
1496
.pdf(допустимое отклонение угла разворота профилей сечений αзак –
впределах ±(8…10)′). Поверхности пера спинки и корыта пера лопатки могут быть линейчатыми или сложнофасонными, которые перемещаются в пространстве по определенному закону. Допустимое смещение профилей пера от теоретического положения в направлении оси X – в пределах 0,1–0,4 мм, в направлении оси Y – в пределах 0,1–0,2 мм в зависимости от длины хорды.
Потери на трение потока сжатого воздуха из-за повышенной шероховатости обтекаемых поверхностей лопаток компрессора, потери давления воздуха из-за неточности выполнения угла закрутки и толщины сечения профиля пера, из-за увеличения коэффициента теплоотдачи снижают КПД газотурбинного двигателя на 15–20 %. На авиационных предприятиях России и за рубежом эти высокие требования при изготовлении лопаток обеспечиваются в основном ручным размерным профильным полированием, так как механизировать данную операцию в настоящее время не представляется возможным
всвязи со сложностью и индивидуальностью геометрического профиля пера каждой лопатки.
При разработке технологических процессов исходят из обеспечения требуемой точности, формы поверхностей и их относительного расположения. При этом геометрическая точность изготовления лопаток тесно связана с параметрами качества поверхностного слоя: шероховатостью, значениями и распределением остаточных напряжений, глубиной и степенью наклепа, т.е. теми параметрами, которые во многом определяют сопротивление усталости данных деталей.
Выявлены производственные проблемы наиболее распространенной на предприятиях авиастроения (ММПП «САЛЮТ», НПО
«Сатурн», ОАО «ПМЗ», Pratt&Whitney (США), Snecma (Франция)
и др.) технологии полирования абразивными и полировальными кругами: низкое и нестабильное качество обрабатываемых профиля, сопряжений и кромок пера лопаток; нестабильное качество кругов, клея, войлока и т.д.; возникновение прижогов и трещин (брак 10– 30 %); периодические случаи появления рисок (брак 10–15 %); высокая трудоемкость процесса полирования (1 лопатка от 20 до 480 мин);
181
необходимость организации участков по производству и накатке кругов; требуется высокая квалификация (6–7 разряд) и большой опыт рабочих (стаж более 5 лет); неудовлетворительная экология процесса обработки: вибрация, шум, запыленность и т.д., вызывающие профзаболевания рабочих (силикоз, виброболезнь, глухота).
Проведен анализ альтернативных финишных технологий обработки профиля пера лопаток ГТД из титановых сплавов, к которым вынуждены переходить авиационные предприятия, применяемые оборудование и инструмент.
В результате анализа технологических процессов окончательной обработки лопаток ГТД из титановых сплавов установлено, что в настоящее время качества формирования геометрии и качества профиля пера лопатки можно достичь двумя методами обработки:
1)методом полирования на полировальной бабке абразивными шлифовальными кругами и полировальными кругами на войлочной основе, накатанными шлифпорошком и микрошлифпорошком на клей (мездровый, казеиновый, силикатный и т.д.);
2)методом полирования на ленточно-полировальных станках бесконечной лентой из шлифовальной шкурки оптимальной характеристики (начинает широко внедряться на многих предприятиях авиастроения, недостаточно изучен).
На первом этапе исследований проведены сравнительные эксперименты по обоснованию целесообразности применения ленточного полирования вместо полирования абразивными кругами для окончательной обработки профиля пера лопаток ГТД из титановых сплавов.
Рассмотрены принципиальные отличия процесса изготовления кругов и лент, структуры абразивного инструмента, схемы и физическая картина механизма съема металла абразивными инструментами для двух процессов полирования (абразивными кругами и лентами). Существенным отличием режущей части абразивных кругов от лент из шлифовальной шкурки является то, что в кругах только 30 % абразивных зерен являются режущими и 70 % – давящими, раздроб-
ленными, свободно расположенными в рабочей зоне зернами
(рис. 82).
182
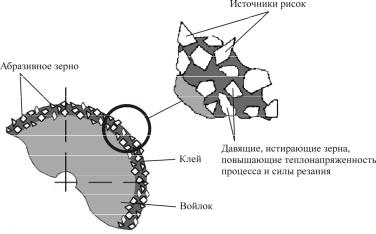
Рис. 82. Особенности структуры абразивных накатных кругов на войлочной основе
В процессе изготовления шлифовальных и полировальных кругов большую роль играет человеческий фактор (полировальные круги на войлочной основе изготавливают вручную). Технологический процесс изготовления абразивных лент автоматизирован, что исключает человеческий фактор и силовое воздействие на абразивные зерна в момент формообразования инструмента.
Нанесение на основу бесконечной ленты абразивного зерна осуществляется в электростатическом поле, выстраивая их острым краем вверх, после фиксации на основе это обеспечивает 100%-ную режущую способность зерна ленты (рис. 83), более равномерное распределение шероховатости и снижает возможность появления единичных рисок, повышая стабильность обработки.
Кроме того, подобная установка зерна на бесконечной ленте выравнивает силовую нагрузку зерен в зоне резания, увеличивает площадь зоны контакта ленты с деталью, снижает теплоту, которая быстро рассеивается и устраняет опасность появления деформаций, прижогов и возникновения внутренних напряжений в полируемой лопатке, так характерных для процесса обработки кругами.
183
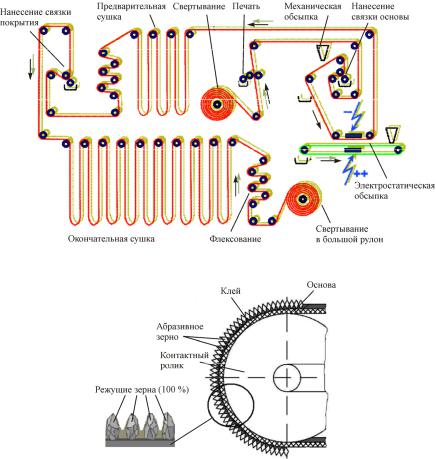
а
б
Рис. 83. Особенности автоматизированного изготовления и структуры шлифовальных бесконечных лент: а – процесс изготовления абразивов; б – общий вид ленты в работе
Выдвинута гипотеза, что применение ленточного полирования позволит решить проблему стабильного повышения качества профиля пера лопаток ГТД из титановых сплавов. С целью подтверждения гипотезы определены аналитические зависимости для расчета мак-
184
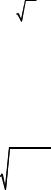
симальной температуры в зоне резания (Тmax), для предварительной сравнительной аналитической оценки теплонапряженности процессов полирования бесконечной лентой и кругом.
При сравнительном расчете максимальной температуры в зоне резания (Тmax) принято, что технологический процесс полирования рассматривается при следующих условиях;
•условная скорость перемещения лопатки при обработке Vдет =
=4,8 м/мин;
•сила прижатия детали к абразивному инструменту при выполнении каждого из переходов операции полирования постоянна
(Pу = const) и определена на основании статистического анализа экспериментальных исследований (размерное полирование – 3,0 Н, черновое полирование – 2,0 Н и чистовое – 1,0 Н).
Максимальная температура в зоне резания (Тmax, °С) при полировании титановых лопаток ГТД абразивными лентами и кругами может быть найдена из выражений, разработанных на основе работ С.Г. Редько, Е.П. Калинина, Л.А. Панькова и Н.В. Костина [4, 48, 53, 54], адаптированных к процессу согласно принятым условиям:
1) при полировании кругом на войлочной основе, накатанным шлифпорошком
T |
= |
250Vк qi lк |
, |
(1) |
|
||||
max |
|
V 3/ 2 |
|
|
|
|
дет |
|
где qi – количество тепла, создаваемого единичным зерном, кал/с; Vк – скорость резания, м/с; Vдет – скорость детали, м/с; lк – длина дуги контакта, мм;
2) при полировании |
|
бесконечной лентой из |
шлифовальной |
||||
шкурки |
|
|
2,6 Pу Vл |
|
|
|
|
Tmax |
= |
|
|
0,18 |
, |
(2) |
|
|
b |
Vдет lк |
|||||
|
|
|
|
|
где Vл – скорость резания (ленты), м/с; Pу – радиальная сила давления детали на инструмент, Н; b – ширина пятна контакта, мм; lк – длина дуги контакта, мм.
185
Результаты расчета максимальной температуры в зоне резания (Тmax) при полировании лопаток ГТД из титановых сплавов абразивными лентами и кругами по полученным аналитическим зависимостям (1) и (2) частично подтверждают выдвинутую гипотезу и являются основой для дальнейшего сравнительного исследования двух процессов полирования (табл. 27).
Таблица 27
Результаты расчета максимальной температуры в зоне резания по формулам (1) и (2) при полировании лопаток ГТД
из титановых сплавов по переходам
Номер |
Температура в зоне резания Тmax, °С |
||
перехода |
при обработке кругом |
при обработке лентой |
|
1 |
659 |
319,9 |
|
|
|
|
|
2 |
471,8 |
196,1 |
|
|
|
|
|
3 |
249,1 |
76,9 |
|
|
|||
155,9 |
|||
|
|
||
|
|
|
Для описания формирования параметра шероховатости (Ra, мкм) разработана математическая модель на базе зависимостей, полученных Ф.С. Юнусовым и Ю.Я. Фельдманом [57]:
|
|
|
|
P1/3 1 |
± R |
/ R |
|
2/3 Н |
|
1/2 |
|
Ra = 5,38 |
|
|
|
( |
рол |
дет) |
|
|
|
− |
|
|
|
|
|
|
|
|
|
|
|
||
1/3 |
2 |
|
1/3 |
4/3 |
|
(1± Rрол / Rдет ) |
5/3 |
||||
|
Dрол 4 |
Vл |
H (2Rрол) |
+ Pу |
|
|
|
|
|||
|
|
|
|
|
|
|
|
|
|
|
|
|
|
|
|
− 0,11 dз, |
|
|
|
|
(3) |
где Rрол – радиус контактного ролика, мм; Rдет – радиус профиля пера лопатки, мм; Н – толщина снимаемого слоя, мм; Dрол – диаметр ролика; Vл – скорость резания (ленты), м/с; Ру – радиальная сила давления детали на инструмент, Н; dз – средний диаметр абразивных зерен, мм.
186
Зависимости адаптированы для полирования лопаток ГТД из титановых сплавов бесконечными лентами из шлифовальной шкурки, где учитываются радиус закругления вершин абразивных зерен, коэффициент стружкообразования, динамический модуль упругости контактного ролика, а также количество работающих зерен во время обработки и коэффициент факторов, влияющих на обработку, определенных эмпирическим путем для ленточного полирования титановых сплавов.
Разработанная аналитическая модель позволила установить теоретическую взаимосвязь между технологическими условиями полирования профиля пера лопаток ГТД бесконечными лентами из шлифовальной шкурки и шероховатостью поверхности (Ra, мкм).
Разработана методика экспериментальных исследований полирования лопаток ГТД из титановых сплавов абразивными кругами
илентами для установления закономерностей и взаимосвязей влияния параметров абразивного инструмента и технологических характеристик процесса на шероховатость, остаточные напряжения, наклеп, микроструктуру, вероятность возникновения случайных глубоких рисок, температуру в зоне контакта инструмента и детали, вибрацию, шум и запыленность в зоне резания.
Для проведения экспериментальных исследований в качестве оборудования выбраны полировальные бабки и ленточно-полиро- вальный станок. На основании проведенного обзора номенклатуры
итехнических характеристик оборудования и оснастки, предлагаемых мировыми производителями (Bader, Lozer, Metabo и др.), сформировано техническое задание для проектирования и изготовления ленточно-полировального станка. В результате спроектирован и разработан специальный ленточно-полировальный станок ЛПС-1 и оснастка (рис. 84, 85). На станке предусмотрены сменные контактные ролики различных диаметров для полирования профильных поверхностей спинки и корыта пера лопаток (см. рис. 84). Натяжение ленты регулируется дросселем пневмоцилиндра. Материалом роликов служат резина, полиуретан различной твердости или войлок. Перед установкой и на станке контактные ролики тщательно балансируются
187
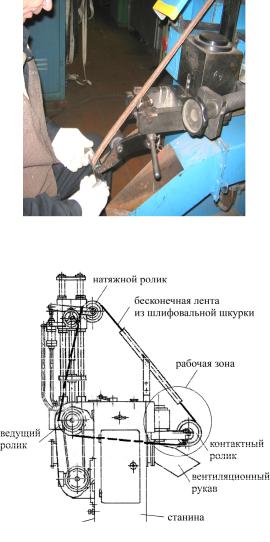
для уменьшения вибрации и улучшения качества полирования. Определена оптимальная скорость ленты для проведения эксперимен-
тов (Vл = 15 м/с).
Рис. 84. Процесс полирования пера лопатки на станке ЛПС-1
Рис. 85. Схема ленточно-полировального станка ЛПС-1
188
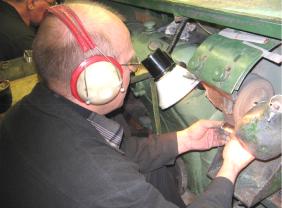
Исследования полирования лопаток абразивными накатными кругами (рис. 86) проводились в лабораторных и производственных условиях на полировальных бабках – заточных станках 3Б634 (n = 2800 об/мин).
Рис. 86. Общий вид полирования лопаток абразивными накатными кругами на заточном станке 3Б634
Для определения наиболее рациональной характеристики бесконечных лент из шлифовальной шкурки при выполнении операции полирования лопаток по параметрам производительности, стойкости лент и шероховатости исследована большая гамма инструментов на гибкой основе различных характеристик и производителей
(ОАО «БАЗ», VSM, HERMES, SAIT и др. (табл. 28).
По результатам испытаний различных лент построены гистограммы изменения шероховатости поверхности (Ra, мкм) и коэффициента шлифования (Кшл) (рис. 87, 88).
В результате совместного анализа гистограмм Ra и Кшл определены наилучшие показатели у лент № 5 и 8 – ЛБ1 40×3600 Р80 C-W (SAIT) и ЛБ1 40×3600 Р80 CR315 X (HERMES).
189
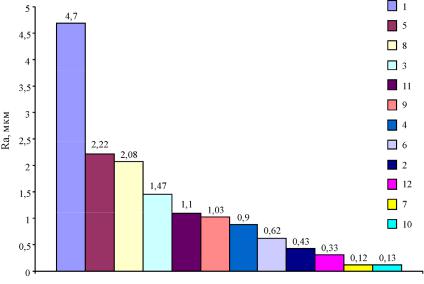
|
|
|
|
Таблица 28 |
|
Кодирование применяемых лент |
|
||
|
|
|
|
|
Номер ленты |
Обозначение |
|
Производитель |
|
1 |
ЛБ1 40×3600 54С Р60 С1 СФЖ |
|
ОАО «БАЗ» |
|
2 |
ЛБ1 40×3600 54С Р320 С1 СФЖ |
|
ОАО «БАЗ» |
|
3 |
ЛБ1 40×3600 54С Р100 С1 СФЖ |
|
ASURA |
|
4 |
ЛБ1 40×3600 54С Р230 С1 СФЖ |
|
ASURA |
|
5 |
ЛБ1 40×3600 Р80 C-W |
|
SAIT |
|
6 |
ЛБ1 40×3600 Р240 C-W |
|
SAIT |
|
7 |
ЛБ1 40×3600 Р400 C-W |
|
SAIT |
|
8 |
ЛБ1 40×3600 Р80 CR315 X |
|
HERMES |
|
9 |
ЛБ1 40×3600 |
Р150 CR315 X |
|
HERMES |
10 |
ЛБ1 40×3600 |
Р500 CR315 X |
|
HERMES |
11 |
ЛБ1 40×3600 |
Р120 CК742J |
|
VSM |
12 |
ЛБ1 40×3600 |
Р120 CК742J |
|
VSM |
Рис. 87. Гистограмма шероховатости поверхности (Ra) после полирования различными лентами на станке ЛПС-1
190