
- •ЧАСТЬ 1
- •Список литературы
- •4.3. ПОЛУЧЕНИЕ
- •вр Ed (р — ар) + уарг) + E0NV '
- •Список литературы
- •Список литературы
- •7.2. ОБРАЗЦЫ ДЛЯ ИСПЫТАНИЙ
- •7.4. СДВИГ
- •8.1. Расчетные зависимости для постоянных упругости однонаправленного материала (монослоя)
- •8.2. ТЕРМОУПРУГОСТЬ
- •многослойных композитов
- •ПРИ ПЛОСКОМ НАПРЯЖЕННОМ
- •состоянии
- •8.4. ИЗГИБ МНОГОСЛОЙНЫХ
- •композитов
- •Шсшгьш-
- •[Фасу] = 1.] [ф°] [7\]т; (8.101)
- •Список литературы
- •9.1. КЛАССИФИКАЦИЯ КОМПОЗИТОВ
- •9.2. СТРУКТУРНЫЕ ЭЛЕМЕНТЫ
- •9.5. Приближенные зависимости для расчета упругих характеристик композита с противофазным искривлением волокон
- •9.6. ЧЕТЫРЕХНАПРАВЛЕННЫЕ КОМПОЗИТЫ (4Д)
- •ЧАСТЬ 2
- •1.1. УРАВНЕНИЯ МЕХАНИКИ АНИЗОТРОПНОГО ТЕЛА
- •Список литературы
- •2.1. КОМПОЗИТНЫЕ БАЛКИ
- •2.2. ТОНКОСТЕННЫЕ СТЕРЖНИ
- •2.4. КРУГОВЫЕ КОЛЬЦА
- •Список литературы
- •4.1. СТАТИКА ОБОЛОЧЕК ВРАЩЕНИЯ
- •Му == ^1я8да 4“ &22®у 4~ CiaKx4“ ^ааКу!
- •в.З. АНИЗОТРОПНЫЕ ДИСКИ
- •6.3. Влияние начальных термических напряжений на удельные энергоемкости дисков, образованных намоткой композитов
- •6.4. ХОРДОВЫЕ МАХОВИКИ
- •Список литературы
- •ОСЕСИММЕТРИЧНАЯ ЗАДАЧА
- •8.1. ПРОЕКТИРОВАНИЕ МЕХАНИЧЕСКИХ СОЕДИНЕНИЙ
- •Список литературы
- •« РЕКЛАМА»
- •« РЕКЛАМА»
кон (по сравнению с прочностью при |
Величина |
скорости |
сверхпластиче |
||||||
комнатной температуре) на 5% (для |
ской деформапни рассчитывается еле |
||||||||
отдельных видов волокон это снижение |
дующим |
образом: |
|
|
|||||
прочности может быть увеличено до |
|
|
взр = Bgpo 4" ^10» |
||||||
10%-ной потери исходной прочности). |
|
|
|||||||
Таким образом, для определения этого |
где ё8Ро — оптимальная скорость де |
||||||||
критериального условия |
необходимо |
||||||||
формации |
в |
отсутствие |
напряжений |
||||||
проведение серии температурных ис*- |
|||||||||
пытаний волокон. |
|
шарового |
тензора (получают испыта |
||||||
Критерий |
компактирования загото |
ниями матричного материала на кру |
|||||||
вок в режиме сверхпластического со |
чение при температуре, |
соответствую |
|||||||
стояния матричного материала. Кри |
щей |
температуре процесса компакти |
|||||||
териальное |
выражение |
определяется |
рования |
композита); |
о — напряже |
||||
двумя равенствами: |
|
ние |
шарового |
тензора |
(гидростатиче |
||||
|
|
|
ское |
давление); kx = |
Dbz/d2spkTsp — |
Т,a p t
*= е.ер»
где Тзр — температура сверхпластиче ского деформирования; ъ8р — ско рость сверхпластической деформации.
Для реализации режима сверхпла стического компактирования заго товок композитов необходимо распо лагать данными электронно-микро скопического исследования струк туры матричной составляющей, а так же данными ряда испытаний, что поз воляет использовать расчетную ме тодику [3], представленную ниже.
Температура сверхпластического де
формирования определяется до Аормуле
Т&р _
1
показатель [D — эффективный коэф фициент диффузии (при температуре Тsp); Ь — вектор Бюргерса; dap — размер зерна в структуре матричного материала; k — постоянная Больц мана ].
Размер зерна, обеспечивающий сверхпластическую деформацию, рас считывается по формуле
а = _________ 6g__________
вр Ed (р — ар) + уарг) + E0NV '
где Е дк Е0 — энергия соответственно дислокации и образования вакансий; р — плотность дислокаций; а — коэф фициент, учитывающий наличие рас щепленных дислокаций и их концент рацию; у и г) — соответственно энер
гия |
и |
ширина |
дефектов |
упаковки; |
||
No |
— |
концентрация |
вакансий. |
|||
Помимо |
общих |
(универсальных) |
||||
критериев |
разработки процессов де |
|||||
формирования |
композитов |
сущест |
вует ряд частных критериев, свойст венных конкретным процессам. Эти критерии и соответствующие критерн альные решения рассматриваются последующих разделах при рассмот рении процессов.
|
4.6. ДИНАМИЧЕСКИЕ ПРОЦЕССЫ |
||||||
|
КОМПАКТИРОВАНИЯ |
|
|
||||
|
КОМПОЗИТОВ |
|
|
|
|
||
|
Динамические |
|
процессы |
деформиро |
|||
go = 180Oq/GVu |
вания |
(прокатка, |
волочение, |
динами |
|||
где д —- теплота активации полиморф |
ческое |
горячее |
прессование) |
широк |
|||
применяют |
для |
компактирования |
|||||
ного превращения (локального раст |
ВКМ. |
Плоские |
компактные |
пол\ |
|||
ворения или плавления); G — модуль |
фабрикаты из конструкционных BKV |
||||||
сдвига. |
получают, в |
частности, |
прокаткой |
||||
|
причем существуют варианты про катки, при которых ось прокатки сов
падает |
с направлением |
оси |
волокон |
||
в |
заготовке |
либо перпендикулярна |
|||
ей |
[9, |
10, И ]. Прокатка поперек во |
|||
локон |
характеризуется |
пониженным |
|||
нагружением |
волокон, |
так |
как шаг |
их укладки в процессе компактирова ния возрастает. Особенности получе ния этим способом сталеалюминиевых и бороалюминиевых листов подробно рассматриваются в работах [10, 11, 16]. Распределение послойных де формаций при прокатке заготовок из плазменных лент благоприятно, так как коэффициенты неравномерности послойной деформации близки к еди
нице (£н = 0,94-г* 1,02). |
Большая |
неравномерность послойных |
дефор |
маций наблюдается при прокатке за готовок, состоящих из чередующихся слоев фольги и рядов волокон.
При прокатке поперек волокон шаг укладки возрастает, поэтому расчет степени деформации вф. к, обеспечива ющей полное уплотнение заготовок, ведется с учетом этого фактора [10]:
при использовании заготовок, со стоящих из чередующихся слоев фольги и рядов волокон:
8ф. к —
df (4«S — ndf) -f- 4AS (df -}- h0j) .
H S + A S )(h 0t + d f )
при использовании заготовок, со держащих пористые плазменные ленты с волокнами:
еф. к —
_ Рщ (Ш л - ”<*/) + 4AS ( К + |
Лф) |
4 (S -f- AS) (Нл + Нф) |
9 |
где Лф и hn — толщина соответственно фольги и пористых лент; AS — изме нение шага укладки волокон' при прокатке (табл. 4.7).
Данные о распределении послойных деформаций используют при расчете параметров заготовок. При заданной толщине листа h толщина заготовки Лзг= Л/(1 — е2), где е^. — оптималь
ное суммарное обжатие при прокатке композита (определение этой величины для различных прокатных процессов применительно к композитам рассмат ривается ниже).
После определения общей толщины заготовки рассчитывают толщины мат ричных слоев h0i для заготовок, со стоящих из чередующихся матричных элементов и рядов волокон:
hoi = hoi ср^нi*
где kHi — коэффициент неравномер ности послойной деформации при оп тимальном значении суммарного от носительного обжатия при прокатке (подробные данные о значениях kH сталеалюминиевых заготовок при ведены в работе [11]);
и— har — dfn .
ft°<с р - |
-> |
п— число слоев волокон в заготовке. Для заготовок, состоящих из по
ристых монослойных армированных лент и фольговых прокладок (и наружных обкладок), определяют сум марную толщину фольговых элементов
[И ] |
Ч : |
|
|
|
|
|
Ьф = |
|
|
|
- n d } ( l - V f + |
pmVf) - - |
|
|
_ |
|
____ — 4hnSpmVf____ w |
|
|
“ |
_ |
WJs |
. |
|
|
|
X (Я1 + |
1), |
(4.2) |
где fif — число слоев армированных пористых лент; рт — пористость мат ричной составляющей в лентах. Сред няя толщина фольгового элемента за готовок этого типа в (п + 1) раз меньше величины, определяемой по
(4.2). |
|
каждого |
фольгового эле |
|||
Толщину |
||||||
мента |
определяют с |
учетом |
&Hi |
: |
||
: Лфi = |
Лф. cpkHi. Значения kBi подроб- |
|||||
но представлены в работе [10]. |
|
|||||
Суммарное |
относительное обжатие, |
|||||
обеспечивающее полное уплотнение |
||||||
заготовки |
и |
формирование |
прочной |
|||
связи |
слоев |
волокон |
между |
собой |
и |
с волокнами при использовании ком
пактных матричных элементов, |
рас |
|
считывают по формуле [5, 11 ] |
|
|
в, |
4я2л2*?Кв |
(4.3) |
ho |
|
|
|
|
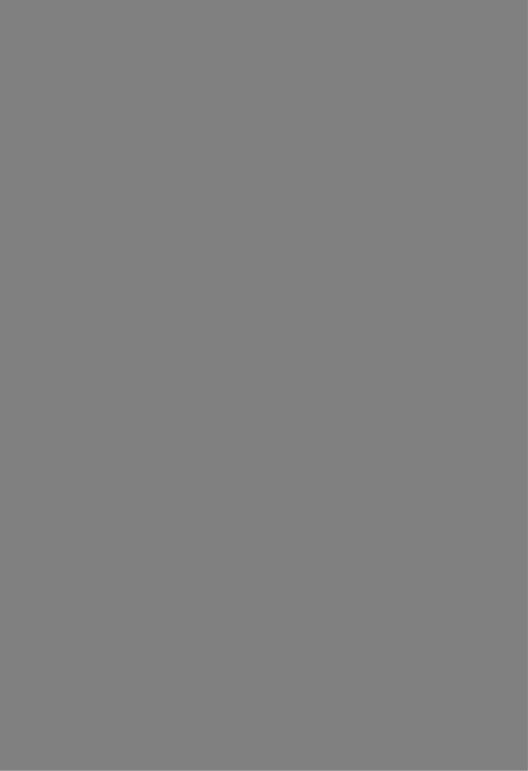
|
а; = |
J SCl |
(6 + 1 ) |
|
hit |
|
|
|
(4.4) |
|||
|
|
|
|
|
|
|
|
|
|
|
|
|
где o'} — сопротивление волокон раз |
ного перехода без разрушения волокон |
|||||||||||
рушению при поперечном сжатии (при |
[Щ : |
|
|
|
|
|||||||
температуре пропесса); a*ci — на |
|
|
|
|
|
|||||||
пряжение течения матрицы композита |
Если на каком-то этапе |
расчета |
||||||||||
при уплотнении «ячейки»; |
Л*/ — тол |
|||||||||||
щина полосы после выполнения дан |
выражение (4.4) не имеет решения, |
|||||||||||
ного прохода; АЛ/ — допустимое аб |
значит этот переход нельзя выпол |
|||||||||||
солютное обжатие на рассматриваемом |
нить с сохранением сплошности во |
|||||||||||
прокатном проходе; о |
= |
2//р/ДЛ/ — |
локон. Зная допустимые значения АЛ/ |
|||||||||
показатель (где р — коэффициент тре |
на всех переходах и суммируя их, |
|||||||||||
ния на контактной поверхности очага |
можно определить максимально допу |
|||||||||||
деформации; |
// |
= |
'\/R BAhi |
— длина |
стимое |
суммарное |
обжатие |
при про |
||||
катке: |
|
|
|
|
||||||||
дуги захвата заготовки валками). |
|
|
|
|
||||||||
|
|
|
|
|
||||||||
Единственным |
неизвестным |
явля |
|
|
|
2 АЛ< |
|
|||||
ется АЛ/. Устанавливая его значения, |
|
|
|
1 |
|
|||||||
легко |
определить |
величины |
относи |
Эта методика |
расчета применяется |
|||||||
тельных обжатий (они могут быть |
||||||||||||
безразмерными, как во всех предыду |
при прокатке поперек волокон. Зна |
|||||||||||
щих выражениях, |
или |
переводятся |
чения относительных обжатий по про |
|||||||||
в проценты). В частности, относитель |
ходам при получении листов из кон |
|||||||||||
ные допустимые обжатия (%), обе |
струкционных |
композитов |
представ |
|||||||||
спечивающие |
осуществление |
прокат |
лены в табл. 4.8. |
|
|
|||||||
4.8. Относительное обжатие в/ по переходам при прокатке армированных |
||||||||||||
листов |
[10] |
|
|
|
|
|
|
|
|
|
|
|
|
|
|
|
V/. % |
|
|
в/, %, на |
прокатном |
переходе |
|
||
Материал |
|
|
|
1 |
2 |
3 |
|
4 |
5 |
|||
|
|
|
|
|
|
|
|
|||||
|
|
|
|
20 |
|
32 |
18 |
12 |
|
5 |
3 |
|
|
|
|
|
25 |
|
28 |
17 |
12 |
|
5 |
3 |
|
АД1—В |
|
|
|
30 |
|
25 |
15 |
10 |
|
5 |
3 |
|
|
|
|
35 |
|
25 |
15 |
8 |
|
4 |
3 |
||
|
|
|
|
44 |
|
23 |
12 |
7 |
|
4 |
2 |
|
|
|
|
|
54 |
|
21 |
12 |
7 |
|
3 |
— |
|
|
|
|
|
20 |
|
* 25 |
17 |
11 |
|
7 |
5 |
|
АМгб—В |
|
|
25 |
|
25 |
17 |
11 |
|
7 |
3 |
||
|
|
30 |
|
25 |
15 |
10 |
|
5 |
— |
|||
|
|
|
|
35 |
|
25 |
15 |
10 |
|
5 |
— |
|
АМг6-ЭП322 |
|
|
20 |
|
|
36 |
23 |
16 |
|
12 |
8 |
|
|
|
30 |
|
|
29 |
17 |
12 |
|
6 |
4 |
||
|
|
|
|
35 |
|
|
25 |
15 |
10 |
|
5 |
3 |
П р и м е ч а н и е . Температура прокатки бороалюминия 520°С, сталеалюминия 400 °С.
Методика расчета процесса прокатки вдоль волокон, помимо критериев пол ного уплотнения заготовки, формиро вания прочного соединения составля ющих и других ранее рассмотренных критериев, базируется на частном кри терии, используемом для процессов, при осуществлении которых в очаге деформации неизбежно действуют рас тягивающие напряжения, приложен ные к волокнам. Этот критерий выра жается неравенством а2 < aft где аг —
межкомпонентное растягивающее на пряжение, приложенное к волокнам в очаге деформации; оу — временное
сопротивление волокон разрыву при температуре, соответствующей тем пературе процесса.
vДЛ, +
где п\ — номер прохода.
Сложность процесса прокатки вдоль волокон заключается в том, что после полного уплотнения (при наличии допустимых отклонений на все пара метры) деформировать заготовку без разрушения волокон нельзя. Единст венной возможностью компенсации отклонений фактических параметров заготовок, процесса, оснастки от рас четных является уширение при про катке узких полос и лент.
В связи с тем, что композиты с од ноосным армированием обладают ярко
В результате анализа процесса ус тановлены варианты методики рас чета параметров процесса [10] в за
висимости от вида применяемых заго товок.
При использовании заготовок, со стоящих из чередующихся фольговых элементов и рядов волокон:
для первого перехода
|
(ndfof/2o‘scl) X |
|
®i |
X y d t/2nRa |
100; |
df [1 - (Kd,/4S)} + S |
для всех последующих переходов, т. е. для я-го перехода
nd^aj
•Ahx — — Ah
------100,
выраженной анизотропией свойств, в ряде случаев необходимо применять другие схемы армирования, называе мые послойно-перекрестными [10, 17]. Поэтому при прокатке таких загото вок необходимы особые методы рас чета допустимых параметров взаим ного расположения рядов волокон по слоям заготовки и допустимых об жатий по прокатным переходам. При прокатке листов с послойно-перек рестным расположением хрупких во локон допустимое обжатие
[g/ - K |
c + gM/)sln P H / |
|
е/ шах — { |
4a*clnm |
(4.5) |
где osc — предел текучести компо зита при растяжении вдоль волокон при температуре процесса; р — коэф фициент межкомпонентного трения при температуре прокатки, равный 0,5 при горячем деформировании; Р — угол смещения волокон относительно поперечной оси полосы; m — коэф фициент, равный отношению 2<рк/я.
Допустимые значения относитель ных обжатий по переходам при про катке бороалюминиевых листов с по слойно-перекрестным армированием и
значения допустимых углов Р пред ставлены в приведенных далее табл.
4.9 и 4.10.
Прокаткой могут быть получены листы с ортогональным комбинирован ным армированием, когда вдоль на правления прокатки в заготовке рас положены проволочные металлические волокна, а в поперечном направлении уложены пористые монослойные ленты с хрупкими волокнами. Расчет пара метров прокатки таких листовых за готовок сводится к следующему [10)
4.9. Допустимые относительные обжатия при прокатке бороалюминиевых листов с послойно перекрестным армированием
|
8/, |
%, |
на переходе |
|
Vf, % |
1 |
2 |
3 |
4 |
|
||||
15 |
35 |
20 |
15 |
б |
20 |
32 |
18 |
12 |
|
25 |
28 |
15 |
10 |
4 |
30 |
25 |
13 |
8 |
3 |
4.10. Допустимые углы 0 послойно-перекрестно армированных листов [10] в зависимости от параметров бороалюминия и его армирующих волокон при температуре прокатки
v f- |
G s d ' |
°sc> |
*/520» |
т |
Э |
% |
МПа |
МПа |
МПа |
|
|
15 |
34 |
159 |
2520 |
0,410 |
21° 12' |
20 |
45 |
180 |
2520 |
0,380 |
17° 28' |
25 |
52 |
207 |
2520 |
0,350 |
15° 41' |
30 |
59 |
231 |
2520 |
0,325 |
13° 23' |
П р и м е ч а н и е . |
Температура |
П р и м е ч а н и я : 1. Значения |
уг |
||
прокатки 520 °С, диаметр валков про |
лов р определены по преобразованной |
||||
катного стана 0,6 м [10J. |
|
формуле (4.5) (фк и Р — в радианах). |
|||
|
|
2. Диаметр волокон бора 100 мкм. |
|||
Допустимое суммарное |
относитель |
необходимое для уплотнения; ДЛц. м— |
|||
допустимое |
абсолютное |
обжатие |
уп |
||
ное обжатие определяется по формуле |
лотненной |
заготовки, |
имеюшей |
тол |
е Х max = |
(^ф . к |
|
^ к . м)/^аг> |
щину hBr. Величины ДЛф. к и |
ДАК. м, |
||||||||||||||||
|
в свою очередь, определяются следую |
||||||||||||||||||||
где ЛЛф. к |
— |
абсолютное |
обжатие, |
щими выражениями: |
|
|
|
|
|||||||||||||
|
ДА |
|
|
_ V X W |
M - ^ / A) , ^ А ( # л5 п - ^ п) . |
|
|
||||||||||||||
|
ДЛф.к---------------- Щ ------------ + |
------------- 33£------------ ’ |
|
|
|
||||||||||||||||
|
д и |
|
__ |
[(СТа/ |
а ас |
° * т ) ^/д |
^ s m ^ e |
|
|
в ^ ф .к ] |
|
|
|
||||||||
|
|
к' “ |
~ |
|
|
|
|
|
|
|
|
|
|
|
|
|
|
|
|
||
где d/д — диаметр расположенных |
ния |
матричной |
составляющей |
ком |
|||||||||||||||||
вдоль прокатываемой заготовки |
про |
позита. |
|
|
|
|
|
|
|
|
|||||||||||
волочных волокон; |
лд — число фоль |
|
По данным расчетов, прокатку таких |
||||||||||||||||||
говых слоев |
заготовки; |
пП — |
число |
заготовок |
целесообразнее |
всего |
вы |
||||||||||||||
слоев пористых лент с хрупкими во |
полнять за два прохода с вели |
||||||||||||||||||||
локнами, расположенными в заготовке |
чинами |
обжатий, представленными |
|||||||||||||||||||
поперек оси прокатки; |
dfn — диаметр |
в табл. 4.11. |
|
|
|
|
|
|
|||||||||||||
хрупких волокон |
в |
пористых лентах; |
Оптимальные |
|
температуры |
про |
|||||||||||||||
hjj —толщина пористых армированных |
|
||||||||||||||||||||
катки |
|
для |
бороалюминия |
500— |
|||||||||||||||||
монослойных лент; 5Д— шаг укладки |
|
||||||||||||||||||||
520 °С |
[11], |
|
для |
сталеалюминия |
|||||||||||||||||
проволочных волокон; h0t |
— толщина |
|
|||||||||||||||||||
380—400 °С при |
использовании |
в |
ка |
||||||||||||||||||
фольговых |
слоев: |
6НП |
— |
коэффи |
|||||||||||||||||
честве |
волокон |
|
проволоки |
из |
сталей |
||||||||||||||||
циент неплотности матрицы пористых |
|
||||||||||||||||||||
08X18Н9Т |
и |
12Х18Н10Т |
и |
420— |
|||||||||||||||||
армированных |
лент; |
о5у — предел |
|||||||||||||||||||
450 °С при |
использовании |
в качестве |
|||||||||||||||||||
текучести |
проволочных |
волокон |
при |
||||||||||||||||||
волокон |
|
проволоки |
из |
сталей |
|||||||||||||||||
температуре |
прокатки; |
о*т — сред |
1Х15К4АМЗ (ВНС-9) и ЭП322 [12]. |
||||||||||||||||||
нее напряжение |
|
пластического |
тече |
Режимы |
термической |
упрочняющей |
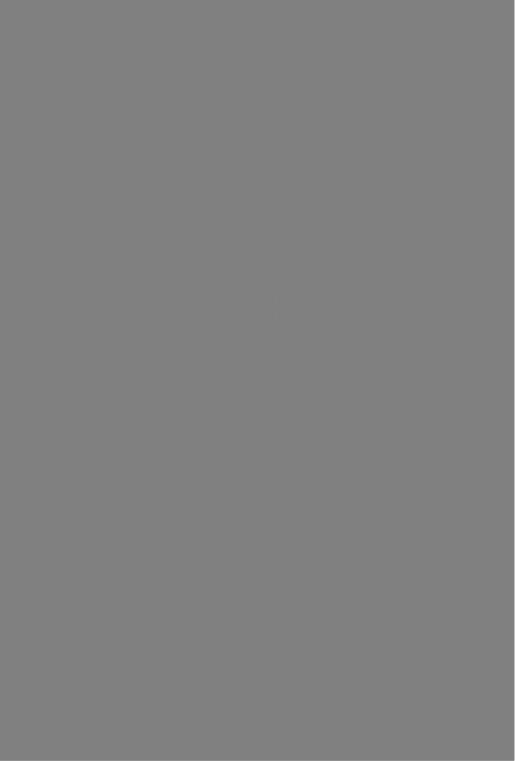
полой пресс-шайбы во вкладыш тех |
Время силового воздействия на еди |
||||||||||||||||||||||
нологического наполнителя |
на стенки |
ничный по длине участок обрабатыва |
|||||||||||||||||||||
сборного пакета (заготовки трубчатого |
емой заготовки |
|
|
|
|
|
|
||||||||||||||||
изделия) действует давление, |
вызван |
|
|
|
*д= |
( h + U |
в)/*. |
|
|
||||||||||||||
ное |
сопротивлением |
материала |
тех |
|
|
|
|
|
|||||||||||||||
нологического |
наполнителя |
истече |
где v — скорость перемещения пресс- |
||||||||||||||||||||
нию в полость пресс-шайбы, |
и проис |
||||||||||||||||||||||
шайбы; h — параметр (см. рис. 4.13); |
|||||||||||||||||||||||
ходит сварка давлением. При опреде |
|||||||||||||||||||||||
/п. з = |
di sin а — длина пластической |
||||||||||||||||||||||
лении |
параметров |
процесса |
|
поль |
зоны |
(<dt |
и |
а — параметры, |
см. |
||||||||||||||
зуются |
критериями |
полного |
уплот |
рнс. |
4.13). |
|
|
|
|
|
|
|
|
||||||||||
нения композита, формировании проч |
|
|
|
|
|
|
|
|
|||||||||||||||
Угол а в прессовых процессах обыч |
|||||||||||||||||||||||
ного |
|
соединения |
составляющих, |
||||||||||||||||||||
|
но |
выбирают |
в |
пределах |
45—60°; |
||||||||||||||||||
сохранения |
прочности и |
сплошности |
|||||||||||||||||||||
величину h определяют из следующего |
|||||||||||||||||||||||
волокрн. Параметр D0 (см. рис. 4.13) |
|||||||||||||||||||||||
выражения: |
|
|
|
|
|
|
|
|
|||||||||||||||
легко связывается с заданным наруж |
|
tcv — di sin a, |
|
|
|||||||||||||||||||
ным диаметром изделия через темпе |
|
|
|
h = |
|
|
|||||||||||||||||
ратуру процесса и термический |
коэф |
где /0 — время образования прочного |
|||||||||||||||||||||
фициент |
линейного |
|
расширения. |
||||||||||||||||||||
|
соединения |
составляющих |
композита; |
||||||||||||||||||||
Внутренний диаметр |
заготовки |
опре |
|||||||||||||||||||||
определение |
этой |
величины |
рассмо |
||||||||||||||||||||
деляется выражением |
|
|
|
|
|
|
|||||||||||||||||
|
|
|
|
|
|
трено |
в |
разд. 4.4. |
|
|
|
|
|
|
|||||||||
|
|
|
|
|
|
|
|
|
|
|
|
|
|
|
|
|
|||||||
|
|
|
|
|
|
|
|
|
|
|
На основании критериального реше |
||||||||||||
|
|
|
|
|
|
|
|
|
|
|
ния |
условия |
сохранения |
сплошности |
|||||||||
|
|
|
|
|
|
|
|
|
|
|
волокон |
получено |
|
выражение |
[10] |
||||||||
а;: |
|
J s c i |
£(еР/sin a) In (d‘4d\) |А + |
(1 /cos2 ^ |
|
d2 In (d2/d\) + |
(4d2/d,) |
|
|
||||||||||||||
|
|
|
|
|
|
|
|
cos у (d2 — d?) |
|
|
|
|
|
|
|
|
|
||||||
|
|
|
|
|
|
|
|
|
|
|
|
|
|
|
|
|
|
||||||
|
|
|
|
|
|
|
|
|
|
|
|
|
|
|
|
|
|
|
|
|
|
(4.6) |
|
где p — коэффициент трения на по |
1300 МПа (при степени сохранения |
||||||||||||||||||||||
яске пресе-шайбы (поверхности ее |
сплошности волокон 97%) [10, 18]. |
||||||||||||||||||||||
скоса); у — угол «естественного» тече |
Расчетные |
данные |
процесса |
пред |
|||||||||||||||||||
ния |
материала |
технологического |
на |
ставлены в табл. 4.12. |
|
|
обычно |
||||||||||||||||
полнителя, |
определяемый |
экспери |
Процессы |
|
прессования |
||||||||||||||||||
ментально, так как он зависит от |
производят с некоторым пресс-остат |
||||||||||||||||||||||
конкретного значения а, |
температуры |
ком; в рассматриваемой зоне в донной |
|||||||||||||||||||||
процесса, |
материала |
наполнителя, |
части |
|
технологического |
вкладыша |
|||||||||||||||||
условий трения на рабочем пояске |
должна оставаться |
непропрессованной |
|||||||||||||||||||||
полости пресс-шайбы; I — длина ка |
некоторая высота V» ее величина |
||||||||||||||||||||||
либрующего пояска |
рабочей |
полости |
должна быть не менее полутора длин |
||||||||||||||||||||
пресс-шайбы, |
которая |
выбирается |
пластической |
зоны |
/п. з* |
Для |
того |
||||||||||||||||
в пределах (3—15) 103 мкм; d — пара |
чтобы |
исключить |
«концевой» |
эффект, |
|||||||||||||||||||
метр, определяемый из практики сбор |
в верхней части технологической обо |
||||||||||||||||||||||
ки трубчатых заготовок (обычно do — |
лочки |
|
заготовки |
предусматривается |
|||||||||||||||||||
= d + |
0,2 мм); oj и о*с{ — показатели |
участок высотой ht , не содержащий |
|||||||||||||||||||||
соответственно |
волокон |
и |
композита |
армированной |
собственно |
заготовки. |
|||||||||||||||||
(см. разд. 4.4). Тогда в выражении |
Высота этого участка Л* должна быть |
||||||||||||||||||||||
(4.6) |
остается |
неизвестным один пара- |
порядка |
(1,5—2,0)/п. з* |
|
|
|
||||||||||||||||
метР dlt который и контролирует сило |
Параметры |
и |
— см. на рис. 4.13. |
||||||||||||||||||||
вые условия процесса. |
|
|
|
|
|
Другим |
вариантом |
изготовления |
|||||||||||||||
Полые изделия, полученные из боро- |
армированных труб является ком- |
||||||||||||||||||||||
алюминия |
по |
рассмотренной |
|
схеме, |
пактирование за счет давления изнутри |
||||||||||||||||||
при объемной доле волокон 50% имеют |
полой |
заготовки |
(в |
технологической |
|||||||||||||||||||
сопротивление |
разрушению |
|
1200— |
оболочке) при прохождении |
через ее |
4.12. Параметры прессования бороалюмнниевых труб с использова нием технологического вкладыша заготовок (см. рис. 4.13)
d |
dt |
Усиляе |
D0, и |
/•10*, |
|
веки |
пpecсова- _ |
|
|
и |
ния, кН |
|
|
0,038 0,024 50—100 22,3—27,0
0,038 0,020 50—100 23,3—31,0
0,04 0,036 0,020 50—100 24,5—27,6
0,036 0,016 30—50 34.5—35,3
0,048 0,032 50—150 31,4—35,0
0,048 0,028 50—80 39,6-42,9
0,05 0,048 0,026 30—50 45,0-46,8
0,046 0,030 50—120 30,5—33,0
0,046 0,022 50—80 51,0—53,0
0,057 0,031 50—100 66,0—68,0
0,057 0,027 50—80 80,0—82,0
0,06 0,057 0,025 30—50 87,0—88,0
0,056 0,030 50—100 63,0—68,0
0,056 0,026 30—50 78,0—80,0
П р и м е ч а н и е . Скорость прессо вания 6,7.10е4 м/с, температура 560 °С Ц0].
Рис. 4.14. Схема радиального уплотнентполых армированных заготовок в техно логических оболочках Ею]:
1 — пресс-шайба; 2 — тяга; 3 — полги |
||
армированная |
сборная заготовка; 4 ~ |
|
внутренняя |
технологическая |
оболочк, |
5 — наружная технологическая |
оболоч |
ка; 6 — контейнер; 7 — нижняя (опорная)
плата оснастки; |
8 — система нагрева; |
9 — подкладная |
плита; 10 — технологи |
ческий вкладыш |
|
полость пуансона |
(или |
нескольких |
||
последовательно уплотняющих |
пуан |
|||
сонов) [10]. |
|
фактором, |
огра |
|
Дополнительным |
||||
ничивающим |
величину |
деформации |
||
в радиальном |
направлении уплотня |
емой заготовки, является устойчивость внутренней технологической обо лочки, поэтому процесс осуществляет ся за несколько проходов, количество которых рассчитывается по следу ющей формуле:
nt ^ bFX]\g kpi ор,
В то же время kFX = Fw/Fr где
F*r — сечение заготовки, a F — сече ние готовой трубы. Наружные диа метры заготовки и трубы совпадают (это Do на рис. 4.14), d — внутренний диаметр готовой трубы задан, т. е. можно определить внутренний диа метр заготовки do. Параметр d нужно устанавливать с учетом заданного на ружного диаметра трубы и коэффи циента термического расширения материала.
Величина kFX связана с коэффи
циентом неплотности заготовки сле дующим образом:
где крг£ — коэффициент уплотнения
заготовки за весь процесс (коэффи циент уменьшения сечения заготовки при уплотнении); k n ср — средний коэффициент уплотнения заготовки за переход (для данного процесса .при менительно к бороалюминиевым тру бам он имеет значения 1,05—1,10) [10].
^FX ~ 4 0 |
^нп)« |
Диаметр полости d* обрабатываемой заготовки после каждого перехода определяется из равенства
л(Fi
а усилие, потребное для осуществле ния перехода, из следующей формулы
ПО):
P t — no*ci х
|
( |
|
|
|
|
|
|
|
|
|
|
|
|
|
|
|
|
|
|
|
|
||
X |
d ' i - d U |
|
|
|
|
|
|
|
|
|
|
|
|
|
|
|
|
||||||
|
|
2 sin 2a |
|
|
|
|
|
|
|
|
|
|
|
|
|
|
|
|
|||||
|
|
|
|
|
|
|
|
|
|
|
|
|
|
|
|
|
|
|
|||||
где lH — |
высота |
пресс-шайбы; |
a = |
|
|
|
|
|
|
|
|
|
|||||||||||
* |
I 2tvzv \ |
|
|
|
|
|
|
|
|
|
|
|
|
|
|
|
|
|
|||||
= arctg ( |
|
|
|
J — угол переходного |
|
|
|
|
|
|
|
|
|
||||||||||
участка от боковой к лицевой поверх |
Рис. 4.15. Схема к определению парамет |
||||||||||||||||||||||
ности пресс-шайбы |
|
= |
/с — время |
ров облойных полостей при радиальном |
|||||||||||||||||||
образования |
соединения; v — скорость |
компактировании |
армированных |
труб: |
|||||||||||||||||||
1 — матрица |
КМ; |
2 — облой; |
3 — рабо |
||||||||||||||||||||
перемещения пресс-шайбы). |
|
|
|
|
чая |
вставка; |
4 — технологическая |
обо |
|||||||||||||||
При изготовлении труб из бороалю- |
лочка; |
5 — волокно |
КМ |
|
|
|
|
||||||||||||||||
миния (волокна бора с покрытием |
|
|
|
|
|
|
|
|
|
||||||||||||||
карбида |
кремния) |
средний |
коэффи |
технологической |
оболочки |
в |
облой |
||||||||||||||||
циент уменьшения |
сечения |
уплотня |
|||||||||||||||||||||
емой заготовки |
составлял |
1,065; |
а = |
определяется |
параметр |
облойной |
по |
||||||||||||||||
= 7°; о = |
0,1 м/мин. Трубы |
с |
объем |
лости |
|
|
|
|
|
|
|
||||||||||||
ной долей волокон 43%, компактиро- |
|
|
|
|
|
|
|
|
|
||||||||||||||
ванные |
при |
температуре 580 °С |
за |
|
2^ ascih - |
as |
|
|
|
|
|
||||||||||||
восемь переходов при высоте пресс- |
Ь |
|
|
|
2цОц |
|
|
|
’ |
||||||||||||||
шайбы 71 • 10а мкм |
и о*с{, возрастав |
|
|
|
|
|
|
||||||||||||||||
шим от перехода к переходу от 8 до |
где |
as — предел текучести |
материала |
||||||||||||||||||||
28 МПа, имеют компактное строение, |
технологической |
оболочки |
при |
тем |
|||||||||||||||||||
полностью |
|
|
сохраняют |
сплошность |
пературе процесса Т; р — коэффи |
||||||||||||||||||
волокон, между составляющими |
|
ком |
циент трения на участке облойной |
||||||||||||||||||||
позита образуется прочное соединение, |
полости; h — величина, определяемая |
||||||||||||||||||||||
сопротивление |
|
разрушению |
|
|
труб |
в зависимости от полного усилия ком |
|||||||||||||||||
при растяжении 950 МПа |
[10]. Полу |
пактирования (табл. 4.13): |
|
|
|
||||||||||||||||||
ченные по такой же схеме трубы из |
|
|
|
|
|
|
|
|
|
||||||||||||||
материалов АД1-В и Д16-В с объемной |
Р = |
а ^ О / тр( 1 + а1Г )(1 4 - а 2Г), |
|||||||||||||||||||||
долей волокон 57% |
имеют более высо |
|
|
|
|
|
|
|
|
|
|||||||||||||
кие значения |
указанной |
характери |
где /тр— длина компактируемой трубы |
||||||||||||||||||||
стики — соответственно 980 и 1150 МПа |
|||||||||||||||||||||||
[13]. |
радиальном |
|
компактировании |
(или |
ее участка); |
и а 2 —• коэффи |
|||||||||||||||||
При |
|
циенты линейного термического |
рас |
||||||||||||||||||||
заготовок |
|
армированных |
труб, |
|
уста |
ширения композита в |
направлениях |
||||||||||||||||
навливаемых на жесткие оправки, ком |
соответственно |
вдоль |
и |
поперек |
|||||||||||||||||||
пенсация |
|
колебаний |
пористости |
ма |
направления |
волокон. |
|
|
армиро |
||||||||||||||
трицы |
композита, |
допустимых |
|
откло |
Изготовление |
спирально |
|||||||||||||||||
нений по толщине элементов заготовок, |
ванных труб с металлическими про |
||||||||||||||||||||||
температур |
деформирования, |
|
номи |
волочными |
волокнами |
может |
осу |
||||||||||||||||
|
ществляться |
методом |
гидростатиче |
||||||||||||||||||||
нальных |
размеров |
|
деталей |
оснастки |
ского прессования по схеме, представ |
||||||||||||||||||
обеспечивается |
облойными |
полостями |
|||||||||||||||||||||
между |
рабочими |
деталями |
оснастки, |
ленной на рис. 4.16. Изделие вы |
|||||||||||||||||||
в которые |
|
может |
истекать |
материал |
давливается через канал матрицы вме |
||||||||||||||||||
технологической |
|
оболочки |
|
сборной |
сте с оправкой под действием высокого |
||||||||||||||||||
|
|
давления жидкости (заготовка должна |
|||||||||||||||||||||
заготовки |
|
(рис. |
4.15). |
Из |
условия |
||||||||||||||||||
компактности, а также из условия |
быть |
предварительно |
герметизиро |
||||||||||||||||||||
вана). При изготовлении сталеалюми |
|||||||||||||||||||||||
равенства |
|
|
сопротивления |
|
течению |
||||||||||||||||||
матричной |
|
составляющей |
композита |
ниевых труб процесс |
осуществляется |
||||||||||||||||||
в заключительной |
стадии |
уплотнения |
с 50%-ным обжатием заготовки по |
||||||||||||||||||||
и сопротивления истечению материала |
сечению при температуре |
200 °С. |
4.13. Высота мостика облойной полости
р. |
А, Мкм |
Р. мн |
А, мкм |
мн |
|||
6,3 |
600—1000 |
20 |
1400—1800 |
10 |
1000—1500 31.5—40 2000—2500 |
||
16 |
1200—1600 |
50—63 |
3000—3500 |
|
1 |
|
|
Рис. 4.16. Схема |
гидростатического |
|
прессования армированных труб |
[11]: |
1 — пуансон; 2 — контейнер; 8 — прессшайба с иглой; 4 н 5 — трубчатые эле менты из матричного материала; 6 — волокно, свернутое в спираль; 7 — рабо чая жидкость; 8 — матрица прессовой оснастки; 9 — армированная труба; 10 — опорная плита; 11 — адгезионный слой
Спрессовывание элементов плоских пакетов — заготовок по схеме диффу зионной сварки применительно к кон струкционным композитам — наиболее универсальный процесс, хотя он и не обеспечивает высокую производитель ность. Этот процесс подробно изучен
и широко освешен в работах |
[5, 6, 9, |
|||
10, |
13, |
21. |
22]. |
панелей |
При |
получении плоских |
|||
и |
листов |
спрессовыванием |
сборных |
ваготовок по схеме диффузионной свар ки в большинстве случаев, когда в ком позите используют хрупкие волокна, в качестве технологической оснастки применяют пресс-формы. В этих усло виях спрессовывание связано с изме нением только одного размера заго товки — ее толщины. При заданной толщине h изделия толщина заготовки
Ляг = Л + ДЛф. к,
где ДЛф. к — абсолютная деформация уплотнения заготовки, количественно равная необходимому рабочему ходу активной части оснастки при дефор мировании. Поэтому с учетом такого процесса уплотнения плоских заго товок можно суммарный объем не-
плотностей заготовки ваписать в виде равенства
к^зг^аг — ^нп^зг-
Так как объем таких заготовок пред ставляет собой произведение трех га баритных размеров, то после сокра щения
АЛф#к = ^нп^зг-
Время образования физическогс контакта по всей площади границ матричной составляющей и волокон при скорости прессования (о)
tф = ДЛф . к! v = ^нп^зг/И-
После уплотнения заготовки необ ходима выдержка под давлением дли тельностью, соответствующей fa, т. е полное время деформирования
= ^ф- к 4- Не полное усилие
^CTscf^ar^3T>
где величина о£С1определяется п<
методике, изложенной в разд. 4.4. Получение по указанной схеме изде
лий из композитов гарантирует наи более стабильные результаты (пс качественным признакам и уровнк характеристик).
Листы из материалов АД1 — ЭП32' иД20 — 1Х15Н4АМЗ после прессова ния при температурах соответственнс 480 и 440 °С при шаге укладки волоксн (диаметры волокон соответственнс 400 и 200 мкм), в 2 раза превышают^ их диаметр, толщине 2-10® мкм имел1 временное сопротивление разрыву при растяжении при комнатной тем пературе соответственно 780 и 975 МП: при объемной доле волокон 28% и 1141
и 1470 МПя соответственно при объем |
фузионная сварка (в отличие от пр~ |
||||||||||||||||||||||||||
ной доле волокон 42% |
[10]. Давление |
катки) |
не |
регламентирует |
|
параметры |
|||||||||||||||||||||
при изготовлении этих изделий со |
послойно-перекрестного |
армирования |
|||||||||||||||||||||||||
ставляло для материала АД1 — ЭП322 |
металлов и сплавов. В частности, этот |
||||||||||||||||||||||||||
34 МПа, а для материала Д20 — |
процесс |
используется |
д.:я |
|
получения |
||||||||||||||||||||||
1Х15Н4АМЗ — 88 МПа |
[10]. Панели |
ортогонально |
армированных |
полос, |
|||||||||||||||||||||||
на основе титановых сплавов с объем |
в которые вводятся волокна бора с по |
||||||||||||||||||||||||||
ной |
долей |
|
волокон |
бора |
21—27% |
крытием кремния и стальная прово |
|||||||||||||||||||||
с покрытием карбида кремния после |
лока. |
Температура |
|
прессования |
|||||||||||||||||||||||
спрессовывания |
|
при |
|
температуре |
500 °С, |
давление |
70 |
МПа, |
|
время |
вы |
||||||||||||||||
760 °С |
и |
давлении |
84.4 |
МПа с |
вы |
держки в вакуумной камере 1 ч [21]. |
|||||||||||||||||||||
держкой 1 ч (или при |
температуре |
|
Боромагниевый композит может быть |
||||||||||||||||||||||||
870 °С, том же давлении |
и выдержке |
получен в вакуумных камерах с вы |
|||||||||||||||||||||||||
0,25 ч) имеют модуль упругости 162— |
держкой 1 ч при температурах 500— |
||||||||||||||||||||||||||
197 ГПа и временное сопротивление |
525 °С и давлениях соответственно |
||||||||||||||||||||||||||
до 1406 МПа |
[11]. |
|
|
|
|
|
|
140—70 МПа [21]. В к?мерах для |
|||||||||||||||||||
При диффузионной сварке пакетов — |
диффузионной |
сварки |
вакуум |
обычно |
|||||||||||||||||||||||
заготовок бороалюминия [22 ] давление |
13,1—1,31 МПа [9]. При получении |
||||||||||||||||||||||||||
определяется |
материалом |
матричной |
композита |
на |
основе |
|
титана |
марки |
|||||||||||||||||||
составляющей, |
например, |
если |
ис |
ВТ 1-0 в вакууме |
необходимы |
темпе |
|||||||||||||||||||||
пользуют материал ВКА-1, то темпе |
ратуря |
780—920 °С, |
|
давления |
со |
||||||||||||||||||||||
ратура |
|
деформирования |
|
составляет |
ответственно 60—40 |
МПа, |
выдержка |
||||||||||||||||||||
500—520 °С, если технический |
алюми |
15—30 мин |
[9]. |
|
|
|
прессованием |
||||||||||||||||||||
ний АД1 или материал САП [22], то |
|
При |
изготовлении |
|
|||||||||||||||||||||||
620—640 °С; давление в обоих случаях |
углеалюминиевых |
композитов |
равно |
||||||||||||||||||||||||
составляет |
30—35 |
МПа |
[22]. |
Время |
мерное |
распределение |
|
элементарных |
|||||||||||||||||||
выдержки под давлен 1 ем в этих усло |
волокон |
(филаментов) |
|
достигается |
|||||||||||||||||||||||
виях |
15—20 |
мин |
[6 j. При |
использо |
только при условии, что процесс вы |
||||||||||||||||||||||
вании для армирования волокон бора |
полняется в присутствии жидкой фазы. |
||||||||||||||||||||||||||
с покрытием карбида кремния компо |
Процесс ведут в вакууме, при высоких |
||||||||||||||||||||||||||
зиции на основе алюминия получают |
температурах, |
обеспечивая |
|
компакти- |
|||||||||||||||||||||||
диффузионной сваркой |
по |
режимам, |
рование заготовки в режимах контакт |
||||||||||||||||||||||||
зависящим не только от материала |
ного |
плавления элементов |
матричных |
||||||||||||||||||||||||
матрицы, но и от атмосферы, в которой |
сплавов [6, 13]. На углеродную ленту |
||||||||||||||||||||||||||
осуществляется |
процесс |
[21]. |
|
|
предварительно |
наносят |
барьерный |
||||||||||||||||||||
Для композиций, в которых при |
слой карбида кремния, затем — техно |
||||||||||||||||||||||||||
меняют |
|
нелегированную |
матричную |
логическое |
покрытие |
никеля, |
после |
||||||||||||||||||||
составляющую (при объемной доле во |
чего |
плазменным |
методом |
производят |
|||||||||||||||||||||||
локон |
36%), |
диффузионная |
сварка |
плазменное |
|
напыление |
алюминия |
||||||||||||||||||||
проводится |
при |
|
температуре |
500 °С, |
[6]. |
Для того чтобы |
образующаяся |
||||||||||||||||||||
при |
приложении |
давления |
35 МПа |
в |
процессе |
спрессовывания |
сборной |
||||||||||||||||||||
и выдержке 1 ч, если используют |
заготовки |
|
алюминиево-никелевая |
||||||||||||||||||||||||
обычную (воздушную) атмосферу; |
при |
жидкая (Ьаза эвтектического состава не |
|||||||||||||||||||||||||
использовании защитной атмосферы ар |
вытекала под давлением активной ча |
||||||||||||||||||||||||||
гона температура может быть увели |
сти рабочего инструмента, в камере |
||||||||||||||||||||||||||
чена |
до |
593 °С, |
давление |
до 70'МПа, |
обеспечивается |
|
(подачей |
|
аргона) |
||||||||||||||||||
а время |
выдержки |
сокращается |
до |
противодавление, равное 0,2 МПа. Про |
|||||||||||||||||||||||
о мин. При применении прочных ле |
цесс |
осуществляют |
при |
температуре |
|||||||||||||||||||||||
гированных |
матриц |
композит |
форми |
640—650 °С, давлении 1,7—3,0 МПа. |
|||||||||||||||||||||||
руется диффузионной сваркой при тем |
Последующая |
термическая |
обработка |
||||||||||||||||||||||||
пературе |
490—565 °С |
при |
давлении |
проводится |
по |
режиму |
|
670 °С, |
300 с |
||||||||||||||||||
~40 МПа в вакууме, однако время |
и обеспечивает в результате гомогени |
||||||||||||||||||||||||||
выдержки под давлением велико (1ч). |
зирующего |
отжига |
получение |
твер |
|||||||||||||||||||||||
Композит алюминий — бериллий мо |
дого раствора никеля в матричной |
||||||||||||||||||||||||||
жет быть получен диффузионной свар |
алюминиевой составляющей |
[6]. |
|
||||||||||||||||||||||||
кой при температуре 538 °С, давлении |
и |
Процесс этого же типа применяется |
|||||||||||||||||||||||||
50 МПа и выдержке 5 мин [21 ]. Диф |
для |
изготовления |
бороалюминия |
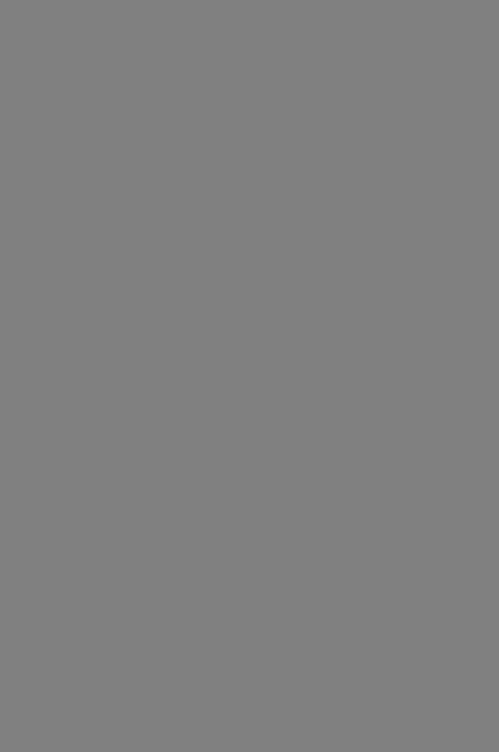
|
|
|
|
|
|
|
|
|
2d/ |
|
|
|
|
|
|
|
—^рф— |
Gpi |
|
^ |
\ f S*— dj arctg -т^гг) |
||||||||||
|
|
|
|
|
|
|
|||||||||
Здесь Opi — радиальное |
напряжение |
радиуса j ^ 80He растяжения р* шах = |
|||||||||||||
в рассматриваемом слое ячеек компо- |
— R |
----- j", |
hjn — расстояние от по |
||||||||||||
г* |
|
= |
Рoam |
In |
К |
— в |
зоне |
||||||||
зита I —oPi |
~ |
верхности |
растяжения |
заготовки |
|||||||||||
растяжения; |
|
—ор/ = |
Рo8m In |
-------- |
при изгибе до ближайшего к ней слоя |
||||||||||
|
волокон). |
|
|
|
|||||||||||
в зоне сжатия (знак «—» для воны |
Окружное |
напряжение |
а0ф связано |
||||||||||||
растяжения при изгибе, знак «+» для |
с —арф условием пластичности: |
||||||||||||||
зоны сжатия |
очага |
|
деформации |
при |
|
±(70ф = |
СГрф zfc Osm, |
||||||||
изгибе)J ; |
—Орф — |
текущее |
значение |
|
|||||||||||
где % |
имеет знак «+» для зоны растя |
||||||||||||||
радиального |
|
напряжения |
в |
ячейке |
|||||||||||
|
жения, знак с—» — для зоны сжатия |
||||||||||||||
композита; |
|
озтп — предел |
текучести |
в очаге деформации при изгибе. |
|||||||||||
матрицы |
композита; |
ф — угловая |
Возможности формообразования из |
||||||||||||
координата |
ячейки |
|
композита |
(см. |
делий из композита свободным изгибом |
||||||||||
разд. 4.4); S — шаг укладки волокон; |
невелики, как правило, процесс осу |
||||||||||||||
dj — диаметр сечения волокна; R — |
ществляют [13, 23] в условиях дей |
||||||||||||||
наружный радиус изгиба, равный сум |
ствия |
радиального |
подпора, создава |
||||||||||||
ме внутреннего радиуса изгиба г и |
емого |
технологическими |
обкладками |
||||||||||||
толщины h изгибаемой заготовки; Р — |
или |
замкнутыми |
технологическими |
||||||||||||
коэффициент |
Лодэ, |
равный |
в |
данном |
оболочками. Необходимо |
напряжение |
|||||||||
случае 1,16; |
р* — |
текущее |
значение |
подпора |
|
|
|
—оп = amf — Paem + |
P<Jem In |
|
exp |
|
—2df |
arctg |
■J/S2 — d) ^ |
||||||||||
|
y s z |
— dj |
|
S - d f |
J ' |
||||||||||||
Основным |
показателем |
технологи |
подпора, шага укладки волокон, их |
||||||||||||||
ческой пластичности при гибке листо |
диаметра и увеличением параметраhm. |
||||||||||||||||
вых заготовок |
является |
отношение |
При гибке в металлическом контей |
||||||||||||||
внутреннего радиуса изгиба к тол |
нере (замкнутой технологической обо |
||||||||||||||||
щине заготовки: |
|
|
|
|
лочке) |
сталеалюминиевых |
заготовок |
||||||||||
|
|
|
|
r/h = |
|
|
|
(Vf = |
30%) показатель r/h находится |
||||||||
|
|
|
|
|
|
|
в пределах 2,5—11, а при гибке боро |
||||||||||
S(h — df — 2hm) - |
bmh (S - df) |
алюминиевых |
листовых |
заготовок |
|||||||||||||
по схеме с жесткоэластичным подпором |
|||||||||||||||||
|
|
26mh ( S - d f) |
' |
* |
|||||||||||||
|
|
его значения |
составляют |
2—8 |
[13] |
||||||||||||
Схема |
|
гибки |
представлена |
на |
в зависимости от параметров внутрен |
||||||||||||
|
него строения ВКМ. |
сталеалюми |
|||||||||||||||
рис. 4.17. В качестве материала вкла |
Изгиб |
армированных |
|||||||||||||||
дыша применяют резину, |
полиуретан, |
ниевых заготовок по схеме, когда |
|||||||||||||||
свинец |
и |
другие материалы |
[23]. |
линия изгиба нормальна к направле |
|||||||||||||
Линия |
изгиба параллельна располо |
нию волокон в заготовке, осущест |
|||||||||||||||
жению осей волокон |
композита. |
про |
вляют |
при |
температурах |
20—200 X |
|||||||||||
Управление |
процессом |
гибки |
с углом изгиба 40—130° (при более |
||||||||||||||
филей из компактных листовых арми |
высоких |
температурах |
формообразо |
||||||||||||||
рованных |
заготовок |
осуществляется |
вания, |
т. |
е. |
при |
315—454 °С, |
угол |
|||||||||
варьированием |
величин напряжений |
изгиба |
составляет |
до 52—118*0 |
till- |
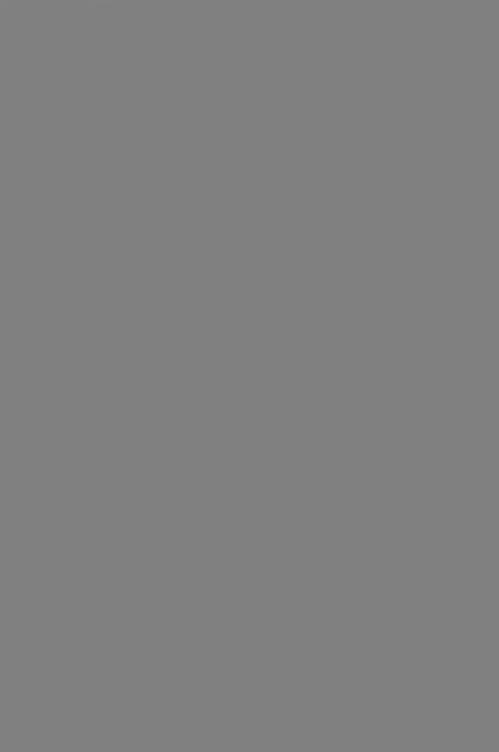
4.14. Механические свойства композита ВКА-1 [13]
/, °с |
а, МПа |
Е, ГПа |
20 |
1000—1200 |
250 |
300 |
900 |
235 |
400 |
700 |
228 |
500 |
500 |
220 |
4.15. Температурный коэффициент линейного расширения а бороалюминия [в]
а-10е, °С~1, в интервалах , °с
|
2 0 - |
100— |
2 0 0 - |
300 — |
4 0 0 - |
|
100 |
200 |
300 |
400 |
500 |
45 |
4,7 |
5,0 |
5,3 |
ел |
6,6 |
30 |
10,2 |
5,4 |
— |
4,0 |
5,7 |
4.17. Прочность и жесткость ортогонально армированного бороалюминия [10]
Объем |
&Q (МПа) |
|
|
||
ная до |
|
|
|||
ля воло |
£ 0 (ГПа) |
при углах*гРаДУсы» |
|||
кон, %, |
|||||
в направ |
между продольным |
направле |
|||
лении |
нием н осью нагружения |
||||
полос |
|
|
|
||
про дольном |
В CV |
|
|
|
|
|
.§ |
0 |
45 |
00 |
|
|
4) В |
||||
|
В Р* |
|
|
|
|
|
о в |
|
|
|
|
20 |
20 |
301—306 |
52—71 |
264—290 |
|
144—173 |
62—67 |
140—162 |
|||
|
|
||||
25 |
15 |
326—354 |
75—87 |
256—296 |
|
131—147 |
69—71 |
77-91 |
|||
|
|
||||
30 |
10 |
672—695 |
66—71 |
159—160 |
|
196—244 |
93 |
67—83 |
|||
|
|
||||
35 |
5 |
735—773 |
42—50 |
160-178 |
|
181—228 |
43—52 |
58—71 |
|||
|
|
4.16. |
Временное сопротивление |
|
П р и м е ч а н и е . |
Общая объем |
||||||
одноосно-армированного бороалюминия |
ная доля волокон 40%. |
|
||||||||
в зависимости от угла разориентации |
|
|
|
|
|
|||||
осей нагружения и армирования |
6 |
4.18. |
Прочность при растяжении |
|||||||
[10] |
|
|
|
|
|
|||||
|
|
|
|
|
материала алюминий — бор — |
|||||
0, гра |
|
0, гра |
|
|
сталь |
[10] |
|
|
|
|
|
*е |
Ев |
|
|
|
|
|
|||
дусы |
|
Ев дусы |
Объемная доля |
ди МПа, |
при рас- |
|||||
|
|
|
|
|
|
|||||
|
|
|
|
|
|
волокон, % |
тяжении |
вдоль оси |
||
0 |
800 |
185 |
20 |
200 |
120 |
|
|
|
|
|
5 |
820 |
180 |
30 |
— |
|
стальной |
волокон |
стальных |
||
10 |
760 |
180 |
45 |
120 |
120 |
бора |
проволоч |
|||
проволо |
бора |
ных воло |
||||||||
15 |
630 |
— |
|
|
|
|
ки |
|
|
кон |
П р и м е ч а н и е . |
Объемная |
доля |
20 |
5 |
652 |
140 |
||||
волокон 30%. |
|
|
|
|
30 |
5 |
835 |
133 |
||
|
|
|
|
|
|
20 |
10 |
640 |
240 |
|
армированных |
материалов |
является |
30 |
10 |
797 |
233 |
||||
|
|
|
|
|
||||||
значительное влияние взаимного рас |
рование в разных направлениях, ком |
|||||||||
положения осей армирования и при |
||||||||||
ложения нагрузки (табл. 4.16). |
сни |
бинированные матрицы). |
ортого |
|||||||
Существуют |
различные |
пути |
Механические |
свойства |
||||||
жения |
анизотропии |
характеристик |
нально |
армированного бороалюминия |
||||||
(в первую очередь — прочности) |
боро |
представлены в табл. 4.17. |
|
|||||||
алюминия |
(перекрестно-послойное |
Менее эффективным |
(в отношении |
|||||||
армирование, |
комбинированное |
арми- |
удельных и абсолютных характеристик |
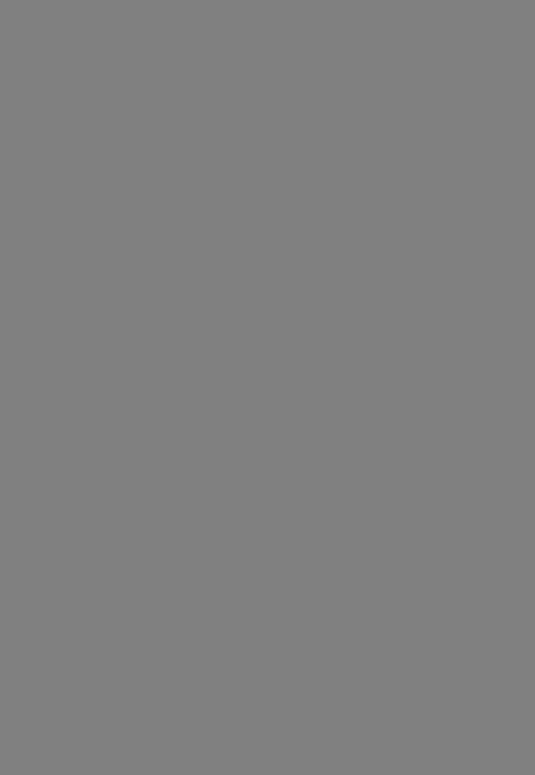
4.20. Механические свойства бороалюминиевых композиций с легированными матрицами
Материал |
vf, % |
|
|
Состояние композита |
|
|
|
о, |
|
|
Еш |
|||
матрицы |
|
|
|
|
МПа |
|
ГПа |
|||||||
|
|
|
|
|
|
|
|
|
|
|
||||
|
30 |
|
После горячего |
деформирова |
870 |
125 |
161,2 |
93,7 |
||||||
|
35 |
|
ния |
|
|
|
|
885 |
92 |
187,2 |
103,6 |
|||
АМгб |
42 |
|
|
|
|
|
|
|
915 |
57 |
202,0 |
127,1 |
||
30 |
|
После отжига |
|
|
865 |
154 |
_ |
_ |
||||||
|
35 |
|
|
|
880 |
128 |
— |
— |
||||||
|
42 |
|
|
|
|
|
|
|
930 |
79 |
— |
— |
||
АМг2 |
35 |
|
После горячего деформирова |
982 |
174 |
189,0 |
102,9 |
|||||||
|
45 |
|
ния |
|
|
|
|
1257 |
168 |
214,7 |
130,5 |
|||
4.21. Прочность при повышенных температурах бороалюминиевых |
|
|
||||||||||||
композиций с комбинированной матрицей |
|
|
|
|
|
|
|
|||||||
|
|
|
|
|
|
|
Объемная |
&t, МПа, при температуре, |
||||||
|
Материал |
|
|
|
|
|
С’С |
|
|
|||||
|
|
|
доля воло |
|
|
|
|
|
|
|||||
|
|
|
|
|
|
|
кон, |
% |
|
|
360 |
|
600 |
|
|
|
|
|
|
|
|
|
|
|
|
|
|
||
Д20—АД1—В |
|
|
|
|
|
25 |
|
|
507 |
|
360 |
|
||
|
|
|
|
|
30 |
|
|
615 |
|
435 |
|
|||
|
|
|
|
|
|
|
35 |
|
|
687 |
|
465 |
|
|
1201—АД1—в |
|
|
|
|
|
30 |
|
|
593 |
|
410 |
|
||
|
|
|
|
|
37 |
|
|
710 |
|
493 |
|
|||
|
|
|
|
|
|
|
|
|
|
|
||||
1201—АМг2—В |
|
|
|
|
|
27 |
|
|
540 |
|
370 |
|
||
|
|
|
|
|
32 |
|
|
655 |
|
425 |
|
|||
|
|
|
|
|
|
|
|
|
|
|
||||
АД1—АМгб—В |
|
|
|
|
|
38 |
|
|
705 |
|
577 |
|
||
|
|
|
|
|
41 |
|
|
737 |
|
595 |
|
|||
|
|
|
|
|
|
|
|
|
|
|
||||
упрочняемые |
сплавы |
|
АМг2, |
АМгЗ, |
В композите КАС-1 в качестве упроч- |
|||||||||
АМгб, а также термически упрочня |
нителя |
применяют проволочные |
во |
|||||||||||
емые сплавы АВ, Д16, Д20, В96 и др. |
локна из стали марки ВНС-9. Механи |
|||||||||||||
В качестве упрочнителей |
применяют |
ческие свойства композита КАС-1 при |
||||||||||||
проволочные |
волокна |
|
из |
коррозион |
комнатной температуре |
следующие: |
||||||||
но-стойких сталей (преимущественно |
а1 == 1300-г-1450 МПа; Е±= |
110 ГПа; |
||||||||||||
из сталей с метастабильным при холод |
сг_! = |
350 МПа (на базе 107 циклов); |
||||||||||||
ной деформации аустенитом, претерпе |
Ti2 = |
МПа; |
\ip — 0,33. Этот |
ком |
||||||||||
вающим мартенситное |
превращение |
позит |
сохраняет |
высокую |
кратко |
|||||||||
при холодном волочении). Наиболее |
временную и |
|
длительную прочности |
|||||||||||
полно данные о проволочных волокнах |
при повышенных |
температурах: |
при |
|||||||||||
из сталей и их влиянии на свойства |
300 °С |
дг = |
960 МПа; |
при |
500 °С |
|||||||||
сталеалюминиевых |
композитов |
рас |
= 400 МПа; |
о100 = 450 МПа |
при |
|||||||||
смотрены в работах |
[5, |
10, 11, 13]. |
температуре испытаний 300 °С. |
|
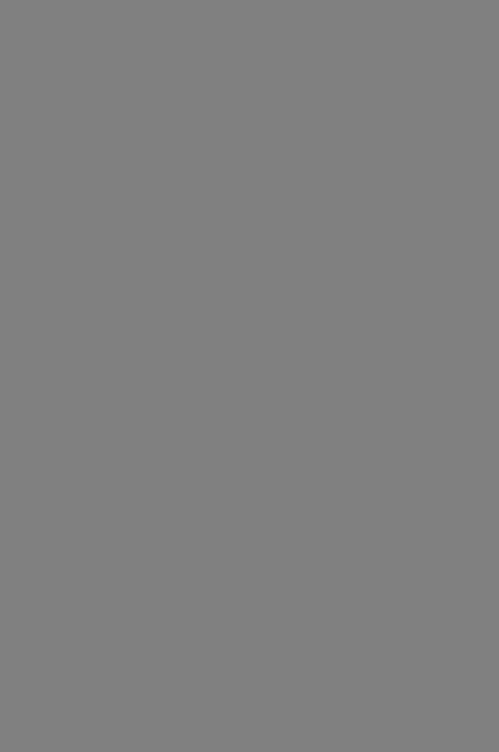
состоянии |
составляет |
136—165 МПа, |
предел выносливости |
(без проведения |
||||||||||||
а после упрочняющей термообработки |
термообработки) — 350 МПа, а времен |
|||||||||||||||
(матрица |
— |
сплав |
ДВ) |
— 235— |
ное сопротивление материала зависит |
|||||||||||
280 МПа, модуль упругости после |
от температуры испытаний следующим |
|||||||||||||||
проведения |
|
упрочняющей |
термиче |
образом |
[13 J: |
|
|
|
|
|
||||||
ской обработки достигает 115 ГПа, |
|
|
|
|
|
|
|
|
||||||||
Температура испытаний, °С |
200 |
300 |
400 |
|
500 |
|||||||||||
аъ МПа |
|
|
|
|
|
|
1100—1250 < |
1200 |
900—100 |
700—750 |
||||||
4.24. Прочность композита |
|
Сталеалюминий |
при |
испытаниях |
||||||||||||
магний — бор |
[21] |
|
|
|
|
в различных средах имеет высокие |
||||||||||
|
|
|
|
|
|
|
|
|
характеристики |
коррозионной |
стой |
|||||
Объемная |
|
а,, МПа, при |
кости |
(табл. 4.25). |
|
композиты |
дру |
|||||||||
|
|
|
|
|
|
Сталеалюминиевые |
|
|||||||||
доля |
воло |
|
|
|
|
|
|
гих составов также обладают высо |
||||||||
кон, |
% |
|
|
растяжении |
|
изгибе |
||||||||||
|
|
|
|
|
кими |
механическими |
и |
технологиче |
||||||||
|
|
|
|
|
|
|
|
|
скими характеристиками (табл. 4.26— |
|||||||
25 |
|
|
880-920 |
|
|
1140 |
4.29). |
Термическая |
обработка стале- |
|||||||
|
|
|
|
алюминия обычно проводится по ре |
||||||||||||
30 |
|
|
J60 |
|
|
— |
||||||||||
45 |
|
|
1200 |
|
|
— |
жиму закалки и отпуска матричной |
|||||||||
50 |
|
|
1250 |
|
|
— |
составляющей, однако при выборе тем |
|||||||||
70 |
|
|
— |
|
|
— |
пературы нагрева перед закалкой не |
|||||||||
75 |
|
|
1330 |
|
|
1600 |
обходимо учитывать, |
что на этой |
ста |
|||||||
|
|
|
|
дии не должно происходить разупроч |
||||||||||||
|
|
|
|
|
|
|
|
|
||||||||
|
|
|
|
|
|
|
|
|
нения |
проволочных |
|
волокон |
(тер |
|||
|
|
|
|
|
|
|
|
|
мического |
или |
разупрочнения, |
свя |
||||
П р и м е ч а н и е . |
При |
сжатии и |
занного с обратным мартенсит-аусте- |
|||||||||||||
объемной |
доле |
волокон |
70% |
= |
нитным |
|
превращением), |
поэтому |
||||||||
= 3200 МПа. |
|
|
|
|
|
в ряде случаев, особенно при исполь |
||||||||||
|
|
|
|
|
|
|
|
|
зовании в материале проволочных во |
|||||||
|
|
|
|
|
|
|
|
|
локон из сталей марок 08X18Н9Т |
|||||||
4.25. Коррозионные характеристики композита КАС-1 [5] |
|
|
|
|
||||||||||||
Состояние |
|
|
Коррозионная |
ореда |
|
Ои МПа |
|
|
|
Скорость |
||||||
торцов |
об |
|
В исходном |
после испыта |
коррозии |
|||||||||||
разца компо |
|
(выдержка |
2 месяца) |
«к- >0*. |
||||||||||||
зита |
|
|
|
|
|
|
|
|
состоянии |
ний в корро |
||||||
|
|
|
|
|
|
|
|
|
|
|
зионной среде |
кг/м* - ч |
||||
Неизолиро |
Тропическая |
камера |
1336 |
|
1345 |
|
|
0,28 |
|
|||||||
ванные |
|
Морская вода |
|
1336 |
|
1224 |
|
|
2,45 |
|
||||||
|
|
|
Полное |
погружение в |
1336 |
|
1172 |
|
|
55,40 |
|
|||||
|
|
|
3% -ный раствор пова |
|
|
|
|
|
|
|
|
|||||
|
|
|
ренной |
соли |
с добавкой |
|
|
|
|
|
|
|
|
|||
|
|
|
0,1% НяОа |
|
|
|
|
|
|
|
|
|
|
|
||
Изолиро |
|
Тропическая |
камера |
1336 |
|
1390 |
|
|
0,07 |
|
||||||
ванные |
|
Морская |
вода |
|
1336 |
|
1274 |
|
|
0,76 |
|
|||||
|
|
|
Полное |
погружение в |
1336 |
|
1251 |
|
|
5,23 |
|
3% -ный раствор поварен ной соли с добавкой 0,1% На0 2

4.30. Остаточные напряжения в составляющих сталеалюминия [10] после горячего компактирования (матрица — сплав АМгв)
|
|
Межкомпонентные |
|
|
Диаметр |
остаточные напря |
|
Vf. % |
жения, МПа |
||
волокон. |
|
|
|
|
мкм |
в матрице |
в волок |
|
|
композита |
нах |
15 |
200 |
+45 |
—265 |
500 |
+70 |
—340 |
|
|
1300 |
+ 105 |
—515 |
4.31. Пределы выносливости ВКМ А1—В и А1—С
Темпера |
Предел выносливости, МПа, |
|||
|
при |
числе циклов |
||
тура испы |
|
|
|
|
таний, °С |
10“ |
10“ |
107 |
10® |
|
Бороалюминий (Vf = 47%) |
|
||||||
20 |
I |
690 |
I *620 |
I |
550 |
I |
430 |
250 |
1| |
600 |
1 400 |
1 240 |
1 |
— |
|
Углеалюминнй (Vf = 33-^-38%) |
|||||||
20 |
| |
250 |
200 |
| |
170 |
1 — |
|
|
|
|
|
|
|
|
|
|
|
|
|
|
же в связи с наличием межкомпо |
||||||||||
|
|
|
|
|
|
|
|
|
нентных |
остаточных |
напряжений |
||||||||
П р и м е ч а н и е . |
«+» |
— |
знак |
(связанных с различием модулей упру |
|||||||||||||||
напряжений растяжения, «—» — знак |
гости |
матричной |
составляющей |
и |
|||||||||||||||
напряжений сжатия. |
|
|
|
|
|
волокон, а также с различием терми |
|||||||||||||
|
|
|
|
|
|
|
|
|
ческих коэффициентов линейного рас |
||||||||||
|
|
|
|
|
|
|
|
|
ширения матрицы и волокон) упрочне |
||||||||||
и 12Х18Н10Т, |
приходится |
проводить |
ние сталеалюминия после закалки и |
||||||||||||||||
отпуска может быть меньше ожида |
|||||||||||||||||||
неполную |
закалку |
матрицы |
компо |
емого. |
|
|
|
|
|
|
|
|
|
||||||
зита, т. е. закалку после нагрева до |
Влияние объемной доли волокон на |
||||||||||||||||||
температуры, более низкой, чем при |
упругие |
характеристики |
сталеалю |
||||||||||||||||
нято для некоторых марок алюмини |
миния проявляется |
|
следующим обра |
||||||||||||||||
евых сплавов. По этой причине, а так- |
зом |
[10]: |
|
|
|
|
|
|
|
|
|||||||||
Объемная доля волокон, % |
|
5 |
8 |
|
15 |
20 |
|
30 |
40 |
|
|
50 |
|||||||
Модуль упругости, ГПа: |
|
|
72,8 |
76.0 |
82,1 |
89,7 |
112,3 |
124,0 |
143,0 |
||||||||||
при растяжении |
|
|
|
|
|||||||||||||||
при изгибе |
|
|
|
|
|
|
72,8 |
76.1 |
85,3 |
96,6 |
117,0 |
— |
|
— |
|||||
Межкомпонентные |
остаточные |
на |
Повышенные |
циклические |
|
харак |
|||||||||||||
пряжения |
в сталеалюминии представ |
теристики |
композитов наблюдаются |
||||||||||||||||
лены в табл. 4.30. |
|
|
|
|
|
не только |
при |
растяжении-сжатии, |
|||||||||||
Композиты на основе легких метал |
но и при циклическом консольном |
||||||||||||||||||
лов и сплавов обладают повышенными |
изгибе. Например, |
материал АМгЗ— |
|||||||||||||||||
характеристиками при |
кратковремен |
Н16К4М5Т2 |
характеризуется |
значе |
|||||||||||||||
ных и длительных, статических и ди |
ниями |
циклической |
прочности |
при |
|||||||||||||||
намических нагружениях |
в широких |
указанном виде испытаний, приведен |
|||||||||||||||||
температурных |
диапазонах |
испыта |
ными в табл. 4.32. |
|
|
|
|
|
|
||||||||||
ний. Обладают |
они |
существенными |
Значительный объем данных накоп |
||||||||||||||||
преимуществами перед традиционными |
лен |
по |
характеристикам |
углеалюми |
|||||||||||||||
металлическими |
материалами |
и |
при |
ниевых |
композитов, |
однако |
большой |
||||||||||||
циклическом |
нагружении. |
В |
ча |
разброс |
характеристик |
углеродных |
|||||||||||||
стности, бороалюминий и углеалюми- |
волокон и лент, различие в технологи |
||||||||||||||||||
ний имеют показатели предела вы |
ческих решениях процессов изготовле |
||||||||||||||||||
носливости |
|
[21], |
|
представленные |
ния полуфабрикатов и изделий из этого |
||||||||||||||
в табл. 4.31. |
|
|
|
|
|
|
|
материала |
проявляется |
в |
широком |
