
Методички / Курс деталей машин
.pdf
Длина нарезанной части червяка:
b1 (c1 c2 z2 )m (11 0, 06 33) 16 207, 68мм.
Принимаем b1 =210 мм. Ширина венца колеса:
b2 0, 75 da1 0, 75 160 120мм.
Угол обхвата червяка
2δ |
2b2 |
|
2 120 |
1,58 рад 1,58 180 / 90,5 [2δ ] 90...110 . |
da1 0,5m |
160 0,5 16 |
Окружная скорость колёс υ = d1n1/60000 = π·128·250/60000 = 1,68 м/с.
Скорость скольжения υs = υ /cos w = 1,68/ cos13,63 º = 1,72 м/с. Уточняем коэффициенты нагрузки для 8-й степени точности: K = 1; Kυ = 1,25 [9]. Рабочее
контактное напряжение:
|
|
|
|
|
|
|
|
|
|
|
|
|
|
|
|
|
|
|
|
|
|
|
|
|
H |
480 |
|
|
T K |
H |
|
|
|
480 7640 103 |
1 1, 25 |
244,5МПа [ H |
] 235МПа. |
||||||||||||
|
|
|
2 |
|
|
|
|
|
|
|
|
|
|
|
|
|
||||||||
d2 |
|
|
dw1 |
|
528 |
|
|
|
|
|
132 |
|||||||||||||
|
|
|
|
|
|
|
|
|
|
|
|
|
|
|
|
|||||||||
Перегрузка составляет δ = (244,5 – 235) 100/235 = 4%, что допустимо (до |
||||||||||||||||||||||||
5%). |
|
|
|
|
|
|
|
|
|
|
|
|
|
|
|
|
|
|
|
|
|
|
|
|
Вывод. Контактная прочность достаточна. |
|
|||||||||||||||||||||||
Окружное усилие на червяке, |
равное осевому на колесе: |
|||||||||||||||||||||||
|
|
|
|
|
|
|
|
|
|
|
|
|
|
|
2 T |
|
|
2 573 103 |
|
|||||
|
|
|
|
F |
F |
|
|
|
|
1 |
|
|
|
|
|
8682Н. |
|
|||||||
|
|
|
|
|
|
|
|
|
|
|
|
|||||||||||||
|
|
|
|
|
|
t1 |
|
a 2 |
|
|
|
dw1 |
|
132 |
|
|
|
|||||||
|
|
|
|
|
|
|
|
|
|
|
|
|
|
|
|
|
|
|
||||||
Окружное усилие на колесе, равное осевому на червяке: |
||||||||||||||||||||||||
|
|
|
|
|
|
|
|
|
|
|
|
|
2 T |
|
|
2 7640 103 |
|
|||||||
|
|
|
|
F |
|
|
|
F |
|
|
|
2 |
|
|
|
|
|
|
28939Н. |
|
||||
|
|
|
|
|
|
|
|
|
|
|
|
|
|
|
|
|
||||||||
|
|
|
|
t 2 |
|
|
|
|
a1 |
|
|
|
d2 |
|
|
|
528 |
|
|
|
||||
|
|
|
|
|
|
|
|
|
|
|
|
|
|
|
|
|
|
|
|
Радиальное усилие Fr = Ft2·tg = 28939·tg20º = 10533 Н.
Нормальное усилие:
Fn = Ft2/(cos · cos w ) = 28939/(cos20º·cos13,63º) = 31689 Н.
Эквивалентное число зубьев колеса:
zv2 33/ cos3 13,63 36.
Коэффициент формы зуба YF 2 1,64.
Нормальный модуль mn = m·cos w = 16·cos13,63º = 15,55 мм.
Уточняем коэффициенты нагрузки: K = 1; Kυ = 1,35. Рабочее изгибное
напряжение колеса:
F2 = 0,7·YF2Ft2 K Kν/(bmn)= 0,7·1,64·28939 ·1·1,35/(120·15,55) = 24 МПа < [59,2].
Вывод. Изгибная прочность достаточна.
Приведенный угол трения 2 30 . Механический КПД передачи:
0,95 |
tg w |
0,95 |
tg13, 63 |
0,8. |
tg( w ) |
tg(13, 63 2,5 ) |
16.12. Тепловой расчёт червячного редуктора
Червячные передачи работают с большим выделением теплоты. В
результате температура масла в ванне редуктора может достигать предельного значения. При этом нарушается нормальный режим трения в контакте червяка и колеса и передача может потерять работоспособность из-за заедания. При детальном рассмотрении данного процесса можно отметить следующие положения:
1) Количество теплоты, выделяющейся в передаче в секунду, или тепловая мощность:
Q |
P ( ), |
(16.36) |
|
|
|
где Р1 – мощность на входном валу, Вт.
2) Количество теплоты, отданной в секунду через стенки редуктора
окружающему воздуху, или мощность теплоотдачи: |
|
Q2 KT (t to )A, |
(16.37) |
где KТ – коэффициент теплоотдачи, Вт/(м2 С); t – температура масла;
tо – температура окружающей среды;
А – площадь поверхности охлаждения, м2. Это та часть площади наружной поверхности корпуса редуктора, которая изнутри омывается маслом, а снаружи – свободно циркулирующим воздухом. Величину А можно определить по эмпирической зависимости:
A 20 a1,7 . |
(16.38) |
w |
|
В формулу (16.38) межосевое расстояние aw ставят в миллиметрах, ответ получают в мм2 и переводят в м2.
3) В начале работы передачи Q1 > Q2 и температура масла повышается.
Через некоторое время наступает тепловой баланс, когда Q1 = Q2, которому соответствует температура масла t. Целью теплового расчёта является
определение температуры масла из уравнения теплового баланса:
P (1 ) K (t t |
)A, откуда |
t t |
|
|
P (1 ) |
[t]. |
(16.39) |
||
|
1 |
||||||||
o |
|
||||||||
1 |
T |
o |
|
|
|
KT A |
|
|
|
|
|
|
|
|
|
|
|
|
|
Допускаемое значение |
[t] |
зависит от |
сорта |
масла, его |
способности |
сохранять смазывающие свойства при повышении температуры. Для обычных редукторных масел [t] = 60…70 С ( 90 С). Авиационные масла имеют [t] =
100…120 С.
4) Невыполнение условия (16.39) приводит к явлению, описываемому следующей логической цепочкой:
а) увеличение температуры масла сверх допустимого приводит к:
б) снижению вязкости масла, что в свою очередь приводит к:
в) разрыву масляной пленки, увеличению трения и соответственно температуры и т.д., следствием чего является:
г) заедание и быстрый выход передачи из строя (катастрофический износ). 5) Для предотвращения описанного процесса в результате анализа формулы
(16.39) принимают следующие меры:
–увеличивают площадь теплоотдачи А проектированием охлаждающих рёбер (рис. 16.10); при этом учитывают только 50% их поверхности;
–применяют искусственное охлаждение установкой на валу червяка
вентилятора (КТ = 20…28 Вт/(м2 С) вместо 8…17), в корпусе редуктора – змеевика с проточной водой (КТ = 90…200) (рис. 16.11) либо использованием циркуляционной системы смазки (рис. 16.12).

Вопросы для самоподготовки
1.Какие виды червячных передач Вы знаете?
2.Оцените червячную передачу.
3.Оцените глобоидную передачу.
4.Какие виды червяков Вы знаете?
5.Чем отличается кинематика червячной передачи от зубчатой?
6.С какой целью выполняют смещение при нарезании червячного колеса?
7.В чём причина более высокого передаточного отношения червячной передачи по сравнению с зубчатой?
8.Как можно повысить КПД червячной передачи?
9.Как определяются усилия в червячном зацеплении?
10.По каким критериям работоспособности рассчитывают червячные передачи?
11.Каковы особенности расчёта червячных передач по контактным напряжениям?
12.Каковы особенности расчёта червячных передач по изгибным напряжениям?
13.Какие материалы применяют для червяка и червячного колеса?
14.Как осуществляется смазка и охлаждение червячного редуктора?
15.В чём заключается тепловой расчёт червячного редуктора?
Вопросы, выносимые на экзамен
1.Червячные передачи. Оценка и применение. Материалы. Геометрия червяков.
2.Червячные передачи. Геометрия червячного колеса и зацепления. Виды разрушения и критерии расчета
3.Расчет червячных передач по контактным и изгибным напряжениям.
Экзаменационные задачи
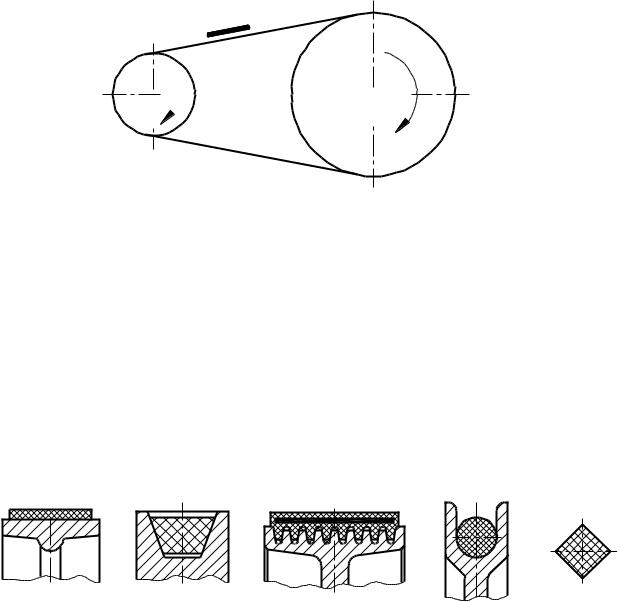

Обычно с помощью ремня передают движение между параллельными валами, вращающимися в одну сторону (рис. 17.1). Благодаря закручиванию ремня реализуют также передачи: перекрестную, полуперекрёстную и угловую
(рис. 17.3, а, б, в).
а) |
|
б) |
|
ω1 |
ω2 |
|
|
|
|
|
в) |
Рис.17.3. Виды ремённых передач
17.2. Материалы ремней
Ремни должны обладать высокой прочностью при переменных напряжениях, износостойкостью, максимальным коэффициентом трения на рабочих поверхностях, минимальной изгибной жёсткостью. Повышенный коэффициент трения обеспечивают клиновой формой ремня, пропиткой ремня и применением фрикционных обкладок. В машиностроении применяют следующие основные типы стандартных ремней.
Кожаные ремни обладают хорошей тяговой способностью и высокой долговечностью, хорошо переносят колебания нагрузки. Имеют ограниченное применение в связи с высокой стоимостью. Чувствительны к влажности окружающей среды.
Прорезиненные ремни состоят из нескольких слоёв хлопчатобумажной ткани, связанных между собой вулканизированной резиной. Ремни эластичные,
малочувствительные к влаге и колебаниям температуры, обладают высокой тяговой способностью. Они имеют доступную стоимость и являются наиболее распространёнными. Чувствительны к попаданию масла, бензина и щелочей.
Хлопчатобумажные ремни изготовляют как цельную ткань с несколькими слоями хлопчатобумажной основы, пропитанной специальным составом. Ремни лёгкие и гибкие, работают на шкивах сравнительно небольших диаметров при высоких скоростях. Тяговая способность и долговечность ниже, чем у прорезиненных.
Шерстяные ремни имеют основу из многослойной шерстяной ткани,
пропитанной специальным составом. Обладая значительной упругостью, они работают при резких колебаниях нагрузки и при малых диаметрах шкивов. Ремни мало чувствительны к температуре, влажности, кислотам. Тяговая способность ниже, чем у других типов ремней.
Плёночные ремни изготовляют из полиамидных лент малой толщины,
армированных кордом из капрона или лавсана. Для увеличения сцепления на рабочую поверхность наклеивают фрикционный слой. Обладают высокой статической и усталостной прочностью. Могут работать при малых диаметрах шкивов с высокой быстроходностью. Весьма перспективны.
Клиновые, поликлиновые, зубчатые и быстроходные плоские ремни изготовляют бесконечными замкнутыми. Плоские ремни, кроме плёночных,
выпускают преимущественно конечными в виде длинных лент, концы которых соединяют.
17.3. Способы натяжения ремней
Условием нормальной работы ремённых передач является наличие натяжения ремня, которое осуществляют следующими способами:
1)предварительным упругим растяжением ремня;
2)перемещением одного из шкивов относительно другого;
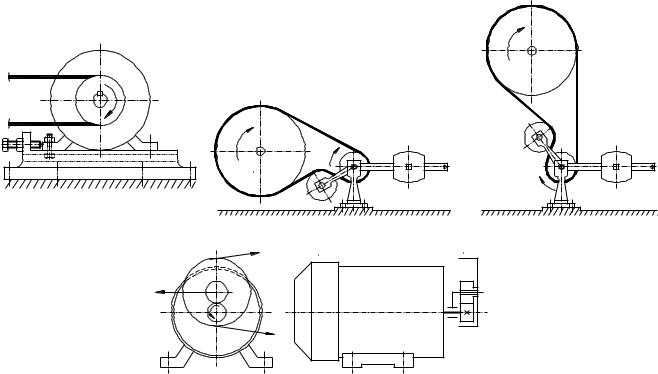
3)натяжным роликом;
4)автоматическим устройством, обеспечивающим регулирование натяжения ремня в зависимости от передаваемой нагрузки;
5)перешивкой конечного ремня.
При первом способе натяжение назначают по наибольшей нагрузке с запасом на вытяжку ремня. Долговечность ремня при этом снижается.
Периодическое натяжение ремня перемещением двигателя на специальных салазках (рис. 17.4, а) является наиболее распространённым способом натяжения
в приводах машин. |
|
а) |
б) |
|
ω2 |
|
ω1 |
|
ω2 |
|
ω1 |
в) |
F2 |
|
|
~ |
2F |
0 |
|
|
T |
F
1
Рис. 17.4. Способы натяжения ремней
Натяжные ролики (рис. 17.4, б) обеспечивают постоянное натяжение плоских ремней. Долговечность ремня понижается за счёт появления знакопеременных напряжений. Устройство для автоматического натяжения ремней (рис. 17.4, в) является наиболее совершенным для долговечности ремня,
однако имеет высокую стоимость. Периодическая перешивка плоского конечного ремня – достаточно надёжное средство восстановления натяжения. При этом не следует забывать, что соединение – наиболее слабый элемент изделия.