
Методички / Курс деталей машин
.pdfбыть больше диаметра вала из условия центрирования по цилиндру по соотношению:
lст = (1,2…1,5)d. |
(8.4) |
Длину стандартной шпонки принимают l |
lст – 5 мм и округляют по ряду |
Ra20 ГОСТ 6636 (Прил. 15). Из двух видов напряжений наиболее опасными являются напряжения смятия, поэтому в расчётах используют только формулу
(8.1). Допускаемое напряжение смятия определяют по известной зависимости:
[ см] = T /s. При нереверсивной нагрузке рекомендуется принимать s = 1,9…2,3;
при частых запусках и остановках s = 2,9…3,5; при реверсивной нагрузке коэффициент запаса повышают на 30%.
С достаточной точностью при стальной ступице можно принимать [ см] =
100 МПа при переходных посадках и [ см] = 150…200 МПа при посадках с натягом. При колебаниях нагрузки их следует снижать на 20…25%, при ударной нагрузке – на 40…50%. При чугунной ступице напряжения уменьшают в два раза.
Размеры сечений шпонок b h выбирают в зависимости от диаметра вала d
из справочников [5, 9]. Если при проверке рабочие напряжения смятия окажутся значительно меньше допускаемых, то можно взять сечение на один размер меньше и расчёты повторить. В случае, когда одна шпонка не может передать заданную нагрузку, шпоночное соединение заменяют шлицевым.
Обозначение: Шпонка b h l ГОСТ 23360-78.
Пример 8.1. Подобрать призматическую шпонку и проверить её по напряжениям смятия по следующим исходным данным: диаметр вала d = 50 мм,
крутящий момент на валу Т = 250 Н м, материал ступицы сталь 45. Нагрузка реверсивная, с частыми запусками и остановками. Шпоночное соединение – основное, посадка – переходная.
Решение.
Предел текучести стали 45 T = 360 МПа (прил. 9). Допускаемое напряжение смятия [ см] = 360/(3,2 1,3) = 86,5 МПа. Принимаем по диаметру вала шпонку с размерами: ширина b = 14 мм, высота h = 9 мм, глубина паза втулки t2 = 3,8 мм [9]. Длина ступицы lст = (1,2…1,5) 50 = 60..75 мм. Принимаем
lст = 70 мм (прил. 15). Принимаем длину шпонки l = 63 мм [9]. Расчётная длина шпонки lp = 63 – 14 = 49 мм. Рабочие напряжения смятия:
см |
|
2 250 |
103 |
53,7МПа см 86,5МПа. |
|
50 49 |
3,8 |
||||
|
|
|
Вывод. Прочность достаточна. Принята шпонка 14 9 63 ГОСТ 23360-78.
Лекция №11
8.3. Соединения сегментными шпонками
Сегментные шпонки распространены меньше призматических. Шпонки изготавливают из чистотянутых сегментных профилей диаметром dш. Высота шпонки h = 0,4 dш, длина l = dш. Шпонки имеют более глубокую посадку (рис. 8.2), не перекашиваются под нагрузкой и не требуют ручной пригонки. Их ставят на относительно тонких участках валов (до 38 мм). При длинных ступицах можно ставить в ряд по оси вала две сегментные шпонки.
Принцип работы сегментных шпонок подобен принципу работы призматических шпонок. Размеры шпонок приведены в справочниках [5, 9].
Расчёт на смятие выполняют по формуле, аналогичной (8.1):
см |
2T |
см . |
(8.5) |
|
|||
|
d l t2 |
|
Обозначение: Шпонка b × h × D ГОСТ 24071-80.
Пример 8.2. Подобрать сегментную шпонку и проверить её по напря-
жениям смятия по следующим исходным данным: диаметр вала d = 30 мм,
крутящий момент на валу Т = 200 Н м, материал ступицы сталь 35. Нагрузка нереверсивная. Шпоночное соединение – основное, посадка – переходная.
Решение.
Предел текучести стали 35 T = 300 МПа (прил. 8). Допускаемое напряжение смятия [ см] = 360/2,1 = 142,9 МПа (коэффициент запаса s в п. 8.2).
Принимаем по диаметру вала шпонку с размерами: ширина b = 8 мм, высота h =
11 мм, глубина паза втулки t2 = 3,3 мм, диаметр шпонки dш = 28 мм (прил. 19).
Длина шпонки l = dш = 28 мм. Рабочие напряжения смятия:
см |
|
2 200 |
103 |
144,3МПа см 142,9МПа. |
|
30 28 |
3,3 |
||||
|
|
|
Вывод. Прочность достаточна, так как рабочее напряжение незначительно ниже допускаемого. Принята шпонка 8 11 28 ГОСТ 24071-80.
8.4. Соединение клиновыми шпонками
Клиновые шпонки (рис. 8.3) располагают в пазу с зазором по боковым граням, а рабочими являются широкие грани шпонки. Передача крутящего момента от вала к ступице осуществляется, в основном, силами трения, которые образуются в соединении от запрессовки шпонки (забивки шпонки в паз). При этом в деталях возникают напряжения смятия по широким граням и по полуцилиндру.
Клиновая форма шпонки может вызвать перекос детали, при котором её торцовая плоскость не будет перпендикулярна оси вала. Обработка паза в ступице с уклоном, равным уклону шпонки (1:100), создаёт дополнительные технологические трудности и часто требует индивидуальной пригонки шпонки по пазу, что недопустимо в условиях крупносерийного и массового производства.
Разновидностью клиновых шпонок являются тангенциальные шпонки (рис. 8.4), которые ставят попарно в паз, располагая их наклонными поверхностями друг к другу и забивая их в противоположные стороны. При необходимости реверса ставят два комплекта шпонок с их расположением под 120 . Размеры клиновых шпонок приведены в литературе [2, 3, 9]. Применение клиновых шпонок значительно сократилось, что позволяет не рассматривать их конструктивные разновидности и расчёт на прочность.
Тема 9: Шлицевые соединения
9.1. Оценка и применение
Шлицевое соединение (рис. 9.1) условно можно рассматривать как много-
шпоночное, у которого шпонки выполнены заодно с валом в виде наружных зубьев, вследствие чего их называют также зубчатыми соединениями. В
отверстии ступицы 2 протяжкой нарезают внутренние зубья, наружные зубья на валу 1 фрезеруют. По сравнению со шпоночными шлицевые соединения имеют следующие достоинства:
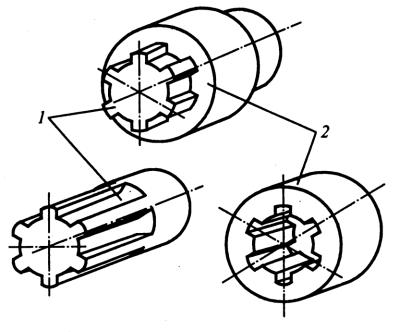
1) Меньше радиальные габариты.
Рис. 9.1. Шлицевое соединение
2)Высокая несущая способность.
3)Взаимозаменяемость.
4)Хорошее центрирование деталей.
Эти преимущества позволяют использовать соединения в условиях массового производства и при большой угловой скорости валов. Шлицевые соединения нашли широкое применение в высоконапряжённых машинах
(автотракторная промышленность, станкостроение, авиастроение,
сельхозмашиностроение). Соединения обеспечивают жёсткое фиксирование деталей в окружном направлении и допускают их взаимные осевые перемещения
(подвижные соединения).
Недостатки:
1)Концентрация напряжений (меньшая, чем у шпоночных соединений).
2)Относительная сложность изготовления.
9.2. Классификация и геометрия
По форме профиля зубьев различают три вида соединений: прямобочные,
эвольвентные и треугольные.
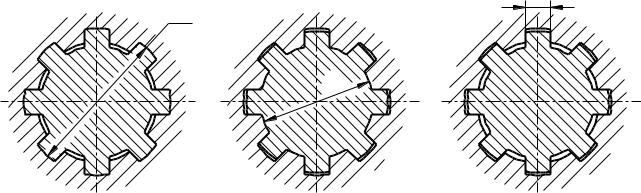
А) Соединения с прямобочными зубьями (рис. 9.2) наиболее распро-
странены в машиностроении. В зависимости от числа зубьев (z = 6…20) и их высоты предусмотрены три серии соединений: легкая, средняя и тяжелая. При переходе от легкой к тяжёлой серии увеличивается число зубьев, внешний диаметр и, как следствие, нагрузочная способность.
b
a) |
D б) |
в) |
|
|
d |
Рис. 9.2. Поверхности центрирования
Центрирование осуществляют по внешнему D (рис 9.2, а) или внутреннему d (рис. 9.2, б) диаметрам зубьев, а также по боковым поверхностям зубьев b (рис. 9.2, в). При центрировании по диаметрам соединение имеет минимальные зазоры по поверхностям диаметров D или d и ограниченный зазор по боковым сторонам.
По нецентрирующему диаметру предусмотрен значительный зазор.
Центрирование по диаметрам D и d обеспечивает высокую соосность вала и ступицы и применяется в соединениях, к которым предъявляются повышенные требования к точности вращения сопряжённых деталей (например, зубчатых колёс) для увеличения их долговечности.
Диаметр центрирования (D или d) выбирают, исходя из технологических условий. Проще и экономичнее центрирование по наружному диаметру D, так как центрирующие поверхности допускают точную и производительную обработку:
вала – круглым шлифованием, ступицы – протягиванием. Этот способ реализуется при твёрдости ступицы Н2 < 350 НВ. При Н2 > 350 НВ рекомендуется центрирование по d.
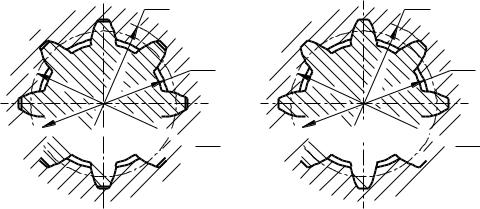
Центрирование по боковым граням b (рис. 9.2, в) обеспечивает более равномерное распределение нагрузки по зубьям. Поэтому его применяют в соединениях, подверженных реверсивным динамическим нагрузкам (например, в
скользящих шлицевых соединениях карданных валов автомобилей). Оно не гарантирует соосности вала и ступицы, но имеет высокую нагрузочную
способность.
Обозначение центрирующей поверхности в обозначении соединения ставят
на первом месте. Обозначение при центрировании по наружному диаметру:
D – z × d × D × b ; например, |
|
|
D – 8 × 36 × 40H8/h7 × 7F10/h9 |
ГОСТ 1139-80. |
|
Обозначение отверстия втулки: |
|
|
D – 8 × 36 × 40H8 × 7F10 |
ГОСТ 1139-80. |
|
Обозначение вала: |
|
|
D – 8 × 36 × 40h7 × 7h9 |
ГОСТ 1139-80. |
|
Рекомендуются при центрировании |
по диаметрам сопряжения |
H10/a11…H12/a11 по нецентрирующим диаметрам; их в обозначении допускается не указывать. Рекомендуемые посадки приведены в [2, 5]. Основные размеры прямобочных шлицевых соединений приведены в прил. 20 и в [5,11].
Б) Соединения с эвольвентными шлицами выполняют с центрированием по боковым граням b (рис. 9.3, а) или по наружному диаметру вала D (рис. 9.3, б).
Наиболее распространён первый способ центрирования.
a) |
D |
б) |
D |
|
|
||
|
d |
|
d |
dср
dср
Рис. 9.3. Эвольвентные шлицевые соединения
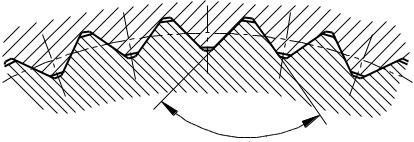
Эвольвентные соединения по сравнению с прямобочными:
1) более технологичны; более современная технология заключается в том,
что эвольвентные зубья протяжки и самого соединения можно изготовлять на зуборезных станках, отсюда:
2)более высокая точность, близкая к точности зубчатых колес;
3)более высокая прочность на смятие благодаря большей площади контакта
ибольшему числу зубьев и на изгиб благодаря рациональной форме зуба;
4)меньшая концентрация напряжений.
Недостатками являются более высокая стоимость протяжек и трудоёмкость шлифования эвольвентных зубьев. Эвольвентные шлицевые соединения получили преимущественное применение в экономически развитых странах. Обозначение соединения:
– при центрировании по боковым сторонам зубьев:
D × m × (посадка по b);
– при центрировании по наружному диаметру:
D × (посадка по D) × m; например,
50 × H7/g6 × 2 ГОСТ 6033-80.
Основные размеры эвольвентных шлицевых соединений приведены в [5,9].
В) Соединения с треугольными зубьями (рис. 9.4) стандартизированы, их применяют, главным образом, как неподвижные при тонкостенных втулках, а
также в соединениях стальных валов со ступицами из легких сплавов, в
приборостроении. Это соединение имеет большое число мелких зубьев.
Соединение центрируют по боковым сторонам зубьев, их размеры выполняют по отраслевым стандартам.
O
Рис. 9.4. Треугольные шлицы
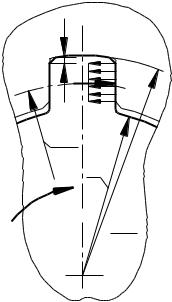
9.3. Проектирование и расчёт соединений
Основные размеры (наружный диаметр D и длину l) шлицевого соединения задают при конструировании вала. Длину соединения принимают не более 1,5D;
при большей длине ступицы существенно возрастают неравномерность распределения нагрузки вдоль зубьев и трудность изготовления.
Основными критериями работоспособности шлицевых соединений является сопротивление рабочих поверхностей зубьев смятию и коррозионно-
механическому изнашиванию. Коррозионно-механическое изнашивание возникает при очень малых колебательных относительных перемещениях сопряженных поверхностей, возникающих при изгибе и скручивании вала. Соединение,
нагруженное только крутящим моментом Т (муфта) на износ не рассчитывают.
А) Расчёт по напряжениям смятия. Расчётная схема приведена на рис. 9.5.
f
|
Ft |
dm |
см |
|
d |
T D
Рис.9.5. Расчётная схема прямобочных шлицев
Условие прочности:
|
|
|
2T |
|
T |
[ |
|
], |
(9.4) |
|
см |
dm z h l |
SF l |
см |
|||||||
|
|
|
|
|
|
|||||
|
|
|
|
|
|
|
|
|||
где dm – средний диаметр; |
|
|
|
|
|
|
|
|
|
|
dm 0,5(D d ); |
dm mz для эвольвентных зубьев; |
(9.5) |
h – рабочая высота профиля зубьев; |
|
|
h 0,5(D d) 2 f ; |
h m для эвольвентных зубьев; |
(9.6) |
f – координата фаски;
l – рабочая длина зубьев;
– коэффициент, учитывающий неравномерное распределение нагрузки между зубьями и вдоль зубьев; = 0,7…0,8;
SF – удельный суммарный статический момент площади рабочих поверхностей в мм3/мм; принимается для прямобочных шлицевых соединений из
прил. 20 или из [5].
Допускаемые напряжения смятия назначают в зависимости от назначения машины и специфики эксплуатации. Значения [ см ] для изделий общего машиностроения и подъёмно-транспортных устройств приведены в прил. 21.
Пример 9.1. Подобрать и проверить на смятие прямобочное шлицевое со-
единение по следующим исходным данным: диаметр вала d = 60 мм, крутящий момент на валу Т = 2000 Н м. Втулка стальная твёрдостью Н2 < 350 НВ. Соеди-
нение неподвижное. Условия эксплуатации средние. Привести обозначение со-
единения с центрированием по d.
Решение.
Допускаемое напряжение смятия [ см] = 80 МПа (прил. 21). Длина ступицы l = (1,2…1,5) 60 = 72...90 мм. Принимаем l = 80 мм (прил. 15). Принимаем прямобочное шлицевое соединение 8 × 62 × 68 × 12 с f = 0,5 мм и SF = 520 мм3/мм
(прил. 20). Рабочие напряжения смятия:
|
|
|
2000 103 |
|
|
||
|
см |
|
|
|
48,1МПа [ |
см |
] 80МПа. |
|
|
||||||
|
|
520 |
80 |
|
|||
|
|
|
|
|
Вывод. Прочность достаточна. Принято соединение d – 8 × 62H8/e8 × 68
H10/a11 × 12F10/f8 ГОСТ 1139-80.
Пример 9.2. Подобрать и проверить на смятие эвольвентное шлицевое со-
единение по следующим исходным данным: расчётный диаметр D = 70 мм, кру-
тящий момент на валу Т = 3200 Н м. Втулка стальная твёрдостью Н2 > 350 НВ .
Соединение неподвижное. Условия эксплуатации хорошие. Привести обозначе-
ние соединения с центрированием по b.