
1496
.pdf
Рис. 133. Кинематическая схема агрегатной четырехмодульной автоматизированной установки для скругления кромок дисков турбины полимер- но-абразивными щетками
агрегатных станков – полуавтоматов с четырьмя шлифовальными головками. Шлифовальный модуль состоит из стойки с вертикальной неподвижной осью, корпуса, кронштейна. На каждом кронштейне
291

закреплена шлифовальная головка с ПАЩ. Положение шлифовальной головки по высоте (в вертикальной плоскости) регулируется поворотом кронштейна вокруг оси. Разворот (в горизонтальной плоскости) шлифовальной головки вместе с кронштейном и корпусом из рабочего положения в отведенное положение осуществляется реечным механизмом вокруг оси. Шлифовальная головка каждого модуля может быть установлена под требуемым углом (см. рис. 133) к оси симметрии обрабатываемого паза в соответствующем диапазоне угла полной окружности разворотом вокруг оси: первый модуль (0±30)°
и (180±30)°, второй модуль (45±30)° и (225±30)°, третий модуль (90±30)° и (270±30)°, четвертый модуль (135±30)° и (315±30)°. Мо-
дули установлены на станине так, что обеспечен подвод и отвод всех шлифовальных головок из рабочего положения в отведенное и обратно без столкновения их друг с другом.
Первый агрегатный станок предназначен для обработки елочных пазов в дисках турбин и содержит станину, стол и четыре шлифовальных модуля (рис. 134).
Рис. 134. Агрегатный станок-полуавтомат для скругления кромок «елочных» пазов в дисках турбин
292
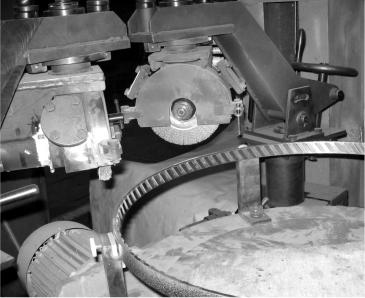
Для скругления острых кромок в пазах «ласточкин хвост» в дисках компрессора и в кольцах направляющего аппарата спректирована и изготовлена вторая агрегатная установка (рис. 135).
Рис. 135. Агрегатная установка для скругления кромок в пазах типа «ласточкин хвост» в дисках и кольцах компрессора ГТД
Обработка на агрегатном станке предусматривает двухчасовой режим работы. Сначала диск вращается на столе со скоростью 1 об/мин в одну сторону 30 мин, затем в противоположную сторону 30 мин, после этого диск переворачивают и обрабатывают аналогично другую сторону диска. В результате стабильно обеспечивается получение требуемого равномерного радиуса скругления и шероховатости обработанной поверхности для всех «елочных» пазов диска.
Для оценки влияния обработки полимерно-абразивными щетками на состояние качества поверхностного слоя торцовых поверх-
293

ностей обода диска проведены исследования остаточных напряжений и микротвердости. Из торцовых поверхностей диска (материал ЭП741НП) электроэрозионным методом вырезаны образцы 15×5×1,2 (мм). Измерения остаточных напряжений проводились методом травления на приборе «Пион-2». Микротвердость измерялась на микроскопе ПМТ-3. Результаты измерений остаточных напряжений приведены на графиках рис. 136. Установлено, что до и после обработки ПАЩ характер и величина остаточных сжимающих напряжений практически не изменяется.
Рис. 136. Изменение остаточных напряжений на торцовой поверхности до и после обработки полимерно-абразивными щетками
Врезультате измерения микротвердости (рис. 137) установлено, что при обработке щетками характер и величина микротвердости не изменяется. Следовательно, обработка щетками не влияет на изменение характеристики торцовых поверхностей.
Врезультате внедрения технологии скругления кромок пазов
дисков турбин полимерно-абразивными щетками по сравнению с ручной обработкой улучшилось качество и повысилась производительность. При ручной обработке острых кромок трудоемкость составляла 8 ч. При этом контролеры выявляли неравномерность и граненость профиля в поперечном сечении, глубокие риски на фасках. После обработки пазов диска на автоматизированном агрегатном станке полимерно-абразивными щетками получено равномерное
294
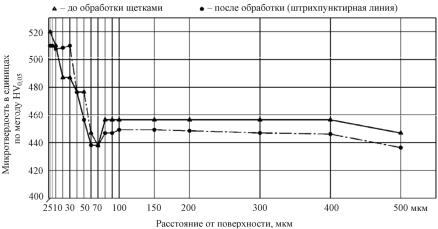
Рис. 137. Изменение микротвердости на торцовой поверхности до и после обработки полимерно-абразивными щетками
стабильное скругление по всему профилю, отсутствует граненость профиля и риски на поверхности скругления. Время обработки сократилось в 4 раза и занимает всего 2 ч.
2.6. Выбор оптимальной характеристики и типа абразивных инструментов для производительного шлифования тонкостенных сотовых уплотнений
В газотурбинных двигателях применяется особый вид сотовых ячеистых уплотнений между вращающимися вершинами лопаток турбины и неподвижным корпусом статора турбины для предотвращения утечки горячих газов и сохранения КПД двигателя. Сотовые уплотнения получаются путем напайки «гофрированного» металла на пластины-основания. Полученные сотовые ячейки имеют различающиеся высотные размеры, так как во время напайки возможен излишний нагрев и усадка материала либо его расплавление. Стенки ячеек сот очень тонкие – имеют толщину 0,05–0,1 мм, что создает серьезные проблемы при обработке. Для получения высотного раз-
295
мера сот в пределах допуска по всему периметру окружности статора обычно применяется такой вид обработки, как шлифование. При данном виде обработки выдерживается не только высотный размер, но и обеспечивается требуемая шероховатость поверхности.
По характеру обрабатываемых поверхностей технологические схемы шлифования можно разделить на три основных вида: 1) обработка наружных и внутренних поверхностей вращения (круглое шлифование); 2) обработка плоских поверхностей (плоское шлифование); 3) обработка сложных поверхностей.
Кпроцессам круглого шлифования относится обработка цилиндрических, конических и фасонных, гладких и ступенчатых, сквозных и глухих, наружных и внутренних поверхностей вращения. При круглом шлифовании обрабатываемая деталь вращается вокруг своей оси. Кроме того, при круглом шлифовании имеет место относительное взаимное перемещение шлифовального круга и детали вдоль ее оси (продольная подача) и нормально к оси детали (поперечная подача). Возможна также подача под углом к оси детали.
Плоское шлифование характеризуется наличием продольной
подачи S1 и (или) поперечными подачами: S2 – вдоль шлифуемой поверхности и (или) S3 – нормально к шлифуемой поверхности. Поперечную подачу осуществляют после каждого хода детали относительно круга и измеряют в миллиметрах на ход стола станка. Шлифование выполняют периферией или торцом круга.
Кпроцессам профильного шлифования относятся обработка резьбо- и зубообразующих поверхностей, шлифование сферы и сложной фасонной поверхности при относительном перемещении обрабатываемой детали и шлифовального круга по копиру или при помощи привода от кулачка, а также шлифование по шаблону плоских деталей со сложным контуром.
Для обработки сотовых уплотнений в цехах ОАО «ПМЗ» используют два вида круглого внутреннего шлифования: алмазное кон- тактно-эрозионное шлифование и обычное шлифование с использованием высокопористых или мелкозернистых кругов.
296
Алмазное контактно-эрозионное шлифование (АКЭШ). Сущ-
ность метода состоит в том, что абразивный инструмент и деталь подключают к полюсам технологического источника импульсного тока и возбуждают между ними в зоне резания импульсные электрические разряды. Обработку ведут в диэлектрической жидкой среде, причем деталь используют в качестве правящего электрода. АКЭШ можно осуществить на обычном шлифовальном станке в условиях каждого предприятия. АКЭШ можно реализовать на серийных станках для плоского, круглого наружного, внутреннего, бесцентрового, координатного, оптического шлифования, а также на заточных станках. Для этого их модернизируют: изолируют шлифовальный круг или обрабатываемую деталь от массы станка и осуществляют надежные токоподводы, причем достаточно изолировать только шлифовальный круг или деталь. Электрический ток должен подводиться непосредственно к вращающемуся кругу и детали или к их оправкам. Следует избегать такого подключения токоведущих шин, при котором ток протекает через подшипники станка, вызывая их преждевременное эрозионное разрушение. Кроме того, токоподводящее устройство должно быть простым конструктивно и технологичным в изготовлении и установке на станок. С учетом этих требований разработана типовая конструкция токоподводящего устройства для использования на шлифовальных станках (рис. 138).
Алмазный круг 7 изолируют изоляционной прокладкой 10 (например, из рентгеновской пленки или фотопластинки) между фланцем 8 оправки круга и шпинделем 11 станка. Между головкой болта 12 и фланцем 8 устанавливают шайбу 9. Токосъемник 5 выполнен в виде резьбовой втулки, которая закреплена в центральном резьбовом отверстии фланца 8. Щеточное устройство состоит из медного стержня-щетки 1 и изоляционного корпуса-втулки 3. Щетку 1 поджимает к токосъемнику 5 пружина 2. Корпус 3 щеточного устройства закреплен на крышке 6 кожуха шлифовального круга прижимной гайки 4. Особенность описанной изоляции круга от станка – применение изоляционной пленочной прокладки 10. Для удобства установки круга на шпинделе ее наклеивают на базирующую поверхность фланца
297

Рис. 138. Общая схема токоподводящего устройства к алмазному кругу на модернизированном шлифовальном станке
на конус шпинделя. Края прокладки должны сопрягаться обязательно встык и не допускается внахлест, что приведет к погрешности базирования круга. В отличие от известных токоподводящих устройств такая конструкция быстро реализуется на практике для большинства типов шлифовальных станков. Появляется возможность балансировки круга в сборе с токосъемником. Если обрабатываемая деталь не вращается, то ток подводят к ней, подключая полюс источника к массе станка вблизи от места закрепления детали. В случае вращения детали щеточный токоподвод осуществляют к зажимной тяге конуса или к оправке детали. Этот способ шлифования получил распространение ввиду заметного повышения режущей способности абразивного инструмента в течение значительного времени эксплуатации. Последнее обусловлено воздействием электрических разрядов на связку инструмента, что обеспечивает постоянное обнажение абразивных зерен и устранение засаливания межзернового пространства. Кроме того, АКЭШ имеет ряд других эксплутационных преиму-
298
ществ. Так, вместо электролитов, применяемых при алмазном электрохимическом шлифовании, в данном случае используют водные растворы СОЖ. Для реализации процесса требуется меньшая выходная мощность источника тока. Износ абразивных кругов при электролитической обработке по сравнению с износом их при обычном шлифовании в 2–10 раз меньше, шероховатость обработанной поверхности достигает Ra = 0,020…0,32 мкм. Процесс может быть реализован по всем схемам абразивного шлифования токопроводящих материалов.
Метод АКЭШ разработан и используется успешно для обработки сотовых уплотнений деталей ГТД. В процессе шлифования этим методом образующиеся мелкие заусенцы сгорают от электрических разрядов и соты получаются чистыми без заусенцев. Однако в связи с появлением на новых двигателях деталей новых конструкций в настоящее время применение данного метода шлифования АКЭШ оказалось невозможным. Новые детали имеют такие поверхности, на которые не допускается попадание любой жидкости из-за возможного разъедания специальных покрытий на этих поверхностях. Поэтому разработаны методы обычного круглого внутреннего шлифования абразивными электрокорундовыми и эльборовыми кругами.
Методы обычного шлифования сотовых уплотнений применяются на модернизированном токарно-лобовом станке модели 1М63 и на токарно-карусельном станке «Димоваг» с использованием дополнительной шлифовальной головки. Для обработки сотовых уплотнений из жаропрочной нержавеющей стали 07Х12НМБФ-Ш (ЭП609-Ш) применяются эльборовые круги характеристики 1А1-1 100(125)×20×32 ЛО(ЛП, ЛД, ЛКВ) 63/50-50/40 СМ1-СМ2 К. Кроме того, применяется обработка мелкозернистыми высокопористыми шлифовальными кругами характеристики 11.125×45×35 25А 6…12 ЗИ 33…35 10К. В процессе внедрения обычного шлифования установлено, что на поверхности сот образуются заусенцы, поэтому требуется введение дополнительной операции для их удаления. Удаление заусенцев проводится вручную с помощью острых тонких над-
299
филей. Эта операция очень трудоемка и малопроизводительна, требует высокой квалификации рабочего. Поэтому поставлена задача поиска механизированного метода удаления заусенцев из ячеек сот. Для выбора наиболее оптимальной характеристики кругов проведены специальные исследования.
Методика работы предусматривает проведение исследований влияния процесса шлифования абразивными кругами различных характеристик на величину образования заусенцев в ячейках сот. Для исследований выбраны восемь абразивных кругов следующих характеристик.
1)1-100×20×20 54С М1 4 СГФ 35Б;
2)1-150×15×32 25А 25 ГТВ61 8Б;
3)1-150×40×32 64С 16 ЭКП120 20 м/с;
4)1-125×40×32 54С 12 ЭКП120;
5)1-150×20×32 СГА0 160/125 С52 4 В1-09;
6)лепестковый круг КЛ150×30×32 25А 16;
7)высокопористый 1-150×25×32 25А 12П ЗИ-37 12К;
8)высокопористый 1-90×40×20 25А 12П М3 К6 35 м/с КФ40 1 кл А ТУ2-036-979–86.
При выборе рациональной схемы шлифования рассмотрены следующие методы: а) шлифование попутное (круг и деталь вращаются в одном направлении); б) шлифование встречное (круг и деталь вращаются в разных направлениях); в) шлифование с реверсом круга (и) или детали (направления вращения круга и детали варьируются, т.е. изменяется со встречного на попутное шлифование и обратно) (рис. 139).
Наиболее эффективным видом шлифования является встречное шлифование. Исследовано влияние на образование заусенцев и режимов шлифования, которые включают в себя такие параметры, как скорость вращения круга, скорость детали, глубина шлифования, продольная подача.
Для анализа влияния элементов режима резания на точность и чистоту обработанной поверхности проведено теоретическое исследование влияния этих факторов на глубину резания, приходящуюся
300