
Методички / Курс деталей машин
.pdf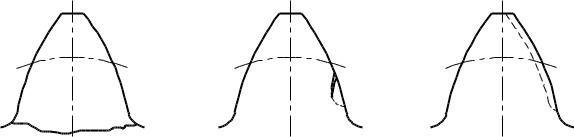
зуба H и F не являются постоянно действующими. Они изменяются во времени по пульсирующему циклу (рис. 4.12, б). Переменные напряжения являются причиной усталостного разрушения зубьев, которое проявляется различным образом.
1) Поломка зубьев. Поломка связана с напряжениями изгиба. Поломка зуба
(выламывание углов или целого зуба, рис. 14.13) является одним из распространённых и наиболее опасных видов разрушения, так как обломок зуба может попасть в зацепление и привести к аварии. Различают два вида поломки:
а) поломка от перегрузок ударного действия;
б) усталостная поломка, связанная с циклической нагрузкой и концентрацией напряжений.
Рис. 14.13. Излом |
Рис. 14.14. Выкрашивание |
Рис. 14.15. Износ |
Меры по предупреждению поломок:
а) расчёт по изгибным напряжениям;
б) увеличение модуля;
в) положительное смещение;
г) термообработка;
д) модифицирование зубьев (рис. 14.8).
Все остальные виды разрушения зубьев – поверхностные. Они связаны с контактными напряжениями и трением.
2) Усталостное выкрашивание. Такой вид разрушения характерен для закрытых зубчатых передач, работающих при хорошей смазке. Зубья таких передач разделены тонким слоем смазки. При этом износ зубьев мал. Передача
работает длительное время до появления усталости в поверхностных слоях зубьев. На контактной площадке малых размеров под действием силы Fn
появляются трещины, расположенные в подповерхностном слое, различно ориентированные на ведущем и ведомом профилях.
За счёт гидростатического давления трещины на поверхности ножек расклиниваются и частички металла со временем откалываются, образуя углубления, напоминающие оспинки, которые растут и превращаются в раковины
(рис. 14.14). Аналогичные процессы рассмотрены во фрикционной передаче (п. 2.9, рис. 2.11). Выкрашивание начинается обычно вблизи полюсной линии на ножке зуба. Причина выкрашивания – контактные напряжения.
В прирабатывающихся передачах (H2 < 350HB) имеет место ограниченное выкрашивание, когда края раковины сглаживаются (завальцовываются). При высокой твёрдости зубьев из "калёной" стали рост раковин протекает катастрофически быстро вследствие хрупкого разрушения их краёв, однако этот процесс происходит гораздо позже, чем в колёсах из "сырых" сталей.
Основные меры по предотвращению выкрашивания:
а) расчёт на выносливость по контактным напряжениям;
б) термообработка с целью повышения твёрдости;
в) повышение степени точности, особенно по норме контакта зубьев.
3) Абразивный износ. Износ является основной причиной выхода из строя
открытых зубчатых передач, работающих при недостаточой смазке. В таких передачах усталостное выкрашивание не наблюдается, так как поверхностные слои истираются раньше, чем появляются трещины усталости. У изношенной передачи вследствие искажения профиля (рис. 14.15) увеличиваются динамические нагрузки и снижается изгибная прочность, что может привести к поломке.
4) Заедание наблюдается преимущественно в высоконагруженных передачах. В месте соприкасания зубьев развивается высокая температура,
способствующая разрыву масляной пленки и образованию металлического контакта. Здесь происходит микросхватывание, своеобразное сваривание частиц металла с последующим отрывом их от менее прочной поверхности.

Образовавшиеся наросты задирают рабочие поверхности зубьев в направлении скольжения (рис. 14.16). Кромочный удар способствует заеданию. Уменьшить склонность к заеданию можно ограничением контактных напряжений.
Рис. 14.16. Задир |
Рис. 14.17. Пластические сдвиги |
5) Пластические сдвиги наблюдаются у тяжелонагруженных тихоходных зубчатых колёс, выполненных из "сырой" стали. При перегрузках на мягкой поверхности зубьев появляются пластические деформации с последующим сдвигом слоёв металла в направлении скольжения. В результате у полюсной линии ведомого колеса образуется хребет, а у ведущего – канавка (рис. 14.17).
Наличие неровностей нарушает правильность зацепления и приводит к динамическим нагрузкам. Анализируя виды разрушения, выявляют основные критерии работоспособности зубчатых передач:
а) контактная прочность;
б) изгибная прочность.
NB 14.5. Основными критериями работоспособности и расчёта зубчатых передач являются контактные и изгибные напряжения. Расчёт по первому критерию предотвращает усталостное выкрашивание и заедание, по второму – поломку зубьев.

Лекция №14
14.8. Расчёт по контактным напряжениям
Расчёты на прочность цилиндрических зубчатых передач стандартизированы по ГОСТ 21345. Задача расчёта состоит в определении таких значений основных параметров передачи, которые наилучшим образом удовлетворяют прочностным, триботехническим, кинематическим,
геометрическим и экономическим требованиям.
Исследованиями установлено, что наименьшей контактной усталостной прочностью обладает околополюсная зона рабочей поверхности зубьев. Поэтому расчёт контактных напряжений принято выполнять при контакте в полюсе зацепления (рис. 14.18).
W Fn
H
ω1 |
|
B1 |
|
w |
d/2 |
O1
Рис. 14.18. Контактные напряжения в зацеплении
Контакт зубьев можно рассматривать как контакт двух цилиндров с радиусами 1 и 2 . При этом контактные напряжения определяют по формуле Герца – формула (2.30):
|
q |
|
E |
|
|
Н |
|
|
|
. |
(14.28) |
|
2 (1 2 ) |
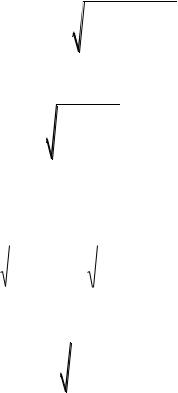
Удельную нагрузку определяют по формуле:
q |
Fn |
|
Ft cos b KH |
|
|
|
, |
(14.29) |
||
|
cos |
|
cos b |
|
|
|
||||
|
l |
w |
|
K |
|
|
||||
|
|
|
w |
|
|
где K – коэффициент, учитывающий неравномерность распределения нагрузки по длине контактной линии; K = 0,95 для косозубых колес;
KH – коэффициент нагрузки при расчёте по контактным напряжениям;
|
|
|
|
|
|
|
|
|
|
|
KH KH KH KHυ , |
|
|
|
|
|
|
|
|
|
|
|
|
|
|
|
|
(14.30) |
||||||||||||||||||||||||||
KH |
– коэффициент, учитывающий неравномерное распределение нагрузки |
|||||||||||||||||||||||||||||||||||||||||||||||||||||
между несколькими зацеплениями (в косозубой передаче). |
|
|
|
|
|
|
|
|
|
|||||||||||||||||||||||||||||||||||||||||||||
Радиус кривизны эвольвенты в полюсе зацепления: |
|
|
|
|
|
|
|
|
|
|||||||||||||||||||||||||||||||||||||||||||||
|
|
|
|
|
|
|
|
|
|
|
|
|
|
|
|
|
1 d1 sin w / 2 . |
|
|
|
|
|
|
|
|
|
|
|
|
|
(14.31) |
|||||||||||||||||||||||
С учетом эквивалентного диаметра (п. 14.2) радиус кривизны |
|
|
||||||||||||||||||||||||||||||||||||||||||||||||||||
|
|
|
|
|
|
|
|
|
|
|
d sin |
w |
/ 2cos2 |
. |
|
|
|
|
|
|
|
|
|
|
|
|||||||||||||||||||||||||||||
|
|
|
|
|
|
|
|
|
|
|
|
1 |
|
|
|
1 |
|
|
|
|
|
|
|
|
|
|
|
|
|
|
|
|
|
|
|
|
|
|
|
|
|
|
|
|
|
|
|
|
|
|
||||
Приведенная кривизна: |
|
|
|
|
|
|
|
|
|
|
|
|
|
|
|
|
|
|
|
|
|
|
|
|
|
|
|
|
|
|
|
|
|
|
|
|
|
|
|
|
|
|
|
|
|
|
|
|
||||||
|
|
1 |
|
1 |
|
|
|
1 |
|
|
|
2cos2 |
|
|
|
2cos2 |
|
|
|
|
2cos2 |
|
u 1 |
. |
(14.32) |
|||||||||||||||||||||||||||||
|
|
|
|
|
|
|
2 |
|
d cos |
w |
|
|
d |
2 |
cos |
w |
|
d cos |
w |
|
u |
|
||||||||||||||||||||||||||||||||
|
|
|
|
|
|
|
|
|
|
|
|
|
|
|
|
|
||||||||||||||||||||||||||||||||||||||
|
|
|
|
1 |
|
|
|
|
|
|
|
|
|
|
1 |
|
|
|
|
|
|
|
|
|
|
|
|
|
|
|
|
|
|
|
|
|
|
1 |
|
|
|
|
|
|
|
|
||||||||
С учетом (14.31) и (14.32) формула Герца примет вид: |
|
|
|
|
|
|
|
|
|
|||||||||||||||||||||||||||||||||||||||||||||
|
|
|
|
|
|
|
|
|
|
|
|
|
|
|
|
|
|
|
|
|
|
|
|
|
|
|
|
|
|
|
|
|
|
|
|
|
|
|
|
|||||||||||||||
|
|
|
|
|
|
|
|
|
Z |
|
Z |
|
Z |
|
|
|
Ft KH |
|
u 1 |
, |
|
|
|
|
|
|
|
|
(14.33) |
|||||||||||||||||||||||||
|
|
|
|
|
|
H |
H |
M |
|
|
|
|
|
|
|
|
|
|
|
|
|
|
|
|
|
|||||||||||||||||||||||||||||
|
|
|
|
|
|
|
|
|
|
|
|
|
|
|
|
|
|
|
|
bw d1 |
|
u |
|
|
|
|
|
|
|
|
|
|
|
|
|
|
||||||||||||||||||
|
|
|
|
|
|
|
|
|
|
|
|
|
|
|
|
|
|
|
|
|
|
|
|
|
|
|
|
|
|
|
|
|
|
|
|
|
|
|
|
|
|
|||||||||||||
где ZH – коэффициент, учитывающий форму сопряжённых поверхностей; |
||||||||||||||||||||||||||||||||||||||||||||||||||||||
|
|
|
|
|
|
|
|
|
|
|
|
|
|
|
|
|
|
|
|
|
|
|
|
|
|
|
|
|
|
|
|
|
|
|
|
|
|
|
|
|
|
|
|
|
|
|
||||||||
|
|
|
|
|
|
|
|
|
|
|
|
Z |
|
|
|
|
2cos2 |
; |
|
|
|
|
|
|
|
|
|
|
|
|
|
|
|
|
|
|
(14.34) |
|||||||||||||||||
|
|
|
|
|
|
|
|
|
|
|
|
H |
|
sin 2 w |
|
|
|
|
|
|
|
|
|
|
|
|
|
|
|
|
|
|
||||||||||||||||||||||
|
|
|
|
|
|
|
|
|
|
|
|
|
|
|
|
|
|
|
|
|
|
|
|
|
|
|
|
|
|
|
|
|
|
|
|
|
|
|
||||||||||||||||
|
|
|
|
|
|
|
|
|
|
|
|
|
|
|
|
|
|
|
|
|
|
|
|
|
|
|
|
|
|
|
|
|
|
|
|
|
|
|
|
|
||||||||||||||
ZM |
– коэффициент, |
|
учитывающий |
|
механические |
свойства материалов |
||||||||||||||||||||||||||||||||||||||||||||||||
колёс; |
|
|
|
|
|
|
|
|
|
|
|
|
|
|
|
|
|
|
|
|
|
|
|
|
|
|
|
|
|
|
|
|
|
|
|
|
|
|
|
|
|
|
|
|
|
|
|
|
|
|
|
|
|
|
|
|
|
|
|
|
|
|
|
|
|
|
|
|
|
|
|
|
|
|
|
|
|
|
|
|
|
|
|
|
|
|
|
|
|
|
|
|
|
|
|
|
|
|
|
|
|
|
|||||||
|
|
|
|
|
|
|
ZM |
|
|
|
|
|
E |
|
|
|
|
|
|
|
|
|
|
|
|
|
|
|
|
|
2E1E2 |
|
|
; |
|
|
|
|
(14.35) |
|||||||||||||||
|
|
|
|
|
|
|
|
|
(1 2 ) |
|
|
|
|
(E E ) |
(1 2 ) |
|
|
|
|
|||||||||||||||||||||||||||||||||||
|
|
|
|
|
|
|
|
|
|
|
|
|
|
|
|
|
|
|
|
|
|
|
|
|
|
|
|
|
|
|
1 |
|
|
|
|
2 |
|
|
|
|
|
|
|
|
|
|
|
|
|
|
|
|
||
Z – коэффициент, учитывающий суммарную длину контактных линий; |
||||||||||||||||||||||||||||||||||||||||||||||||||||||
|
|
|
|
|
|
|
|
|
|
|
|
|
|
|
|
|
|
|
|
|
|
|
|
|
|
|
|
|
|
|
|
|
|
|
|
|
|
|
|
|
|
|
|
|
|
|
|
|
|
|
|
|
||
|
|
|
|
|
|
|
|
|
|
|
|
|
|
|
|
Z |
|
|
|
|
|
|
|
1 |
|
|
|
|
. |
|
|
|
|
|
|
|
|
|
|
|
|
|
|
|
|
|
|
(14.36) |
||||||
|
|
|
|
|
|
|
|
|
|
|
|
|
|
|
|
|
|
|
|
|
|
|
|
|
|
|
|
|
|
|
|
|
|
|
|
|
|
|
|
|
|
|
|
|
|
|
||||||||
|
|
|
|
|
|
|
|
|
|
|
|
|
|
|
|
|
|
|
K |
|
|
|
|
|
|
|
|
|
|
|
|
|
|
|
|
|
|
|
|
|
||||||||||||||
|
|
|
|
|
|
|
|
|
|
|
|
|
|
|
|
|
|
|
|
|
|
|
|
|
|
|
|
|
|
|
|
|
|
|
|
|
|
|
|
|
|
|
|
|
|
|
|
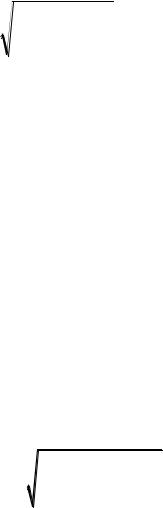
Формулу (14.33) можно видоизменить и упростить, приняв стальные колёса
с E E 2,15 105 |
|
МПа и |
|
μ = |
|
0,3, |
|
коэффициент |
перекрытия |
|
|
1,8, |
|||||||||||||
1 2 |
|
|
|
|
|
|
|
|
|
|
|
|
|
|
|
|
|
|
|
|
|
|
|
|
|
коэффициент K 0,95, угол |
|
зацепления w 20º, а |
параметры |
Ft |
|
и d1 |
|||||||||||||||||||
записать с учётом геометрических соотношений: |
|
|
|
|
|
|
|
|
|
|
|||||||||||||||
d |
|
d u ; a |
|
|
d1 d2 |
|
|
d1 |
(u 1) , откуда d |
|
2 aw |
|
, |
|
(14.37) |
||||||||||
2 |
w |
|
|
|
|
|
|
|
|
||||||||||||||||
|
1 |
|
|
|
2 |
2 |
|
|
|
|
|
1 |
|
u 1 |
|
|
|
|
|||||||
|
|
|
|
|
|
|
|
|
|
|
|
|
|
|
|
|
|
||||||||
|
|
Ft 2T2 / d2 |
2T2 / d1u T2 (u 1) / awu . |
|
|
(14.38) |
|||||||||||||||||||
После упрощений формула проверочного расчёта примет вид: |
|
|
|
|
|||||||||||||||||||||
|
|
|
|
|
|
|
|
|
|
|
|
|
|
|
|
|
|
|
|
|
|
|
|
||
|
|
H |
|
K |
a |
|
T K |
H |
(u 1)3 |
|
[ H ] . |
|
|
|
|
|
|
|
|||||||
|
|
|
2 |
|
|
|
|
|
|
|
|
(14.39) |
|||||||||||||
|
|
aw u |
|
|
|
|
|
bw |
|
|
|
|
|
|
|||||||||||
|
|
|
|
|
|
|
|
|
|
|
|
|
|
|
|
|
|
|
|
|
|
где Ka – численный коэффициент, равный 270 для косозубых и шевронных колес и 315 – для прямозубых; величина коэффициента соответствует единицам измерения Ньютон и миллиметр, то есть Т2 в Н мм, bw в мм, Н в МПа (Н/мм2).
Формула (14.39) не пригодна для проектного расчета, так как содержит два неизвестных геометрических параметра aw и b. Для дальнейшего упрощения решения задачи один параметр выражают через другой. Вводят коэффициент ширины колеса
|
a bw / aw , откуда bw a aw . |
(14.40) |
Коэффициент a |
для косозубых колес принимают a = |
0,2…0,5. |
Подставляя (14.40) в формулу (14.39) и решая её относительно aw , получают
формулу проектного расчёта:
|
(u 1) |
|
|
K |
a |
2 |
T K |
H |
|
|
a |
3 |
|
|
|
2 |
. |
(14.41) |
|||
|
|
|
|
|||||||
w |
|
|
|
|
a |
|
|
|
||
|
|
|
|
[ ] u |
|
|
|
|||
Вычисленное значение aw |
округляют до ближайшего значения либо по |
ГОСТ 2185, либо из ряда Ra40 ГОСТ 6636 (Прил. 15). Остальные геометрические параметры определяют в результате расчёта геометрии. В дальнейшем определяют окружную скорость, уточняют коэффициенты нагрузки, определяют силы в зацеплении и выполняют проверку контактных и изгибных напряжений.

При расчёте внутреннего зацепления в формулах (14.39) и (14.41) ставят (u - 1)
вместо (u + 1).
В реечной передаче должны быть известны: Ft - окружная сила на шестерне, v – скорость рейки. Делительный диаметр из расчёта на контактную выносливость:
d |
480 |
|
Ft KH |
. |
(14.42) |
||
|
|
||||||
1 |
[ H |
] |
d |
|
|||
|
|
Рекомендуется коэффициент ширины d = b/d1 = 0,4…0,8. Предварительное значение модуля:
m |
4,5 Ft KF |
. |
(14.43) |
||
|
|||||
|
d [ |
F |
] |
|
|
|
d 1 |
|
|
|
Число зубьев шестерни реечной передачи z1 = d1/m 12. После округления модуля и числа зубьев уточняют диаметр шестерни: d1 = mz1.
14.9. Расчёт по изгибным напряжениям
Расчётная схема представлена на рис. 14.19. Зуб рассматривают как консольную балку, нагруженную нормальной силой Fn , которая приложена к кромке зуба (наиболее неблагоприятный случай). Предпосылки расчёта:
1) Вся нагрузка прямозубого зацепления передается одной парой зубьев и приложена к вершине зуба. Нормальная сила будет в этом случае располагаться не под углом зацепления w , а под углом давления w 28…30 для прямозубой передачи.
2)Влиянием сил трения пренебрегают ввиду их малости.
3)Зуб рассматривают как консольную балку, для которой справедлива гипотеза плоских сечений, следовательно, методы сопротивления материалов.
Нормальную силу Fn переносят на ось симметрии зуба и раскладывают на две составляющие: силу Fr Fn sin , направленную по оси симметрии, и ей перпендикулярную силу Ft Fn cos . Составляющие силы приводят к опасному сечению с размерами b и s, расположенному вблизи основания зуба. При
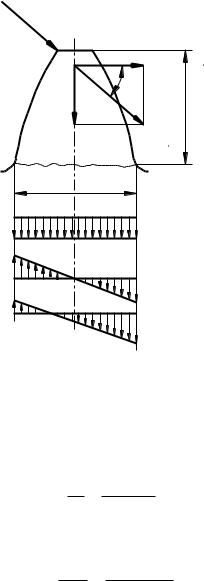
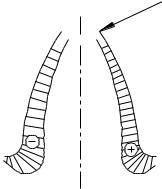
KF – коэффициент нагрузки,
KF KF KF KFυ . |
(14.47) |
1,67 1,09
3,64 3,15
Рис. 14.20. Концентрация напряжений на ножке зуба
Для упрощения расчетов используют геометрическое подобие зубьев различного модуля и выражают параметры через безразмерные коэффициенты l и s:
|
|
|
|
l l m ; |
|
s s m . |
|
|
|
|
(14.48) |
|||||
После подстановки получают: |
|
|
|
|
|
|
|
|
|
|
|
|
||||
F |
F K |
F |
|
6 l cos |
|
sin |
K |
T |
YF |
F K |
F |
[ ], |
|
|||
t |
|
|
|
|
|
|
|
t |
(14.49) |
|||||||
|
|
(s ) |
2 |
|
|
|
|
|
|
|||||||
|
m |
|
|
|
|
s |
|
cos w |
|
bwm |
|
где YF – коэффициент формы зуба.
YF |
KT |
|
6 l cos |
|
sin |
|
||
|
|
|
|
|
. |
(14.50) |
||
|
(s ) |
2 |
|
|||||
|
cos w |
|
|
s |
|
|
Форма зуба зависит, в основном, от числа зубьев колеса z и коэффициента смещения инструмента x. С улучшением формы зуба коэффициент формы зуба уменьшается, так как он характеризует напряжение изгиба при единичной нагрузке (q = 1) и единичном размере зуба (m = 1 мм). Например, в прямозубых колёсах при z = 20…80 и смещении x = 0 YF = 4,07…3,6. При коэффициенте смещения x = + 0,5 и z = 20 YF = 3,39, что свидетельствует об улучшении формы зуба (о повышении изгибной прочности). Формула проверочного расчёта на
изгиб, например, шестерни: |
|
F1 = YF1Y Ft KFαKF KFν KFд/(b1m) ≤ [ F], |
(14.51) |
