
Методички / Курс деталей машин
.pdf
где – определяемый экспериментально предел выносливости образца,
имеющего поверхность обработанную по определённому классу шероховатости;
– предел выносливости стандартного образца (полированного).
|
Так, например, для стальной детали с |
B = 800 МПа шлифование даёт |
|
= 0,92, грубое точение - = 0,76 [6] , для |
цементованных сталей = 0,82 [6]. |
При расчёте валов рекомендуется принимать |
= 0,97…0,90 при шероховатости |
|
поверхности Ra = 0,32…2,5 мкм [5]. |
|
|
|
2.6.4. Число циклов нагружения |
|
|
Найденный из кривой выносливости (рис. 2.6) предел выносливости , |
внесенный в справочники, соответствует базовому числу циклов NG. База напряжений, то есть точка перехода кривой выносливости в прямую, зависит от вида деформации и свойств материала. Например, база изгибных напряжений зубьев колес NFG = 4·106. Для вращательного движения число циклов нагружения
(наработку) определяют по формуле:
N = 60·n·Lh, |
(2.10) |
где n – частота вращения в об/мин; Lh – долговечность, ч.
Если наработка N меньше базы NG, то в соответствии с кривой выносливости (рис. 2.6) предельное напряжение должно быть выше. Уравнение
кривой выносливости: |
|
|
|
|
|
|
|
|
|
|
|
|
|
|
m N const . |
|
|
|
|
(2.11) |
|||||||
Из него находят предел выносливости |
при числе циклов N: |
|
|||||||||||
|
|
|
|
|
|
|
1 |
|
|
|
|
|
|
|
|
|
|
|
|
|
|
|
|
|
|
|
|
|
|
|
m |
NG |
|
|
|
K |
|
, |
(2.12) |
||
|
|
|
L |
||||||||||
|
|
|
|
N |
|
|
|
|
|
|
|||
|
|
|
|
|
|
|
|
|
|
|
|
|
где m – показатель степени кривой выносливости, характеризующий крутизну ветви кривой выносливости, который колеблется в весьма широких пределах в зависимости от размеров образца, наличия концентрации напряжений,
упрочнения материала и др.; так, для стальных зубчатых колёс m = 3 при расчёте

на контактную прочность, m = 6 или 9 – при расчёте на изгиб в зависимости от термообработки.
KL – коэффициент долговечности; |
|
KL , так как предел выносливости 1 |
в забазовой области не может быть меньше предела выносливости 1 , принятого из справочника. При расчёте зубчатых колес вводят коэффициент долговечности,
определяемый как обратная величина KL.
К |
|
m |
|
|
N |
|
. |
(2.13) |
Д |
|
|
||||||
|
|
|
NG |
|
||||
|
|
|
|
|
||||
NB 2.6. При наработке меньше |
базовой |
предельные напряжения |
металла увеличиваются в соответствии с кривой выносливости.
Пример 2.1. Рассчитать коэффициент долговечности зубчатых передач из объёмно закалённых колёс по контактным напряжениям, если ресурс передачи
Lh = 8000 ч, частота вращения колеса n = 40 об/мин, база контактных напряжений
NG = 36·106.
Решение.
Число циклов нагружения по формуле (2.10): N = 60·40·8000 =19,2·106.
Коэффициент долговечности – формула (2.13):
К |
|
3 |
19,2 106 |
|
0,81. |
НД |
36 106 |
|
|||
|
|
|
|
Рассмотренные факторы учитываются при циклической нагрузке, в расчётах деталей на выносливость.
2.7.Коэффициенты запаса прочности
Винженерных расчётах наибольшее распространение получил расчёт по запасам прочности. Условие прочностной надежности при такой оценке имеет вид:
s R . |
(2.14) |
max
Вчастности, для пластичного материала коэффициент запаса по текучести определяют по формуле:
sT |
|
|
T |
[s] . |
(2.15) |
|
a |
m |
|||||
|
|
|
|
От правильности назначения sT зависит степень рациональности конструкции детали. При этом заниженное значение запаса прочности может привести к разрушению детали, завышенное – к неоправданному увеличению массы изделия и перерасходу материала. Факторы, влияющие на запас прочности,
многочисленны и разнообразны. Их полный учёт невозможен в связи с взаимоисключением некоторых из них. Принята методика определения допускаемого коэффициента запаса дифференцированным методом. Он заключается в определении [s] как произведения минимального числа коэффициентов
[s] = s1· s2· s3, |
(2.16) |
где s1 – коэффициент, учитывающий точность расчётной схемы, s1=1…1,5;
s2 – коэффициент, учитывающий однородность механических свойств материала, s2=1,2…1,5;
s3 – коэффициент, учитывающий специфические требования безопасности, s3=1…1,5.
Обычно [s] =1,5….2. В каждой отрасли машиностроения выработаны свои нормы запасов прочности для конкретных деталей. Так, например, для стальных зубчатых колёс, подвергнутых объёмной закалке, рекомендуется коэффициент
запаса по изгибным напряжениям [sF ] = 1,8 [9].
При циклической нагрузке на прочность оказывают влияние концентрация
напряжений и другие факторы, учитываемые соответствующими
коэффициентами. Коэффициенты запаса соответственно по нормальным и касательным напряжениям:
s |
|
|
|
|
|
|
|
1 |
|
|
; |
(2.17) |
||
|
K |
|
|
|
|
|
||||||||
|
|
|
|
|
a |
m |
|
|||||||
|
|
|
|
|
|
|
|
|||||||
|
|
|
|
|
|
|
|
|
|
|||||
|
|
|
|
|
|
|
|
|
|
|
|
|
|
|
s |
|
|
|
|
|
|
|
|
1 |
|
. |
|
(2.18) |
|
|
|
K |
|
|
|
|
|
|
|
|||||
|
|
|
|
|
a |
m |
|
|||||||
|
|
|
|
|
||||||||||
|
|
|
|
|
|
|
|
|
||||||
|
|
|
|
|
|
|
|
|
|
|
|
|
|
|

В формулах (2.17) и (2.18) и - коэффициенты, учитывающие чувствительность материала к асимметрии цикла; = 0…0,15; = 0…0,1 [9].
Общий коэффициент запаса:
s |
s |
s |
|
[s]. |
(2.19) |
|
|
|
|
|
|||
|
s2 |
s2 |
||||
|
|
|
|
|
||
|
|
|
|
|
|
|
Обычно [s] > 1,5. При расчёте валов рекомендуется [s] = 2,5…3,5, что гарантирует не только прочность, но и достаточную жёсткость.
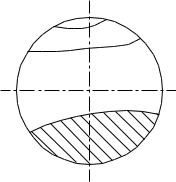
Лекция №3
2.8. Объёмная прочность
Прочность является основным критерием работоспособности большинства деталей. Отказы деталей происходят вследствие потери статической прочности и сопротивления усталости. Потеря статической прочности происходит тогда,
когда значение рабочих напряжений превышает предел статической прочности,
например, B . Это связано обычно со случайными перегрузками, не учтёнными при расчётах, или со скрытыми дефектами деталей (с раковинами, трещинами и т.п.). Такой вид отказа происходит внезапно и является весьма опасным.
Потеря сопротивления усталости происходит в результате длительного действия переменных напряжений, превышающих предел выносливости материала 1 . Сопротивление усталости значительно понижается при наличии концентраторов напряжений, связанных с конструктивной формой детали
(галтели, резьбы и т.п.) или с дефектами производства (царапины, трещины и пр.).
Статистический анализ случаев поломок деталей машин показывает, что
80 % этих разрушений носит усталостный характер вследствие цикличности напряжений и концентрации напряжений. Типичный усталостный излом имеет две зоны (рис. 2.10): зона усталостного разрушения с мелкозернистой, почти гладкой поверхностью там, где усталостная трещина постепенно проникала в глубь сечения, и зона статического разрушения (заштрихована), по которой произошло окончательное, хрупкое разрушение — с крупнокристаллическим строением.
Рис. 2.10. Поверхность усталостного излома

Зарождение усталостной трещины – процесс трудноуловимый. Для ответственных деталей применяют дефектоскопирование. Основы расчёта на прочность изучают в курсе сопротивления материалов. В курсе деталей машин общие методы расчётов на прочность рассматривают в приложении к конкретным деталям и придают им форму инженерных расчётов.
При растяжении – сжатии используется следующая формула:
FA [ ].
При срезе:
FA ср [ ].
При смятии:
см FA см [ см ].
При изгибе:
И WM [ И ] .
В формулах (2.20)…(2.22) А – площадь опасного сопротивления:
– для прямоугольного сечения:
(2.20)
(2.21)
(2.22)
(2.23)
сечения. Моменты
|
|
|
|
|
|
W |
|
bh |
|
; |
|
|
|
|
(2.24) |
|||
|
|
|
|
|
|
|
|
|
|
|
|
|
||||||
|
|
|
|
|
|
|
|
|
|
|
|
|
|
|
|
|
||
– для круга |
|
|
|
|
|
|
|
|
|
|
|
|
|
|
|
|
|
|
|
|
|
|
|
|
W |
|
d |
. |
|
|
|
(2.25) |
|||||
|
|
|
|
|
|
|
|
|
|
|
|
|
|
|||||
|
|
|
|
|
|
|
|
|
|
|
|
|
|
|
|
|
||
Моменты инерции соответственно: |
|
|
|
|
|
|
|
|
|
|||||||||
|
|
|
I |
|
bh3 |
|
d |
4 |
|
|
|
|
||||||
|
|
|
|
|
; I |
|
|
|
|
. |
|
|
|
(2.26) (2.27) |
||||
|
|
12 |
64 |
|
|
|
||||||||||||
|
|
|
|
|
|
|
|
|
|
|
|
|
||||||
При кручении: |
|
|
|
|
|
|
|
|
|
|
|
|
|
|
|
|
|
|
|
T |
|
T max |
; |
для круга W |
|
d 3 |
; I |
|
d 4 . |
(2.28) |
|||||||
|
|
p |
p |
|||||||||||||||
Wp |
|
I p |
|
|
|
|
|
|
|
|
16 |
|
32 |
|
||||
|
|
|
|
|
|
|
|
|
|
|
|
|
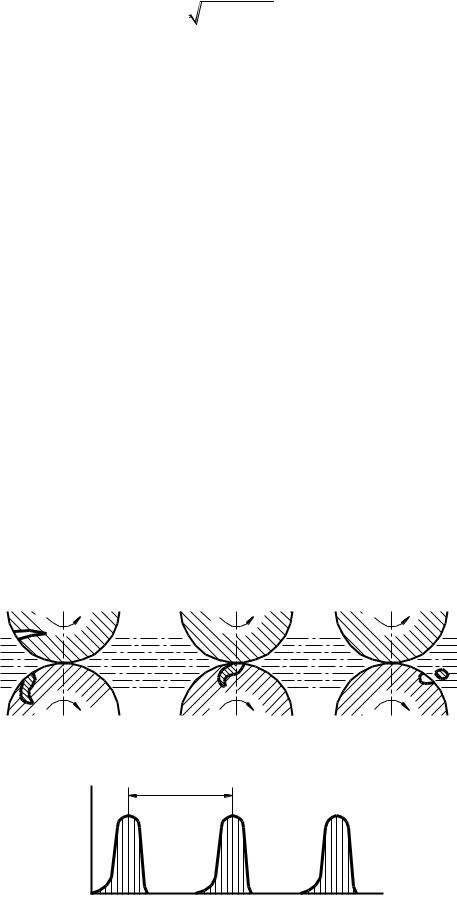
При сложном напряженном состоянии используются теории прочности,
например, четвертая (энергетическая):
|
|
|
|
|
|
|
пр.iv |
|
2 3 2 [ ]. |
(2.29) |
|
|
|
|
|
|
2.9. Контактная прочность
Кроме поломок деталей в практике многочисленны случаи разрушения их поверхностей. Последние связаны с так называемыми контактными напряжениями. Если значения контактных напряжений больше предельных, то на поверхности деталей появляются вмятины, борозды, трещины или мелкие раковины. Подобные повреждения наблюдаются у зубчатых, червячных,
фрикционных и цепных передач, а также в подшипниках качения.
Один из характерных видов поверхностных разрушений приведен на рис. 2.11. При работе цилиндрических катков фрикционной передачи в масляной ванне на площадке малых размеров при действии сжимающей силы возникают высокие напряжения сжатия Н , которые изменяются по пульсирующему циклу .
При циклической нагрузке на поверхности катков появляются усталостные трещины, которые под влиянием сил трения распространяются наклонно к поверхности контакта.
ω1
ω2
Один оборот |
H |
t |
Рис. 2.11. Процесс усталостного выкрашивания |
Развитию образующихся усталостных трещин способствует гидростатическое давление смазочного материала, проникающего в трещины с поверхности. На ведущем катке трещины ориентированы так, что в зоне наибольших контактных давлений масло из трещины выдавливается, и темп роста трещины не увеличивается. На ведомом катке (отстающая поверхность) при встрече с сопряженной поверхностью края трещины замыкаются и давление в слое масла, находящегося внутри неё, резко возрастает. Этим обусловлено расклинивающее действие, способствующее постепенному развитию трещины и выходу её на поверхность (выламывание частичек металла).
Усталостное выкрашывание может иметь ограниченный или прогрессирующий характер. Прогрессирующее выкрашивание характерно для деталей с высокой твёрдостью рабочих поверхностей. При появлении первых оспин края их в результате нового контакта обламываются, и площадь разрушений катастрофически увеличивается. Однако первые оспины появляются в этом случае гораздо позже, чем на поверхностях менее твёрдых.
Контактные напряжения изучают в специальном курсе – теории упругости. Контактная задача получила аналитическое решение в 1882 г., когда известный немецкий механик Г. Герц вывел формулу, которая носит его имя. Им рассмотрен контакт двух цилиндров, двух шаров, шара и плоскости и т. д.
Предпосылки расчёта на контактную прочность:
1.Площадка контакта весьма мала по сравнению с поверхностями соприкасающихся тел.
2.Материалы соприкасающихся тел однородны и изотропны.
3.Действующие усилия направлены нормально к поверхностям соприкасающихся тел, то есть силы трения не учитываются.
4.Нагрузки, приложенные к телам, создают в зоне контакта только упругие деформации.
На рис. 2.12 представлена расчётная схема нагружения двух цилиндров
распределённой нагрузкой q. Контактные напряжения в МПа определяют по
формуле Герца:
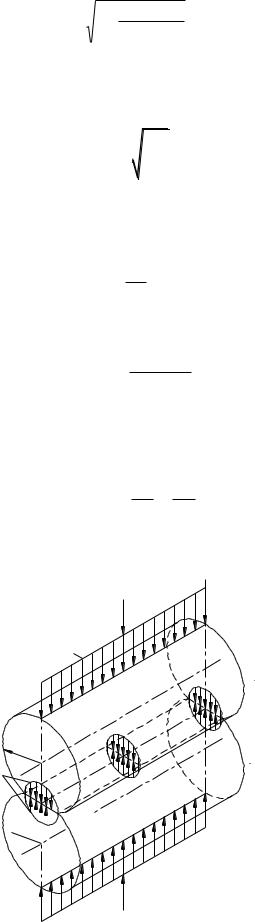
Н |
q |
|
E |
|
|
|
2 (1 2 ) |
, |
(2.30) |
||
|
где μ – коэффициент Пуассона; приняв μ = 0,3 (0,25…0,35) получают более простую формулу:
|
|
0, 418 |
qE |
[ |
|
] , |
(2.31) |
Н |
|
H |
|||||
|
|
|
|
|
|||
|
|
|
|
|
|
q – удельная нагрузка в Н/мм; при действии сосредоточенной силы Fn
площадке длиной b в мм
q Fbn ;
Е – приведенный модуль упругости в МПа;
E E E , E E
Е1 и Е2 – модули упругости соприкасающихся тел;
ρ– приведенный радиус кривизны:
;
ρ1 и ρ2 – радиусы кривизны контактирующих поверхностей.
в Н на
(2.32)
(2.33)
(2.34)
Fn
q
R1
H
R2
q
Fn
Рис. 2.12. Расчётная схема контактных напряжений
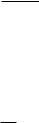
2.10. Жёсткость деталей машин
Жёсткость – свойство деталей сопротивляться изменению формы под действием сил. Недостаточная жёсткость деталей столь же опасна, как и малая прочность. Расчёт на жёсткость предусматривает ограничение упругих перемещений деталей, допустимых для конкретных условий работы. Такими условиями могут быть: условия работы сопряжённых деталей (зубчатых колёс,
подшипников, закрепляемых на валу) и технологические условия (станина металлорежущего станка должна быть жёсткой для получения точных размеров деталей).
Норму жёсткости деталей устанавливают на основе практики эксплуатации и расчётов. Значение расчётов на жёсткость возрастает в связи с широким внедрением высокопрочных сталей, у которых увеличиваются характеристики прочности (σT, σB, σ-1), а модуль упругости Е (характеристика жёсткости) остается неизменным.
При растяжении расчёты на жёсткость заключаются в определении линейного удлинения детали по формуле Гука, справедливого для прямолинейного участка кривой растяжения (рис. 2.6). Он соответствует упругим деформациям, пластические деформации недопустимы. Удлинение
l F l ,
E A
где l – длина детали.
Формула (2.35) может быть записана в ином виде:
l CF F ,
(2.35)
(2.36)
где С– коэффициент жёсткости; он равен силе, вызывающей единичное перемещение рассматриваемого сечения в Н/мм;
λ – коэффициент податливости – величина, обратная коэффициенту жёсткости – перемещение сечения под действием единичной силы в мм/Н. Из формулы (2.36) следует: