
1496
.pdfПрименение пропитанных абразивных кругов на операции зубошлифования позволило снизить величину брака по прижогам
в2–3 раза (рис. 110, в), повысить стойкость абразивного инструмента
в1,4–1,8 раза и уменьшить в 1,2–1,3 раза шероховатость поверхности в сравнении со шлифованием непропитанными абразивными кругами.
Операция заточки фрез из быстрорежущей стали Р9К5, Р6М5Ф3 и др. осуществляется абразивными кругами характеристики 15А25-40 МЗ-СМ1К. Для повышения кромкостойкости круги бакелизируют. Однако режущая способность таких кругов снижается, и процесс сопровождается появлением прижогов. Разработанный комплексный состав позволяет, в зависимости от исходной характеристики, управлять в определенном диапазоне износостойкостью и режущей способностью абразивного инструмента. Это достигается путем изменения процентного содержания ПХАВ и ПМС в составе импрегнатора. Использование пропитанных кругов при заточке инструмента позволяет, как показали производственные испытания, исключить брак по прижогам, снизить шероховатость поверхности в 1,2–1,4 раза и повысить в 2,5–3,5 раза кромкостойкость кругов в сравнении с непропитанными. Всего за год водными растворами пропитано 1034 круга, что значительно меньше пропускной способности полуавтоматической установки для пропитки, созданной в ПНИПУ. Эта установка позволяет пропитать круги
диаметром до 350 мм весом до 6 кг с производительностью 30– 65 кг/ч.
Установка карусельного типа состоит из рамы, сваренной из уголков 40×40×3, и карусели, на раму установлены ванна и бак, изготовленные из листов нержавеющей стали 12Х18Н10Т. Между собой бак и ванна соединяются через поплавковый клапан, служащий для поддержания уровня импрегнатора в ванне в процессе работы установки. Карусельное колесо крепится в раме через подшипниковые корпуса. Торцовое биение колеса относительно стоек рамы регулируется с помощью перемещения подшипниковых корпусов и должно быть не более 2 мм. На колесо крепятся кронштейны, к которым под-
231
вешиваются подвески с абразивными кругами. Типоразмер подвесок зависит от размеров абразивных кругов.
Привод колеса осуществляется от двигателя постоянного тока через червячные редукторы. Двигатель и червячные редукторы крепятся на каретке, которая имеет возможность перемещаться в раме. Это необходимо в случае, когда потребуется изменить скорость вращения колеса с помощью изменения передаточного числа зубчатой пары и регулировки нового межосевого расстояния. Позиционирование колеса в процессе пропитки осуществляют через 90° с помощью конечного выключателя, установленного на стойке рамы.
Принцип работы установки. Импрегнатор приготавляется в специальной емкости и перекачивается в бак установки. Из бака импрегнатор через поплавковый клапан перетекает в ванну. По достижении определенного уровня импрегнатора в ванне клапан закрывается и поддерживается постоянный уровень раствора в ванне.
Предварительно подготовленные абразивные круги нанизываются на подвески и подвешиваются на колесо установки в «рабочей позиции». Подвески с абразивными кругами опускаются в импрегнатор со скоростью меньшей, чем скорость капиллярного всасывания. В самом нижнем положении подвески с кругами привод колеса отключается с помощью конечного выключателя. Время выключения привода регулируется с помощью реле времени. Во время паузы, когда абразивные круги выдерживаются в импрегнаторе, оператор в рабочей позиции подвешивает подвески с кругами или же заменяет подвески с пропитанными кругами. После паузы автоматически включается привод вращения колеса. Такой цикл продолжается до нажатия кнопки «стоп». После пропитки абразивных кругов оставшийся импрегнатор из ванны перекачивается в специальную емкость для хранения импрегнатора и дальнейшего повторного его использования. После слива балласта (оставшегося импрегнатора) бак и ванну необходимо промыть теплой водой.
Основные технические данные.
Максимальная производительность – 65 кг/ч. Тип привода – двигатель постоянного тока СЛ521.
232
Режимы работы установки:
непрерывное вращение колеса с числом оборотов 0,5–5 об/мин; дискретное вращение колеса с угловым шагом 90°; время выдержки колеса в позиции загрузки 0,3–3 мин.
Максимальный размер пропитанного инструмента – 350 мм. Форма кругов – Т, ПП, ЧЦ, ЧК.
Диапазон твердости пропитанного инструмента – ВМ1–СМ1; Тип крепления инструмента для пропитки – кассетный. Максимальная масса одной кассеты с инструментом – 10 кг. Емкость ванны для пропитки: минимальная – 30 л, максималь-
ная – 80 л.
Габариты установки – 1500×1300×90 мм. Масса – 120 кг.
Напряжение питания переменного тока – 220 В.
Увеличение количества пропитанных водными составами кругов возможно в случае внедрения пропитанных кругов при заточке лезвийного инструмента из быстрорежущих сталей. Предполагаемый объем пропитки 11 000 кругов в год.
Разработанная технология предполагает дифференцированную пропитку этих кругов водными составами в зависимости от их эксплуатационной характеристики (необходимости повысить или понизить твердость). Отсутствие надежных методов контроля твердости фасонных кругов типов 6 (ЧЦ), 11 (ЧК), 12 (Т) не позволяет осуществлять дифференцированную пропитку без предварительного опробования кругов в производственных условиях.
Дополнительный объем пропитываемого водными составами инструмента может возникнуть в случае положительного результата проводящегося в настоящее время исследования возможности использования при глубинном шлифовании пропитанных высокопористых кругов. Ориентировочный объем – до 1000 кругов в год. Пропиткой этих кругов можно регулировать их эксплуатационную твердость в пределах 2 звуковых индексов. В случае положительных результатов исследований для внедрения пропитки этих кругов потребуется спроектировать и изготовить оборудование для пропитки
233
кругов диаметром до 500 мм, а также использовать грузоподъемное оборудование, так как вес этих кругов достигает 30 кг.
Таким образом, применение пропитки шлифовальных кругов новыми пропиточными составами позволяет решать практически любые проблемы, возникающие при шлифовании твердых поверхностей деталей ГТД:
1)ликвидировать дефекты в виде шлифовочных прижогов и тре-
щин;
2)обеспечить минимальную величину шероховатости Rа =
=0,16 мкм;
3)повысить кромкостойкость кругов с радиусом кромки 0,2– 0,5 мм в 10–15 раз;
4)повысить производительность труда в 1,5–2 раза;
5)заменить на отдельных операциях круги из сверхтвердых материалов;
6)сократить отбраковку покупных кругов по твердости.
Кроме того, появилась реальная возможность управлять износостойкостью и режущей способностью абразивного инструмента и, в конечном счете, управлять самим процессом шлифования.
2.3. Применение новых абразивных материалов для интенсификации ленточного шлифования титановых сплавов
При обработке профиля пера титановых лопаток из сплавов ВТ3-1 и ВТ8-М применяются бесконечные водостойкие шлифовальные ленты типа ЛБ1 40…120×2400…3100 У1С 54С 40Н СФЖ (ГОСТ 13344–79) Белгородского абразивного завода, который превратился сегодня в единственного в России монопольного производителя отечественных шлифовальных лент. В то же время качество производимых на заводе лент неудовлетворительное для производства лопаток ГТД в авиастроении и в газотурбостроении из-за низкой их стойкости (2–4 обработанных лопаток одной лентой). Преждевременный съем лент со станка вызывается низкой режущей способно-
234
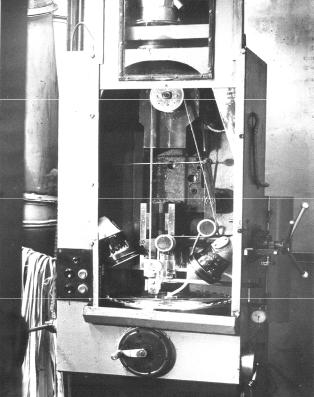
стью, засаливанием и сходом лент с роликов, значительным продольным их растяжением при работе. Прежде при ленточном шлифовании профиля пера лопаток из титановых сплавов ВТ3-1 и ВТ8-М на станках типа ПЛШ-9 и 3813Д использовались бесконечные ленты из карбида кремния зеленого и черного производства Запорожского абразивного комбината (ЗАК) (ТУ 2-036-853–80 с дополнительными условиями) (рис. 111). В связи с прекращением поставок бесконечных лент Украиной на ОАО «ПМЗ» перешли на поставку лент с Белгородского абразивного завода (БАЗ).
Рис. 111. Станок ПЛШ-9 для ленточного шлифования профиля пера лопаток компрессора
235
Была проведена дополнительная настройка станков на более высокую зернистость лент, уменьшено натяжение лент на 5–8 кг в сравнении с серийной настройкой.
Сопоставление лент Белгородского и Запорожского заводов показало, что стойкость лент БАЗ в 2–4 раза ниже стойкости лент ЗАК. Одной из причин низкой стойкости лент БАЗ является их сильное удлинение, приводящее к соскальзыванию с копира и появлению зарезов на полках и других дефектов лопатки, а также превышение величины шва над толщиной основы.
Механические испытания образцов лент ОАО «БАЗ» показали, что их разрывная нагрузка нестабильна и составляет 1250–1650 Н, удлинение лент при разрыве достигает 10 %, в то время как ленты производства ЗАК выдерживают разрывную нагрузку не менее 2070 Н, а удлинение лент при разрыве не более 8 %.
В связи с тем, что шлифование лопаток на окончательный размер производится только после приработки лент на первых двух лопатках, на которых оставляют припуск на окончательное шлифование приработанной лентой, при стойкости лент 1–2 лопатки их применение невозможно.
Для обеспечения качественного производительного ленточного шлифования необходимо повысить прочность лент ОАО «БАЗ», обеспечив разрывную нагрузку не менее 1666 Н, удлинение при разрыве не более 8 %, режущую способность по ГОСТ 27181. Остальные технические характеристики лент ОАО «БАЗ» также не должны уступать характеристикам лент ЗАК.
При посещении ОАО «БАЗ» выяснилось, что это связано с низким качеством поступающего с Волжского абразивного завода зерна из карбида кремния. Изменились и поставщики связующего СФЖ и тканевой основы. Например, прочность на разрыв поставляемой из Новосибирска саржи для тканевой основы в 1,5 раза меньше требуемой. Руководство ОАО «БАЗ» отказалось согласовать специальные ТУ для ОАО «ПМЗ». В связи с этим осуществлен поиск зарубежных поставщиков шлифовальных лент.
236

Известная немецкая фирма VSM предложила для обработки лопаток бесконечные шлифовальные ленты с вновь разработанным специальным абразивным зерном «Компакткорн». Компактное зерно VSM представляет собой крупные режущие частицы, состоящие из большого числа мелких зерен, соединенных между собой связующим материалом. Крупные зерна не разрушаются, как обычно на крупные частицы, а распадаются в процессе изнашивания на мелкие фрагменты путем отделения мелких зерен. При этом острота кромок и режущая способность зерен постоянно сохраняется, а срок службы инструментов из нового зерна многократно увеличивается (рис. 112).
Время шлифования
Рис. 112. Схема износа и микроразрушения компактного зерна фирмы VSM (Германия) при ленточном шлифовании
По контракту с фирмы VSM (Германия) получены бесконечные ленты с зерном «Компакткорн» следующих характеристик: 300×2400 (10 шт.), 300×3100 (10 шт.) СК 742 J Р80 (бесконечная лента из карбида кремния на ткани гибкой с компактным зерном № 25 для интенсивного шлифования металлов). Склейка шва «встык» под углом 80° с дополнительной соединительной упрочняющей пленкой на нерабочей стороне ленты. Производственные испытания проводились при обработке нескольких партий лопаток из титановых сплавов ВТ3-1 и ВТ8-М на ленточно-шлифовальных станках модели ПЛШ-9.
Припуск по перу под шлифование составлял 0,3...0,6 мм (отдельные точки до 0,8 мм). Требуемая шероховатость Rа ≤ 2,5 мкм, СОЖ – 1,5%-ная водная эмульсия.
При обработке партии лопаток из сплава ВТ3-1 одной лентой обработано 48 лопаток по корыту пера, а другой лентой 53 лопатки по спинке. Средняя стойкость опытных лент в 10–15 раз выше стой-
237
кости лент ОАО «БАЗ». Удлинение лент после обработки от 10 до 15 мм. Ленты порвались по основе вдоль и поперек направления нитей на ткани.
Толщина новых лент Н = 1,66 мм, толщина изношенной ленты со стороны спинки до Н = 0,83 мм, со стороны корыта Н = 0,53 мм. Шероховатость лопаток, обработанных опытной лентой, Rа = = 1,5...0,65 мкм.
Режимы обработки: скорость ленты V = 28 м/с;
количество качаний n = 80...95 кач/мин; подача на глубину врезания t = 0,01...0,15 мм/с; время обработки Т = 48 с.
Для обеспечения лучшего самозатачивания пришлось увеличить подачу на врезание. При этом время обработки сократилось на 30 %.
При обработке партии лопаток из сплава ВТ8-М стойкость лент VSM также выше в 6–10 раз, чем лент ОАО «БАЗ».
Три лопатки, обработанные опытными лентами, и три – серийными, отправили на исследование остаточных напряжений и наклепа. Оставшиеся лопатки обработали по технологии полностью. Из них три лопатки отправили на исследование остаточных напряжений
инаклепа, а остальные 25 шт. – на усталостные испытания для определения предела выносливости.
Врезультате анализа сравнительных исследований качества пера лопаток из титановых сплавов, обработанных опытной (VSM)
исерийной (БАЗ) бесконечными лентами, установлено:
1.Качество поверхности пера лопаток не ухудшилось, а стабильность обеспечения параметров качества повысилась. Остаточные напряжения, степень и глубина наклепа, шероховатость не ухудшились по сравнению с серийной обработкой.
2.Предел выносливости выдержан согласно ТУ.
Несмотря на высокую эффективность новых шлифовальных лент фирмы VSM c зерном «Компакткорн», экономический анализ показал, что затраты на приобретение импортных лент достаточно велики и часто не покрывают преимущества в более высокой стойко-
238
сти и сокращении расхода новых лент. Поэтому перед отечественными абразивными заводами необходимо поставить задачу по разработке и освоению технологии производства нового абразивного зерна типа «Компакткорн» и выпуску на его основе отечественных более дешевых, чем импортных, но более качественных высокоэффективных шлифовальных лент нового поколения.
Основные требования к изготовлению бесконечных шлифовальных лент из водостойкой шкурки для обработки профиля пера титановых лопаток следующие:
1.Бесконечные ленты (ЛБ) должны изготовляться с исполнением 1 класса А.
2.Размеры бесконечных лент: ширина лент В должна быть рав-
на 30, 38, 40, 42, 45, 48, 50, 55, 60, 70, 82, 85, 90, 95, 100, 105, 120 +
1,0 мм; длина Lном – 1900, 2400, 3000, 3100 + 3 мм.
Пример условного обозначения бесконечной шлифовальной ленты исполнения 1, шириной В = 120 мм, длиной L = 3100 мм, на ткани – сарже утяжеленной, из карбида кремния зеленого марки 63С, зернистость 40П (с повышенным содержанием зерна), на фенолформальдегидной смоле:
ЛБ1 120×3100 УГ 63С 40-П СФЖ СТУ...
3.Шлифовальная шкурка должна изготовляться из карбида кремния зеленого марки 63С или черного карбида кремния марки 54С зернистости 40П.
4.Химический состав карбида кремния черного и зеленого по ГОСТ 26327. Зерновой состав шлифзерна с индексом не ниже П по ГОСТ 3657.
5.Для изготовления шлифовальной шкурки должны применяться хлопчатобумажные ткани по ГОСТ 3357, ГОСТ 27181 (С2У) [4] .
6.Шлифматериал должен быть нанесен на одну из сторон аппретированной ткани-основы и прочно закреплен на ней связкой – формальдегидной смолой марок СФЖ-3038 или СФЖ-3039 по ГОСТ 20907.
239
7.Для повышения жесткости основы лента должна быть пропитана с обратной стороны аппретирующим составом.
8.На рабочей поверхности бесконечной ленты не допускаются морщины, складки, залитость связкой, площадки без зерен, повреждения кромок. Не допускаются изломы рабочего слоя бесконечных лент с повреждением основы.
9.Бесконечные ленты должны иметь обрезные кромки.
10.Не допускается более двух вырезов и разрывов длиной до 3 мм на кромках.
11.Разность длин кромок бесконечных лент не должна превышать 2 мм.
12.Неравномерность толщины шлифовальной шкурки должна быть 0,2 мм для зернистости 40.
13.Толщина шва бесконечных лент должна быть занижена на 0,2 мм не менее относительно толщины шкурки, из которой она изготовлена при склеивании шва внахлест. При склеивании шва встык занижение не требуется. Шов должен быть гладким, без дефектов на рабочей поверхности.
14.На бесконечной ленте не допускается сдвиг шва в поперечном направлении с образованием морщин, а также смещение тор-
цов [7].
15.Разрывная нагрузка и удлинение шлифовальной шкурки во влажном состоянии должна соответствовать значениям, указанным
вТУ.
16.Сопротивление разрыву шва бесконечных лент должно быть не менее сопротивления разрыву шлифовальной шкурки, из которой они изготовлены. Разрывная нагрузка ткани УГ, СУ2 в продольном направлении 1666 Н, в поперечном – 441 Н. (Образцы выдержать
вводе в течение 1 ч.)
17.Режущая способность бесконечных лент должна соответствовать режущей способности шлифовальной шкурки, из которой они изготовлены, и соответствовать значениям, указанным в ГОСТ 13344 (510 мм3/мин) и ГОСТ 27181 (258 мм3/мин) (для зернистости 40).
18.Коэффициент водостойкости 0,75.
240