
1496
.pdfс поверхности (при увеличении в 500 раз), показали, что микротвердость в зоне этих пятен не отличается от микротвердости основного материала. Рентгеноспектральный анализ на микроанализаторе МАР-2 не выявил различий в количественном составе в зоне «белого пятна» и вне его. Газонасыщение поверхностного слоя данным микроанализатором определить нельзя.
Следовательно, предположения о прижогах, о внедрении абразивного зерна связки или алмазного круга, о налипании от полировальных паст не подтвердились.
Рентгеноструктурный анализ, проведенный на дифрактометре «ДРОН-3», показал, что фазовый состав в зоне пятна и вне его одинаков, метастабильных фаз в поверхностном слое не обнаружено.
Вместе с тем в пятне, которое не удалось вывести после двух дополнительных переполировок и травления, на дифрактометре «ДРОН-2» обнаружена 1 линия метастабильной фазы. По-видимому, это «белое пятно» – результат термомеханического воздействия до механической обработки на операции штамповки.
В микроструктуре металла в зоне светлых пятен сильной интенсивности, расположенных на кромках пера лопатки, имеются изменения в β-фазе. Рентгеноструктурный анализ на дифрактометре «ДРОН-2» показал некоторое размытие дифракционных линий и фаз и наличие следов метастабильных фаз в светлых пятнах.
Для уточнения природы этих пятен был преднамеренно сделан перегрев лопатки путем полировки изношенным кругом до образования цветов побежалости различных оттенков. После травления на кромке лопатки выявлено сквозное пятно от белого до темно-серого цвета. В месте «белого пятна» выявлены изменения в β-фазе.
Рентгеноструктурный анализ пятна показал сильное размытие дифракционных линий и β-фаз, расщепление отражений β-фазы и появление мартенситной фазы. Микротвердость металла в зоне сквозного пятна значительно ниже, чем в основном материале (снижение с 341 до 244 МПа), что также указывает на наличие в этой зоне β-фазы. Изменения в структуре металла произошли в результате
171
значительного местного разогрева лопатки (прижога), который при обычной обработке практически недостижим.
При получении преднамеренного прижога тепло подводилось к лопатке в середине пера, а прижог с изменением структуры оказался на выходной кромке. Таким образом, получить прижог на середине пера, не прижигая кромку, практически не удалось.
С целью определения теплового состояния титановых лопаток при ручной полировке, температур, при которых возникают «белые пятна» при травлении, и самого теплонапряженного перехода на операции ручной полировки проведены температурные исследования.
Титановые лопатки из сплавов ВТ8-М и BT3-1 обрабатывались по следующему маршруту: штамповка, термообработка, фрезерование, алмазное или ленточное шлифование, ручная подгонка бакелитовым кругом, ручная полировка фетровым кругом, ручная глянцовка фетровым кругом, ручная глянцовка фетровым кругом с пастой, травление на прижоги.
Ручная подгонка осуществляется бакелитовым кругом 63С40...25М3...СМ1Б, полировка – фетровым кругом 63С12М, глянцовка фетровым кругом 63С5М с пастой. Скорость резания – до
30 м/с.
Температуры в зоне обработки титановых лопаток замерялись искусственными термопарами.
Хромель-алюминиевые термопары (проволока 0,3 мм) делались малоинерционными (без шарика) за счет замыкания электродов через тело лопатки на расстоянии друг от друга до 0,5 мм. Электроды присоединялись конденсаторной сваркой. Провода изолировались при помощи кремнеземной нити K11C6-180, пропитанной лаком
KO-815.
Применение искусственной термопары позволило использовать стандартную (по ГОСТ 3044–77) градуировочную таблицу, а выполнение их без шарика – замерять температуру расположенного между электродами основного металла – титана.
Показания термопар выводились на светолучевой осциллограф H043.1 и фиксировались на светочувствительную бумагу УФ-67 при
172
помощи гальванометров M14-400 (ƒ = 400 Гц). Скорость протяжки бумаги, выбранная в ходе предварительных экспериментов, равнялась 5 мм/с.
Измерительные каналы осциллографы градуировались от потенциометра ПП-63 (или компаратора Р3003) с 0 до 1200 °С через 50 °С в соответствии с градуировочной таблицей на хромельалюмелевую термопару (по ГОСТ 3044–77). По полученным данным строился градуировочный график.
Для замера температур методом естественной малоинерционной термопары были выбраны лопатки BT3-1 и ВТ8-М после операций алмазного и ленточного шлифования. На каждую лопатку устанавливалось по 6 термопар. Термопары № 2 и 5 выводились на обрабатываемую поверхность в среднем сечении лопатки. Глубина заделки термопар составляла 0,2–0,3 мм от поверхности. В процессе обработки эти термопары срезались, а поэтому температура замерялась непосредственно в зоне обработки.
Для определения температурного состояния поля лопаток в процессе обработки (распределение температур) использовался метод термокрасок, дополненный методом искусственных малоинерционных термопар.
При реализации метода термокрасок применялись 2 термокраски: ТР-8 фирмы «Роллс-Ройс» (Великобритания) и ТК-30 (г. Ставрополь). Метод термопар соответствовал описанному выше: на расстоянии 0,3–0,4 мм от кромки лопатки были установлены термопары № 1, 3, 4 и 6 со стороны, противоположной обрабатываемой (при обработке лопаток по спинке термопары со стороны корыта и наоборот). Этими термопарами регистрировался прогрев лопаток. Результаты, полученные методом термопар и методом термокрасок, сравнивались.
Сущность метода термокрасок заключается в том, что лопатка покрывается термокраской, которая при различных температурах нагрева необратимо меняет цвет. Цветная картинка, образующаяся на лопатке после обработки, характеризует распределение максимальных температур на обратной стороне обработанной лопатки.
173
Градуировка термокрасок осуществлялась на образцах на установке Г21-018СБ. В центре образца устанавливалась искусственная хромель-алюмелевая термопара (проволока 0,5 мм) в изоляции из кремнеземной нити K11С6-180, пропитанной лаком KO-815. Показания с термопары выводились на цифровой прибор А565 (класс точности 0,15). Образец нагревался переменным током (I = 150 A, U = 0...12,5 В), при этом температура нагрева контролировалась по прибору А-565.
На этапе отработки методики замеров температур и выбора подходящей термокраски на лопатке из ВТ8-М со стороны корыта было установлено 6 термопар. Кроме того, вся лопатка была покрыта краской ТР-8. Ручная подгонка этой лопатки со стороны спинки показала, что краска ТР-8 не удовлетворяет поставленным требованиям: нижний предел реагирования этой краски (420 °С) не позволяет регистрировать низкотемпературные процессы в процессе обработки на серийных режимах.
Одновременно была подтверждена сходимость методов термопар и термокрасок: термопары № 4 и 5 показали температуру до 665– 675 °С, термокраска – до 610 °С (обработка велась на интенсивном режиме).
Поэтому в дальнейших экспериментах использовалась многопереходная краска ТК-30, имеющая удовлетворительную адгезию к титану и широкий спектр температурных переходов (от 120 до 1015 °С). Для определения температур, вызывающих образование прижогов на титане, лопатки покрывались термокраской ТК-30 со стороны, противоположной обрабатываемой, затем обрабатывались на интенсивных режимах фетровым кругом без зерна (с одним клеем) до появления интенсивных цветов побежалости, после чего обработанная поверхность аккуратно заполировалась фетровым кругом 63С5M с пастой и лопатки промывались в керосине.
С полученной лопатки зарисовывался вид температурного состояния, после чего термокраска удалялась этиловым спиртом и мелкой шкуркой (зернистостью М40–М28). Подготовленные указанным образцом лопатки травились до появления прижогов по серийной
174
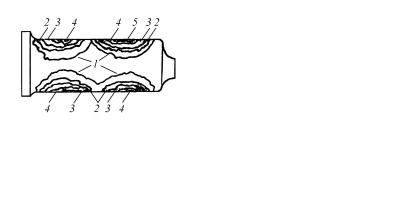
технологии. «Белые пятна», обнаруженные при травлении, зарисовывались и накладывались на вид температурного состояния лопатки.
Экспериментальная обработка лопаток осуществлялась на заточном станке 3М642Е при чистоте вращения круга 3150 об/мин. Были использованы шлифовальные бакелитовые круги ПП135×32×32 и ПП160×32×32 характеристики 63С25СМ1Б, полировальный фетровый круг диаметром 90 мм с накаткой зерна 63С № 12 на мездровый клей (63C12M) и полировальный фетровый круг диаметром 90 мм с накаткой зерна 63С № 5 на мездровый клей с пастой № 18 (63С5M + паста). Скорость резания при подгонке составляла 22 и 26 м/с, при полировке – 15 м/с.
В процессе подгонки снимался припуск 0,2–0,3 мм. При этом обеспечивалась шероховатость Rа = 0,32 мкм при отсутствии рисок.
Результаты замеров температур термопарами № 2 и 5 и зарисовки распределения температурных полей на профиле пера лопаток (в зоне обработки) приведены на рис. 78 и 79.
Рис. 78. Характер распределения температурных полей на пере лопатки при полировке: 1, 2, 3, 4, 5 – соответственно температура 120–300, 300–400, 400–560, 560–680 и 680–810 °С
175
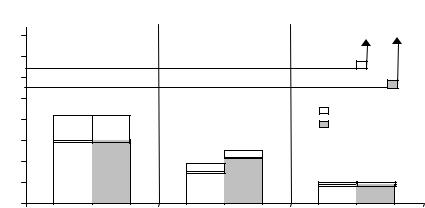
T, °C |
|
|
|
700 |
ЗОНА «белых пятен» ВТ3-1 |
|
|
600 |
ЗОНА «белых пятен» ВТ8-М |
|
|
500 |
|
|
ВТ3-1 |
400 |
|
|
|
|
|
ВТ8-М |
|
|
|
|
|
300 |
|
|
|
200 |
|
|
|
100 |
|
|
|
0 |
|
|
|
|
Подгонка |
1-я полировка |
2-я полировка |
|
(63С25СМ1Б) |
(63С12М) |
(63С5М) |
Рис. 79. Влияние вида обработки профиля пера лопаток из титановых |
|||
|
сплавов ВТ3-1, ВТ8-М на температуру полирования |
Как видно из диаграмм, максимальная температура (305–470 °С) в данном случае наблюдается при подгонке бакелитовым кругом. При этом при обработке корыта температуры выше (до 430–470 °С), чем при обработке спинки (до 305–390 °С).
При первой полировке (63C12M) температуры ниже и достигают лишь 170–230 °С. При этом при обработке лопаток из сплава ВТ8-М они выше (до 220–230 °С), чем при обработке лопаток из сплава BT3-1 (до 170–180 °С).
При второй полировке (63С5М + паста) во всех случаях температуры не превышали 110 °С.
Таким образом, при правильной обработке серийным инструментом в поверхностном слое лопаток возникают температуры, не превышающие 470 °С, что ниже температур отжига (550 °С для сплава ВТ8-М и 640 °С для сплава BT3-1).
Существенной разницы в температурном состоянии лопаток из сплавов ВТ8-М и BT3-1 не обнаружено.
176
Из сопоставления результатов замеров температур вытекает следующее: наиболее теплонапряженный переход зависит от принятой схемы обработки, т.е. при съеме большого припуска (0,2–0,3 мм и более) бакелитовым кругом зернистостью № 25 именно на этом переходе возникают максимальные температуры (до 470 °С), при съеме же малого припуска бакелитовым кругом зернистостью № 40 максимальные температуры (до 400 °С) отмечаются при первой полировке фетровым кругом 63C12M. Для обеспечения минимальных температур необходимо уменьшить припуск на ручную подгонку, а первую полировку фетровым кругом 63С12M осуществлять после подгонки бакелитовым кругом зернистостью № 25.
Как видно на рис. 78, прижоги при травлении обнаружены в зонах, подвергшихся разогреву при обработке в диапазоне 560–680 °С. При этом зона «белого пятна» значительно меньше по площади зоны с температурой более 560 °С. Таким образом, можно считать, что «белые пятна» при травлении появляются при температурах выше
600 °С.
Следовательно, более интенсивная механическая обработка с прогревом до температур 650–680 °С для сплава BT3-1 и 600– 620 °С для сплава ВТ8-М приводит к появлению на кромках «белых пятен». Фактически в серийном производстве при полировке лопаток применяются более низкие режимы обработки, которые не должны вызывать появления «белых пятен» на пере, так как максимальные температуры при этом не превышают 400–470 °С.
На партии лопаток, обработанных под наблюдением, были обнаружены после травления светлые пятна в основном в среднем сечении, причем на предыдущей операции в этих местах пятен не было. Связь между вероятностью появления пятен, съемом на операции ленточного шлифования и припуском на полировку не установлена. В поверхностном слое после ленточного шлифования, подгонки и полирования изменения не обнаружены, метастабильные фазы отсутствуют. В поверхностном слое в месте темного пятна после ленточного шлифования интенсивность линии (110) β-фазы несколько
177
занижена. В зоне «белого пятна» после полировки изменения микроструктуры не обнаружены, нет также отличий и интенсивности линий (110) и (200) β-фазы. Многократная переполировка и травление не всегда устраняют «белые пятна». Отжиг, выполненный до травления, исключает «белые пятна» на большинстве лопаток. Виброгалтовка не изменяет характер и форму «белых пятен» на профиле пера лопаток.
При усталостных испытаниях лопатки с «белыми пятнами» на пере и без них имели практически одинаковый предел выносливости, причем разрушение лопаток происходило не по месту «белых пятен».
Таким образом, установлено, что основная причина появления «белых пятен» на пере титановых лопаток – разнотравимость металла с различной термопластической деформацией, полученной при штамповке. Прижоги могут возникнуть только на кромках пера лопаток при преднамеренном интенсивном полировании пера затупленным кругом с большим усилием прижима, поэтому появление «белых пятен» на пере титановых лопаток не является браковочным признаком.
1.16. Эффективность применения ленточного полирования лопаток вместо полирования абразивными
накатными кругами
В современных газотурбинных двигателях устанавливается более 3,5 тыс. рабочих, сопловых и направляющих лопаток компрессора и турбин. Функциональное назначение этих лопаток в двигателе различное, но все они должны быть изготовлены с высокой точностью и низкой шероховатостью для обеспечения требуемых высоких аэродинамических параметров и коэффициента полезного действия двигателя (рис. 80).
На большинстве двигателей до 60–70 % лопаток изготавливаются из титановых сплавов (ВТ8-М, ВТ3-1 и др.). Однако эти сплавы, обладая ценными конструкционными свойствами (теплоустойчи-
178
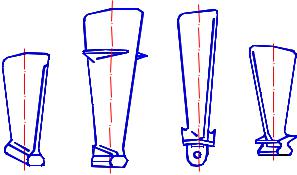
вость, коррозионная стойкость, малый удельный вес и т.д.), характеризуются весьма низкой обрабатываемостью резанием лезвийным и абразивным инструментом и низкой теплопроводностью, что увеличивает трудоемкость механической обработки и приводит при абразивной обработке к появлению шлифовочных прижогов и трещин. Теплопроводность титана, равная 7,5 Вт/(м°С), в 5 раз меньше, чем у железа, и в 14 раз меньше, чем у алюминия. Во столько же раз ниже и его температуропроводность.
Рис. 80. Общий вид полируемых поверхностей пера различных лопаток компрессора газотурбинного двигателя
Наиболее сложной, ответственной и дорогостоящей операцией в технологии изготовления лопаток из титановых сплавов у нас в стране и за рубежом является размерное полирование – окончательная механическая обработка сложного закрученного профиля, сопряжений и кромок пера. По данным зарубежной литературы, стоимость одной операции полирования – более 50 долл. США, а трудоемкость операции полирования составляет более 60 % от всей трудоемкости изготовления лопатки.
Высокая трудоемкость размерного профильного полирования лопаток ГТД обусловлена повышенными требованиями к обеспечению качества поверхностного слоя лопаток ГТД (Ra ≤ 0,32...0,16 мкм, от-
179

сутствие рисок, прижогов и трещин, обеспечения требуемого уровня остаточных напряжений, микротвердости и структуры металла в поверхностном слое) и к аэродинамическим характеристикам профиля пера (допустимое отклонение точек профиля пера от теоретического положения по 6–9 контрольным сечениям – в пределах 0,02–0,04 мм в зависимости от длины хорды).
Весьма тонкое перо лопаток компрессора (толщина сечения 0,5– 2 мм) имеет сложную пространственную форму с несколькими профилями сечений, изменяющимися на различной высоте лопаток от 50 до 500 мм. Каждое сечение имеет свои геометрические параметры (рис. 81) по длине b, по толщине сердцевины Cmах и кромок ∆П, по величинам радиусов кромок R1 и R2. Сечения профиля пера лопаток развернуты по его длине друг относительно друга на углы αзак до 90°
Y
|
b ± ∆b |
∆Пвых |
R2 |
|
|
||
|
|
|
|
R1 |
П |
∆Пк |
П |
∆Пвых |
|
∆Пс |
X |
|
|
||
Сmax |
|
|
|
Спинка пера
αзак
Корыто пера
Рис. 81. Конструктивные требования к аэродинамической точности профиля рабочих лопаток компрессора в одном сечении лопатки: ∆Пк – толщина кромок корыта; ∆Пс – толщина кромок спинки
180