
1496
.pdfстной прочности характер их распределения по глубине поверхностного слоя.
При увеличении скорости детали со 100 до 2000 мм/мин величина микронеровностей увеличивается незначительно: с 0,63 до 1,25 мкм, что не должно сказаться существенно на снижении σ–1. Степень наклепа в этом случае повышается также незначительно: с 35 до 42 %, а глубина наклепа не изменяется. В связи с этим при оптимизации процесса были опробованы режимы с увеличенными числом проходов и скоростью детали (табл. 2). При использовании импортных кругов лучшие результаты были получены на шестипроходном шлифовании Р4 без предварительной обработки клина хвостовика лопаток.
Таблица 2
Режимы глубинного шлифования без предварительной обработки клина (СОЖ: 3–8%-ная эмульсия Аквол-6 или Пермол-6)
Ре- |
Изготови- |
Номер |
Скорость |
Скорость |
Глубина |
Предел |
Время |
жим |
тель круга |
прохода |
круга, м/с |
стола, |
шлифова- |
выносли- |
обра- |
|
|
|
|
мм/мин |
ния, |
вости, |
ботки, |
|
|
|
|
|
мм |
МПа |
мин |
Р4 |
Тиролит |
1,2 |
20–25 |
250–300 |
0,7–2,2 |
|
|
|
(Австрия) |
3,4 |
20 |
300 |
0,3–0,45 |
150 |
14 |
|
|
5,6 |
20–25 |
300 |
0,025–0,125 |
|
|
Р5 |
Ильич |
1–3 |
25 |
250–350 |
0,5–1,8 |
|
|
|
(С.-Петер- |
4–6 |
20 |
350 |
0,15–0,4 |
160 |
15 |
|
бург) |
|
|
|
|
|
|
|
7–9 |
20–25 |
350 |
0,02–0,08 |
|
|
|
|
|
|
|
||||
Р6 |
Ильич |
1–3 |
25 |
500 |
0,5–1,8 |
160 |
12 |
|
(С.-Петер- |
4–6 |
20 |
500 |
0,15–0,4 |
|
|
|
бург) |
|
|
|
|
|
|
|
7–9 |
20–25 |
500 |
|
|
|
|
|
|
|
|
|
При использовании трехпроходного режима обе плоскости клина хвостовика обычно предварительно шлифуются с обеспечением припуска по вершинам «елочного» профиля в пределах 0,25–0,35 мм. При исключении предварительного шлифования припуск по верши-
31
нам «елочного» профиля составляет 1–2 мм. Усталостные испытания лопаток, обработанных кругами фирмы «Тиролит» на шестипроходных режимах глубинного шлифования Р4 с тремя правками, показали, что предел выносливости замков лопаток составляет 150 МПа, что вполне удовлетворяет техническим требованиям. Статистический анализ и математическая обработка результатов методом планирования экспериментов позволили вывести следующую зависимость предела выносливости от режимов шлифования сплавов ЖС6К и ЖС6УВИ кругами фирмы «Тиролит» (Австрия):
σ−1 |
= |
Vдет0,22Vк0,3 |
, |
|
tср |
||||
|
|
|
где Vдет – скорость детали, мм/мин; Vк – скорость круга, м/с; tср – средняя глубина шлифования; tср = ∆t/n; ∆t – общий припуск, мм; n – число проходов.
Как показывает эта зависимость, с увеличением скорости детали Vдет, скорости круга Vк, числа проходов n и уменьшением глубины шлифования tср предел выносливости σ–1 увеличивается. Приведенная зависимость действительна для условий шлифования «елочно-
го» профиля кругами фирмы «Тиролит» Vк = 15...25 м/с, Vдет = = 100...500 мм/мин, tср = 0,6...0,8 мм.
Таким образом, подбор оптимальных соотношений Vк, Vдет, tср позволяет оптимизировать процесс глубинного шлифования на основе обеспечения требуемого предела выносливости σ–1 и максимальной производительности обработки.
В связи с этим на станках SS13L был впервые в ОАО «Пермские моторы» внедрен процесс шестипроходного глубинного шлифования «елочных» профилей хвостовиков лопаток из сплавов ЖС6УВИ и ЖC6К на режиме Р4 (см. табл. 2) импортными кругами. Цикл обработки составил 14 мин (на 4 лопатки), что привело к снижению трудоемкости в 4 раза по сравнению с фрезерованием, позволило высвободить 16 фрезерных станков, 22 фрезеровщика.
32
Ввиду того, что импортные круги, поставленные вместе со станками фирмой «Элб-Шлифф», через некоторое время закончились, проведены работы по внедрению отечественных высокопористых кругов. Испытаны высокопористые круги завода «Ильич» 3П 500×20
...25×203 25А 10П ЗИ 31–32 12 К5 П40-15. Установлено, что лопатки,
прошлифованные этими кругами на шестипроходном режиме Р4 (см. табл. 2), имеют предел выносливости только 130 МПа, что меньше допустимого. Снижение предела выносливости «елочных» замков лопаток при использовании отечественных кругов по сравнению с импортными может быть объяснено большим ростом силы резания в зоне шлифования, что, по-видимому, связано с меньшей (в 1,5 раза) пористостью кругов, худшим качеством зерна и связки, неравномерностью их распределения в круге и большим дисбалансом.
Так, токовая нагрузка электродвигателей при использовании отечественных кругов выше, чем при использовании импортных на 8–15 %, причем большее ее возрастание наблюдается при шлифовании четвертой лопатки, что указывает на интенсивное затупление (засаливание). При использовании более мягких отечественных кругов характеристики 25А 10П ЗИ 29–30 12 К5 П40-15 не удалось обеспечить требуемую точность «елочного» профиля ввиду катастрофически быстрого осыпания кругов.
С целью обеспечения требуемого предела выносливости лопаток при шлифовании отечественными кругами характеристики 25А 10П ЗИ 31–32 12 К5 П40-15 выбран наиболее рациональный режим девятипроходного шлифования Р5 с четырьмя правками (см. табл. 2). При шлифовании «елочных» профилей на этом режиме предел выносливости «елочных» замков лопаток достигает 160 МПа. За счет большего числа проходов, более высокой скорости стола и уменьшения глубины шлифования устранено интенсивное засаливание кругов, в результате этого получено идентичное качество всех прошлифованных лопаток. Время цикла при шлифовании «елочных» профилей отечественными кругами на девятипроходном режиме Р5 составило 15 мин (на 4 лопатки), что позволило внедрить отечест-
33

венные круги вместо импортных практически без потери производительности.
Отработанный режим девятипроходного глубинного шлифования Р5 обеспечивает хорошее качество поверхностного слоя и высокую надежность «елочных» хвостовиков только при использовании кругов в узком диапазоне твердости – звуковой индекс ЗИ 31–32. Однако технология производства на заводе «Ильич» не позволяет получать круги в таком диапазоне твердостей. При использовании более твердых кругов (ЗИ 33–34) на режиме Р5 предел выносливости «елочных» замков лопаток составлял только 130 МПа, что меньше требуемого. Причиной снижения предела выносливости в данном случае является повышенная засаливаемость кругов. С целью уменьшения засаливаемости этих кругов был отработан режим Р6 с повышенной до 500 мм/мин скоростью стола (см. табл. 2). Предел выносливости «елочных» замков лопаток в этом случае составил
160 МПа.
Таким образом, увеличение числа проходов с плавным снижением глубины шлифования позволяет повысить предел выносливости замков лопаток турбин. На рис. 17 изображена гистограмма
Рис. 17. Гистограмма изменения предела выносливости σ–1 замков лопаток турбины, обработанных за различное число проходов при шлифовании
34
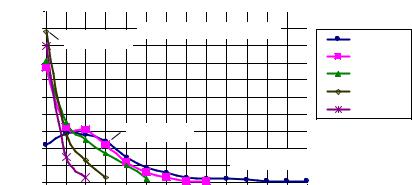
изменения σ–1 в зависимости от числа проходов, построенная по результатам экспериментальных исследований. С увеличением числа проходов от 3 до 14 предел выносливости σ–1 удалось увеличить практически в 1,5–2 раза.
Для анализа интенсивности изменения нагрузки на шпиндели шлифовальных станков и обрабатываемые детали в зависимости от глубины шлифования и числа проходов в процессе глубинного шлифования производилась запись нагрузки, действующей на оба шпинделя станка SS13L, с помощью датчиков станка и осциллографа Н115 на ленту УФ последовательно на всех 14 проходах. Кроме того, с помощью специального пакета программ «Юниграфикс» на рабочих станциях ЭВМ «Индиго 2» фирмы «Силикон Графикс» (США) в режиме САD/САМ/САЕ рассчитаны объем снимаемого металла Qм (мм3) и площади снимаемой стружки S (мм2) в зависимости от номера прохода n и глубины шлифования tшл на каждом проходе (рис. 18).
Q 1000, 3 |
|
|
|
|
|
|
|
|
|
|
|
|
|
|
|
м |
мм |
|
|
|
|
|
|
|
|
|
|
|
|
|
|
|
900 |
|
|
|
|
Сплавы ЖС6УВИ, ЖС26 |
|
|
14 проходов |
||||||
|
800 |
t шл = 2,6 мм |
|
|
|||||||||||
|
700 |
|
|
|
|
|
|
|
|
|
|
|
|
|
9 |
|
|
|
|
|
|
|
|
|
|
|
|
|
|
|
|
|
600 |
|
|
|
|
|
|
|
|
|
|
|
|
|
6 |
|
|
|
|
|
|
|
|
|
|
|
|
|
|
|
|
|
500 |
|
|
|
|
|
|
|
|
|
|
|
|
|
4 |
|
|
|
|
|
|
|
|
|
|
|
|
|
|
|
|
|
400 |
|
|
|
|
|
|
|
|
|
|
|
|
|
3 |
|
|
|
|
|
|
|
|
|
|
|
|
|
|
|
|
|
300 |
|
|
|
t шл = 0,6 мм |
|
|
|
|
|
|
|
|||
|
200 |
|
|
|
|
|
|
|
|
|
|
|
|
|
|
|
100 |
|
|
|
|
|
|
|
|
/ |
t шл = 0,03 мм |
t шл = 0,002 мм |
|||
|
0 |
|
|
|
|
|
|
|
|
|
|
|
/ |
|
|
|
|
|
|
|
|
|
|
|
|
|
|
|
|
|
|
|
1 |
2 |
3 |
4 |
5 |
6 |
7 |
8 |
9 |
10 |
11 |
12 |
13 |
14 |
|
|
|
|
|
|
|
|
Число проходов n |
|
|
|
|
Рис. 18. Характер изменения объема снимаемой стружки Q при глубинном шлифовании «елочного» профиля турбинной лопатки на различном числе проходов
35
Рассчитывался теоретический объем срезаемого слоя металла на всех проходах последовательно с первого до последнего. Результаты этого уникального расчета, приведенные на рис. 18, показали, что применение 9 и 14 проходов вместо 3–4 приводит к более плавному постепенному снижению объема снимаемой стружки Q и соответственно к плавному снижению тепловой и силовой нагрузки на режущих зернах, особенно на последних проходах. Это позволяет получить более благоприятные параметры качества поверхностного слоя и обеспечивает выполнение требований к усталостной прочности.
Усталостные испытания замков лопаток первой ступени двигателя ПС-90А из нового сплава ЖС26, обработанных глубинным шлифованием, также показали при внедрении снижение усталостной прочности до 90 МПа (вместо 110 МПа, требуемых по инструкции). В связи с этим исследовано влияние режимов глубинного шлифования, применяемых кругов, правящих роликов, режимов правки и типа СОЖ на основные параметры качества поверхностного слоя – остаточные напряжения, наклеп, шероховатость поверхности и на усталостную прочность замков лопаток.
Установлено, что на всех режимах глубинного шлифования характер распределения σо практически одинаков, но величина и глубина распространения различные. Статистический анализ максимальной величины сжимающих остаточных напряжений, возникающих на различных режимах глубинного шлифования, и последующих результатов усталостных испытаний показал, что величина предела выносливости σ–1 в значительной степени зависит от величины градиента сжимающих напряжений в весьма тонком поверхностном слое (2–10 мкм). Чем больше величина градиента ∆σсж, тем меньше предел выносливости σ–1. Оптимальная величина градиента сжимающих остаточных напряжений ∆σсж = 200...300 МПа (не более). При ∆σсж более 300–400 МПа предел выносливости замков лопаток ниже требуемого. Например, на лопатках, выдержавших испытания, σ–1 = 140 МПа, ∆σсж = 300 МПа, а на лопатках, не выдержавших испытание, ∆σсж = 500 МПа на глубине 5–10 мкм.
36
Кроме того, возможной причиной снижения усталостной прочности при глубинном шлифовании по сравнению с фрезерованием могут быть длинные продольные глубокие риски от абразивных зерен шлифовальных кругов. Фреза имеет наружный диаметр 70– 90 мм, а шлифовальный круг – 450–500 мм. Поэтому длина дуги контакта шлифовального круга в несколько раз больше, чем у фрезы. После фрезерования на поверхности замков видны короткие (2–5 мм) риски, имеющие ровные края и небольшую глубину.
На поверхности замков, обработанных глубинным шлифованием, заметны длинные продольные риски различных размеров и глубины. Края рисок острые, рваные с выдавленными заусенцами. В самих рисках видны следы адгезионного взаимодействия металла, налипшего на зерно круга, и металла детали. На профилограмме шероховатости после глубинного шлифования микронеровности сильно различаются по высоте, глубине, остроте впадин. Такой характер микронеровностей можно объяснить, во-первых, врезным характером правки кругов алмазными роликами, имеющими достаточно крупную зернистость алмазных зерен (300–500 мкм), во-вторых, врезным характером шлифования и применением весьма мягких высокопористых шлифовальных кругов. Наличие крупных неравномерно расположенных пор в круге и низкая твердость кругов приводят к большей неравномерности распределения режущих зерен на периферии круга как по высоте, так по ширине обрабатываемого профиля. В результате на периферии круга имеются абразивные режущие зерна, выступающие как на 2–5 мкм, так и на 0,5–1,0 мкм. Причем располагаются эти зерна случайно, хаотически. После правки и при затуплении круга характер распределения зерен может полностью измениться.
Дробеструйная упрочняющая обработка не всегда устраняет рисочность, приводит к завальцовке глубоких рисок. При усталостных испытаниях глубокие продольные риски в качестве концентраторов напряжений являются, по-видимому, очагами зарождения трещин. Это подтверждается характером усталостных трещин во впадинах «елочных» замков и в радиусе перехода к торцу замка, причем часто
37
трещины располагаются в продольном направлении, совпадая с глубокими рисками от шлифования.
Исследовано влияние различных параметров глубинного шлифования на величину градиента остаточных сжимающих напряжений. Определена зависимость ∆σсж от изменения скорости детали Vдет, твердости применяемых кругов ЗИ и величины концентрации СОЖ эмульсии Пермол-6. С увеличением скорости детали (подачи стола) с 250 до 290 мм/мин ∆σсж уменьшается с 750 до 270 МПа при одинаковых других условиях шлифования. Увеличение концентрации СОЖ с 1 до 7 % приводит к снижению ∆σсж с 450 до 150 МПа. Установлено существенное влияние на градиент остаточных сжимающих напряжений основных параметров и качества высокопористых кругов. С увеличением твердости кругов с ЗИ 31 до ЗИ 41 градиент остаточных напряжений резко возрастает – с 200 до 800 МПа. Этот факт явился, по-видимому, одной из причин нестабильности процесса глубинного шлифования, случайного характера снижения усталостной прочности на отдельных замках лопаток турбин при внедрении глубинного шлифования, так как был установлен большой разброс твердостей кругов, поставляемых заводом «Ильич». В связи с недостаточным качеством отечественных высокопористых кругов
вОАО «Пермские моторы» введен 100%-ный входной контроль геометрии, твердости, пористости, дисбаланса покупных кругов.
Наиболее интересным является установление зависимости остаточных напряжений от глубины резания, числа проходов и порядкового номера лопатки по ходу шлифования. Эта зависимость показывает, что на первых проходах с большой глубиной резания tшл остаточные сжимающие напряжения минимальны и даже могут быть растягивающими до +150 МПа, например у первой по ходу лопатки. С увеличением числа проходов и снижением глубины шлифования
вповерхностном слое возникают все более увеличивающиеся остаточные сжимающие напряжения, достигающие, например, на последнем девятом проходе –300...–450 МПа. Причем у первой по ходу лопатки остаточные напряжения больше, чем у четвертой. Такой характер распределения остаточных напряжений можно объяснить со-
38
вместным воздействием силового и теплового факторов процесса шлифования. На первых проходах, когда глубина шлифования большая (tшл = 0,6...1,5 мм), превалирующее воздействие оказывает тепловой фактор. Поэтому сжимающие напряжения минимальны. При небольших глубинах шлифования на последних проходах (tшл = = 0,01...0,02 мм) действие теплового фактора уменьшается и усиливается действие силового фактора. Поэтому сжимающие напряжения увеличиваются. С увеличением износа круга действие теплового фактора усиливается, поэтому на четвертой лопатке сжимающие напряжения уменьшаются с –450 до –300 МПа по сравнению с первой лопаткой. На качество обработки влияют жесткость системы ста- нок–приспособление–инструмент–деталь (СПИД), качество очистки и подачи СОЖ.
Обеспечить высокую производительность обработки, качество и усталостную прочность деталей ГТД может лишь качественный абразивный инструмент. Десятилетняя эксплуатация отечественных высокопористых кругов при обработке «елочных» хвостовиков турбинных лопаток ГТД глубинным шлифованием на станках с ЧПУ SS13L фирмы «Элб-Шлифф» выявила неудовлетворительные качественные и эксплуатационные параметры кругов, такие как нестабильная твердость партии кругов, дисбаланс, неравномерное распределение пор, низкое качество зерна, непостоянные режущие свойства, малая стойкость кругов. Эти недостатки и появление новых жаропрочных материалов типа ЖС26, ЖС32 с повышенными прочностными характеристиками в итоге привели к ухудшению качества обработки и снижению эксплуатационных характеристик деталей.
Впоследнее время поставки высокопористых шлифовальных кругов для обработки замков лопаток турбин с завода «Ильич» (г. Санкт-Петербург) осуществляются с большими перебоями из-за отсутствия требуемого порообразователя.
Всвязи с этим была поставлена задача – выбрать оптимальные характеристики высокопористых кругов и фирмы, поставляющие качественную продукцию на рынок абразивных инструментов России.
39
Для решения этой задачи проведены переговоры с рядом абразивных фирм по поводу испытания опытных партий высокопористых кругов. В результате предприятием получены следующие абразивные круги, которые могут, по рекомендациям фирм, заменить серийные круги:
500×25×203,2 89А 1001 Н10А Н2, «Тиролит», Австрия [Т]; 500×25×203 99 ВА 100G, «Экоабразив», г. Москва [С]; 500×25×203 25А 12 Т16 К35 А2 (ОСТ 2И70-11–92), «ОАЗ
ВНИИАШ», г. Санкт-Петербург [Р]; 500×25×203 24А 12Н ЗИ 31–32 12 К13 (ТУ 3981-001-11037779–
94), «ЭКСИ», г. Курган [К]; 500×25×203 25А 10П ЗИ 33 10 К5 ПГ КФ-40 (ОСТ 2И70-11–92),
«Ильич», г. Санкт-Петербург [Ф];
500×25×203 ЕК1 100В-Д11 WVY 357, «Атлантик», Германия [А].
Круги изготовлены по особым технологиям, сущность которых фирмами не раскрывается.
Полученные круги проверялись согласно ОСТ 2И70-11–92 при входном контроле по геометрии, твердости, пористости, по дисбалансу, удельному весу, соотношению зерна, связки и пор. Результаты приведены в табл. 3.
Определение относительного объема пор в кругах показало, что у кругов А и Ф наименьшее число пор, а у кругов Т и К – максимальное. Наиболее благоприятные геометрические параметры имеют круги фирм «Тиролит» и «Экоабразив» (рис. 19).
Особенностью данных кругов является то, что вместо обычного электрокорунда в качестве режущих зерен используется спеченный оксид алюминия, изготовленный по технологии золь-гель (SG). Использование кругов изготовленных по SG-технологии, по данным фирмы «Нортон», обеспечивает эффективную самозатачиваемость и высокую стойкость инструмента. Входной контроль показал, что круги имеют следующие достоинства и недостатки:
• круги фирмы «Тиролит» и «Экоабразив» – повышенную твердость, хорошую пористость, хорошие параметры по геометрии и первый класс неуравновешенности, наименьшую плотность;
40