
Методички / Курс деталей машин
.pdf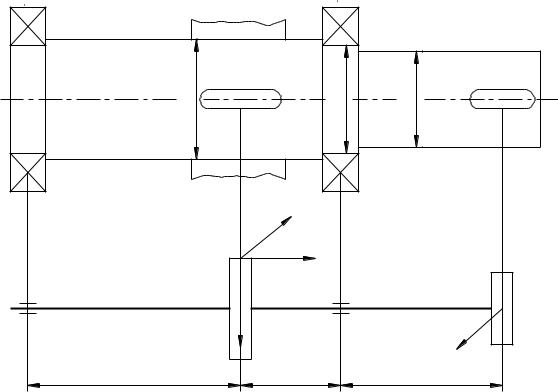
Поэтому для машины задача определения и выбора нагрузок является весьма важной и ответственной. Для деталей машин нагрузки рассчитывают по аналитическим соотношениям либо их определяют как допускаемые.
Ж50 H7/s6 |
Ж45 L0/k6 |
Ж40 H7/k6 |
|
Ft |
|
|
Fa |
|
|
Fr |
Fм |
|
|
|
l1+l2 |
l3 |
l4 |
Рис. 2.1. Вал (конструкция и расчётная схема) |
3) Выбор материала для деталей машин также является ответственным этапом проектирования. Выбирая материал, учитывают, в основном, следующие факторы:
–соответствие свойств материала основному критерию работоспособности (прочность, износостойкость и т.п.);
–стоимость материала;
–требования к массе и габаритам детали и машины в целом;
–другие требования, связанные с назначением детали и условиями её эксплуатации (фрикционные и антифрикционные свойства, антикоррозионная стойкость и т. д.);
–соответствие технологических свойств материала конструктивной форме
инамечаемому способу обработки (штампуемость, свариваемость, литейные
свойства, обрабатываемость резанием и пр.);
Рекомендации по выбору материала различных групп деталей машин разработаны и рассматриваются при изучении конкретных деталей машин. Выбор материала и его термической обработки завершается определением допускаемых напряжений, по которым рассчитывают большинство деталей.
4) Выполнение проектного расчёта.
Проектный расчёт выполняется по основному критерию
работоспособности. При одном критерии расчёт ведут по одной формуле,
определяя одну неизвестную величину. Но число неизвестных обычно превышает число расчётных уравнений. Поэтому некоторыми неизвестными параметрами задаются, а некоторые второстепенные параметры просто не учитывают. Такой упрощённый расчёт необходим для определения тех размеров, без которых невозможна первая графическая проработка конструкции. Рассчитав один параметр, остальные определяют из геометрических, технологических,
конструктивных и других соображений. Начиная с этого этапа, расчёт и конструирование ведут параллельно.
5) Вычерчивание деталей и сборочных единиц.
Данный этап представляет собой чисто конструкторскую работу. Выполняя
эскиз детали в составе сборочной единицы, куда она входит, её размеры и конфигурацию корректируют. Назначают класс шероховатости поверхностей,
допуски размеров в зависимости от вида посадки, допуски формы и расположения поверхностей, специальные технологические требования в процессе выполнения рабочего чертежа детали, по которому деталь можно изготовить.
6) Выполнение проверочных расчётов.
Проверочный расчёт – уточнённый расчёт известной конструкции –
выполняется в целях проверки её по основному критерию работоспособности
или определения допускаемой нагрузки. Для вала, в частности, определяют коэффициенты запаса прочности в опасных сечениях с учетом различных факторов и сравнивают с допускаемым значением. В других случаях определяют рабочие напряжения и сравнивают их допускаемыми. Когда требуемое соответствие между этими величинами не обеспечивается, в конструкцию вносят изменения, после чего вновь производят проверки и т.д. В практике реального
проектирования разрабатывается несколько вариантов конструкций и делается их технико-экономическое обоснование.
Стадии проектирования.
В соответствии с ГОСТ 2.103 разработка конструкторской документации состоит из четырёх стадий: техническое предложение, эскизный проект,
технический проект, рабочая конструкторская документация. В курсовом проекте,
в частности, на стадии эскизного проекта выполняют все проектные расчёты и эскизную компоновку редуктора, на стадии технического проекта – разработку конструктивных элементов и проверочные расчёты, на стадии рабочей конструкторской документации – рабочие чертежи деталей и сборочные чертежи.
Лекция №2
2.4. Виды нагрузок и вызываемые ими напряжения
Из рассмотренных шести этапов проектирование конкретной детали имеет свою специфику. В то же время при проектировании деталей присутствует много общих положений, которые рассмотрены в следующих пунктах. Прочность
является основным критерием работоспособности большинства деталей.
Непрочные детали не могут работать. Прочность оценивают несколькими способами:
–с помощью допускаемых напряжений;
–запасами прочности;
–по вероятности неразрушения и др.
Для того, чтобы реализовать эти способы, надо знать максимальные напряжения в опасных (расчётных) точках детали. А для этого надо знать
нагрузку.
По характеру изменения нагрузок (напряжений) их подразделяют на статические и циклические. Статическими называют нагрузки, медленно изменяющиеся во времени. Обычно они нарастают постепенно от нуля до своего максимального значения и остаются практически неизменными в течение длительного времени. Такими нагрузками являются, например, вес деталей, силы предварительной затяжки болтов и др. В большинстве случаев характер
изменения нагрузок и напряжений совпадает (рис. 2.2).
Циклическое напряжение характеризуется параметрами цикла:
амплитудными а или а и средними m или m напряжениями цикла и коэффициентом асимметрии цикла R. Последний определяет форму цикла.
Асимметричный цикл рассматривается как общий случай циклического напряжения (рис. 2.3). Амплитудное напряжение определяют как полуразность, а
среднее напряжение цикла – как полусумму максимального и минимального напряжений:
|
а |
max min ; |
|
m |
max min . |
(2.1) (2.2) |
|
|
|
|
|
||
|
|
|
|
|
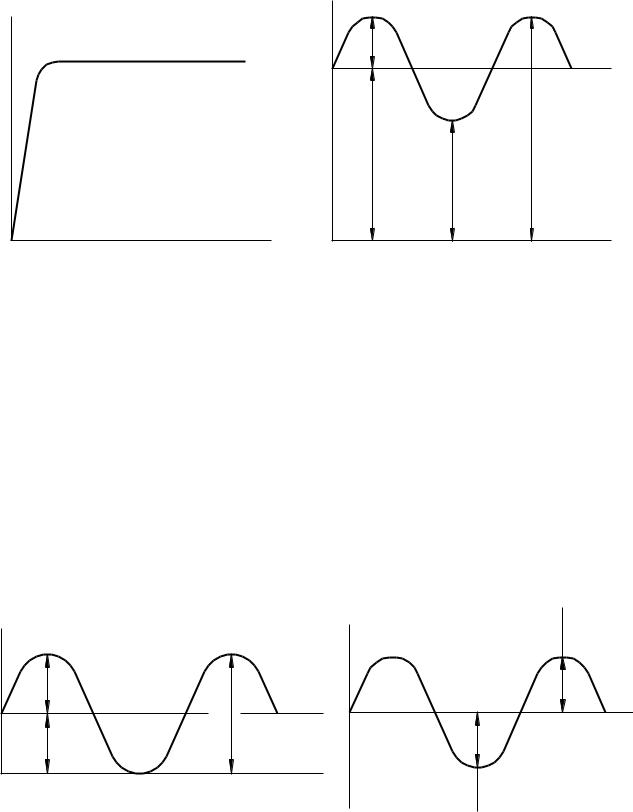
Коэффициент асимметрии цикла определяют отношением минимального |
|||
напряжения к максимальному: |
|
|
|
|
|
|
|
F |
( ) |
|
|
( ) |
a |
|
|
|
|
|
|
|
|
|
|
|
m |
|
max |
|
|
min |
|
|
|
|
|
t |
|
|
t |
Рис. 2.2. Статическая нагрузка |
Рис. 2.3. Асимметричный цикл |
||
R |
min . |
|
(2.3) |
|
max |
|
|
Формулы, аналогичные (2.1)…(2.3), могут быть также записаны для |
|||
касательных напряжений. |
|
|
|
Частный случай асимметричного нагружения - пульсирующий (отнулевой) |
|||
цикл (рис. 2.4). Его параметры: а m , max ;R . |
|||
Цикл нагружения, в котором максимальное и минимальное напряжения |
|||
равны по модулю, но противоположны |
по знаку, называют симметричным |
||
(знакопеременным, рис. 2.5). Его параметры: а max ; т ;R . |
|||
|
|
|
max |
|
|
||
|
|
|
|
a |
|
|
|
|
max |
|
t |
m |
|
|
|
|
|
||
|
|
|
|
|
t |
|
min |
|
|
|
|
Рис. 2.4. Пульсирующий цикл |
|
Рис. 2.5. Симметричный цикл |
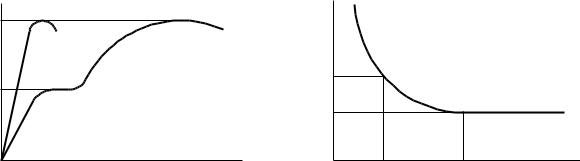
Как правило, асимметричный цикл сводят к двум последним. В справочной литературе [2] напряжениям при пульсирующем и симметричном циклах присваивают индексы II и III, (обозначают II в отличие от напряжения при статическом нагружении I ).
2.5. Допускаемые напряжения
При статическом нагружении допускаемое напряжение определяют по
формуле: |
|
|
|
|
|
|
|
|
|
|
|
[ ] R / s , |
|
(2.4) |
|||
где R – предельное напряжение, МПа; для пластичных материалов R |
T , |
|||||||
для хрупких материалов R B , T |
– предел текучести; B – предел прочности; |
|||||||
предельные напряжения принимают по справочным данным, опредённым по |
||||||||
диаграммам растяжения (рис. 2.6); s – коэффициент запаса прочности для |
|
|||||||
рассчитываемой детали. |
|
|
|
|
|
|
||
При циклическом нагружении для симметричного цикла R . Предел |
||||||||
выносливости |
|
определяют по |
|
кривой усталости (рис. 2.7). Для |
других |
|||
|
|
|
|
|
|
|
|
|
циклов используют эмпирическую зависимость: |
|
|
||||||
|
|
|
|
|
|
|
|
|
|
|
R |
|
|
|
|
. |
(2.5) |
|
|
|
( , |
, R) |
||||
|
|
|
|
|
|
B |
T |
δ |
Рис. 2.6. Диаграммы растяжения |
|
|
-'1 |
|
-1 |
|
N |
NG |
Рис. 2.7. Кривая выносливости
2.6. Факторы, влияющие на прочность
Основной вид разрушения деталей машин – усталостные поломки. Они возникают внезапно и нередко приводят к тяжёлым последствиям. При циклических напряжениях на усталостную прочность оказывают влияние концентрация напряжений, масштабный фактор, качество поверхности и число циклов нагружения.
2.6.1. Концентрация напряжений
Концентрацией напряжений называется резкое местное изменение поля напряжений. Она вызывается конструктивными и технологическими факторами.
Концентрацию напряжений оценивают теоретическим коэффициентом концентрации напряжений:
К М , |
(2.6) |
Т |
Н |
|
где М – максимальное местное напряжение, определённое экспериментально или вычисленное методами теории упругости; Н – номинальное напряжение,
рассчитаннное по формулам из сопротивления материалов.
Более объективную оценку дает эффективный коэффициент концентрации напряжений, который учитывает влияние материала:
|
|
|
|
|
К |
|
|
, |
(2.7) |
|
||||
|
|
К |
|
|
где К – предел выносливости образца с концентрацией напряжений. |
||||
Наличие переходных сечений, |
канавок, отверстий, |
резьбы, напрессовок |
(рис. 2.8, а) и т. п., а также газовые пузыри и шлаковые включения способствуют концентрации напряжений. На рис. 2.8, б показана эпюра касательных напряжений на валу в зоне переходного сечения от действия крутящего момента.
На рис. 2.9 в качестве примера показано распределение напряжений при растяжении полосы прямоугольного сечения с двумя надрезами. Зона возмущения
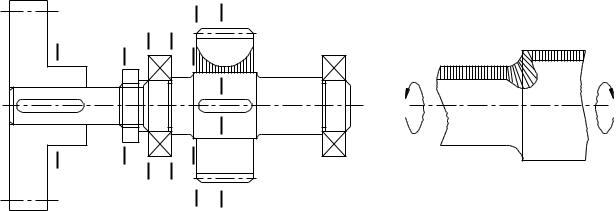
поля напряжений невелика, однако концентрация напряжений существенно снижает прочность детали при циклическом нагружении.
Значения коэффициентов концентрации напряжений зависят от вида концентратора, материала и характера нагрузки. Так, например, для резьб
К =1,96…2,39, для шлицев К =1,55…1,75, при напрессовке К = 2,0…4,5 [9].
Таким) образом, при наличии концентрации напряжений и циклической нагрузке
б)
KT =4,65 |
KT =3 |
Рис. 2.8. Концентраторы напряжений
предельные напряжения уменьшаются в несколько раз, что снижает усталостную прочность деталей. Из приведенных примеров напрессовка – сильнейший концентратор. Полностью устранить концентрацию напряжений практически невозможно, но максимально её снизить – задача конструктора.
NB 2.2. При циклической нагрузке и наличии концентрации напряжений
(зубьев, резьб, шпоночных канавок, переходных сечений, напрессовок и т. д.)
усталостная прочность деталей снижается.
NB 2.3. Основная задача конструктора – максимально возможное снижение концентрации напряжений
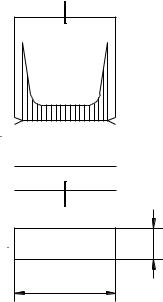
F
M
H
F
δ
b |
Рис. 2.9. Эпюры напряжений растяжения
В деталях из пластичных материалов при превышении местных напряжений над пределом текучести металл начинает течь, острый надрез становится округлым и влияние концентрации напряжений снимается. Также нечувствительны к концентрации напряжений серые чугуны, но не по причине пластичности (она вообще отсутствует), а из-за микроструктуры, которая изначально содержит многочисленные концентраторы – включения графита в сталистую основу.
NB 2.4. При статической нагрузке пластичные материалы и серые
чугуны нечувствительны к концентрации напряжений.
2.6.2. Масштабный фактор
Сравнивая прочность стального каната и гладкого стержня одинаковых диаметров можно безошибочно утверждать, что стальной канат прочнее. Ответ оказывается верным, несмотря на то, что суммарное сечение проволок каната меньше сечения стержня. Действительно, с увеличением размера заготовок физическая и химическая неоднородность структуры материала, обусловленная
металлургическими процессами и термической обработкой, проявляется в большей степени, и предельные напряжения снижаются. Так, например, в тонкой стальной ленте или проволоке может быть достигнут предел текучестиT = 4000 МПа, в то время как в массивном стальном монолите возможен максимум в 800 МПа.
Изменение предела выносливости в зависимости от размеров детали учитывают масштабным коэффициентом:
|
|
|
|
d |
, |
(2.8) |
|
|
|||||
|
|
|
|
|
||
|
|
|
|
|
||
|
|
|
|
|
|
|
где – предел выносливости |
образца |
стандартного |
размера, например, |
диаметром 10 мм; d – предел выносливости образца диаметром d.
Например, для углеродистой стали при d = 20 мм = 0,92; при d = 70 мм= 0,76 [9].
NB 2.5. При увеличении размеров детали её предельные напряжения
уменьшаются вследствие неоднородности структуры металла.
2.6.3. Состояние поверхности
Важная роль поверхностных слоёв обусловлена тем, что в большинстве случаев первичные усталостные трещины возникают на поверхности. Этому способствуют:
–наличие на поверхности концентраторов напряжений в виде микронеровностей (микронадрезов) от механической обработки;
–воздействие внешней среды;
–более высокая напряжённость поверхностных слоев (наибольшие напряжения изгиба и кручения);
–специфические свойства поверхностных слоев как граничных и содержащих разрушенные зерна.
Коэффициент состояния поверхности:
|
|
П , |
(2.9) |
|
|||
|
|
|
|
|
|
|
|