
1496
.pdfДополнительную экономию зерна 63С может дать технология изготовления комбинированных кругов со ступицей из дешевого абразива. Она была опробована при изготовлении кругов ПП200×32×32. Из формовочного песка предварительно при давлении 2,8 МПа прессовались ступицы, высота которых была на 2–5 мм меньше глубины пресс-формы для окончательного изготовления кругов. Чтобы получить требуемую структуру рабочей части круга, давление прессования нужно повысить в 1,3–1,5 раза. Круги, изготовленные по этой технологии, имеют разрывную скорость 67–84 м/с, что обеспечивает безопасную эксплуатацию при рабочих скоростях до 40 м/с. Трудоемкость изготовления кругов возрастает в 1,65– 1,85 раза.
Изготовление кругов ПП200×32×32 и ПП300×40×76 со ступицей из формовочного песка позволит снизить расход зеленого карбида кремния на 30 %: будет дополнительно экономиться около 27 т карбида кремния зернистости № 25 и около 36 т карбида зернистости № 40.
Производственные испытания комбинированных кругов дали вполне удовлетворительные результаты. Для изготовления таких кругов разработано специальное автоматическое устройство.
Одним из путей экономии зерна 63С является применение высокопористых кругов. Однако производственные испытания высокопористых кругов на бакелитовой связке с различными наполнителями не дали положительных результатов.
В результате исследований во всех рассмотренных вариантах выбран и внедрен в производство вариант изготовления смесевых (63С(60 %)+54С(40 %) кругов. В комбинации с изготовлением ступицы кругов из дешевых абразивных материалов, этот вариант позволяет экономить более 50 % (или более 150 т в год) зерна 63С.
251
2.4.2. Интенсификация процессов полирования путем спецподготовки абразивного зерна
и микропорошков
Для интенсификации процессов полирования проведены работы по повышению стойкости полировальных войлочных кругов с накаткой, по совершенствованию технологии приготовления клеевого раствора, по обеспечению стабильной шероховатости на профиле пера лопаток.
Лопатки ГТД, являющиеся ответственнейшими деталями двигателя, характеризуются сложной геометрией профиля пера, шероховатость которого в зависимости от назначения лопатки должна быть Rа = 0,63…0,32 мкм. Требуемая высокая точность профиля и низкая шероховатость обеспечиваются ручным полированием. Этот процесс состоит из предварительного размерного полирования и собственно полирования (глянцевания).
Предварительное размерное полирование позволяет получить требуемый профиль (осуществляется подгонка профиля до требуемых размеров по контрольным сечениям). Для выполнения его используются эластичные бакелитовые круги, на поверхность которых нанесен абразив.
Глянцевание обеспечивает получение требуемой шероховатости практически без снятия припуска (в пределах допуска на размер). При этом используются эластичные круги, покрытие абразивными пастами.
При полировании применяются различные типы эластичных кругов: войлочные и фетровые, хлопчатобумажные и бумажные, а при глянцевании дополнительно применяют круги из морской травы и капроновой лески.
Наибольшее распространение на предприятии получили войлочные круги с накатанным на мездровый клей абразивом. При полировании лопаток из жаропрочных сталей, никелевых и алюминиевых сплавов применяются, как правило, электрокорундовые материалы 14A и 24А, при полировании титановых лопаток − карбид кремния 63С. Зернистость шлифпорошков – от М40 до M12. В поли-
252
ровальных пастах используются те же абразивы зернистостью от М5 до М6.
Ручное полирование имеет низкую производительность труда, для его выполнения требуются высококвалифицированные рабочие, работать им приходится в антисанитарных условиях, что является одной из причин большой утомляемости рабочих, кроме того, качество продукции при ручном полировании зависит от квалификации рабочего.
Положение усугубляется низким качеством накатных полировальных кругов из-за недостаточной клеящей способности мездрового клея и некачественной подготовки абразивного зерна перед накаткой.
Указанные недостатки обусловили необходимость проведения специальной исследовательской работы, нацеленной на повышение качества полировальных кругов (стойкости, режущей способности), а также на гарантированное обеспечение требуемой шероховатости (Rа = 0,63 мкм) при полировании лопаток.
Применяемая в ОАО «ПМЗ» технология накатки состоит в следующем. На поверхность войлочных полировальных кругов накатывается шлифпорошок. В качестве связки используется мездровый клей марки КМЭ или КМВ. Чешуйчатый мездровый клей разваривается в горячей воде для получения клеевого раствора требуемой вязкости. Горячий раствор наносится на поверхность войлочного круга. Далее круг посредством оправки при некотором усилии прокатывается в лотке с подогретым шлифпорошком до полного насыщения клея абразивом. Накатка шлифпорошка может осуществляться однократно иди многократно. После нанесения абразивно-клеевой массы круги сушат.
Анализ показал, что в ОАО «ПМЗ» в отличие от родственных предприятий разварка мездрового клея осуществляется при более высокой температуре, что, по литературным данным, снижает его клеящую способность. Кроме того, клеевой раствор доводится до требуемой вязкости путем разбавления водой, чего не делают на других предприятиях. На ряде родственных заводов для повышения
253
клеящей способности в клей добавляют желатин. Таким образом, существующая технология накатки войлочных кругов имеет ряд существенных недостатков и требует совершенствования.
При полировании войлочными кругами титановых лопаток используются шлифпорошки карбида кремния зеленого 63С зернистостью 8–12 (предварительно), а лопаток из жаропрочных сталей, никелевых и алюминиевых сплавов – шлифпорошки нормального электрокорунда 24А зернистостью 5–6 (окончательно). Предварительное полирование осуществляется без полировальных паст, окончательное, как правило, с пастами. Скорость круга колеблется в пределах 8–35 м/с и зависит от частоты вращения шпинделя шлифовальной бабки (2800–7800 об/мин) и диаметра круга 55–200 мм).
Перед полированием профиль пера лопаток подгоняется шлифовальными кругами на бакелитовой или керамической связках из белого электрокорунда 24А или зеленого карбида кремния 63C зернистостью 25–40. Сформированные на этом переходе глубокие риски требуется вывести на последующих переходах полировальными кругами. После окончательного полирования шероховатость профиля пера лопаток должна соответствовать Rа = 0,32 мкм или Rа = = 0,63 мкм (в зависимости от назначения лопатки), риски не допускаются.
На родственных предприятиях требования к операции полирования и применяемый инструмент аналогичны.
Технология полирования за 2 перехода в ряде случаев не обеспечивает требуемую шероховатость на профиле пера и удаление рисок от предыдущих проходов. Для гарантированного получения требуемой шероховатости необходимо исследовать влияние режимов полирования и характеристик кругов на величину шероховатости и на базе полученных результатов уточнить технологию полирования ряда лопаток.
Для повышения стойкости полировальных кругов следует увеличить прочность удержания зерен клеевой пленкой. Прочность удержания можно повысить двумя способами: увеличением количества клея (за счет повышения вязкости клеевого раствора) или уве-
254
личением адгезии между абразивом и клеем. Увеличение рабочей вязкости клеевого раствора уменьшает поровое пространство для размещения стружки, что приводит к снижению режущей способности кругов. Более целесообразно увеличение адгезии между зерном
иклеем.
Вкачестве критерия смачиваемости абразива клеем можно использовать величину капиллярности шлифпорошка, характеризуемую высотой подъема жидкости в трубке, заполненной абразивом.
Из технической литературы известно, что капиллярность абра-
зивного зерна, подвергнутого термообработке при 450–480 °С, а также имеющего покрытие (алюмофосфатожелезооксидное, железо-, титан- и хромоксидное), значительно больше (в 2–3 раза). Стойкость абразивного инструмента, изготовленного с применением данного зерна, повышается в 1,5–5,0 раза.
Из описания в литературе способов повышения капиллярности абразивов наиболее простым является термообработка, обеспечивающая активацию клеем и зерном. Однако при хранении термообрабатываемого зерна его капиллярность снижается. Поэтому необходима разработка системы мер по предотвращению дезактивации поверхности термообработанного шлифпорошка в процессе его хранения.
Существенное влияние на режущую способность абразива оказывает гранулометрический состав зерна. Одним из экспрессметодов определения гранулометрического состава и степени изометричности зерен является контроль насыпного веса. Для микропорошков выявлена линейная зависимость абразивной способности от их насыпного веса. Насыпной вес увеличивается с увеличением изотермического зерна, а также с увеличением размеров зерен. Можно попробовать стабилизировать режущую способность кругов путем стабилизации насыпного веса.
Гранулометрический состав шлифпорошков исследовался методом контроля насыпного веса. Применялся прибор ПКНВ по ГОСТ 26327–84 с объемом мерного стакана 200 мл, спроектированный и изготовленный для проведения данной работы.
255
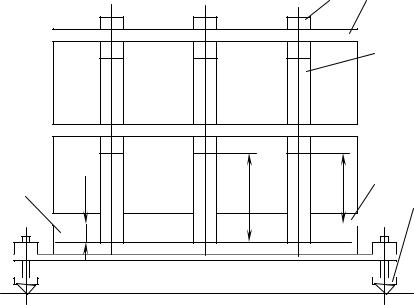
Установлено, что термообработка шлифпорошков не влияет на их насыпной вес. Вместе с тем не обнаружено увеличения насыпного веса с увеличением зернистости: у карбида кремния 63С зернистостью 5 насыпной вес (1,373 г/см3) меньше, чем у порошка зернистостью 12 (1,336 г/см3) и карбида кремния черного 54C12 (1,35–1,353 г/см3), но больше, чем у карбида кремния зеленого
(1,336 г/см3).
Капиллярность шлифпорошков, характеризующая их смачиваемость водными растворами клея, определялась путем изменения высоты столба смоченного водой зерна. Для реализации этого метода был спроектирован и изготовлен прибор ПКК-1 (рис. 114).
|
|
|
2 |
3 |
|
|
|
|
4 |
1 |
12 |
H |
К |
5 |
|
||||
|
|
|
6 |
|
|
|
|
|
Рис. 114. Схема прибора ППК-1 для контроля капиллярности абразивного зерна: 1 – жидкость (вода); 2 – трубка; 3 – стойка; 4 – абразивный порошок; 5 – стойка; 6 – установочный винт
256
Исследования показали, что в начальный период скорость подъема жидкости 1 по трубке 2 с зерном 4 максимальна, затем она снижается и через некоторый промежуток времени после начала контроля стабилизируется на уровне К. Время контроля устанавливается в 1,5–2,0 раза больше, чем время стабилизации скорости подъема жидкости.
Для порошков различной зернистости время контроля различно:
Зернистость |
6 и менее |
8–12 |
16–25 |
32–40 |
35–63 |
Время, мин |
10 |
6 |
4 |
3 |
2,5 |
Исследовалась капиллярность шлифпорошков зеленого и черного карбида кремния зернистостей 5 и 12. Сравнивались шлифпорошки в состоянии поставки, а также в активированном состоянии (непосредственно после термообработки и после выдержки на воздухе). Активирование осуществлялось термообработкой шлифпорошков при 800 °С с выдержкой 1,5–4,0 ч и последующим охлаждением на воздухе.
Термообработка в течение 4 ч шлифпорошка 54C12 повысила его капиллярность на 45–50 % (со 115–130 до 180–190 мм). Хранение этого активированного зерна в картонной упаковке при комнатной температуре (20–25 °С) и относительной влажности 40–60 % в течение 1–2 суток привело к снижению капиллярности на 10 % (до 160– 175 мм). При дальнейшем хранении зерна в течение 10 суток капиллярность осталась на прежнем уровне.
Увлажнение активированного зерна путем его погружения в воду и последующая сушка при комнатной температуре (20–25 °С) до воздушно-сухого состояния снижают капиллярность на 15 % (до 150–165 мм).
Замасливание активированного зерна резко уменьшает его капиллярность (до 20–35 мм).
Таким образом, активация шлифпорошков путем термообработки при 800 °С обеспечивает повышение их капиллярности до 1,5 раза. Хранение активированного зерна во влажной атмосфере
257
и даже в контакте с водой незначительно снижает его капиллярность
(на 10–15 %).
Исследования также показали, что активация шлифпорошков повышает не только высоту подъема столба жидкости, но и скорость капиллярного поднятия в 1,5 раза. Так, скорость капиллярного поднятия воды в первую минуту для шлифпорошка 54C12 возросла с 50 до 70 мм/мин, а после стабилизации – с 10 до 15 мм/мин. Время же стабилизации скорости капиллярного поднятия снизилось после термообработки шлифпорошка с 4 до 3 мин.
Исследования проводились на лопатках из литейного никелевого сплава ВЖЛ 14ВИ и из титанового сплава ВТ8-М.
Сравнивались круги с термообработанным при 800 °С (выдержка 0,5 ч и более) и нетермообработанным зерном.
Введение термообработки повысило стойкость кругов при полировании ВЖЛ 14ВИ в 2–3 раза, при полировании лопаток из ВТ8-М в 3–4 раза.
Такое существенное повышение стойкости кругов объясняется лучшим удержанием мездровым клеем термообработанных зерен, имеющих большую капиллярность. Наряду с повышением стойкости круга увеличивается и режущая способность. Это объясняется тем, что при правке полировального круга с использованием активированных шлифпорошков крупные зерна не осыпаются и участвуют в полировании.
Исследование влияния режимов полирования на шероховатость профиля пера лопаток показало, что с уменьшением зернистости полировального круга шероховатость снижается с 1,0 мкм (24А6
и 14A6) до 0,8 (24А М63) и 0,5 мкм (14A M40), т.е. при уменьшении зернистости шлифпорошка на 1 номер (в 1,25 раза) шероховатость снижается на 1 разряд (в 1,25 paзa). Однако при использовании кругов зернистостью М63 и мельче после полирования остаются риски от предыдущей обработки вследствие уменьшения режущей способности мелкозернистых кругов. Следовательно, для стабильного удаления ранее сформированного микрорельефа при полировании накатными кругами без пасты зернистость шлифпорошка на после-
258
дующем переходе должна быть мельче, чем на предыдущем, не более чем в 2 раза. При этом каждый последующий переход улучшает шероховатость обработанной поверхности не более чем на 1 класс.
Применение твердой смазки в виде карандашей (КТС) уменьшает шероховатость поверхности в 2,5–3,0 раза (более чем на 1 класс). Однако при полировании без поперечной подачи смазка размазывается на обрабатываемой поверхности и затрудняет полирование.
Полировальные пасты обеспечивают шероховатость, почти в 2 раза меньшую (на 1 класс), чем полировальные круги с накаткой этим же зерном, но несколько более грубую (на 30 %, т.е. на 1 разряд), чем полировальные круги с КТС. Режущая способность у «елочных» кругов с пастой значительно ниже, чем у кругов с накаткой зерна, в результате на обрабатываемой ими поверхности остаются риски от предыдущей обработки.
При накатке кругов шлифпорошки карбида кремния обеспечивают несколько меньшую шероховатость, чем электрокорунд, при равной зернистости.
Применение активированного термообработкой шлифпорошка для накатки кругов приводит в ряде случаев к снижению шероховатости в 1,5 раза (при использовании зерна 24А6 и 24А М63) или к ее увеличению на 20 % (зерно 14A M40).
С увеличением скорости круга при полировании с 8 до 22 м/с шероховатость ухудшается в 3 раза.
Два последних момента (увеличение шероховатости с ростом скорости шлифования и неоднозначное влияние термообработки зерна) не укладываются в традиционное понятие о формировании шероховатости при шлифовании, что потребовало дополнительных исследований.
Традиционно считается, что при шлифовании с увеличением скорости круга за счет уменьшения толщины срезов шероховатость снижается и одновременно увеличивается режущая способность круга.
Установлено, что по мере затупления накатного круга на первых 1–2 деталях шероховатость обработанной поверхности в среднем не-
259
сколько снижается, а затем стабилизируется. Поэтому сравнение осуществлялось не по первым деталям, а по последующим, начиная с 3-й, где шероховатость стабилизировалась.
С увеличением скорости круга с 18 до 25 м/с происходит некоторый рост шероховатости (на 10 %), что может быть объяснено следующим. При ручном полировании увеличение режущей способности круга, связанное с ростом скорости шлифования, приводит при постоянном усилии прижима детали к кругу к увеличению толщины среза и, как следствие, к увеличению шероховатости.
Применение активированного шлифпорошка для накатки кругов несколько повышает шероховатость обработанной поверхности: с 0,63 мкм (для стандартного зерна 24А6 и 24А М63) до 0,8 мкм (для активированного зерна 24А М63) и 1,0 мкм (для активированного зерна 24А6). Увеличение шероховатости объясняется лучшим удержанием клеем крупных зерен после их активации. Следовательно, полировальные круги, накатанные активированным шлифпорошком, работают как более крупнозернистые. Поэтому при использовании активированного зерна для накатки кругов с целью обеспечения требуемой шероховатости необходимо, как правило, брать его зернистостью на 1–2 номера мельче.
При полировании образцов из алюминиевого сплава ВД-17 (полки лопаток 42-01-101) с поперечной подачей получены аналогичные результаты. Применение активированного шлифпорошка 24А6 привело к увеличению шероховатости на 25–30 %.
На основании исследований можно сделать следующие выводы:
1)с целью снижения шероховатости и удаления рисок необходимо последовательно осуществлять полирование кругами с накаткой, уменьшая их зернистость не более чем в 2 раза на каждом последующем переходе;
2)уменьшение зернистости до 2 раз пропорционально снижает величину шероховатости;
3)применение смазки (КТС) улучшает шероховатость на 1 класс
иболее;
260