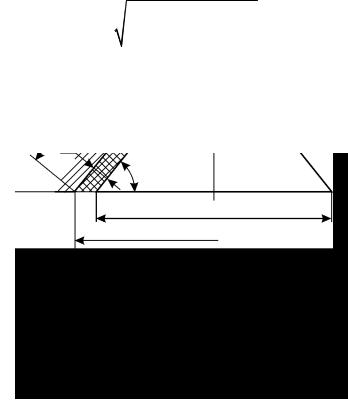
Силу, що рухає матеріал Р, визначають так:
P = G sin γ −Gf cos γ = ma, |
(1.4) |
де G = mg; m — маса шматка; a — прискорення руху шматка. Розв’язуючи рівняння (1.4) щодо прискорення, одержуємо
a = g(sinγ – fcosγ).
Тоді шлях шматка, що дорівнює довжині зони паралельності, визначають так:
|
at2 |
|
1 2 |
|
|
L = |
2 |
= g(sin γ − f cos γ) |
|
. |
(1.5) |
|
|||||
|
|
2n |
|
Розв’язуючи рівняння (1.5) щодо обертової частоти n, одержуємо
n = |
g(sin γ − f cos γ) |
, |
|
2L |
|||
|
|
де γ — кут між твірною і основою рухомого конуса, γ = 40…45°; f — коефіцієнт тертя; L = 0,08dн; dн — нижній діаметр рухомого конуса, м (рис. 1.15).
Dв
dв
L = 0,08dн
H
e
γ = 41°
dн
Dср
Рис. 1.15
Визначення продуктивності. Площу перерізу об’єму, що випадає, для дробарки з крутим конусом визначають (див. рис. 1.13) так:
F = |
e + e + S |
h = dсрh = dср |
S |
|
. |
|
tg α + tg α |
|
|||
2 |
|
2 |
|
||
|
|
|
1 |
|
16

За один оберт випадає об’єм матеріалу
V = FµπD1,
де µ — коефіцієнт розпушення матеріалу; D1 ≈ Dн — нижній діаметр нерухомого конуса.
Масова продуктивність
Пρ = 3600Vnρ = 3600dнdсрµSρn , tg α1 + tg α2
де лінійні розміри виражено в метрах. Для дробарки з положистим конусом
F = Le = 0,08dне.
Тоді
Пρ = 3600Vnρ = 288dн2ndсрµρπ.
Потужність дробарок визначають за формулою (1.2), якщо ηд = 0,2…0,3.
1.2.3. Валкові дробарки
Валкові дробарки широко застосовують у хімічній промисловості для подрібнювання матеріалів середньої і малої міцності, вторинного дроблення твердих і крихких порід.
Залежно від фізико-механічних властивостей подрібнюваного матеріалу і технологічного призначення продукту дроблення використовують валки з різною робочою поверхнею: гладкою, рифленою, зубчастою чи ребристою.
Валкові дробарки бувають: із зубцюватими валками; каменевідбірні; з гладкими валками для попереднього й остаточного дроблення; з дірчастими валками; одновалкові; для брикетування; комбіновані. Продуктивність валкових дробарок досягає 100 м3/г, ступінь подрібнювання 4…15.
Кут захоплення. Для визначення кута захоплення валкової дробарки розглянемо рис. 1.16.
Для того щоб шматок матеріалу був втягнутий між валками, потрібно, щоб
2Pfcosα ≥ 2Psinα.
Дістанемо
β ≤ 2α ≤ 2ϕ.
17
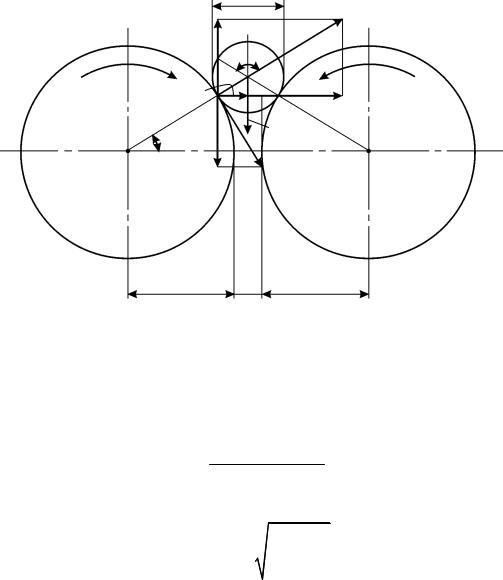
|
|
2r |
P |
|
|
|
|
|
Psinα |
|
|
|
|
β |
|
|
fPsinα |
|
|
|
|
|
Pcosα |
A |
α |
|
G |
|
B |
||
O1 |
fPcosα |
|
O2 |
2e R
Рис. 1.16
Співвідношення між розмірами валків і шматків подрібнюваного матеріалу визначаємо за рис. 1.16:
D + 2e = (D + Dср)cosα,
звідки
D = Dср cos α − 2e . 1 − cos α
Критичну обертову частоту валків визначаємо за формулою Левенсона, с–1:
nкр = 0,32 |
f |
, |
|
ρDDср |
|||
|
|
де ρ — об’ємна маса матеріалу, т/м3; Dср — середній діаметр шматків на вході, м; D — діаметр валка, м.
На практиці розрахункову обертову частоту варто зменшувати на
20—35 %.
Визначення продуктивності. Площа перерізу вихідної стрічки матеріалу дорівнює F = L·2e. З урахуванням швидкості стрічки і ступеня розпушення матеріалу в стрічці продуктивність, т/г,
Пρ = 3600πDnLeµl,
де L — довжина валків, м; е — ширина щілини, м; µ — коефіцієнт розпушення, який застосовують для в’язких вологих матеріалів, µ = 0,5…0,6.
Потужність валкових дробарок визначають за формулою (1.2), якщо
ηg = 0,25.
18

1.2.4. Молоткові дробарки
Молоткові дробарки застосовують для подрібнювання крихких матеріалів з невеликою вологістю.
Подрібнювання в молотковій дробарці відбувається внаслідок:
—удару швидкообертових молотків безпосередньо по шматках матеріалу й удару шматків один об один;
—удару матеріалу об дробильні плити;
—подрібнювання матеріалу між молотками і броньовими плитами;
—подрібнювання матеріалу між молотками і колосниками.
На підставі конструктивних ознак молоткові дробарки поділяють за кількістю роторів на однороторні і двороторні, за способом кріплення молотків — із жорстко закріпленими і шарнірнопідвішеними молотками, за розміщенням молотків — однорядні й багаторядні. Продуктивність молоткових дробарок залежно від розмірів машини і шматків, що надходять до неї, ступеня подрібнювання і твердості матеріалу коливається в межах від 3 до 250 т/г.
Розрахування параметрів ротора. Довжина молотка
Lм = (0,4...0,5) D2р ,
де Dp — діаметр ротора, м.
Швидкість молотка після удару визначають з рівняння динамічної рівноваги (рис. 1.17):
V g(M |
0 |
+ |
IA |
+ m) = ω g( |
l1IA |
− ml |
) + |
IAωк |
+V gM |
0 |
+ mgV |
; |
||||||||||||||
|
|
|
|
|
||||||||||||||||||||||
1 |
|
|
R2 z |
|
1 |
R2 z |
2 |
|
|
Rz |
к |
|
|
шм |
||||||||||||
|
|
|
|
|
|
|
|
|
|
|
|
|
|
|
|
|||||||||||
|
|
l2 I |
A |
|
+ l2m) =V g |
|
l I |
A |
|
|
|
|
|
l I |
A |
ω |
|
|
|
|||||||
ω g(i + |
1 |
|
( |
1 |
|
− ml |
2 |
) + iω − |
1 |
|
o |
|
+ mgV l |
, |
||||||||||||
|
|
|
|
|
|
|
|
|
||||||||||||||||||
1 |
|
|
R2 z |
2 |
1 |
|
R |
2 z |
|
|
o |
Rz |
|
k 2 |
|
|||||||||||
|
|
|
|
|
|
|
|
|
|
|
|
|
|
|
де V1 — колова швидкість центра ваги молотка після удару, м/с; М0 — маса молотка, кг; IA — момент інерції ротора, кг·м2; m — маса максимального розміру шматка подрібнюваного матеріалу, кг; z — кількість молотків; ω1 — кутова швидкість молотка після удару, 1/с; Vк = (R + + l1)ωк — колова швидкість центра ваги до удару, м/с; Vшм — швидкість шматка подрібнюваного матеріалу у напрямку колової швидкості ротора. За вертикального завантаження Vшм = 0.
Розрахування продуктивності молоткової дробарки. Продуктив-
ність молоткової дробарки визначають за емпіричною формулою, т/г,
Пρ = 6DpLp2n,
де Dp — діаметр ротора, м; Lp — довжина ротора, м; n — обертова частота, с–1.
19
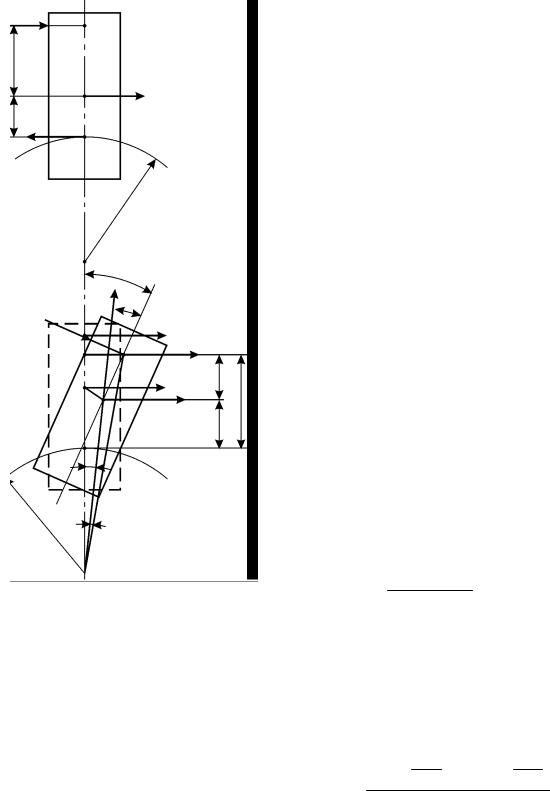
|
SD |
D |
|
|
|
|
|
|
|
|
|
2 |
|
|
|
|
|
l |
|
|
|
|
|
|
|
C |
U |
|
|
1 |
SB |
B |
|
|
|
l |
|
|
|
||
|
|
|
R |
|
|
|
|
A |
|
|
|
|
|
Pуд |
Pу |
|
|
|
|
|
V1 |
|
|
|
|
D |
|
V0 |
|
|
|
|
|
||
|
|
E |
D' |
V0 |
2 |
|
|
C C' |
|
V1l' |
|
|
|
|
|
1 |
|
|
|
B |
|
|
l' |
|
|
|
|
|
|
|
|
ψ |
|
|
|
|
|
R |
γ |
|
|
|
|
A |
|
|
|
Рис. 1.17
l3
Визначення потужності молоткової дробарки. У молотковій дробарці потужність витрачається на відновлення енергії, що втрачають молотки під час ударів по шматку матеріалу (N1) і стирання подрібнюваного матеріалу на колосникових ґратах (N2).
Потужність, потрібна для відновлення енергії, втраченої молотками під час ударів по шматку матеріалу, кВт,
N1 = A′y1zзагn.
Кінематична енергія, втрачена молотком під час ударів по шматку подрібнюваного матеріалу, Нм,
′ |
|
V 2 M m |
|
||
|
y1 |
1 0 |
|
||
Ay1 |
= |
|
|
, |
|
2(M1 |
+ m0 ) |
||||
|
|
|
де Vy′1 = (R + l1 + l2′)ω0 — швидкість молотка до моменту удару (у точці удару), м/с; l1 — відстань від осі обертання молотка до осі центра ваги, м; l′2 — відстань від осі центра ваги молотка до точки уда-
ру, м; m0 = Пρ 1000 — маса се-
3600 zзагn
реднього за продуктивністю шматка подрібнюваного матеріалу, що припадає на один молоток, кг.
Відстань
l1 + l2 = Lм – Сср,
де Lм — довжина робочої частини молотка; Сср = (Сmin D2ср ) + (Сmax D2ср ) — 2
середнє значення глибини проникнення матеріалу (точки зіткнення); Сmin = 0,6Dср — мінімальна глибина проникнення, Сmax < l — максимальна глибина проникнення.
20