
Методички / Курс деталей машин
.pdf
Прямые валы различают: простые (ступенчатые и гладкие, сплошные и полые), торсионные и трансмиссионные. Последние два вида прямых валов передают только вращающий момент (изгибающий момент М = 0).
Рис. 23.2. Гибкий вал
Опорные участки валов и осей называются цапфами. Цапфа,
воспринимающая радиальные нагрузки, называется шейкой, реже – шипом.
Цапфа, воспринимающая осевую нагрузку, называется пятой.
23.2. Конструкции валов
А) Ступенчатая конструкция.
Такая конструктивная форма вала определяется условиями монтажа и посадками соединяемых с валом деталей. Ступенчатая конструкция вала (рис. 23.3) типична для редукторов общего машиностроения. Она имеет следующие обоснования:
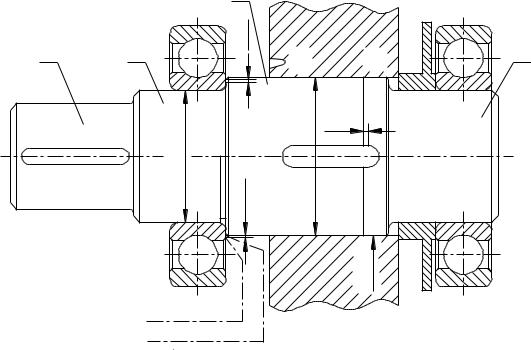
так же, как и фаски, выбирают в зависимости от диаметра. Минимальную разность диаметров соседних участков определяют из условия обеспечения надёжного упора насаживаемой детали. Таким упором служит кольцевая площадка Д шириной не менее 1 мм. Шейки и другие посадочные поверхности шлифуют до шероховатости Rz = 10…3,2 мкм. Тяжело нагруженные валы шлифуют по всей длине.
Кольцевые проточки Г для выхода шлифовальных кругов глубиной
0,2…0,4 мм устраняют необходимость применения фасонных шлифовальных кругов, но существенно снижают усталостную прочность валов из-за значительной концентрации напряжений; их применяют в малонагруженных участках валов.
Для осевой фиксации подшипников на валах делают упорные буртики
(уступы, заплечики), высота которых должна обеспечить надёжный упор,
который обязателен для деталей длиной l меньше диаметра d (центрирование по торцу), и в то же время обеспечить демонтаж подшипника. По технологии ремонта для снятия подшипника с шейки вала лапки съёмника Е должны захватывать выступающее внутреннее кольцо подшипника по высоте не менее 1
мм. Практически разность диаметров соседних участков принимают d = 5…15
мм.
Подступичная часть (головка) 3 вала имеет наибольший размер. На усталостную прочность вала в месте посадки ступицы оказывает значительное влияние тип соединения с валом. При передаче крутящего момента основным шпоночным соединением посадка с небольшим натягом H7/p6 обеспечивает хорошее центрирование ступицы на валу. Передача нагрузки за счёт натяга
H7/r6 или H7/s6 разгружает шпонку, её ставят для надёжности окружной фиксации деталей.
С целью облегчения сборки шпоночного соединения часть подступичной части Н выполняют по посадке H7/h6. Для уменьшения концентрации напряжений от напрессовки необходимо проектировать специальную форму ступицы: кольцевые проточки К и монтаж ступицы с торцом Л, выходящим за торец головки. Участок 2 у правого торца вала также является шейкой вала.
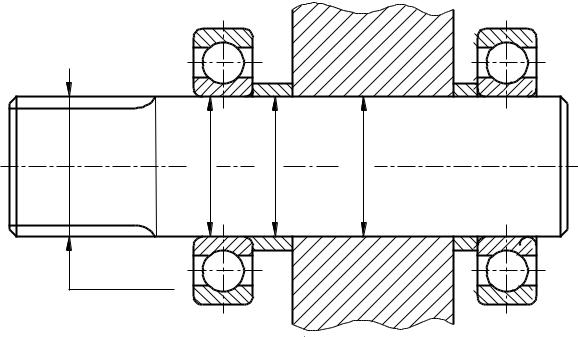
прессовую посадку вала со ступицей назначают со смешанными предельными отклонениями, например, S7/k6.
Таким образом, высокотехнологичная гладкая конструкция валов серьёзно конкурирует со ступенчатой и она в последнее время получила широкое распространение.
23.3. Причины отказов и критерии расчёта
А) Поломка является наиболее опасным видом отказа. Она составляет
40…50% случаев и происходит по следующим причинам:
–циклическое изменение напряжений изгиба;
–наличие концентраторов напряжений, связанных с конструктивной формой (переходное сечение) и технологическими дефектами;
–нарушение норм технической эксплуатации: неправильная регулировка подшипников, уменьшение необходимых зазоров и т.п.
Б) Износ шеек, а также его крайнее проявление: заедание (задир) и
выплавление вкладышей характерны для подшипников скольжения.
В) Недостаточная изгибная и крутильная жёсткость валов могут привести к концентрации нагрузки в зубчатом зацеплении, защемлению тел качения в подшипниках качения либо к разрыву масляной пленки в подшипниках скольжения.
Г) Для валов опасны изгибные и крутильные колебания, которые в состоянии резонанса могут привести к поломке вала. Таким образом, основными критериями работоспособности и расчёта валов являются:
1.Объёмная прочность и выносливость.
2.Жёсткость.
3.Виброустойчивость.
Прямые валы изготавливают из углеродистых и легированных сталей. Чаще других применяют сталь Ст5 для валов без термообработки, сталь 45 или 40Х для улучшенных валов, сталь 20 или 20Х для быстроходных валов на подшипниках скольжения, у которых шейки цементируют для повышения износостойкости.
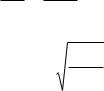

диаметры шеек и головки. Конструкция вал–шестерня возможна при отношении диаметра вершин шестерни к диаметру головки
d d 2. |
(23.3) |
a1 г |
В процессе ориентировочного расчёта выполняется предварительное конструирование вала.
Пример 23.1. Выполнить ориентировочный расчёт редукторных валов по данным примера 11.1: крутящие моменты на валах Т1 = 161,9 Н·м, Т2 = 551,8 Н·м,
диаметр вершин шестерни da1 = 65,31 мм. Недостающими данными задаться.
Решение.
Диаметр головки быстроходного вала:
16161,9103
d3 38мм.
15
Принимаем диаметр головки dг = 38 мм (прил. 15). Проектируем ступенчатый вал. Принимаем диаметр шейки d = 30 мм [9]. Диаметр хвостовика dх
= 25 мм. Разность диаметров головки и шейки d = 38 - 30 = 8 мм.
Предварительно назначаем подшипники 206 со следующими характеристиками: d×D×B×r = 30×62×16×1,5 [9]. За вычетом двух координат фаcки подшипника 2r =
2·1,5 = 3 мм и двух координат фаски на головке (с = 1,5 мм [9]) заплечик для упора подшипника равен 2t = d – 2(r + c) = 8 – 3 – 2·1,5 = 2 мм. Ширины кольцевой площадки t = 1 мм достаточно для надёжного упора.
Отношение da1/ dг = 65,31/38 = 1,7. Принимаем конструкцию вал–шестерня.
Диаметр головки тихоходного вала:
16551,8103
d3 57,2мм.
15
Принимаем диаметр головки dг = 60 мм (прил. 15). Проектируем гладкий вал с хвостовым шлицевым участком.
23.5. Приближённый расчёт валов
Приближенный расчёт валов заключается в определении диаметров из расчёта при сложном напряженном состоянии, то есть по крутящему Т и

изгибающему М моментам. Вал обычно рассматривают как балку, шарнирно закрепленную в двух жёстких опорах. Такая модель формы вала и закрепления близка к действительности для валов, вращающихся в опорах качения.
Нагрузки от зубчатых колес, шкивов, звёздочек и т.п. деталей передаются на вал через поверхности контакта. В расчётах валов эти нагрузки для упрощения заменяют сосредоточенными эквивалентными силами, приложенными в середине ступицы. В процессе расчёта назначают расстояния между опорами,
которые в дальнейшем могут быть уточнены. По этим причинам расчёт называется приближённым. Последовательность расчета:
1.Выполняют эскизную компоновку, имеющую целью предварительное конструирование вала и корпуса редуктора и, прежде всего, определение расстояний между линиями действия всех сил (пример на рис. 23.5). Начинают компоновку с нанесения осей валов, контуров валов и деталей, на них закреплённых. Диаметры валов принимают по ориентировочному расчёту, для них назначают подшипники лёгкой серии. Затем намечают внутренние контуры редуктора, конструируют подшипниковые узлы и т.д.
2.Строят расчётную схему, в которой действующие силы (Fa и Ft) приводят
коси вала с добавлением сосредоточенного момента m = Fa·d/2 и вращающего момента Т. Расчётную схему разделяют на две схемы – от сил, действующих в направлении двух координатных осей.
3.Определяют реакции опор. Для этого используют два уравнения равновесия: моментное уравнение и уравнение проекций. Третье уравнение равновесия (второе моментное уравнение) используют для проверки.
4.Определяют изгибающие моменты и строят эпюры изгибающих моментов от сил, действующих в двух плоскостях.
5.Определяют суммарные изгибающие моменты в опасных (расчётных)
сечениях по формуле:
|
|
|
|
|
|
|
|
|
|
M M M. |
(23.4) |
|||
|
x |
y |
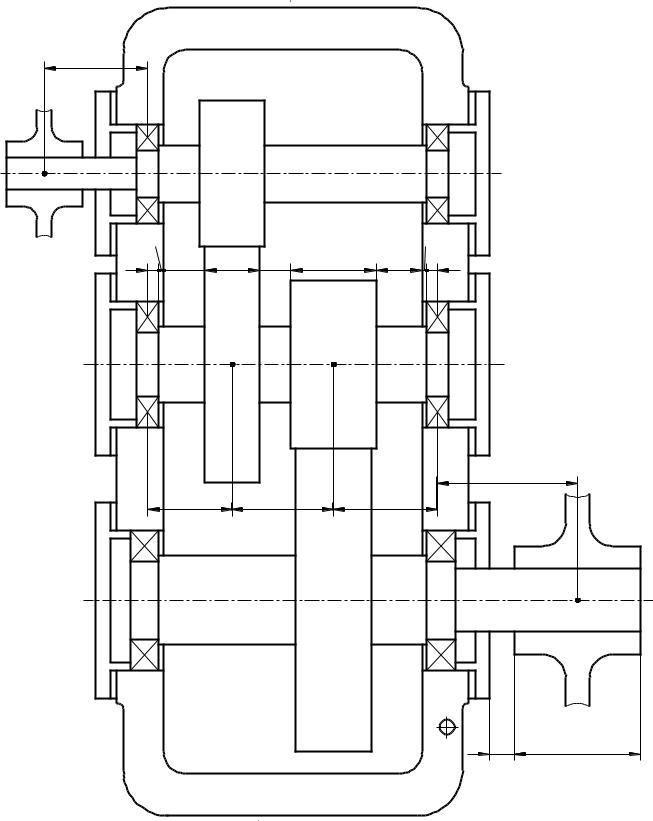
lкб |
|
|
|
|
|
|
|
4 |
2 |
|
1 |
|
2 |
4 |
|
B/2 |
b'2 |
b''1 |
B/2 |
|
|||
|
|
|
|
|
|
|
lкт |
|
l1 |
|
l2 |
|
l3 |
|
|
|
|
|
|
|
|
2 |
l ст |
Рис. 23.5. Эскизная компоновка двухступенчатого редуктора
6. Определяют приведенный момент:
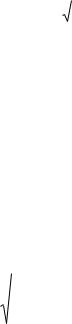
M пр |
M 2 T 2 , |
(23.5) |
где – коэффициент соответствия циклов изменения касательного и нормального напряжений; при нереверсивной работе вала (пульсирующий цикл изменения касательных напряжений) = 0,7; при реверсивной работе
(симметричный цикл) = 1. Изгибные напряжения вала всегда изменяются по симметричному циклу.
7. Определяют диаметр вала в расчётном сечении (по наибольшему моменту
Мпр):
d |
|
32M |
|
|
|
|
|
пр |
(23.6) |
||||
|
|
, |
||||
3 |
|
[ |
] |
|
||
|
|
|
||||
|
|
1 |
|
|
|
где [ -1] – допускаемое изгибное напряжение; для валов из углеродистых и легированных сталей рекомендуется принимать [ -1] = 50…60 МПа.
В процессе приближённого расчёта окончательно назначают размеры валов и их предельные отклонения, допуски формы и расположения поверхностей, шероховатость поверхностей и т.п. Расчёт осей выполняют по формуле (23.6) по наибольшему изгибающему моменту М.
Пример 23.2. Выполнить приближённый расчёт промежуточного вала двухступенчатого коническо-цилиндрического редуктора по следующим исходным данным: крутящий момент TII = 84 Н·м, делительные диаметры колёс dm2 =171,77 мм; d1 = 65,57 мм; окружные усилия Ft1 =1032 Н, Ft2 = 2562 Н;
радиальные усилия Fr1 = 102 Н, Fr2 = 956 Н; осевые усилия Fa1 = 362 Н, Fa2 = 572
Н; расстояния между линиями действия сил: l1 = 70 мм, l2 = 60 мм, l3 = 50 мм.
Материал вала сталь 40Х, термообработка – улучшение. Работа нереверсивная.
Решение.
1) Составляем расчётную схему вала (рис. 23.6). На схеме нагружения валов действующие силы приложены в соответствии с кинематической схемой: силы на коническом колесе приложены в верхней точке, а на цилиндрической шестерне – в нижней точке зацепления. Окружные силы Ft показаны действующими в одном направлении, но они создают крутящие моменты противоположного направления.
Направление Ft1 определяет направление вращения вала. Сила Ft2 на шестерне