
1496
.pdfным уменьшением зернистости 40, 25, 12, 6; 2-й вариант исключает полировку войлочными кругами 14А12Т с целью сокращения трудоемкости; 3-й вариант – подгонку кругами 25А25СМ1К с целью снижения вероятности глубоких рисок; 4-й вариант – подгонку крупнозернистым кругом 25А40СМ1К и полировку войлочными кругами 14А12Т с целью сокращения трудоемкости и вероятности появления рисок.
|
|
|
|
Таблица 25 |
|
Варианты полирования лопаток |
|
||
|
|
|
|
|
Номер |
1-й вариант |
2-й вариант |
3-й вариант |
4-й вариант |
перехода |
|
|
|
|
1 |
25А40НСМ1К, |
25А40НСМ1К, |
25А40НСМ1К, |
25А25НСМ1К, |
|
подгонка |
подгонка |
подгонка |
подгонка |
2 |
25А25НСМ1К, |
14А12Т, |
14А12Т, |
25А6Т, |
|
подгонка |
полировка |
полировка |
полировка |
3 |
14А12Т, |
25А6Т, |
25А6Т, |
25А6Т + пас- |
|
полировка |
полировка |
полировка |
та № 18, |
|
|
|
|
полировка |
4 |
25А6Т, |
25А6Т + пас- |
25А6Т + пас- |
Круг Т |
|
полировка |
та № 18, |
та № 18, |
с пастой № 24, |
|
|
полировка |
полировка |
полировка |
5 |
25А6Т + пас- |
Круг Т |
Круг Т |
|
|
та № 18, |
с пастой № 24, |
с пастой № 24, |
|
|
полировка |
глянцовка |
глянцовка |
|
6 |
Круг Т |
|
|
|
|
с пастой № 24, |
|
|
|
|
глянцовка |
|
|
|
Предварительно и после каждого перехода до окончательного полирования войлочным кругом 25А6Т с пастой № 18 проведены измерения фактического припуска у лопаток в корневом сечении на приборе ПОМКЛ-4, результаты замеров занесены в табл. 26 и составлены диаграммы.
161
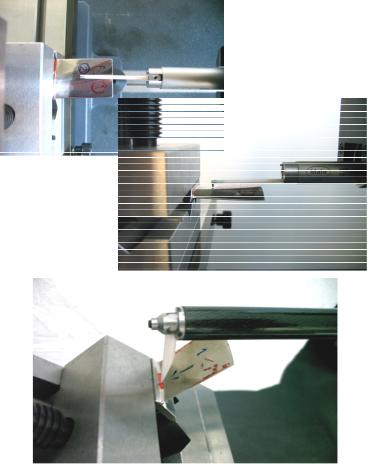
После каждого перехода отобраны по две лопатки для определения шероховатости обработанной поверхности в радиусе сопряжения пера с замком (рис. 75).
Рис. 75. Измерение шероховатости профиля пера и сопряжения лопатки с помощью профилометра фирмы Mahr
162
Глубину рисок в радиусе сопряжения у лопаток замерить с помощью приборов не удалось. Поэтому риски определялись с помощью специально сделанных оттисков (слепков). Оценка глубины рисок на оттисках проводилась с помощью записи профилограммы. По данным заводской ЦИЛ при контроле рисочности методом ЛЮМ1-ОВ возможны недопустимые свечения при глубине риски от 4 мкм. Результаты измерений величины снимаемого припуска и высоты микронеровностей на различных переходах операции полирования представлены в табл. 26. В результате анализа этих данных построены графики изменения осредненного срезаемого припуска и шероховатости пера последовательно по переходам операции полирования со стороны спинки и корыта пера лопаток (рис. 76, 77).
Таблица 26
Величины припуска и шероховатости на пере лопаток по переходам операции полирования
Но- |
Номер |
Снимаемые припуски |
Шероховатость, |
Шерохова- |
мер |
перехо- |
(с – спинка, к – корыто), |
Rа, Rz, мкм, |
тость Rа, Rz, |
вари- |
да |
мкм |
по эталону |
Rаmaх, мкм, |
анта |
|
|
|
по оттиску |
1 |
1 |
с – 1110…50; к – 140…10 |
Rz = 20; Rа = 2,5; |
1,68…2,84; |
|
|
|
|
Rаmaх = 24,6 |
|
2 |
с – 360…100; к – 250…60 |
2,5 |
– |
|
3 |
с – 70…70; к – 0…60 |
– |
– |
|
4 |
с – 0…110; к – 0…60 |
1,25…63 |
– |
|
5 |
с – 10…30; к – 40…20 |
0,63 |
0,34…0,73; |
|
|
|
|
Rаmaх = 5,06 |
|
6 |
– |
0,32 |
– |
|
Общий |
с – 520…200; к – 340…170 |
|
|
2 |
1 |
с – 130…20; к – 110…10 |
Rz = 20; Rа = 2,5 |
1,32…1,79; |
|
|
|
|
Rаmaх = 14,6 |
|
2 |
с – 50...260; к – 60…280 |
– |
– |
|
3 |
с – 10…110; к – 10…80 |
1,25…0,63 |
– |
|
4 |
с – 30…50; к – 50…40 |
0,63 |
0,42…0,6; |
|
|
|
|
Rаmaх = 3,59 |
|
5 |
– |
0,32 |
– |
|
Общий |
с – 200…440; к – 190…310 |
|
|
|
|
163 |
|
|
Окончание табл. 26
Но- |
Номер |
Снимаемые припуски |
Шероховатость, |
Шерохова- |
мер |
перехо- |
(с – спинка, к – корыто), |
Rа, Rz, мкм, |
тость Rа, Rz, |
вари- |
да |
мкм |
по эталону |
Rаmaх, мкм, |
анта |
|
|
|
по оттиску |
3 |
1 |
с –70…30; к – 90…0 |
2,5 |
– |
|
2 |
с – 50…160; к – 60…190 |
1,25 |
0,61; |
|
|
|
|
Rаmaх = 6,2 |
|
3 |
с – 10…220; к – 20…150 |
1,25…0,63 |
– |
|
4 |
с – 10…10; к – 60…20 |
0,63 |
0,2…0,41; |
|
|
|
|
Rаmaх = 1,96 |
|
5 |
– |
0,32 |
– |
|
Общий |
с – 180…460; к – 200…340 |
|
|
4 |
1 |
с – 30…220; к – 20…230 |
2,5…1,25 |
1,24…1,78; |
|
|
|
|
Rаmaх = 17,3 |
|
2 |
с – 30…200; к – 40…190 |
1,25 |
0,78…0,86 |
|
3 |
с – 90…20; к – 60…0 |
0,63…0,32 |
0,2…0.32; |
|
|
|
|
Rаmaх = 2,58 |
|
4 |
с – 60…110; к – 30…30 |
0,32 |
0,11…0,15 |
|
Общий |
с – 200…470; к – 200…310 |
|
|
На основании сравнительного анализа табл. 26 и рис. 76, 77 установлено:
1.После фрезерования на пере лопаток остается значительный
инеравномерный припуск под операцию полирования: со стороны спинки – 0,5–0,18 мм, со стороны корыта – 0,34–0,16 мм. В результате полировщику необходимо применять крупнозернистые круги на первых переходах, что наводит крупные риски на пере.
2.Большая неравномерность припуска в пределах одного сечения по трем точкам (со стороны спинки до 0,26 мм, со стороны корыта до 0,2 мм) усложняет получение точного профиля без рисок.
3.Наибольший съем припуска по переходам при полировании радиуса сопряжения у лопаток составляет:
1-й вариант – при подгонке абразивными кругами 25А40 и 25А25 (спинка до 0,47 мм, корыто до 0,39 мм) на полировку и удаление рисок припуска не осталось;
164

Припуск, мкм
700
600
500
400
300
200
100
0
0 |
2 |
4 |
6 |
Номер перехода
Припуск, мкм
180
160
140
120
100
80
60
40
20
0
0 |
2 |
4 |
6 |
Номер перехода
1-й вариант |
2-й вариант |
|
140 |
|
|
|
|
140 |
мкм |
120 |
|
|
|
мкм |
120 |
100 |
|
|
|
100 |
||
Припуск, |
80 |
|
|
|
Припуск, |
80 |
20 |
|
|
|
20 |
||
|
60 |
|
|
|
|
60 |
|
40 |
|
|
|
|
40 |
|
0 |
|
|
|
|
0 |
|
0 |
2 |
4 |
6 |
|
0 |
|
|
Номер перехода |
|
|
|
2 |
4 |
6 |
Номер перехода
3-й вариант |
4-й вариант |
Припуск на спинке, мкм |
Припуск на корыте |
Рис. 76. Изменение съема припусков по переходам на пере лопаток при полировке спинки и корыта по 1, 2, 3, 4-му варианту соответственно
2-й вариант – при подгонке абразивным кругом 25А25 (спинка до 0,26 мм, корыто до 0,28 мм) и полировании войлочным кругом, накатанным 25А6 (спинка до 0,11 мм, корыто до 0,08 мм) полировка не обеспечивает удаление рисок, однако остается припуск 0,1 мм для дополнительной полировки;
3-й вариант – при полировании войлочными кругами, накатанными 14А12Т и 25А6Т (спинка до 0,38 мм, корыто до 0,34 мм) остаются неглубокие риски, которые удаляются последующей глянцовкой;
165
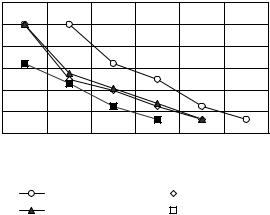
Ra, мкм |
|
|
|
|
|
3 |
|
|
|
|
|
2,5 |
|
|
|
|
|
2 |
|
|
|
|
|
1,5 |
|
|
|
|
|
1 |
|
|
|
|
|
0,5 |
|
|
|
|
|
0 |
|
|
|
|
|
1 |
2 |
3 |
4 |
5 |
6 |
|
|
|
|
Номер перехода |
1-й вариант |
|
|
|
2-й вариант |
|
|
|
||
3-й вариант |
|
|
|
4-й вариант |
|
|
|
Рис. 77. Изменение шероховатости поверхности Ra в зависимости от варианта полирования и абразивного инструмента на различных переходах
4-й вариант – при подгонке абразивным кругом 25А25 (спинка до 0,22 мм, корыто до 0,23 мм) и полировании войлочным кругом, накатанным 25А6 (спинка до 0,2 мм, корыто до 0,19 мм), остаются неглубокие риски, которые удаляются последующей глянцовкой.
4.Шероховатость при подгонке кругом 25А40 Rа = 2,8…1,7 мкм, на класс ниже, чем кругами 25А25 – Rа = 1,78…1,2 мкм; при полировании войлочными кругами, накатанными 14А12, Rа = 1,0…0,63 мкм, 25А6 – Rа = 0,42…0,2 мкм.
5.При обработке по 3-му и 4-му вариантам полирования шероховатость лучше, чем по 1-му и 2-му вариантам: 1-й – 0,4…0,67 мкм; 2-й – 0,42…0,6 мкм; 3-й – 0,2…0,41 мкм; 4-й – 0,2…0,32 мкм.
6.Для обеспечения требуемой шероховатости Rа ≤ 0,32 мкм
ивысокой стойкости войлочных кругов, накатанных шлифпорошком 25А6, необходимо предварительно обработать поверхность с шеро-
ховатостью Rа ≤ 1,7 мкм.
166
7.При анализе глубины единичных рисок необходимо учитывать величину параметра шероховатости Rаmax.
8.При полировании по 1-му варианту наблюдается наибольшая
высота микронеровностей от Rаmах = 24,6 мкм на 1-м переходе, которая снижается до Rаmах = 5,06 мкм перед глянцовкой. При обработке по 2-му варианту шероховатость Rаmах снижается от 14,6 до 3,59 мкм. При обработке по 3-му варианту перед глянцовкой обеспечивается
шероховатость Rаmах = 1,96 мкм. По 4-му варианту шероховатость Rаmах снижаетсяот 17,3 до 2,58 мкм.
9.Наиболее благоприятными схемами полирования радиуса сопряжения с позиции обеспечения наименьшей рисочности являются варианты № 3 и 4. После окончательной обработки (глянцовки) 16 лопаток были дообработаны по техпроцессу. При визуальном контроле на 3 лопатках замечаний по рисочности не было. На остальных лопатках обнаружены риски в основном на кромках пера со стороны корыта и спинки. При ЛЮМ1-ОВ контроле данных лопаток в радиусе сопряжения пера рисок не обнаружено.
После виброгалтовки этих лопаток при визуальном контроле на 3 лопатках обнаружены риски в радиусе сопряжения. Все эти лопатки были обработаны по 4-му варианту. Таким образом, виброгалтовка может вскрывать глубокие риски, которые были «замазаны» при полировке войлочным кругом 25А6Т после подгонки абразивным кругом 25А25СМ1К.
В результате проведенных исследований установлено, что к числу причин, косвенно влияющих на образование рисок в радиусе сопряжения, относятся большая величина и нестабильность припуска (0,5 мм вместо 0,3 мм) и его неравномерность в пределах одного сечения (до 0,26 мм) из-за некачественного фрезерования радиуса сопряжения.
К числу причин появления рисочности в радиусе сопряжения лопаток относится низкое качество абразивных полировальных кругов и других материалов, применяемых при полировании профиля пера лопаток (абразивные круги низкого класса Б, нет входного контроля кругов; применение мездрового клея низкого качества марок
167
КМ2, несоблюдение технологии приготовления клея и накатки кругов, низкое качество полировальных паст).
Наименьшая шероховатость и рисочность в радиусе сопряжения лопаток обеспечивается при использовании 3-го варианта полирования.
Для исключения рисочности при полировании радиуса сопряжения лопаток необходимо:
1)на операции фрезерования радиуса сопряжения обеспечить стабильность припуска (не более 0,3 мм) и неравномерность его не более 0,1 мм под операцию полирования;
2)припуск под обработку полировальными войлочными кругами принимать не менее 0,2 мм;
3)операцию полирования сопряжений проводить по следующим переходам:
1 – подгонка абразивным кругом 25А 25Н СМ1 К; 2 – полирование войлочными кругами, накатанными зерном
14А(25А)12Т;
3 – полирование войлочными кругами, накатанными зерном
25А6Т;
4 – полирование войлочными кругами, накатанными зерном 25А, 25А6Т с пастой № 18;
5 – полирование отработанным войлочными кругами, накатанными зерном 25А6Т с пастой № 24.
Указанные рекомендации приняты к внедрению и вписаны в технологию полирования лопаток. Случаи появления недопустимых рисок в сопряжении лопаток на предприятии практически прекратились.
1.15. Исследование появления дефектов в виде «белых пятен» при полировании лопаток
Периодически после полировки титановых штампованных лопаток абразивными кругами обнаруживаются дефекты на пере в виде «белых пятен».
168
Технологический процесс изготовления компрессорных лопаток из титановых сплавов построен таким образом, что после операции ручного полирования лопатки проходят операцию травления на макроструктуру и прижоги. В результате травления на пере лопаток иногда появляются «белые пятна» различной интенсивности, которые контролеры БТК считают прижогами, и лопатки бракуются. По этому дефекту ежегодно выбраковывается от 0,2 до 14 % лопаток из сплава BT3-1. После замены на изделии ПС-90А титанового сплава BT3-1 сплавом ВТ8-М данный брак резко увеличился.
Травление лопаток из сплава BT3-1 производится в следующем растворе: серная кислота (плотность 1,19 г/см3) – 175 см3; фтористый натрий – 25 г; вода – 330 см3.
Все виды разнотравимости (появление «белых пятен» на лопатках) можно поделить на две группы:
1)пятна на кромках пера;
2)пятна в средней части профиля пера: продольные полосы; пятна округлой формы; штриховые пятна, расположенные группами
(«рябь»).
Известно, что продольные светлые полосы на профиле пера – это следы пластической деформации лопаток в процессе штамповки, металл в зоне полосы отличается от основного металла более мелкозернистой структурой. Такие полосы, по мнению металлургов, не являются браковочным признаком.
Природа же «белых пятен» другой формы требует более глубокого изучения. Были проанализированы литературные источники по шлифованию титановых сплавов и исследованию поверхностных слоев. Единого мнения о природе выявляемых при травлении «белых пятен» у исследователей нет.
Так, в монографии А.В. Якимова [58] указывается, что в зоне «белых пятен» при рентгеноструктурном анализе отмечено повы-
шенное содержание α-фазы (от 5 до 30 %), а исследования микротвердости показали ее снижения 3800–3850 МПа в сердцевине до 3300–3500 МПа в зоне прижога. Вместе с тем отмечается наличие «белых пятен» с повышенной твердостью Н100 = 4400…4550 МПа,
169
что объясняется насыщением поверхностного слоя водородом, кислородом и азотом.
Исследования поверхностных слоев титановых сплавов после шлифования, выполненные в Волжском филиале ВНИИАШ под руководством Г.И. Саютина [34], показали следующее. После шлифования кругами из карбида кремния на обработанной поверхности имеются участки размерами до 5×10 мкм, насыщенные кремнием (содержание кремния увеличено в 4–5 раз).
Путем электронно-графических исследований обнаружена новая фаза – оксикарбиды и оксикарбонитриды титана. Рентгеноструктурный анализ показал увеличение в прошлифованной поверхности содержания β-фазы с 14 до 34 %, при обработке же на жестких режимах увеличивается содержание α-фазы. Металлографическими исследованиями также подтверждено исчезновение в тонком поверхностном слое β-фазы при шлифовании на жестких режимах, при этом вместо структуры корзиночного строения фиксируется белый слой «аморфного» характера – структуры, имеющей в 2 раза большую твердость, чем исходная структура.
Таким образом, образование «белых пятен» в процессе механической обработки сплавов может быть объяснено рядом причин: под воздействием термопластических деформаций увеличивается содержание β-фазы и одновременно снижается микротвердость; исчезает β-фаза и повышается микротвердость; образуется новая фаза – оксикарбиды и оксикарбонитриды титана; поверхностный слой насыщается кремнием и газами.
Для определения природы «белых пятен», которые проявляются на пере лопаток после травления, проводились сравнительные металлографические исследования металла в зоне пятна и вне его, рентгеноспектральный анализ на микроанализаторе MAP-2 (на образцах размером 9×15, вырезанных из пера лопаток), определение фазового состава металла на дифрактометрах «ДРОН-2».
Металлографические исследования «белых пятен» в средней части пера лопаток, проведенные на микрошлифах, приготовленных
170