
Методички / Курс деталей машин
.pdf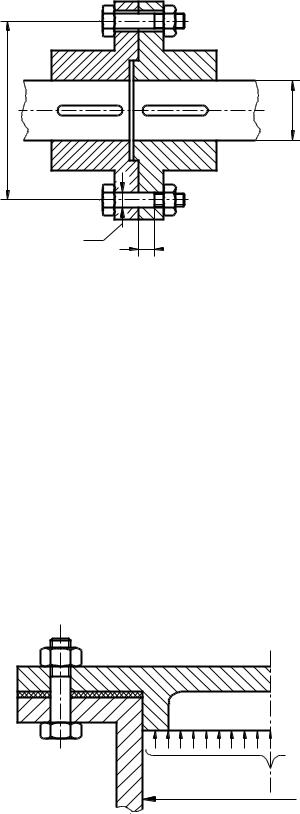
Задача №14
Рассчитать групповое болтовое соединение фланцевой муфты. Нагрузка
статическая. Определить диаметр резьбы и привести её обозначение на эскизе |
|
соединения. |
|
0 |
d |
D |
|
d0 |
δ |
Наименование параметра |
|
|
Вариант |
|
|
||
1 |
2 |
3 |
4 |
5 |
6 |
||
|
|||||||
Диаметр расположения осей болтов D0, мм |
160 |
200 |
240 |
260 |
300 |
320 |
|
Крутящий момент Т, Н·м |
400 |
800 |
1200 |
1400 |
1800 |
2200 |
|
Вид болта (1-чистый; 2-черный) |
1 |
2 |
1 |
1 |
2 |
1 |
|
Материал болтов – сталь |
30Х |
20 |
40ХН |
40Х |
50 |
30ХГСН |
|
Число болтов z |
4 |
6 |
8 |
10 |
12 |
14 |
|
Высота поверхности смятия δ, мм |
10 |
– |
12 |
16 |
– |
20 |
Примечание. Недостающими данными задаться.
Задача №15
Рассчитать групповое болтовое соединение крышки резервуара высокого давления. Определить диаметр резьбы и привести её обозначение на эскизе соединения. Нагрузка статическая.
p |
D |

Наименование параметра |
|
|
Вариант |
|
|
||
1 |
2 |
3 |
4 |
5 |
6 |
||
|
|||||||
Внутренний диаметр ёмкости D, мм |
800 |
900 |
1000 |
1100 |
1200 |
1400 |
|
Давление среды р, МПа |
0,4 |
0,5 |
0,6 |
0,7 |
0,8 |
1,0 |
|
Число болтов z |
8 |
12 |
16 |
20 |
24 |
36 |
|
Материал болтов – сталь |
25 |
45 |
35 |
50 |
40Х |
40ХН |
Примечание. Недостающими данными задаться.
Задача №16
Рассчитать групповое болтовое соединение кронштейна, нагруженного отрывающей и опрокидывающей нагрузкой из условия нераскрытия стыка.
Определить диаметр резьбы и привести её обозначение на эскизе соединения.
Нагрузка статическая.
F |
M |
A
B
l
Наименование параметра |
|
|
Вариант |
|
|
||
1 |
2 |
3 |
4 |
5 |
6 |
||
|
|||||||
Отрывающая сила F, кН |
1,6 |
1,8 |
2,0 |
2,4 |
2,6 |
3,0 |
|
Момент М, Н·м |
400 |
500 |
600 |
700 |
800 |
350 |
|
Размеры основания А, мм |
200 |
220 |
240 |
260 |
280 |
320 |
|
В, мм |
160 |
180 |
180 |
200 |
210 |
250 |
|
Материал болтов – сталь |
30Х |
40Х |
40ХН |
50 |
30ХГСН |
40ХН |
|
Координаты болтов l, мм |
70 |
65 |
80 |
85 |
90 |
100 |
Примечание. Недостающими данными задаться.
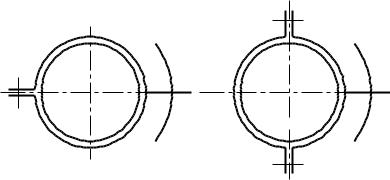
Лекция № 9
Тема 6: Клеммовые соединения
6.1. Общие сведения
Клеммовые соединения применяют для закрепления деталей на валах и осях,
цилиндрических колоннах, кронштейнах и т.д. По конструктивным признакам различают 2 основных типа клеммовых соединений (рис. 6.1):
а) со ступицей, имеющей прорезь;
б) с разъёмной ступицей.
а) |
б) |
T
T
Рис. 6.1. Типы клеммовых соединений
Разъёмная ступица несколько увеличивает массу и стоимость соединения,
но при этом становится возможным установить клемму в любой части вала независимо от формы соседних участков и расположенных рядом деталей.
При соединении деталей с помощью клемм используют силы трения,
которые зависят от затяжки болтов. Силы трения позволяют нагружать соединение моментом Т, осевой силой Fа, а также их комбинацией.
Достоинства:
1)простота монтажа и демонтажа;
2)самопредохранение от перегрузки;
3)возможность перестановки и регулировки взаимного расположения деталей в осевом и окружном направлениях.
Недостатки:
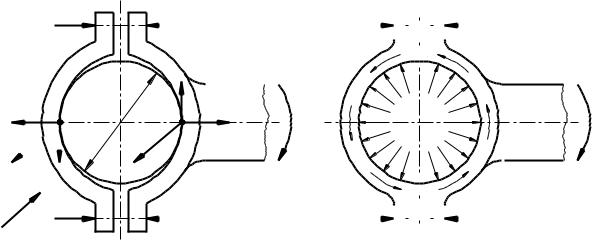
1)ограниченная передаваемая нагрузка;
2)низкая прочность деталей клеммы при некачественном монтаже.
6.2.Расчёты на прочность
При проектировании клеммового соединения прежде всего требуется
определить силу затяжки болтов, обеспечивающую передачу требуемой нагрузки. Сравнительно точный расчёт такого соединения возможен путем решения контактной задачи методом конечных элементов, при котором рассматриваются два предельных случая.
А) Жёсткая клемма (рис. 6.2, а).
В этом случае клемма обладает большой жёсткостью, а посадка деталей выполнена с большим зазором. При этом допускают, что контакт деталей происходит по линии в точках "с". Данный случай является дефектным, так как при затяжке болтов клемма может разрушиться.
а) Fзат
N c
Nf
Nf
Fa
Fзат
d
Fзат |
|
б) Fзат |
|
|
|
|
|
|
|
|
Fзат |
||||
|
|
|
|
|
|||||||||||
|
|
|
|
|
|
||||||||||
|
|
|
|
|
|
|
|
|
|
|
|
|
|
|
|
|
|
|
|
|
|
|
|
|
|
|
|
|
|
|
|
|
|
|
|
|
|
|
|
|
|
|
|
|
|
|
|
|
|
|
|
|
|
|
|
|
|
|
|
|
|
|
|
Nf |
c |
N |
p |
|
|||
|
|
|
|
Nf |
|
T |
T |
|
|
|
|
|
|
|
|
|
|
|
|
|
|
|
|
|
|
|
|
|
|
|
|
|
|
|
|
|
|
|
|
|
|
|
|
|
|
|
|
|
|
|
|
|
|
|
|
|
|
|
|
|
|
|
|
|
|
|
|
|
|
|
|
|
|
|
|
|
|
|
|
|
|
|
|
|
Fзат |
Fзат |
|
|
|
|
|
|
|
|
Fзат |
||||
|
|
|
|
|
|
|||||||||
|
Рис. 6.2. Конструкции жёсткой и гибкой клеммы
Для восприятия осевой силы Fа необходимо болты затянуть усилием Fзат,
что вызывает в точках контакта "с" реакцию N и силу трения Nf. Из условия равенства внешней нагрузки и сил трения можно записать:
KFa Nf . |
(6.1) |
Из условия равновесия любой половины клеммы:
N Fзат. |
|
(6.2) |
|
Из равенств (6.1) и (6.2) находят усилие затяжки Fзат: |
|
||
F |
KFa |
, |
(6.3) |
|
|||
зат |
f |
|
|
|
|
|
где K – коэффициент запаса по сцеплению; K = 1,3…1,8.
Б) Гибкая клемма (рис. 6.2, б).
В такой клемме форма сопрягаемых деталей строго цилиндрическая, зазор в
соединении близок к нулю, а при затяжке болтов образуется натяг. В этом случае полагают, что давление p распределяется равномерно по поверхности соприкосновения деталей. Данный случай наиболее рациональный с точки зрения требуемой затяжки болтов. Условие равенства внешней нагрузки и сил трения:
KFa dlfp, |
(6.4) |
где l – длина клеммы, мм; рекомендуется l = (1,2…1,5)d,
р – давление в соединении, МПа;
f – коэффициент трения; для стальных и чугунных клемм и сухих несмазанных поверхностей f = 0,15…0,2.
Условие равновесия полуклеммы:
Fзат pdb. |
(6.5) |
||
В данном соединении давление p равнозначно напряжению смятия, а db - |
|||
условная площадь смятия. Из равенств (6.4) и (6.5) следует: |
|
||
F |
KFa |
. |
(6.6) |
|
|||
зат |
f |
|
|
|
|
Из формул (6.3) и (6.6) видно, что нагрузочные способности для двух предельных случаев относятся как 2/ . В современном машиностроении размеры деталей клеммового соединения выполняют под посадку Н8/h8, при которой обеспечивается свободная сборка деталей без излишних зазоров. Это дает основание рассматривать условия работы практически выполненных клеммовых соединений как средние между крайними случаями и рассчитывать их на прочность по формуле:
F |
KFa |
. |
(6.7) |
зат fz
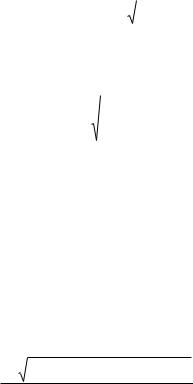
Здесь коэффициент 5 приближенно равен среднему между 4 и 2 . В
формулу (6.7) дополнительно ставится z – число болтов, расположенных с одной стороны вала.
Расчет клеммового соединения с односторонним расположением болтов также выполняют по формуле (6.7). При этом условно полагают, что функции второго болта соединения выполняет сама деталь рычага. При нагружении моментом Т его действие можно заменить силой Ft, приложенной к поверхности вала диаметром d, по условию:
F |
2T |
|
(6.8) |
|
|
|
|||
t |
d |
|
|
|
|
|
|
|
|
и формула (6.7) примет вид: |
|
|
|
|
F KT . |
(6.9) |
|||
зат |
|
dfz |
|
|
|
|
|
|
При комбинированной нагрузке расчёт ведут по геометрической сумме усилия от момента и осевой силе:
|
|
|
|
|
|
|
Fзат |
K Fa2 |
(2Т / d )2 |
|
. |
(6.10) |
|
|
|
|
||||
|
|
|
5 fz |
|
Расчётный диаметр болтов определяют по формуле:
d |
|
4 1,3Fзат |
|
. |
(6.11) |
|
|||||
1 |
|
[ ] |
|
||
|
|
|
Пример 6.1. Рассчитать болты клеммового соединения (рис. 6.2). Исходные данные: диаметр соединения d = 60 мм, крутящий момент Т = 500 Н·м, осевая нагрузка Fa = 6 кН, число болтов z = 2. Клеммы и вал – стальные. Материал болтов cталь 30Х, коэффициент трения f = 0,15.
Решение.
Предел текучести стали 30Х T = 640 МПа (прил. 9). Усилие затяжки при К = 1,5:
1,5 60002 (2 500 103 / 60)2
F 17714Н.
зат |
5 |
0,15 2 |
|
При неконтролируемой затяжке принимаем резьбу М20 (прил. 8). Коэффициент запаса для легированных сталей sT = 4,3 (прил. 13). Допускаемое напряжение [] =T/sT = 640/4,3 = 148,8 МПа. Внутренний диаметр резьбы:

d1 |
1,3 4 17714 |
|
14мм. |
|
|
|
|||
148,8 |
||||
|
|
|
Этот диаметр соответствует резьбе М16, для которой d1 = 13,835 мм. Её следует уточнить, так как для М16 коэффициент запаса должен быть выше, чем принято, а допускаемое напряжение – ниже. Ориентируемся на резьбу М18; по линейной интерполяции находим из прил. 13 коэффициент запаса sT = 4,7.
Расчётный диаметр:
d |
1,3 4 17714 4,7 |
|
14,67мм. |
|
|||
1 |
640 |
|
|
|
|
|
Резьба М18 имеет d1 = 15,294 мм, что больше рассчитанного.
Вывод. Принимаем болты М18 с d1 = 15,294 мм.
Вопросы для самоподготовки
1.Как классифицируются клеммовые соединения?
2.Дайте оценку клеммового соединения.
3.Что такое жёсткая клемма, гибкая клемма?
4.Как рассчитывают болты клеммового соединения?
Вопрос, выносимый на экзамен
1. Клеммовые соединения. Общие сведения. Расчет жёсткой и гибкой клемм.
Вопрос, выносимый на Олимпиаду
1. Клеммовые соединения. Общие сведения. Расчет жёсткой и гибкой клемм при действии осевой нагрузки. Расчет болтов соединения.
Экзаменационные задачи
Задача №17
Рассчитать болты клеммового соединения. Определить диаметр резьбы и дать её обозначение на эскизе соединения.
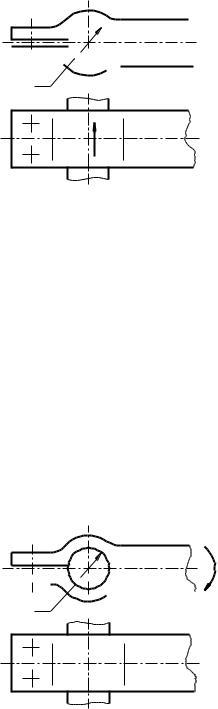
M d
Fa |
Наименование параметра |
|
|
Вариант |
|
|
||
1 |
2 |
3 |
4 |
5 |
6 |
||
|
|||||||
Осевая сила Fа, кН |
4 |
0 |
6 |
10 |
0 |
20 |
|
Момент М = Т, Н·м |
0 |
800 |
400 |
900 |
1000 |
700 |
|
Диаметр вала d, мм |
50 |
40 |
60 |
70 |
90 |
110 |
|
Число болтов z |
1 |
2 |
3 |
4 |
5 |
6 |
|
Материал болтов – сталь |
45 |
50 |
30Х |
40Х |
40ХН |
30ХГСН |
Примечание. Недостающими данными задаться.
Задача №18
Определить допускаемый момент М = Т при заданной конструкции
клеммового соединения со стальной клеммой.
M d
Наименование параметра |
|
|
Вариант |
|
|
||
1 |
2 |
3 |
4 |
5 |
6 |
||
|
|||||||
Диаметр вала d, мм |
80 |
90 |
100 |
110 |
120 |
140 |
|
Число болтов z |
2 |
3 |
4 |
5 |
6 |
8 |
|
Диаметр болтов |
М16 |
М12 |
М8 |
М10 |
М20 |
М16 |
|
Материал болтов – сталь |
10 |
20 |
35 |
45 |
50 |
30Х |
Примечание. Недостающими данными задаться.

Тема 7: Соединения с гарантированным натягом
7.1. Общие сведения
Соединение двух деталей по цилиндрической поверхности можно осуществить со значительной нагрузочной способностью. Для этого необходимо изготовить детали с такими размерами, чтобы обеспечить натяг соединения, а при сборке запрессовать одну деталь в другую (рис. 7.1). Натягом N называют
положительную разность диаметров вала и отверстия, то есть |
|
N = d – D = В - А. |
(7.1) |
а) |
|
б) |
p |
Fa |
A |
Fa |
|
|
|
d |
|
|
B |
|
|
|
Рис. 7.1. Соединяемые детали |
|
После сборки диаметр d посадочных поверхностей становится общим. При этом на поверхностях соединяемых деталей возникает давление р и
соответствующие ему силы трения. Они обеспечивают неподвижность соединения и позволяют воспринимать нагрузки Fa , T и их комбинацию.
Полученное таким образом прессовое соединение имеет нежёсткую фиксацию деталей в осевом и окружном направлениях.
Нагрузочная способность прессового соединения зависит от натяга,
значение которого рассчитывают в соответствии с нагрузкой. Практически расчётный натяг невелик, он измеряется десятками микрометров (сотыми долями миллиметра) и не может быть выполнен точно. Неизбежные погрешности производства приводят к рассеиванию натяга, а, следовательно, и к рассеиванию нагрузочной способности соединения.
7.2. Допуски и посадки
При сборке сопрягаемых деталей, входящих одна в другую, различают охватывающую поверхность (отверстие) и охватываемую (вал). Размер сопрягаемых поверхностей отверстия и вала носит общее название номинального размера соединения, который одинаков для отверстия и вала. Его принимают по стандарту (Прил. 15) и проставляют на чертежах.
Изготовить деталь по номиналу практически невозможно. Измерительными инструментами определяют действительный размер, получаемый обработкой,
который должен находиться между предельными отклонениями, ограниченными стандартными значениями.
Разность между размерами отверстия и вала определяет посадку, то есть характер соединения сопряжённых деталей, которая может быть с зазором, с натягом и переходная, допускающая как зазор, так и натяг.
В отечественной Единой системе допусков и посадок (ЕСДП) принята международная буквенно-цифровая система обозначений предельных отклонений размеров от номинала. Отклонения a – h (для валов) и A – H (для отверстий)
предназначены для образования полей допусков и посадок с зазором; p – z (P – Z) – для обеспечения гарантированного натяга (прессового соединения); js, k, m, n (Js, K, M, N) дают переходные посадки.
На рис. 7.2 представлено соединение с зазором, где d = D – номинальный размер.
Наибольший и наименьший предельные размеры определят по зависимостям:
для отверстия:
Dmax = D + ES; |
Dmin = D + EI; |
(7.2) |
для вала: |
|
|
dmax = d + ei; |
dmin = d + es; |
(7.3) |