
Методички / Курс деталей машин
.pdf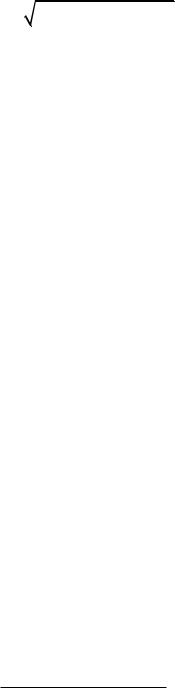
Проведём расчёт вероятностных натягов для этой посадки при P = 0,95.
Средний натяг: Nm = 0,043 + 0,5(0,016 - 0,025) = 0,0385 мм.
SA = 0,025/6 = 0,0042 мм; SB = 0,016/6 = 0,0027 мм.
Среднее квадратичное отклонение табличного натяга:
SN 0,00422 0,00272 0,0050мм.
Квантиль нормального распределения up = 1,64 (табл. 7.1). Вероятностные натяги:
N N
p min
p max
0,0385 1,64 0,005 0,0303мм 30,3мкм;
0,0385 1,64 0,005 0,0467 мм 46,7 мкм.
|
Вывод. |
Результаты расчётов совпадают с табличными. Посадка |
||
|
|
|
0,025 |
|
Ж50 |
H 7 |
Ж50 |
|
пригодна. |
|
|
|||
|
s6 |
|
0,059 |
|
|
|
|
0,043 |
По минимальному натягу Nmin или Npmin можно определить минимальное давление в соединении по формуле Лямэ.
Пример 7.4. По исходным данным примера 7.1 и его решению рассчитать давление в соединении с посадкой
|
|
|
|
0,025 |
|
|
Ж50 |
H 7 |
Ж50 |
|
|
|
. |
r6 |
|
0,050 |
|
|||
|
|
|
|
|
||
|
|
|
|
0,034 |
|
|
Номинальный диаметр d = 50 мм, минимальный натяг Nmin = 9 мкм,
коэффициенты C 0,7; |
C 3,38; модуль упругости Е = 21,5·104 |
МПа. |
1 |
2 |
|
Решение. Давление в соединении – формула (7.7):
|
9 10 3 104 |
p |
50 (0,7 / 21,5 3,38 / 2,15) 9,5МПа. |
7.7. Расчёт прочности соединяемых деталей
Выбранная посадка может быть недопустима по условиям прочности сопрягаемых деталей, так как её максимальный натяг может вызвать чрезмерные
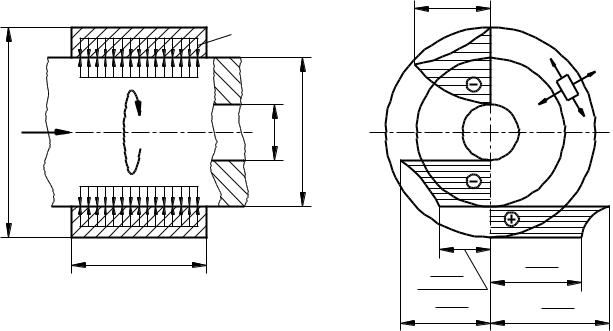
деформации, например, в кольцах подшипников качения, или разрушение.
Расчёт прочности деталей является проверкой возможности применения намеченной посадки. Последовательность расчёта:
1) По максимальному табличному либо вероятностному натягу определяют расчётный натяг из формулы (7.13):
N N p max u; |
(7.19) |
2)Определяют максимальное давление pmax по формуле Лямэ (7.7).
3)Рассчитывают максимальное касательное напряжение на внутренней поверхности втулки и минимальное напряжение в радиальном нааправлении (рис. 7.8, б).
|
d |
2 |
d |
||
t 2 |
p |
|
2 |
|
; |
|
2 |
|
|||
|
d2 |
d |
а)
p |
2 |
Fa |
T |
1 |
d |
|
|
d d |
l |
r |
p. |
|
|
|
|
|
|
(7.20) |
б) |
|
|
p |
|
|
|
|
|
|
|
|
|
|
|
|
||
|
|
|
|
|
|
|
|
r |
|
r |
|
|
|
|
|
|
|
|
2 |
|
1 |
|
|
|
t |
|
|
|
|
|
|
|
|
|
|
|
t1 |
|
|
|
|
|
||
|
|
|
|
|
|
|
|
t2 |
|
p( |
d 2+d12 |
|
2p( |
2d 2 |
2) |
||
|
|
2 |
2) |
|
d2 - d |
|
||
|
|
d - d1 |
|
|
|
|
||
|
2p( |
d |
2d 2 |
2) |
|
p(d222+d 22) |
||
|
|
|
- d1 |
|
d2 |
- d |
Рис. 7.8. Эпюры напряжений
4)Определяют приведенное напряжение по теории наибольших
касательных напряжений:
|
|
|
|
|
пр |
T ; |
|
|
|
(7.21) |
|||
d |
d |
|
( p) p |
d |
|
|
|
|
|
|
|||
p |
|
|
|
|
|
|
|
|
|
T |
, |
(7.22) |
|
|
|
|
|
|
|
||||||||
|
d |
|
|
d |
|
|
|
||||||
d |
|
|
|
d |
|
|
|
|
|
|
5) Определяют давление, при котором пластические деформации будут отсутствовать; для втулки:
|
|
T |
(d d ) |
|
|
p |
|
|
, |
(7.23) |
|
|
|
d |
|||
|
|
|
|
|
|
|
|
|
|
|
|
где Т2 – предел текучести материала втулки.
Для вала:
p |
|
|
(d d ) |
. |
(7.24) |
|
T |
|
|||
|
|
|
d |
|
|
Увеличение наружного диаметра втулки, например, кольца подшипника,
вызванное растяжением от посадки, определяют по формуле:
d |
2 |
2 pd 2d |
2 |
/(E (d 2 |
d 2 )). |
(7.25) |
|
|
|
2 |
2 |
|
|
7.8. Оценка и применение
Прессовые соединения относятся к группе неразъёмных и предварительно напряжённых. Они также относятся к группе соединений вал-ступица, как и клеммовые соединения. Разборка соединения связана с применением специальных приспособлений, сопровождается повреждением посадочных поверхностей и поэтому не рекомендуется без применения специальных мер.
Достоинства:
1)Простота конструкции.
2)Хорошее центрирование сопрягаемых деталей.
3)Способность воспринимать значительные статические и динамические нагрузки.
Недостатки:
1)Высокая концентрация напряжений.
2)Высокая трудоёмкость сборки при больших натягах.
3) Большое рассеивание фактических натягов и невозможность определения истинной нагрузочной способности.
Развитие технической культуры и повышение точности изготовления деталей обеспечивает этому соединению всё более широкое применение.
С помощью прессовых посадок с валом соединяют зубчатые колеса, шкивы,
маховики, подшипники качения и т.п. детали. Прессовые посадки используют при изготовлении составных коленчатых валов, червячных колес, колёсных пар.
На практике часто применяют комбинацию прессового соединения со шпоночным. При этом прессовое соединение может быть основным или вспомогательным. В первом случае большая доля нагрузки воспринимается прессовой посадкой, а шпоночное соединение по существу выключено из работы и оказывается резервным, а шпонка лишь обеспечивает жёсткую фиксацию деталей в окружном направлении. Во втором случае прессовую посадку используют для центровки деталей и частичной разгрузки шпонки. Расчёт комбинированного соединения выполняют по схеме расчёта соединения с натягом.
Вопросы для самоподготовки
1.Как образуется натяг в прессовом соединении?
2.Как собирают детали в прессовом соединении?
3.Какие принимают меры для снижения концентрации напряжений?
4.Когда в расчёты вводится поправка на шабровку?
5.Как выбирают посадку по технологическому натягу?
6.Как образуются вероятностные натяги?
7.В чём заключается расчёт прочности соединяемых деталей?
Вопрос, выносимый на экзамен
1.Прессовые соединения. Общие сведения, технология механической и тепловой сборок, концентрация напряжений. Правила конструирования прессовых соединений.
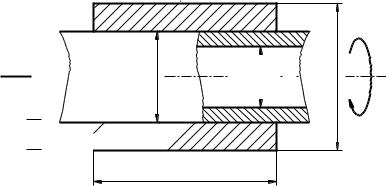
Вопросы, выносимые на Олимпиаду
1.Прессовые соединения. Общие сведения, технология сборки под прессом и при помощи температурных деформаций; концентрация напряжений.
2.Расчёт прессового соединения при действии комбинированной нагрузки.
3.Расчёт прочности соединяемых деталей в прессовом соединении.
Экзаменационные задачи
Задача №19
Рассчитать натяг, выбрать посадку и вычертить эскиз с обозначением
посадки соединения с гарантированным натягом.
Технология сборки — механическая. Вероятность неразрушения Р = 1
Fa d
1
2
l
|
d1 |
|
|
|
|
|
|
d2 |
|
|
|
|
|||||
|
|
|
|
|
|
|
|
|
T
Наименование параметра |
|
|
Вариант |
|
|
|
|
1 |
2 |
3 |
4 |
|
5 |
6 |
|
|
|
||||||
Осевая нагрузка Fа, кН |
8 |
16 |
0 |
25 |
|
0 |
30 |
Крутящий момент Т, Н·м |
1000 |
0 |
1600 |
1400 |
|
2000 |
1800 |
Номинальный диаметр d, мм |
30 |
40 |
50 |
60 |
|
70 |
90 |
Внутренний диаметр вала d1, мм |
0 |
10 |
0 |
0 |
|
24 |
0 |
Наружный диаметр втулки d2, мм |
120 |
200 |
80 |
100 |
|
150 |
180 |
Материал вала |
Сталь |
Сталь |
Сталь |
Сталь |
|
Сталь |
Сталь |
Материал втулки |
Сталь |
Чугун |
Бронз |
Чугун |
|
Бронз |
Сталь |
|
а |
|
а |
||||
|
|
|
|
|
|
||
Максимальная высота неровностей |
6,3 |
3,2 |
1,6 |
3,2 |
|
6,3 |
1,6 |
Rz1, мкм |
|
||||||
|
|
|
|
|
|
|
|
Rz2, мкм |
10 |
6,3 |
3,2 |
6,3 |
|
10 |
3,2 |
|
|
|
|
|
|
|
|
Примечания. 1. Недостающие данные взять из таблиц Приложения. |
2. Длину втулки |
принять l = (1,2…1,5) d.
Задача №20
Рассчитать допускаемую нагрузку соединения с гарантированным натягом.
Технология сборки — тепловая. Использовать расчётную схему задачи №27.
Наименование параметра |
|
|
|
|
|
|
|
Вариант |
|
|
|
|
|
|
|||||
1 |
|
2 |
|
3 |
|
4 |
|
|
5 |
|
6 |
|
|||||||
|
|
|
|
|
|
|
|
||||||||||||
Вид допускаемой нагрузки |
Fa |
T |
Fa |
T |
|
Fa |
T |
||||||||||||
Вероятность неразрушения |
0,999 |
0,99 |
|
0,9 |
|
0,95 |
|
|
0,9 |
|
0,99 |
|
|||||||
Номинальный диаметр вала d |
60 |
H 7 |
70 |
H 8 |
80 |
H 7 |
90 |
H 7 |
|
100 |
H 7 |
120 |
H 7 |
||||||
и посадка |
s6 |
|
r7 |
|
p6 |
|
r6 |
|
|
t6 |
|
s6 |
|
||||||
Внутренний диаметр вала d1, |
0 |
|
10 |
|
0 |
|
20 |
|
|
0 |
|
40 |
|
||||||
мм |
|
|
|
|
|
|
|
|
|
|
|
||||||||
|
|
|
|
|
|
|
|
|
|
|
|
|
|
|
|
|
|
|
|
Наружный диаметр втулки d2, |
120 |
|
140 |
|
150 |
|
160 |
|
|
180 |
|
200 |
|
||||||
мм |
|
|
|
|
|
|
|
|
|
|
|
||||||||
|
|
|
|
|
|
|
|
|
|
|
|
|
|
|
|
|
|
|
|
Материал вала |
Сталь |
Сталь |
Сталь |
Сталь |
|
Сталь |
Сталь |
||||||||||||
Материал втулки |
Сталь |
Чугун |
Бронза |
Чугун |
|
Бронза |
Сталь |
||||||||||||
Примечания. 1. Недостающие данные взять из таблиц Приложения. |
2. Длину втулки |
принять l = (1,2…1,5) d.
Тема 8: Шпоночные соединения 8.1. Общие сведения
Шпоночные соединения служат для закрепления деталей на осях и валах и передачи крутящего момента Т. Такими деталями являются шкивы, зубчатые колёса, муфты, маховики, кулачки и т.д. Соединения осуществляют с помощью шпонки – специальной детали, закладываемой в пазы соединяемых вала и ступицы.
В машиностроении применяют ненапряжённые соединения (с помощью призматических и сегментных шпонок), их также называют призматическими, и
напряжённые (с помощью клиновых шпонок), их также называют клиновыми.
Шпонки этих типов стандартизированы.
Различают неподвижные и подвижные шпоночные соединения. У подвижных соединений, например, в коробках передач, ступица может перемещаться на валу вдоль его оси; в этом случае используют длинные направляющие шпонки, которые крепят к валу винтами.
Достоинства:
1) Простота конструкции.
2)Сравнительно низкая стоимость.
3)Возможность жёсткой фиксации ступицы в окружном направлении.
Недостатки:
1)Ослабление пазами вала и ступицы.
2)Концентрация напряжений в зоне шпоночной канавки.
3)Необходимость ручной подгонки или подбора.
Последний недостаток ограничивает использование соединений в машинах крупносерийного и массового производства. Шпоночное соединение применяют преимущественно в тех случаях, когда посадку с натягом не удается реализовать по условиям прочности или технологическим возможностям.
Призматические шпонки (рис. 8.1) применяют в конструкциях наиболее широко, так как они просты в изготовлении и имеют сравнительно небольшую глубину врезания в вал. Но по последней причине шпонка в пазах имеет
недостаточную устойчивость. Сегментная шпонка (рис. 8.2) с глубоким пазом обладает в этом отношении преимуществом. Её предпочитают применять в массовом производстве. Однако паз под шпонку существенно ослабляет вал,
поэтому сегментные шпонки используют преимущественно для закрепления деталей на малонагруженных участках вала, например, на входных и выходных хвостовиках валов.
Соединения клиновыми шпонками (рис. 8.3 и 8.4) характеризуется свободной посадкой ступицы на вал (с зазором). Запрессовка (забивка) шпонки в пазы
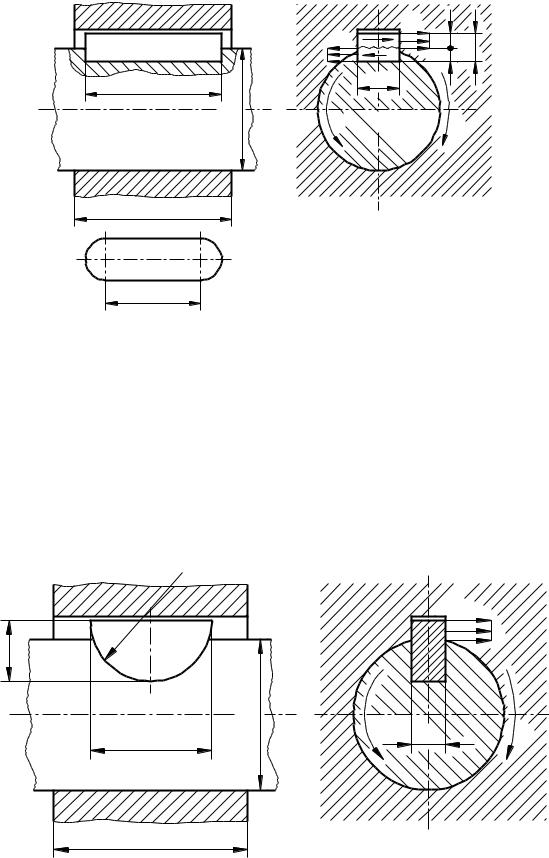
l |
d
l ст |
см |
|
см |
|
2 |
|
|
t |
|
|
1 |
|
|
t h |
|
|
b |
|
T
T
l р |
Рис. 8.1. Соединение призматической шпонкой
смещает центры вала и ступицы, что вызывает дебаланс и неблагоприятно сказывается на работе механизма при больших угловых скоростях. Все виды шпонок малонадёжны при действии ударных, циклических и реверсивных нагрузок. При этих условиях их в крупносерийном и массовом производстве
заменяют шлицевыми.
h |
d |
ш |
|
||
|
|
|
|
|
d |
|
|
l |
lст |
|
|
см |
T |
b |
T |
Рис. 8.2. Соединение сегментной шпонкой
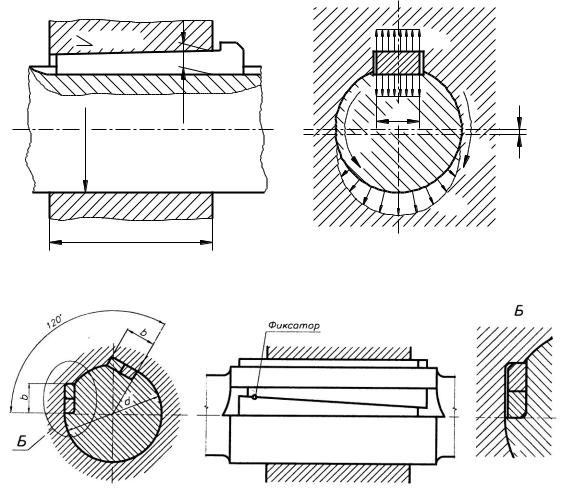
1:100 |
h
d
lст
|
см |
b |
|
T |
T |
|
|
|
см |
Рис. 8.3. Соединение клиновой шпонкой
Рис. 8.4. Соединение клиновыми тангенциальными шпонками
8.2. Соединения призматическими шпонками
Призматические шпонки имеют прямоугольное сечение с отношением ширины к высоте b/h 1. Их устанавливают с небольшим натягом в пазы валов.
Рабочими у шпонок являются боковые узкие грани (рис. 8.1). В радиальном направлении предусмотрен зазор. Материал шпонок – чистотянутая сталь 45 и
сталь Ст6 с B >590 МПа. В сильно нагруженных соединениях применяют легированные стали с термообработкой.
Торцы шпонок могут быть плоскими либо скруглёнными (рис. 8.1). Это зависит от технологии изготовления паза вала. Предпочтительно изготовление шпоночного паза дисковой фрезой (рис. 8.5, б); при этом достигается высокая точность выполнения размера ширины паза и меньшая концентрация напряжений.
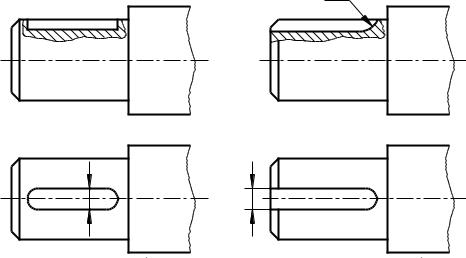
Однако осевая фиксация шпонки менее надёжна, чем при его фрезеровании
пальцевой фрезой (рис. 8.5, а).
R |
b |
b |
Рис. 8.5. Шпоночные пазы
Пазы в ступице выполняют долблением (строганием) или протягиванием одношлицевой протяжкой. Глубина паза ступицы t2 меньше глубины паза вала t1 и
является расчётной при определении напряжений смятия. Призматические шпонки вставляют в паз вала с небольшим натягом, а в паз ступицы – с зазором.
Извлечение шпонки из паза вала технологией ремонта не предусмотрена.
При передаче момента Т на боковых гранях возникают напряжения смятия
см, а в продольном сечении шпонки – напряжения среза (рис. 8.1). Условия прочности:
см |
|
2T |
см ; |
(8.1) |
|||
|
|
|
|||||
d lp t2 |
|||||||
|
|
|
|
||||
|
2T |
|
, |
(8.2) |
|||
|
|
|
|||||
|
d b lp |
|
|
||||
где lp – расчётная длина шпонки со скругленными торцами; |
|
||||||
|
lр = l – b. |
(8.3) |
В формулах (8.1) и (8.2) отношение 2Т/d соответствует окружному усилию
Ft, которым заменяют действие момента – формула (6.8). Длина ступицы должна