
1496
.pdf
|
|
|
|
|
|
|
|
|
|
Таблица 3 |
|
|
|
Результаты входного контроля опытных кругов |
|
|
|||||
|
|
|
|
|
|
|
|
|
|
|
|
Обозна- |
Частота |
Звуко- |
Твердость по прибору |
Внутренний |
Высота |
Дисба- |
Плотность |
Относи- |
|
|
чение |
звуковых |
вой |
«Калибр» |
диаметр |
круга, мм |
ланс |
круга, |
тельный |
|
|
круга |
колебаний, |
индекс |
|
|
круга, мм |
|
(класс) |
г/см3 |
объем пор, |
|
Глубина |
Степень |
|
|||||||
|
|
кГц |
(ЗИ) |
лунки, |
твердости |
|
|
|
|
% |
|
|
|
|
мм |
|
|
|
|
|
|
|
|
|
|
|
|
|
|
|
|
|
41 |
Т |
1,59 |
35 |
6,2–6,7 |
М1 |
203,2–203,3 |
24,8–25,0 |
1 |
1,57–1,58 |
48,2 |
|
С |
1,54–1,56 |
34 |
7,0–7,1 |
ВМ2 |
203,2–203,3 |
23,7–24,3 |
1 |
1,59–1,62 |
43,6 |
|
Р |
1,45–1,47 |
32 |
7,1–8,5 |
ВМ1 |
203,5–203,7 |
24,8–25,0 |
2–3 |
1,62 |
45,7 |
|
К |
1,49–1,52 |
32–33 |
7,4–8,9 |
ВМ1 |
– |
24,9–25,6 |
2–3 |
1,67–1,71 |
50,6 |
|
Ф |
1,49–1,50 |
32–33 |
7,1–8,1 |
ВМ1-ВМ2 |
203,3-203,35 |
25,0–25,5 |
2–3 |
1,72–1,76 |
41,8 |
|
А |
1,78–1,82 |
39–40 |
4,9–5,2 |
М2 |
|
24,7–25,0 |
1 |
1,74–1,76 |
41,5 |
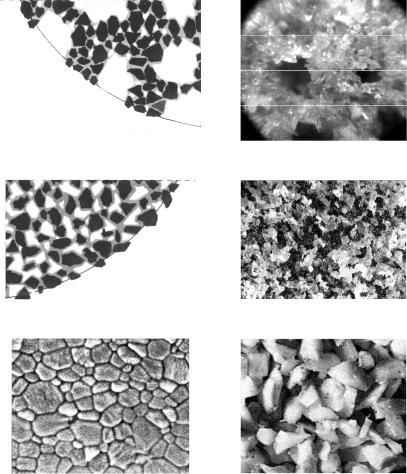
а
б
в
Рис. 19. Особенности применяемого зерна и распределения пор в кругах различных фирм: а – обычный высокопористый круг завода «Ильич»; б – высокопористый круг с мелкими равномерно распределенными порами фирмы «Тиролит»; в – зерна, изготовленные по SG-технологии (sol-gel)
фирмы «Нортон» (см. также с. 43)
42
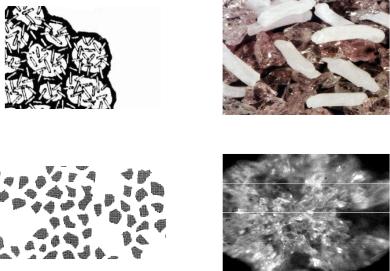
г
д
Рис. 19. Особенности применяемого зерна и распределения пор в кругах различных фирм: г – новейшая разработка фирмы «Нортон» – зерно TGX;
д– высокопористый круг фирмы «Тиролит» с двойной пористостью
•круги фирмы «ОАЗ ВНИИАШ» – нормальную твердость, неудовлетворительные параметры по геометрии, повышенный дисбаланс, нормальную пористость;
•круги фирмы «ЭКСИ» – среднюю твердость, значительные недостатки по точности геометрии, большой дисбаланс и хорошую пористость;
•круги фирмы «Ильич» – среднюю твердость, отклонение от допуска по внутреннему диаметру;
•круги фирмы «Атлантик» – высокую твердость, удовлетворительные геометрические параметры и дисбаланс, высокую плотность круга.
В процессе шлифования на типовых режимах резания определялся износ кругов после второго, четвертого и шестого проходов. Для этого лопатки снимались со станка и устанавливались на проек-
43
тор. На экране проектора измерялась разница между готовым профилем и фактическим на данном проходе. Результаты приведены в табл. 4.
|
|
|
|
|
|
|
|
|
Таблица 4 |
|
|
Результаты измерения износа кругов |
|
|
|
||||||
|
|
|
|
|
|
|
|
|||
Обозначение |
|
Износ круга по радиусу после проходов, мм |
||||||||
круга |
|
2 |
|
4 |
|
|
6 |
|||
К |
0,32 |
|
0,20 |
0,20 |
|
0,06 |
|
0,06 |
|
0 |
Т |
0,08 |
|
0,04 |
0,04 |
|
0,02 |
|
0 |
|
0 |
Р |
0,07 |
|
0,03 |
0,03 |
|
0 |
|
0 |
|
0 |
Ф |
0,08 |
|
0,03 |
0,03 |
|
0 |
|
0 |
|
0 |
А |
|
|
|
Износа нет |
|
|
|
|||
С |
|
|
|
Износа нет |
|
|
|
Анализ результатов показал, что круги С и А практически не имеют износа на четвертых лопатках, что можно объяснить повышенной твердостью кругов. Наибольший износ наблюдается у кругов К по радиусу первой впадины «елочного» профиля. Круги Т, Р, Ф имеют значительно меньший износ: до 0,03–0,08 мм.
Одновременно с измерением износа кругов проводилась запись тока нагрузки электродвигателей по проходам с помощью осциллографа Н115 на ленту УФ6. Изменение силы резания при шлифовании вызывает изменение потребляемой мощности привода шпинделя станка. Это изменение фиксировалось с помощью подключенных параллельно приборов. Результаты измерений показания прибора I от глубины tшл по проходам приведены на рис. 20.
Анализ графиков показал следующее, что с повышением глубины шлифования tшл нагрузка I на шпиндель двигателя станка возрастает из-за увеличения сил сопротивлению резанию.
Более твердые круги (Т, А, С) работают с большей нагрузкой, чем мягкие круги (К, Р, Ф). Интенсивность нарастания нагрузки I у твердых кругов (Т и А) по мере увеличения tшл больше, чем у мяг-
44

ких (К, Р, Ф). Твердые круги С работают как мягкие. Круги Т и А имеют более интенсивное увеличение нагрузки из-за интенсивного изнашивания зерна и разрушаются в процессе обработки, у остальных же кругов (С, К, Р, Ф) происходит процесс самозатачивания.
18 |
|
|
|
|
|
I , мА |
Т |
А |
С |
К |
|
16 |
|||||
|
|
|
Р |
||
14 |
|
|
|
||
|
|
|
Ф |
||
12 |
|
|
|
||
|
|
|
|
||
10 |
|
|
|
|
|
8 |
|
|
|
|
|
6 |
|
|
|
|
|
4 |
|
|
|
|
|
2 |
|
|
|
|
|
0 |
|
|
|
|
|
|
0 |
0,05 |
|
0,1 |
|
|
|
|
|
t шл, мА |
Рис. 20. Изменение мощности шлифования I в зависимости от глубины шлифования tшл
Таким образом, с позиции обеспечения высокой режущей способности, наименьшего износа и высокой стойкости более предпочтительны круги фирмы «Экоабразив» (С), «Атлантик» (А) и «Тиролит» (Т).
После обработки вырезались образцы из первой и четвертой лопаток по ходу шлифования для исследования параметров качества поверхностного слоя: шероховатости поверхности, микротвердости и остаточных напряжений. Остальные лопатки проходили дальнейшую обработку замка, термообработку и упрочнение.
Шероховатость поверхности замка измерялась на микроскопе МИС11, рисочность определялась на растровом электронном микроскопе, микротвердость – на приборе ПМТ-2. Результаты приведены в табл. 5.
45
Таблица 5 Результаты исследования качества поверхности замков лопаток
Обозна- |
Шерохо- |
Микротвердость |
Глубина |
Степень |
||||
НВ, кгс/мм2 |
наклепа h, мкм |
наклепа H, % |
||||||
чение кру- |
ватость |
|
|
|
|
|
|
|
1-я |
4-я |
1-я |
4-я |
1-я |
4-я |
|||
га |
Ra, мкм |
|||||||
|
|
лопатка |
лопатка |
лопатка |
лопатка |
лопатка |
лопатка |
|
Т |
0,61 |
540 |
550 |
15 |
20 |
40,0 |
42,5 |
|
|
|
|
|
|
|
|
|
|
С |
0,61 |
530 |
555 |
15 |
15 |
39,1 |
43,1 |
|
Р |
0,66 |
585 |
615 |
10 |
20 |
42,0 |
49,3 |
|
|
|
|
|
|
|
|
|
|
К |
0,67 |
610 |
625 |
10 |
15 |
43,0 |
47,3 |
|
|
|
|
|
|
|
|
|
|
Ф |
0,67 |
615 |
585 |
10 |
25 |
43,4 |
33,7 |
|
А |
0,37 |
645 |
645 |
20 |
30 |
53,4 |
53,4 |
|
|
|
|
|
|
|
|
|
Наименьшая величина шероховатости Ra = 0,37 мкм наблюдается при обработке кругами А, имеющими наибольшую твердость. При обработке остальными кругами шероховатость практически не меняется (Ra = 0,61...0,67 мкм). Меньшая шероховатость при обработке более твердыми кругами объясняется постепенным износом наиболее выступающих режущих зерен круга, работающего в режиме засаливания. Более мягкие круги работают в режиме самозатачивания, выкрашивания абразивных зерен. Наибольшая глубина наклепа наблюдается при обработке кругами Р, А и Ф. Причем с увеличением износа этих кругов глубина наклепа может увеличиться в 1,5–2,0 раза. Наименьшие глубина и степень наклепа наблюдаются при обработке кругами С (фирма «Экоабразив»).
Остаточные напряжения определялись по методу Давиденкова на приборе «Пион-2». Характер распространения остаточных напряжений σост по глубине поверхностного слоя показан на рис. 21.
Наиболее благоприятный характер распределения остаточных напряжений имеют круги С, так как у них градиент остаточных напряжений в тонком поверхностном слое меньше, чем у твердых
46
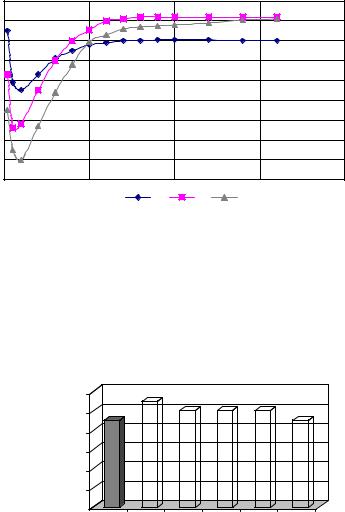
σост , кг/мм2 |
|
|
|
|
20 |
|
|
|
|
10 |
|
|
|
|
0 |
|
|
|
|
-10 0 |
50 |
100 |
150 |
200 h , мкм |
-20 |
|
|
|
|
-30 |
|
|
|
|
-40 |
|
|
|
|
-50 |
|
|
|
|
-60 |
|
|
|
|
-70 |
|
|
|
|
|
Ф |
С |
А |
|
Рис. 21. Изменение остаточных напряжений σост по глубине поверхностного |
||||
|
слоя h при обработке разными кругами |
|
кругов, и остаточные напряжения переходят в зону растяжения на поверхности так же, как у мягких кругов.
Результаты усталостных испытаний замков лопаток, прошлифованных различными кругами (рис. 22) показывают, что требуемый предел усталостной прочности σ–1 = 110 МПа (11 кгс/мм2) обеспечивают только круги С.
σ–1, |
12 |
|
11 |
10 |
10 |
10 |
кгс/мм2 |
|
|
||||
|
10 |
9 |
|
|
|
9 |
8
6
4
2
0
А |
С |
Т |
Р |
К |
Ф |
Круги
Рис. 22. Гистограмма результатов усталостных испытаний лопаток
47
Оценка экономической эффективности от замены кругов Ф (завод «Ильич») новыми кругами различных фирм проведена с учетом стойкости кругов (коэффициента расхода). Результаты приведены в табл. 6.
|
|
|
|
|
Таблица 6 |
|
Эффективность замены серийных кругов Ф |
|
|||
|
|
|
|
|
|
Обозначе- |
Цена круга, |
Коэффициент |
Годовой |
Годовые |
Экономия |
ние круга |
руб. |
расхода |
расход |
затраты, |
затрат, |
|
|
|
|
тыс. руб. |
тыс. руб. |
Р |
307–48 |
1,65 |
638 |
196,2 |
–26,0 |
К |
114–78 |
1,50 |
638 |
73,0 |
– |
С |
326–00 |
0,75 |
319 |
104,0 |
+67,0 |
Т |
720–00 |
1,00 |
425 |
306,0 |
– |
А |
1000–80 |
1,00 |
425 |
425,3 |
–255,0 |
Ф |
401–54 |
1,00 |
425 |
170,7 |
– |
Анализ рис. 22 и табл. 6 позволяет сделать вывод, что круги С (фирма «Экоабразив») обеспечивают максимальную усталостную прочность замка при обработке. Кроме того, и с экономической точки зрения они выгоднее кругов Ф завода «Ильич». Таким образом, наиболее оптимальными шлифовальными кругами, отвечающими требованиям производства, признаны круги фирмы «Экоабразив» (г. Москва).
На фирме «Экоабразив» разработан принципиально новый вид абразивного инструмента – высокопористый инструмент с закрытой структурой, который имеет более широкие эксплуатационные возможности, чем круги с открытой структурой. Новая технология основана на применении невыгорающих порообразователей при изготовлении абразивной массы, что обеспечивает экологическую чистоту производства, позволяет получать круги более высокой твердости со стабильными физико-механическими свойствами. А качество кругов для глубинного шлифования, как уже отмечалось, является ре-
48
шающим фактором обеспечения требуемого качества и усталостной прочности деталей. Установлено, например, что увеличение зернистости кругов снижает градиент сжимающих напряжений и повышает усталостную прочность. Увеличение скорости алмазного ролика с 9 до 18 м/с при правке кругов для глубинного шлифования снижает ∆σсж с –810 до –320 МПа. Увеличение подачи алмазного правящего ролика с 1 до 3 мкм/10 об. круга приводит к снижению ∆σсж с –350 до –70 МПа, что также является благоприятным фактором.
Таким образом, в результате широких комплексных исследований процесса глубинного шлифования «елочных» замков турбинных лопаток установлены основные причины появления дефектов и снижения усталостной прочности деталей. Назначение оптимальных режимов шлифования и правки (9 проходов для лопаток из сплавов ЖС6К и ЖС6УВИ, 14 проходов для лопаток из сплавов ЖС26, ЖС32, ЧС70), выбор наиболее эффективных шлифовальных кругов (С, Т), обеспечение невысокого градиента сжимающих остаточных
напряжений σост = 250...350 МПа на глубине 5–10 мкм, снижение рисочности поверхности и другие мероприятия позволили стабилизи-
ровать процесс глубинного шлифования, обеспечили получение требуемых параметров качества и предела усталостной прочности замков лопаток турбин различных ГТД.
Дальнейшее развитие процесса глубинного шлифования будет идти по пути использования новых скоростных шлифовальных кругов и скоростных шлифовальных станков с ЧПУ нового поколения.
Определение теплового баланса. В процессе профильного глу-
бинного шлифования, как и при любом другом виде механической обработки, практически вся механическая энергия, направленная на резание и деформирование слоев металла, переходит в тепловую энергию контактирующих тел. В соответствии с законом сохранения энергии математическое выражение баланса механической и тепловой энергии принимает вид
PVz к =Q =Qдет +QСОЖ +Qc +Qк,
49
где Q – общее количество выделившегося тепла, Вт; Qдет – тепловой поток, направленный в деталь, Вт; QСОЖ – количество тепла, отводимое охлаждающей жидкостью, Вт; Qc – количество тепла, уносимое стружкой, Вт; Qк – количество тепла, направленное в зерна
и связку шлифовального круга.
При профильном глубинном шлифовании высокопористыми кругами с гидродинамическим способом подачи СОТС, теплоотдача с обработанной поверхности имеет большое значение. Однако непосредственно в зону резания попадает меньшее количество охлаждающей жидкости, тем более, что при температурах свыше 100– 150 °С наблюдается процесс пузырькового и пленочного кипения. Чтобы эффективно охлаждать зону контакта при профильном глубинном шлифовании, применяют гидродинамическую подачу охлаждающей жидкости под давлением свыше 0,7 МПа, чтобы пробить воздушный поток от шлифовального круга и доставить жидкость в зону контакта.
Большим количеством исследователей установлено, что при глубинном шлифовании значительная часть тепла распределяется между деталью и охлаждающей жидкостью. Исследователи Аутвотер, Зауэр и др. [36] определили, что около 30 % работы сдвига в процессе стружкообразования идет на нагрев детали. Однако разные исследователи утверждают, что количество тепла, направленного в деталь, составляет 30–80 %. Вопрос определения теплового баланса, как расчетным путем, так и экспериментальным, представляет сложную задачу, которую решали различными путями, поэтому долю тепла, поступающего в деталь для профильного глубинного шлифования, было решено определить экспериментально. Для этого проведено препарирование замков лопаток турбин искусственными термопарами с подведением точки измерения (спая) под первую впадину «елочного» профиля (рис. 23). Запись значений силы и температуры при глубинном шлифовании проводилась на пленку шлейфового осциллографа Н115 с помощью специального стенда
(рис. 24).
50