
1496
.pdf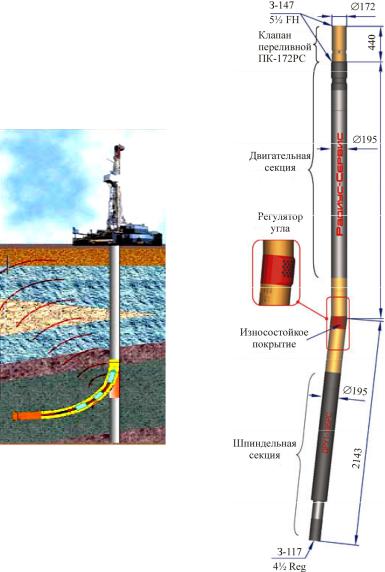
Рис. 142. Схема горизонтального |
Рис. 143. Винтовой забойный двига- |
бурения |
тель с регулятором угла ДРУ1-195РС |
|
311 |
•комплектация двигателей регуляторами угла;
•оснащение двигателей рабочими парами российского и зарубежного производства с различными энергетическими характеристиками;
•комплектация двигателей переливными клапанами собственного производства для опорожнения и наполнения бурильной колонны при спуско-подъемных операциях;
•изготовление нижней радиальной опоры с использованием твердых сплавов, ее максимальная приближенность к долоту;
•соединение ротора двигательной секции и вала шпиндельной секции посредством карданного вала с маслонаполненными шарнирами;
•армирование твердым сплавом поверхностей косых переводников и зубчатых муфт регулятора угла в местах их касания со стенкой скважины.
Фирмой «Радиус-Сервис» помимо двигателей разработано и поставляется другое буровое и сервисное оборудование: керноотборные снаряды, элементы бурильной колонны, турбобуры, механические ключи для сборки и разборки гидравлических забойных двигателей, стенды для испытаний забойных двигателей, стенды для выполнения неразрушающего контроля бурового оборудования.
В винтовом забойном двигателе рабочие камеры, образованные поверхностями ротора и статора, должны быть отделены друг от друга в течение всего рабочего цикла. Для выполнения этого условия необходим непрерывный контакт по профилю зуба в любой фазе зацепления. Это обстоятельство еще более ужесточает требования к точности профиля ротора и формующего сердечника пресс-формы статора. Форма ротора – винт. К нему предъявляются жесткие требования по шероховатости. Шероховатость ротора должна быть минимальна, для того чтобы рабочая жидкость, которая приводит ротор во вращение, испытывала минимальное трение о поверхность ротора. Ротор также должен обладать такими качествами, как коррозионная стойкость и износостойкость.
312
Перечисленные требования дают основание характеризовать ротор винтового забойного двигателя как сложную и ответственную деталь.
В недавнем времени роторы гидравлических забойных двигателей обрабатывали на универсальных фрезерных и токарных станках. Но экономика диктует свои правила. Чтобы продукция была конкурентоспособная, необходимо повысить качество ее изготовления. Именно для этого фирмой «Радиус-Сервис» закуплен станок «Weingartner» (Австрия) модели Finish 450 с ЧПУ. Станок предназначен для профильного ленточного шлифования и полирования длинномерных деталей с винтовой поверхностью типа ротор, шнек, червяк. Полное ограждение рабочей зоны, система управления CNC и 3-мерная система оптических измерений ATOS входят в объем стандартной комплектации станка.
Обработка роторов на станке производится шлифовальными лентами. Ленточное шлифование имеет ряд преимуществ перед шлифованием профильными кругами.
Основные преимущества ленточного шлифования:
1.Станки для ленточного шлифования безопасны в эксплуатации, так как разрыв абразивной ленты не приводит к катастрофическим последствиям, как это бывает при разрыве шлифовальных кругов.
2.Ленточно-шлифовальные станки не требуют предварительной балансировки шлифовального круга, что значительно экономит время и упрощает работу при смене инструмента.
3.Стоимость современных абразивных лент ниже, а стойкость вполне сопоставима в сравнении со шлифовальными кругами аналогичных характеристик.
4.Энергозатраты при ленточном шлифовании значительно ниже, чем при работе шлифовальными кругами.
5.Процесс шлифования абразивными лентами поддается автоматизации значительно легче, чем процесс шлифования абразивными кругами.
313
6. Обработка на станке «Weingartner» модели Finish 450 с ЧПУ более точная и более производительная, чем на универсальном токарном модернизированном станке.
В качестве недостатка новой технологии нужно отметить, что станок «Weingartner» модели Finish 450 с ЧПУ работает не на полную мощность. Отмечается фактическая низкая стойкость абразивных лент и низкая скорость резания, что отражается на снижении производительности обработки.
Для повышения стойкости и производительности лент проведены предварительные испытания шлифовальных лент различных ха-
рактеристик: 2803 SIARON P120; СК11Х Р120; 2546 SIABITE JJ P120; 2820 SIAMET X P120; 2848 SIACUT X P120 и др. В результате испытаний установлено, что все перечисленные ленты быстро изнашивались и производительность обработки осталась на прежнем уровне. Испытания возможности применения на этом станке профильного вулканитового круга оказались неудачными, так как станок стал работать ненадлежащим образом.
Для решения проблемы проведены исследования по подбору оптимальных характеристик шлифовальных и оптимальных режимов шлифования. Критериями оптимизации являются параметры обеспечения наименьшей шероховатости и наибольшей производительности.
Одно из решений проблемы – это уменьшение припуска на полировку. Необходимо пересмотреть предыдущий процесс обработки ротора – фрезерование. Если получать минимальный припуск на операции фрезерования, то производительность обработки ротора шлифованием увеличится. Все эти вопросы необходимо рассмотреть в комплексе, так как такие понятия, как качество и производительность, очень зависят друг от друга.
Общая схема винтового двигателя изображена на рис. 144. Многозаходный винтовой героторный механизм представляет
собой цилиндрическую планетарную зубчатую передачу внутреннего зацепления с разницей в числах зубьев статора 1 и ротора 2, равной единице, и межосевым расстоянием, равным половине высоты зубьев героторного механизма.
314
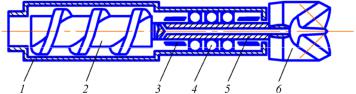
Рис. 144. Упрощенная схема забойного винтового двигателя: 1 – статор; 2 – ротор; 3 – радиальная опора; 4 – осевая опора; 5 – выходной вал; 6 – породоразрушающий инструмент
Особенностью таких зубчатых передач является то, что из-за большой длины героторных механизмов зубья статора выполняются на обкладке из эластомера, привулканизированного к внутренней стенке корпуса статора. Зубчатая поверхность статора формируется сердечником в специальной пресс-форме. Выбор эластомера (обычно это резина) в качестве материала обкладки статора определяется следующими соображениями:
• необходимостью получения достаточной износостойкости
вабразивной среде;
•возможностью прокачивания через рабочие органы случайно попавших в жидкость взвесей;
•технологичностью выполнения рабочих поверхностей зубьев статора;
•необходимостью компенсации неизбежных погрешностей изготовления ротора и статора по профилю, диаметрам, шагу винтовой линии и прямолинейности оси и создания при этом первоначальной герметичности рабочей пары за счет некоторого натяга. Ротор винтового забойного двигателя представляет собой многозаходный винт с нарезкой специального профиля и шагом винтовой линии 300– 1000 мм, выполняемый из конструкционной или нержавеющей стали
(рис. 145).
Предъявляются жесткие требования к точности выполнения диаметров выступов и впадин, профиля зуба, окружного и осевого шагов ротора, а также к шероховатости поверхности, его коррозионной стойкости и износостойкости.
315

Рис. 145. Многозаходный героторный механизм винтового забойного двигателя: 1 – статор; 2 – ротор; 3 – резина
В винтовом забойном двигателе рабочие камеры, образованные поверхностями ротора и статора, должны быть отделены друг от друга в течение всего рабочего цикла. Для выполнения этого условия необходим непрерывный контакт по профилю в любой фазе зацепления. Это обстоятельство еще более ужесточает требования к точности профиля ротора и формующего сердечника пресс-формы статора.
Шероховатость поверхности ротора после фрезерования составляет Ra ≤ 1,6. Условия эксплуатации винтового забойного двигателя
316
требуют более высокой чистоты рабочих поверхностей ротора. Стендовые исследования и промысловые испытания показали, что полированные роторы имеют более высокие срок службы и коррозионную стойкость, чем неполированные.
Ротор винтового забойного двигателя представляет собой многозаходный винт с нарезкой специального профиля и шагом винтовой линии 300–1000 мм. Ротор героторного механизма гидравлического забойного двигателя изготавливается из нержавеющих сталей 20Х13 и 40ХН2МА по следующему технологическому маршруту: прокат, термообработка, токарная, сверлильная, фрезерная операция на станке «Weingartner» модели Vario 700-7000, отрезная, токарная, токарная с ЧПУ, полировальная в два прохода «Weingartner» Finish 450-7000 (шлифовальная лента «БАЗ» СK11X Р120), хромирование, полировальная 1М63 (модернизованный), лента 3М «Scoth-Brite» 300×50×75, токарная, токарная с ЧПУ. При изготовлении предъявляются жесткие требования к точности выполнения диаметров выступов и впадин, профиля зуба, окружного и осевого шагов ротора, а также к шероховатости поверхности, его коррозионной стойкости и износостойкости.
Для активизации процесса шлифования абразивными лентами в настоящее время существуют несколько методов повышения эффективности ленточного шлифования:
1. Метод, предложенный Л.А. Паньковым и Н.В. Костиным [53, 54], – так называемое «реверсирование инструмента». Метод заключается в периодическом изменении направления движения бесконечной абразивной ленты. Авторы предлагают проводить реверсирование через определенные, равные промежутки времени, ориентируясь на изменение величины съема материала. Однако многочисленными исследованиями установлено, что процесс изнашивания абразивных зерен на рабочей поверхности шлифовальной шкурки, является неравномерным по времени, зависящим от многих условий и для успешного использования этого метода необходима методика оперативного контроля состояния инструмента.
317
2.Метод, подробно описанный в работах А.В. Якимова [58], заключающийся в переходе на прерывистое шлифование. Реализация метода связана с получением шлифовальных лент с прерывистой рабочей поверхностью или наложением на абразивный инструмент
низкочастотных колебании в направлении составляющей Ру силы резания. Рекомендаций по применению подобных методов при шлифовании абразивными лентами в литературе крайне мало.
3.Метод регулирования натяжения абразивной ленты. Натяжение абразивной ленты действительно играет большую роль при назначении режимов обработки, однако механизмов, позволяющих регулировать этот параметр в процессе работы по определенной программе пока нет.
4.Применение новых видов смазочно-охлаждающих технологических средств (СОТС). Этот способ не приносит большого эффекта, во-первых, потому, что общее снижение теплового потока, направленного в обрабатываемую поверхность, при применении жидких СОТС составляет не более 30–35 %, во-вторых, применение жидких
СОТС значительно снижает силу сцепления абразивной ленты с опорным роликом, что может привести к пробуксовке и разрушению инструмента, в-третьих, применение жидких СОТС при шлифовании с постоянным усилием прижима может вызвать так называемый эффект аквапланирования, при котором абразивная лента скользит над поверхностью заготовки, опираясь на водомасляный клин. В этом случае наиболее целесообразно применение твердых СОТС на основе стеаринов и парафинов.
5. Увеличение скорости резания до 70 м/с и более. При этом наблюдаются явления, оказывающие как положительное, так и отрицательное влияние на выходные параметры процесса. К положительным явлениям относят следующие:
• С увеличением скорости резания при шлифовании уменьшается толщина среза, приходящаяся на единичное абразивное зерно, кроме того, одновременно происходит увеличение количества режущих зерен, проходящих в единицу времени через зону резания. За счет этого появляется возможность увеличить съем металла в едини-
318
цу времени, т.е. увеличить скорость движения заготовки при сохранении глубины резания, таким образом поднимая производительность.
•Уменьшение толщины среза с увеличением скорости резания приводит к снижению сил резания, шероховатости обработанной поверхности и уменьшению изнашивания инструмента.
•Увеличение скорости резания приводит к уменьшению сопро-
тивления резанию за счет «охрупчивания» материала заготовки. В некоторых работах при увеличении скорости шлифования отмечается уменьшение силы трения в зоне резания.
К отрицательным явлениям, возникающим при увеличении скорости резания, относят следующие:
•С увеличением скорости резания возрастает работа шлифования и температура в зоне контакта инструмента с обрабатываемой поверхностью. В ряде случаев рост температур может быть столь велик, что это приводит к нежелательным изменениям качества обработанных поверхностей: снижению усталостной прочности, струк- турно-фазовым изменениям, увеличению остаточных напряжений.
•В ряде работ шлифование с повышенными скоростями резания приводит к общему снижению стойкости абразивного инструмента из-за большой тепловой нагрузки на режущие зерна.
•Значительное повышение скорости резания может вызывать снижение устойчивости абразивной ленты на лентопротяжном механизме. Могут возникать автоколебания в технологической системе, увеличивается аэродинамический эффект вблизи инструмента.
•Увеличение скорости резания ведет к повышению мощности холостого хода лентопротяжного механизма, что вызывает необходимость повышения мощности привода главного движения.
В производственных условиях технологам трудно ориентироваться в большом количестве разнообразных вариантов повышения эффективности шлифования абразивными лентами, поэтому необходимо создать теоретические и технологические основы повышения эффективности процесса ленточного шлифования.
319
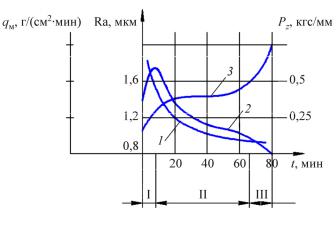
Основной характеристикой ленточного шлифования большинство авторов считают величину съема металла в единицу времени, т.е. режущую способность абразивных лент. В то же время по данным Л.А. Панькова и Н.В. Костина [53, 54] известно, что в период приработки инструмента, происходит резкое изменение большинства выходных параметров, снижение шероховатости и производительности обработки и увеличение усилия резания (рис. 146). Такие изменения приводят к значительному снижению точности обработки, а в отдельных случаях, особенно при шлифовании с постоянным усилием прижима, – к браку.
Рис. 146. Изменение шероховатости поверхности Ra (кривая 1), удельного съема металла qм (кривая 2) и силы резания Pz (кривая 3) по периодам работы абразивной ленты: лента 24А40 на мездровом клее, обрабатываемый материал сталь 40ХЗСМВФЮ; I, II, III – периоды работы инструмента
В этом случае при проектировании операции шлифования для обеспечения требуемого качества и точности обработанной поверхности технологически закладываются искаженные данные, что также приводит к браку. Длительность периода приработки абразивных лент принимается в весьма широком диапазоне: от 4–5 до 8–10 мин и более.
320