
1496
.pdfКроме того, после осмотра ведущего твердосплавного круга было обнаружено образование на нем тонкой масляной пленки. Причиной ее появления, по-видимому, стало минеральное масло, входящее в состав эмульсола ВЭЛС-1. Образовавшаяся на ведущем твердосплавном круге масляная пленка явилась причиной нестабильного шлифования, так как она препятствовала надежному фрикционному сцеплению деталей
сведущим кругом. Это привело к неравномерной скорости вращения детали и к изменению величины продольной подачи детали. В связи
сэтим нами был сделан вывод, что для работы на бесцентровошлифовальном станке фирмы «Модлер» СОЖ ВЭЛС-1 не пригодна. СОЖ для этого станка не должна содержать минеральные масла, т.е. это должна быть синтетическая водорастворимая эмульсия.
Поэтому следующей была испытана синтетическая СОЖ Тех- мол-1, Техмол-1 представляет собой стабильный концентрат синтетической СОЖ, содержащий полиалкиленгликоли, жирные кислоты, ингибиторы коррозии и другие добавки, придающие СОЖ необходимые эксплуатационные свойства. При этом СОЖ Техмол-1 по сравнению с СОЖ ВЭЛС-1 обладает более высокими антикоррозионными свойствами, более длительным сроком службы, более высокой стойкостью к биопоражению и более высокими моющими свойствами.
В результате испытаний установлено, что при шлифовании с СОЖ Техмол-1 наблюдается обильное пенообразование. Анализ состава СОЖ показал, что склонность этой эмульсии к пенообразованию и стойкость пены зависят главным образом от качества и количества исходных поверхностно-активных веществ в эмульсоле, в частности, олеиновой кислоты. Пена представляет собой пузырьки воздуха, окруженные пленкой поверхностно-активных веществ. Вследствие того, что пена обладает значительно меньшей теплопроводностью, чем вода, охлаждающие свойства эмульсии резко снижаются. Кроме того, наличие пены приводит к загрязнению оборудования и рабочих мест.
Для снижения склонности эмульсии к пенообразованию в эмульсию добавили антипенную присадку ПМС-200А, а также
141
уменьшили в СОЖ содержание олеиновой кислоты. В результате этих мероприятий пенообразование в 1-й день снизилось. Однако на следующий день пена образовывалась вновь при шлифовании. Дополнительные добавки пеногасителя для снижения пенообразования не дали положительных результатов. В то же время нужно отметить, что, несмотря на возникшую проблему с пенообразованием, требуемое качество обработки было обеспечено, а именно: точность получения диаметрального размера 14–0,006 мм, шероховатость обработанной поверхности Rа ≤0,32 мкм, отклонение от цилиндричности – не более 2 мкм, отсутствие коррозии и прижогов на обработанных деталях.
Всвязи с этим была продолжена работы по исследованию другой синтетической СОЖ Карбамол-С1П, которая в своем составе имеет более низкое содержание олеиновой кислоты, по сравнению с СОЖ Техмол-1. Водосмешиваемая синтетическая СОЖ Кар- бамол-С1П обычно используется при обработке шлифованием конструкционных, нержавеющих, жаропрочных и жаростойких сталей
исплавов.
Врезультате проведенных исследований и производственных испытаний установлено, что качество обработанных деталей после шлифования соответствовало требованиям технологии, однако коррозионная стойкость СОЖ уменьшилась и на станке появились пятна коррозии. Для подавления коррозионной агрессивности СОЖ добавили ингибиторы и пассиваторы коррозии. Ингибиторы – вещества, замедляющие электрохимические процессы между внешней средой
иметаллом. Действия пассиваторов металла заключается в образовании на его поверхности защитной пленки, предохраняющей металл от дальнейшего развития коррозионных процессов. В качестве ингибитора коррозии использовался триэтаноламин, а в качестве пассиватора коррозии – нитрит натрия. В результате добавления этих веществ коррозия на станке исчезла, но это привело к появлению липкой пленки на деталях, несмываемой ни керосином, ни другими моющими жидкостями.
142
После дополнительных исследований составов синтетических СОЖ было найдено наиболее рациональное решение: при шлифовании применять СОЖ Карбамол-С1П, а при последующей промывке деталей в ванне использовать СОЖ Техмол-1. Результаты последующих длительных производственных испытаний по этой методике показали, что после шлифования обеспечиваются стабильно требуемые геометрические параметры деталей, отсутствует интенсивное пенообразование, коррозия станка и липкая пленка на деталях. Процесс шлифования на этом станке стабилизировался на том же уровне, что и при использовании импортной СОЖ.
1.12. Особенности роторного шлифования наружных концов пера лопаток компрессора
Впроцессе сборки роторов компрессора высокого давления ГТД на вал ротора устанавливается комплект дисков и лопаток компрессора. Размеры устанавливаемых лопаток отличаются по длине в пределах размерного допуска. В результате диаметральный размер ротора может иметь отклонения от норматива на 0,5–1,5 мм. Для придания необходимых диаметральных размеров ротора с допуском 0,05–0,1 мм применяется обработка шлифованием по вершинам лопаток. На ОАО «ПМЗ» обработка роторов проводится на модернизированном токарно-винторезном станке ДИП-300 (рис. 61). Шлифовальная головка установлена на салазки резцедержателя, связанные
скопировальным устройством. Обработка происходит при вращении ротора и поступательном перемещении шлифовальной головки по копиру. Шлифование осуществлялось без применения СОЖ, всухую, так как попадание жидкости в ротор недопустимо. Для повышения жесткости лопаток применяется обмотка лопаток резиновыми жгутами.
Впроцессе шлифования обрабатываются лопатки 14 ступеней компрессора с постепенным увеличением наружного диаметра на каждой последующей ступени. Первые по ходу продольной подачи круга ступени лопаток имеют меньший диаметр и изготовлены из
143
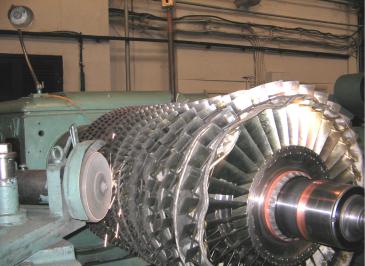
жаропрочных сплавов на никелевой основе ВЖЛ 14 (2 ступени) и из ЭИ787ВД (6 ступеней). Последующие ступени лопаток большего диаметра изготовлены из титанового сплава ВТ8-М (6 ступеней).
Рис. 61. Общий вид процесса шлифования наружного диаметра ротора компрессора
В качестве шлифовальных кругов на первом этапе этого комбинированного шлифования предложены шлифовальные круги из электрокорунда белого следующей характеристики: 1 250×40×32 25А 25Н СТ1 5 К5. Правка круга проводилась на конус с помощью стандарных алмазных карандашей. Скорость вращения круга составляла 22 м/с, продольная подача по копиру 200 мм/мин, глубина шлифования 0,1 мм/ход. В результате шлифования установлено, что жаропрочные сплавы ВЖЛ 14 и ЭИ787ВД шлифуются вполне удовлетворительно, однако при дальнейшем шлифовании лопаток из титанового сплава ВТ8-М происходило засаливание круга, увеличивалась температура и на концах лопаток появлялись следы прижогов. Применение кругов меньшей твердости, изменение связки и плотно-
144
сти кругов не дали положительных результатов. На втором этапе испытаны круги из карбида кремния зеленого 63С на тех же режимах шлифования. Результаты испытаний более эффективные. Круги меньше засаливались, но на последних ступенях титановых лопаток зачастую появлялись прижоги, т.е. процесс шлифования нестабилен.
Для повышения стабильности процесса шлифования проведено испытание метода смазки карандашами твердой смазки. В состав карандашей твердой смазки введены материалы, плавящиеся при повышении температуры контакта и обладающие смазывающими свойствами: сера, парафин, дисульфид молибдена и др. Кроме того, в состав смазки введены кластерные алмазы для повышения эффективности шлифования. В результате применения новой технологии удалось решить полностью проблему шлифования наружных концов лопаток ротора на модернизированном токарно-винторезном станке.
1.13. Выбор эффективных абразивных методов удаления дефектов на поверхности проточной части рабочих турбинных лопаток при их изготовлении и ремонте
На ОАО «Пермский моторный завод» наряду с изготовлением новых двигателей проводится ремонт отработавших положенный ресурс двигателей с полной разборкой и дефектацией деталей.
В течение длительного времени на предприятии существует проблема отбраковки ремонтных рабочих лопаток турбины по недопустимым свечениям на поверхности проточной части лопаток, выявляемые при люминесцентном контроле (ЛЮМ1-ОВ контроле). Причинами свечений могут быть дефекты поверхностного слоя в виде пор, рисок, забоин, наплывов и др. Удаление этих дефектов, как при изготовлении (литейные дефекты), так и при ремонте представляет большую проблему на многих моторостроительных предприятиях. Работа была поставлена с целью разработки перспективных технологических процессов ремонта рабочих лопаток турбин, обеспечивающих повышение качества ремонта лопаток при удалении поверхностных дефектов на проточной части и уменьшение отбраковки.
145
Существующая технология ремонта с помощью абразивных головок путем местной обработки поверхности проточной части лопаток на участке полировки имеет недостаточное качество и низкую производительность, поэтому после такой зачистки лопатки с оставшимися недопустимыми свечениями бракуются.
Методика проведения экспериментальной работы предусматривала выбор наиболее эффективных абразивных методов удаления дефектов в следующей последовательности:
1.Подготовлена партия ремонтных лопаток турбины III–VI ступеней двигателя ПС-90А с характерными дефектами в виде недопустимых свечений на поверхности проточной части лопаток.
2.Проведен анализ поверхностных дефектов на проточной части лопаток, после чего все лопатки разбиты по группам с характерными местами свечений.
3.Проведена обработка мест недопустимых свечений лопаток различными способами механической обработки.
4.Зафиксирован характер изменения количества свечений на ЛЮМ1-ОВ контроле.
5.Проведен анализ проспектов и каталогов перспективного оборудования и подготовлены предложения для ремонта лопаток турбин.
6.Проанализированы результаты исследований и составлены рекомендации.
Партия забракованных ремонтных рабочих лопаток турбины III–VI ступеней двигателя ПС-90А прошла местные зачистки по действующей ремонтной технологии, с характерными дефектами на поверхности проточной части. Дефекты на поверхности проточной части лопаток выявлялись в виде недопустимых свечений на ЛЮМ1-ОВ контроле согласно ТУ 08.068 «Несоответствия поверхности на литые лопатки турбин» не позже двух дней с момента нанесения краски.
Лопатки разделены на следующие группы по местам расположения и типам характерных свечений:
• радиус перехода пера к бандажной полке – групповые и одиночные свечения;
146
•групповые свечения на пере;
•групповые совпадающие свечения на пере;
•групповые совпадающие свечения в радиусе перехода бандажной полки;
•штриховые свечения на поверхности проточной части;
•одиночные точечные свечения на поверхности проточной
части.
Указанные на ЛЮМ1-ОВ контроле места с недопустимыми свечениями подвергались местной механической обработке. Для исследования технологии ремонта проточной части лопаток были выбраны такие способы механической обработки, которые можно опробовать на предприятии в настоящее время:
1) серийная обработка абразивными головками;
2) пескоструйная обработка на новой установке настольного ти-
па «EasyBlast»;
3) струйная гидроабразивная обработка на цеховой стационарной установке;
4) ленточное полирование на станке ЛПС-1.
Оценка качества поверхностного слоя проточной части обработанных лопаток оценивалась только параметром шероховатости поверхности Ra.
Лопатки по геометрическим характеристикам не оценивались, так как основная цель работы была направлена на определение и опробование дополнительных эффективных методов удаления дефектов для выбора и приобретения оборудования. Точная оценка геометрии возможна только при обработке крупной партии лопаток на полученном оборудовании с учетом его технологических возможностей.
Серийная технология ремонта поверхностей проточной части рабочих лопаток в настоящее время предусматривает (рис. 62) применение следующих инструментов:
1) круги войлочные полировальные:
•А2793-4099 13А-24А 6-12ПГ (200×50×20),
•А2793-4023 13А-24А 6-12ПГ (40×50×3),
147
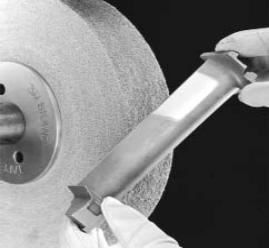
Рис. 62. Общий вид зачистки профиля пера лопатки турбины полировальными абразивными кругами при серийном ремонте
•А2793-4171 13А-24А 6-12ПГ (40×15×6),
•А2793-4249 13А-24А 6-12ПГ (35×40×5); 2) головки шлифовальные:
•ГК3 20×32 24А25ПСТ1-СТ3К,
•ГУ 25×8 24А25НСТ1-СТ3К;
3) оправки:
•А6374-0098,
•А6374-0088,
•А6274-0571 с А6274-0422,
•А6274-0570;
4) шлифовальный круг для правки – 1.150×32×51 54С 80Н ВТК. В результате выполнения ремонта по серийной ремонтной технологии установлено, что при обработке мест свечений с целью удаления дефектов полировка является недостаточно эффективным, непроизводительным и трудоемким способом. При зачистке мест свечений образуются местные углубления, риски и другие макро-
148
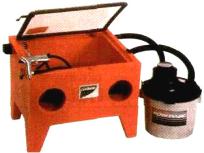
имикронеровности на поверхности проточной части лопаток, которые требуют последующего их выведения войлочными накатными кругами с мелким зерном.
Пескоструйная обработка мест дефектов струйно-абразивным способом проведена на новой пескоструйной установке настольного типа «EasyBlast» (рис. 63). Установка снабжена регулятором давления в диапазоне 1–6 атм, устройством ручной загрузки абразивного зерна в специальную камеру. Рабочая зона установки имеет два небольших сопла для подачи струи
иместное освещение камеры.
Для устойчивой работы |
без |
|
потери давления, т.е. для постоян- |
|
|
ной интенсивности обработки на |
|
|
данной установке применяют до- |
Рис. 63. Общий вид пескоструйной |
|
полнительный воздушный |
ком- |
|
прессор. |
|
установки настольного типа |
|
|
Экспериментально выбран режим, обеспечивающий удаление дефектов на установке «EasyBlast»: давление воздуха 4 атм, время обработки 45–50 с. Сначала обрабатывается местный точечный дефект – 2 с, затем плавно увеличивается пятно обработки.
Лопатки по проточной части имеют удовлетворительный внешний вид. Параметр шероховатости поверхностного слоя Ra обработанных лопаток находится в диапазоне 1,15–1,17 мкм, что соответствует 7-му классу чистоты поверхности. Абразивная среда – электрокорунд белый 25А10 – обеспечивает получение требуемой шероховатости поверхности.
Проведенные исследования показали, что пескоструйной обработкой можно уменьшить количество недопустимых свечений и получить до 15 % годных по ЛЮМ1-ОВ контролю лопаток.
Пескоструйным методом также опробована обработка радиусов щели выходной кромки рабочих лопаток турбины из сплава ЖС26 с целью исключения появления трещин в эксплуатации. Принято
149
решение по внедрению пескоструйного метода при обработке радиусов выходной щели.
Установка «EasyBlast» имеет небольшие технологические возможности:
•малый объем камеры, приводимый к быстрому износу смотрового стекла и его замене;
•малый объем емкости, подающей абразивный материал; возможна обработка не более 7–8 лопаток;
•нет устройства повторной циркуляции абразива.
К положительным сторонам установки можно отнести следую-
щие:
•малый диаметр сопла обеспечивает местную зачистку. Целенаправленный поток струи исключает рассеивание абразивного материала;
•установка снабжена регулировкой давления и манометром;
•дистанционное управление подачи абразива с помощью пе-
дали.
Установка для пескоструйной обработки лопаток должна иметь: 1) износостойкие сопла разных выходных диаметров из карбида
вольфрама или полиуретана; 2) удобное для работы подающее сопло «карандашного» типа;
3) автоматическую блокировку подачи абразива при открывании камеры;
4) дистанционное управление подачи абразива (педаль); 5) емкость для абразива должна иметь объем 8–10 л; 6) циркуляцию абразива для повторного использования.
Пескоструйная обработка – перспективный производительный способ удаления дефектов. На обработанной поверхности образуется неориентированный микрорельеф, как и при струйной гидроабразивной обработке, что также может повышать предел выносливости лопаток при усталостных испытаниях.
Струйная гидроабразивная обработка (СГАО) проводилась на цеховой струйно-гидроабразивной установке заводского изготовления.
150