
Методички / Курс деталей машин
.pdf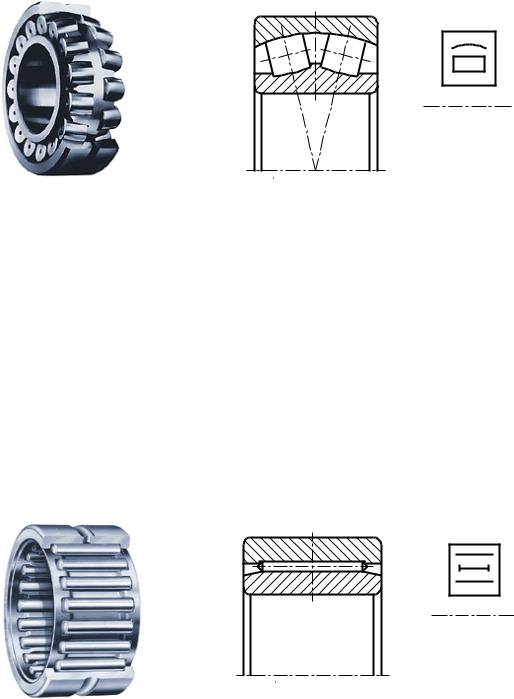
а) |
б) |
в) |
Рис. 26.4. Сферический роликоподшипник
4. Роликоподшипники игольчатые 4000 (рис. 26.5) обладают при
минимальных габаритах максимальной радиальной грузоподъёмностью. Как правило, ролики (иглы) не разделены сепаратором, поэтому занимают промежуточное положение между подшипниками качения и скольжения. Осевые нагрузки не воспринимают. Применяются на поршневых пальцах, в крестовинах
карданных валах и в коробках передач автомобилей, узлах фрезерных станков и
т.д., то есть в узлах, которые должны обеспечить компактность в радиальном направлении, и в узлах с качательным движением.
а) б) в)
Рис. 26.5. Игольчатый подшипник
5. Роликоподшипники с витыми роликами 5000 (рис. 26.6) воспринимают только радиальные нагрузки. Они могут воспринимать ударные нагрузки, мало чувствительны к загрязнению. Они имеют высокую радиальную податливость роликов и, как следствие, высокую демпфирующую способность. Относительная грузоподъёмность С = 0,5. Подшипники могут работать только при небольших частотах вращения. Подшипники неперспективны, их применение сокращается.
Применяют в тихоходных узлах, не требующих точности вращения,
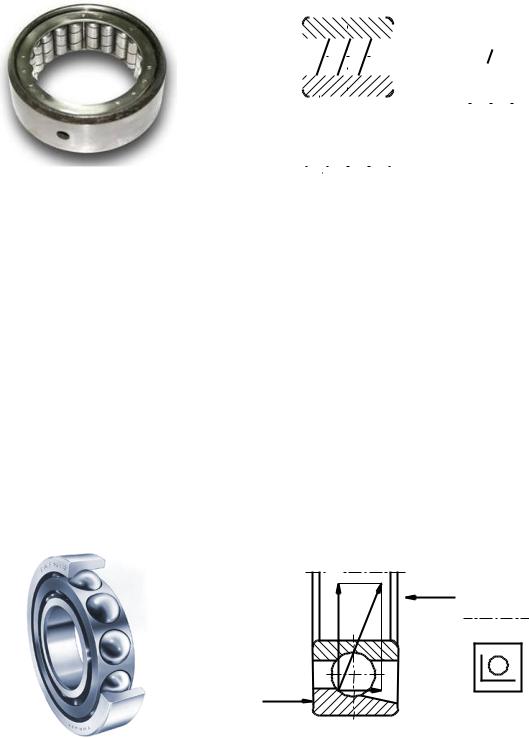
подверженным ударным нагрузкам, и |
в условиях |
|
повышенного загрязнения |
|||||||||||||||||||||||||
(сельскохозяйственные машины, неответственные узлы тракторов и т.п.). |
||||||||||||||||||||||||||||
а) |
б) |
|
|
|
|
|
|
|
|
|
|
|
|
|
в) |
|||||||||||||
|
|
|
|
|
|
|
|
|
|
|
|
|
|
|
|
|
|
|
|
|
|
|
|
|
|
|
|
|
|
|
|
|
|
|
|
|
|
|
|
|
|
|
|
|
|
|
|
|
|
|
|
|
|
|
|
|
|
|
|
|
|
|
|
|
|
|
|
|
|
|
|
|
|
|
|
|
|
|
|
|
|
|
|
|
|
|
|
|
|
|
|
|
|
|
|
|
|
|
|
|
|
|
|
|
|
|
|
|
|
|
|
|
|
|
|
|
|
|
|
|
|
|
|
|
|
|
|
|
|
|
|
|
|
|
|
|
|
|
|
|
|
|
|
|
|
|
|
|
|
|
|
|
|
|
|
|
|
|
|
|
|
|
|
|
|
|
|
|
|
|
|
|
|
|
|
|
|
|
|
|
|
|
|
|
|
|
|
|
|
|
|
|
|
|
|
|
|
|
|
|
|
|
|
|
|
|
|
|
|
|
|
|
|
|
|
|
|
|
|
|
|
|
|
|
|
|
|
|
|
|
|
|
|
|
|
|
|
|
|
|
|
|
|
|
|
|
|
|
|
|
|
|
|
|
|
|
|
|
|
|
|
|
|
|
|
|
|
|
|
|
|
|
|
|
|
|
|
|
|
|
|
|
|
|
|
|
|
|
|
|
|
|
|
|
|
|
|
|
|
|
|
|
|
|
|
|
|
|
|
|
|
|
|
|
|
|
|
|
Рис. 25.6. Роликоподшипник с витыми роликами
26.4.Радиально-упорные подшипники
6.Шарикоподшипники радиально-упорные 6000 (рис. 26.7) способны воспринимать комбинированные радиальные и осевые нагрузки. Осевая грузоподъёмность их зависит от угла контакта, который имеет следующие значения: = 12 (обозначение 36000), = 26 (46000), = 36 (66000).
Увеличение угла контакта повышает грузоподъёмность, но снижает |
||||
быстроходность подшипников. Относительная грузоподъемность С = 1,2 за счёт |
||||
большего числа тел качения, чем в подшипниках типа 0000. |
|
|
||
а) |
б) |
Fr |
R |
в) |
|
|
|
|
Fa |
|
|
|
|
|
|
|
Fa |
S |
|
Рис. 26.7. Радиально-упорный шарикоподшипник
Однорядные подшипники способны воспринимать осевую нагрузку только в одном направлении, поэтому для фиксации вала в обоих направлениях их устанавливают симметрично по два на вал (по схемам «враспор» или

«врастяжку») или по два в одну опору, или по два в обе опоры. Наклон контактных линий приводит к тому, что наклонные (под углом ) реакции от радиальных нагрузок Fr сопровождаются внутренними осевыми силами S,
величины которых определяют по формуле:
S eFr , |
(26.1) |
где е – параметр осевой нагрузки. |
|
Небольшая осевая нагрузка, удовлетворяющая условию: |
|
Fa / Fr e, |
(26.2) |
приводит к положительному эффекту, связанному с тем, что под нагрузкой будет
находиться примерно половина тел качения, а не один – два шарика. Такую осевую нагрузку в расчётах не учитывают. Сборку радиально-упорных подшипников выполняют с предварительным натягом в осевом направлении.
Сепараторы подшипников могут быть штампованными или точёными из
цветных металлов и текстолита. Подшипники используют в шпинделях
металлорежущих станков, электродвигателях, червячных редукторах и др.
устройствах.
7. Конические роликоподшипники 7000 (рис. 26.8) могут воспринимать значительные радиальные (С = 2) и односторонние осевые нагрузки. Осевая
составляющая радиальной нагрузки: |
|
S , eFr . |
(26.3) |
а) |
б) |
|
R |
Fa |
в) |
|
Fr |
|
|
|
|
|
Fa |
|
S |
|
|
|
|
|
|
|
|
|
Рис. 26.8. Конический роликоподшипник |
|
|
Конические роликоподшипники имеют съёмное наружное кольцо, что позволяет производить раздельный монтаж и демонтаж колец. Наряду с основной конструкцией 7000 ( = 12), выпускают ряд разновидностей, среди которых
подшипники с большим углом конусности 27000, двухрядные 97000 и
четырехрядные 77000. Однорядные подшипники применяют в колёсах автомобилей и кранов, в катках гусеничных тракторов, в редукторах и многих других случаях. Являются основным видом радиально-упорных подшипников.
Двухрядные подшипники используют в мощных редукторах, опорах барабанов и других тяжелонагруженных узлах. Четырехрядные подшипники применяют, в основном, для опор валов прокатных станов.
26.5.Упорные и упорно-радиальные подшипники
8.Упорные шарикоподшипники могут воспринимать только осевые нагрузки: однорядные имеют обозначение 8000, а двойные - 38000 (рис. 26.9).
Предельные частоты вращения упорных подшипников ограничены величиной центробежных сил. Применяются в червячных редукторах, в домкратах,
крюковых подвесках кранов и др.
8 . Упорно-радиальные шарикоподшипники 68000 (рис. 26.10) способны воспринимать наряду с осевыми небольшие радиальные нагрузки. Они имеют более высокую быстроходность, чем упорные. Имеют ограниченное применение.
8.Упорные роликоподшипники 9000 (рис. 26.11) способны воспринимать большие осевые нагрузки. Быстроходность этих подшипников низкая.
Данный тип может использовать три вида роликов: короткие цилиндрические (9000), конические (19000) и бочкообразные (39000).
Последний тип является упорно-радиальным. Основные области применения: нажимные устройства прокатных станов, глобоидные редукторы и др.
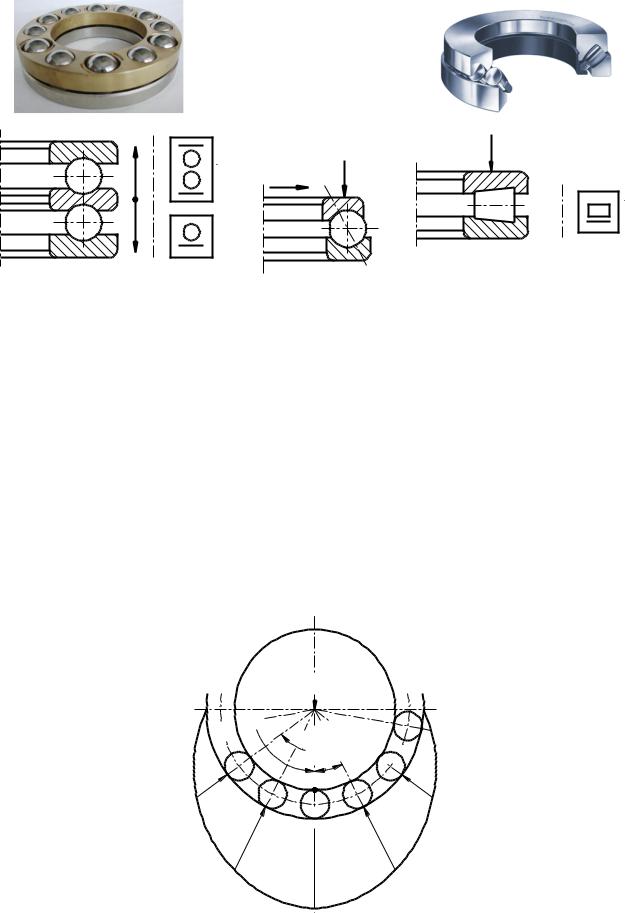
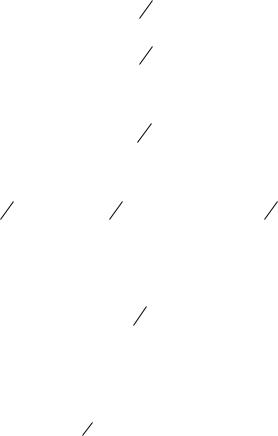
По условию равновесия:
Fr F F cos F cos ... Fn cos n , |
(26.4) |
где 0, 1, 2,…, n – номер нагруженного тела качения; |
|
– угловой шаг тел качения: |
|
360 / z, |
(26.5) |
z – число тел качения.
Исследование зависимости между силами F0, F1, F2,…, Fn с учетом контактных деформаций при абсолютной точности размеров тел качения и колец и отсутствия радиального зазора позволили установить, что величины реакций соответствуют зависимостям:
F |
F cos |
; |
(26.6) |
|
|
|
|
F |
F cos |
; |
|
|
|
|
|
………………….. |
|
||
F |
F cos |
n . |
|
n |
|
|
|
Подставляя эти значения в формулу (26.4), получают:
F F |
F |
cos F |
cos F cos |
n , |
(26.7) |
|
r |
|
|
|
|
|
|
откуда реакция наиболее нагруженного тела качения:
F |
Fr |
|
|
. |
(26.8) |
n |
|
|
|||
|
cos |
n |
|
i
Установлено, что отношение
z |
|
K p |
4,37 0,01 |
(26.9) |
|
|
|||
n |
|
|||
1 2 cos |
5 2 n |
|
|
i 1
для любого числа тел качения, встречающихся в подшипниках. Поэтому реакцию
F0 определяют по формуле:
F , Fr . |
(26.10) |
z
Вводя поправку на влияние радиального зазора и неточности размеров деталей, принимают для шарикоподшипников:

F |
Fr |
. |
(26.11) |
z
Для роликоподшипников, учитывая иное напряженное состояние, получают:
F |
, Fr |
. |
(26.12) |
z
Приведенные коэффициенты достаточно приблизительны, так как распределение нагрузки зависит от многих факторов, в том числе от точности изготовления подшипников. От износа подшипников увеличиваются зазоры, в
результате ухудшаются условия работы вплоть до разрушения подшипника.
26.7. Контактные напряжения
При известных F0, F1, F2,…, Fn можно определить контактные напряжения
в подшипниках. Например, для роликоподшипника может быть использована известная формула Герца, по которой определяют максимальное напряжение:
H , |
|
F E |
|
, |
(26.13) |
|
lw |
||||||
|
|
|
|
|
где lw – эффективная длина ролика (без фасок);
– приведенный радиус кривизны.
Реальные напряжения значительно отличаются от расчётных при выпукло-
вогнутом контакте, так как площадки контакта изменяются при различных нагрузках. Анализ формулы (26.13) показывает, что величина радиуса существенно влияет на напряжённое состояние в точках контакта ролика с выпуклой поверхностью колец или с вогнутой. Так, в точке а максимальные контактные напряжения будут значительно меньше, чем в точке б, где контактируют выпуклые поверхности (рис. 26.13 и 26.14). В этом случае большое значение приобретает тот факт, какое из колец вращается.
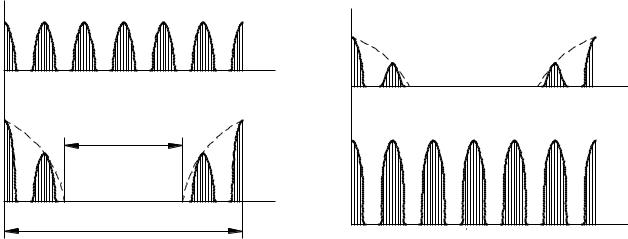
точка а |
H |
|
H |
точка а |
|
|
t |
|
|
|
t |
точка б |
|
|
0,5 оборота |
|
точка б |
|
|
|
|
t |
|
1 оборот |
|
t |
|
|
|
Рис. 26.13. Контактные напряжения |
|
Рис. 26.14. Контактные напряжения |
при вращении внутреннего кольца |
|
при вращении наружного кольца |
В каждой точке поверхности контакта колец и тел качения контактные напряжения изменяются по отнулевому циклу. При вращении внутреннего кольца
напряжения в контактных точках а и б меняются по закону, приведенному на рис. 26.13. В точках а и б период цикла напряжений равен времени перемещения очередного тела качения в данную точку.
Несмотря на то, что в точке б максимальные напряжения выше, чем в точке
а, но при перемещении точки контакта в точки 1, 2,…, n напряжения уменьшаются и на половине оборота точка а разгружается полностью. Такое напряженное состояние в точках а и б при вращении внутреннего кольца можно оценить приблизительно эквивалентным.
При вращении наружного кольца (рис. 26.14) напряжённое состояние в точке б резко ухудшается; контактные напряжения вызовут усталостные разрушения прежде всего в этой точке. В то же время точка б будет значительно недогружена. Таким образом, наиболее благоприятным является случай вращения внутреннего кольца. При расчете этот фактор учитывают кинематическим коэффициентом V, который принимают:
V = 1 – при вращении внутреннего кольца;
V = 1,2 – при вращении наружного кольца.
26.8.Виды повреждений подшипников
1.Усталостное выкрашивание дорожек и тел качения является основным видом повреждения подшипников, хорошо смазываемых и защищённых от попадания абразивных частиц. Наблюдается после длительной работы в нормальных условиях.
2.Абразивный износ деталей распространен в подшипниках, не имеющих надёжной защиты от попадания абразивных частиц (в строительных, дорожных,
горных машинах и т.д.).
3.Разрушение сепараторов дает значительный процент выхода из строя подшипников качения, особенно быстроходных.
4.Раскалывание колец и тел качения связано с ударными и вибрационными перегрузками либо неправильным монтажом.
5.Остаточные деформации на беговых дорожках в виде лунок и вмятин
(бринеллирование), возникающие при больших статических нагрузках,
характерных для тяжелонагруженных тихоходных валов.
Для исключения разрушений беговых дорожек и тел качения в течение заданного ресурса подшипника выполняют расчёты по критериям прочности.
Существует две методики расчёта:
1.Расчёт на статическую грузоподъемность по остаточным деформациям.
2.Расчёт на ресурс (долговечность) по усталостному выкрашиванию.
26.9. Расчёт по динамической грузоподъёмности
Расчёт по заданному ресурсу выполняют при частоте вращения n 10 об/мин. При n = 1…10 об/мин в расчёт принимают n = 10 об/мин. Условие расчёта:
Cр C . |
(26.14) |
Динамическая грузоподъёмность С – это такая постоянная нагрузка,
которую подшипник может воспринимать в течение номинальной долговечности в 1 млн. оборотов. Значения С приведены в каталогах [9] для каждого
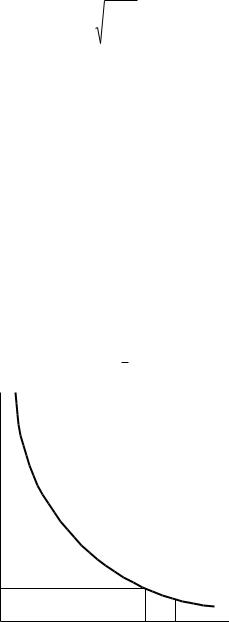
типоразмера подшипника. Потребная (расчётная) динамическая грузоподъёмность и ресурс связаны эмпирической зависимостью:
Cр P |
p |
L |
, |
(26.15) |
|
||||
|
|
a1 a2 |
|
где P – приведенная нагрузка;
p – показатель степени кривой усталости подшипника (p = 3 для шариковых и p = 3,33 для роликовых подшипников);
L – ресурс, млн. оборотов;
а1 – коэффициент надежности; при вероятности Р = 0,9 а1 = 1;
а2 – обобщённый коэффициент совместного влияния материала деталей подшипников и условий их эксплуатации [6].
На рис. 26.15 приведена кривая выносливости, соответствующая степенной зависимости
1 |
|
C P Lp . |
(26.16) |
C |
|
C |
|
90% 100% |
|
Рис. 26.15. Кривая выносливости
Базовая динамическая грузоподъёмность С гарантирована для 90%
подшипников определённого типоразмера. Следовательно, в партии выпущенных подшипников вероятность отказа составляет 10%, в то время как фактическая динамическая грузоподъёмность 90% подшипников в соответствии с кривой выносливости может быть значительно выше паспортной. При постоянной частоте вращения ресурс Lh удобнее считать в часах. В этом случае: