
Методички / Курс деталей машин
.pdf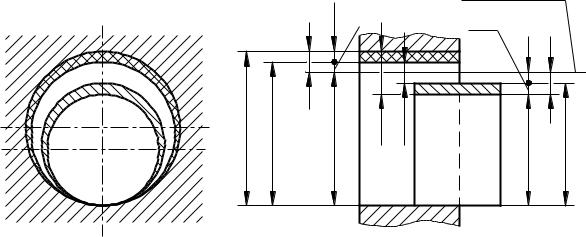
а) |
|
б) |
|
ном. размер |
|
|
|
|
|
||
|
|
D |
EI отверстие |
Td |
|
|
|
T |
|
||
|
|
|
|
ei es |
|
|
|
ES |
|
|
|
D max |
dmin |
D=d |
Smax Smin |
dmin |
dmax |
|
|
|
вал |
|
|
Рис. 7.2. Соединение с зазором |
|
|
В формулах (7.2) и (7.3) Dmax и Dmin - предельные размеры отверстия, dmax и dmin
– предельные размеры вала; EI и ei – основные отклонения соответственно отверстия и вала, ES – максимальное предельное отклонение отверстия, es -
максимальное предельное отклонение вала. Предельные отклонения:
ES = EI + ITD; es = ei + ITd, |
(7.4) |
где ITD – допуск отверстия, определяемый как разность между предельными отклонениями; ITd – допуск вала.
Величины ES и es зависят от квалитета (quality – качество, имеет смысл класса точности), по которому назначается допуск IT (I – ISO, Toleranz – допуск).
Установлено 20 квалитетов, из которых квалитеты 6…8 характеризуют высокую точность размеров, квалитеты 12…15 используют для свободных размеров. Если назначить для вала 6-й квалитет, а для отверстия 7-й, то в формуле (7.3) можно записать IT6 вместо ITd и IT7 вместо ITD.
В системе отверстия, являющейся предпочтительной по техническим и экономическим соображениям, минимальное предельное отклонение EI = 0.
Каждый из заштрихованных прямоугольников на рис. 7.2, ограниченных верхними и нижним отклонениями, называется полем допуска. На рисунке показаны поля допусков с зазорами от Smin = Dmin – dmax до Smax = Dmax – dmin.
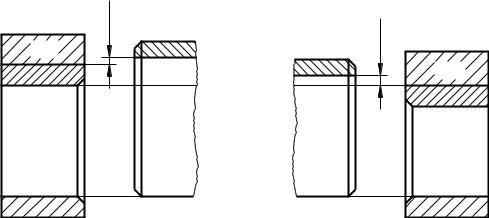
Предельные отклонения наиболее распространённых размеров и посадок приведены в прил. 16.
На рис. 7.3 изображён пример полей допусков посадок с натягом, выполненных в системе отверстия (рис. 7.3, а) и внесистемная посадка (рис. 7.3, б). Обозначают предельные отклонения размеров деталей по типу:
|
Ж50H 7 Ж50 0,025 |
Ж50H 7( 0,025 ); |
|
|
|||
|
Ж50s6 Ж50 0,059 Ж50s6( 0,059 ). |
|
|
||||
|
|
|
0,043 |
|
0,043 |
|
|
а) |
=1 |
|
|
|
б) |
|
|
H7 |
|
|
|
k6 |
=2Nmin |
|
|
Nmin |
p6 |
+42 |
|
|
|||
|
|
|
|
|
|
||
|
|
|
|
|
|
|
|
+25 |
|
|
+26 |
+18 |
|
M7 |
|
|
|
|
+2 |
|
|
||
0 |
|
|
|
|
0 |
||
|
|
|
|
|
|||
|
|
|
|
|
|
||
|
|
|
|
|
|
|
-21 |
Отверстие |
|
Вал |
|
|
Вал |
Отверстие |
|
|
|
|
|
|
|||
Рис. 7.3. Поля допусков посадок с натягом |
|
В соединениях предельные отклонения обеих поверхностей обозначают по
типу:
|
|
H 7 |
|
|
0,025 |
|
||
Ж50 |
Ж50 |
|
|
-посадка с зазором: |
||||
|
|
0,09 |
||||||
|
|
g6 |
|
|||||
|
|
0,025 |
|
|||||
|
|
|
|
|
|
|
||
|
H 7 |
|
|
|
0,025 |
|
||
Ж50 |
Ж50 |
|
|
|
- посадка с натягом. |
|||
|
|
0,059 |
||||||
|
|
s6 |
|
|||||
|
|
0,043 |
|
|||||
|
|
|
|
|
|
|
Из приведенных примеров нетрудно рассчитать допуски: IT6 = 0,016 мм; IT7 =
0,025 мм.
7.3. Технология сборки
Детали соединяют механическим или тепловым способами. При сборке
механическим способом охватываемую деталь с помощью пресса или молотка устанавливают в охватывающую деталь или наоборот (рис. 7.1, а). Однако этому
способу присущи некоторые недостатки: смятие или частичное срезание
(шабровка) шероховатостей посадочных поверхностей, возможность неравномерных деформаций деталей и повреждения их торцов. Шабровка и смятие шероховатостей приводит к ослаблению прочности соединения. Для облегчения сборки и уменьшения шабровки концу вала и краю отверстия придают коническую форму.
Тепловой способ сборки применяют при больших натягах и производится путем нагрева охватывающей детали (втулки) до температуры 300С в масляной ванне или охлаждением охватываемой детали (вала) до температуры не выше –
150С в жидком азоте или жидком воздухе. Выбор способа сборки зависит от соотношения массы и конфигурации деталей. При нагревании возможно появление окалины, коробления, изменение структуры металла. Метод охлаждения свободен от этих недостатков. Обычно охлаждение и экономичнее,
так как вал имеет меньшую массу.
В качестве примеров прессовых посадок на рис. 7.4 приведен эскиз локомотивной колёсной пары, где соединения 2 и 3 получают напрессовкой,
соединение 4 – нагревом бандажа, а в соединении 1 применяют оба вида сборки.
Усилия напрессовки зависят от величины натяга; в частности, усилие при напрессовке колёсного центра на ось Fa = 500…800 кН.
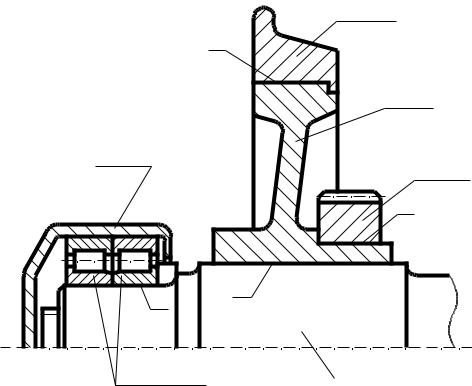
|
Бандаж |
|
4 |
|
Центр |
Букса |
|
|
Колесо |
|
3 |
1 |
2 |
|
|
Подшипники |
Ось |
|
Рис. 7.4. Соединения с натягом локомотивной колёсной пары Необходимую разность температур t нагрева втулки или охлаждения вала,
обеспечивающую свободную сборку, рассчитывают по формуле:
t |
Nmax So |
, |
(7.5) |
|
|||
|
d |
|
где Nmax – наибольший натяг посадки, мм;
So – минимально необходимый зазор, обеспечивающий свободную сборку,
мм; рекомендуется принимать равным минимальному зазору посадки H7/g6;
– температурный коэффициент линейного расширения (для стали и чугуна = 10 10-6 С-1;
d – номинальный диаметр в мм.
7.4. Концентрация напряжений
Прессовое соединение является сильным концентратором. Действительная эпюра давлений по длине втулки является кривой с максимумом давлений по краям втулки (рис. 7.5, а), а не прямоугольник, как на рис. 7,1, б. Именно у краёв

втулок наблюдается концентрация напряжений, вызванная вытеснением сжатого материала от середины втулки в обе стороны.
а)
K =2 |
б)
K =1,4 |
в)
K =1,2 |
Рис. 7.5. Меры по снижению концентрации напряжений
Эффект концентрации напряжений можно уменьшить изготовлением деталей специальной формы и определённых размеров:
1)применение разгружающих выточек во втулке, что повышает её податливость у краёв; При этом эффективный коэффициент концентрации напряжений снижается на 30% (рис. 7.5, б);
2)изготовление втулки (ступицы) длиной больше длины подступичной части вала (головки, рис. 7.5, в); снижение коэффициента на 40%;
3)ограничение длины ступицы до l/d ≤ 2.
7.5. Расчёт прочности соединения
Расчёт прочности (неподвижности) заключается в определении расчётного натяга и выборе посадки. Расчётная схема представлена на рис. 7.6.
Fa |
1 |
|
d |
l |
p
p Fa T
d
d2
T
Рис. 7.6. Расчётная схема соединения

Условие прочности при нагружении осевой силой записывают аналогично клеммовому соединению:
|
KFa dl f p. |
(7.6) |
||||
По теории расчёта толстостенных сосудов давление на поверхности |
||||||
контакта в зависимости от натяга определяют по формуле Лямэ: |
|
|||||
p |
|
|
N |
|
, |
(7.7) |
|
||||||
d (C / E C / E ) |
||||||
1 |
1 |
2 |
2 |
|
|
где d – номинальный размер соединения, мм;
N – расчётный натяг, мм;
С1 и С2 – коэффициенты задачи Лямэ;
Е1 и Е2 – модули упругости, МПа.
Коэффициенты С1 и С2 определяют по формулам:
C |
d 2 |
d 2 |
; |
C |
|
d 2 |
d 2 |
|
|
|
(7.8) |
|||||
|
1 |
|
|
2 |
|
|
|
|
, |
|||||||
d 2 |
d 2 |
|
d 2 |
d 2 |
||||||||||||
1 |
1 |
2 |
|
|
|
2 |
|
|
||||||||
|
|
1 |
|
|
|
|
|
|
2 |
|
|
|
|
|
|
|
где μ 1 и μ 2 – коэффициенты Пуассона; |
|
|
|
|
|
|
|
|
|
|
|
|||||
d1 и d2 – диаметры вала (внутренний) и втулки (наружный). |
|
|||||||||||||||
Из формул (7.6) и (7.7) находят расчётный натяг: |
|
|||||||||||||||
|
|
|
|
KF |
C |
1 |
|
C |
2 |
|
|
|
|
|||
|
|
|
N |
a |
|
|
|
|
|
|
. |
|
(7.9) |
|||
|
|
|
|
|
|
|
|
|
|
|
|
|||||
|
|
|
|
l f |
|
E1 |
|
E2 |
|
|
|
|
||||
|
|
|
|
|
|
|
|
|
|
Для крутящего момента Т и комбинации нагрузок справедливы следующие равенства:
N |
2KT C |
|
C |
|
|
||
|
|
1 |
2 |
|
; |
||
|
|
|
|||||
|
dl f |
E1 |
|
E2 |
|
|
|
|
|
|
|
C |
|
|
|
|
|
|
|
K Fa2 |
(2T / d 2 ) |
1 |
|
C |
2 |
|
||||
N |
|
|
|
|
|
|
|
|
. |
||
|
|
|
|
|
|
|
|
||||
|
|
|
l f |
|
|
E1 |
|
E2 |
|
||
|
|
|
|
|
|
|
(7.10)
(7.11)
Механические характеристики материалов соединений приведены в прил. 17.
Формула (7.11) является универсальной. Поправка на шабровку (вводится только для механической сборки):
u 1,2 (Rz1 Rz 2 ), |
(7.12) |

где Rz1 и Rz2 – максимальные высоты шероховатостей посадочных поверхностей,
мм; рекомендуется для прессовых соединений следующие сочетания шероховатостей: Rz1/Rz2 = 0,0063/0,01; 0,0032/0,063 мм.
Технологический натяг:
NT N u. |
(7.13) |
По технологическому натягу выбирается посадка с выполнением условия:
(7.14)
где Nmin - минимальный табличный натяг.
Рекомендуемые посадки и их натяги приведены в прил. 18.
Пример 7.1. Рассчитать посадку ступицы на цилиндрический вал с d = 50
мм, d1 = 0, d2 = 70 мм, l = 80 мм. Материал деталей – сталь (Е = 21,5·10-4 МПа, =
0,3). Крутящий момент Т = 240 Н м; осевая нагрузка Fa = 800 Н. Сборка тепловая.
Решение.
Коэффициенты – формула (7.8):
C |
50 |
0,3 0,7; |
C |
702 |
502 |
0,3 3,38. |
|
702 |
502 |
||||
1 |
50 |
|
2 |
|
При коэффициенте запаса К = 1,5 расчётный натяг – формула (7.11):
N1,5 8002 (2 240 103 / 50)2
80 0,13
|
0,7 |
|
3,38 |
|
|
|
3 |
|
|
|
|
|
|
|
|
|
10 |
|
8,39 мкм. |
21,5 104 |
21,5 |
10 |
4 |
|
|||||
|
|
|
|
|
|
Принимаем посадку
|
|
|
|
0,025 |
|
Ж50 |
H 7 |
Ж50 |
|
|
|
r6 |
|
0,050 |
|
||
|
|
|
|
||
|
|
|
|
0,034 |
|
с минимальным натягом Nmin = 0,034 – 0,025 = 0,009 мм = 9 мкм > N.
Вывод. Принята посадка Ж50 Hr67 .
Пример 7.2. Рассчитать посадку ступицы на цилиндрический вал диаметром d = 50
мм с шероховатостью Rz1 = 6,3 мкм; Rz2 = 10 мкм. Расчётный натяг N = 10 мкм.
Сборка механическая.
Решение.
Определяем поправку на шабровку:
u = 1,2 (6,3 + 10) = 19,56 мкм.
Технологический натяг: NT = 10 + 19,56 = 29,56 мкм.
0,025
Принимаем посадку: Ж50Н7/t6 = Ж50 |
|
с табличными натягами Nmin = 29 |
0,070 |
||
|
0,054 |
|
мкм > и Nmax = 70 мкм (прил. 18). |
|

Лекция № 10
7.6. Расчёт вероятностных натягов
Предельные табличные натяги Nmin и Nmax не отражают степени надёжности соединений. Распределение действительных размеров по полям допусков делает маловероятной сборку соединений из деталей с предельными размерами.
Поэтому, обрезая «хвосты» кривых распределения действительных размеров и допуская тем самым вероятность разрушения соединений, можно увеличить минимальный и снизить максимальный табличные натяги (рис. 7.7). Полученные таким образом натяги называют вероятностными.
|
ITD |
|
|
D |
|
|
|
EI=0 |
ES |
Nmin |
ITd |
|
|||
d |
|
ei |
|
|
|
es=Nmax |
|
|
|
f(D) |
f(d) |
|
|
|
|
|
|
Npmin |
|
|
|
Nm |
|
|
|
Npmax |
|
|
Рис. 7.7. Вероятностные натяги |
Площадь под кривой распределения считают равной 1. После обрезания
«хвостов» она уменьшается. Например, при вероятности неразрушения Р = 0,99
она составляет 0,99. При нормальном законе распределения размеров
вероятностные натяги определяют по формулам:
N p min Nm up SN ; (7.15)
N p max Nm up SN ,
где Nm – средний натяг;

up – квантиль нормального распределения;
SN – среднее квадратичное отклонение табличного натяга.
Средний натяг определяют средними значениями отклонений:
Nm 0,5(es ei) 0,5(ES EI ) ei 0,5(ITd ITD ).
Среднее квадратичное отклонение табличного натяга:
SN SA2 SB2 ,
SA (ES EI ) / 6 ITD / 6,
SB (es ei) / 6 ITd / 6.
(7.16)
(7.17)
(7.18)
Квантиль нормального распределения принимает следующие значения в зависимости от вероятности Р неразрушения (неразбираемости) соединения
(табл. 7.1).
|
|
|
|
|
Таблица 7.1 |
|
|
Квантили нормального распределения |
|
|
|||
|
|
|
|
|
|
|
Р |
0,9 |
0,95 |
0,99 |
0,995 |
0,999 |
|
|
|
|
|
|
|
|
up |
1,28 |
1,64 |
2,33 |
2,58 |
2,9 |
|
|
|
|
|
|
|
|
Таблица вероятностных натягов приведена в прил. 18.
Пример 7.3. Проверить пригодность посадки Ж50Н7/s6 с учетом
вероятности неразрушения. Технологический натяг NТ = 30 мкм.
Решение.
Изучение таблицы вероятностных натягов (прил. 18) позволяет принять
вероятность |
Р |
= 0,95 для обеспечения |
пригодности |
посадки |
|||
|
|
|
0,025 |
|
|
||
Ж50 |
H 7 |
Ж50 |
|
|
. |
|
|
|
0, |
|
|
|
|||
|
s6 |
059 |
|
|
|
||
|
|
|
0,043 |
|
|
||
|
Минимальный табличный натяг: Nmin = 0,043 - 0,025 = 0,018 мм. Он не |
||||||
обеспечивает заданный технологический натяг. Максимальный натяг |
Nmax = |
||||||
0,059 мм. Наименьшее предельное отклонение вала: |
еi = 0,043 мм. Допуски: ITD |
= 0,025 мм; ITd = 0,059 - 0,043 = 0,016 мм. Вероятностные натяги Nmin = 30 мкм,
Nmax = 47 мкм (прил. 18).