
1496
.pdf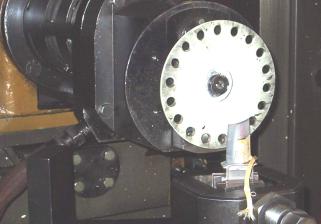
в
Рис. 9. Окончание
контакта на 0,9–1,0 мм по первой впадине «елочного» профиля, испытывающей максимальную нагрузку. За предел выносливости принято максимальное напряжение, заданное по тензорезистору № 1, соответствующее наработке базы 20·106 циклов, при котором не разрушилось 6 лопаток. При разрушении хотя бы одной лопатки проводилось повторное испытание, но уже партии из 25 лопаток. В этом случае определяется действительный предел выносливости σ–1 лопаток турбин. Если σ–1 фактически оказывается ниже допустимого, то данный технологический процесс считается нестабильным и разрабатываются мероприятия по повышению его стабильности и увеличению предела усталостной прочности до необходимого значения.
В результате проведенных многочисленных исследований установлено, что на сопротивление усталости хвостовиков лопаток влияют следующие факторы:
• условия глубинного шлифования: качество абразивного инструмента и алмазных правящих роликов, состояние станка и оснастки, тип, концентрация и условия подачи и очистки СОЖ, режимы шлифования и правки кругов;
21
•последующая обработка: торцовых поверхностей, радиусов на торцах, обдувка поверхности профиля микрошариками и гидроабразивом, диффузионный отжиг;
•качество, точность литья и точность изготовления «елочного» профиля относительно охлаждаемого канала;
•условия проведения усталостных испытаний и др.
Все перечисленные факторы в процессе глубинного шлифования действуют в той или иной мере одновременно, накладываясь друг на друга. Одним из главных факторов, существенно влияющих на сопротивление усталости хвостовика, является высокопористый абразивный инструмент. В процессе проведения испытаний установлено, что высокое качество поверхностного слоя и требуемое значение предела выносливости лопаток ГТД обеспечивается применением соответствующего высококачественного инструмента. Вместе с тем, сравнительные усталостные испытания турбинных лопаток, обработанных высокопористым абразивным инструментом разных фирм на воздушно-пульсирующем стенде при колебаниях по первой изгибной форме с симметричным циклом напряжений при базе испытаний 20 106 циклов является дорогостоящим, низкопроизводительным и обладающим большой трудоемкостью методом определения выбора рационального абразивного инструмента. Кроме того, при анализе результатов усталостных испытаний лопаток очень трудно выделить ту составляющую из всех действующих факторов, которая непосредственно зависит от качества испытываемого круга.
В связи с этим была разработана и реализована методика ускоренного испытания высокопористых кругов для глубинного шлифования хвостовиков лопаток. Разработанная методика включает в себя следующие этапы:
1. Проектирование и изготовление специальных образцов для усталостных испытаний. Специально была спроектирована и изготовлена пресс-форма для получения отливок образцов из сплава ЖС26 по выплавляемым моделям методом направленной кристаллизации по технологии отливки серийных лопаток турбин (рис. 10).
22
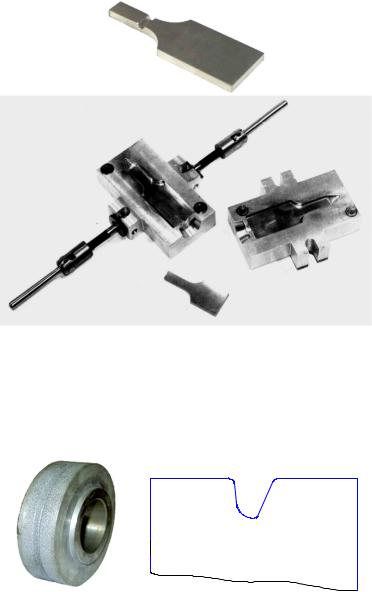
Рис. 10. Пресс-форма для изготовления модели образца
иобразец для усталостных испытаний
2.Проектирование и изготовление алмазного ролика для правки шлифовальных кругов в процессе шлифования, за основу взят профиль первого паза «елочного» замка турбинной лопатки двигателя ПС-90А, эскиз алмазного профиля ролика приведен на рис. 11.
Рис. 11. Профиль специального алмазного ролика для шлифования канавки первой впадины «елочного» профиля замка лопатки
23
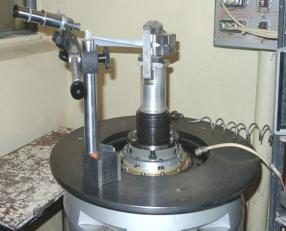
3.Проектирование и изготовление приспособления для установки и закрепления образцов на столе станка ЛШ-220.
4.Глубинное шлифование профильной канавки образцов различными кругами на различных режимах.
5.Усталостные испытания образцов на электродинамическом вибростенде.
6.Сравнение результатов усталостных испытаний образцов, обработанных различными кругами.
Применение данной методики при испытании новых шлифовальных кругов вместо прежней методики испытаний серийных деталей обладает следующими преимуществами:
1)снижение затрат на испытания, так как вместо деталей используются специальные образцы;
2)отсутствие загрузки станка SS13L, используемого в серийном производстве, так как обработка образцов производится на специальном плоскошлифовальном полуавтомате с ЧПУ ЛШ-220;
3)отсутствие загрузки воздушно-пульсирующего стенда, так как при усталостных испытаниях образцов используется электродинамический стенд (рис. 12);
Рис. 12. Усталостные испытания образцов на электродинамическом стенде
24
4)сокращение времени испытаний на 50 %;
5)более высокая точность и достоверность результатов испытания образцов по сравнению с испытанием лопаток и оценка непосредственного влияния отдельных характеристик шлифовального инструмента на сопротивление усталости обработанных образцов.
Помимо дополнительных усталостных испытаний образцов лопаток турбин в случае снижения предела усталостной прочности проводится контроль макро- и микроструктуры, остаточных напряжений и наклепа поверхностного слоя, анализ химического состава материала лопаток. Анализ результатов исследований остаточных напряжений и наклепа позволяет судить о термодинамических процессах, происходящих в поверхностном слое обработанных деталей,
иих влиянии на изменение усталостной прочности. При решении проблемы обеспечения требуемого качества и усталостной прочности замков простое копирование процесса глубинного шлифования согласно разработкам ОАО «Рыбинские моторы» и рекомендациям Научно-исследовательского института двигателестроения (НИИД, г. Москва) оказалось невозможным в связи с более жесткими требованиями к качеству в ОАО «Пермский моторный завод», чем на других предприятиях отрасли.
Предварительные исследования показали существенную зави-
симость σ–1 от основных параметров шлифования. Различные параметры глубинного шлифования влияют на шероховатость, наклеп и величину градиента остаточных напряжений в тонком поверхностном слое замков лопаток, которые, в свою очередь, влияют на величину σ–1. Первоначально отрабатывались режимы шлифования импортными высокопористыми кругами из белого электрокорунда характеристики 89А 100 G211 А V фирмы «Тиролит» (Австрия). Исследованы рекомендованные НИИД режимы глубинного шлифования Р1, Р2, Р3 «елочного» профиля хвостовиков лопаток из жаропрочных никелевых сплавов ЖC6К и ЖС6УВИ с предварительной обработкой клина (табл. 1).
25
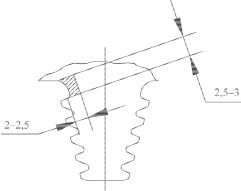
Таблица 1
Режимы глубинного шлифования с предварительной обработкой клина
Режим |
Но- |
Скорость |
Ско- |
Глубина |
Глуби- |
Предел |
Время |
|
мер |
круга, |
рость |
шлифова- |
на |
выносли- |
обработки, |
|
про- |
м/с |
стола, |
ния, мм |
правки, |
вости, |
мин |
|
хода |
|
мм/мин |
|
мм |
МПа |
|
|
1 |
25 |
120 |
1,9–2,1 |
0,15 |
|
|
Р1 |
|
|
|
|
|
80 |
12,5 |
2 |
25 |
150 |
0,2 |
0,15 |
|||
|
3 |
30 |
200 |
0,05 |
– |
|
|
|
|
|
|
|
|
|
|
|
1 |
25 |
50 |
1,9–2,1 |
0,15 |
|
|
Р2 |
|
|
|
|
|
90–100 |
15 |
2 |
25 |
150 |
0,2 |
0,15 |
|||
|
3 |
30 |
200 |
0,05 |
– |
|
|
|
|
|
|
|
|
|
|
|
1 |
27 |
50 |
1,9–2,1 |
0,15 |
|
|
Р3 |
|
|
|
|
|
90 |
18,5 |
2 |
27 |
100 |
0,09 |
0,15 |
|||
|
3 |
27 |
100 |
0,05 |
– |
|
|
|
|
|
|
|
|
|
|
Для исследования остаточных напряжений, наклепа и шероховатости поверхности замков лопаток после глубинного шлифования вырезались образцы электроэрозионным способом по схеме на рис. 13.
Рис. 13. Схема вырезки образца для исследования шероховатости, остаточных напряжений и микротвердости
26
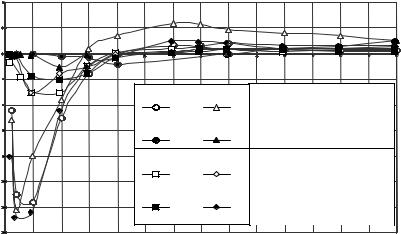
Результаты исследования характера распределения осевых остаточных напряжений в замке лопатки из сплава ЖС6УВИ представлены на рис. 14. После шлифования в тонком поверхностном слое замков на глубине 25–40 мкм наводятся сжимающие остаточные напряжения с максимумом 180–650 МПа на глубине 5–15 мкм. Эти напряжения переходят в небольшие растягивающие 50–100 МПа на глубине 25–40 мкм. После механической обработки лопатки турбин проходят термообработку (отжиг) для снятия напряжений. На рисунке видно, что после отжига величина остаточных напряжений уменьшается до –20–150 МПа. Для повышения усталостной прочности замков лопаток турбин после глубинного шлифования и отжига предложено ввести дополнительную операцию: обдувку замков стальными микрошариками на специальной дробеметной установке.
σо, МПа |
|
|
|
|
|
|
|
|
|
|
|
|
|
|
200 |
|
|
|
|
|
|
|
|
|
|
|
|
|
|
100 |
|
|
|
|
|
|
|
|
|
|
|
|
|
|
0 |
|
|
|
|
|
|
|
|
|
|
|
|
|
|
–100 |
|
|
|
|
|
|
|
|
|
шлифованные |
|
|
||
|
|
|
|
|
|
|
|
|
|
|
|
|||
–200 |
|
|
|
|
|
|
|
|
со стороны спинки |
|
|
|||
–300 |
|
|
|
|
|
|
|
|
со стороны корыта |
|
|
|||
|
|
|
|
|
|
|
|
|
|
|
||||
–400 |
|
|
|
|
|
|
|
|
|
отожженные |
|
|
||
–500 |
|
|
|
|
|
|
|
|
со стороны спинки |
|
|
|||
|
|
|
|
|
|
|
|
|
|
|
|
|
|
|
–600 |
|
|
|
|
|
|
|
|
со стороны корыта |
|
|
|||
–700 |
|
|
|
|
|
|
|
|
|
|
|
|
|
|
0 |
10 |
20 |
30 |
40 |
50 |
60 |
70 |
80 |
90 |
100 |
110 |
120 |
130 |
140 |
|
|
|
|
|
|
|
|
|
|
|
|
|
h, мкм |
|
|
Рис. 14. Распределение остаточных напряжений σо по глубине h |
|
||||||||||||
поверхностного слоя после глубинного шлифования и отжига (ЖС6УВИ) |
27
Врезультате остаточные напряжения сжатия вновь возросли
исоставили для времени упрочнения 3 мин 280–400 МПа, а для времени упрочнения 15 мин 310–600 МПа. Глубина залегания сжимающих напряжений увеличилась до 50–80 мкм, затем на глубине 140 мкм остаточные напряжения переходят в растягивающие (до 80– 200 МПа). Сравнительное исследование усталостной прочности замков лопаток и образцов-имитаторов «елочного» замка из сплава
ЖС6УВИ, проведенное как в ОАО «Пермские моторы», так и в Центральном институте авиационного моторостроения (ЦИАМ) при нормальной (293 К) и рабочей температуре (923–973 К), показало, что упрочнение микрошариками повышает предел выносливости на 25–60 % по сравнению с неупрочненными деталями. В результате упрочнения предел выносливости σ–1 повысился до 110–120 МПа, что еще недостаточно для серийного производства лопаток из сплава
ЖС6УВИ. После глубинного шлифования глубина |
наклепа |
h = |
||
= 20...30 |
мкм, |
а степень наклепа Н = 19...24 %, |
после отжига |
|
h = 9...14 |
мкм, |
Н = 5...20 %, после упрочнения h |
= 10...20 |
мкм, |
Н = 14,1 %.
После усталостных испытаний проводилось исследование замков лопаток, не выдержавших испытаний. Анализ места расположения и микроструктуры трещин в замках лопаток показал (рис. 15), что большинство трещин носит усталостный характер. Одни трещины идут под углом 30° к наружной поверхности, а другие – вглубь металла под прямым углом. Обнаружены трещины и во внутренней полости замка лопатки, в алитированном слое после глубинного шлифования. Причем протяженность этих трещин достигала
9–12 мм, а глубина 0,1–0,4 мм.
Излом по трещине представляет собой несколько площадок усталостных внутрикристаллических сколов, расположенных под углом 45° к основанию первой впадины замка. Преимущественное ориентирование усталостной трещины идет от основания первого зуба, далее в результате перераспределения напряжений образуются крупнокристаллические сколы.
28
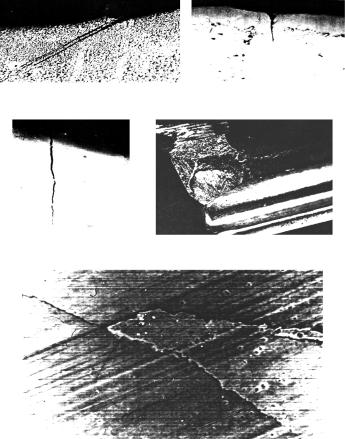
×300 |
×300 |
×300 |
×6 |
×650
Рис. 15. Типичный характер трещинообразования в поверхностном слое обработанных глубинным шлифованием «елочных» замков лопаток после усталостных испытаний
Дефектов материала в изломе не обнаружено. Исследование шероховатости поверхности первого паза «елочного» замка лопатки на растровом микроскопе РЭМА-202 (рис. 16) и на профилографепрофилометре М1 выявило продольные риски различной ширины и глубины вдоль паза, оставленные зернами высокопористого шли-
29
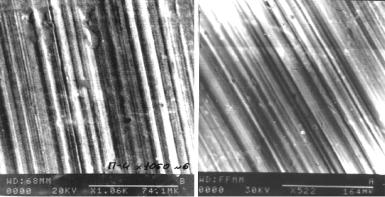
фовального круга. Трещины в пазу местами совпадают с этими острыми глубокими рисками, а местами идут под углом 45–60° к ним. Наиболее эффективным путем повышения предела выносливости «елочных» замков лопаток и сохранения требуемой производительности является плавное снижение глубины шлифования по проходам за счет увеличения числа проходов с одновременным повышением скорости стола. Уменьшение глубины шлифования tшл снижает составляющие силы резания Рz и Ру, а увеличение скорости детали способствует некоторому повышению температуры в зоне резания.
Рис. 16. Общий вид характерной рисочности поверхности хвостовиков лопаток турбин после глубинного шлифования
В результате уменьшается действие силового фактора на формирование высокого градиента сжимающих напряжений в тонком (5–10 мкм) поверхностном слое. Так, при уменьшении глубины шлифования с 0,6 до 0,02 мм величина усилия резания Ру снижается с 720 до 200 кН при скорости детали 100 мм/мин. При скорости детали 500 мм/мин это снижение еще больше: с 850 до 190 кН. Увеличение скорости детали с 100 до 500 мм/мин при глубине окончательного шлифования 0,02 мм приводит к повышению средней температуры контакта с 573 до 773 К, что снижает градиент высоких сжимающих напряжений и создает более благоприятный для устало-
30