
Методички / Курс деталей машин
.pdfглавному требованию. Ниже рассмотрены другие характеристики наиболее распространённых резьб.
NB 5.2. Минимальные углы профиля ходовых резьб обеспечивает
минимальный момент трения и максимально возможный КПД.
5.3.2. Метрическая резьба
Метрическая резьба имеет треугольный профиль с углом α = 60о (рис. 5.2).
Вершины витков и впадин притуплены по прямой или окружности для:
а) уменьшения концентрации напряжений;
б) предохранения от повреждений;
в) повышения стойкости инструмента.
ГОСТ 8724 предусматривает резьбы с крупным и мелкими шагами. Так, для диаметра d = 20 мм стандарт предусматривает крупную резьбу с шагом 2,5 мм и пять мелких резьб с шагами 2; 1,5; 1; 0,75; 0,5 мм. При уменьшении шага
уменьшается высота резьбы и угол подъёма, а внутренний диаметр d1
увеличивается. Это даёт следующие преимущества:
1)снижается концентрация напряжений вследствие уменьшения перепада диаметров соседних участков болта;
2)повышается усталостная выносливость вследствие снижения концентрации напряжений;
3)повышается статическая прочность вследствие увеличения минимального диаметра болта d1;
4)повышается технологичность вследствие уменьшения объёма металла,
снимаемого механической обработкой; 5) уменьшается возможность самоотвинчивания вследствие уменьшения
угла подъёма винтовой линии.
В общем машиностроении основное применение имеют крупные резьбы как наименее чувствительные к износу и ошибкам изготовления.
Геометрические параметры метрической резьбы приведены в прил. 11.
Обозначения резьб нормального класса точности:

а) с крупным шагом: М20.5.6,
где М – метрическая резьба; 20 – наружный диаметр резьбы d; 5.6 – класс прочности: цифра 5, умноженная на 100, даёт предел прочности σB в МПа, а
цифра 6, делённая на 10 – отношение σТ/σB (в ГОСТ 1759 предусмотрено 12
классов прочности, см. прил. 8);
б) с мелким шагом: М20×1,5.5.6,
где 1,5 – шаг резьбы.
Признаком левой резьбы является наличие в конце обозначения LH .
Материалы резьбовых деталей, их механические характеристики и классы прочности приведены в прил. 8.
5.3.3. Трубная резьба
Трубная резьба (рис. 5.5) применяется для герметичного соединения труб и арматуры. Особенности конструкции и обозначения:
1)резьба имеет мелкий шаг, так как на тонкой стенке трудно нарезать резьбу с крупным шагом;
2)резьба выполняется без зазоров между выступами и впадинами, и с закруглениями профиля для лучшего уплотнения;
3)угол профиля α = 55 о, как в дюймовой резьбе; в международном стандарте сохранено измерение диаметра в дюймах;
4)в обозначении указывают в дюймах диаметр отверстия трубы.
Параметры резьбы d , d1 и другие принимают из ГОСТ 6357. Обозначение резьбы: G 112 A ,
где А – класс точности.
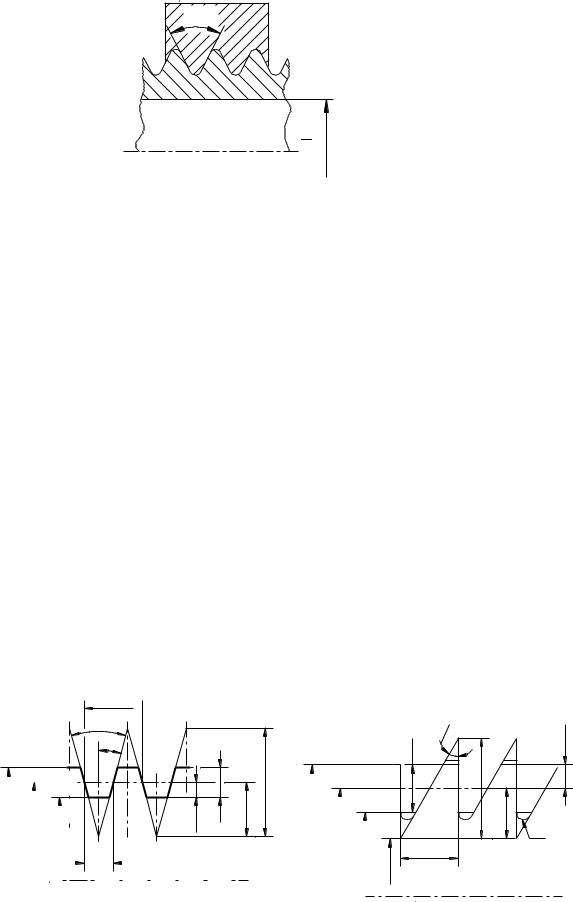
55° |
-A |
|
1 |
2 |
G1 |
Рис. 5.5. Трубная резьба
К крепёжным резьбам относятся также круглая резьба, применяемая для литых и пластмассовых и тонкостенных деталей, а также резьба винтов для дерева (шурупов).
5.3.4. Трапецеидальная резьба
Резьба трапецеидальная одно- и многозаходная (рис. 5.6) относится к
кинематическим резьбам и используется для передачи двухстороннего движения под нагрузкой. Угол симметричного профиля α = 30о. Другие параметры трапецеидальной резьбы приведены в прил. 10.
Обозначение резьбы: Tr 20 4 (Р2),
где 20 – наружный диаметр d, 4 – ход резьбы (Ph = 4 мм), 2 – шаг резьбы Р.
D |
|
|
|
|
|
|
|
|
|
D |
|
1 |
|
|
|
|
|||
|
|
|
|
|
|||||
d, |
2 |
|
D |
|
|
|
|
||
2 |
|
|
|
|
|
||||
|
|
|
|
|
|||||
|
, |
|
|
|
|
|
|
|
|
|
d |
|
1 |
|
|
|
|
||
|
|
|
|
, |
|
|
|
|
|
|
|
|
|
d |
|
|
|
|
|
|
|
|
|
|
|
|
|
||
|
|
|
|
|
|
|
|
|
|
|
|
|
|
|
|
|
|
|
|
P Гайка
30°
15°
|
|
H |
/2 |
1 |
H/2 |
1 |
H |
|
H |
P/2 |
|
|
|
Винт |
|||||||||
|
|
|
|
|
|
|
Ось резьбы |
||||||
|
|
|
|
|
|
|
|
|
|
|
|
|
|
, D |
2 |
|
|
|
|
|
|
||
d |
, D |
1 |
|
3 |
|
||||
|
d |
D |
|
|
|
2 |
|
|
d |
|
|
|
|
|
|
|
|
|
|
33° |
Гайка |
/2 |
|
|
|
|||
1 |
|
|
|
|
|
|
|
1 |
|
H |
|
|
|
H |
|
H |
|
|
|
|
|
H/2 |
R1 |
|
|
|
|
|
|
P |
|
Винт |
|
|
|
Ось резьбы |
Рис. 5.6. Трапецеидальная резьба |
Рис. 5.7. Упорная резьба |
Прямоугольная резьба (рис. 5.4), широко применяемая ранее, в настоящее время не стандартизирована и почти вытеснена трапецеидальной. Изготовить такую резьбу высокопроизводительными методами невозможно, так как для образования чистой поверхности у фрезы должны быть режущими не только передние, но и боковые грани. Прямоугольная резьба менее прочна, чем трапецеидальная.
5.3.5. Упорная резьба
Упорные резьбы обычно предназначаются для одностороннего движения под нагрузкой, поэтому имеют несимметричный профиль. Закругление впадин
(рис. 5.7) уменьшает концентрацию напряжений. Малый угол наклона (3о)
упорной стороны профиля резьбы ( на рис. 5.7 не показан) позволяет уменьшить потери на трение и в то же время изготовлять винты на резьбофрезерных станках.
Большой угол (α = 30о) с другой стороны повышает прочность витков и нагрузочную способность соединения. Параметры упорной резьбы приведены в прил. 11.
Обозначение резьбы аналогично трапецеидальной: S 20 4 (Р2).
5.4. Оценка соединения
Резьбовое соединение – единственная конструкция, не имеющая альтернативной, с которой можно её сравнивать. Используют объективные критерии оценки.
Достоинства:
1)высокая несущая способность и надёжность;
2)удобство сборки и разборки;
3)относительно малая стоимость, обусловленная стандартизацией;
4)наличие большой номенклатуры резьбовых деталей.
Недостатки:
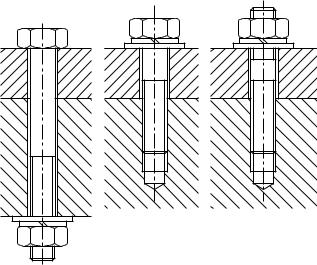
1)наличие значительной концентрации напряжений;
2)нетехнологичность некоторых специальных конструкций резьбовых деталей (см. п. 5.7.3).
5.5. Крёпежные детали
Наибольшее распространение среди резьбовых деталей получили крепёжные болты, винты, шпильки, гайки и шайбы (рис. 5.8). В зависимости от технологии изготовления различают болты и шайбы чёрные и чистые. Чёрные болты изготавливают штамповкой, их головки – высадкой, а резьба нарезается или накатывается. Чистые болты имеют гладкую поверхность стержня,
полученную на токарном станке.
a) |
б) |
в) |
Рис. 5.8. Крепёжные изделия Основным преимуществом соединения болтами является то, что не
требуется нарезать резьбу в соединяемых деталях (рис. 5.8, а), когда они имеют относительно небольшую толщину. Соединение позволяет многократную сборку и разборку. Однако обе соединяемые детали должны иметь места для расположения гайки или головки винта, что увеличивает массу изделия и ухудшает его внешние очертания. А при завинчивании гайки требуется удерживать головку винта от проворачивания.
Винты и шпильки (рис. 5.8, б, в) применяют в тех случаях, когда постановка болта невозможна или нерациональна. Например, когда нет места для размещения
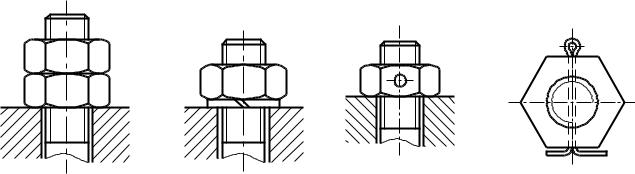
головки болта либо когда нет доступа к гайке (головке болта) при большой толщине изделий. Подкладную шайбу (рис. 5.8, а) ставят под гайку или головку болта (винта) для:
1)уменьшения смятия детали, если деталь изготовлена из менее прочного материала;
2)предохранения чистых поверхностей деталей от царапин при завинчивании;
3)перекрытия большого зазора отверстия.
В других случаях ставить простую шайбу нецелесообразно (ставят пружинную шайбу).
5.6. Способы стопорения
Крепёжные резьбы являются самотормозящими, так как угол подъёма резьбы больше угла трения. Однако при вибрациях, носящих систематический или случайный характер, резьбовые соединения часто «теряют» напряжение предварительной затяжки в результате смятия микронеровностей на рабочих поверхностях резьбы, а также из-за самоотвинчивания. Вибрация понижает трение и нарушает условие самоторможения в резьбе. На практике применяют три основных способа стопорения:
1) повышение трения в резьбе путем постановки контргайки, пружинной шайбы (рис. 5.9) и другими способами;
Рис. 5.9. Стопорение повышением трения |
Рис. 5.10. Постановка шплинта |
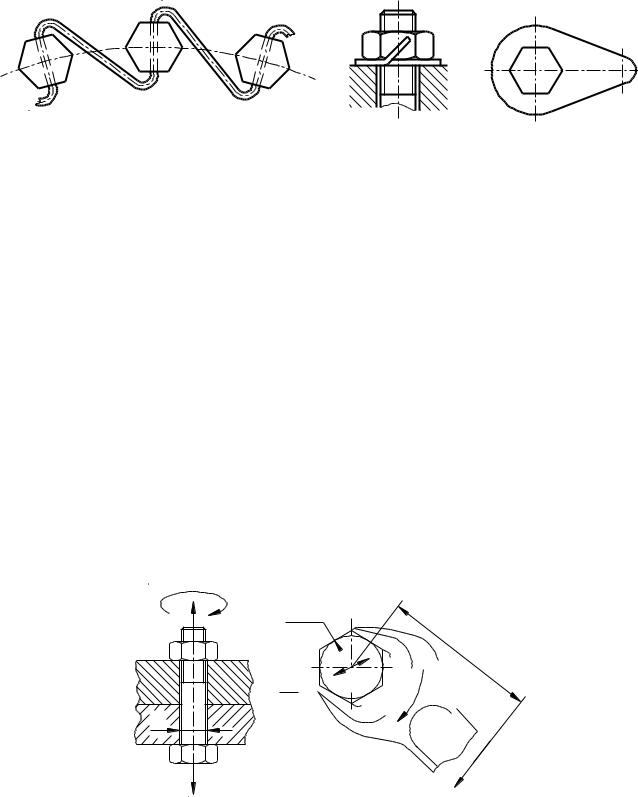
2) жёсткое соединение гайки со стержнем винта с помощью шплинта
(рис. 5.10) или соединение головок группы винтов проволокой (рис. 5.11);
Рис. 5.11. Стопорение проволокой Рис. 5.12. Стопорная планка
3) жёсткое соединение гайки с соединяемой деталью с помощью специальной шайбы или планки (рис. 5.12).
NB 5.3. Стопорение резьбовых деталей – необходимое условие безопасной работы машины.
5.7. Теория винтовой пары
5.7.1. Силовые соотношения и КПД
При нагружении винта осевой силой Fa (рис. 5.13) для завинчивания гайки к ключу необходимо приложить момент Тк, определяемый как сумма моментов
трения в резьбе Тр и на опорном торце гайки ТТ: |
|
Тк = Тр + ТТ. |
(5.5) |
F |
Tк |
а |
d0 |
Dк
d0
l
Tк
19
F |
Fк |
а |
|
Рис. 5.13. Схема к определению момента трения
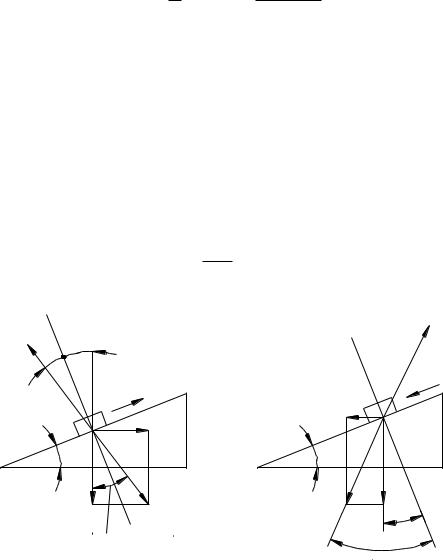
Для определения момента ТT |
принимают силу |
трения |
приложенной |
||||||||
посередине кольца, образованного |
отверстием под болт d0 |
и наружным |
|||||||||
диаметром гайки DК (размер под ключ). При этом |
|
|
|
||||||||
|
|
Т |
Т |
F |
f d |
F |
f DK d0 , |
|
|
(5.6) |
|
|
|
|
|
a |
2 |
a |
4 |
|
|
|
|
|
|
|
|
|
|
|
|
|
|
||
где Fa - осевая нагрузка; |
|
|
|
|
|
|
|
|
|||
f – коэффициент трения на торце гайки. |
|
|
|
||||||||
Момент трения в резьбе определяют, рассматривая гайку как ползун, |
|||||||||||
поднимающийся по виткам резьбы, как по наклонной плоскости. При |
|||||||||||
завинчивании (рис. 5.14, а), то есть при подъёме по наклонной поверхности, на |
|||||||||||
ползун кроме осевой силы Fa действует окружная сила Ft: |
|
|
|
||||||||
|
|
|
|
|
|
Ft 2TP . |
|
|
(5.7) |
||
|
|
|
|
|
|
|
d2 |
|
|
|
|
|
|
n |
|
|
|
|
|
|
|
|
|
|
R ' |
|
|
|
|
|
|
n |
R |
|
|
a) |
|
|
|
|
б) |
|
|
||||
|
|
|
|
|
|
|
|
|
|||
|
|
|
|
|
υ |
|
|
|
|
υ |
|
|
|
|
|
|
|
F |
|
|
|
||
|
|
|
|
|
|
|
|
|
|
|
|
|
|
|
|
|
|
Ft |
|
t |
|
|
|
|
|
|
|
|
|
|
|
|
|
|
|
|
|
|
|
|
|
|
|
|
|
|
|
|
|
F |
|
|
|
|
F |
|
F |
|
|
|
|
а |
|
|
Fn |
|
n |
|
а |
n |
|
|
|
|
|
|
|
|
|
|
|
||
|
|
' |
|
n |
|
|
|
||||
|
|
|
|
|
|
' |
|
||||
|
|
|
|
|
|
|
|
|
|
|
|
|
|
Рис. 5.14. Силы в резьбовой паре |
|
|
|
Реакция R , действующая на ползун, направлена противоположно равнодействующей Fn сил Fa и Ft и отклоняется от нормали к наклонной поверхности на угол трения в сторону, противоположную движению ползуна.
Из прямоугольного треугольника находят:
Ft Fa tg( ) . |
(5.8) |
С учетом формулы (5.7) находят момент трения в резьбе при завинчивании:
TPЗ |
1 |
|
(5.9) |
|
|||
2 Fаd2tg ( ) . |
Момент на ключе при завинчивании с учётом формулы (5.5):
|
|
|
dcp |
1 |
|
|
|
|
|
TК Fа f |
2 |
|
2 |
Fа d2tg ( ) FK |
l . |
(5.10) |
|||
При отвинчивании гайки окружная сила Ftо |
и силы |
трения |
меняют |
||||||
направление (рис. 5.14, б). При этом получают: |
|
|
|
||||||
|
Ftо Fа tg( ) . |
|
|
(5.11) |
|||||
Момент трения в резьбе при отвинчивании определяют из формул (5.7) и |
|||||||||
(5.11): |
|
|
|
|
|
|
|
|
|
1 |
|
|
|
) . |
|
|
(5.12) |
||
|
|
|
|
|
|
||||
|
|
|
|
|
|
||||
TPО 2 Fаd2tg ( |
|
|
Если ψ < φʹ, то сила Ft направлена влево, как на рис. 5.14, б. При ψ > φʹ гайка отвинчивается без приложения внешних сил, а Ft – это сила, которую необходимо приложить, чтобы удержать гайку от самоотвинчивания.
NB 5.5. При затяжке болтового соединения стержень винта не только
растягивается силой Fа , но и скручивается моментом ТРЗ.
Формула (5.12) позволяет рассчитать отношение осевой силы винта к силе,
приложенной на ручке ключа FK. Для метрических резьб при стандартной длине ключа l 15d (рис. 5.13) и коэффициенте трения f = 0,15 отношение Fа/FK = 70
…80. Следовательно, рабочий, приложив к ключу силу в 200 Н, создает осевое усилие в 15 кН.
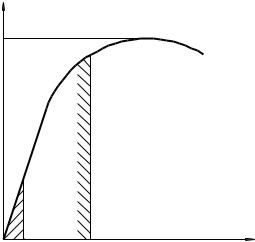
Лекция №6
5.7.2. Самоторможение и КПД
Условие самоторможения в резьбе можно записать в виде ТРО > 0. Из формулы (5.11) следует:
tg( ) 0 или ψ < φʹ. |
(5.13) |
Условие ψ < φʹ называют условием самоторможения резьбы. В метрической резьбе с крупным шагом это условие выполняется, так как угол подъёма ψ = 2,5…3,5º, а приведенный угол трения φʹ = 6…16º при fʹ = 0,1…0,3. Поэтому все крепёжные резьбы самотормозящие. Это, однако, не значит, что резьбовые соединения не нуждаются в стопорении (см. п. 5.6).
NB 5.6. В самотормозящей резьбе угол подъёма резьбы больше угла
трения.
КПД винтовой пары вычисляют по отношению работы, затраченной на завинчивание гайки без учета трения, к той же работе с учетом трения:
А = ТРЗ . (5.14)
Так как углы поворота гаечного ключа в обоих случаях одинаковы, то отношение работ равно отношению моментов, то есть
|
|
|
tg |
|
|
|
|
TРЗ |
|
|
. |
(5.15) |
|
|
|
|
||||
Т РЗ |
|
tg( |
) |
|
Анализ формулы (5.15) показывает, что при увеличении угла подъёма
числитель и знаменатель сближаются и КПД винтовой пары повышается, что представлено на графике (рис. 5.15).
|
|
|
0,75 |
|
|
4 |
20...25 |
o |
Рис. 5.15. График зависимости КПД от угла подъёма