
Методички / Курс деталей машин
.pdf25.4. Оценка и применение
Достоинства:
1.Простота конструкции.
2.Высокая демпфирующая способность.
3.Малые радиальные габариты.
Недостатки:
1.Высокое трение и износ при всех режимах, кроме жидкостного трения.
2.Необходимость сложной системы смазки.
3.Необходимость применения дорогостоящих материалов.
Область применения подшипников скольжения в современном машиностроении значительно сократилась в связи с широким распространением подшипников качения, однако в определенных областях они сохранили преимущество.
1.Высокоскоростные подшипники, в условиях работы которых долговечность подшипников качения резко сокращается (при n > 10000 об/мин).
2.Подшипники тяжелонагруженных тихоходных валов, для которых не изготавливаются стандартные подшипники качения.
3.Подшипники, работающие в особых условиях (вода, агрессивная среда), в
которых подшипники качения неработоспособны.
4.Подшипники прецизионных машин, от которых требуется особое точное направление валов и возможность регулирования, например шпиндель шлифовального станка.
5.Разъёмные подшипники коленчатых и других валов.
6.Подшипники тесно расположенных валов.
25.5. Виды разрушения и критерии расчёта
Опыт эксплуатации показал, что подшипники, работающие в режиме граничного и полужидкостного трения, выходят из строя по следующим причинам:
1.Заедание, проявляющееся в виде намазывания и задира, способствующее выплавлению подшипника – основная причина разрушения.
2.Абразивное изнашивание, особенно опасное при засорении смазочного материала.
3.Усталостное выкрашивание и отслаивание фрикционного слоя при вибрационных и ударных нагрузках.
4.Хрупкое разрушение фрикционного слоя – характерно для баббитов и некоторых пластмасс.
Основным критерием работоспособности и расчёта подшипников
скольжения, работающих в режиме полужидкостного трения, является износостойкость. Износостойкость характеризуется параметрами р, рυ и υ,
являющимися по существу критериями подобия, обобщающими опыт эксплуатации подшипников. Так как режим жидкостного трения возможен в ограниченном числе случаев, методика его расчёта не рассматривается. Для повышения износостойкости в подшипниках применяют антифрикционные материалы:
1.Баббит на оловянной, свинцовой и другой основе – один из лучших материалов. Отличается высокой хрупкостью.
2.Бронзы оловянистые, свинцовые, кремниевые и прочие обладают достаточно высокими механическими характеристиками, но сравнительно плохо прирабатываются и способствуют окислению масла. Их широко применяют в крупносерийном и массовом производстве.
3.Чугун обладает хорошими антифрикционными свойствами благодаря включениям свободного графита, но прирабатывается хуже, чем бронза.
4.Пластмассы (капрон, текстолит и др.), дерево, резина и другие материалы могут работать при водяной смазке.
5.Металлокерамика получается прессованием при высоких температурах порошков бронзы или железа с добавлением графита, меди, олова или свинца.
Поры занимают 20…30% объёма вкладыша и используются как маслопроводящие каналы.
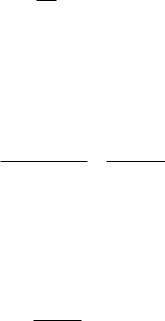
Вопросы для самоподготовки
1) Как классифицируют подшипники по виду трения и воспринимаемой нагрузке?
2)Какие виды трения Вы знаете?
3)Какие условия необходимы для образования режима жидкостного трения?
4)Дайте оценку подшипников скольжения.
5)В каких областях подшипники скольжения получили исключительное применение?
6)Какие материалы применяют в подшипниках скольжения?
7)В каких единицах измеряется вязкость масла?
8)Какие виды разрушений характерны для подшипников скольжения?
9)Как назначается длина подшипника скольжения?
10)По каким критериям подобия рассчитываются подшипники скольжения в режиме полужидкостного трения?
Вопросы, выносимые на экзамен
1.Подшипники скольжения. Оценка и применение. Виды разрушений,
расчёт на износостойкость и нагрев.
2.Виды трения. Жидкостное трение. Условия, необходимые для его образования.
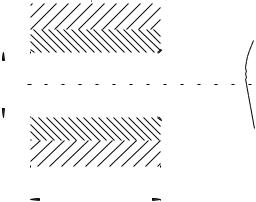
Экзаменационная задача
Задача №43
Выполнить проверочный расчёт подшипника скольжения по давлению,
скорости и на нагревание. Вал стальной.
|
|
|
|
|
|
|
|
|
|
|
|
|
|
|
|
|
|
|
|
|
|
|
|
|
|
|
|
|
|
|
|
|
|
|
|
|
|
|
|
|
|
|
|
|
|
|
|
|
|
|
|
|
|
|
|
|
|
|
|
|
|
|
|
|
|
|
|
|
|
|
|
|
|
|
|
|
|
|
|
|
|
|
|
|
|
|
|
|
|
|
|
|
|
|
|
|
|
|
|
|
|
|
|
|
|
|
|
|
|
|
|
|
|
|
|
|
|
|
|
|
|
|
|
|
|
d |
|
|
|
|
|
|
|
|
|
|
|
|
|
|
|
|
|
|
|
|
|
|
|
|
|
|
|
|
|
|
|
|
|
|
|
|
|
|
|
|
|
|
|
|
|
|
|
|
|
|
|
|
|
|
|
|
|
|
|
|
|
|
|
|
|
|
|
|
|
|
|
|
|
|
|
|
|
|
|
|
|
||
|
|
|
|
|
|
|
|
|
|
|
|
|
|
|
|
|
|
|
|
|
|
|
|
|
|
|
|
|
|
|
|
||||||||||
|
|
|
|
|
|
|
|
|
|
|
|
|
|
|
|
|
|
|
|
|
|
|
|
|
|
|
|
|
|
|
|
|
|
|
|
|
|
|
|
|
|
|
|
|
|
|
|
|
|
|
|
|
|
|
|
|
|
|
|
|
|
|
|
|
|
|
|
|
|
|
|
|
|
|
|
|
|
|
|
|
|
|
|
|
|
|
|
|
|
|
|
|
|
|
|
|
|
|
|
|
|
|
|
|
|
|
|
|
|
|
|
|
|
|
|
|
|
|
|
|
|
|
|
|
|
|
|
|
|
|
|
|
|
|
|
|
|
|
|
|
|
|
|
|
|
|
|
|
|
|
|
|
|
|
|
|
|
|
|
|
|
|
|
|
|
|
|
|
|
|
|
|
|
|
|
|
|
|
|
|
|
|
|
|
|
|
|
|
|
|
|
|
|
|
|
|
|
|
|
|
|
|
|
|
|||||
|
|
|
|
|
|
|
|
|
|
|
|
l |
|
|
|
|
|
|
|
|
|
|
|
|
|
|
|
|
|
|
|
|
|
|
|
|
|||||
|
|
|
|
|
|
|
|
|
|
|
|
|
|
|
|
|
|
|
|
|
|
|
|
|
|
|
|
|
|
|
|
|
|
|
|
|
|
|
|
|
|
|
|
|
|
|
|
|
|
|
|
|
|
|
|
|
|
|
|
|
|
|
|
|
|
|
|
|
|
|
|
|
|
|
|
|
|
|
|
|
|
|
|
|
|
|
|
|
|
|
|
|
|
|
|
|
|
|
|
|
|
|
|
|
|
|
|
|
|
|
|
|
|
|
|
|
|
|
|
|
|
|
|
|
|
Наименование параметра |
|
|
|
|
|
|
|
|
|
|
|
|
|
|
|
|
|
|
|
Вариант |
|
|
|||||||||||||||||||
1 |
|
|
|
2 |
|
|
|
3 |
4 |
5 |
6 |
||||||||||||||||||||||||||||||
|
|
|
|
|
|
|
|
|
|
|
|
|
|
|
|
|
|
|
|
|
|
|
|
||||||||||||||||||
Диаметр шейки d, мм |
60 |
|
|
65 |
|
|
70 |
80 |
85 |
90 |
|||||||||||||||||||||||||||||||
Частота вращения n, об/мин |
250 |
|
350 |
|
500 |
400 |
450 |
600 |
|||||||||||||||||||||||||||||||||
Радиальная нагрузка Fr, кН |
3 |
|
|
|
3,5 |
|
|
4 |
5 |
7 |
2 |
||||||||||||||||||||||||||||||
Материал вкладыша (1 – антифрикционный |
|
|
|
|
|
|
|
|
|
|
|
|
|
|
|
|
|
|
|
|
|
|
|
|
|||||||||||||||||
чугун АЧВ-2; 2 – бронза БрО10Ф1; 3 – баббит Б- |
1 |
|
|
|
2 |
|
|
|
3 |
4 |
5 |
6 |
|||||||||||||||||||||||||||||
16; 4 – бронза БрА9Ж4; 5– бронза БрС30; 6– |
|
|
|
|
|
|
|||||||||||||||||||||||||||||||||||
|
|
|
|
|
|
|
|
|
|
|
|
|
|
|
|
|
|
|
|
|
|
|
|
||||||||||||||||||
цинковый сплав ЦАМ 10-5) |
|
|
|
|
|
|
|
|
|
|
|
|
|
|
|
|
|
|
|
|
|
|
|
|
Примечание. Длину подшипника принять l = d, при необходимости увеличить.
Лекция №23
Тема 26: Подшипники качения
26.1. Оценка и применение
Подшипники качения являются основным видом опор вращающихся деталей. Применение подшипников качения позволило заменить трение скольжения трением качения и существенно уменьшить зависимость их работы от смазки.
Достоинства:
1.Малое трение (условный коэффициент трения f = 0,0015…0,006).
2.Малые осевые размеры (в 2…3 раза в сравнении с подшипником скольжения).
3.Простота технического обслуживания и подачи смазочного материала.
4.Низкая стоимость изготовления, определяемая изготовлением подшипников в массовых количествах как стандартной продукции.
Недостатки:
1.Большие радиальные габариты.
2.Низкая работоспособность при вибрационных и ударных нагрузках.
3.Ограниченная быстроходность, связанная с центробежными силами.
4.Отсутствие разъёмных конструкций.
Отмеченные достоинства обеспечили широкое применение подшипников качения во всех машинах и многих приборах. В России ежегодно изготовляется сотни миллионов подшипников качения.
26.2. Конструкции и маркировка
Подшипник качения (рис. 26.1) состоит из двух колец, наружного и внутреннего, между которыми расположены тела качения. Для предохранения тел качения от соприкосновения между собой их отделяют друг от друга
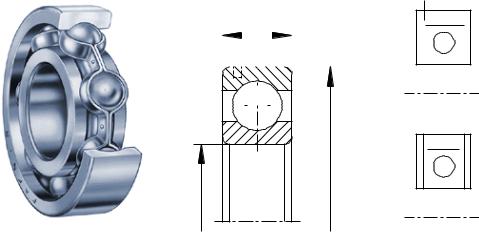
сепаратором. Встречаются подшипники без сепаратора (игольчатые подшипники) либо без одного из колец или без обоих колец.
а) |
б) |
|
|
B |
|
|
|
в) |
|||||
|
|
|
|
|
|
|
|
|
|
||||
|
|
|
|
|
|
|
|
||||||
|
|
|
|
|
|
|
|
|
|
|
|
|
|
|
|
|
|
|
|
|
|
|
|
|
|
|
|
|
|
|
|
|
|
|
|
|
|
|
|
|
|
|
|
|
|
|
|
|
|
|
|
|
|
|
|
|
|
|
|
|
|
|
|
|
|
|
|
|
|
|
|
|
|
|
|
|
|
|
|
|
|
|
|
|
|
|
|
|
|
|
|
|
|
|
|
|
|
|
|
|
|
|
|
|
|
|
|
|
|
|
|
г)
d D
Рис. 26.1. Радиальный однорядный шарикоподшипник
По форме тел качения подшипники подразделяют на шариковые и роликовые; последние в свою очередь делят по форме роликов на подшипники с короткими цилиндрическими, длинными цилиндрическими, коническими,
бочкообразными и витыми роликами.
Грузоподъёмность подшипников зависит от следующих конструктивных факторов:
1.Формы тел качения (роликовые подшипники имеют большую площадку контакта).
2.Числа тел качения, размещаемых между кольцами.
3.Числа рядов.
4.Серии подшипников, при увеличении которой увеличивается ширина подшипника В, наружный диаметр D и диаметр тел качения dw.
Кольца и тела качения изготовляют из специальных подшипниковых сталей марок ШХ15, ШХ15Ш, ШХ15СГ, ШХ20СГ и др., закаливаемых до твердости
Н = 60…66 HRC. Сепараторы изготовляют из мягкой углеродистой стали,
текстолита, латуни и других материалов, обладающих антифрикционными свойствами.
Условные обозначения подшипников качения содержат информацию о внутреннем диаметре подшипника d, его серии, типе, конструктивных

особенностях и классе точности. Все перечисленные параметры обозначаются цифрами. В общем обозначении:
8 |
7 |
6 |
5 |
4 |
3 |
2 |
1 |
цифры, отсчитываемые справа, обозначают: 1 и 2, помноженные на 5 , дают d;
3 и 7 (чаще 3) – серию подшипника; например, 2 – легкая серия, 3 – средняя
и т.д.,
4 – тип подшипника;
5 и 6 – конструктивные особенности;
8 – класс точности, который указывают перед обозначением через черточку:
0 – нормальный класс, 6 – повышенный, 5 – высокий и т.д. Нули, стоящие в обозначении слева, в том числе класса точности, опускают.
26.3.Радиальные подшипники
0.Шарикоподшипники радиальные однорядные – тип 0000 (рис. 26.1) могут воспринимать радиальную Fr, а также умеренную осевую нагрузку Fa,
действующую в обоих направлениях. Конструкция подшипника обеспечивает возможность фиксирования вала в осевом направлении. Допустимый угол взаимного перекоса осей колец подшипника составляет θ = 10…15 . Сепаратор – змейковой конструкции. На рисунках а) – фотография, б) – чертёж, в) – условные обозначения на сборочных чертежах.
Промышленность изготовляет значительное количество конструктивных модификаций подшипников данного типа. Например, подшипник 50000 имеет канавку на наружном кольце под стопорное наружное кольцо. Подшипник 80000
имеет две защитные шайбы (рис. 26.1, г).
Пример 26.1. Расшифровать обозначение подшипника 180208.
Решение.
Обозначение соответствует радиальному шарикоподшипнику (0 на четвёртом месте справа) легкой серии (2) с внутренним диаметром
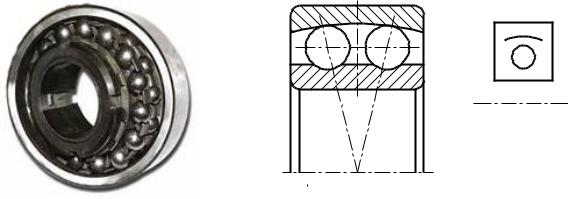
d = 08 × 5 = 40 мм с двумя защитными шайбами (8) и двусторонним уплотнением
(1). Класс точности – нормальный (0 опущен).
Подшипники 0000 наиболее простые и дешёвые, поэтому при
проектировании при отсутствии специальных требований следует
ориентироваться на их применение; их относительная грузоподъёмность С = 1.
1. Шариковые радиальные двухрядные сферические подшипники 1000 (рис.
26.2) предназначены для восприятия радиальных и небольших осевых нагрузок (С
= 0,8 за счёт уменьшения площадки контакта вследствие большой разницы радиусов шарика и дорожки качения). Конструкция подшипника позволяет поворот цапф на θ = 2…3 . Сепаратор штампованный лепесткового типа.
Применяют, например, в грузоподъёмных машинах при расположении подшипников в разных корпусах (опоры барабанов).
а) б) в)
Рис. 26.2. Сферический шарикоподшипник
3. Роликоподшипники с короткими цилиндрическими роликами 2000
(рис. 26.3) предназначены для восприятия значительных радиальных нагрузок
(С = 1,5). Только некоторые из конструкций воспринимают кратковременные небольшие осевые нагрузки, фиксируя вал в осевом направлении.
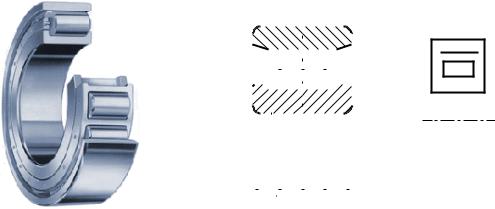
а) |
б) |
|
|
|
|
|
|
|
|
|
|
|
|
|
|
в) |
||
|
|
|
|
|
|
|
|
|
|
|
|
|
|
|
|
|
|
|
|
|
|
|
|
|
|
|
|
|
|
|
|
|
|
|
|
|
|
|
|
|
|
|
|
|
|
|
|
|
|
|
|
|
|
|
|
|
|
|
|
|
|
|
|
|
|
|
|
|
|
|
|
|
|
|
|
|
|
|
|
|
|
|
|
|
|
|
|
|
|
|
|
|
|
|
|
|
|
|
|
|
|
|
|
|
|
|
|
|
|
|
|
|
|
|
|
|
|
|
|
|
|
|
|
|
|
|
|
|
|
|
|
|
|
|
|
|
|
|
|
|
|
|
|
|
|
|
|
|
|
|
|
|
|
|
|
|
|
|
|
|
|
|
|
|
|
|
|
|
|
|
|
|
|
|
|
|
|
|
|
|
|
|
|
|
|
|
|
|
|
|
|
|
|
|
|
|
|
|
|
|
|
|
|
|
|
|
|
|
|
|
|
|
|
|
|
|
|
|
|
|
|
|
|
|
|
|
|
|
|
|
|
|
|
|
|
|
|
|
|
|
|
|
|
|
|
|
|
|
|
|
|
|
|
|
|
|
|
|
|
|
|
|
|
|
|
Рис. 26.3. Радиальный роликоподшипник
Основная конструкция (без буртов на одном из колец) позволяет иметь
плавающие опоры и валы. Подшипники требуют высокой соосности посадочных мест (θ = 2). Применяют в буксах железнодорожного подвижного состава,
вентиляторах, электродвигателях, паровых и газовых турбинах и т.д.
3. Роликоподшипники радиальные сферические двухрядные 3000 (рис. 26.4)
имеют повышенную радиальную грузоподъёмность (С = 2). Они способны компенсировать значительную несоосность, прогибы вала (θ = 2…3 ) и
воспринимать небольшие осевые нагрузки (до 25% от неиспользованной радиальной). Применение бочкообразных роликов позволяет снизить концентрацию напряжений на их кромках и повысить долговечность.
Сферические роликоподшипники обычно устанавливают на длинных валах,
подверженных значительным прогибам или в опорах отдельных корпусов. Их применяют также в подвижном составе, опорах насосов, прокатных станов и в других машинах, где действуют большие радиальные нагрузки и неизбежна несоосность посадочных мест.