
1496
.pdf2.Минимально достижимый радиус 0,05–0,08 мм (острая кромка) можно получить при формировании радиусов, образованных шлифованием пересекающихся плоскостей, независимо от вида шлифования и марки материала.
3.Минимальные радиусы 0,15−0,25 мм можно получить при формировании внутреннего радиуса в скруглениях и галтелях при достаточной частоте правок и использовании оптимальной характеристики абразивного инструмента определенным методом шлифования.
4.Величина минимального радиуса зависит от метода шлифования. При шлифовании материалов торцом круга величина радиуса значительно ниже, чем при шлифовании на врезание периферией круга, однако радиусы менее 0,15 мм конструкторам не следует назначать.
5.Методом врезания периферией круга можно стабильно обеспечить радиусы в пределах 0,4 мм и более. Оформление радиусов менее 0,4 мм таким методом затруднительно.
6.По мере износа круга, например, при последовательном съеме
припуска до 2 мм с подачей на глубину резания 0,01−0,02 мм/дв.ход, происходит увеличение этого радиуса в 1,5−2 раза независимо от метода шлифования и применяемых материалов заготовки и круга.
7. Используемый метод правки абразивных кругов позволяет обеспечить первоначальный минимальный радиус на инструменте
0,1−0,2 мм.
Таким образом, результаты работы позволяют конструкторам изделий научно обоснованно назначать при проектировании деталей машин минимальные значения радиусов сопрягаемых элементов, которые заведомо могут быть обеспечены технологически при шлифовании различными методами.
1.5. Турбоабразивная обработка деталей газотурбинных двигателей
Многие детали газотурбинных двигателей (ГТД) – диски турбины и компрессора, промежуточные кольца, дефлекторы и др. – имеют сложную конфигурацию, большое количество отверстий, пазов,
81

канавок и выемок (рис. 46). Слесарная обработка заусенцев, острых кромок, полировка поверхностей этих деталей представляет значительные трудности, так как требуется различный слесарный и вспомогательный инструмент и оборудование. Слесарная обработка таких деталей имеет большую долю ручного труда, низкую производительность, не обеспечивает стабильное качество поверхностного слоя.
Рис. 46. Общий вид различных поверхностей диска турбины (профильные пазы, отверстия, полотно, радиусы сопряжений), требующих слесарной обработки
Кроме того, детали ГТД работают при высоких температурах и значительных динамических нагрузках, поэтому физико-механи- ческое состояние поверхностного слоя (характер остаточных напряжений, усталостная прочность материала и шероховатость обработанной поверхности) в значительной степени определяет надежность работы и ресурс выпускаемых авиадвигателей. Улучшение качества поверхностного слоя за счет внедрения более совершенных методов финишной обработки имеет большое значение.
Одним из таких методов является турбоабразивная обработка (ТАО), позволяющая механизировать непроизводительный ручной труд, уменьшить шероховатость обработанной поверхности и каче-
82
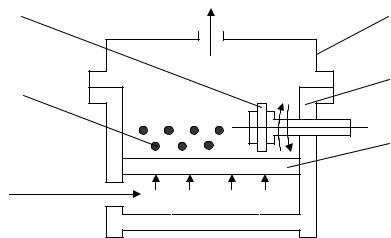
ство поверхностного слоя, увеличить усталостную прочность материала и производительность, повысить культуру производства.
Метод ТАО деталей ГТД разработан совместно со специалистами ВНИИАШ (г. Санкт-Петербург) и впервые в отрасли внедрен в ОАО «Пермский моторный завод».
Принципиальная схема турбоабразивной установки показана на рис. 47.
2 |
К фильтру |
3 |
|
||
|
|
4 |
1 |
|
|
|
|
5 |
Сжатый воздух |
|
|
|
К А М Е Р А |
|
Рис. 47. Принципиальная схема турбоабразивной установки:
1 – «кипящий» слой абразивных зерен; 2 – обрабатываемая деталь; 3 – крышка; 4 – корпус установки; 5 – распределительная решетка
В установку через специальную воздухопроницаемую керамическую или порометаллическую распределительную решетку 5, на которую насыпан определенный слой абразивного зерна 1, подается сжатый воздух от напорного вентилятора ВВД-5 производительностью 2000 м3/ч. В результате этого абразивные частицы поднимаются и совершают интенсивное хаотическое движение. Создается так называемый «кипящий» слой абразивного зерна. Обрабатываемой детали 2 придается вращение со скоростью до 30 м/с в одну и другую сторону. При этом происходит микрорезание выступающих острых
83
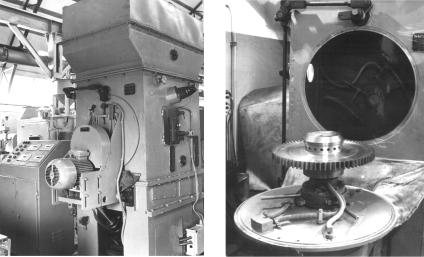
кромок путем соударения абразивных зерен с ними. На рис. 48 показаны общий вид и рабочая зона загрузки полуавтоматической установки Г816-5177, разработанной конструкторами отдела механизации и автоматизации ОАО «ПМЗ», предназначенной для обработки острых кромок и полировки полотна дисков турбин.
а |
б |
Рис. 48. Общий вид турбоабразивной установки Г816-5177 (а) для обработки дисков турбины и рабочей зоны установки деталей (б)
Турбоабразивная обработка за один рабочий цикл позволяет выполнять одновременно несколько технологических операций: снижать шероховатость поверхности до Ra = 0,2...0,4 мкм при исходной шероховатости Ra = 2...5 мкм, снимать заусенцы с исходной высотой до 1,5 мм, округлять острые кромки и регулировать радиус округления, создавать микрорельеф с высокими адгезионными свойствами, что повышает прочность сцепления при нанесении различных видов покрытий (гальванических, плазменных, лакокрасочных, резиновых).
84
При ТАО микрорельеф обработанной поверхности хорошо удерживает смазку в парах трения (например, гильза – поршневое кольцо). Данный процесс удаляет окалину, нагар, коррозию, различные виды загрязнений поверхности. ТАО улучшает качество поверхности: усталостная прочность повышается до 45 % и более, а контактная жесткость до 60 %, в поверхностном слое создаются остаточные напряжения сжатия.
Одна турбоабразивная установка повышает производительность труда в 5–10 раз и освобождает 3–5 квалифицированных рабочих от ручного труда. Установка работает в полуавтоматическом режиме. Возможна одновременная обработка группы деталей, машинное время обработки в зависимости от состояния заготовки составляет
2–10 мин.
Для обработки невыступающих частей деталей (канавки, выточки, карманы) применяются специальные эжекторные гибкие сопла с подачей абразивного зерна из рабочей камеры от сети сжатого воздуха давлением 4–6 кгс/см2.
Таким образом, вращающаяся с большой скоростью деталь в среде низкоскоростного воздушно-абразивного потока обрабатывается одновременно по всем наружным поверхностям, имеющим различные сложные профили. Например, хорошо полируются радиусы на торцах пазов в дисках турбин и компрессоров, имеющих профили типа «елка» или «ласточкин хвост». Интенсивность съема металла при скорости вращения диска турбины 25 м/с составляет 2–5 мкм/мин. Расчеты показали, что число соударений абразивных зерен с обрабатываемой поверхностью достигает 200–500 в секунду на 1 мм2. Процесс является низкотемпературным, фазово-структур- ные изменения в поверхностном слое не происходят, поверхностный слой упрочняется на 15–20 %. На предприятии изготовлено несколько установок для обработки различных деталей ГТД (табл. 14). В настоящее время в ОАО «Пермский моторный завод» работает 6 таких установок, обрабатывающих более 100 наименований деталей.
Сравнительный анализ методов обработки деталей свободным абразивом показал существенное преимущество турбоабразивного
85
метода. По сравнению с магнитоабразивной обработкой ТАО имеет меньшую текучесть абразивного потока, меньшие энергетические затраты, более простое оборудование, обеспечивает более высокий съем металла, лучшее качество обработки.
|
|
|
Таблица 14 |
|
Технические данные разработанных установок |
||||
|
|
|
|
|
Параметр |
Г816-5177 |
Г816-5201 |
0065-2620 |
|
|
|
|
|
|
Диаметр обрабаты- |
250–600 |
900 |
15–400 |
|
ваемых деталей, мм |
75–150 |
|||
|
|
|||
Высота, мм |
До 250 |
До 250 |
До 150 |
|
Скорость обработки, |
25–30 |
25–30 |
25–30 |
|
м/с |
||||
|
|
|
||
Абразивный мате- |
14А63...80 |
14А63..80 |
14А63...80 |
|
риал |
||||
|
|
|
||
Масса обрабатывае- |
До 50 |
До 50 |
6–10 |
|
мых деталей, кг |
||||
|
|
|
||
Габаритные размеры |
3600×3300×2660 |
3600×3300×2660 |
3600×3300×2660 |
|
установки, мм |
|
|
|
|
Размеры электро- |
500×350×1500 |
500×350×1500 |
500×350×1500 |
|
шкафа, мм |
||||
|
|
|
На предприятии были проведены исследования с целью выбора абразивного материала, зернистости и режимов обработки, а также определения шероховатости обработанной поверхности, съема металла, наличия остаточных напряжений, микротвердости, наклепа, усталостной прочности.
Для исследования остаточных напряжений, микротвердости и усталостной прочности изготовили образцы из сплавов ЭИ698ВД и ВТ3-1.
При испытаниях использовали абразивы из электрокорунда белого (24А) зернистостью 25 и 40 мкм, карбида кремния зеленого (63С) зернистостью 40 и 63 мкм и электрокорунда нормального (14А) зернистостью 63 и 80 мкм.
86
Установлено следующее:
а) при обработке абразивом 24А зернистостью 25 и 40 мкм съем металла снижается, улучшается шероховатость поверхности;
б) абразив из карбида кремния зеленого 63С быстро дробится на более мелкие фракции и требует частой замены;
в) обработка абразивом из электрокорунда нормального 14А обеспечивает удовлетворительный съем металла и требуемую шероховатость.
Абразивы заменяют 2 раза в месяц.
По сравнению с ручной обработкой ТАО улучшается шероховатость поверхности на 1–2 класса (до Ra = 0,32...0,63 мкм зерном 14А80). Зарезы, уступы и риски необходимо предварительно зачищать. Съем металла с торцов полотна и обода дисков составляет 0,01–0,02 мм на сторону при скорости резания до 30 м/с, а с возрастанием скорости (и плотности зерна в рабочей камере) он увеличивается. При снятии заусенцев и округлении острых кромок съем металла достигает 0,3–0,6 мм в зависимости от времени обработки и величины абразивного зерна. По контуру отверстий, пазов, выемок и выкружек металл снимается неравномерно, съем его минимален со стороны, касательной к окружности вращения.
В поверхностном слое ТАО, как правило, создает сжимающие напряжения σо = 19...27 кгс/мм2 на глубину 5–10 мкм (для сплава ЭИ698ВД) или практически не изменяет их (для сплава ВТ3-1). На степень и глубину наклепа ТАО не влияет.
При ТАО предел усталостной прочности выше, чем при ручной полировке. Так, для образцов из сплава ЭИ698ВД он составляет 28 кгс/мм2 вместо 24 кгс/мм2, для образцов из сплава ВТ3-1 35 кгс/мм2 вместо 26 кгс/мм2.
На турбоабразивный метод обработки переведены диски турбины и компрессора, промежуточные кольца, дефлекторы и другие детали, имеющие большой объем слесарных ручных операций. Машинное время обработки диска турбины составляет 6–10 мин, диска компрессора – 3–4 мин. Метод опробован на ремонтных лопатках
87
турбины для снятия нагара с поверхности пера длиной до 80 мм, на торцах замков лопаток турбин.
Кроме дисков и дефлекторов турбоабразивным методом предлагается обрабатывать обоймы, фланцы, кольца направляющих аппаратов, опоры роликоподшипников (сепараторы) и др.
По мере внедрения ТАО и расширения номенклатуры обрабатываемых деталей возникла необходимость в проектировании и изготовлении малогабаритной установки для обработки деталей небольших габаритов и малой массы (диаметром 75–400 мм, весом до
6–10 кг).
Такая установка была создана в экспериментально-технологиче- ском цехе. Она работает в наладочном и полуавтоматическом циклах от сети сжатого воздуха давлением 4–6 кг/см2, может быть установлена на участках механических цехов, непосредственно в местах работы слесарей.
За время испытания экспериментальной установки проведены следующие работы:
1.ТАО образцов из шлицевых и гладких валов. Доказана принципиальная возможность выполнения операций по скруглению острых кромок, снятию мелких заусенцев по контуру шлиц и полированию гладких поверхностей валов при оптимальных режимах обработки.
2.Опытная обработка серийных деталей ГТД – фланцев, крышек, колен, обойм и др. – с целью определения возможности их ТАО, выбора режимов обработки, подбора характеристики абразивного зерна
ипроверки конструкции экспериментальной оснастки – приспособлений, переходников и др. Все эти детали имеют на торцах, наружных
ивнутренних поверхностях отверстия и фаски, выемки, карманы, канавки и фигурный контур фланцев, что усложняет ТАО, так как наличие карманов и выемок приводит к экранированию отдельных мест обработки и уменьшению съема металла. Кроме того, съем металла в направлении вектора скорости меньше, чем в перпендикулярном к нему направлении. Для устранения вышеназванных недостатков применены специальные эжекторные сопла, подающие абразивное зерно в неудобные для обработки места и медные трубки с внутрен-
88
ним диаметром 4 мм, обеспечивающие подвод сжатого воздуха для выдувания зерна из этих мест.
Для улучшения обработки торцовых поверхностей деталей спроектирован и изготовлен механизм осцилляции шпинделя с закрепленной деталью при ее вращении.
Для создания удобства при установке и снятии деталей после ТАО установлен механизм подъема и опускания воздухораспределительной камеры вместе со слоем абразивного зерна. В конструкции установки внесены и другие изменения, облегчающие ее наладку, обслуживание и эксплуатацию. Все изменения указаны в постоянных чертежах полупромышленной установки 0065–2620.
Экспериментальные и производственные испытания малогабаритной (1100×1000×2100 мм) установки после ее модернизации показали, что на ней можно проводить ТАО большой номенклатуры деталей (тел вращения) сложной конфигурации, диаметром от 150 до 350 (400) мм и весом до 6 кг на оптимальных режимах.
Для ТАО деталей диаметром от 75 до 150 мм, с целью расширения технологических возможностей установки и обеспечения более оптимальных режимов обработки, спроектирована и изготовлена насадная угловая головка с вертикальной осью вращения шпинделя детали, которая устанавливается на основном (горизонтальном) шпинделе установки и от него получает вращение в одну и другую сторону.
В результате внедрения нового метода турбоабразивной обработки механизирован тяжелый ручной труд полировщиков, повысилась производительность отделочной обработки в 4–5 раз, улучшилось качество поверхностного слоя и повысилась усталостная прочность обработанных деталей. После турбоабразивной обработки улучшился внешний товарный вид изделий.
1.6. Выбор и эффективное применение современных СОТС при различных процессах шлифования
Одним из наиболее простых и доступных путей интенсификации процесса шлифования является увеличение режимов обработки. Наибольший эффект в этом случае дает увеличение толщины срезае-
89
мого слоя. Но при этом приходится существенно снижать скорость резания для сохранения заданного периода стойкости кругов. Исключить эти ограничения возможно, если при шлифовании использовать смазочно-охлаждающие технологические средства (СОТС).
На ОАО «Пермский моторный завод» совместно с кафедрой «Технология машиностроения» и Пермским заводом смазки и СОЖ проведена работа по исследованию эффективности различных видов современных отечественных смазочно-охлаждающих жидкостей (СОЖ) при шлифовании образцов и деталей газотурбинных двигателей из различных жаропрочных сталей и сплавов. При выборе типов СОЖ для этих материалов использовались известные рекомендации, по которым наиболее интенсивное охлаждение происходит при использовании СОЖ с наиболее высокой теплопроводностью, теплоемкостью и плотностью, наименьшей кинематической вязкостью, с наибольшей скоростью подачи потока и лучшей смачиваемостью. Проведен анализ физико-химических свойств СОТС и методов их контроля при их производстве и эксплуатации.
СОТС является одним из наиболее важных переменных факторов состояния системы резания. За счет изменения состава и состояния СОТС можно эффективно осуществлять глубокие и многосторонние изменения параметров функционирования системы резания. Поэтому при выборе наиболее рациональной СОТС очень важно знать и учитывать основные свойства, особенности производства и применения современных СОТС. В связи с этим проведен предварительный подробный анализ различных свойств, особенностей изготовления и применения современных СОТС.
Применение эффективных СОТС выдвигают на первый план всякий раз, когда создают вновь или совершенствуют существующие методы обработки резанием в целях обеспечения резкого повышения режима резания, что сопровождается соответствующим увеличением объема снимаемой стружки в единицу времени. В этих случаях СОТС играет роль, с одной стороны, фактора, снижающего интенсивность силовых и тепловых нагрузок на режущий инструмент и обрабатываемую деталь, а с другой стороны, средства, позволяющего
90