
Методички / Курс деталей машин
.pdfC |
EA |
; |
l |
. |
(2.37) |
|
|
||||
|
l |
|
EA |
|
Расчёты по изгибной и крутильной жёсткости изучаются при расчёте валов.
Вопросы для самоподготовки по темам 1 и 2
1.Что такое деталь?
2.Что такое сборочная единица?
3.Каковы основные задачи курса?
4.Что следует понимать под основными критериями работоспособности и расчёта деталей машин?
5.Каков порядок проектирования деталей машин?
6.Каковы характеристики цикла переменных напряжений?
7.Как определить циклические напряжения?
8.В чём заключается концентрация напряжений и как она учитывается в расчётах?
9.Как влияют абсолютные размеры деталей на усталостную выносливость?
10.Каковы причины влияния состояния поверхности детали на усталостную выносливость?
11.Как определяют предельные напряжения при малом числе циклов нагружения?
12.В чём заключается дифференцированный метод определения допускаемого коэффициента запаса прочности?
13.Как происходит потеря сопротивлению усталости?
14.Какие виды разрушения поверхности происходят при чрезмерных контактных напряжениях?
15.Каковы предпосылки расчёта по контактным напряжениям?
16.Что такое коэффициенты жёсткости и податливости?
Вопросы по темам 1 и 2, выносимые на экзамен
1.Понятия «деталь», «сборочная единица». Цели и задачи дисциплины
«Детали машин и основы проектирования».
2.Основные критерии работоспособности и расчёта деталей машин. Порядок проектирования деталей машин.
3.Виды нагрузок, действующих на детали машин. Циклы напряжений,
характеристики циклов.
4.Допускаемые напряжения. Коэффициенты запаса прочности.
Дифференцированный метод определения допускаемых коэффициентов запаса прочности.
5.Факторы, влияющие на величину допускаемого напряжения: концентрация напряжений, абсолютные размеры, качество поверхности, число циклов нагружения. Учёт этих факторов в расчётах.
6.Контактная прочность. Контактные напряжения. Предпосылки расчёта.
Формула Герца.
Вопросы, выносимые на Олимпиаду
1.Понятия «деталь», «сборочная единица». Основные критерии работоспособности и расчёта деталей машин.
2.Виды нагрузок, действующих на детали машин. Циклы напряжений,
характеристики циклов.
3.Факторы, влияющие на прочность.
4.Допускаемые напряжения. Коэффициенты запаса прочности.
Дифференцированный метод определения допускаемых коэффициентов запаса прочности.
5.Объёмная прочность. Потеря сопротивления усталости. Потеря статической прочности. Основы расчёта на прочность.
6.Контактная прочность. Контактные напряжения. Предпосылки расчёта.
Формула Герца.
7.Жёсткость деталей машин. Расчёты на жёсткость при растяжении.
Тема 3: Соединения
Узлы, а также машины, приборы и аппараты в целом собирают из деталей в определенном взаимном положении. Образующиеся при этом связи можно разделить на подвижные и неподвижные. Наличие подвижных связей в машине обусловлено её кинематической схемой. Например, в редукторе такими связями обладают зацепления, подшипники.
Неподвижные связи обусловлены целесообразностью расчленения машины на узлы и детали для того, чтобы упростить производство, облегчить сборку,
ремонт, транспортировку и т. п. Неподвижные связи в технике называют
соединениями. По признаку разъёмности все виды соединений можно разделить на разъёмные и неразъёмные.
Разъёмные соединения позволяют разъединять детали без их повреждения.
К ним относятся резьбовые, шпоночные, шлицевые, штифтовые и другие соединения. Неразъёмные соединения не позволяют разъединять детали без их разрушения или повреждения поверхностей. К этой группе соединений относятся:
сварные, клёпанные, прессовые, паяные, клеевые.
NB 3.1. Соединениями в технике называются неподвижные связи в сборочных единицах.
Соединения являются важными элементами конструкции. Многие отказы в
работе машин и сооружений обусловлены неудовлетворительным качеством
соединений.
NB 3.2. Основным критерием работоспособности и расчёта соединений является прочность.
Необходимо стремиться к тому, чтобы соединение было равнопрочным с соединяемыми элементами. Мерой качественной оценки равнопрочности может служить коэффициент прочности:
φ =[σ]'/[σ] 1, (3.18)
где [σ]' – напряжение, допускаемое соединением;
[σ] – напряжение, допускаемое основным материалом детали.
В отдельных случаях в формуле (3.18) может быть отношение площадей расчётных сечений. При φ = 1 достигается равнопрочность (например, в
стыковых швах сварных соединений). В заклёпочных же соединениях равнопрочность никогда не будет обеспечена вследствие ослабления соединяемых деталей отверстиями.
Тема 4: Сварные соединения
4.1. Общие сведения
Сварные соединения получают за счёт формирования межатомных связей
в свариваемых деталях, возникающих в результате нагрева деталей до жидкого или тестообразного состояния. На практике применяют свыше 60 способов сварки. Приоритет многих из них принадлежит русской науке. Благодаря открытию в 1802 году Петровым Н. П. явления электрической дуги Бенардос Н.
Н. в 1882 году предложил способ электродуговой сварки неплавящимся электродом. В 1888 году Славянов Н. Г. использовал в способе Бенардоса Н. Н.
плавящийся электрод. Этот способ широко используется и в наши дни.
В СССР был изобретён способ электросварки под флюсом, который повысил производительность в несколько раз и качество сварного шва. В
сороковые годы в нашей стране получил развитие способ электрошлаковой сварки, который позволяет сваривать детали неограниченной толщины
(например, до 2000 мм). Его применение позволяет заменить сложные и тяжелые цельнолитые и цельнокованые конструкции сварными из отдельных простых элементов. Электросварка подразделяется на два основных вида – дуговую и контактную.
4.2. Классификация сварных соединений и швов.

В зависимости от расположения свариваемых деталей различают следующие виды соединений: стыковые, нахлёсточные, тавровые, угловые.
Условные изображения и обозначения швов сварных соединений регламентированы ГОСТ 2.312. Сварной шов независимо от способа сварки изображают на чертеже соединения сплошной основной линией, невидимый – штриховой линией. От изображения шва проводят линию-выноску,
заканчивающуюся односторонней стрелкой. Упрощенная структура условного изображения шва следующая (примеры на рис. 4.1 и 4.2):
1)Обозначения стандарта на типы и конструктивные элементы швов соединений. Например:
ГОСТ 5264-80. Ручная дуговая сварка. Соединения сварные.
ГОСТ 8713-80. Сварка под флюсом. Соединения сварные.
2)Буквенно-цифровое обозначение швов (некоторые обозначения приведены в Прил. 1).
3)Знак и размер катета шва (для угловых швов, рис. 4.2).
В стыковых соединениях свариваемые детали соединяются своими торцами;
они имеют прочность, близкую к прочности основного металла, и применяются, в
основном, в ответственных конструкциях. В зависимости от толщины деталей сварку выполняют односторонним или двухсторонним стыковым швом, а также при необходимости производят подготовку кромок (рис. 4.1).
С2
С5
ГОСТ 5264-80-С5
Рис. 4.1. Стыковые швы
В нахлёсточных соединениях боковые поверхности одной детали частично перекрывают боковые поверхности другой (рис. 4.2). Соединение осуществляется
угловыми швами.
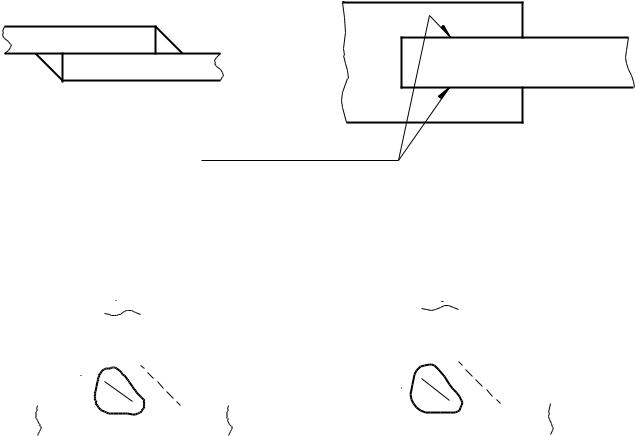
В тавровых соединениях торец одной детали соединяется с боковой поверхностью другой детали (рис. 4.3).
ГОСТ 5264-80-H2- 5
Рис. 4.2. Нахлёсточное соединение
|
|
|
T1 |
|
|
У1 |
|
|
|
|
|
|
|||
|
|
|
|
|
|
||
|
|
|
|
|
|
|
|
|
|
|
|
|
|
|
|
|
|
|
|
|
|
|
|
Рис. 4.3. Тавровое соединение |
Рис. 4.4. Угловое соединение |
Угловые соединения являются частным |
случаем тавровых соединений |
(рис. 4.4). Последние два вида соединений осуществляются двумя видами швов:
стыковыми и нахлёсточными, поэтому приняты две методики расчёта.
NB 4.1. В четырёх видах сварных соединений расчёты ведут по двум
видам швов: стыковыми или угловыми.
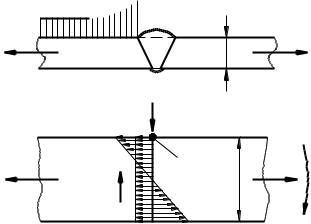
Лекция №4
4.3. Стыковое соединение
Стыковое соединение во многих случаях является наиболее простым и надёжным. Его следует применять везде, где позволяет конструкция изделия.
Полный и бездефектный провар стыка обеспечивает равнопрочность сварного шва и основного металла. Сваривают встык листы и полосы, а также трубы и уголки, швеллеры и другие фасонные профили.
На железных дорогах используют стыковую контактную сварку рельсов.
Стыковое соединение является наиболее совершенным видом неразъёмного соединения, где теряется понятие «стык». Оно применяется в ответственных конструкциях, так как составная сборочная единица имеет прочность, близкую к целой детали. В зависимости от толщины соединяемых элементов соединения выполняют с обработкой или без обработки кромок, с подваркой и без подварки с другой стороны детали.
В соединении двух полос стыковым швом «усиление» (утолщение) шва является источником концентрации напряжений (рис. 4.5). В ответственных соединениях образовавшиеся валики удаляют механической обработкой, что почти полностью снимает концентрацию напряжений. Стыковые соединения могут разрушаться по шву, месту сплавления металла шва с металлом детали, а
также по сечению самой детали в зоне термического влияния (околошовной зоне),
врайоне закалочной структуры.
K =1,6
F |
|
|
F |
|
|
δ |
|
|
|
Q |
|
F |
|
A |
F |
|
b |
||
|
|
M |
|
|
M |
|
|
|
|
|
|
|
|
F |
|
Рис. 4.5. Напряжения в стыковом шве
Практикой установлено, что при качественном выполнении сварки разрушение соединения стальных деталей происходит преимущественно в зоне термического влияния. Поэтому расчёт прочности следовало бы выполнять по размерам сечения детали в этой зоне. Возможное снижение прочности деталей,
связанное со сваркой (с невозможностью выполнить отжиг детали после сварки),
учитывают при назначении допускаемых напряжений, а размеры расчётного сечения принимают по размерам детали.
Основной расчёт ведут по максимальным статическим нагрузкам. Такими нагрузками являются продольная сила F, поперечная сила Q и моменты:
изгибающий M и крутящий Т. При циклических напряжениях вводят коэффициент , понижающий допускаемое напряжение, а расчёт ведут по максимальной нагрузке.
А) При действии продольной силы F нормальное напряжение:
|
|
F |
|
F |
[ ], |
(4.1) |
|
|
|||||
F |
|
A |
|
bδ |
|
|
|
|
|
|
|
||
где [ ] – допускаемое напряжение |
для сварных соединений |
(содержит в |
обозначении штрих), МПа; в зависимости от способа сварки и марки электрода
|
|
|
(4.2) |
|
|
|
[ ] (0,9....1,0) [ ] , |
||
[ ] |
– допускаемое напряжение для основного металла, МПа (прил. 2); |
|||
численный коэффициент принимают из прил. 3; |
|
|||
– |
коэффициент переменной нагрузки; для |
металлоконструкций из |
||
углеродистых сталей |
|
|||
|
1 |
|
|
|
|
|
|
1. |
(4.3) |
|
(0,6 Кэф 0,2) R(0,6 Кэф 0,2) |
Эффективный коэффициент концентрации напряжений Кэф зависит от материала и вида сварного шва; он принимается по справочнику (прил. 4).
Например, для стыкового шва с полной проваркой корня Кэф = 1,2, для фланговых угловых швов Кэф = 3,5. Из формулы (4.2) видно, что в стыковом шве
коэффициент прочности

|
[ ] |
0,9....1, |
(4.4) |
|
[ ] |
||||
|
|
|
то есть стыковое соединение может быть равнопрочным с соединяемыми деталями.
Б) При действии изгибающего момента М возникает нормальное напряжение, которое будет максимальным в наиболее нагруженной точке сварного шва А (в расчётной точке):
|
|
М |
|
6M |
[ ]. |
(4.5) |
||
|
|
|
||||||
M |
|
W |
|
|
b2δ |
|
||
В) При действии поперечной нагрузки Q возникает касательное напряжение: |
||||||||
|
|
|
|
Q |
[ ], |
(4.6) |
||
|
|
|
||||||
|
|
Q |
|
|
bδ |
|
||
|
|
|
|
|
|
|||
где [ ] – допускаемое касательное напряжение (см. прил. 3). |
|
|||||||
[ ] |
(0,5...0,65) [ ] . |
(4.7) |
NB 4.2. Нормальные и касательные допускаемые напряжения сварных швов определяют в зависимости от нормального допускаемого напряжения для основного материала.
Г) При действии всех трёх нагрузок используют выражения (4.1), (4.5) и (4.6), а рабочее нормальное напряжение в наиболее нагруженной точке сварного шва А определяют по энергетической теории прочности (четвёртой):
|
|
|
|
|
|
2 |
|
2 |
|
(4.8) |
пр |
( F |
M ) |
|
3(Q ) |
|
[ ]. |
||||
|
|
IV |
|
|
|
|
|
|
|
|
NB 4.3. При |
|
действии |
комбинированной нагрузки |
результирующее |
нормальное напряжение в стыковом сварном шве определяют по теории
прочности.
При комбинации из двух нагрузок одно из слагаемых в формуле (4.8) равно
нулю. Основная методика расчёта сварных соединений – проверочный
расчёт с определением рабочих приведенных или результирующих напряжений.
По его результатам делают вывод о достаточной или недостаточной
прочности.
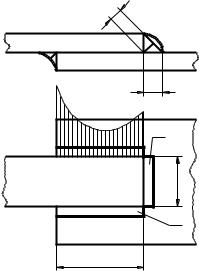
4.4.Нахлёсточное соединение
4.4.1.Общие сведения
Нахлёсточное соединение выполняют с помощью угловых швов (рис. 4.6). В
зависимости от формы поперечного сечения различают угловые швы:
нормальные, вогнутые и выпуклые. Наибольшее распространение получили нормальные швы. Выпуклый шов образует резкое изменение формы деталей в месте соединения, что является причиной повышенной концентрации напряжений. Вогнутый шов снижает концентрацию напряжений и рекомендуется при действии циклических нагрузок. Расчётным принят нормальный шов.
h |
k |
|
1 |
b |
2 |
l |
Рис. 4.6. Угловые швы |
Основные геометрические характеристики углового шва – толщина соединяемых деталей δ , катет шва k и высота его опасного сечения h; для нормального шва высота по биссектрисе прямого угла:
h k sin o , k .
По условиям технологии сварки принимают k мм, если толщина листа
δ мм. В большинстве случаев k δ . Максимальная величина k 10 мм. В
зависимости от расположения различают швы: фланговые, лобовые, комби-
нированные.