
1496
.pdf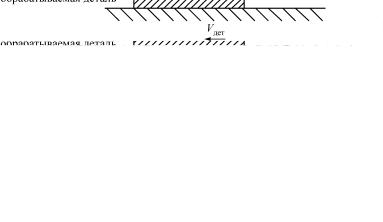
Рис. 41. Схема шлифования с непрерывной правкой алмазным роликом с учетом износа шлифовального круга
Станки также могут быть укомплектованы двухосными CNC индексирующими столами, предоставляющими возможность использования 5 осей для комплексного применения, например, для обработки лопастей турбины, соплового направляющего аппарата и герметизирующих сегментов. Дополнительные преимущества этой современной машины – высокая скорость, возможная благодаря быстрому движению оси, непревзойденная гибкость и производительность. Радиусная поверхность полок формируется путем интерполирования перемещения шлифовального круга системой ЧПУ при неподвижном столе с деталью и продольном перемещении стойки станка (рис. 42). Точность профиля бандажной полки обеспечивается точностью профиля алмазного правящего ролика. Для эффективного охлаждения зоны шлифования предусмотрена подача СОЖ по профильным направляющим под давлением 12 атм. Очистка круга с помощью СОЖ производится с периферии и торца через три сопла под давлением 14 атм. Тонкая очистка СОЖ осуществляется с помощью ленточного бумажного фильтра. Система ЧПУ станка осуществляет непрерывную правку круга с контролем его диаметра и обеспечением постоянной скорости шлифования. По мнению специалистов, та-
71
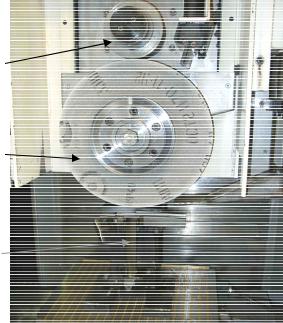
кая схема обработки позволяет обеспечить более качественную обработку, с точки зрения формирования качественного поверхностного слоя и обеспечения максимального ресурса эксплуатации.
Алмазный правящий ролик
Шлифовальный круг
Обрабатываемая
деталь
Рис. 42. Общий вид зоны шлифования и правки круга на плоскошлифовальном станке Micro Cut 4
Практика применения глубинного шлифования (ГШ) показала, что профильную обработку поверхностей полок лопаток турбин наиболее рационально проводить за три прохода. При этом величина общего припуска на обработку, зависящая от способа получения заготовки, разбивается на три части. На долю первого прохода приходится в среднем 90–95 % от общей величины удаляемого припуска, на второй проход – порядка 3–7 % и на окончательный проход – около 1–3 %. Такая обработка является оптимальной как с точки зрения производительности, так и с точки зрения формиро-
72
вания поверхностного слоя требуемого качества. Оптимальные режимы глубинного шлифования полок лопаток турбин, приведены в табл. 10.
Таблица 10
Оптимальные режимы глубинного шлифования полок турбинных лопаток
Номер |
Глубина |
Установка |
Скорость |
Скорость |
Подача |
Фактор, |
про- |
резания, |
круга, мм |
круга Vк, |
детали Vдет, |
ролика, Sр, |
К* |
хода |
мм |
|
м/с |
мм/мин |
мкм/об. круга, |
|
1 |
~7 |
2,55 |
20 |
100 |
0,2 |
–0,8 |
|
|
|
|
|
|
|
2 |
1 |
1,55 |
20 |
150 |
0,2 |
–0,8 |
|
|
|
|
|
|
|
3 |
1 |
0,55 |
20 |
150 |
0,2 |
–0,8 |
|
|
|
|
|
|
|
4 |
0,5 |
0,05 |
20 |
200 |
0,2 |
–0,8 |
|
|
|
|
|
|
|
5 |
0,05 |
0 |
20 |
300 |
– |
– |
|
|
|
|
|
|
|
* К = Vр/Vк.
Шлифовальный круг 1. 400×37×127 F13A 70 FF21 V (STRATO) фир-
мы «Тиролит» (Австрия). Бумага фильтровальная МО22055. 1,4 % эмульсия ELB-ISOGRIND 130EP. Автоматическая балансировка и попутная правка круга.
Исследования качества поверхностного слоя проводились путем сравнения шероховатости, остаточных напряжений, наклепа и микроструктуры, полученных при старой и новой технологии. В результате установлено, что шероховатость поверхности Ra при глубинном шлифовании уменьшается с 0,85–1,2 до 0,64–0,81 мкм; распределение остаточных напряжений носит более благоприятный характер; глубина и степень наклепа снизились на 30–40 %; улучшилось струк- турно-фазовое состояние поверхностного слоя; трещины в поверхностном слое не обнаружены. В результате проведенных исследований внедрена обработка 11 наименований лопаток турбины. Таким образом, внедрение новой технологии шлифования бандажных полок турбинных лопаток позволило значительно сократить время обра-
73
ботки, улучшить качество и стабильность точностных параметров, облегчить и значительно повысить культуру и интеллектуальность труда рабочих.
1.4. Технологическое обеспечение минимально возможных радиусов сопряжений поверхностей деталей машин методом шлифования
В процессе технологической подготовки производства и проработки на технологичность новых высокотехнологичных конструкций машин, таких как, например, газотурбинные двигатели для авиации и наземных установок, часто возникают конфликты между конструкторами и технологами из-за споров по возможности технологического обеспечения минимальных радиусов сопряжений поверхностей деталей 0,05−0,5 мм методом шлифования. На чертежах ответственных деталей машин конструкторы пытаются устанавливать такие размеры радиусов сопряжений, которые обычными методами шлифования трудно выполнить. В связи с этим на ОАО «ПМЗ» возникла необходимость в проведении объективной опытной работы по определению реально достижимых минимальных радиусов галтелей и скруглений на обычно применяемых операциях шлифования деталей ГТД.
Известно, что сопряжения двух поверхностей можно выполнить различными методами шлифования. На рис. 43 представлены схемы различных видов круглого шлифования. В предварительных опытах установлено, что при маятниковом шлифовании (рис. 43, а) образуется острая кромка на торце детали с незначительным радиусом округления. При глубинном круглом шлифовании (рис. 43, б) радиус округления острой кромки больше, чем при маятниковом шлифовании. При врезном круглом шлифовании канавок или ступенчатых валов (рис. 43, в, г) радиусы сопряжений на дне канавки или ступеньки зависят от величины радиуса кромки шлифовального круга и способности круга противостоять разрушению этой кромки.
74
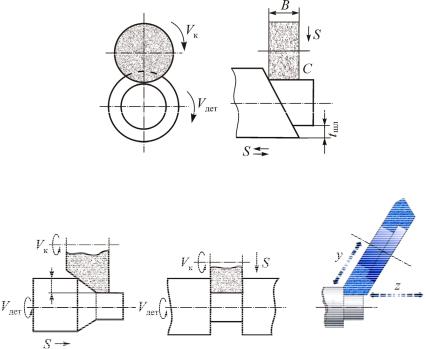
а
б |
в |
г |
Рис. 43. Возможные методы формирования радиусов сопряжений при круглом наружном шлифовании: а – маятниковое с продольной подачей; б – глубинное круглое; в – канавочное методом врезания; г – врезное ступенчатое шлифование с наклоном круга
При шлифовании плоских сопряженных ступенчатых поверхностей на различных плоскошлифовальных станках радиус сопряжения можно получить также различной величины в зависимости от метода шлифования и применяемых шлифовальных кругов. На рис. 44 представлены различные схемы шлифования ступенчатых плоских поверхностей, наиболее часто встречающиеся на производстве: периферией, торцом круга и методом врезания.
В результате анализа этих методов предложено все многообразие шлифовальных операций, обеспечивающих образование радиу-
75

сов сопряжений плоских и круглых ступенчатых поверхностей деталей свести к двум типам: шлифование периферией круга на врезание и шлифование торцом круга.
а б в
Рис. 44. Схемы формирования радиусов сопряжений при плоском шлифовании: а – периферией круга; б – торцом круга; в – врезанием
В связи с этим экспериментальные исследования по определению минимально возможных радиусов сопряжений при шлифовании различных поверхностей проведены периферией и торцом круга с использованием как плоскошлифовального станка 3Е721ВФ1, так и круглошлифовального станка РУ-100.
Для исследований выбраны материалы пяти различных групп обрабатываемости (табл. 11), наиболее часто встречающиеся в авиационной промышленности, термообработанные по серийной технологии.
Из выбранных материалов изготовлены специальные плоские и круглые образцы, имеющие сопряженные ступенчатые поверхности для формирования различных радиусов сопряжений. Форма и размеры образцов приведены в табл. 12. Часть плоских образцов обрабатывалась периферией круга, а часть – торцом круга. Круглые образцы обрабатывались периферией и врезанием круга.
76
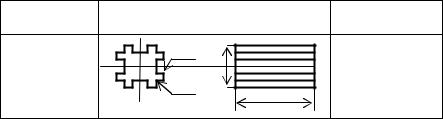
|
|
Таблица 11 |
|
Характеристика исследуемых обрабатываемых материалов |
|||
|
|
|
|
Группа материалов |
Марка |
Твердость |
|
материалов |
материалов |
||
|
|||
Конструкционные |
Ст.45, закалка |
HRC 54–58 |
|
углеродистые стали |
|
|
|
Конструкционные |
|
|
|
легированные стали: |
|
|
|
азотируемые |
38Х2МЮАШ |
HRC 58–60, |
|
цементируемые |
ЭИ415, 12Х2Н4А |
HRC > 60 |
|
Жаропрочные стали |
ЭП609, ЭИ961Ш |
НВ 255–285, |
|
мартенситного класса |
|
НВ 310–380 |
|
Титановые сплавы |
ВТ3-1 |
НВ 310–350 |
|
Жаропрочные сплавы на |
ЭИ437Б, |
НВ 240–255, |
|
никелевой основе – де- |
ЖС6К, ВЖЛ 14 |
НВ 340–360, |
|
формируемые и литейные |
|
НВ 240–290 |
Для шлифования материалов каждой группы подобраны исходя из рекомендаций справочников, технической литературы и производственного опыта соответствующие шлифовальные круги одного типоразмера 1.300×40×127 из различных широко применяемых абразивных материалов следующих семи характеристик: 24А 25П СМ1 7 К5; 64С 25Н СМ2 7 К5; ЛО 125/100 СМ2 К27-100 %; 24А 25П М3 7 К5
с пропиткой дисульфидом молибдена МоS2; 96А 16 СТ3 6 К20ПГ; 91А 25П СМ2 6 К20ПГ; ЛО 50/40 СМ1 К27.
Таблица 12 Виды образцов, используемых для проведения испытаний
Вид
шлифования
Плоское
периферией
Эскизы образцов и места замера R
R
60
R
150
Обрабатываемые
материалы
ЭП609, ЭИ961Ш, ВТ3-1
77
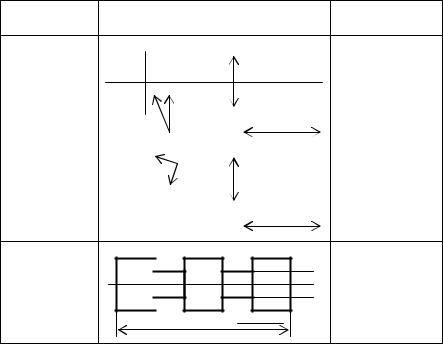
Окончание табл. 12
Вид |
Эскизы образцов и места замера R |
|||||||||
шлифования |
||||||||||
|
|
|
|
|
|
|
|
|
||
Плоское торцом |
|
|
|
|
|
|
|
|
|
|
|
|
|
|
|
|
|
60 |
|
||
|
|
|
|
|
|
|
|
|||
|
|
|
|
|
|
|
|
|
|
|
|
|
|
|
|
|
R |
|
150 |
||
|
|
|
|
|
|
|
|
|
|
|
|
|
|
|
|
|
R |
|
|
|
|
|
|
|
|
|
|
|
|
|
||
|
|
|
|
|
|
|
40 |
|
||
|
|
|
|
|
|
|
|
|
|
|
|
|
|
|
|
|
|
|
100 |
||
|
|
|
|
|
|
|
|
|
|
Обрабатываемые
материалы
ЭИ437Б, 38Х2МЮАШ, Ст.45, ВЖЛ 14ВИ,
ЭИ415
Круглое
8
40
200 R
ЭП609, ЭИ961Ш, ВТ3-1, 12Х2Н4А
Применение пропитанных кругов вызвано тем, что в результате пропитки абразивных кругов разведенным в ацетоне или спирте составом на основе фенолформальдегидного связующего с добавкой дисульфида молибдена МоS2 повышается прочность связки и одновременно уменьшается коэффициент трения и адгезионные явления в зоне шлифования. После пропитки и термообработки круги имеют твердость на 2–5 степеней выше, чем до пропитки. Наиболее эффективны пропитанные круги при шлифовании элементов деталей с малыми радиусами: канавок, резьб, уступов. В свою очередь увеличение твердости кругов после пропитки не приводит к образованию шлифовальных трещин и прижогов.
Правку кругов прямого профиля по торцу проводили с помощью углового приспособления алмазным карандашом типа 3908-
78
0062. Поднутрение торца круга выполняли под углом 2−3°. Режимы шлифования материалов и характеристика абразивных кругов назначались согласно техническим рекомендациям, разработанным для материалов авиационной промышленности. Для контроля радиусов использовали два метода:
1. Метод копирования фактического радиуса кромки абразивного круга. Для этого после шлифования образца проводили шлифование тонкой стальной пластинки (толщина 0, 1 мм) кромкой шлифовального круга, а затем полученный на пластинке радиус измеряли на проекторе типа «Микрофот-3» АЧМ-22 при увеличении ×10. Этим методом можно достаточно точно определить внутренние радиусы сопряжений поверхностей обрабатываемых образцов и деталей при шлифовании.
2. Метод копирования радиуса кромки сопряженных поверхностей образца по оттиску на медной тонкой пластине путем удара или вдавливания. Отпечаток радиуса в данном случае получали вдавливанием тонкой медной пластины. Этим методом можно достаточно точно измерять наружные радиусы сопряжений, образованных шлифованием двух пересекающихся поверхностей. Полученный на медной пластинке радиус измеряли затем на проекторе.
В результате испытаний для каждой марки обрабатываемого материала подобран абразивный круг оптимальной характеристики и назначены оптимальные режимы шлифования. Результаты измерений полученных радиусов сопряжений приведены в табл. 13 и на диаграмме (рис. 45).
На основе проведенного анализа возможности получения при шлифовании минимальных радиусов сопряжений поверхностей деталей различных форм, материалов, методов обработки можно сделать следующие выводы:
1. При шлифовании различных материалов оптимально подобранными кругами можно стабильно обеспечить минимально возможные радиусы сопряжений поверхностей образцов в диапазоне от
0,15 до 0,48 мм.
79
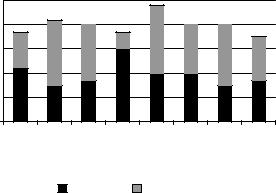
|
|
Таблица 13 |
Оптимальные характеристики кругов для обеспечения Rmin |
||
|
|
|
Обрабатываемые |
Rmin, мм |
Предпочтительный круг |
материалы |
|
|
ВТ3-1 |
0,22–0,37 |
64С25НСМ27К5 |
ЖС6К |
0,15–0,42 |
24А25ПМ37К5 с пропиткой дисульфидом |
|
|
молибдена |
ЭИ961Ш |
0,17–0,40 |
24А25ПМ37К5 с пропиткой дисульфидом |
|
|
молибдена |
ЭИ437Б |
0,30–0,37 |
24А25ПМ37К5 с пропиткой дисульфидом |
|
|
молибдена |
ЭП609 |
0,20–0,48 |
24А25ПМ37К5 с пропиткой дисульфидом |
|
|
молибдена |
ВЖЛ 14 УВИ |
0,20–0,40 |
24А25ПМ37К5 с пропиткой дисульфидом |
|
|
молибдена |
38Х2МЮАШ |
0,15–0,40 |
ЛО 125/100 СМ2К27-100 % |
Ст. 45 |
0,17–0,35 |
ЛО 125/100 СМ2К27-100 % |
500 |
|
|
|
|
|
|
|
|
|
|
|
|
|
|
|
|
|
|
|
|
400 |
|
|
|
|
|
|
|
|
|
|
|
|
|
|
|
|
|
|
|
|
300 |
|
|
|
|
|
|
|
|
|
|
|
|
|
|
|
|
|
|
|
|
200 |
|
|
|
|
|
|
|
|
|
|
|
|
|
|
|
|
|
|
|
|
100 |
|
|
|
|
|
|
|
|
|
|
|
|
|
|
|
|
|
|
|
|
0 |
|
|
|
|
|
|
|
|
|
|
|
|
|
|
|
|
|
|
|
|
|
1 |
|
К |
|
|
|
Б |
|
|
|
|
|
|
|
И |
|
|
|
|
5 |
|
- |
|
Ш |
|
|
|
|
Ш |
|
|
|
|
Ш |
|
4 |
|||||
|
3 |
|
6 |
1 |
|
3 |
|
|
9 |
|
|
В |
|
А |
. |
|||||
Т |
С |
|
|
|
|
У |
|
|
т |
|
||||||||||
6 |
|
4 |
|
0 |
|
|
|
Ю |
С |
|
|
|||||||||
В |
|
Ж |
|
9 |
И |
|
6 |
|
|
4 |
|
|
|
|
||||||
|
|
|
И |
Э |
|
П |
|
|
1 |
|
|
М |
|
|
|
|
||||
|
|
|
Э |
|
|
|
Э |
|
|
|
Л |
|
|
|
2 |
|
|
|
|
|
|
|
|
|
|
|
|
|
|
|
Ж |
|
|
Х |
|
|
|
|
|
||
|
|
|
|
|
|
|
|
|
|
|
|
8 |
|
|
|
|
|
|
||
|
|
|
|
|
|
|
|
В |
|
3 |
|
|
|
|
|
|
||||
|
|
|
|
Rmin, мкм |
|
|
|
Rmах, мкм |
|
|
|
|
Рис. 45. Гистограмма формирования фактических минимально возможных радиусов сопряжений по-
верхностей образцов в диапазоне от Rmin до Rmax (мкм) при шлифовании различных материалов
80